Aspectos importantes a tener en cuenta en el cierre de molde
José Ramón Lerma, dpto. técnico de Biesterfeld Ibérica
19/11/2018Seguramente en alguna ocasión nos habremos encontrado con la situación siguiente: Conocemos la presión pico de llenado de un molde (este valor lo podemos obtener del mando de control de la inyectora), conocemos el área o superficie proyectada sobre la que el material ejercerá fuerza en la dirección de abrir el molde, multiplicamos estos factores de presión y área y obtenemos una fuerza de cierre teórica. A esta fuerza le añadimos un factor de seguridad del 10% y obtenemos un valor de fuerza de cierre teórico final.
Es cierto que en preferentemente en la industria intentamos ubicar un molde en la máquina más pequeña posible, siempre que sea capaz, por un tema de coste horario, consumo, etc.
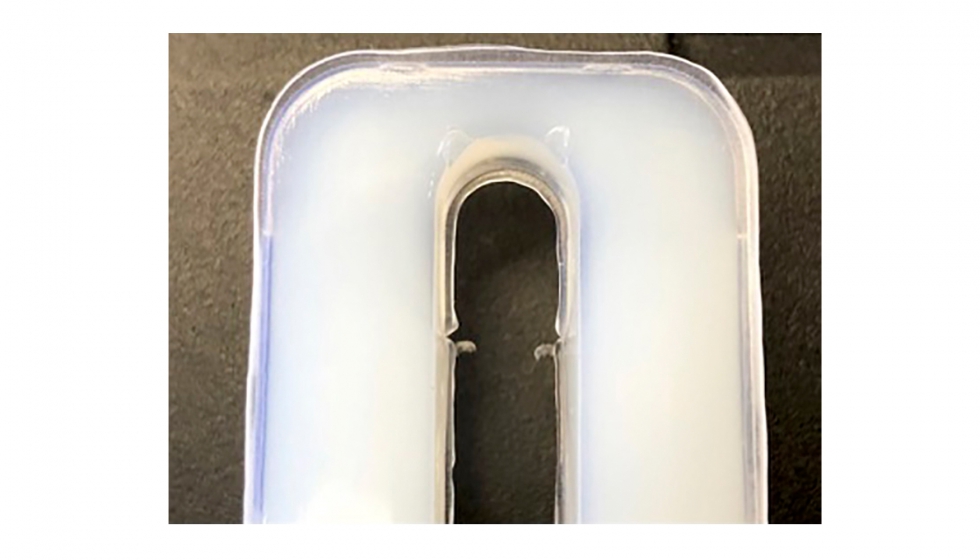
Rebaba perimetral de partaje en pieza inyectada.
Aplicamos esta fuerza de cierre calculada y para nuestra sorpresa se producen rebabas en las piezas... ¿Qué puede estar pasando?
Si analizamos el llenado del molde, tan solo aplicaremos en el interior de la cavidad una parte de la presión de inyección pico necesaria para llenar el molde. Aquí se producen, como hemos comentado en anteriores artículos, unas pérdidas de presión debidas a, por ejemplo, la boquilla de la inyectora, el canal caliente o canales de distribución frío y las entradas de las cavidades. Entonces, si el pico de presión real en el interior de la cavidad es menor que el pico de presión que nos indica la inyectora en su mando de control, no deberíamos de ningún modo tener rebabas en las piezas.
Siguiendo con el análisis del llenado del molde, ¿hemos tenido en cuenta toda el área proyectada?
Durante el llenado, por unos instantes el plástico fundido que hacemos entrar en la cavidad, cuando el llenado está llegando a su fin, el material fundido actúa de manera hidrostática, es decir, actúa como un líquido estático transmitiendo la presión en todas direcciones (en circunstancias ideales). Es decir, la masa fundida ejercerá presión en todas direcciones del molde no tan solo en la dirección frontal o en la dirección del eje de la inyectora o del molde.
Si el diseño del molde contempla correderas o patines o noyos hidráulicos (si estos son bloqueados en su posición de cierre por sistemas mecánicos que el cierre de máquina mantiene bloqueados), las superficies de estos elementos que entrarán en contacto con el polímero fundido, una parte de la presión de llenado será aplicada en estas superficies y debe tenerse en cuenta como fuerza de cierre necesaria añadida en el cálculo de la fuerza de cierre teórica necesaria.
En el caso de correderas con cierre por plano inclinado, un método de cálculo de la fuerza de cierre que hay que añadir en este cálculo sería, multiplicar el área o superficie proyectada de la corredera por el seno del ángulo del plano inclinado del bloqueo de la misma y multiplicado a su vez por la presión pico de llenado.
Estas fuerzas que las correderas ejercerán en el sentido de abrir el molde, y por tanto la unidad de cierre, deben ser añadidas al cálculo inicial de la superficie proyectada para tener un cálculo más exacto.
Hay moldes con relativamente poca superficie proyectada pero que tienen grandes superficies en correderas que requieren grandes cierres de molde.
También hay autores que indican que, tan solo para cerrar el molde y mantenerlo alineado puede ser necesario un 10% del total de la fuerza de cierre aplicada.
Hay casos donde los esfuerzos para comprimir muelles de movimiento de placas expulsoras, amortiguadores neumáticos, casos en los que diferentes temperaturas de cada semi molde para mejorar el desmoldeo de zonas de molde o diferentes coeficientes de expansión térmica pueden provocar un aumento de la fuerza de cierre necesaria para un molde determinado.
Analicemos el cierre de una inyectora, que es el elemento responsable de mantener el molde cerrado durante todo el proceso de llenado y compactación del material en la cavidad.
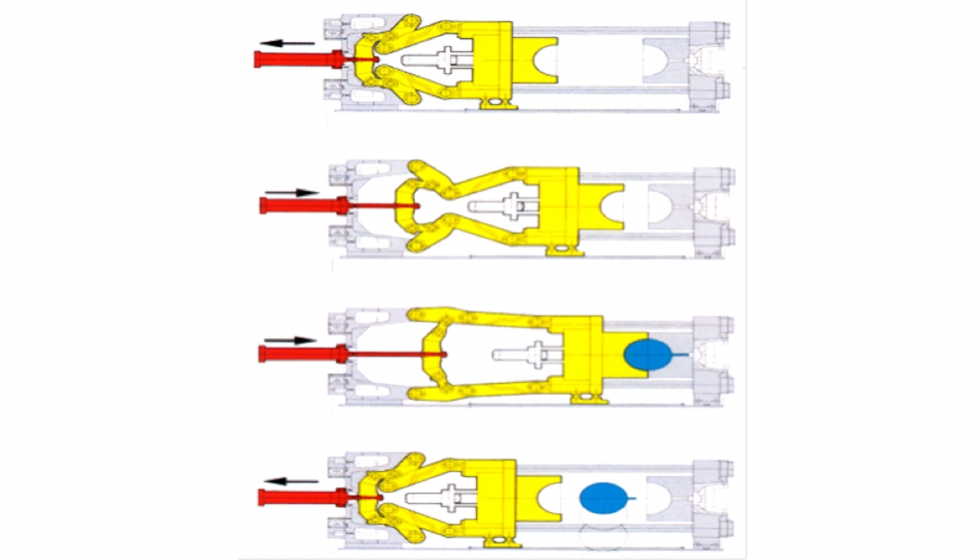
La inyectora, independientemente de si es de cierre hidráulico o cierre mecánico, si dispone de columnas (en el mercado hay inyectoras de cierre sin columnas con excelente funcionamiento), estas trabajan como cuatro grandes muelles. Cuando el molde es comprimido por el sistema de cierre, las columnas se estiran como un muelle y ejercen la fuerza de cierre que es ejercida entre el plato fijo y el plato móvil y por tanto sobre el molde que esta contenido entre estos dos platos.
Este estiramiento de las columnas es muy importante pues indica el nivel de esfuerzo aplicado durante el cierre y debe estar dentro de unos valores aceptables para el acero del cual están realizadas las columnas.
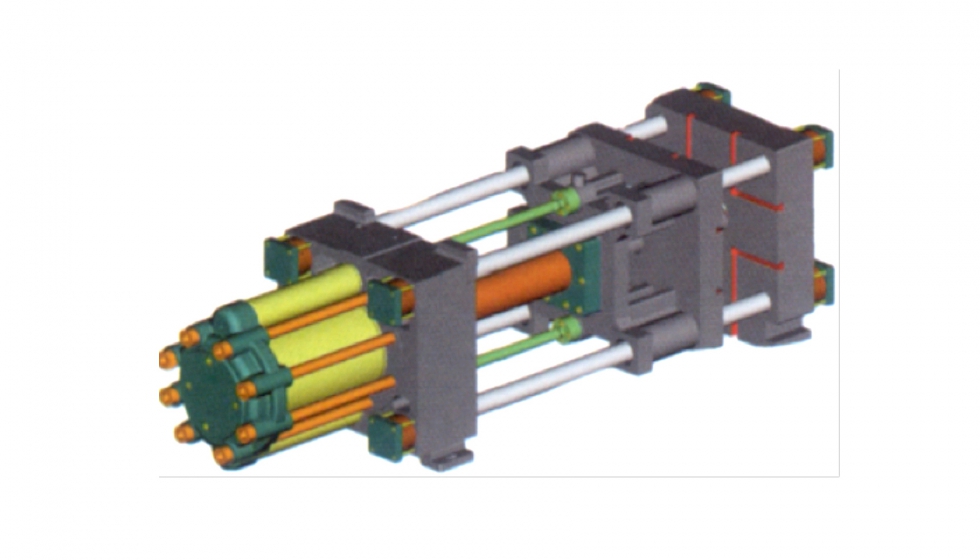
En resumen, cuando colocamos un molde en máquina, debemos tener en cuenta, además de la superficie proyectadas de las cavidades, las superficies de las correderas que actuaran también durante el llenado, la fuerza necesaria para cerrar y alinear el molde durante el bloqueo.
También los muelles o sistemas de compresión para movimientos deben tenerse en cuenta diferencias de temperatura entre semi moldes y la fuerza necesaria para cerrar y bloquear el molde.
Hay técnicos que aplican azul de Prusia en los partajes del molde, cierran con un 5% del total de la fuerza de cierre disponible y van incrementando en 5% o 10% hasta que el azul de Prusia indica que todo el partaje esta completamente ajustado. Esta sería la fuerza de cierre necesaria para bloquear el molde. Estos valores suelen ser, dependiendo del tamaño del molde y de la máquina del orden, de ente el 5 y el 20% del total de la fuerza necesaria.
Pueden aparecer otros tipos de rebaba que nada tienen que ver con el ajuste y cierre del molde. Estas son normalmente debidas a otros desajustes de otros elementos del molde tales como expulsores, noyos, correderas, patines, etc.
Además del cierre de molde y máquina comentados, las rebabas de ajuste de partaje pueden producirse por diferentes causas que nada tienen que ver con la fuerza de cierre. Estas podrían ser entre otras, velocidades de inyección, exceso de temperatura de masa, exceso de temperatura de molde, exceso tiempo de permanencia, viscosidad del material, deficiente deshumidificado del material, pack de aditivos del material, imprecisiones de la máquina de inyectar, incorrecta parametrización del proceso, etc., … Pero esto es material para otros artículos.
José Ramón Lerma es autor del Libro Manual Avanzado de Inyección de Termoplástico, que tiene como objetivo ser, por un lado, una herramienta para la formación y, por otro, un manual de ayuda para todo el personal de una empresa de inyección de plásticos. El libro, comercializado por Plásticos Universales / Interempresas (libros@interempresas.net), consta de detallados casos prácticos, amplia información de moldeo científico y un ‘pendrive’ con 20 hojas de cálculo y herramientas de SC Molding o Scientific Injection Molding, además de optimización y definición de proceso, lo que lo hacen único en el mercado. Página web sobre Scientific Injection Molding: www.asimm.es
Más información sobre los cursos Scientific Molding online impartidos en Inefco, en los que José Ramón Lerma es tutor https://tienda.novaagoraformacion.com/home/62-procesos-avanzados-de-inyeccion-de-termoplasticos.html