El lema ‘Wir sin da’ (“estamos allí”) pone de manifiesto uno de los puntos fuertes de Arburg: acompañar al cliente
Los Días Tecnológicos de Arburg tiñen de verde la Selva Negra
Cerca de siete mil visitantes de 53 países. 50 máquinas y aplicaciones en funcionamiento. Estas cifras que fácilmente podrían referirse a un salón del sector del plástico, son el resultado de los Días Tecnológicos de Arburg que celebra en su sede alemana de Lossburg, en la que es ya una cita ineludible del sector que se celebra desde 1999. Aplicaciones de la Industria 4.0, de la fabricación ligera o la fabricación aditiva, máquinas de inyección trabajando simultáneamente con Freeformer o curiosas aplicaciones llave en mano, vistieron la fábrica del 15 al 18 de marzo.
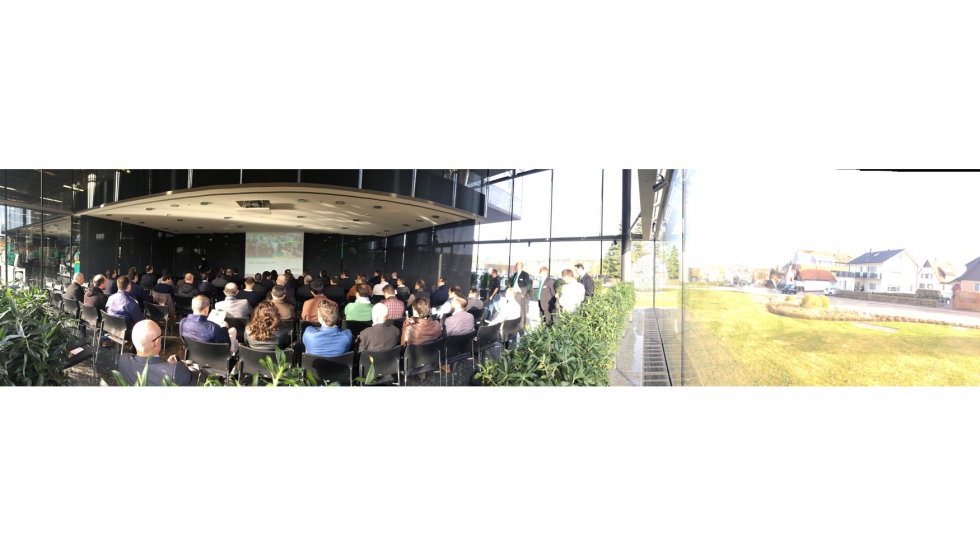
Nada más llegar a la sede de Arburg ubicada en el privilegiado entorno de la Selva Negra alemana llama la atención el nuevo y espectacular aparcamiento que la firma familiar ha creado para sus empleados. El diseño de la construcción, que trató de minimizar su impacto con la naturaleza, le hizo merecedor del premio a la ‘Construcción ejemplar’ del la Cámara de Arquitectos de Baden-Württemberg.
Una vez dentro de las instalaciones sorprendió a cerca de los sesenta clientes procedentes de España y Portugal– grupo patronado por la filial de Arburg España–, todo el espectro de máquinas Allrounder y Freeformer funcionando a pleno rendimiento en los más de 171.000 metros cuadrados de su sede central.
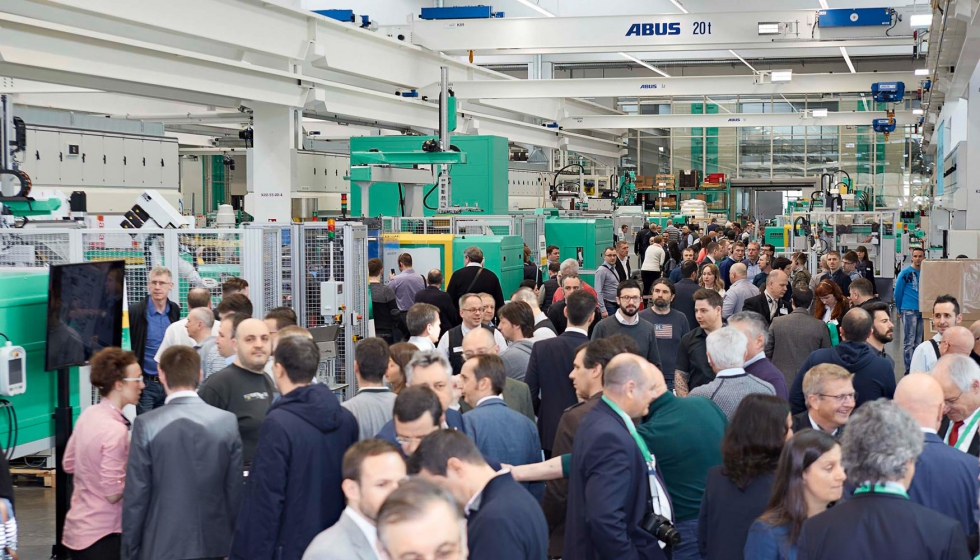
Los visitantes pudieron acceder a las diferentes áreas de exposición: el Efficiency Arena bajo el lema Industria 4.0 en la práctica, soluciones de moldeo por inyección llave en mano, el nuevo Centro de Prototipos Arburg para la fabricación de aditiva con el Freeformer, así como un área especial de servicio.
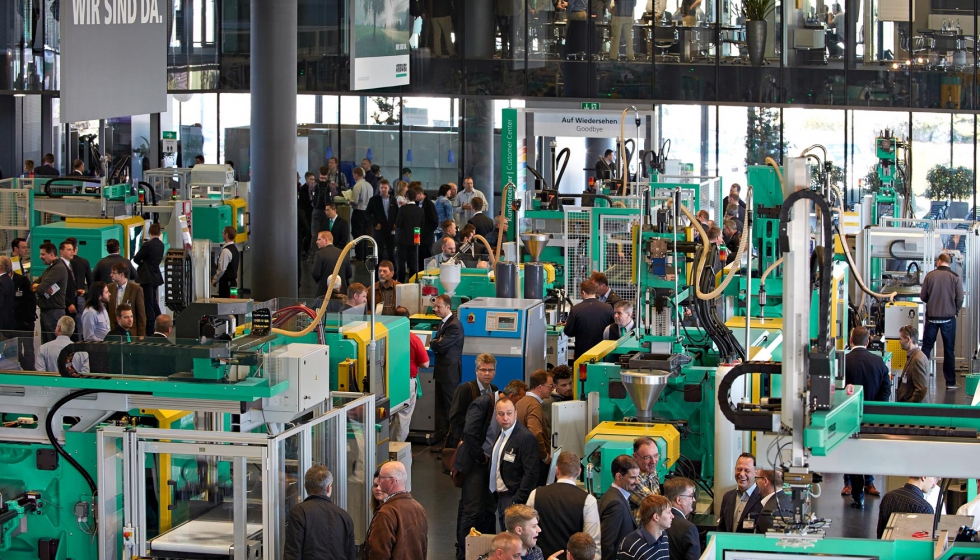
Allrounder, a lo grande
Una de las máquinas que llamaron más la atención del público y no sólo por su excepcional tamaño fue la inyectora Allrounder 1120 H híbrida con una fuerza de cierre de 6.500 kN, con un nuevo diseño y una nueva unidad de mando Gestica, que pudieron ver por primera vez en la pasada edición de la K.
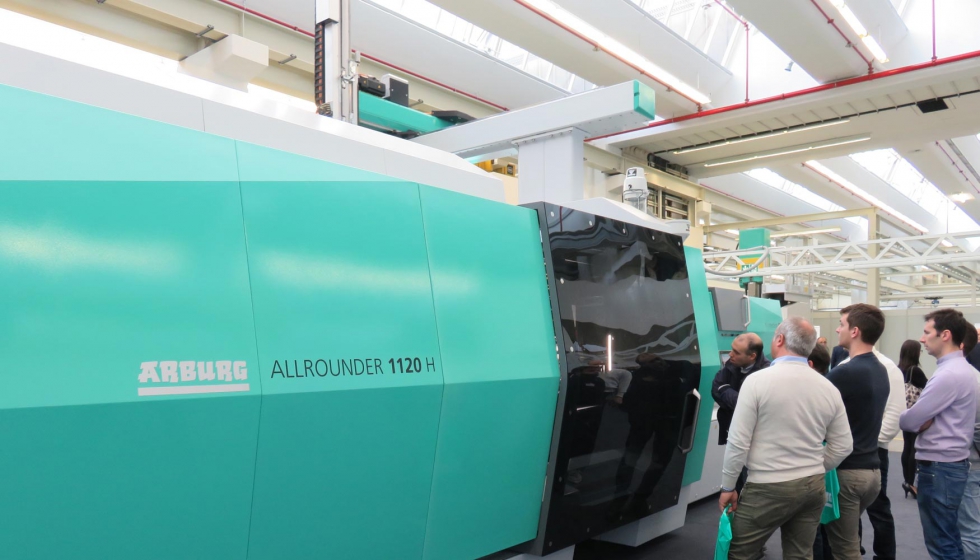
Allrounder 1120 H, nuevo tamaño, nueva unidad de mando, nuevo diseño.
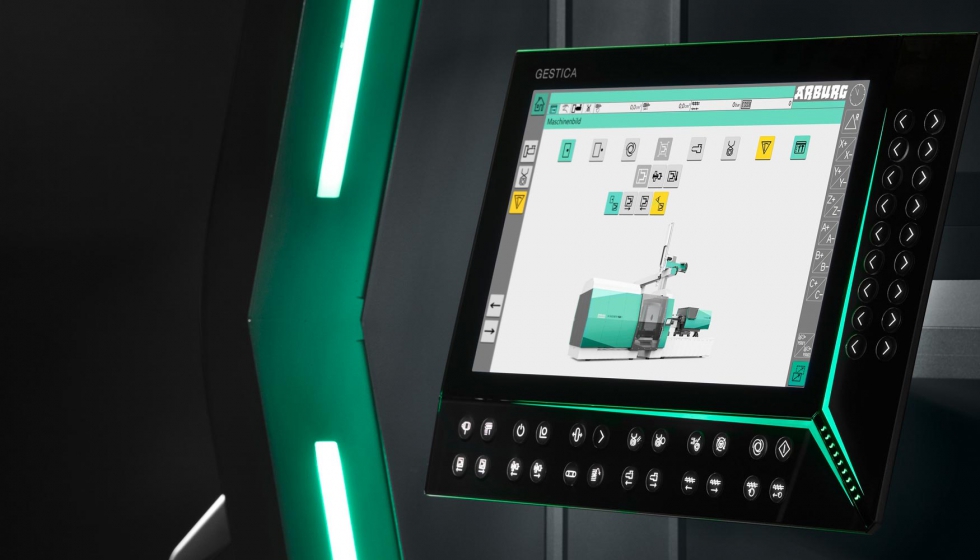
El manejo es muy sencillo e intuitivo. El panel de control puede girarse, regularse en altura y posee una técnica LED de colores variables.
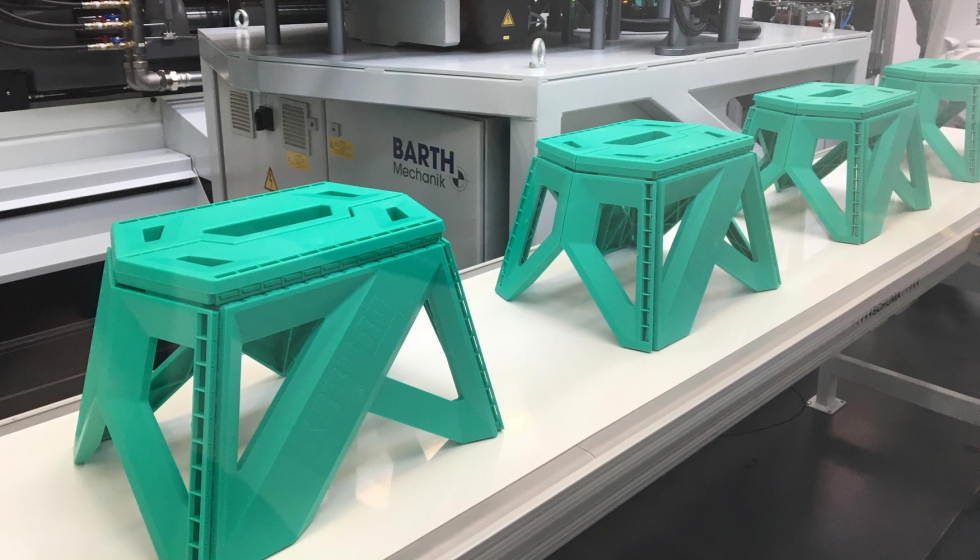
Taburete plegable funcional en u solo paso y un peso de 1080 gramos. Las ocho piezas que lo componen se crean en un tiempo de ciclo de aproximadamente 60 segundos: cuatro piezas en la mitad superior del conjunto de moldes y cuatro en la mitad inferior. Al abrirse el molde se desmoldean los 8 destalonados mediante correderas de arrastre.
Aparte de su porte, con un diseño totalmente novedoso, la máquina destacó por el interés que mostraron algunos visitantes para conseguir una de las espectaculares piezas que inyectaba: taburetes plegables listos para usar. Estaban formados por ocho piezas individuales que eran moldeadas en un molde de ocho toneladas con un tiempo de ciclo de alrededor de 60 segundos. Las piezas se montaban, dejando el producto listo para usar, en un conjunto formado por un robot Multilift V 40 de seis ejes y una estación de montaje.
Inyectoras y Freeformers trabajando conjuntamente
El Efficiency Arena también fue uno de los espacios más transitados. Aquí, Arburg y una serie de socios de la firma alemana mostraron ejemplos prácticos de la implementación de la Industria 4.0 para lograr producciones más eficientes.
Un ejemplo fue la producción de etiquetas de equipaje inteligentes en lotes de una sola unidad. Para esta finalidad se combinaron una inyectora Allrounder y dos Freeformers para fabricación aditiva. El sistema de ordenador central (ALS) de Arburg garantizaba la trazabilidad de principio a fin para cada pieza. También se presentaron dos módulos complementarios ALS: Energy Visualization, para la asignación basada en órdenes de datos de energía y Material Staging Interface para cambios de lotes.
Otros temas tratados en el Efficiency Arena fueron la trazabilidad desde la pieza terminada hasta el granulado original, la monitorización online para asegurar la calidad, los registros sistemáticos de consumo de energía y la integración de equipos periféricos en el sistema de control de máquina Selogica.
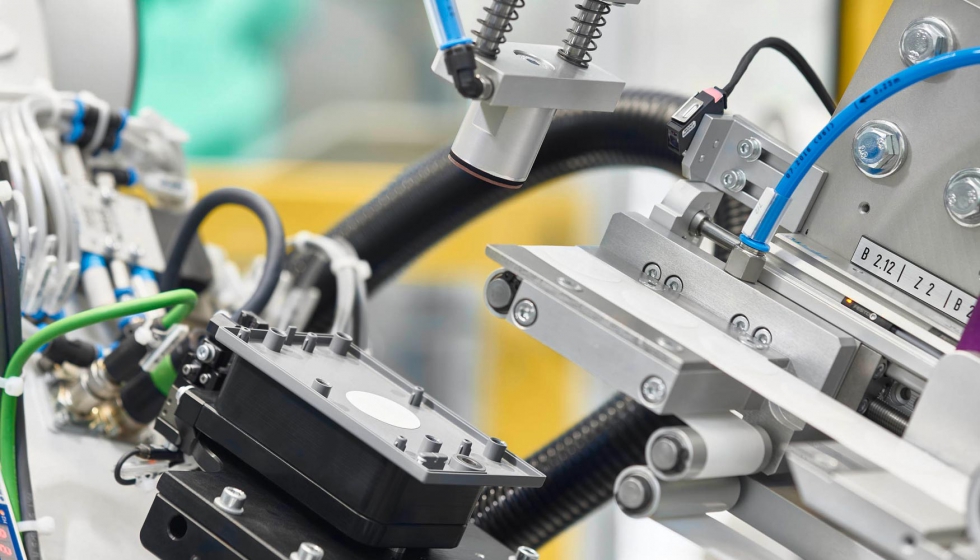
Más que inyección: ocho Freeformers en acción
La visita incluyó un total de ocho exposiciones de fabricación aditiva relacionadas con Arburg Plastic Freeforming (APF), cinco de ellas en el nuevo Arburg Prototyping Center.
El foco de atención se centraba en la fabricación aditiva de piezas finales funcionales, tanto de forma individual como en lotes pequeños (pinzas hechas de PA y TPE, cubiertas de teléfonos móviles con superficies optimizadas y piezas hechas de un PC aprobado para uso en la industria aeroespacial). Además, se presentaron piezas electrónicas a prueba de llama e implantes de PLA de grado médico.
Otra máquina Freeformer ubicada en el Customer Center produjo poleas de cuerda optimizadas mecánicamente a partir de poliamida orgánica. A todo ello hay que sumar los Freeformers mencionados del Efficiency Arena para la individualización de las etiquetas de equipaje inteligentes.
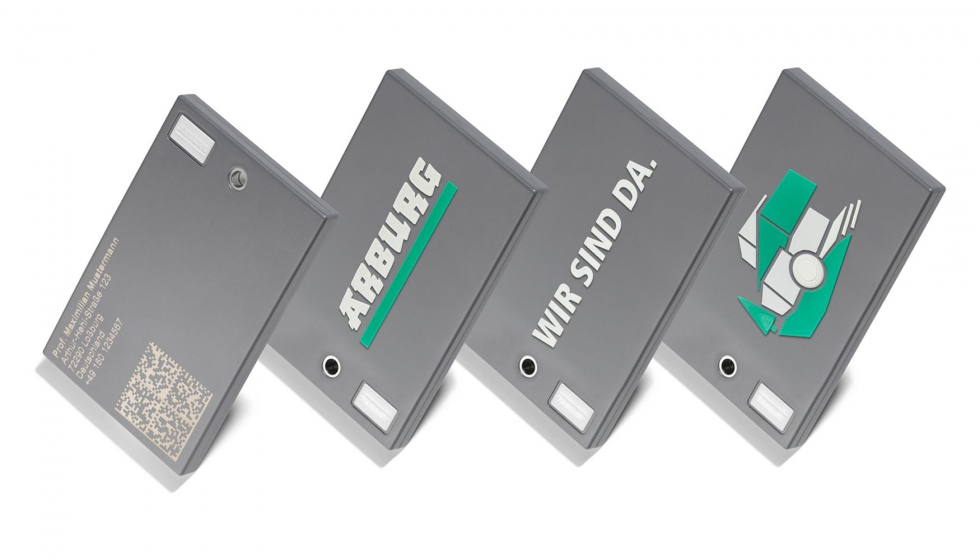
Otras aplicaciones
La amplia gama de inyectoras incluyó soluciones para diversas aplicaciones. Así, por ejemplo, en el área de tecnología médica, Arburg mostró cinco aplicaciones y diferentes conceptos de salas blancas, incluyendo una Allrounder 370 A eléctrica de acero inoxidable compatible con GMP que inyectaba implantes PEEK de alta calidad en un ambiente de sala limpia.
La capacidad de rendimiento de la serie Hidrive para la industria del packaging fue demostrada por una Allrounder 570 H en una versión especialmente configurada para piezas de pared delgada. La máquina producía cuatro botes de PP con IML en un tiempo de ciclo de menos de dos segundos.
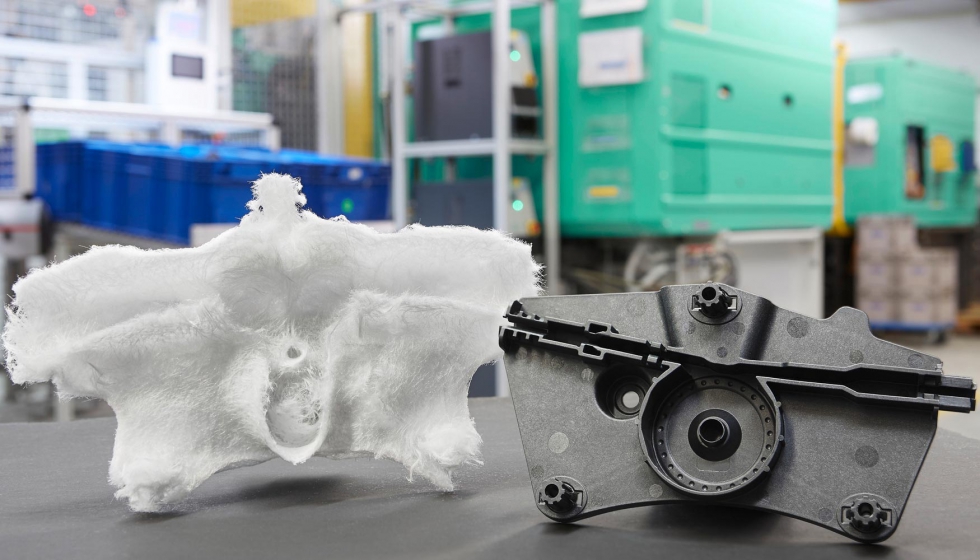
Otra de las novedades que pudieron verse fue la inyectora Allrounder Cube para aplicaciones de ciclo rápido con técnica de cubos. Las máquinas especiales de dos componentes están disponibles en los tamaños Cube 2900 y Cube 4600. Gracias a los tiempos de marcha en vacío más cortos, con las nuevas máquinas de moldes cúbicos pueden reducirse los tiempos de ciclo en hasta u segundo y aumentar la tasa de producción en un 10%.
Arburg también presentó soluciones de Fiber Direct Compounding (FDC) y Profoam, tecnología de espumado físico en dos aplicaciones de automoción. Además de reducir el peso, estos procesos también se pueden utilizar específicamente para mejorar las características mecánicas de las piezas y para minimizar la distorsión, como se demostró con una carcasa de transmisión de cables reforzada con fibra de vidrio para ventanas eléctricas y una placa base de espuma.
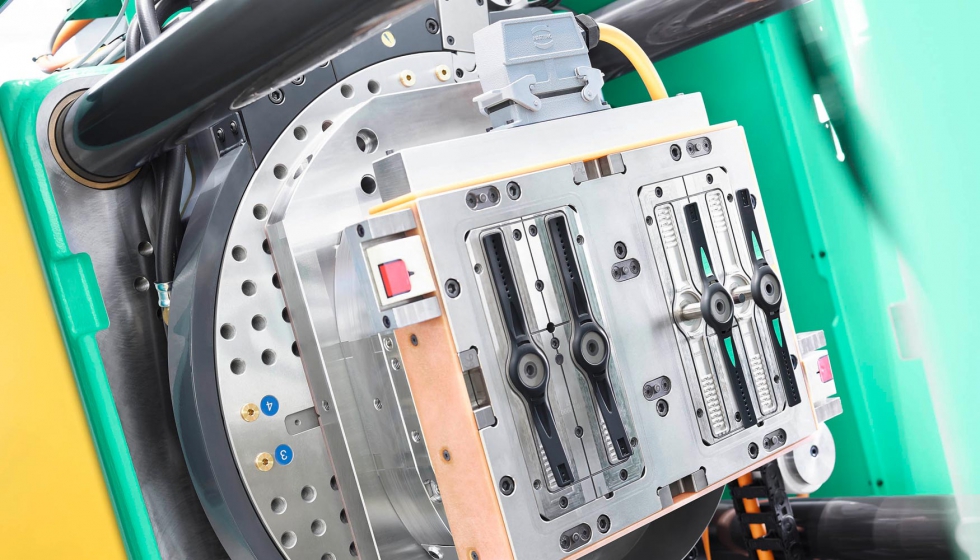
Relojes en silicona líquida
Si bien en la pasada edición de la K llamaron la atención, durante los Días Tecnológicos el interés no fue menor. Los relojes de pulsera LSR / LSR requerían complejos procesos de fabricación y establecían el estándar para lo que actualmente se puede lograr en el procesamiento de silicona líquida. El sistema llave en mano asociado, basado en una inyectora eléctrica bicomponente, Allrounder 570 A, produjo pulseras LSR de dos colores de forma totalmente automática. El montaje del reloj de pulsera listo para usar tenía lugar dentro del ciclo de moldeo por inyección.
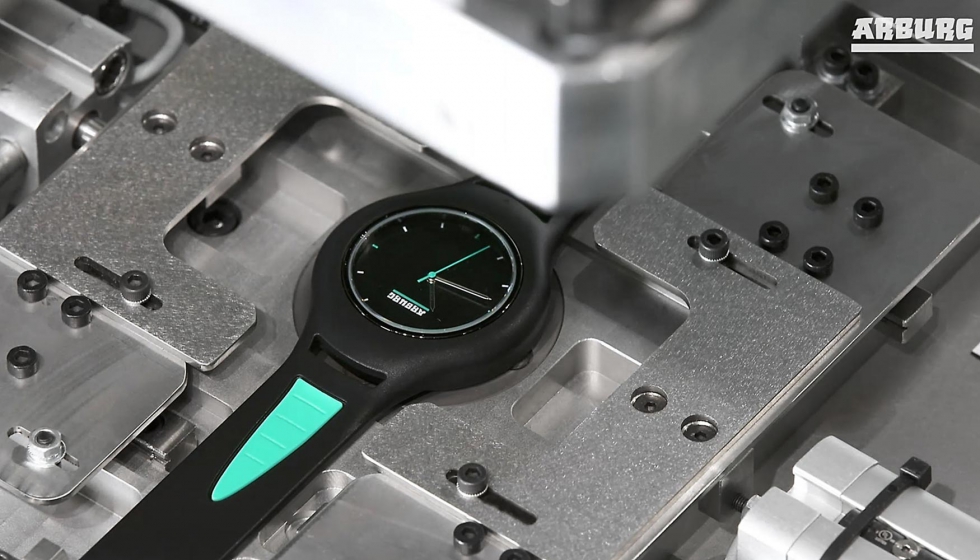
Un punto culminante en el área de moldeo por inyección de polvo fue el primer marco MIM del mundo para teléfonos inteligentes. Una Allrounder 470 C Golden Edition hidráulica procesó materia prima de BASF para producir un compacto verde de Arburg con un espesor de sólo 1 milímetro y una longitud de 136 milímetros.
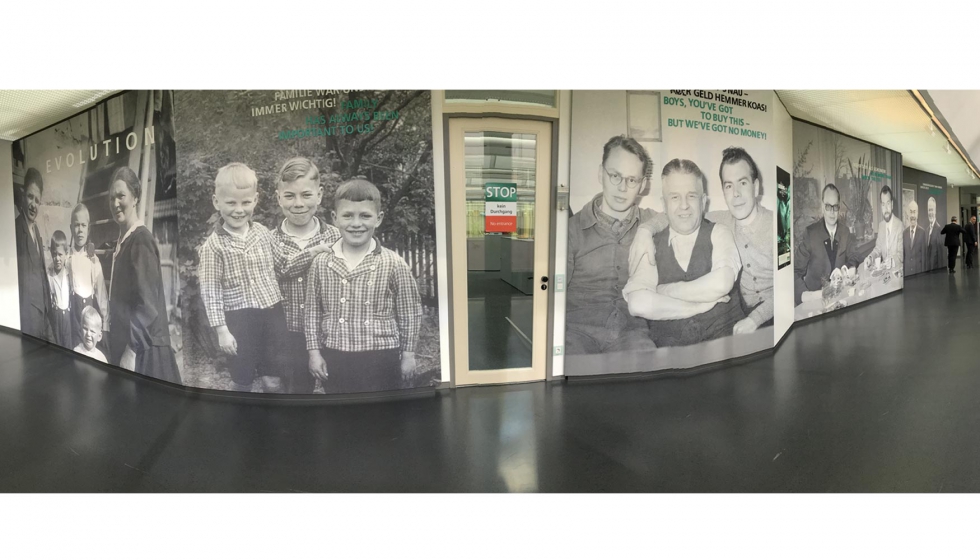
El lema ‘Wir sin da’ que puede verse por toda la planta de Lossburg y que protagonizó el stand de la K pone de manifiesto dónde Arburg centra sus esfuerzos: el trato al cliente. Como curiosidad, debe saber que difícilmente podrá leerlo en otro idioma que no sea alemán, no por que no tenga traducción, que la tiene: “estamos allí”, sino porque es una forma de recordar la calidad alemana que garantiza la firma.
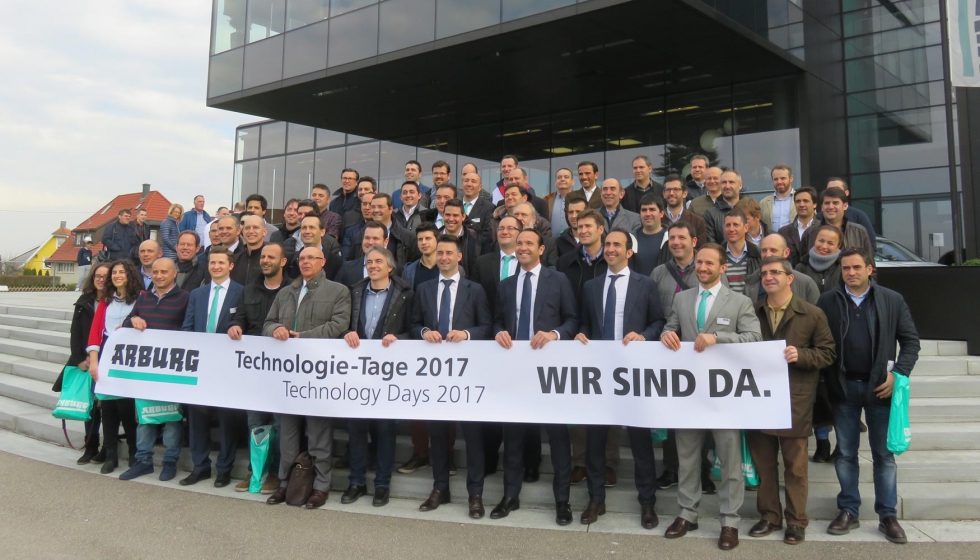
La etiqueta de identificación de equipaje también fue una aplicación sorprendente. Durante su producción se puso de manifiesto cómo con la interconexión informática entre las Allrounder y los Freeformer pueden individualizar las piezas creadas de horma flexible y producirse a su vez en tamaños de lote 1.
En la primera estación se inyecta la pieza en serie ‘etiqueta de equipaje’ en una Allrounder 375 V vertical. A continuación un robot de seis ejes integra un chip NFC (Near Field Communication) en la pieza moldeada.
En la estación siguiente, el visitante registra sus datos personales y selecciona un motivo gráfico. La tarjeta de visita electrónica (vCard) y los datos para el siguiente ciclo de producción se memorizan en el chip, con lo que el producto se transforma un un soporte de datos e información. De ese modo es posible integrar con láser en el tercer paso la producción el nombre, la dirección y el código QR de la vCad en la etiqueta del equipaje. La manipulación completa la realiza un Integralpicker V.
En el paso siguiente una Freeformer invidualiza la etiqueta de equipaje integrando aditivamente en 3D el motivo gráfico elegido.
Se puede ver la trazabilidad y el pedido online a través del propio producto. Según el tipo de dispositivo móvil utilizado, los datos de la etiqueta se leen y memorizan a través del código QR o a través del chip NFC. Estos datos incluyen la dirección URL individual de la respectiva etiqueta de equipaje, lo que permite acceder en todo momento a todos los datos de producción. Además, gracias al chip integrado el visitante puede enviar con su etiqueta otra información son Industria 4.0 por correo electrónico y colgar naturalmente la etiqueta en su maleta.
Durante nuestra visita a los Días Tecnológicos de Arburg tuvimos ocasión de entrevistar a tres clientes de la compañía: