Nuevas tecnologías para el pulido de materiales de acero
Se han aplicado en el estudio dos técnicas muy novedosas, el pulido mediante láser (de fundamento térmico) y la técnica de bruñido mecánico o ball-burnishing (fundamento mecánico) para conseguir pulir piezas y moldes de acero reduciendo los tiempos de producción y de control del proceso.
Pulido láser
Existen pocos estudios sobre el pulido láser de superficies metálicas y actualmente no hay resultados experimentales disponibles. El pulido láser de superficies metálicas se basa en la fusión de una capa microscópica de material con un haz de láser y la posterior solidificación del material fundido. La capa microscópica fundida debe ser lo suficientemente profunda como para fundir los picos de la topografía pero sin llegar al fondo de los valles, de forma que el material fundido solidifique rellenando el hueco de los valles, dando como resultado una topografía con una menor rugosidad superficial que la inicial.
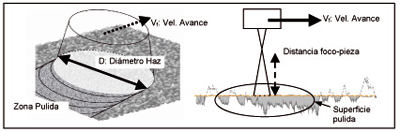
Ball-Burnishing
El principio de funcionamiento del ball-burnishing está fundamentado en un muelle hidrostático. La presión es suministrada por un una bomba hidráulica, que se alimenta de la propia taladrina de la máquina de mecanizado en la que se monta el equipo de pulido. El elemento clave es una bola cerámica que es soportada hidrostáticamente, gracias a la presión de la bomba. Esta bola actúa sobre las crestas de mecanizado aplastándolas y logrando la mejora en la rugosidad.
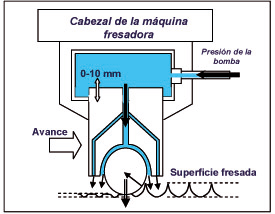
Sinterizado selectivo por láser
El sistema SLS trabaja creando capa a capa los objetos tridimensionales, diseñados en soporte informático mediante CAD, partiendo de la solidificación selectiva de partículas de material en polvo, y utilizando el aporte de calor generado por un láser de CO2 incorporado al sistema. Los ficheros de CAD, en formato STL, son ‘cortados’ en finas capas y dibujados mediante un fino rayo láser en una superficie cubierta por una leve capa de partículas de polvo. Estas partículas se funden, soldándose a la capa anterior por lo que encajan perfectamente al diseño realizado en CAD. A medida que se funden las capas, las piezas van tomando forma en el interior de la máquina. Una vez terminado el proceso, se elimina el polvo sobrante no solidificado.
El proceso de SLS (Sinterizado Selectivo por Láser) permite la fabricación de piezas complejas en diferentes materiales como polímeros, cerámicas y algunas aleaciones metálicas. La rugosidad superficial típica de las piezas fabricadas mediante SLS suele oscilar entre 5 y 8 μm Ra, mientras que el valor medio de la rugosidad para moldes de inyección debe ser menor de 1μm Ra.
Resultados
a) Pulido láser
Para los estudio del proceso de pulido láser se utilizaron tres materiales: un acero con bajo contenido en carbono F114, un acero para trabajo en caliente denominado Orvar Supreme y un material empleado en los procesos de sinterizado selectivo por láser, denominado LaserForm, aleación de bronce y acero inoxidable.
En el primer caso se utilizaron dos sistemas, el mecanizado de alta velocidad y el sistema de electroerosión por penetración para producir una rugosidad inicial. Los resultados demostraron un mayor nivel de reducción de la rugosidad al pulir las superficies con láser en las piezas electroerosionadas que en las fresadas.
En el segundo material, Orvar Supreme, los resultados muestran una clara mejoría de la rugosidad en todos los casos. Y al igual que sucede en el caso del acero F114, a medida que la superficie inicial es más rugosa, el acabado final es mucho mejor.
Al mismo tiempo, los resultados experimentales sobre acero aleado (AISI P20) con dureza 290-335 HB (usado en moldes de inyección de aluminio) han demostrado un avance en tiempo de 15 minutos, alcanzando un nivel de pulido de 0,1.
En el caso del Laserform ST-200, el cual consiste en un composite de acero inoxidable con graduación 420 que contiene un material polimérico que actúa como ligante, se diseñó una pieza con una geometría específica que se sinterizó tras realizar previamente una optimización del proceso de SLS, variando distintos parámetros: potencia del láser, temperatura de la cámara, % de infiltración, espesor de capa, etc., con objeto de obtener piezas con la menor rugosidad inicial posible y buenas propiedades mecánicas y dimensionales.
Los resultados observados tras el pulido láser no fueron tan buenos, aunque se observó una clara mejoría de la rugosidad.
Posteriormente, se realizó una segunda pieza probeta “Pieza test 3D” diseñada con tres pendientes diferentes (15º, 30º y 45º), para poder realizar diferentes pruebas en diferentes planos.
La estrategia de pulido desarrollada fue perpendicular a las capas formadas en el proceso de SLS. La Rugosidad inicial se determinó entre 7.52 y 8.31 μm).
b) Ball burnishing
La técnica de bruñido mecánico o ball-burnishing se investigó en un banco de ensayos con un equipo de bruñido con bola en un dentro de mecanizado de 5 ejes Ibarmia ZV 25 U en el taller mecánico del Dpto. de Ingeniería Mecánica de la Universidad del País Vasco, compuesto por una bomba portátil de 20 MPa y un cabezal de bruñido.
Los materiales empleados fueron dos: el AISI P20 pre-tratado con una dureza de 31 HRC y, al igual que en el caso anterior, acero de trabajo en caliente Orvar Supreme templado hasta 52 HRC.
Los resultados obtenidos demostraron que se pueden obtener superficies pulidas hasta 0.2 µm Ra. La principal dificultad sería el acceso de la bola cerámica a las zonas de detalle. Para la realización del ensayo se emplearon las siguientes características: paso 0,1 mm; avance 15 m/min.
Las piezas a su vez, fueron cortadas y analizadas en microscopio mediante inspección metalúrgica y medición de dureza superficial.
Se observó una penetración de capa aplastada: hasta 14 µm. Este efecto es debido al trabajo en frío que realiza la bola sobre la superficie, alterando la orientación de las fibras y comprimiéndolas en la superficie. Las tensiones son de compresión lo cual conduce a una mejor vida a fatiga, mejor comportamiento.
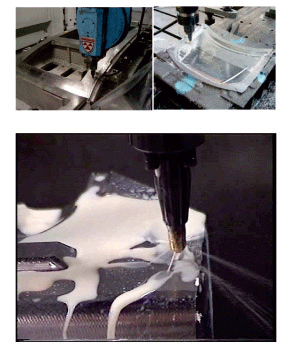
Conclusiones
Los resultados muestran claras reducciones de la rugosidad en dos tipos de superficies de material y textura diferente. Se ha observado que según los parámetros utilizados existe un rango de potencias y distancias entre cabezal y pieza en el que se obtienen los resultados óptimos. A medida que se aumenta la potencia o se acerca el cabezal, se obtienen peores resultados de rugosidad en zonas tratadas más estrechas. Se observa en estas zonas, que la zona fundida es más profunda, lo que corresponde con el fenómeno de cambio de régimen SSM a SOM.
Se puede afirmar a la vista de los resultados que el proceso es más efectivo cuanto más rugosa sea la superficie inicial. Se puede afirmar también que es un proceso aplicable a superficies de tamaño pequeño-mediano, mediante la superposición de líneas de barrido. La zona de solape entre diferentes pasadas del láser no presenta saltos ni mayor zona afectada por el calor.
Por último, en el caso de piezas sinterizadas mediante SLS, los resultados muestran una gran mejoría de la rugosidad superficial, aunque no se han alcanzado valores de rugosidad como los del acero. Este hecho se debe a que el material es una mezcla de acero inoxidable y bronce, por lo que es necesario operar con parámetros que fundan los dos materiales (lo que afecta a una capa más profunda). Este tipo de régimen no permite alcanzar mejoras de rugosidad comparables a las obtenidas en acero.
Este sistema todavía se encuentra en estado experimental para poder aplicarse sobre el proceso de moldes convencional, pero tiene una gran proyección de futuro. Por ese motivo, y para continuar desarrollando este proceso, se ha realizado una nueva propuesta de continuación de investigación al Ministerio para los próximos años.
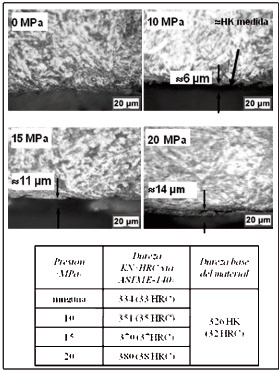