Preformas de PET al alcance de muchos
Responsable Oficina Técnica de Mir15/06/2002
ENVASES DE PET
Por motivos económicos y ecológicos, el uso de botellas y envases desechables hechos con PET, bien en procesos de una etapa (moldeo por inyección-estirado-soplado) o de dos etapas (inyección, almacenamiento y posterior calentamiento de las preformas antes del soplado) está creciendo mucho en todo el mundo, sobre todo en sustitución de envases de vidrio.
El uso del vidrio significa, de hecho, un mayor coste energético durante la producción, transporte, lavado previo al uso y reciclado. Es más, por motivos higiénicos, el vidrio debe ser lavado con sustancias cáusticas, lo cual supone otro factor negativo para el vidrio, originado en la necesidad de lavar adecuadamente los residuos de lavado En algunos países, como Alemania, donde los productores de agua mineral eran muy reacios a abandonar el vidrio, la industria pasó parcialmente a las botellas de plástico reutilizables, pero también surgieron problemas relacionados con el lavado de las mismas, orientando a las empresas hacia la adopción de envases desechables de PET.
La clarísima versatilidad de su uso es otro de los argumentos que explica el creciente éxito de las botellas de PET. En España y Reino Unido, por ejemplo, se utilizan incluso para envasar aceite de oliva. En Italia se está observando que el mercado aprecia la leche fresca de alta calidad envasada en botellas de PET y no incontables los productores de bebidas carbónicas y refrescos sin gas que han elegido esta solución para comercializar sus marcas. Finalmente, se está abriendo en la actualidad un mercado enorme para las botellas de PET. Tras unas pruebas costosas realizadas con PEN, algunas marcas de cerveza ya han comenzado a verse en PET en las estanterías de los supermercados, sobre todo en EE.UU.
Una prueba más del aprecio de este tipo de envases en todo el mundo viene dada por la diversidad de los sistemas de producción que proponen los fabricantes de máquinas, tanto para el producto final como para las preformas.
De todas formas, la mayor parte de los sistemas productivos han sido concebidos para responder a las necesidades de grandes compañías. Esto se demuestra fácilmente observando los moldes utilizados, muchos de ellos con un gran número de cavidades: hasta 144 cavidades en capacidades de 33.000 preformas de 26 a 29 g por hora, destinadas a envases de 55 cc. Y no menos sofisticada es la tecnología que incorporan. Todo esto redunda en altos costos tanto para adquirir como para operar estas líneas de producción, sólo justificados en producciones muy altas y muy estandarizadas. Esto se ajusta muy bien a los mercados más maduros en países muy industrializados. Sin embargo, no se puede decir lo mismo en el caso de los pequeños y medianos productores de botellas, por cierto cada vez mayor en número, ubicados en mercados en desarrollo en Oriente Medio, Oriente Lejano. Europa del este, Africa del norte, etc.
En la mayoría de los casos, estas empresas producen botellas y envases en maquinaria poco adecuada, porque sus producciones limitadas y frecuentes cambios en el moldeo no concuerdan con la estrategia de alta tecnología y elevadas producciones planteada por los especialistas en maquinaria.
Por este motivo, Mir y Gefit decidieron unir sus conocimientos en el moldeo por inyección y la construcción de moldes y robots respectivamente. El resultado, un sistema para la producción de preformas compacto, versátil y totalmente automatizado, pensado para volúmenes de producción razonables y un uso sencillo. El objetivo, satisfacer la demanda de los productores pequeños y medianos de botellas y envases de PET. Esta nueva línea de producción, ya disponible en el mercado, se identifica con el nombre PPS (PET Preform System).
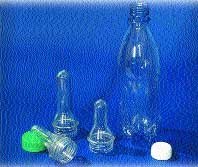
Inyección dual y un robot
PPS es una célula de producción completa, que incluye una inyectora dual de 280 toneladas, un molde de canal caliente con 16 o 24 cavidades, un manipulador giratorio de 4 estaciones para la extracción y enfriamiento, un sistema de refrigeración, una unidad de secado del material y un dispositivo de deshumidificación del molde, un control computerizado y centralizado y un sistema de gestión.
La configuración de la inyectora y del sistema robotizado para la extracción de la preforma y la refrigeración responde a dos necesidades críticas y contradictorias cuando se procesa PET para preformas: un ciclo rápido y un tratamiento cuidadoso del material, asociado a un intervalo de enfriamiento suficiente para asegurar la solidificación del material. La primera necesidad se refiere a la productividad, pero también a la prevención de un exceso de acetaldehído en la preforma, que afectaría a las características organolépticas de los productos envasados. La segunda es inevitable si se quiere obtener un producto ajustado a las especificaciones, pero no debe entrar en conflicto con el ciclo.
El sistema de inyección dual elegido está sobredimensionado en comparación con la fuerza de cierre de la máquina. De hecho, husillos de 90 mm (L/D = 24) y una unidad de inyección Euromap 2707, específicos para PET, responden de sobra a las exigencias de presión y volumen de una inyectora de 280 toneladas. La capacidad de sobre-plastificación permite el procesado adecuado del polímero y facilita una alimentación consistente de las cavidades del molde. De esta forma se reducen los intervalos entre inyecciones al mínimo y el material se ajusta perfectamente a la aplicación, incluso en lo relativo a los niveles de acetaldehído, muy por debajo de los aprobados por las regulaciones internacionales. En otras palabras, mientras el polímero se procesa con una intensidad por uno de los husillos, el otro alimenta el inyector y el molde y luego retrocede para la plastificación, sustituido inmediatamente por el primero. El ciclo resultante es muy rápido y muy preciso.
El objetivo del manipulador giratorio de cuatro estaciones desarrollado por Gefit y ubicado en el lateral de la máquina, incluye la extracción de la pieza y su enfriamiento. El enfriamiento de la preforma comienza ya en las cavidades del molde y prosigue en el robot antes de dejar las piezas en una cinta transportadora. Las cuatro estaciones giratorias se alternan en la entrada rápida en el molde para captar las preformas y mantenerlas hasta que enfríen. Esto permite una producción continuada ya que mientras una de las pinzas del robot sujeta las preformas, otra está libre para operar y puede ser sustituida inmediatamente por la pinza posterior. Al final del cuarto ciclo, la primera pinza del robot ya habrá soltado las preformas solidificadas para comenzar de nuevo con la extracción y enfriamiento.
Este sistema es interesante, como se ha dicho, para empresas pequeñas y medianas. Por ejemplo, con un molde de 24 cavidades y preformas de 26 g (para envases de 500 cc para agua mineral), los dos husillos operando a una velocidad de 60 rpm proporcionan una capacidad de plastificación de 278 kg, en un ciclo de moldeo total de 11 s, lo que viene a significar una producción horaria de 7.854 preformas. En producciones de tres turnos, estamos ante producciones de 188.509 preformas diarias.
Sólo un control
Todas estas ventajas se completan con otra, muy interesante: la posibilidad de trabajar sólo con un inyector, incluso para aplicaciones diferentes.