Saint-Gobain apuesta por la impresión 3D en su línea de producción para automoción
La multinacional francesa Saint-Gobain, dedicada a la fabricación de vidrios para múltiples sectores industriales, ha encontrado en la tecnología de impresión 3D, desarrollada por la multinacional barcelonesa BCN3D, el aliado perfecto para aumentar la eficiencia de sus procesos de fabricación. Sus impresoras 3D y distintas soluciones tecnológicas innovadoras permiten ahora a los ingenieros de Saint-Gobain en su planta de L’Arboç (Barcelona) mejorar de forma significativa la eficiencia en los procesos de fabricación de piezas y componentes para sus clientes del sector del automóvil creando utillajes y herramientas impresas en 3D mejorando la eficiencia de su línea de producción de lunas.
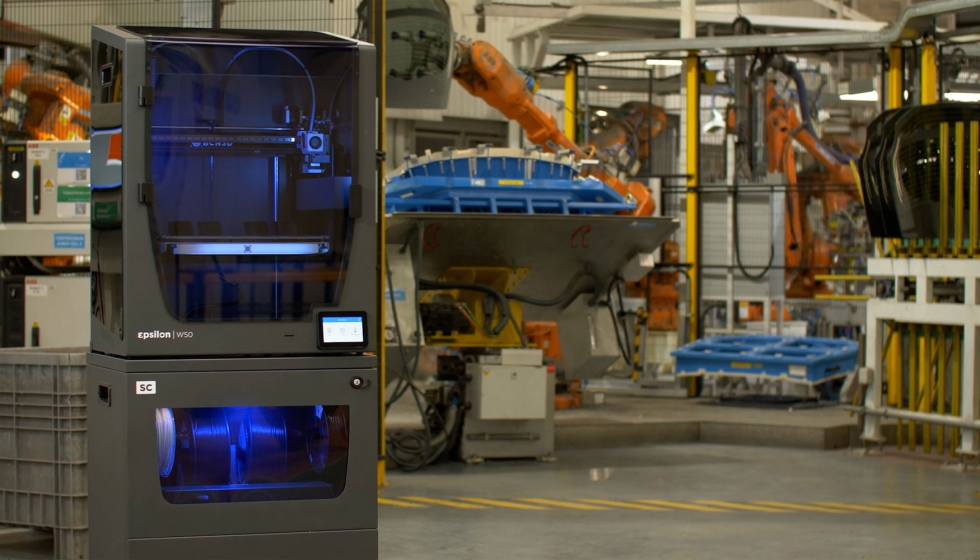
Desde 2019, la unidad de negocio Sekurit de Saint-Gobain en la planta de L’Arboç —donde producen al año 19 millones de distintos equipos de acristalamiento para automoción (backlites y sidelites)— ha incorporado la tecnología de impresión 3D tras externalizar durante años la fabricación de utillajes que confiaba a procesos mecanizados con costes mucho más elevados comparados con la impresión 3D.
La incorporación de esta tecnología de fabricación aditiva le ha permitido desde entonces a la planta española de Saint-Gobain ahorrar alrededor de 170.000 euros y reducir sus plazos de fabricación de utillajes y otras herramientas en un 93%. Las piezas impresas en 3D adoptan la forma de herramientas, plantillas y accesorios hasta el control de calidad.
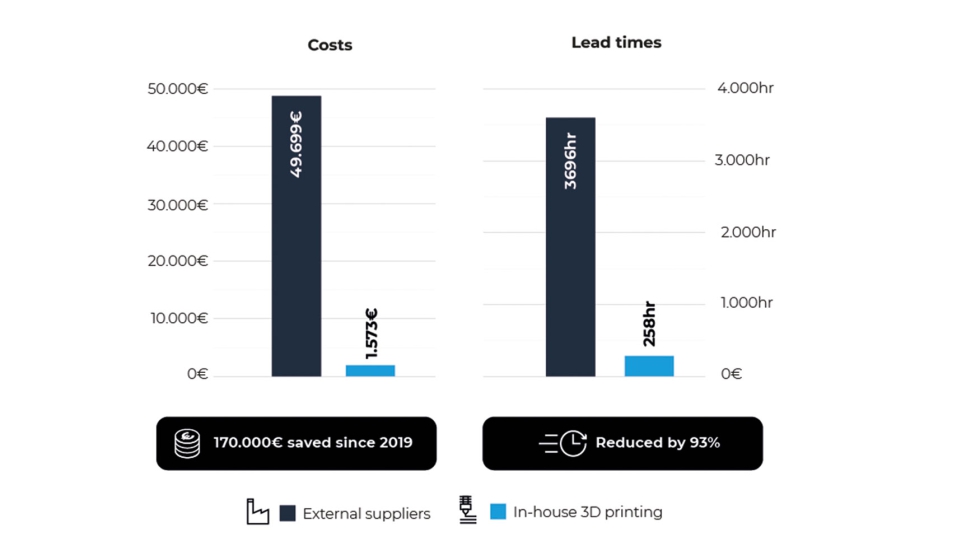
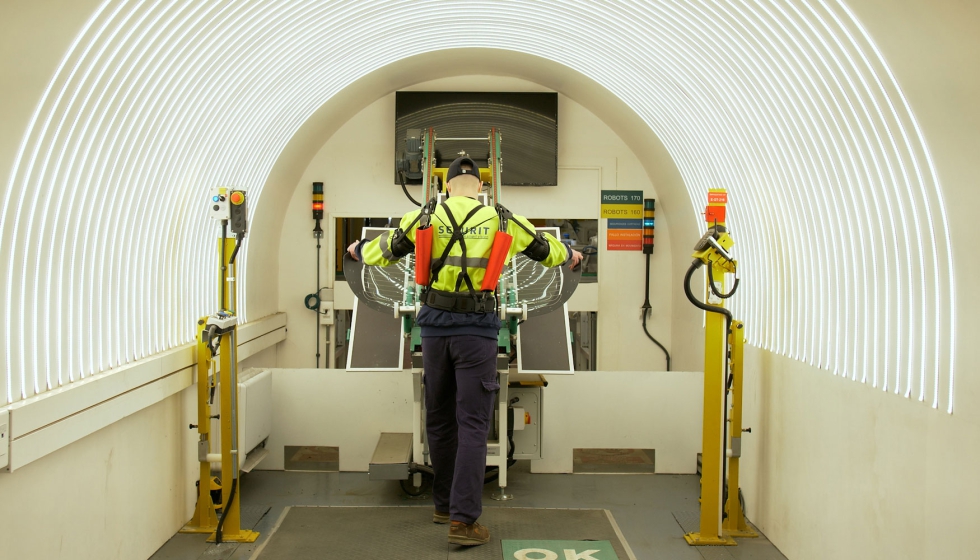
La impresión 3D revoluciona la producción en Saint Gobain
La planta barcelonesa de Saint-Gobain ha incorporado en su taller la tecnología de impresión 3D con varias impresoras de la serie Epsilon W50 de BCN3D que incluye la tecnología Idex de doble extrusión y Smart Cabinets, con lo que la multinacional ha mejorado considerablemente los procesos creativos de sus ingenieros y les resulta más sencillo desarrollar nuevas ideas, crear de forma cómoda y sencilla nuevos prototipos en un período más corto de tiempo respecto de otras tecnologías mecanizadas y realizar pruebas y piezas de uso final en cuestión de días, todo ello manteniendo la máxima calidad del acabado final.
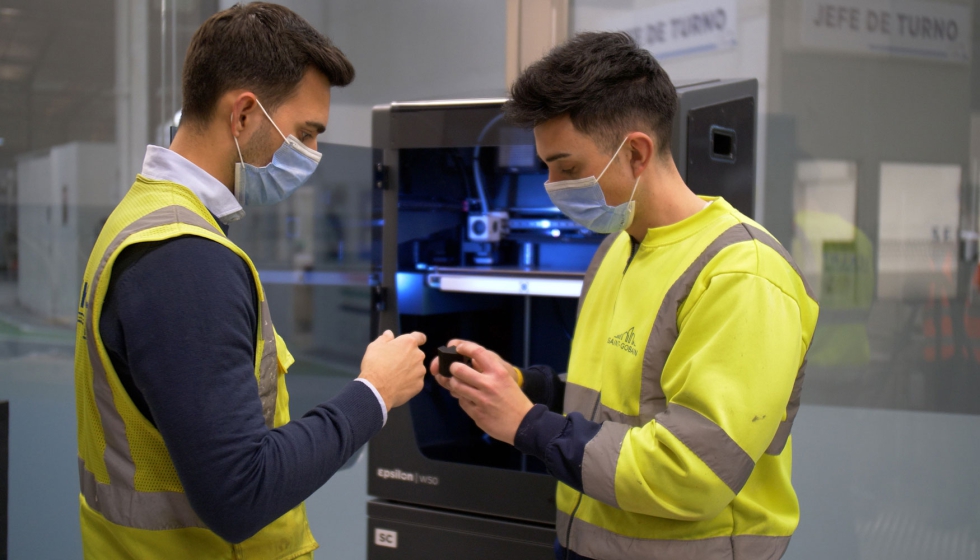
Fabricación aditiva integrada en la automatización
A continuación, el acristalamiento se recoge y se introduce en un horno para crear las curvas. Recién salido del horno, se comprueban las dimensiones y la calidad del acristalamiento, primero mediante una cámara, y luego se clasifican en aprobados o pendientes para su comprobación manual.