Aumento de la estabilidad del proceso de moldeo por inyección de materiales reciclados posconsumo mediante el uso de la presión de cavidad para el control del proceso
Katharina Hornberg, M.Sc.. Spritzgießen | Prozessregelung Injection moulding | Process Control del Institut für Kunststoffverarbeitung (IKV) in Industrie und Handwerk an der RWTH Aachen
15/05/2023En el moldeo por inyección, el proceso se ve continuamente afectado por perturbaciones que influyen en la calidad de la pieza. En consecuencia, es necesario ajustar constantemente los parámetros del proceso para mantener los requisitos de calidad. Por ejemplo, cuando cambia la viscosidad del material, hay que ajustar el tiempo de cambio y el nivel de presión de mantenimiento para evitar marcas de cambio en la pieza o la formación de rebabas. Al procesar materiales reciclados, especialmente reciclados posconsumo, los cambios de viscosidad de los lotes son muy pronunciados. Como los lotes de material reciclado siguen siendo comparativamente pequeños, es necesario realizar frecuentes ajustes en el proceso. Además, hay ingredientes incompatibles en el material, lo que suele provocar grandes fluctuaciones en el proceso. En este artículo se presenta un control de la presión de cavidad como concepto alternativo al control convencional del proceso, con el que se pretende compensar los efectos de las influencias perturbadoras.
Se realizan ensayos de moldeo por inyección procesando dos lotes diferentes de material posconsumo para evaluar el potencial de compensación de un método de control de la presión de cavidad. Además, se modifican los ajustes del proceso para reflejar las influencias térmicas y las fluctuaciones de dosificación como variables perturbadoras adicionales. Los ensayos se realizan comparativamente con control de presión de cavidad y con control de proceso convencional. La calidad de la pieza se evalúa mediante el peso y las propiedades mecánicas de la pieza. La evaluación del peso de la pieza muestra una consistencia del proceso significativamente mayor con el control de la presión de cavidad. Los efectos de las fluctuaciones del lote en el peso de la pieza pueden reducirse en más de un 70%. En el caso de los cambios térmicos, la consistencia del proceso es incluso superior al 80% en comparación con el proceso convencional. Sin embargo, las propiedades mecánicas fueron más de 1 MPa superiores con el control de proceso convencional, lo que podría deberse a un nivel de presión inferior del plan experimental para el control de la presión de la cavidad. En conclusión, los resultados muestran claramente el potencial del control de proceso basado en variables de proceso. Mediante el control unificado de fase de la presión de la cavidad, se pueden compensar las fluctuaciones del lote, así como las influencias térmicas. La calidad puede ajustarse específicamente mediante el nivel de presión de retención. Este enfoque aumenta significativamente la consistencia del proceso cuando se procesan materiales reciclados posconsumo, lo que permite utilizar el material para nuevas aplicaciones, aumentar el uso de residuos posconsumo para nuevos productos y cumplir los objetivos climáticos.
Introducción
Con un volumen total de procesamiento de 14,23 millones de toneladas en Alemania, los reciclados posconsumo (PCR) representan 1,02 millones de toneladas, una cuota de aproximadamente el 7%, y siguen aumentando en torno al 4,1% anual [LSH20]. Es necesario aumentar la procesabilidad de los residuos plásticos para conseguir una industria de plásticos reciclables. El polipropileno (PP) es el plástico más utilizado para artículos producidos en masa mediante moldeo por inyección, y representa la segunda mayor parte de la PCR después del PE [LSH20]. Los residuos se trituran, se lavan, se clasifican finamente, se secan y se extrusionan para producir un nuevo granulado de plástico [RAK17]. En la norma DIN ISO/TR 17098 [NN14] se especifica el reciclaje de los residuos de plástico posconsumo y las sustancias y materiales que los componen. Sin embargo, los rangos de los constituyentes individuales se mantienen amplios en varios porcentajes, lo que provoca que las propiedades del material difieran mucho de un lote a otro. Entre los componentes incompatibles se encuentran los metales, el vidrio y el papel [NN14].
El uso de materiales reciclados provoca fluctuaciones en las condiciones de procesamiento debido a la diferente composición e historial de los lotes de material [MK11, BB14]. Las fluctuaciones en la calidad de la pieza resultante aumentan con el uso de reciclados y provocan una disminución de las propiedades mecánicas y ópticas de la pieza [ASUM03, MOY08]. La investigación sobre el reciclado posconsumo es débil debido a la gran variación en la composición del reciclado, lo que dificulta la consecución de condiciones de ensayo reproducibles [BHHM08, PH07, vCA+21]. Por lo tanto, la reproducibilidad del proceso es baja mediante el uso de PCR, que es causada por la baja consistencia de las propiedades de PCR, además de las influencias perturbadoras habituales, tales como cambios en el proceso térmico. Investigaciones recientes ya han demostrado que el uso de un concepto de control de proceso en tiempo real puede permitir un mejor procesamiento y una mayor consistencia del proceso para el procesamiento de reciclado [MDK+20]. Sin embargo, el concepto de control de procesos presentado se limita al control de la fase de inyección. Este artículo propone un concepto alternativo de control de procesos basado en la presión de cavidad, que controla el proceso en un enfoque de unificación de fases, especificando una referencia de presión de cavidad para el ciclo completo. El objetivo es aumentar la consistencia del proceso al procesar diferentes materiales en diversas condiciones ambientales para poder producir piezas de calidad constante.
3.2 Estado de la técnica
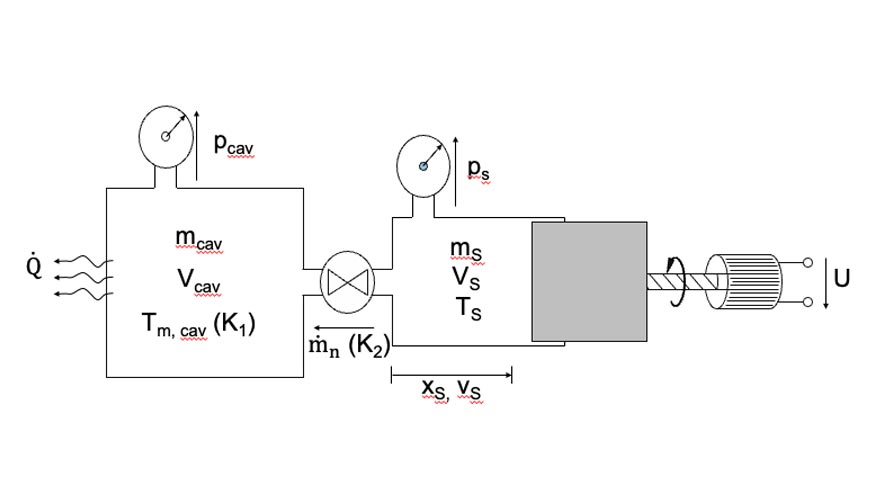
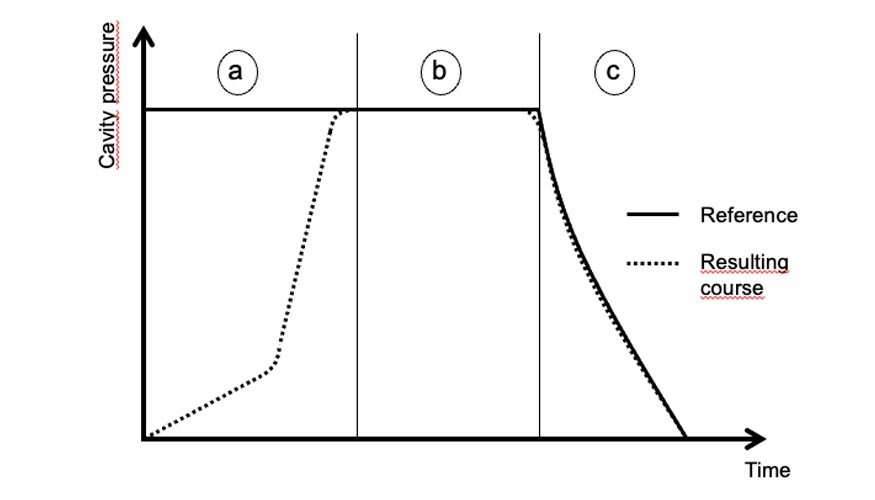
3.3 Diferencias entre los lotes de PCR en el comportamiento pvT
3.4 Métodos
Se utilizó una máquina de inyección del tipo Allrounder 520A 1500-400/400, fabricada por Arburg GmbH Co. KG, Loßburg, Alemania. El algoritmo de control se aplicó a un controlador externo en tiempo real “PXI-8108” y se configuró en LabVIEW 2020, de National Instruments, Austin (TX), EEUU. El tiempo de muestreo del controlador en tiempo real se fijó en 8 ms. La geometría de la pieza y las posiciones de los sensores se muestran en la figura 3.4.
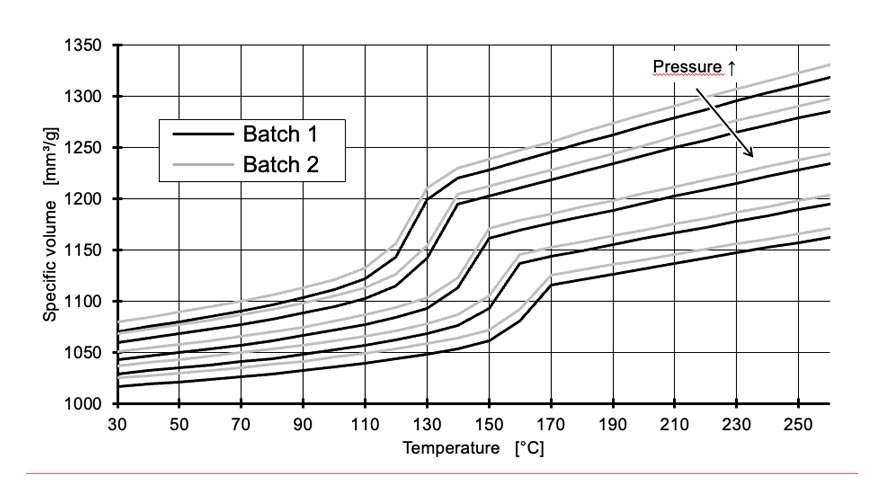
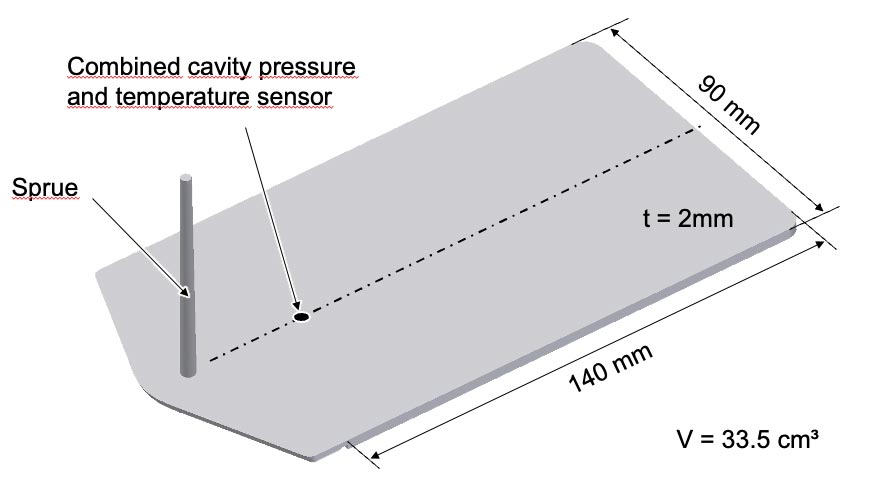
3.5 Resultados
3.5.1 Análisis de secciones delgadas de piezas de plástico reciclado
La composición de los lotes de material influye en los defectos del interior de las piezas moldeadas por inyección. Las impurezas incompatibles como el metal, el vidrio o el papel pueden aparecer en la PCR con un porcentaje pequeño. Dado que los defectos pueden reducir las propiedades mecánicas de las piezas moldeadas por inyección, se investigaron las inclusiones de material y las profundidades de corte (causadas por contaminantes) mediante imágenes microscópicas ligeras de sección fina utilizando un microscopio Leica DM4500M, fabricado por LeicaBiosystems, Wetzlar, Alemania. Los exámenes microscópicos estructurales se realizaron con un aumento de 200. La figura 3.5 muestra los defectos cerca y lejos del bebedero a través de la sección transversal de la pieza.
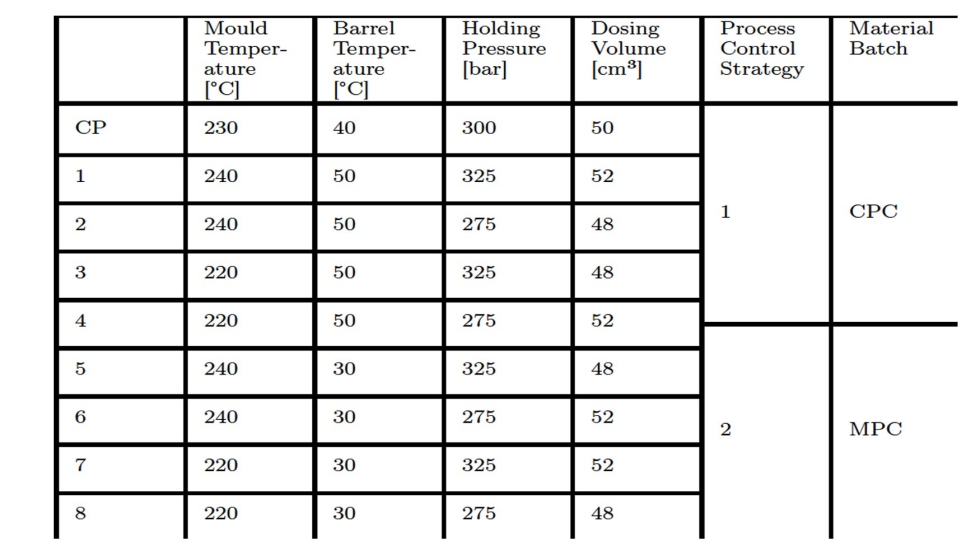
3.5.2 Influencia de las perturbaciones en la estabilidad del proceso para diferentes estrategias de control
La influencia de los cambios de los parámetros del proceso en el peso de la pieza se muestra en la Figura 3.6 para las diferentes estrategias de control del proceso y lotes de material. Puede verse claramente que la reproducibilidad de la calidad de la pieza puede aumentar significativamente con el MPC. Se realizó un análisis estadístico de regresión para evaluar en detalle los datos experimentales: las piezas con control de la presión de cavidad son, en general, más ligeras. No es posible una transferencia completa de los parámetros experimentales entre la presión del tornillo y la presión de la cavidad. Con el control convencional del proceso, la presión de la cavidad desciende durante la fase de mantenimiento de la presión, mientras que con el control de la presión de la cavidad, la presión de la cavidad se mantiene constante y, por tanto, aumenta la presión del tornillo. La diferencia de peso entre las estrategias de control tiene una influencia insignificante en la variación del peso de la pieza al cambiar los ajustes del proceso, por lo que se da la significación de los resultados de la prueba.
Además, la estabilidad del proceso dentro de un entorno de ensayo indica la capacidad de compensar perturbaciones aleatorias, como impurezas en el material PCR (véase 3.5.1). La estabilidad del proceso es mayor cuando se utiliza el control de presión de cavidad. La desviación estándar del peso es de 10,2 mg de media, mientras que la desviación estándar con el control de proceso convencional es de 27,5 mg. Esto significa que las fluctuaciones cíclicas en la homogeneidad del material debidas a las impurezas se compensan más eficazmente.
3.5.3 Análisis mecánico
Las propiedades mecánicas de las piezas moldeadas por inyección se ven influidas por la estrategia de control, así como del lote de material y de los ajustes del proceso. Las barras de tracción a lo largo de la dirección dúctil, mientras que las varillas de tracción transversales a la dirección del flujo
muestran un fallo frágil. Al comparar las propiedades mecánicas a lo largo de la dirección de flujo en rotura, la resistencia a la tracción es dos veces mayor utilizando el control de la presión de cavidad, así como el alargamiento a la rotura. La resistencia a la tracción es de 11,1 MPa (6 MPa) y el alargamiento a la rotura es del 90% (cf. 50%). En el caso de las varillas de tracción transversales a la dirección de flujo, no se aprecian diferencias significativas.
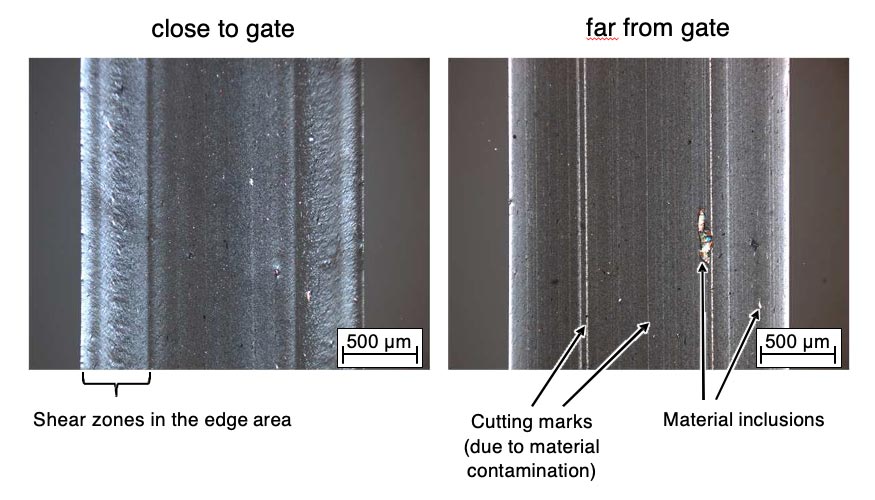
La resistencia máxima a la tracción es uno de los parámetros mecánicos más importantes, además de la resistencia a la tracción y el alargamiento a la rotura. Los valores medios y las desviaciones estándar de la resistencia máxima a la tracción longitudinal y transversal a la dirección de la Tabla 3.2 como media de todos los puntos de ensayo.
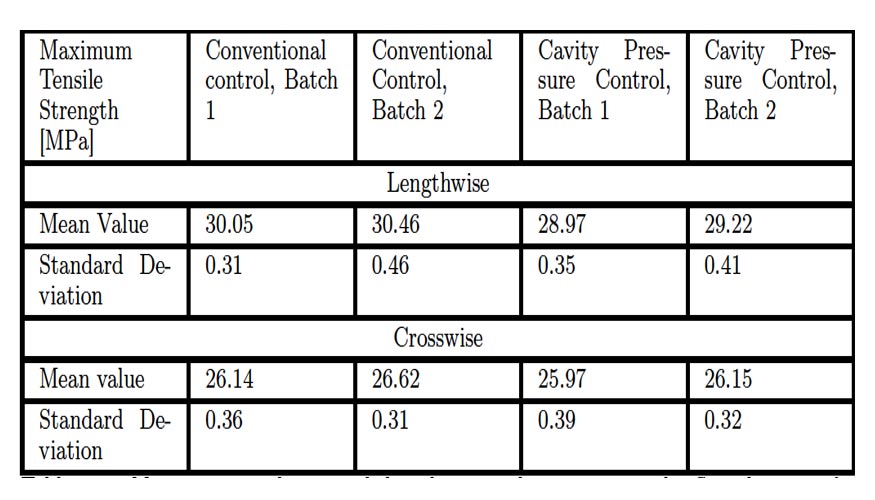
Tabla 3.2: Resistencia máxima a la tracción longitudinal y transversal a la dirección del flujo para diferentes lotes y estrategias de control.
Las varillas de tracción del lote 1 presentan una resistencia máxima a la tracción inferior a la de las varillas de tracción del lote 2, aunque la proporción de impurezas es menor. El lote 1 tiene una proporción de 5,5% de impurezas en comparación con el lote 2, cuya proporción es del 2%. Sólo la proporción de impurezas metálicas es un 0,22% superior a la del lote 2, que tiene una proporción del 0,08%. Las impurezas metálicas podrían ser más altas y, por tanto, causar mayores defectos en la pieza. Habría que comprobar esta hipótesis examinando otros lotes. No obstante, las diferencias entre los dos lotes en total son pequeñas, con una desviación en la resistencia máxima a la tracción inferior a 0,5.
Existen diferencias significativamente mayores entre las dos estrategias de control, así como en función de la colocación de la muestra de ensayo en la pieza. La resistencia máxima a la tracción es más de 3 veces mayor en la dirección de flujo que en sentido transversal a la dirección de flujo. La resistencia de la pieza es anisótropa a pesar de la ausencia de fibras en el material. Las barras de tracción transversales a la dirección de flujo se fresaron lejos del bebedero, de modo que en esta zona se ejerce menos presión de sujeción y, por lo tanto, se reduce la resistencia a la tracción. A efectos de verificación, las probetas podrían someterse a otros ensayos cerca del bebedero en sentido transversal a la dirección de flujo, a fin de cuantificar su posición
Con el control convencional del proceso se consiguen resistencias a la tracción globalmente más altas, especialmente en sentido longitudinal a la dirección de flujo, con una mayor resistencia a la tracción máxima de hasta 1,24 y, por tanto, 4,2%. Esto puede deberse a las mayores presiones en la fase de presión de mantenimiento de este método de control del proceso. En consecuencia, el material se comprime más, lo que da lugar a una mayor homogeneidad de las barras de tracción, como se describe en el análisis microscópico de la sección anterior. Este argumento se ve reforzado por el hecho de que las diferencias de resistencia son inferiores a de 0,5 a partir del bebedero.
Los resultados de los ensayos de cada uno de los puntos experimentales se examinan detalladamente para la influencia de los parámetros del proceso en la resistencia de la pieza en función del control y del lote de material. Las resistencias máximas a la tracción en sentido longitudinal a la dirección de flujo se muestran en la figura 3.7.
La estrategia de control tiene una gran influencia en la resistencia a la tracción de las piezas. A altas temperaturas del molde y del cilindro combinadas con una presión de mantenimiento baja (caso 1), así como a temperaturas bajas y una presión de mantenimiento alta (caso 2), la resistencia a la tracción es mayor con el control de la presión de cavidad que con el control convencional del proceso. La mayor resistencia en el caso 1 podría deberse a una mejor transmisión de la presión de mantenimiento causada por las temperaturas más altas. Además, la duración de la presión de mantenimiento aumenta con la trayectoria de la presión de cavidad optimizada para pvT, de modo que es posible un enfriamiento homogéneo de la pieza. A bajas temperaturas y presiones altas (caso 2), la disminución de la presión de la cavidad en la fase de presión de mantenimiento es más pronunciada con la presión de mantenimiento convencional, lo que podría dar lugar a una falta de homogeneidad en el enfriamiento de la pieza. Estos efectos parecen ser independientes del material.
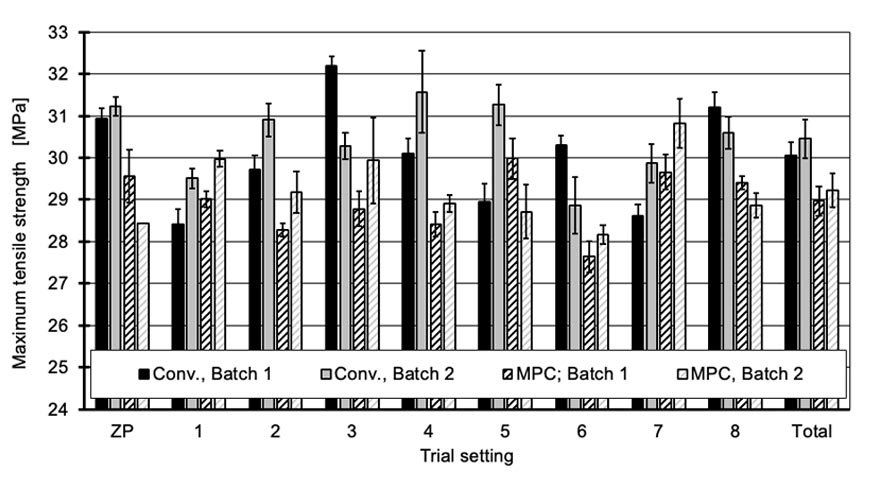
La resistencia máxima a la tracción es la más alta en el punto central con control de proceso convencional, lo que demuestra que las temperaturas de proceso estándar de los materiales. Con el control de la presión de cavidad, las resistencias a la tracción son mayores en montaje experimental 7 a bajas temperaturas y alta presión de mantenimiento.
Las desviaciones estándar de los resultados experimentales son demasiado grandes para evaluar estadísticamente la influencia de la temperatura del molde, la temperatura de la botella, el nivel de presión de mantenimiento y el volumen de dosificación. Los modelos de regresión tienen una precisión inferior al 40 %, por lo que no es posible determinar la importancia de las variables del proceso. En consecuencia, es necesario realizar más pruebas con una muestra mayor, por ejemplo, diez probetas de tracción. El moldeo por inyección de barras también ofrece una forma de reducir la variación, ya que el procesamiento mecánico de las barras de tracción durante el fresado puede tener también una gran influencia en la resistencia a la tracción.
3.6 Conclusiones y perspectivas
Este trabajo presenta un sistema de control de la presión de cavidad diseñado para aumentar la estabilidad de procesos de moldeo por inyección. El uso de PCR-PP y el cambio de las condiciones del proceso térmico en pruebas de moldeo por inyección. La investigación de diferentes lotes de PCR mostró que sólo podían detectarse pequeñas diferencias en el comportamiento pvT de los lotes, en comparación con otras imprecisiones. Las imágenes microscópicas de luz transmitida mostraron defectos en la pieza, que pueden provocar fallos mecánicos.
El procesamiento de PCR-PP puede mejorarse utilizando métodos avanzados de control del proceso de presión de cavidad. La estabilidad del proceso se evaluó valorando el peso de la pieza. Los resultados demuestran que el control de la presión de cavidad puede reducir las variaciones de lote a lote en más de un 73% en comparación con el control de proceso convencional. Las fluctuaciones térmicas pueden reducirse en más del 80%.
Las propiedades mecánicas de la pieza se evaluaron mediante ensayos de tracción. Se comprobó que la resistencia a la tracción era hasta 1,24 mayor con el control de proceso convencional. Una de las razones podría ser la menor carga de presión en la fase de inyección y mantenimiento de la presión con el control de la presión de cavidad.
Las desviaciones estándar de todos los ajustes del proceso fueron muy altas para todos los puntos experimentales, lo que impide una correlación estadística entre el ajuste del proceso y la resistencia a la tracción. Por consiguiente, es necesario un mayor tamaño de la muestra para que los resultados sean más significativos. Se necesitan más experimentos con lotes de material adicionales para evaluar la influencia de la composición del material en la resistencia a la tracción de la inyección. Se supone que un alto contenido metálico influye negativamente en la resistencia a la tracción.
3.7 Agradecimientos
Los estudios presentados en este informe sobre el desarrollo de una estrategia de control de procesos entre fases (Proyecto de investigación DFG nº HO 4776/44-1) están financiados por la Fundación Alemana de Investigación (DFG). alemana (DFG). Hacemos extensivo nuestro agradecimiento a la DFG. También queremos dar las gracias a todas a todas las empresas que han apoyado este trabajo con material plástico, maquinaria y otros equipos.
Referencias
[ASUM03] Aurrekoetxea, J.; Sarrionandia, M. A.; Urrutibeascoa, I.; Maspoch, M.: Effects of injection moulding induced morphology on the fracture behaviour of virgin and recycled polypropylene. Polymer 44 (2003) 22, S. 6959– 6964
[BB14] Bhattacharya, D.; Bepari, B.: Feasibility study of recycled polypropylene through multi response optimization of injection moulding parameters using grey relational analysis. Procedia Engineering (2014) 97, S. 186–196
[BHHM08] Brachet, P.; Høydal, L. T.; Hinrichsen, E. L.; Melum, F.: Modification of mechanical properties of recycled polypropylene from post-consumer containers. Waste Management 22 (2008) 12, S. 2456–2464
[GM16] Gießauf, J.; Maier, C.: Wie reproduzierbar ist die Reproduzierbarkeit?. Kunststoffe 106 (2016) 6, S. 62–66
[HH20] Hopmann, C.; Hornberg, K.: The Switchover Problem and its Consequences: Phaseless Process Control Should Revolutionize the Switchover Process. Kunststoffe International 110 (2020) 2, S. 40–44
[HHV+21] Hornberg, K.; Hopmann, C.; Vukovic, M.; Stemmler, S.; Abel, D.: Auswirkungen zyklischer Prozesseinflu¨sse auf den Werkzeuginnendruckverlauf und die Bauteilqualität im Spritzgießprozess. Zeitschrift Kunststofftechnik/ Journal of Plastics Technology 17 (2021) 3, S. 179–203
[HRR+16] Hopmann, C.; Ressmann, A.; Reiter, M.; Stemmler, S.; Abel, D.: A Self-optimising Injection Moulding Process with Model-Based Control System Parameterisation. International journal of computer integrated manufacturing 29 (2016) 11, S. 1190–1199
[HRRZ13] Hopmann, C.; Ressmann, A.; Reiter, M. C.; Zöller, D.: Strategy for Robust System Identification for Model Predictive Control of Cavity Pressure in an Injection Moulding Process. In: Schmitt, R.; Bosse, H. (Hrsg.): ISMTII 2013. Aachen: Apprimus-Verl., 2013
[KVW+10] Kazmer, D. O.; Velusamy, S.; Westerdale, S.; Johnston, S.; Gao, R. X.: A comparison of seven filling to packing switchover methods for injection molding. Polymer Engineering & Science 50 (2010) 10, S. 2031–2043
[LSH20] Lindner, C.; Schmitt, J.; Hein, J.:. Stoffstrombild Kunststoffe in Deutschland2020
[MDK+20] Moritzer, E.; Deuse, J.; Kroll, A.; Richter, R.; Hopp, M.; Schmitt, J.; Schulte, L.; Schrodt, A.; Wittke, M.: Einsatz von maschinellem Lernen fu¨r die Rezyklat-Verarbeitung. In: Institut fu¨r wissenschaftliche Veröffentlichungen (Hrsg.): Jahresmagazin Kunststofftechnik 2020., 2020
[MK11] Mehat, N. M.; Kamaruddin, S.: Investigating the Effects of Injection Molding Parameters on the Mechanical Properties of Recycled Plastic Parts Using the Taguchi Method. Materials and Manufacturing Processes (2011) 26,
[MOY08] Meran, C.; Ozturk, O.; Yuksel, M.: Examination of the possibility of recycling and utilizing recycled polyethylene and polypropylene. Materials &
Design 29 (2008) 3, S. 701–705
[NN14] N.N.:. DIN ISO/TR 17098: Stoffliche Verwertung von Verpackungsmaterialien – Bericht u¨ber Substanzen und Materialien, die die stoffliche Verwertung behindern können2014
[NN17] N.N.: DE 10 2015 117 237 B3: Verfahren zur Bestimmung eines realen Volumens einer spritzgießfähigen Masse in einem Spritzgießprozess: Patentschrift., 33 31st International Colloquium Plastics Technology 2022 · Session 1
[NN19] N.N.:. DIN EN ISO 2818: Herstellung von Probekörpern durch mechanische Bearbeitung2019
[PH07] Premphet, K.; Horanont, P.: Improving performance of Polypropylene through combined use of aalcium carbonate and metallocene-produced impact modifier. Polymer-Plastics Technology and Engineering 40 (2007) 3, S. 235– 247
[RAK17] Rudolph, N. S.; Aumanate, C.; Kiesel, R.: Understanding plastics recycling: Economic, ecological, and technical aspects of plastic waste handling. Cincinnati and Munich: Hanser Publishers and Hanser Publications, 2017
[RSH+14] Reiter, M.; Stemmler, S.; Hopmann, C.; Ressmann, A.; Abel, D.: Model Predictive Control of Cavity Pressure in an Injection Moulding Process. IFAC Proceedings Volumes 47 (2014) 3, S. 4358–4363
[SAV+19] Stemmler, S.; Ay, M.; Vukovic, M.; Abel, D.; Heinisch, J.; Hopmann, C.: Cross-phase Model-based Predictive Cavity Pressure Control in Injection Molding. 2019 IEEE Conference on Control Technology and Applications (CCTA). 2019
[Sch11] Schreiber, A.:. Regelung des Spritzgießprozesses auf Basis von Prozessgrößen und im Werkzeug ermittelter Materialdaten. 2011
[Sch19] Schötz, A.: Abmusterung von Spritzgießwerkzeugen: Strukturierte und analytische Vorgehensweise. Mu¨nchen and © 2019: Hanser3., aktualisierte und erweiterte auflage edition, 2019
[ST17] Schiffers, R.; Topic, N.: More Stability Increases Attractiveness: Optimized Process Control for Injection Molding of Thermoset Molding Compounds. Kunststoffe International 107 (2017) 8, S. 26–29
[Ste07] Steinko, W.: Optimierung von Spritzgießprozessen. Mu¨nchen, Wien: Carl Hanser Verlag, 2007
[Ste19] Stemmler, S.: Intelligente Regelungsstrategien als Schlu¨sseltechnologie selbstoptimierender Fertigungssysteme. RWTH Aachen, Dissertation, 2019
[vCA+21] van Thoden Velzen, E. U.; Chu, S.; Alvarado Chacon, F.; Brouwer, M. T.; Molenveld, K.: The impact of impurities on the mechanical properties of recycled polyethylene. Packaging Technology and Science 34 (2021) 4,
S. 219–228
[WHSH19] Wang, J.; Hopmann, C.; Schmitz, M.; Hohlweck, T.: Influence of measurement processes on pressure-specific volume-temperature relationships of semi-crystalline polymer: Polypropylene. Polymer Testing 78 (2019), S. 105992
Publicación secundaria de la ponencia presentada en el 31°Coloquio Internacional de Tecnología de los Plásticos, Instituto de Procesamiento de Plásticos (IKV) en la Industria y la Artesanía de la Universidad RWTH-Aachen, 7-8 de septiembre de 2022, Aquisgrán, Alemania)