Inyección de termoplásticos, ¿arte o ciencia? Parte 2 de 2
Me preguntan en muchas ocasiones en mis seminarios, si este porcentaje de llenado en el momento de la conmutación o paso a la fase de compactación (95% al 98%) debe aplicarse sobre el peso o sobre el volumen de la pieza e incluso si es un porcentaje aplicado sobre el porcentaje de la dosis utilizada. Veamos algunos ejemplos.
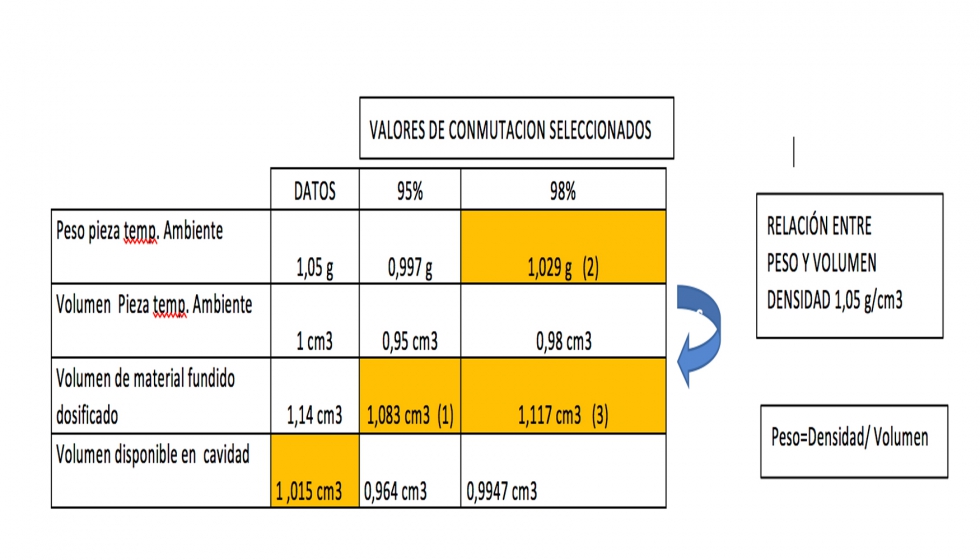
- Si nuestra cavidad dispone de 1,015 cm3 de volumen disponible para llenar, en estos tres casos marcados en color naranja, estamos sobre llenando el molde y generando rebabas o tensiones si seleccionamos los valores en naranja para conmutar. Parece pues que la forma mas exacta de aplicar el porcentaje de llenado en el punto de conmutación es sobre el volumen de la cavidad que vamos a llenar. También indicar que para seleccionar el porcentaje ideal a aplicar en el punto de conmutación hay que tener en muy en cuenta el espesor de las piezas que estamos inyectando.
- Como puede verse en la tabla 3, la relación entre los valores de peso de la pieza y el volumen de la pieza a temperatura ambiente es la densidad. Por lo tanto, los valores de conmutación son iguales si se realizan por peso de la pieza a temperatura ambiente o por volumen de la pieza a temperatura ambiente.
Este sería nuestro punto de conmutación, o punto de cambio de la fase de llenado de la cavidad a la fase de compactación.
Este punto de conmutación es vital en el proceso. Debe ser repetitivo y constante durante las series de producción. Para fijar este punto debemos controlar: tiempo de llenado, cota de conmutación, presión necesaria de llenado y también, como insisto en mis seminarios, el peso de las piezas en el punto de conmutación.
Respecto al punto de conmutación y su necesaria repetibilidad es recomendable, si estamos trabajando con altas velocidades, reducir un poco la velocidad en la etapa de llenado en la que alcanzamos este punto de cambio. Esta bajada de velocidad es interesante para la repetibilidad del proceso, en relación con esta bajada de velocidad. Para explicar esto, expongo una alegoría:
La alegoría de esta bajada de velocidad es como cuando aparcamos un coche en una plaza de un parking. Nadie llega a toda velocidad y clava las ruedas antes de llegar. Si hacemos esto probablemente tendremos un serio golpe. Lo que hacemos es ir despacio a medida que nos acercamos a la “park position” e intentamos asegurar con cuidado esta posición.
Hay quien, en casa, se coloca neumáticos, gomas, etc. para amortiguar el posible impacto que puede producirse. También hay quien coloca una pelota colgando del techo para asegurar que siempre dejará el coche en la posición de contacto de la pelota con el parabrisas.
Esta es nuestra posición de punto de conmutación. Intentaremos que siempre sea la misma y que la máquina pueda reproducirla con exactitud. Por ello se recomienda una bajada de velocidad al acercarnos al punto de conmutación, tal como haríamos en la 'park position' de nuestro parking.
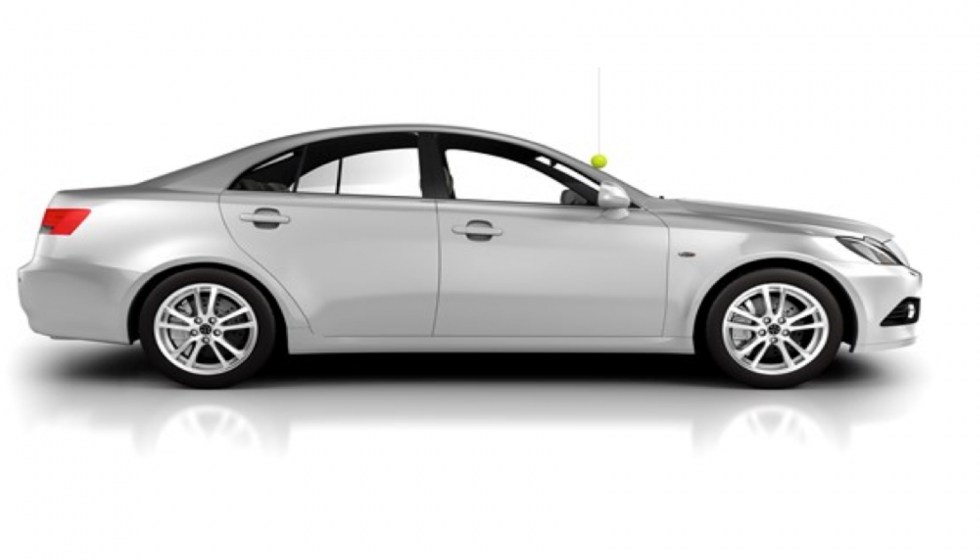
Automóvil.
Una vez definido el punto de conmutación donde hemos inyectado el 95-98% del volumen de la cavidad, pasamos a la fase de compactación. En esta fase. lo primero que sucede es que seguimos introduciendo plástico fundido (hasta ahora habíamos llenado el 95-98% del volumen disponible en la cavidad).
A medida que se va produciendo el enfriamiento del material introducido en la cavidad se va produciendo la contracción del material y por tanto, hay una pérdida de volumen que queda disponible para compensar en esta etapa.
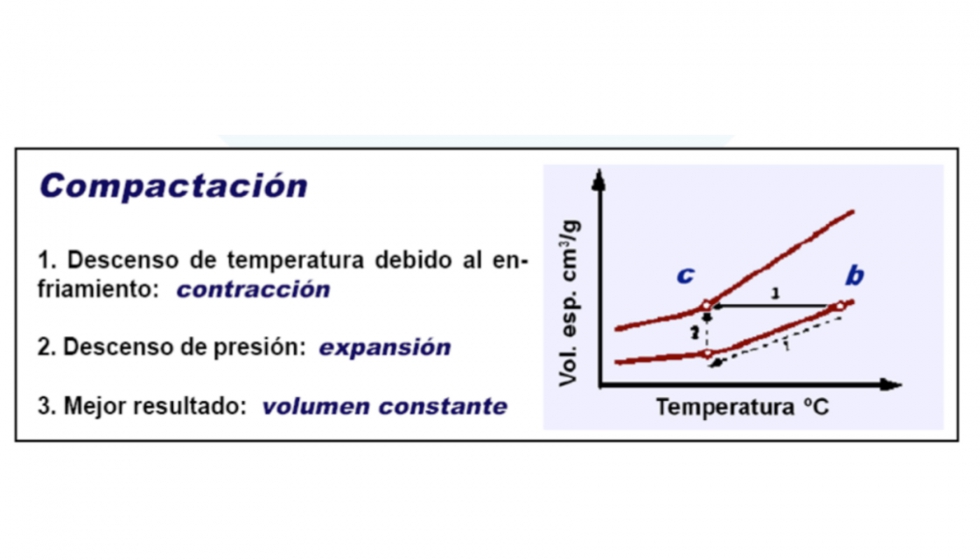
En nuestro ejemplo, hemos dosificado 1,14 cm3 y nuestra cavidad tiene un volumen disponible de 1.015 cm3.
Nuestro punto de conmutación teórico sería el 95-98% de este volumen disponible, es decir, entre 0,96 cm 3 y 0,99 cm3, ver tabla 3.
El resto de volumen dosificado para esta cavidad (1,14 cm3) debemos hacerlo entrar duranta la fase de compactación. Esta la podemos subdividir en 3 subfases:
- Llenado y compensación de la pérdida volumétrica que se producirá durante el enfriamiento
- Presurización de la cavidad para representar las medidas, acabados superficiales, etc. del molde
- Permanencia de la presión para asegurar el sellado de la entrada
Atención a esta última subfase. Lo último que queremos es que después de llenar y presurizar la cavidad con unos cuantos cientos de bares, dejemos de presurizar con la entrada aun abierta. Con ello se producirá un 'back flow' y despresurización de la cavidad, lo cual es absolutamente no recomendable, especialmente en materiales semicristalinos.
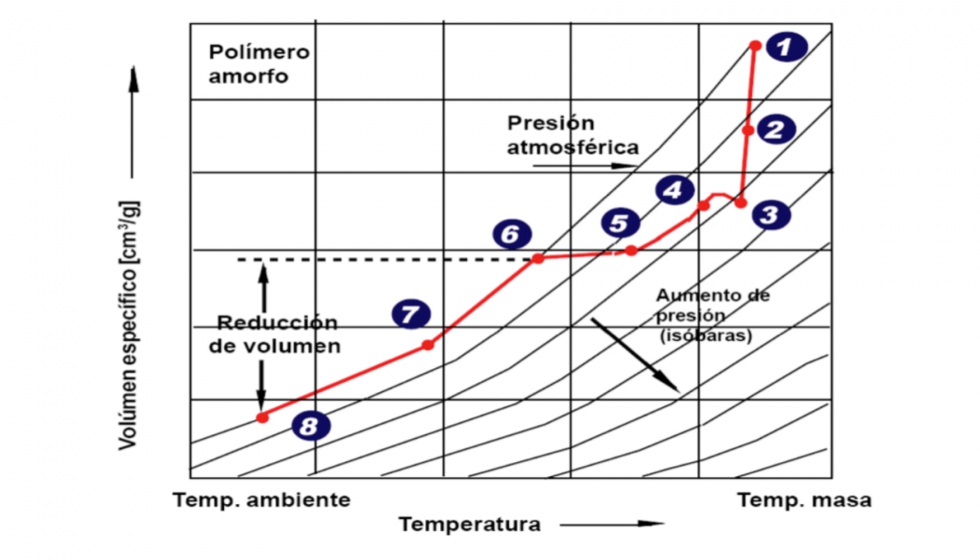
Si hacemos entrar en nuestra cavidad de 1,015 cm3, los 1,14 cm3 necesarios de plástico fundido, tendremos muchas posibilidades de que la pieza obtenida, finalmente después de enfriarse tenga unas dimensiones de 10 mmx10 mmx10 mm y pese 1,05 gramos que es lo que pretendíamos.
José Ramón Lerma es autor de los libros: 'Libro Manual Avanzado de Inyección de Termoplástico', que tiene como objetivo ser, por un lado, una herramienta para la formación y, por otro, un manual de ayuda para todo el personal de una empresa de inyección de plásticos y, del recientemente editado, 'Scientific Injection Molding Tools. Productividad a través del dominio del proceso'. Ambas publicaciones, comercializadas por Plásticos Universales / Interempresas (libros@interempresas.net), consta de detallados casos prácticos, amplia información de moldeo científico y un ‘pendrive’ con 20 hojas de cálculo y herramientas de SC Molding o Scientific Injection Molding, además de optimización y definición de proceso, lo que lo hacen único en el mercado. Página web sobre Scientific Injection Molding: www.asimm.es