La empresa de transformación de silicona Sei Woo se asocia con Engel para ampliar sus capacidades de microinyección
Tecnología LSR para el futuro
Durante los trayectos largos en coche, la función de masaje en el asiento del vehículo ayuda a eliminar tensiones. Esta prestación de confort es posible gracias a la presencia, en el respaldo y la superficie de asiento, de unas cámaras de aire que se llenan y se vacían rápida y alternativamente mediante válvulas SMA. La empresa Sei Woo Hi-Tech Polymer de Holzhausen, Alta Austria, produce estas diminutas válvulas de entrada con juntas de silicona integradas y utiliza para ello máquinas de moldeo por inyección Engel. Realizando proyectos de desarrollo difíciles, la empresa procesadora de silicona ha ascendido a la primera división del micromoldeo por inyección.
Los complejos elementos multicomponente miden solamente cuatro milímetros de anchura y 3 mm de altura. La junta de silicona, con un peso de inyección de 0,02 gramos, está en el extremo superior de la carcasa de la válvula, que está hecha de termoplástico. Dicha carcasa contiene un fino alambre metálico con memoria que es fundamental para el funcionamiento de la válvula. SMA es la sigla en inglés de Shape Memory Alloy (aleación con memoria de forma). Cuando está sometido a corriente, el alambre se calienta y se contrae, haciendo que la válvula SMA se accione. Si el flujo de corriente se interrumpe, el alambre se enfría en fracciones de segundo y la válvula se cierra. De este modo se controla el llenado de las cámaras de aire y, con ello, la presión de masaje.
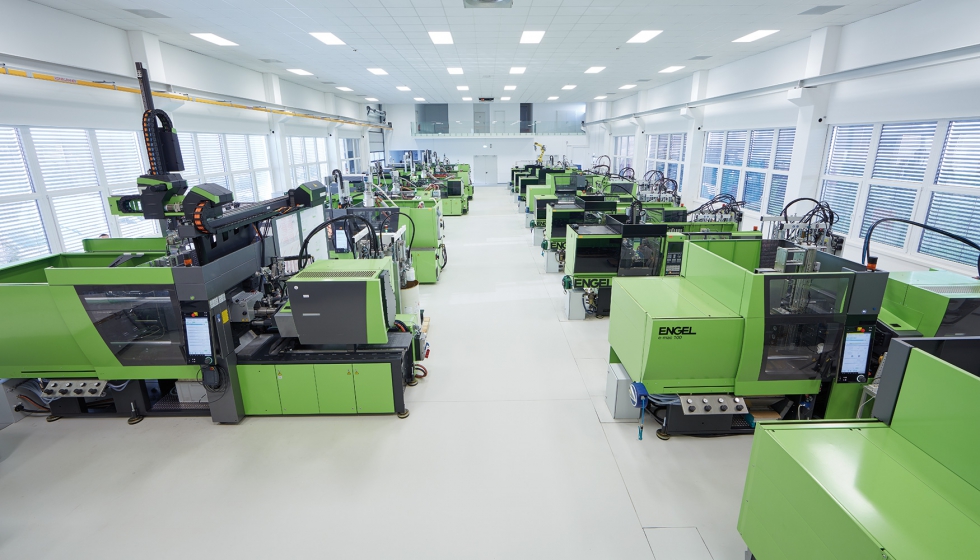
Sei Woo Austria decidió apostar desde un principio por Engel debido a la experiencia y capacidad de innovación de esta empresa en el ámbito de la silicona líquida. En la planta de Holzhausen se utilizan 17 máquinas de moldeo por inyección de las series victory, e-victory y e-mac. (Imagen: Sei Woo).
Los dos materiales polímeros se combinan en un solo paso mediante una máquina de moldeo por inyección Engel e-victory 140. En un molde de plato giratorio de 16+16 cavidades se inyectan primero las carcasas de poliamida (PA). En la segunda posición del plato giratorio, se inyecta directamente silicona líquida (LSR) mientras, al mismo tiempo, se producen otros 16 cuerpos base de carcasa. La PA y la LSR dan lugar a un enlace químico. Sin embargo, por motivos de seguridad, y dado que la superficie de contacto es muy pequeña, inmediatamente después del moldeo por inyección las piezas terminadas se recuecen a 200 °C. Con ello, el termoplástico y la silicona quedan permanentemente unidos. A continuación, las piezas pasan por un control de calidad 100 por cien basado en cámaras y luego se transfieren de inmediato al departamento de logística para su envío al cliente, “que es un líder del mercado mundial en sistemas de masaje para asientos de vehículo”, explica Peter Lehmann, director general de Sei Woo Hi-Tech Polymer GmbH. Hasta la fecha, Sei Woo ha entregado más de 200 millones de estos componentes.
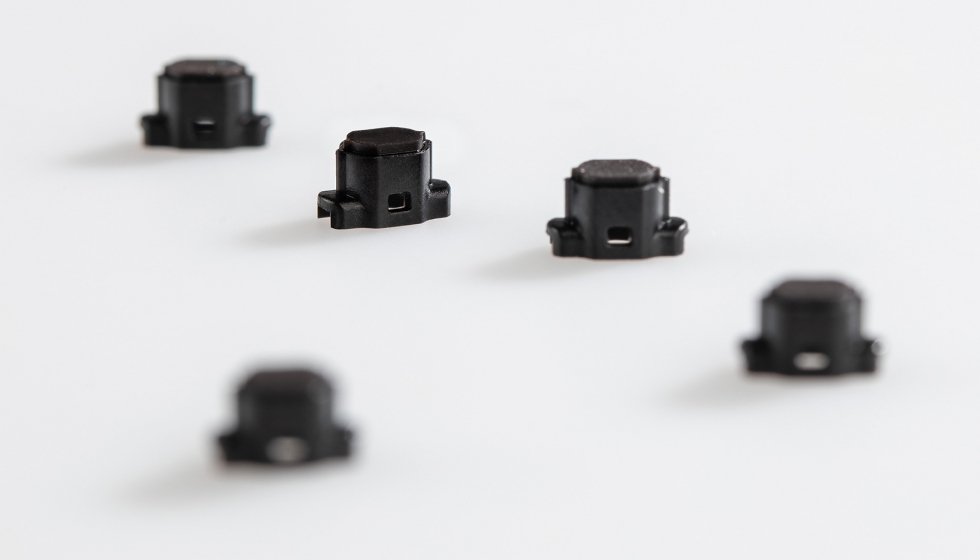
La válvula de admisión de aire se produce con poliamida y silicona líquida mediante una única operación de moldeo por inyección. La carcasa de poliamida envuelve un alambre metálico mediante el cual se controla la posición de la válvula. Este elemento funcional tiene tan solo 4 mm de anchura y 3 mm de altura. (Imagen: Sei Woo).
Desperdicios reducidos a cero
“El moldeo por inyección multicomponente reduce el riesgo de error, que sería inmenso si las micropiezas se montaran individualmente”, explica Lehmann y subraya: “La estrategia de cero errores es un pilar de nuestro éxito”. A menudo, Sei Woo colabora estrechamente con el cliente desde la fase misma de desarrollo y optimización del producto. Las válvulas de admisión utilizadas en el sistema de masaje para asientos son el mejor ejemplo de ello. “Inicialmente, este producto lo elaboraba otra empresa, pero el número de piezas rechazadas era alto”, dice Lehmann. “Nosotros hemos modificado su concepción y su diseño, logrando así reducir a cero el número de piezas rechazadas durante el proceso”. Gracias a su gran pericia en desarrollo, su decidida atención a las necesidades del cliente y su alta flexibilidad, Sei Woo se ha ganado la confianza de los grandes actores del mercado en el sector de la LSR.
La fundación de Sei Woo en Austria en el año 2000 demuestra que el Grupo Sei Woo, con sede en Singapur, percibe un gran potencial en la silicona líquida y tiene visión de futuro. Hace muchos años que la LSR va aumentando su participación en el mercado gracias a su extraordinaria estabilidad y biocompatibilidad y a la posibilidad de ser procesada con eficiencia. Especializándose en microtecnología y en aplicaciones multicomponente, Sei Woo está aprovechando la oportunidad de ocupar un nuevo nicho. Entre las piezas más pequeñas que Sei Woo ha producido hasta la fecha, están los anillos de obturación para cables de carga de teléfonos móviles, un producto que pesa unas pocas milésimas de gramo. “Con este producto nos hemos adentrado en un ámbito en el que se anula el efecto de la gravitación”, comenta Lehmann. “La manipulación de micropiezas es un desafío”.
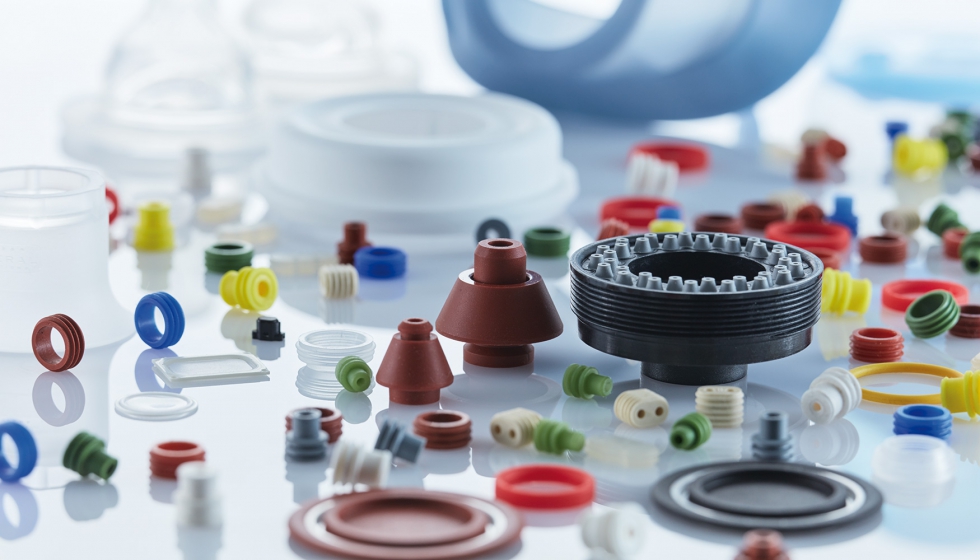
Sei Woo Hi-Tech Polymer produce una amplia gama de piezas para sectores como la industria de la automoción, la aeronáutica, la electrónica y las ciencias biológicas. Las micropiezas y las piezas multicomponente representan una parte cada vez mayor de su gama de productos. (Imagen: Sei Woo).
Calidad constante con costos unitarios competitivos
Son sobre todo las aplicaciones nuevas las que impulsan la tendencia hacia componentes con dimensiones cada vez más pequeñas en sectores como la electrónica para automóviles, las radiocomunicaciones móviles, la tecnología de altavoces y la medicina. Al disminuir las dimensiones de los componentes, aumentan continuamente los requisitos que debe cumplir el proceso de moldeo por inyección. “Solamente puedo ofrecer a nuestros clientes aquello que la máquina de moldeo por inyección y el molde me permiten extraer”, aclara Lehmann. Procesos de producción estables, máxima reproducibilidad y precisión son los requisitos que, en el caso de las válvulas de admisión de aire, cumple óptimamente una máquina de moldeo por inyección Engel e-victory. Con su unidad de inyección eléctrica, combinada con una unidad de cierre sin columnas servohidráulica, este tipo de máquina combina una altísima precisión con una extraordinaria rentabilidad. Esto se nota sobre todo en las aplicaciones multicompo-nente. En la unidad de cierre sin columnas, las platinas de montaje del molde se pueden aprovechar hasta el borde e incluso los moldes grandes y voluminosos, con una mesa giratoria, caben en una máquina de moldeo por inyección comparativamente pequeña.
En las naves de producción ultramodernas que Sei Woo tiene en Holzhausen, hay un total de 17 máquinas de moldeo por inyección, entre ellas seis máquinas multicomponente. Todas ellas provienen de Engel, que está en Schwertberg, a solo 50 kilómetros de distancia. El equipamiento incluye, además de máquinas híbridas e-victory —que se usan para producir las válvulas de admisión de aire—, las máquinas hidráulicas victory y las totalmente eléctricas e-mac, en las que Sei Woo ha invertido para proyectos de tecnología médica. Un ejemplo actual de este tipo de proyectos son las juntas de paso de cables para marcapasos.
Todas las máquinas trabajan de forma totalmente automatizada. “Sin automatización, en Europa no tendríamos ni una oportunidad”, precisa Lehmann. “No ofrezco a nuestros clientes piezas de muestra hasta estar seguro de que podemos producirlas de forma automatizada”.
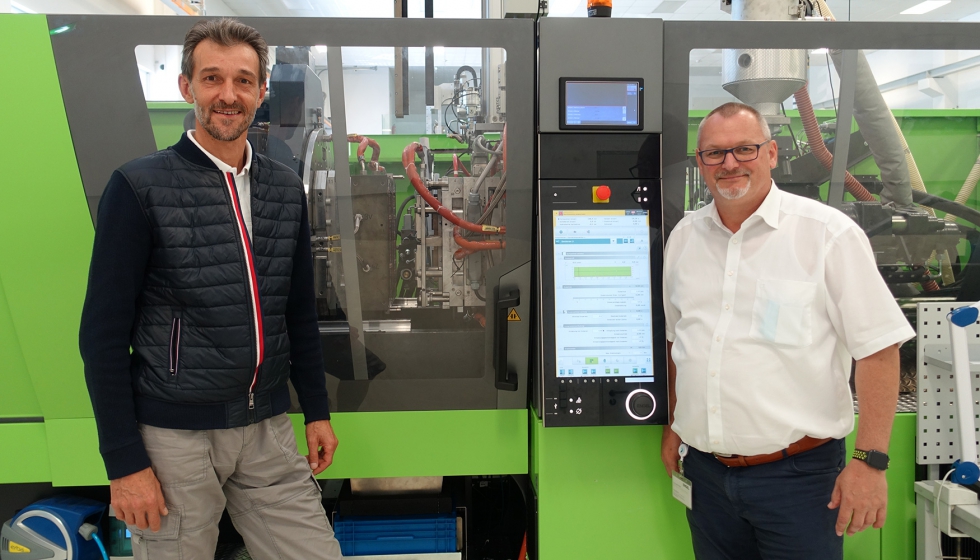
Socios desde hace más de 20 años: Peter Lehmann de Sei Woo (izquierda) y Leopold Praher de Engel. (Imagen: Engel).
Experiencia y capacidad de innovación como factores decisivos
Muchos años de experiencia con LSR y gran capacidad de innovación en este ámbito: estos fueron para Peter Lehmann los factores que decidieron, desde el principio, su apuesta por Engel. “Mi anterior trabajo ya me permitió reunir alguna experiencia con Engel, firma representada por Roegele, y sé que es una empresa líder en tecnología. Esto nos da mucha seguridad y nos otorga la necesaria ventaja competitiva”.
Así, Sei Woo es una de las primeras empresas en aplicar la nueva unidad de microinyección de LSR que Engel presentó en otoño de 2020. Esta unidad ha debutado en el mercado produciendo componentes de precisión para oftalmología con un peso por pieza de 0,0013 gramos. “Con ello hemos marcado nuevas pautas”, afirma Leopold Praher, director de ventas de Elast/LIM de Engel. La alta flexibilidad fue un aspecto central a la hora de desarrollar la unidad de microinyección. Gracias a su sistema de acoplamiento rápido, la unidad puede ser sustituida en menos de 30 minutos por una unidad de inyección de husillo convencional. “Nuestros clientes pueden aprovechar óptimamente el tiempo productivo de la máquina de moldeo por inyección”, explica Praher.
En el desarrollo de la unidad de microinyección de LSR ha colaborado ACH Solution. Esta empresa especializada en silicona y procesos multicomponente también tiene su sede en Alta Austria y es el socio más importante de Sei Woo para la fabricación de moldes.
La cercanía espacial entre las tres empresas asociadas no es casual. El cluster industrial “Alta Austria“ concentra varias compañías importantes para el sector mundial de la silicona.”La cercanía de nuestros proveedores nos beneficia mucho. Cuando se necesitan servicios postventa o refacciones, todo se resuelve con una rapidez enorme”, añade Peter Lehmann. “También eso refuerza nuestra posición competitiva”.
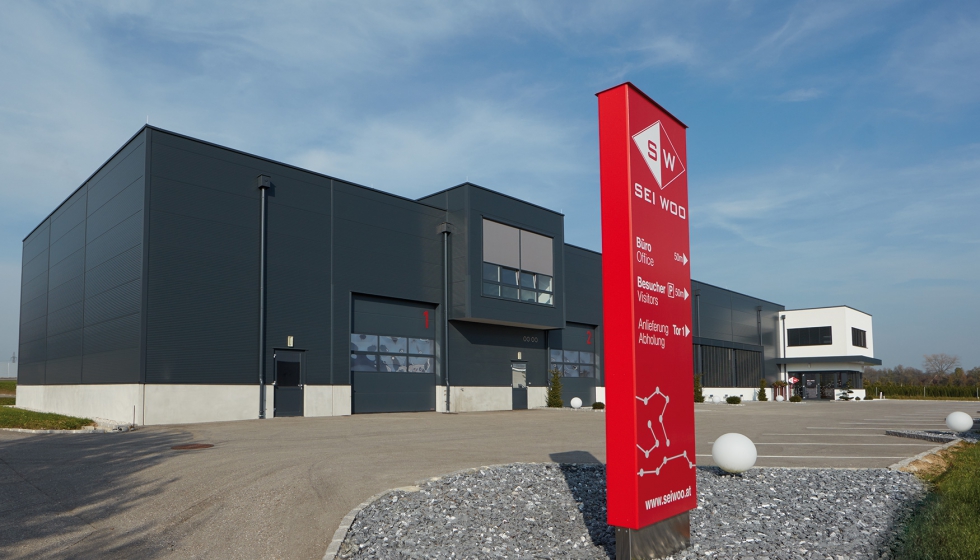
Sei Woo Austria tiene su sede en Holzhausen, una plantilla de 25 empleados y una facturación anual que en la actualidad alcanza casi 5 millones de euros. (Imagen: Sei Woo).