Conceptos que hacen mas fácil la vida en la planta de inyección
Inyección de termoplásticos, ¿arte o ciencia? Parte 1 de 2
La inyección de plástico es el sistema más efectivo en términos de costes para fabricar piezas de plástico. Algunos dicen que es un arte, otros que es una ciencia. En este proceso se combinan ambas, pero también algo de química e ingeniería además de altos niveles de tecnología, tanto en moldes como en máquinas, periféricos y por supuesto, también en materiales. En este proceso, a pesar del alto nivel de la tecnología, no basta con pulsar un botón en la máquina y obtener piezas correctas. Este proceso requiere conocimientos profundos de materiales plásticos, moldes, periféricos y proceso, porque no se trata tan solo de hacer entrar un plástico fundido rápidamente dentro de un molde, esperar que se enfríe para poder extraerlo y ¡voilà¡! Ya tenemos piezas.
Entendiendo la relación entre volumen específico, densidad, temperaturas, compactación, cavidad de molde y pieza.
Experimento
Si tenemos una pieza obtenida de un molde, de un cubo perfecto de 1 cm3, es decir, sus dimensiones son de 10 mm por 10 mm x 10 mm fabricada en ABS, este pesará 1,05 gramos dada la densidad del material a 23 grados (1,05g/cm3).
Si fundimos este cubo de 1 cm3 y 1,05 gramos de peso en un crisol a 240 grados tendremos un volumen de plástico fundido en el crisol de 1,14 cm3 debido a la expansión del material (ver gráfica PVT de material amorfo). Es decir, tendremos en el crisol, 1,05 gramos de material ABS fundido que ocupa un espacio de 1,14 cm cúbicos y su densidad en estado fundido es ahora de 0,92 gramos /cm3.
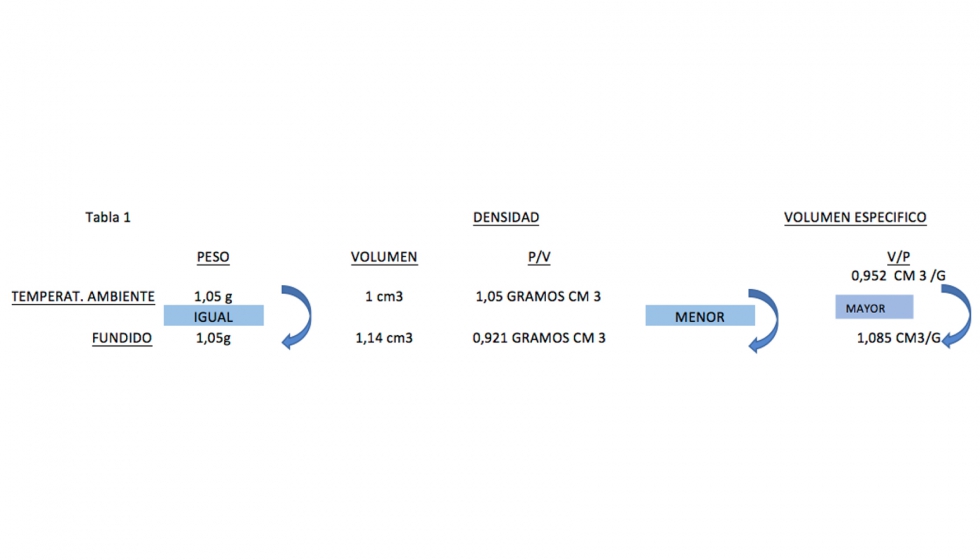
En el esquema vemos datos de peso, volumen, densidad y volumen específico a temperatura ambiente y a temperatura de fundido. Vemos en la tabla que la densidad ha bajado y el volumen específico ha aumentado al calentar el cubo de plástico de temperatura ambiente a 240 grados centígrados. Podemos decir entonces que al fundir el plástico, este aumenta su volumen especifico y reduce su densidad.
Tenemos pues en el crisol 1,14 cm3 de polímero ABS. Imaginemos que tenemos el molde en acero con una cavidad de 1 cm3 con el cual se fabricó el cubo que hemos fundido, es decir, de 10x 10x 10 mm y tenemos que introducir el material que tenemos fundido en el crisol que, cuando estaba en estado sólido, era 1 cm3 de material y conformaba un cubo perfecto de 1 cm de lado, vertiendo el material fundido dentro del molde por gravedad.
¿Que nos pasará? Pues que llenaremos el molde de 1 cm3 y aun nos quedará material fundido en el crisol, concretamente 0,14 cm3.
Para introducir este material en el molde, por gravedad, deberemos esperar a que el material introducido en el molde se vaya enfriando para que deje espacio por la contracción volumétrica que se producirá al reordenarse las moléculas. Para poder volcar más material fundido así poco a poco conseguiremos introducir el material fundido que ocupa 1,14 cm3 en el espacio del molde que dispone de 1cm3 de volumen.
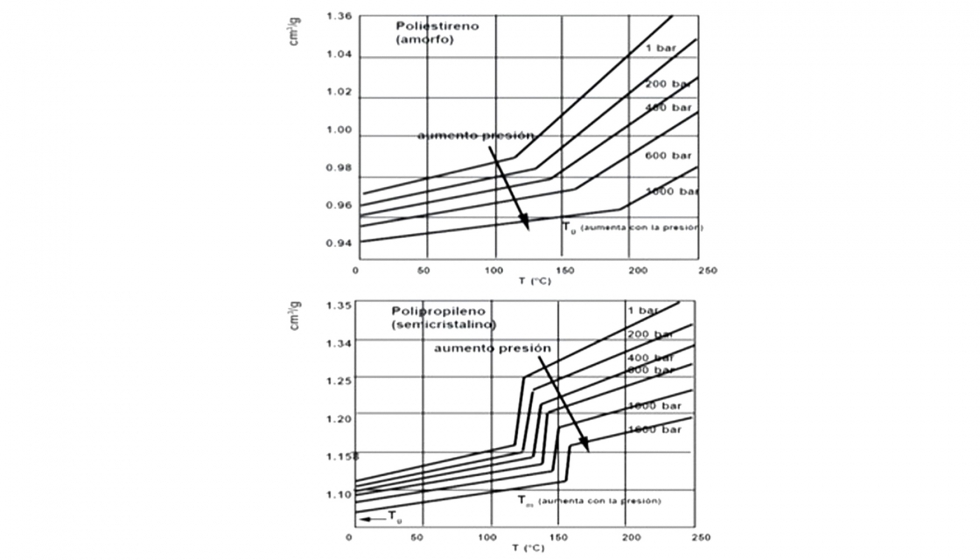
Figura 1.
El cubo de plástico procedente del este mismo molde, una vez fundido e introducido en el molde ,al enfriarse,vuelve a ocupar el volumen de la cavidad ,que es de 1 cm3 a temperatura ambiente
En la figura 1 podemos ver el cambio de volumen específico de los materiales plásticos, amorfos y semicristalinos en función de la temperatura y de la presión
El plástico aumenta su volumen al calentarlo , por lo tanto su densidad desciende también.
En la industria de la fabricación de piezas de plástico, no disponemos del tiempo que hemos empleado en el experimento anterior en dejar enfriar el material para que se produzca la contracción volumétrica que nos libera espacio para introducir más material en el molde.
Es por ello por lo que tendríamos dos posibles situaciones:
Situación 1
Fabricamos un molde con mayor dimensión para poder volcar todo el material fundido de una vez sin esperar a que el material se enfríe y así podemos hacer el llenado de una vez. Para ello tendríamos que dimensionar un molde con las dimensiones incrementadas para que cuando el material se enfríe y se contraiga quede con las dimensiones deseadas de 10x 10 x 10 mm. En este caso, si el material que pesa 1,05 gramos, ha aumentado su volumen a 1,14 cm3 nuestro molde debe tener un volumen de 1,14 cm3, es decir, si nuestro molde tiene unas dimensiones de 10,446x10,446 x 10,446 mm, deberíamos esperar que el material fundido que ocupa 1,14 cm3 pueda entrar en el molde de una vez y cuando contraiga hasta temperatura ambiente, tengamos un cubo perfecto de 1cm3 de 10x10x10 mm. (El lector debe tener en cuenta que en este teórico ensayo el volcado es a presión atmosférica, no tenemos presión de inyección y que la contracción se produce isotrópicamente es decir igual en todas direcciones).
Obtendríamos pues un cubo de 1 cm3 de volumen y con un peso de 1,05 gramos al llegar a temperatura ambiente.
Situación 2
Esta es la situación más común en la industria de transformación. Tenemos un molde con una entrada pequeña, alimentada por un canal de distribución que a su vez alimenta más cavidades similares y tenemos que llenarlas a la vez. Para esta situación no podemos pensar en hacer un llenado por gravedad. Aquí necesitaremos presión para introducir el material en el molde, presión de inyección. Esta presión de inyección hace que la contracción volumétrica esperada no sea tan alta ya que empaquetaremos moléculas durante el llenado volumétrico de la cavidad.
En el caso del cubo. En nuestra máquina de inyección, deberemos dosificar el volumen fundido necesario para que obtengamos un volumen final de 1 cm3, es decir (al margen de cojín no considerado en este ejemplo) tendremos que dosificar 1,14 cm3 de material fundido.
La cavidad. Para obtener piezas de 10x10x10 mm la cavidad del molde debe ser sobre dimensionada debido al factor de la contracción del material durante el enfriamiento en el molde y a la salida del molde o post contracción
Una contracción estándar para un ABS podría ser de 0,4 A 0,7%. Escogemos 0,5%. Nuestra cavidad debe sobredimensionarse en un 0,5%, es decir tendríamos una cavidad de 10,05x10,05x10,05mm.
Así pues, nuestra cavidad tendrá un volumen de 1,015 cm3 que tendremos que llenar con un volumen de material dosificado fundido de 1,14 cm3 de ABS que cuando se enfríe a temperatura ambiente tendrá un volumen de 1,0 cm3, la pieza medirá 10x10x10mm y pesará 1,05 gramos.
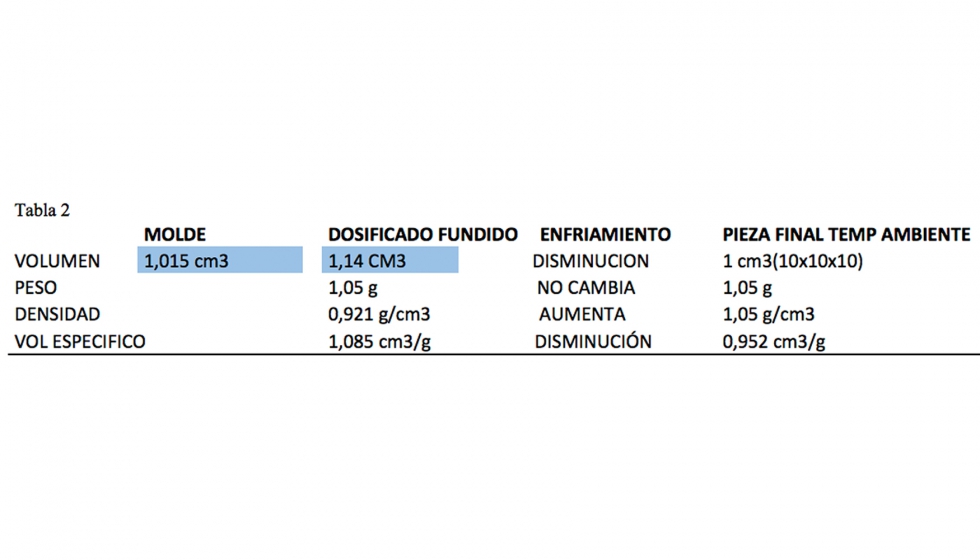
En la tabla 2 arriba podemos ver la evolución al pasar de fundido a temperatura ambiente de diferentes valores de: volumen, peso, densidad y volumen específico.
Cambio de volumen específico en la dosificación.
Seguidamente, realizaremos el llenado del molde aplicando presión para hacer entrar el material dentro de la cavidad. Con ello comprimiremos el material y las moléculas se compactarán entre ellas, aumentando su densidad.
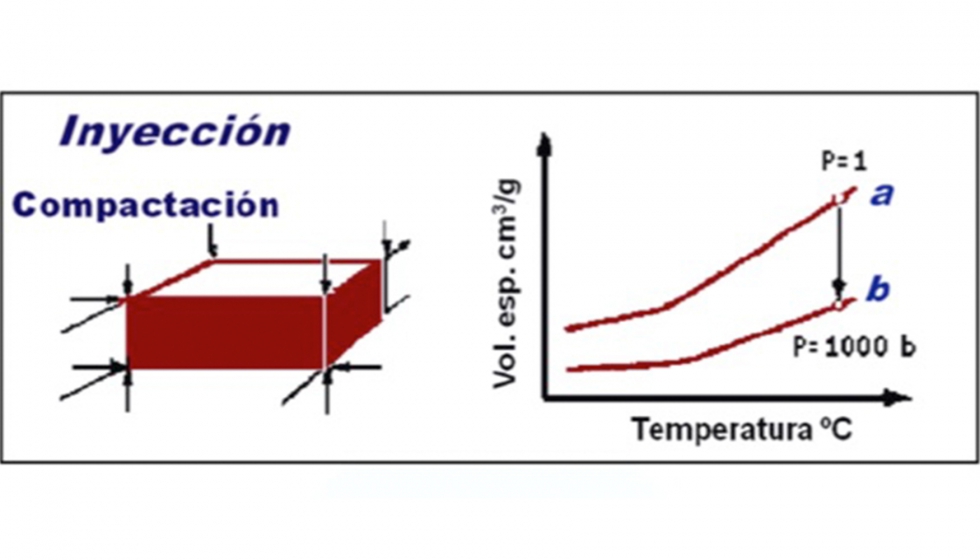
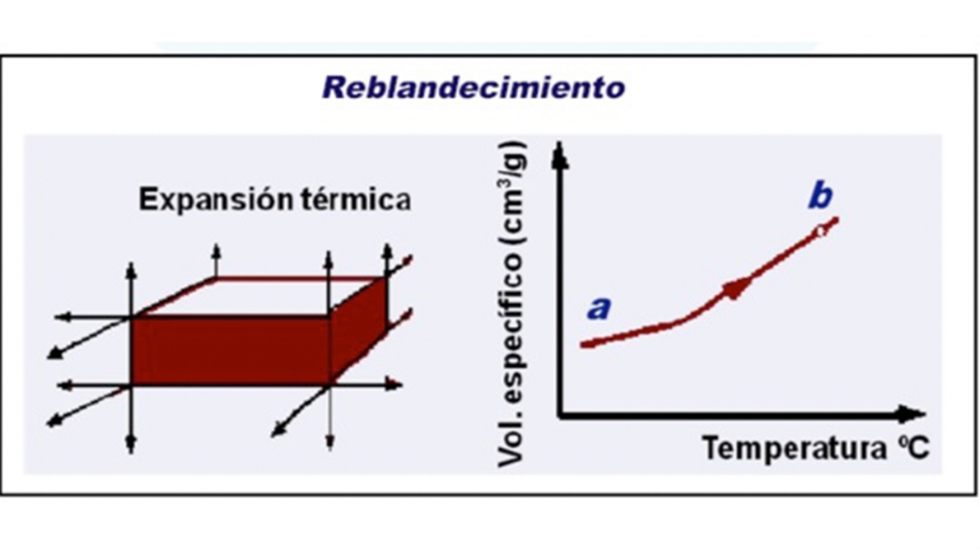
Compresión del material durante el llenado
Claramente, no podemos hacer entrar en esta etapa los 1,14 cm3 dosificados, pues no caben en la cavidad de 1,05 cm3(números marcados en azul) provocaríamos rebabas y sobrepresiones. Debemos introducir un volumen dentro de la cavidad pero no el 100% de la dosificación.Tampoco podemos hacer entrar 1 cm3 que sería el volumen final esperado de la pieza pues cuando el material se enfríe, el volumen disminuirá bastante.
Además, el polímero en estado fundido es como una pelota de espuma entre nuestras manos fácilmente compresible y debido a su comportamiento no newtoniano, su viscosidad decrece con la cizalla y el shear rate Por ello, si pretendemos introducir el 100% del volumen de la cavidad durante la fase de llenado, podemos muy probablemente provocar rebabas por exceso de llenado y por qué no: daños en el molde.
Se recomienda realizar un llenado de la cavidad en esta fase del orden del 95-98%, con ello nos aseguramos de que no estamos sobre inyectando o sobre presurizando la cavidad del molde.
Pero, 95% ó 98% ¿de qué valor? ¿del peso? ¿de la dosis? Esto lo trataremos en el siguiente artículo.