Presión de compactación (IV)
Pospresión
Antes de la fase de compactación o pospresión se realiza la fase de llenado volumétrico. En esta se produce el llenado completo de la cavidad con plástico fundido, pero al ser el plástico un material compresible, desconocemos cuándo se ha llenado el molde al 100% exactamente. Puede suceder que en realidad estemos llenando por encima de este valor provocando sobre inyección de la cavidad, rebabas, tensiones en las piezas y dalos en el molde, etcétera.
Es por ello por lo que se recomienda llenar en esta fase de inyección dinámica o de llenado volumétrico hasta el 90-98% del total del volumen con el fin de asegurar que no se sobre inyecta el molde y estar seguro de que no hemos forzado la inyección del material por encima de lo recomendado.
Fase de empaquetado
En esta fase debemos compensar la contracción volumétrica que se produce por efecto del enfriamiento y la reorganización molecular del plástico. En esta fase controlamos la presión.
Debemos tener en cuenta una vez que el molde está lleno al 90-98% que ya no tendremos la valiosísima aportación del calor que genera la cizalla de las moléculas friccionando entre sí, pues el flujo se ralentiza y este efecto de “calor interno” ya no está presente.
Además, el polímero al entrar en contacto con las paredes del molde, donde está convenientemente instalado el sistema de refrigeración del molde, empieza a enfriarse de manera inminente. Estos dos factores, la ausencia del calor ejercido por la cizalla y la refrigeración del molde, hacen que el polímero empiece a enfriarse y a contraer, es decir, empiece a reorganizarse molecularmente. Empieza pues la cristalización en los materiales semicristalinos y la contracción tanto en amorfos como en semicristalinos.
En esta fase debemos hacer entrar a través de la presión de compactación y el tiempo de compactación, más moléculas en la cavidad que ocupen los espacios o el volumen que se está generando nuevamente debido a la contracción y reorganización molecular. Es por tanto una fase de compensación de la pérdida de volumen generada por el enfriamiento.
Una vez que ha finalizado esta fase de compensación de la pérdida volumétrica pasaremos a la siguiente fase.
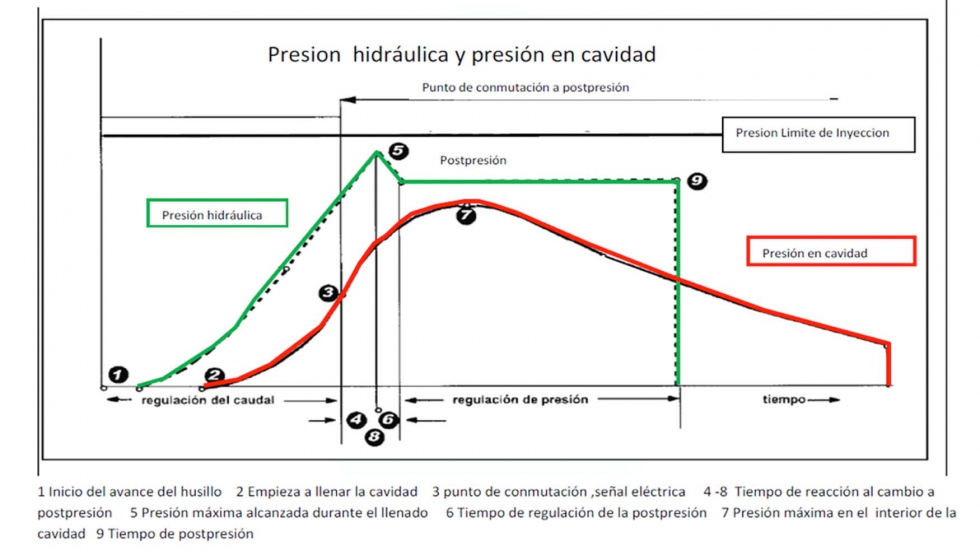
Fase de mantenimiento de la presión o hold
En esta fase debemos mantener la presión para definir las medidas, definir el acabado superficial del molde, etc. y esperar a que la entrada se selle por congelación del polímero.
Finalmente es esta la fase que sirve para mantener la presión hasta que se cierre la entrada por efecto del enfriamiento del plástico. Esto evitará que el plástico pueda retroceder desde la cavidad hacia atrás, realizando el desaconsejable efecto llamado back flow. En esta fase controlamos el tiempo de compactación y la presión de compactación.
Muchos inyectadores no diferencian entre la fase de empaquetado y la de mantenimiento o entre la fase de pack y la de hold y se programa en la inyectora una presión y un tiempo para ambas fases.
Influencias de la fase de compactación:
- Formación de rebabas
- Contracción general de la pieza, dimensiones
- Dificultad de expulsión de la pieza
- Tensiones en la zona de la entrada
- Rechupes
- Vacuolas
- Resistencia de las líneas de unión
- Peso de la pieza
Se puede determinar el tiempo ideal de compactación o postpresion a través de dos sistemas:
Tiempo de post-presión
Determinado a través de:
- Caída de presión en cavidad (para ello es necesario un sensor en cavidad)
- Control del peso de la inyectada.
Caída de presión en cavidad
Para determinar el tiempo óptimo de postpresión a través de este sistema necesitamos tener instalados sensores de presión en el molde y el sistema de monitorización de la presión.
Si aplicamos un tiempo corto de postpresión, al cesar la presión hidráulica, la presión en cavidad cae bruscamente. En cambio, si el tiempo es suficientemente largo, al suprimir la presión hidráulica, la presión en cavidad permanece y cae lentamente, lo cual indica que la entrada se había sellado.
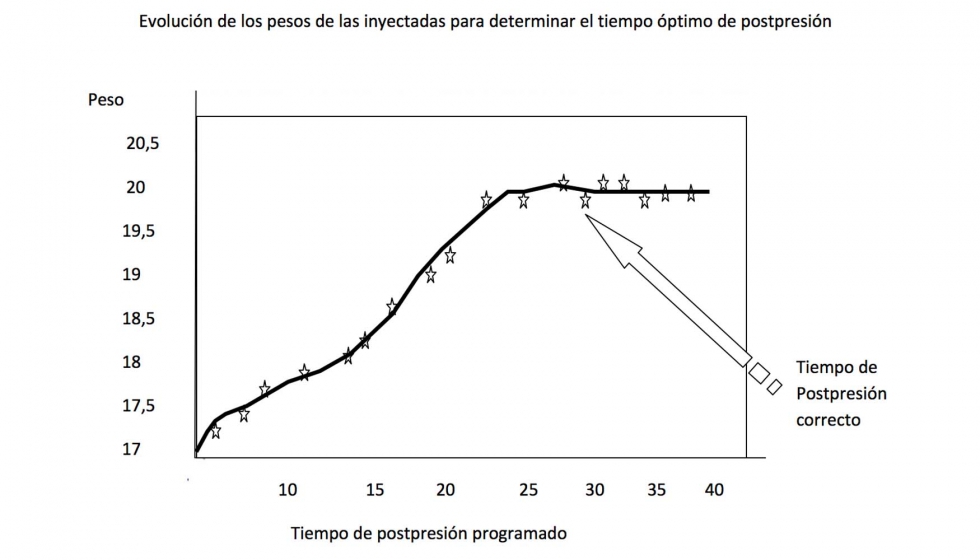
Control del peso de la inyectada.
Para utilizar este sistema tan solo hace falta una balanza calibrada y se trata de pesar una serie de inyectadas con diferentes tiempos de compactación. Es importante pesar las piezas sin el canal de distribución o colada. Es por tanto la balanza un elemento imprescindible en la puesta a punto de un molde.
- El tiempo óptimo es el que consigue el peso máximo de la pieza, al principio al incrementar el tiempo de postpresión obtenemos incrementos de peso, hasta que el peso deja de crecer al realizar aumentos de tiempo.
- Hay que tener en cuenta no contemplar la colada en el control de pesos o contemplarla aparte con su propio control de pesos.
- Si la colada se congela antes que la pieza no podremos nunca compactar adecuadamente la cavidad.
Si no aplicamos para la definición del tiempo óptimo de presión de compactación, el control de la evolución de los pesos o de evolución de la presión en cavidad y lo hacemos de modo empírico, lo más probable es que estemos fabricando coladas preciosas, compactadas y brillantes con toda su pérdida de volumen compensada durante la fase de compactación. Pero esto será un derroche que nadie nos compensará.
José Ramón Lerma es autor del Libro Manual Avanzado de Inyección de Termoplástico, que tiene como objetivo ser, por un lado, una herramienta para la formación y, por otro, un manual de ayuda para todo el personal de una empresa de inyección de plásticos. El libro, comercializado por Plásticos Universales / Interempresas (libros@interempresas.net), consta de detallados casos prácticos, amplia información de moldeo científico y un ‘pendrive’ con 20 hojas de cálculo y herramientas de SC Molding o Scientific Injection Molding, además de optimización y definición de proceso, lo que lo hacen único en el mercado. Página web sobre Scientific Injection Molding: www.asimm.es
Más información sobre los cursos Scientific Molding online impartidos en Inefco, en los que José Ramón Lerma es tutor https://tienda.novaagoraformacion.com/home/62-procesos-avanzados-de-inyeccion-de-termoplasticos.html