Mold-Masters E-Multi ofrece al inyectoador la capacidad de maximizar la productividad
La empresa EasyPlast fabrica moldes y moldeando plásticos desde 1994. Está especializada en moldes multicavidades para productos de consumo y en el moldeo de piezas en PP, LDPE, HDPE y LLDPE. Los componentes disponibles incluyen tapones, cápsulas, dispensadores, casquillos, productos médicos, artículos para el hogar y envases, entre otros. La empresa fabrica más de mil millones de artículos moldeados cada año.
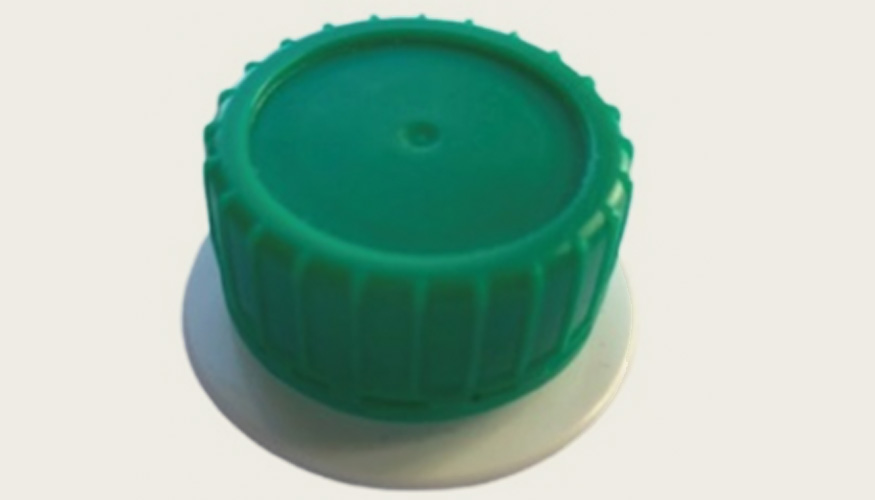
Aplicación
EasyPlast producía un complejo cierre estilo (tapa de rosca de 3 componentes de HDPE, 2 -color). El proceso actual implicaba moldear cada componente en 3 celdas separadas con 3 moldes distintos. Este diseño específico de cierre incorpora un elemento de corte que abre el sello de aluminio una vez que el consumidor abre el cierre.
Como parte de este proceso, desde el/los molde(es) se extraen mediante un robot a una plantilla de ensamblaje donde los tapones son finalmente expulsados completamente ensamblados.
Reto
EasyPlast esperaba mejorar el proceso de fabricación para mejorar la productividad y la eficiencia general para reducir el coste de las piezas:
- minimizar la utilización del equipo y la mano de obra
- mejorar la calidad de las piezas
- reducir el tiempo de ciclo (y la manipulación)
- ahorrar espacio en el suelo
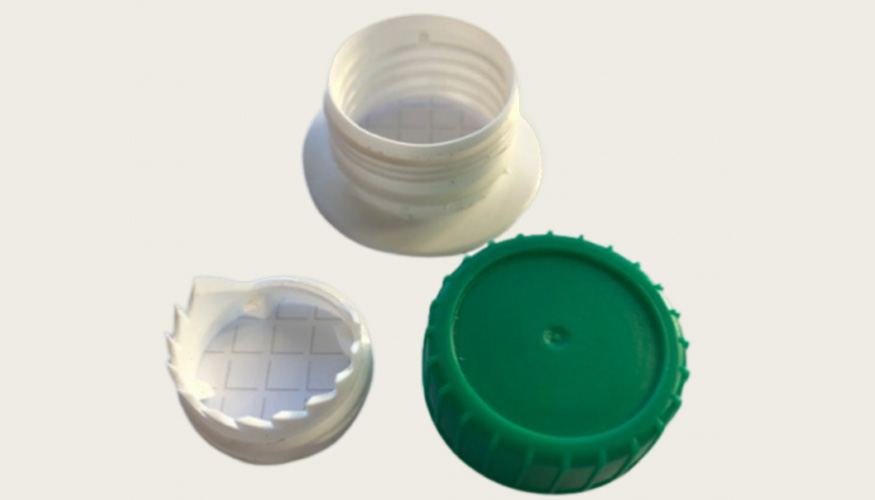
Solución técnica
EasyPlast había desarrollado un molde único de la familia 24+24+24 y finalmente patentó la tecnología. Como componente de esta solución se utilizó una unidad de inyección auxiliar E-Multi (EM4) y un controlador para inyectar el componente con el segundo color.
La unidad E-multi se montó en una configuración horizontal casi paralela a la prensa (ángulo de 15°) utilizando un soporte de suelo. La unidad E-Multi fue seleccionada por su capacidad de inyección de precisión, repetibilidad, fiabilidad y capacidad de disparo.
Resultados
El cliente estima que el tiempo para completar el proceso de inyección y montaje se ha reducido en aproximadamente un 50% como resultado de este nuevo sistema. La contracción se produce en las tres piezas de manera uniforme después del montaje, lo que da lugar a tolerancias extremadamente altas y a una excelente calidad de las piezas. Como resultado de la minimización de los requisitos de manipulación después del moldeo, la tasa de desechos se ha reducido hasta en un 75% (era del 2%, ahora es del 0,5-1%).
En general, el cliente informa de que este nuevo proceso le ha permitido reducir los costes de las piezas en aproximadamente un 40% y prevé un ahorro anual de al menos 100.000 euros. El cliente atribuye este ahorro al proceso más eficiente (posibilitado por la E-Multi y el diseño especial del molde) que requiere 1 persona menos, 2 máquinas de inyección menos, menos equipo de refrigeración, menores tiempos de producción, menores tiempos de montaje, menor tasa de desechos y menor consumo de energía.
Además, EasyPlast espera poder mejorar aún más los tiempos de ciclo, ya que la E-Multi de Mould-Masters no se ha utilizado hasta su límite de rendimiento (no es el cuello de botella en el proceso de producción). El cliente está muy contento con la unidad. Funciona muy bien y está previsto encargar otra para un futuro proyecto similar. El controlador también es muy apreciado por su interfaz, su facilidad de uso y su instalación.