Soluciones de sistema inteligentes de Engel en la feria NPE 2018
Máxima calidad y máxima rentabilidad: Engel firma austriaca representada por Helmut Roegele, demuestra que esto no es ninguna contradicción en la NPE2018, del 7 al 11 de mayo en Orlando, Florida, con una gran variedad de fascinantes aplicaciones de moldeo por inyección. Para proporcionar la ventaja decisiva a sus clientes de los sectores de automoción, teletrónica, moldeo técnico y medicina, el fabricante de máquinas de moldeo y proveedor de sistemas apuesta por tecnologías innovadoras, conceptos de producción hechos a medida y controles inteligentes.
Desde máquinas de moldeo por inyección individuales hasta células de fabricación totalmente integradas, Engel ofrece soluciones hechas a medida a la industria del moldeo por inyección. Para desarrollar soluciones a medida de los clientes, hace falta algo más que conocimientos tecnológicos. Es fundamental comprender profundamente los requisitos individuales de los clientes y aplicarlos de manera eficiente. Para ello, Engel aglutina sus conocimientos de los sectores en cinco unidades de negocio, no solo en la planta matriz de Austria.
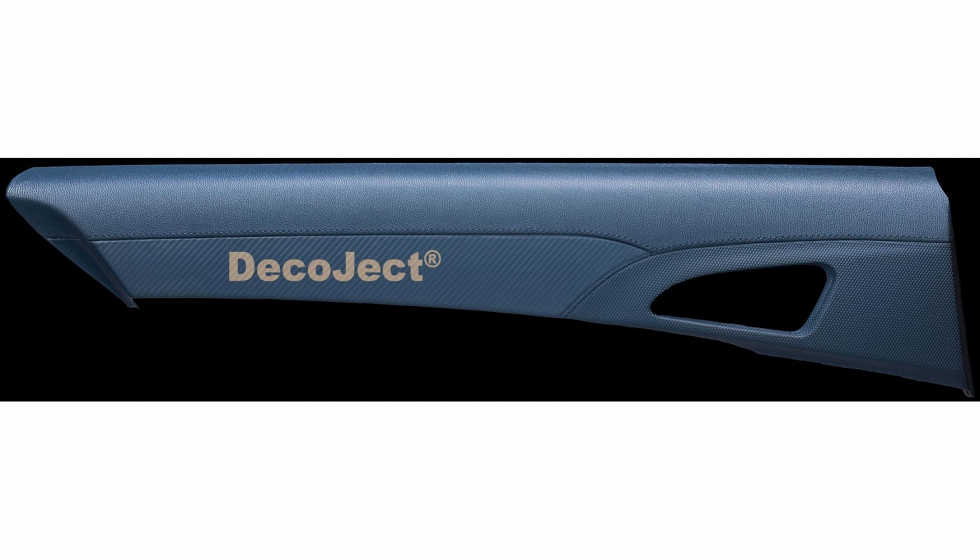
[
DecoJect permite fabricar de forma rentable incluso componentes interiores grandes. Las características deseadas de la superficie, como el color, la textura, la robustez y el tacto, se realizan mediante la lámina. (Imagen: Engel)
Hace tres años, Engel Machinery Inc., con sede en York, Pensilvania, nombró a sus propios directores de las unidades de negocio para Norteamérica y, desde entonces, ha reforzado tanto sus conocimientos locales del sector como sus capacidades técnicas para aplicaciones. "Los comentarios que nos llegan de los clientes son muy buenos. Los éxitos más recientes confirman que hemos tomado el camino correcto", relata Mark Sankovitch, presidente de Engel en los Estados Unidos, con vistas a la NPE2018. "Somos capaces de responder todavía más rápido a los requisitos y deseos de nuestros clientes en los distintos sectores, así como ayudarles a encontrar solución a sus retos concretos de forma todavía más específica. Como proveedor de sistemas, acompañamos a nuestros clientes cada vez más a menudo a lo largo de todo el ciclo de vida de las máquinas y células de fabricación; con la nueva estructura respondemos justamente a esta tendencia".
Desde la automoción hasta la medicina y el embalaje, pasando por el moldeo técnico y la teletrónica: cada sector plantea sus requisitos específicos, si bien las tendencias generales son las mismas. La integración de procesos y la automatización cobran cada vez más importancia en Norteamérica. Al mismo tiempo, la digitalización y la interconexión centran cada vez más la atención de los procesadores. Todas estas tendencias aumentan la calidad, la eficiencia y la rentabilidad, pero también la complejidad de los procesos de fabricación. "Como proveedores de sistemas, nos ocupamos de que incluso los procesos complejos se puedan controlar de manera segura», dice Sankovitch. "Los equipos expuestos en nuestro stand de la feria lo muestran de forma ilustrativa".
Automoción: componentes interiores de alta calidad a costos unitarios bajos
Por primera vez en Norteamérica, Engel presenta en su stand de la feria una célula de fabricación integrada y totalmente automatizada para el proceso DecoJect. La tecnología aúna el moldeo por inyección y el granulado en molde (IMG), por lo que abre nuevas vías para la producción de componentes de alta calidad para el interior del automóvil. A diferencia de los procesos de decoración en molde (IMD) convencionales, en este caso la pintura no se transfiere simplemente de la lámina al componente, sino que la lámina se troquela y queda fijada en el componente. De esta forma, además del color y el estampado, entran en juego también la estructura de la superficie y las propiedades táctiles. Al mismo tiempo, aumenta la resistencia a los arañazos de las superficies. "DecoJect constituye una forma extremadamente rentable, incluso para lotes pequeños, de mejorar estéticamente las piezas moldeadas por inyección y de armonizar las superficies en el interior del vehículo", destaca Larry Alvey, director de la unidad de negocio de automoción de Engel en Norteamérica.
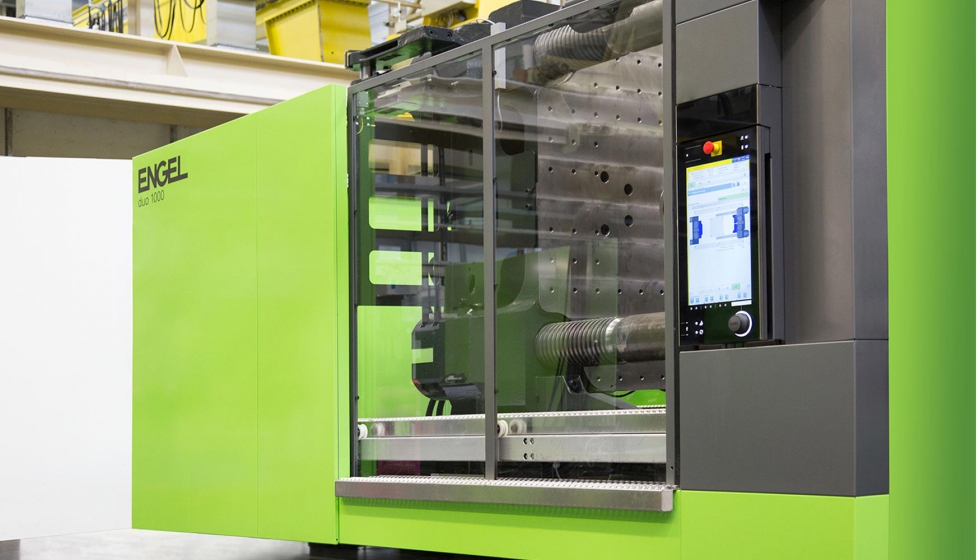
[
En la NPE se utiliza una máquina de moldeo por inyección duo 5160/1000 para fabricar paneles de puerta listos para montar. (Imagen: ENGEL)
Durante la NPE, Engel producirá paneles de puerta para automóviles en una máquina de moldeo por inyección duo 5160/1000, que presentan diferentes estructuras de superficie: desde un sofisticado graneado de cuero con costura hasta un moderno aspecto de carbono. Las láminas finas de DecoJect han sido desarrolladas por Benecke-Kaliko, miembro del grupo Continental con sede en Hanóver, Alemania.
Para iniciar el proceso, la lámina se introduce desde el rodillo al molde abierto, se calienta con un radiador de infrarrojos ubicado en la pinza del robot y se preforma directamente en el molde con ayuda de un sistema de vacío. Inmediatamente después, se inyecta polipropileno sobre el reverso de la lámina y se troquela antes de que el robot retire el componente y lo transfiera a la estación láser integrada para el corte de precisión. Cada 60 segundos sale un componente listo para montar de la célula de fabricación. Para cambiar de diseño solo hacen falta unos minutos para sustituir el rodillo, de modo que el tamaño del lote ya no repercute en los costos unitarios. Para ahorrar además materia prima, se emplea la tecnología de inyección de espuma MuCell de Trexel (Wilmington, MA, EE UU). Otras empresas asociadas que participan en el proyecto son Georg Kaufmann Formenbau (Suiza), Galvanoform Gesellschaft für Galvanoplastik (Alemania), HRSflow (Italia), ICO SYSTEM international coating (Alemania) y Borealis (Austria).
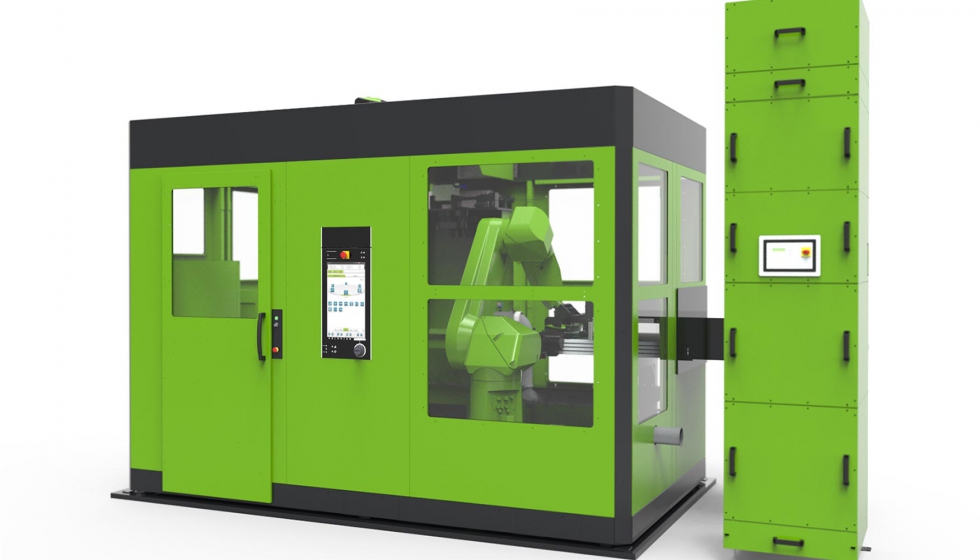
La unidad de automatización easiCell, desarrollada por ENGEL, hace que la célula completa sea muy compacta. Para el proceso DecoJect, la easiCell integra un robot easix y una estación láser. (Imagen: ENGEL)
Con su gran competencia en automatización, Engel contribuye significativamente a la rentabilidad y la flexibilidad del proceso. Un robot lineal Engel viper se encarga de calentar las láminas y de retirar los componentes del molde. Asimismo, junto con la estación láser, que somete las láminas al corte de precisión, un robot multieje Engel easix está integrado en una easiCell ubicada justo al lado de la unidad de cierre de la máquina de moldeo por inyección. El diseño estandarizado y modular de la célula de automatización desarrollada por Engel permite la integración extremadamente compacta de robots y unidades de procesamiento, tanto anteriores como posteriores, a la fase de moldeo por inyección. Además, reduce notablemente la complejidad de la aplicación. Todo el proceso se puede controlar mediante el mando CC300 de la máquina de moldeo por inyección. La lógica de manejo uniforme para todos los componentes de la célula de fabricación hace que los operadores de las máquinas puedan controlar el proceso integrado con facilidad, incluso sin formación específica.
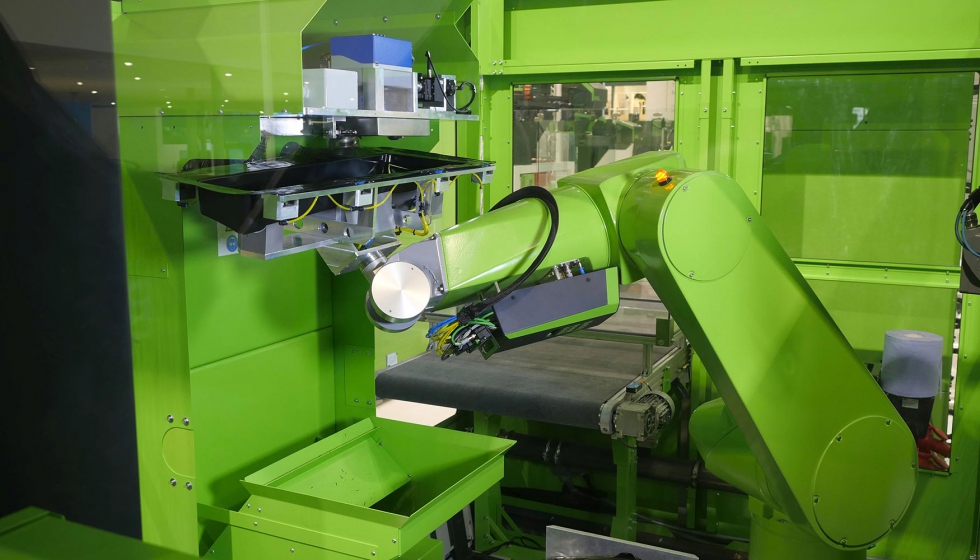
El robot multieje easix conduce el contorno del componente a lo largo del láser y seguidamente coloca el panel de puerta listo para montar en la cinta transportadora. (Imagen: ENGEL
Medicina: cepillos interdentales en un proceso de una sola inyección
Con un grado altísimo de integración, también destaca la aplicación para el sector sanitario presentada en Orlando. En la versión para salas limpias de una máquina de moldeo por inyección totalmente eléctrica e-motion 170/110 T se fabricarán cepillos interdentales del tipo "scrub!", desarrollados por pheneo (Alemania). Mediante el moldeo por inyección de un solo componente, se pueden producir directamente hasta 500 cerdas con la varilla y el mango. El molde de precisión de alto rendimiento, provisto de ocho cavidades y extremadamente delicado en la zona de las cerdas, es de Hack Formenbau (Alemania), mientras que Hekuma, también de Alemania, es responsable de la automatización. En la feria se presentará una célula de fabricación totalmente automatizada con el diseño modular HEKUflex de Hekuma.
Inmediatamente después del moldeo por inyección, las piezas son revisadas por una cámara y embaladas en bolsas para la venta de 16 unidades cada una. De la célula de producción sale una bolsa cada cuatro segundos. "El proceso de fabricación totalmente integrado y el diseño de un solo componente nos permiten multiplicar la eficiencia de los productos y procesos establecidos en el mercado", señala Jon Kelm, director de las unidades de negocio de medicina y embalaje de Engel en Norteamérica. "Normalmente, los cepillos interdentales constan de tres componentes: el mango, una malla metálica y los filamentos, que suelen fabricarse en procesos independientes entre sí. Nuestra solución permite suprimir fases de trabajo enteras y, además, reducir la logística".
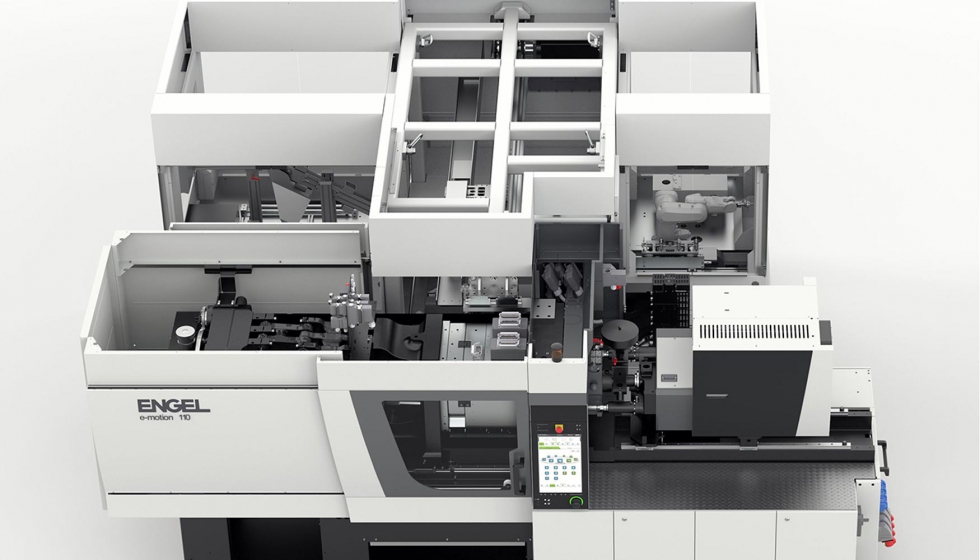
En su stand de la feria, Engel fabrica cepillos interdentales de forma completamente automatizada en una máquina de moldeo por inyección totalmente eléctrica e-motion 170/110 T. (Imagen: ENGEL)

La tecnología de fabricación desarrollada por ENGEL juntamente con Hack Formenbau y Hekuma permite moldear hasta 500 cerdas en un proceso de un solo componente. (Imágenes: ENGEL)
Llenar completamente ocho cavidades con estructuras extremadamente delicadas y con un peso total de inyección de tan solo 1,93 gramos plantea exigencias muy elevadas no solo para el molde, sino también con relación a la precisión y la constancia de la máquina de moldeo por inyección. Para ello Engel tiene dos respuestas: por un lado, la máquina de moldeo por inyección de alto rendimiento completamente eléctrica e-motion y, por el otro, inject 4.0. Bajo el concepto general inject 4.0, Engel aglutina productos de software para la digitalización y la interconexión de los procesos de fabricación, como los sistemas de asistencia inteligentes de la familia de productos iQ, que detectan y compensan automáticamente las fluctuaciones en las condiciones del entorno y en la materia prima, antes de que produzcan piezas defectuosas. En el mando CC300 de la máquina e-motion, los visitantes de la NPE pueden seguir en vivo cómo iQ weight control analiza la evolución de la presión en relación con la posición del husillo durante la inyección y ajusta tanto el punto de conmutación como el perfil de inyección y la presión mantenida a las condiciones actuales, inyección a inyección.
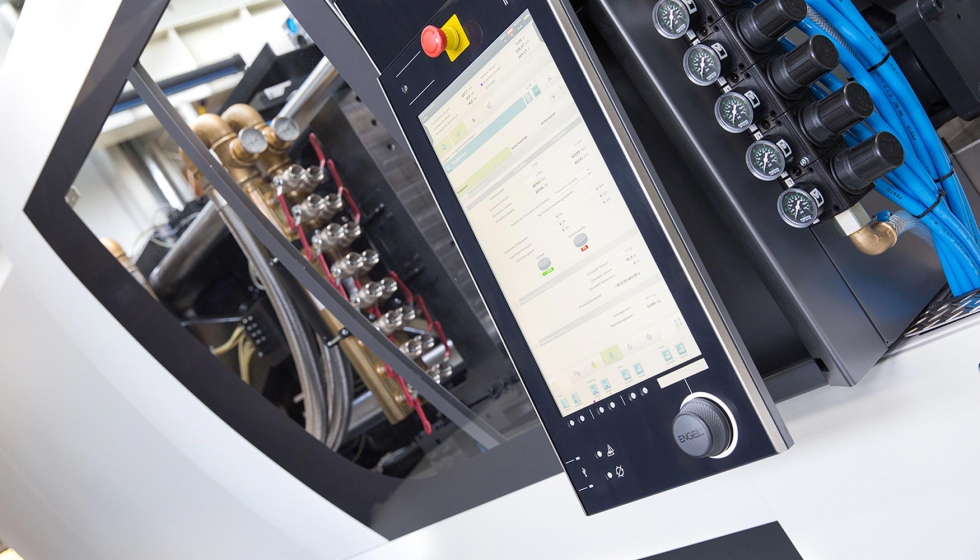
Los sistemas de asistencia iQ integrados en el mando CC300 de la máquina de moldeo por inyección e-motion compensan las fluctuaciones del proceso en línea. (Imagen: ENGEL)
Paralelamente, iQ clamp control calcula la fuerza de cierre óptima para el proceso y la ajusta automáticamente a partir de la respiración del molde. Como tercer sistema de asistencia, iQ flow control regula las diferencias de temperatura en los distintos circuitos distribuidores del molde, así como la potencia de las bombas en los atemperadores, para asegurar una atemperación constante y reducir el consumo de energía. «Con los sistemas de asistencia inteligentes, la máquina de moldeo por inyección se optimiza a sí misma continuamente», explica Kelm. «Así, incluso los operadores de las máquinas con poca experiencia pueden obtener resultados óptimos».
Teletrónica: la integración consecuente de procesos aumenta la competitividad
En la industria de la teletrónica, la integración de procesos a menudo gira en torno a los componentes compuestos de plástico y metal. Engel también ofrece soluciones específicas para este desafío, tal y como el fabricante de máquinas demuestra en la NPE con la fabricación de carcasas de interruptores térmicos. Desde el troquelado de los contactos hasta la inspección y la rotulación de los componentes electrónicos listos para usar, todas las fases de trabajo están completamente automatizadas. La materia prima de las placas de soporte de latón se conduce directamente desde el rodillo y se pretroquela en línea, incluida la extrusión de un agujero roscado. La rosca se moldea con un sistema servoeléctrico, antes de que las placas de soporte, que todavía se encuentran en la cinta, se sobremoldeen con poliamida reforzada con fibras de vidrio en una máquina de moldeo por inyección vertical ENGEL insert 60V/35 single. El control de calidad también se lleva a cabo en línea. Para ello, además de la inspección por cámara, el molde progresivo lleva integrado un control de alta tensión, el cual garantiza una prueba de cortocircuito del cien por cien durante la producción. Para garantizar una trazabilidad completa, las piezas buenas se marcan con un láser antes de que se retiren los distribuidores de colada y subdistribuidores y se separen de la cinta las piezas acabadas. Cada 20 segundos salen de la célula de fabricación ocho piezas listas para ser instaladas.
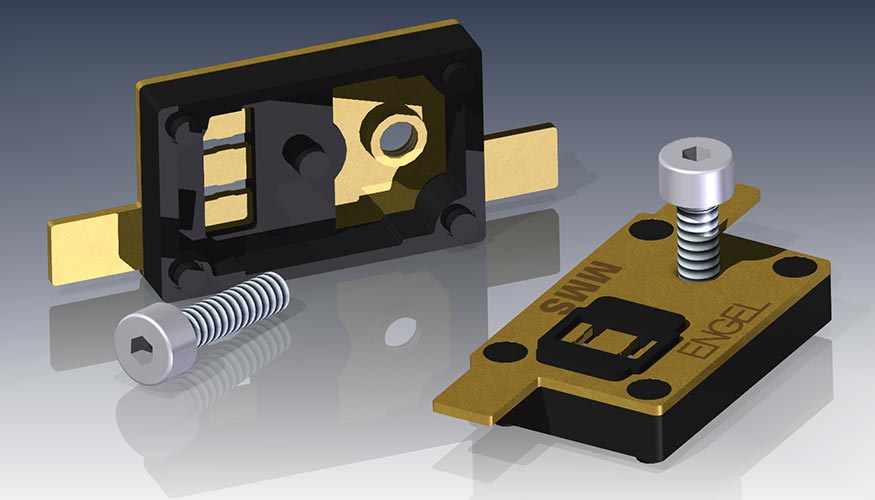
[
Engel integra las numerosas fases de trabajo que implica la fabricación de cajas de interruptores térmicos en un solo proceso global claro. (Imagen: MMS)
La solución de fabricación creada por Engel juntamente con su socio MMS Modular Molding Systems (Austria) garantiza costos unitarios mínimos y, además, consigue una gran flexibilidad. Gracias al diseño modular de los sistemas MMS, es posible integrar módulos de mecanizado adicionales, por ejemplo, para soldadura por resistencia, soldadura láser, remachado, montaje o limpieza de los componentes. "Independientemente de la cantidad de módulos, todo el proceso se puede visualizar y controlar a través del mando CC300 de la máquina insert", afirma Stefan Aberl, director de automatización de Engel Norteamérica. "Esto reduce la complejidad y simplifica considerablemente el manejo del conjunto del proceso".
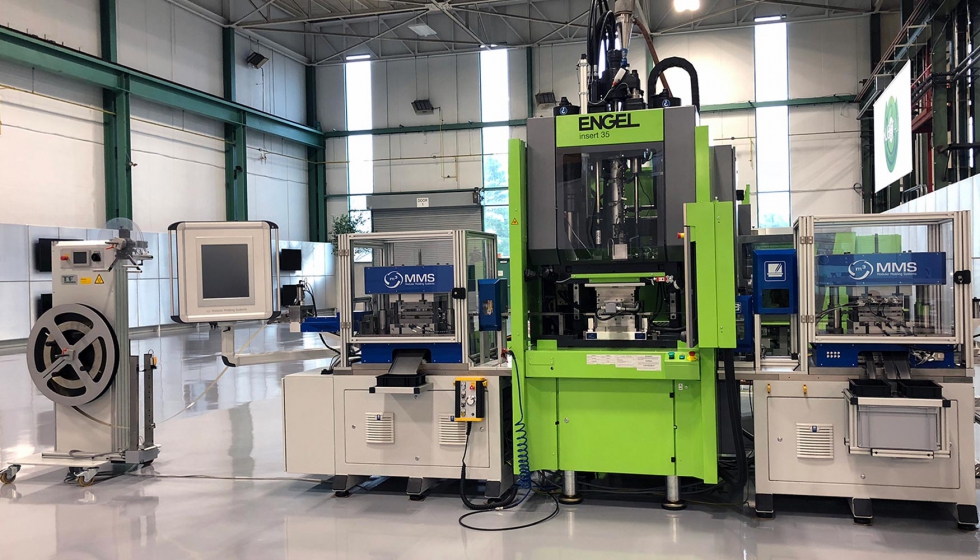
[
El proceso totalmente integrado hace que la fabricación de cajas de interruptores térmicos sea especialmente rentable. Antes del proceso de moldeo por inyección hay un mecanismo para desenrollar las cintas, un módulo de prensado y un módulo de mecanizado para moldear una rosca; después vienen los controles de calidad, la rotulación con láser y otro módulo de prensado. (Imagen: Engel)
El proceso de producción de los interruptores térmicos, por ejemplo los que se usan para el monitoreo de los motores eléctricos de los automóviles o en el sector de los electrodomésticos, ha sido tradicionalmente complejo y ha constado de varias fases. Normalmente, el troquelado y el sobremoldeo de los componentes de metal tienen lugar incluso en ubicaciones distintas. Esto no solo supone un esfuerzo logístico considerable, sino también una gran cantidad de material, ya que hay que llevar a cabo dos procesos independientes. Todo ello genera costos importantes, sobre todo cuando se emplean metales no ferrosos.
Embalaje: máxima eficiencia de producción
Máxima eficiencia con la mejor calidad y los tiempos de ciclo más breves: este es el desafío al que se enfrentan los fabricantes de tapones de bebidas a diario. En la NPE, Engel presenta una solución innovadora para la fabricación de tapones de 26 mm con precinto de seguridad de HDPE. Durante los cinco días de la feria, la célula de fabricación funciona con un tiempo de ciclo de aproximadamente 2 segundos en condiciones de producción reales, y se distingue además por una extraordinaria eficiencia energética y la máxima constancia de proceso.
El corazón de la solución de sistema totalmente integrada es una máquina de moldeo por inyección e-cap 2440/420 US totalmente eléctrica, equipada con un molde de 96 cavidades de z-moulds (Austria). Engel integra en periféricos un sistema de aire seco de Eisbär Trockentechnik (Austria), así como un sistema de inspección óptico de Intravis (Alemania) en el conjunto de la instalación.
Para combinar un consumo energético mínimo con una constancia de proceso y precisión extraordinarias, Engel apuesta por máquinas de alto rendimiento totalmente eléctricas de la serie e-cap para la fabricación de tapones, una serie que ha sido desarrollada específicamente para este segmento de mercado. Con sus potentes servoaccionamientos directos, las máquinas e-cap aseguran la capacidad de plastificación necesaria y el máximo porcentaje de piezas buenas, incluso empleando materiales de HDPE de alta resistencia, con un MFI claramente por debajo de 2 o incluso de 1 g/10 min. "Geométricamente, los tapones de bebidas han alcanzado su mínimo de ligereza", explica el experto en embalaje, Jon Kelm. "Así, los requisitos en términos de precisión y repetibilidad de las máquinas de moldeo por inyección son más elevados que nunca". A pesar de su excelente rendimiento, la e-cap consume muy poca energía y agua refrigerante incluso en funcionamiento rápido. La mayor fuerza del expulsor y el accionamiento de cierre reforzado aseguran tiempos de ciclo muy cortos.
Máximo rendimiento para recipientes de pared delgada
En total, Engel packaging está representada con dos células de fabricación integradas en la NPE2018. Campetella Robotic Center, de Italia, fabrica vasos para aerolíneas en su stand de la feria (pabellón sur, stand S27009) con tecnología de pared delgada en una máquina de moldeo por inyección EngelL e-motion 740/240 T US totalmente eléctrica, en un molde de Fostag (Suiza). Los vasos se sacan del molde con ayuda de una automatización de alta velocidad y se envasan inmediatamente después del moldeo por inyección.
Con tiempos de ciclo muy por debajo de los 3 segundos y velocidades de inyección de más de 500 mm por segundo, las máquinas de moldeo por inyección totalmente eléctricas de la serie e-motion se utilizan cada vez más para la fabricación de recipientes de pared delgada. El sistema cerrado para rodilleras y husillos garantiza una lubricación óptima y limpia de todos los componentes móviles de la máquina en todo momento, y cumple los estrictos requisitos de higiene de la industria alimentaria.
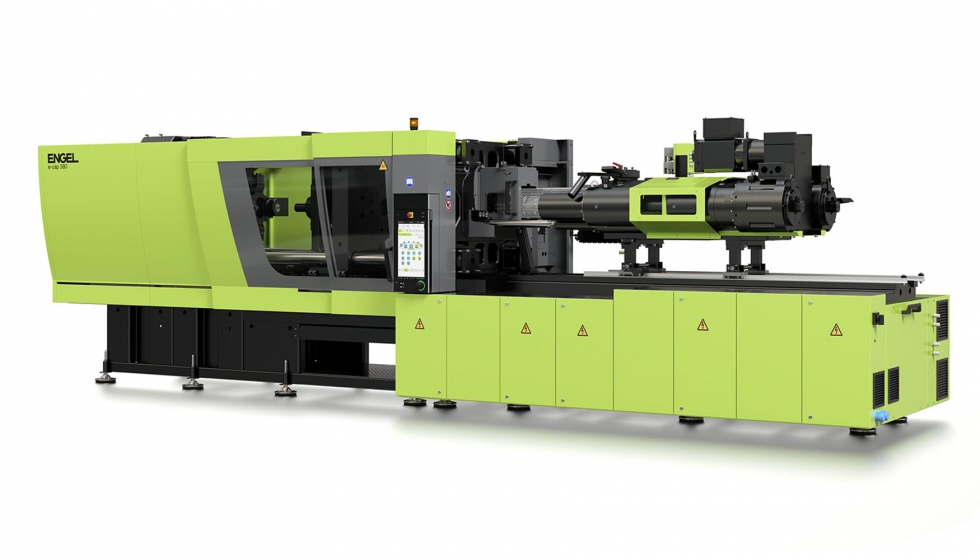
Máximo rendimiento con un consumo de energía mínimo: durante la NPE, una máquina de moldeo por inyección totalmente eléctrica e-cap 420 produce tapones de 26 mm con precinto de seguridad con un molde de 96 cavidades, con un tiempo de ciclo de aproximadamente 2 segundos. (Imagen: Engel)
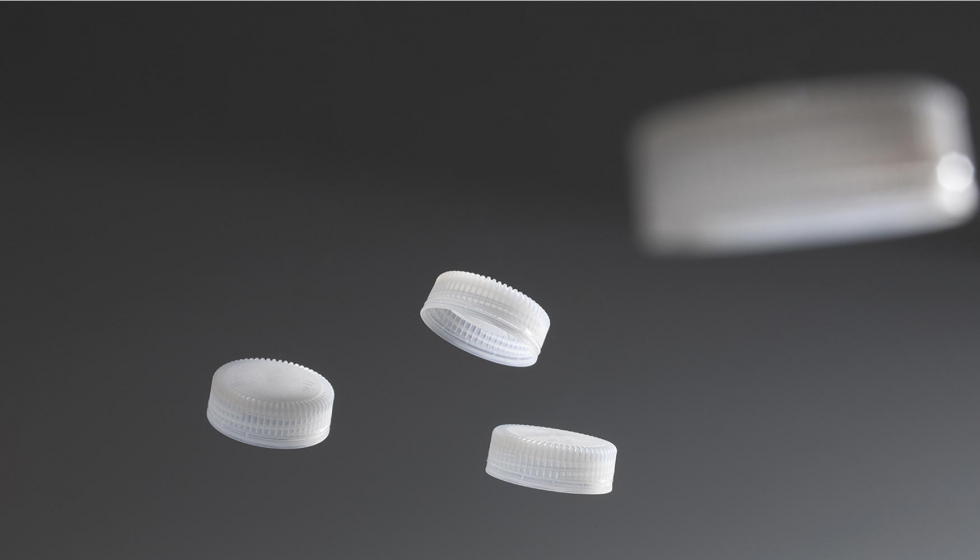
Geométricamente, los tapones de bebidas han alcanzado su mínimo de ligereza, por lo que los requisitos en términos de precisión y repetibilidad de las máquinas de moldeo por inyección son más elevados que nunca. (Imagen: ENGEL)
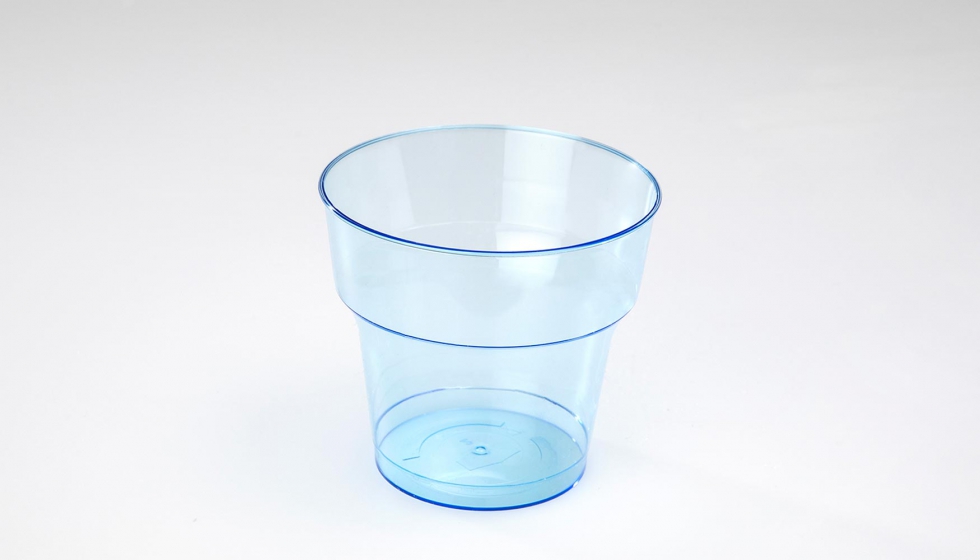
Campetella Robotic Center, de Italia, fabrica vasos para aerolíneas en su stand de la feria con tecnología de pared delgada en una máquina de moldeo por inyección ENGEL e-motion 740/240 T US totalmente eléctrica. (Imagen: ENGEL)
Moldeo técnico: lentes LED sofisticadas de silicona líquida
El espacio de exposición de moldeo técnico de Engel en la NPE2018 se centra en el sofisticado procesamiento de la silicona líquida (LSR). En una máquina de moldeo por inyección e-victory 310/120 US, con un robot lineal viper 40 integrado, se producen lentes para focos LED en un molde de dos cavidades de ACH solution (Austria). Los componentes representan un amplio abanico de aplicaciones. Desde sistemas de iluminación para automóviles hasta el alumbrado público o la iluminación de edificios, la LSR cobra cada vez más importancia en la fabricación de sistemas de iluminación LED de alta calidad.
Todo ello se debe a sus propiedades especiales. La LSR altamente transparente presenta un índice de amarilleamiento inferior a los materiales de lentes convencionales, es resistente a los rayos UV y es estable en un amplio rango de temperaturas de entre -20 y +150 °C. Asimismo, permite reproducir incluso geometrías de lentes complejas de forma eficiente y reproducible en el moldeo por inyección.
Engel tiene una gran experiencia a nivel mundial con proyectos con LSR en sectores muy diversos, de modo que es uno de los socios favoritos del sector de la iluminación en la introducción al mercado del nuevo material para lentes. Engel presenta la producción de lentes de LSR en una feria por primera vez.
"Los requisitos indispensables para fabricar productos sofisticados de silicona líquida de forma rentable son unos procesos automatizados y una elevada precisión y estabilidad del proceso de moldeo por inyección", señala Steve Broadbent, responsable de los proyectos con elastómeros en la tecnología de aplicación de Engel en Norteamérica. "Gracias a su unidad de cierre sin columnas, la máquina e-victory con unidad de inyección eléctrica es idónea para ello". El acceso libre a la zona del molde simplifica la preparación y hace que la célula de fabricación sea compacta. Las platinas de montaje pueden aprovecharse al máximo hasta el borde, de modo que el molde para lentes, bastante voluminoso a causa de la compleja estructura de los componentes, cabe en una máquina de moldeo por inyección relativamente pequeña de 120 toneladas. Además, el robot puede acceder a la cavidad directamente desde el lateral sin tener que salvar obstáculos, de modo que necesita poco espacio por arriba.
Las máquinas de moldeo por inyección sin columnas deEngel destacan por el excelente paralelismo de las platinas de montaje. El divisor de fuerza patentado Force Divider asegura que la platina móvil siga el molde de forma exacta durante la formación de la fuerza de cierre y que la fuerza aplicada se distribuya de forma homogénea por toda la superficie. Esto evita eficazmente la formación de rebabas, incluso en el procesamiento de materiales de baja viscosidad como la LSR. Los componentes no necesitan ningún mecanizado posterior y están listos para usar directamente después del proceso de moldeo por inyección.
Engel ofrece esta solución de alta tecnología junto con su socio. ACH solution (Austria) ha desarrollado y construido tanto el molde como el equipo de dosificación; en el interior del molde está implantada la nueva regulación eléctrica de boquilla ServoShot.
Como proveedor de sistemas, Engel integra todos los componentes de la célula de fabricación en un único mando también en el procesamiento de LSR, de modo que todo el proceso se puede ajustar y controlar a través del panel de control de la máquina de moldeo por inyección, incluidos el robot y la dosificación de LSR.
Control seguro de los procesos con LSR con la tecnología sin columnas de Engel
La NPE2018 confirma una vez más el liderazgo de Engel y las máquinas sin columnas en el procesamiento de LSR. En la feria se presentan un total de cuatro aplicaciones de LSR con máquinas Engel, de las cuales tres con máquinas sin columnas. En Wacker Silicones (con planta matriz en Alemania), en el pabellón sur, stand S24179, se fabrican salvamanteles en una victory 200/120 hidráulica, en un molde de 4 cavidades. Otra aplicación sin columnas tiene lugar en una victory 200/55 en el stand del fabricante de moldes Burteck de Windsor, CT, EE UU: pabellón sur, stand S30045. Asimismo, en el pabellón sur, stand S20125, Shin-Etsu Silicones de Akron, Ohio, produce lentes para gafas de una LSR óptica en una e-mac 170/55 totalmente eléctrica, en un molde de Roembke, de Ossian, Indiana.
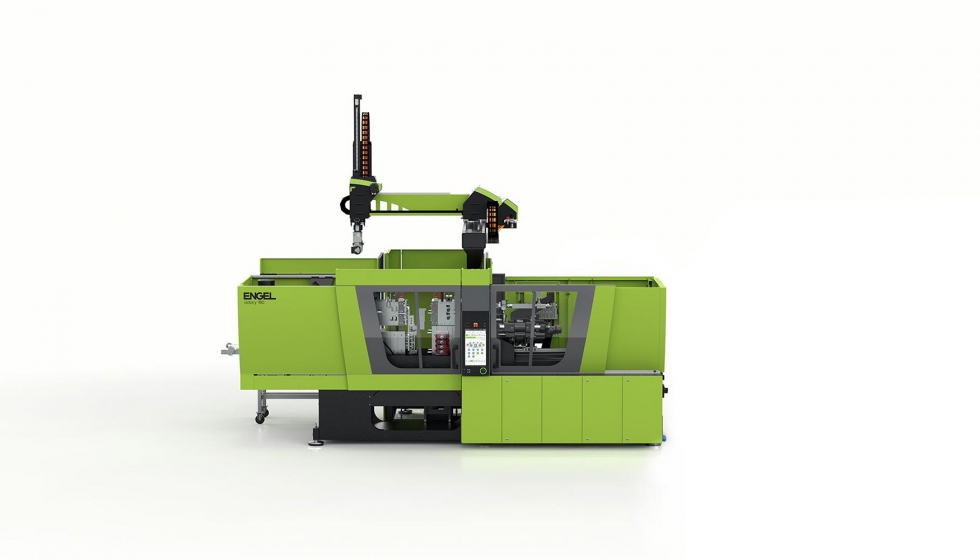
[
Gracias a su unidad de cierre sin barreras, la máquina de moldeo por inyección sin columnas e-victory ofrece un gran potencial de eficiencia en el procesamiento de silicona líquida. (Imagen: ENGEL)

[
Engel ofrece la célula de fabricación para la producción de lentes LED junto con su socio, ACH solution. Es la primera vez que ACH solution presenta su nueva unidad de dosificación, ACH MaxiMix, en Norteamérica. (Imagen: ACH solution)
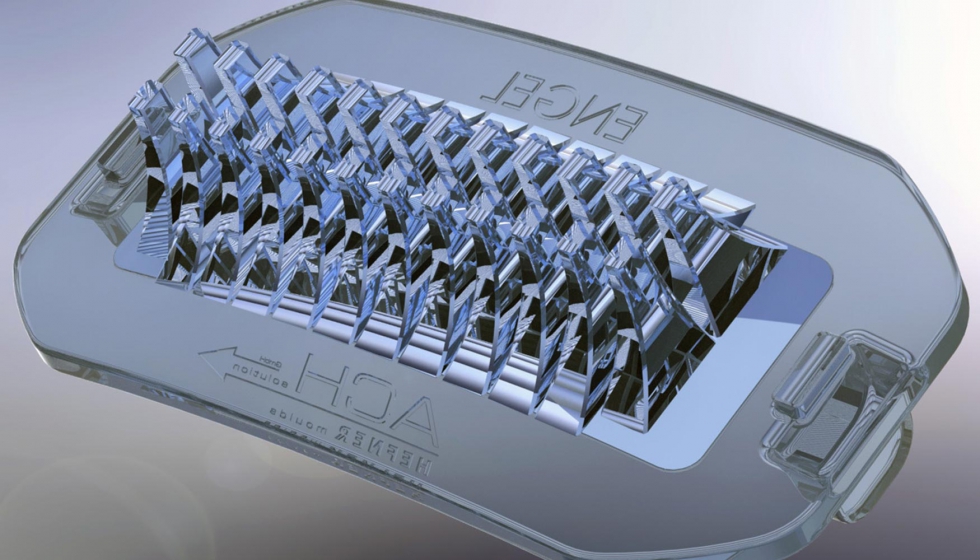
[
Con su compleja estructura, las lentes LED de silicona requieren una elevada precisión del proceso de moldeo por inyección. En la NPE, Engel presenta la fabricación de lentes en una feria por primera vez. Se utiliza una máquina de moldeo por inyección sin columnas e-victory. (Imagen: ACH solution)