Parámetros clave del proceso de inyección: temperatura de molde, dosificación y cojín
Temperatura de molde (V)
La temperatura de molde o temperatura de la cavidad es un elemento determinante del tiempo de ciclo y de la calidad de la estructura de la pieza inyectada y por tanto, de las propiedades mecánicas finales que obtendremos tras el proceso de inyección.
Bajas temperaturas de molde provocan tiempos de enfriamiento cortos y grandes velocidades de enfriamiento pero pueden influir negativamente en la calidad de la pieza y en el nivel de stress interno de la estructura de la misma.
En el caso de los termoplásticos semicristalinos, las propiedades de las piezas inyectadas dependen de la velocidad de enfriamiento. Un enfriamiento rápido da lugar a una capa exterior amorfa y a un nivel bajo de cristalinidad. Por contra, un enfriamiento lento da lugar a un alto grado de cristalinidad, lamelas y cristales estables y mejores propiedades mecánicas.
El ideal es un enfriamiento homogéneo en virtud de una distribución homogénea de las temperaturas, tanto en la distribución térmica del molde como en la distribución térmica de la masa. Para ello es necesario un correcto acondicionamiento térmico del molde.
El nivel de cristalinidad final obtenido es una decisión del inyectador. Es su responsabilidad y debe depender de la aplicación final de la pieza inyectada. Si los requerimientos son exigentes desde el punto de vista de propidades mecánicas tenemos que obtener el mayor nivel posible de cristalinidad.
Según el material que estemos transformando tendremos que actuar de distinta forma para conseguir la temperatura de molde conveniente. Normalmente se utilizan estos sistemas:
- Refrigerar con agua hasta 90 grados
- Atemperar con agua presurizada o aceite térmico hasta temperaturas de 120 -150 grados
- Calefactar con resistencias eléctricas para temperaturas mayores
- Influencia de la temperatura de molde (incremento).
El incremento de la temperatura de molde puede influir en:
- Aumento del brillo superficial
- Disminución de las tensiones internas
- Aumento de la resistencia al impacto
- Mejora de las líneas de soldadura
- Aumento de la contracción de moldeo
- Aumento de la formación de rebabas
- Aumento del ciclo de inyección.
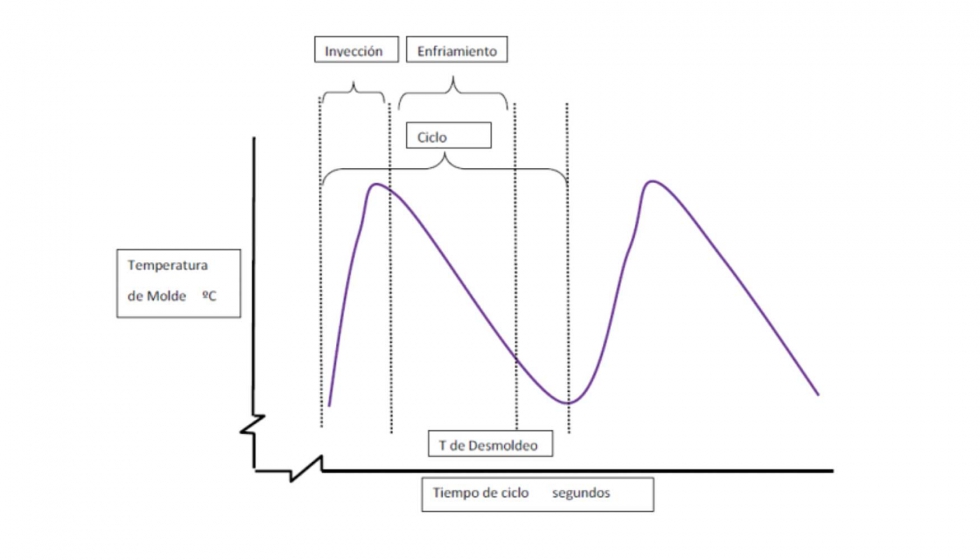
El proceso de inyección es un proceso térmico. Añadimos gran cantidad de calor durante el llenado del molde a través de la temperatura de la masa fundida y seguidamente extraemos parte de este calor aportado mediante el sistema de refrigeración del molde. Estos aumentos y reducciones de calor en el molde hacen que la temperatura finalmente se estabilice en un valor resultante del propio proceso.
Esquema de efectos de la temperatura de molde alta y temperatura de molde baja:
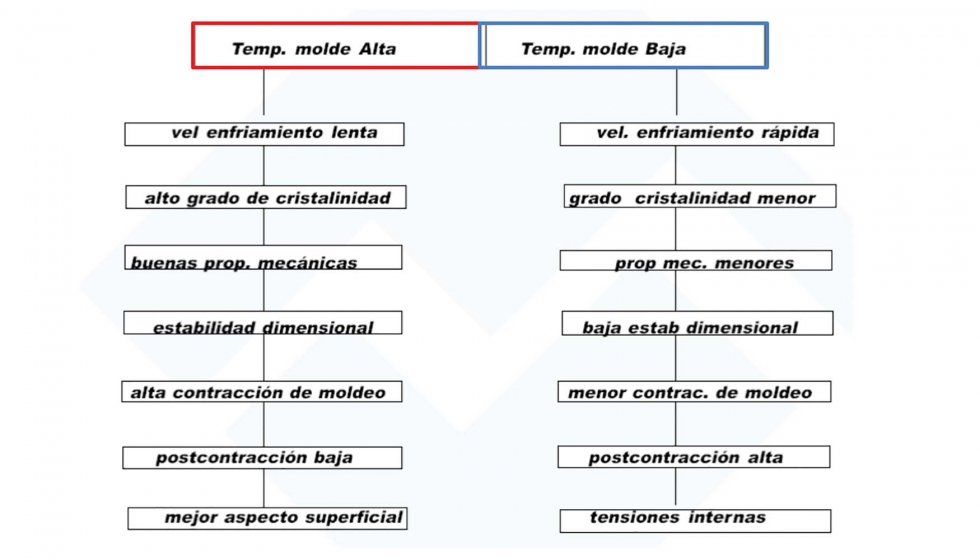
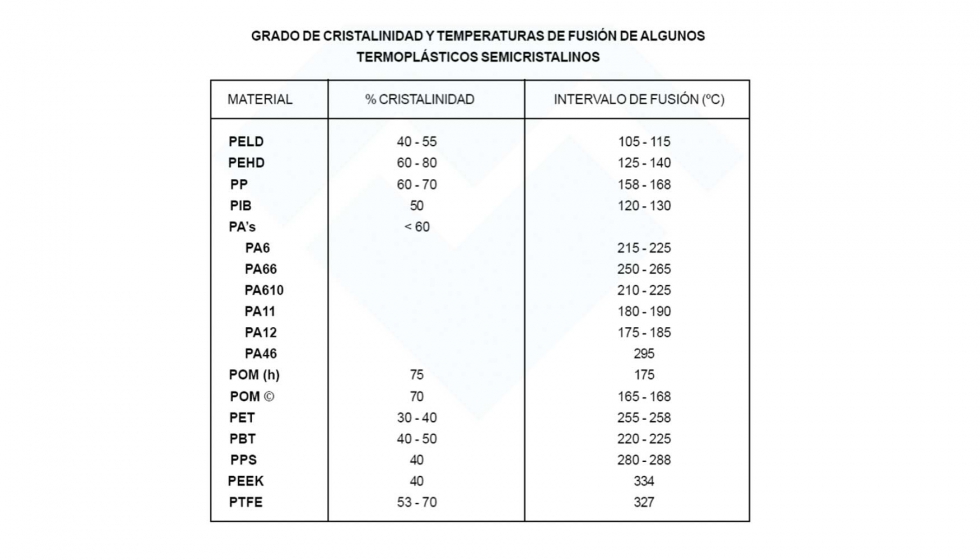
Temperaturas de molde recomendadas para algunos materiales:
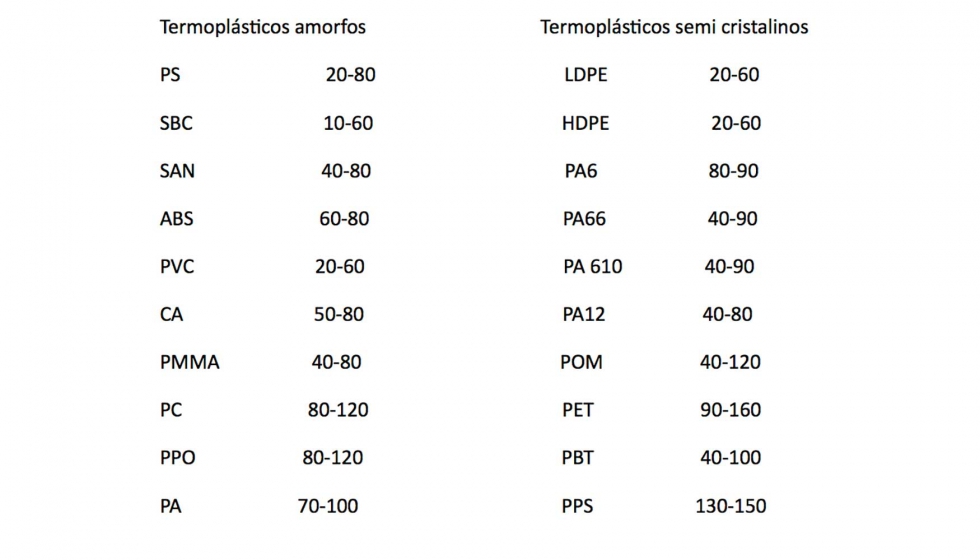
Siempre hay que escoger la temperatura de molde teniendo en cuenta el espesor de la pieza y el recorrido de flujo necesario. Evidentemente, cuantas más restricciones de paso de material fundido más alta escogeremos la temperatura de molde. Es muy importante en el caso de requerir propiedades mecánicas por solicitaciones en la pieza durante su aplicación o vida útil, seleccionar temperaturas que permitan la adecuada cristalinidad.
Dosificación
Experimentalmente se ha podido determinar que el recorrido óptimo del husillo en la dosificación es el equivalente a una carrera entre 1 a 3 diámetros de husillo.
Deberían evitarse dosificaciones menores de 1 diámetro y mayores de 4 diámetros.
Esto no viene a indicar que el volumen utilizado de una unidad de inyección es del orden del 70 al 80% de su capacidad máxima y un mínimo del orden del 20 al 30%.
El tiempo de dosificación es un output que nos da una idea de la repetibilidad del proceso y está afectado por condiciones y parámetros tales como:
Rpm o velocidad tangencial del husillo, contrapresión a la carga, estado de precisión y desgaste de la punta del husillo, estado y precisión de desgaste del conjunto husillo-cámara, granulometría del plástico, temperatura de la traversa, precisión en la regulación térmica de la cámara de plastificación, etc.
Es importante controlar este output pues nos aporta información de la precisión y estado de cantidad de condiciones de proceso relacionadas con él.
Cojín
Este es el volumen residual al final de la fase de compactación que queda en la zona delantera del husillo. Es imprescindible disponer de cierto cojín para asegurar la correcta aplicación “aguas arriba” de la presión de inyección. Este volumen también permite absorber diferencias de volumen entre ciclos aportando estabilidad en los pesos y volúmenes inyectados.
Es claramente un output del proceso cuyo valor es una resultante de cómo está definido el proceso.
Este es un parámetro que da una muy buena información de la estabilidad y precisión del proceso establecido.
En general y en función del diámetro de husillo se establece como cojín objetivo el mantener entre un 5 a un 10% del volumen inyectada.
José Ramón Lerma es autor del Libro Manual Avanzado de Inyección de Termoplástico, que tiene como objetivo ser, por un lado, una herramienta para la formación y, por otro, un manual de ayuda para todo el personal de una empresa de inyección de plásticos. El libro, comercializado por Plásticos Universales / Interempresas (libros@interempresas.net), consta de detallados casos prácticos, amplia información de moldeo científico y un ‘pendrive’ con 20 hojas de cálculo y herramientas de SC Molding o Scientific Injection Molding, además de optimización y definición de proceso, lo que lo hacen único en el mercado. Página web sobre Scientific Injection Molding: www.asimm.es
Más información sobre los cursos Scientific Molding online impartidos en Inefco, en los que José Ramón Lerma es tutor https://tienda.novaagoraformacion.com/home/62-procesos-avanzados-de-inyeccion-de-termoplasticos.html