Premios a la innovación de JEC 2017, los “campeones del material compuesto”
Aunque la exposición de este año tendrá lugar del martes 14 de marzo al jueves 16 de marzo de 2017 en el Pabellón de Exposiciones Nord Villepinte de París, Francia, JEC Group ha desvelado los nombres de los 13 ganadores de los Premios a la Innovación de JEC.
Los premios a la innovación de JEC recompensan los mejores descubrimientos en material compuesto basándose en su interés técnico, potencial de mercado, asociaciones, impacto económico y medioambiental y originalidad.
Innovaciones en material compuesto en el punto de mira en JEC World
Este año, las presentaciones para el programa de premios fueron sorprendentes, tanto en cantidad como en diversidad y, lo que es más importante, en calidad. “Los procesos de fabricación para grandes cadenas están ganando importancia este año. Se espera que este movimiento desencadene un uso más masivo de materiales compuestos. Por lo tanto, podríamos ver un cambio de escala en nuestra industria, particularmente en ciertos sectores de producción en masa, como el sector de la automoción, por ejemplo, donde la cadena de suministro se está reconfigurando a través de fusiones y adquisiciones, la integración anterior de los proveedores automotrices y la integración posterior de productores de materias primas”, afirma Frédérique Mutel, presidenta y directora ejecutiva del Grupo JEC.
Igual que el año pasado, un gran número de presentaciones procedía de la industria de la automoción, lo que ilustra perfectamente las tendencias actuales del mercado. La mejora de los procesos fue también uno de los temas más representados, destacando la importancia de la reducción del tiempo de ciclo.
Con 13 categorías que van desde materias primas hasta procesos, para aplicaciones en diversos campos como aeronáutica, automoción, construcción, náutica y vivir mejor, los proyectos ganadores ofrecen una completa visión de conjunto de la cadena de valor del material compuesto y las muchas oportunidades futuras que todavía están por aprovechar en el campo de los materiales compuestos.
La ceremonia de los premios a la innovación de JEC destacará 13 innovadores en el escenario y tendrá lugar el miércoles 15 de marzo a las 5 p.m. en JEC World (Paris Nord Villepinte - Francia).
LOS 13 “CAMPEONES DEL MATERIAL COMPUESTO” GANADORES DEL PREMIO A LA INNOVACIÓN DE JEC
Aeronáutica– IHI Corporation (Japón) Innovador sistema de ventiladores de material compuesto para motores de aviación
Automoción, estructural – Forward Engineering GmbH (Alemania) T-RTM
Automoción, exterior– LG Hausys (Corea del Sur) Portaequipajes de una pieza
Construccción – Accion Construcción SA (España) Innovadores paneles de material compuesto, una alternativa al acero y al hormigón para la construcción de túneles ferroviarios de alta velocidad
Proceso – IRT M2P (Francia) RTM rápido
Fabricación – Voith Composites GmbH & Co. KG (Alemania) Aplicador de hilos de fibra de vidrio Voith
Sostenibilidad – Faurecia (Francia) NAFILite™ material espumado microcelular
Náutica – VABO Composites (Países Bajos) Puerta para buque de material compuesto “lista para usar”
Impresión 3D – +LAB - Politecnico di Milano University (Italia) Fabricación inteligente de materiales compuestos de fibra continua: Atropos
Software – e-Xstream (Luxemburgo) Digimat AM
Deportes – Leibniz-Institut fu¨r Polymerforschung Dresden e.V. (IPF) (Alemania) Maneral de arco recurvo
Materias primas – Covestro Deutschland AG (Alemania) Desmocomp – una solución novedosa para materiales compuestos
Vivir mejor – Brødrene AA (Noruega) Vision of the Fjords, Barco del año 2016 en Noruega.
Categoría: Aeronáutica
- Ganador: IHI Corporation (Japón)
- Socios: IHI Aerospace (Japón), Industrial Technology Center of Fukui Prefecture (Japón), Mitsuya Co., Ltd. (Japón), SHINDO Co. (Japón), Mitsubishi Rayon Co., Ltd. (Japón), Toray Industries, Inc. (Japón)
- Nombre del producto o proceso: Innovador sistema de ventiladores de material compuesto para motores de aviación
Descripción:
IHI Corp., junto con sus socios, desarrolló un innovador y ligero sistema de material compuesto para carcasas de ventilador y el primer álabe guía estructural (SGV) de material compuesto termoplástico.
Para incrementar la eficiencia del combustible en los motores de los aviones, se debe incrementar la relación de derivación (relación entre el caudal másico en la entrada del motor y el caudal másico que entra en el núcleo). Pero esto requiere una carcasa del ventilador más grande, que, si estuviera hecha con materiales tradicionales, supondría un gran aumento del peso del motor y anularía parte del aumento de eficiencia.
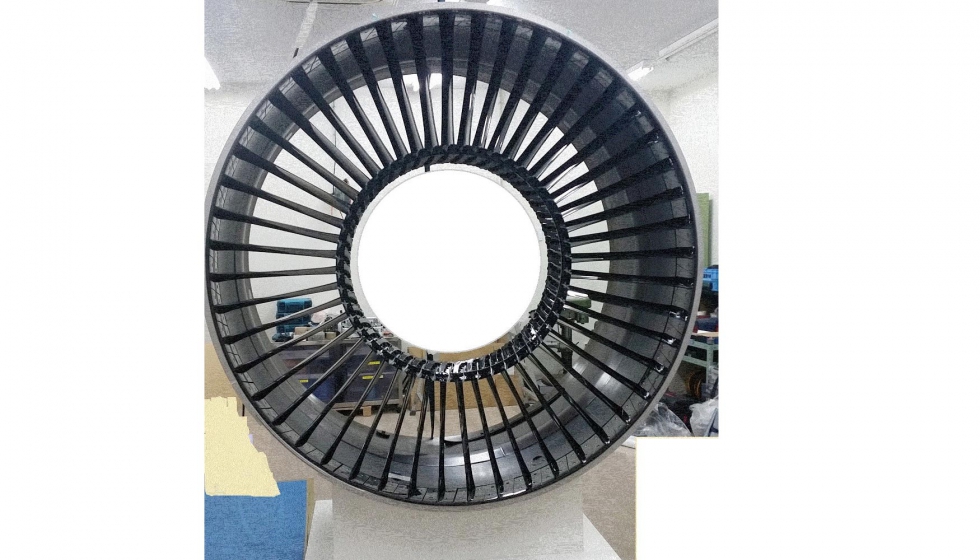
IHI Corporation (Japón) Innovador sistema de ventiladores de material compuesto para motores de aviación. Foto: JEC Group/IHI Corporation.
El uso de materiales compuestos para la carcasa del ventilador estructural primaria y el SGV fue el camino que ha elegido IHI para conseguir la relación de derivación requerida. Usando materiales de desarrollo propio, un termoestable para la carcasa del ventilador y un termoplástico para el SGV, junto con fibras de carbono en ambos casos, IHI consiguió un ahorro de peso del 20% respecto a los motores de aeronaves de la generación anterior, contribuyendo de este modo a reducciones adicionales del consumo de combustible.
Con este proyecto, es la primera vez que se seleccionan materiales compuestos termoplásticos para piezas de la estructura primaria en motores de aeronaves. Los SGV termoplásticos se fabrican mediante corte y disposición de preimpregnado en la fábrica de IHI en Soma, y la principal ventaja es que muestran baja delaminación después de un impacto a alta velocidad. El termoestable usado para la carcasa del ventilador también fue desarrollado para mostrar una absorción de energía de impacto superior contra un impacto a alta velocidad, que es uno de los principales criterios para ambas piezas del motor.
Esta innovación se aplicó con éxito al Airbus A320neo, que funciona con el motor PW1100G-JM. Este motor fue certificado por la FAA en diciembre de 2004 mientras que el Airbus A320neo fue certificado en diciembre de 2015.
Categoría: Automoción, estructural
- Ganador: Forward Engineering GmbH (Alemania)
- Socios: KraussMaffei (Alemania), Alpex Technologies GmbH (Austria), Dieffenbacher (Alemania), Saertex (Alemania), Henkel (Alemania), Handtmann (Alemania), TUM/LCC (Alemania)
- Nombre del producto o proceso: T-RTM
Descripción:
El objetivo de este proyecto es desarrollar el proceso de T-RTM (moldeo por transferencia de resina termoplástica) ‘near-net-shape’ (forma casi acabada) para producción de alto volumen. Este innovador proceso combina las ventajas de la resina termoplástica y la libertad de diseño ofrecida por la tecnología HP-RTM para piezas complejas.
Para demostrar el potencial del proceso, se rediseñó un bastidor del techo para el roadster Roding, teniendo en cuenta que el bastidor del techo es un elemento estructural para el coche.
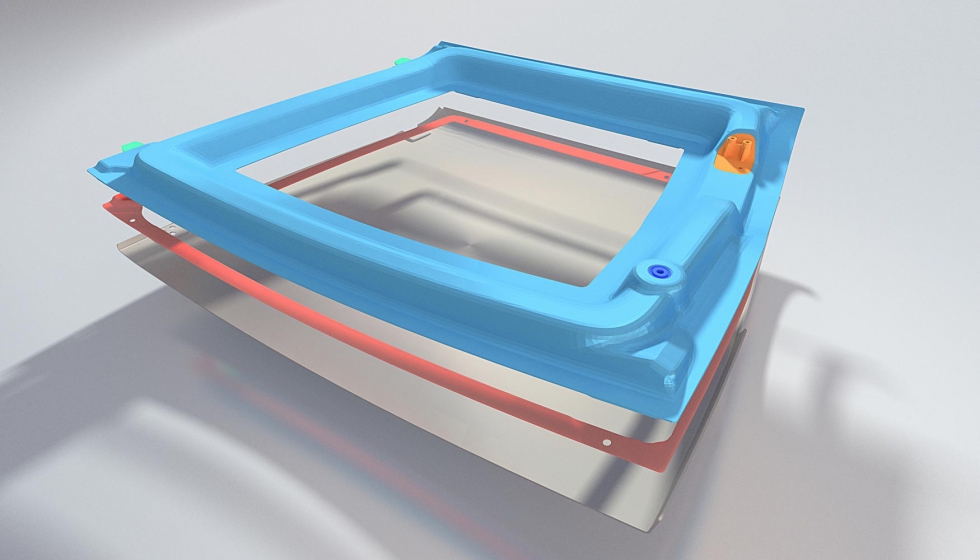
La estructura del techo está hecha de una pieza compleja de múltiples preformas con textiles híbridos e insertos metálicos integrados, impregnada con una poliamida 6 (PA6) de baja viscosidad por HP-RTM. Esta baja viscosidad permite una mejor impregnación de las fibras, una mayor fracción de volumen de fibra y, por lo tanto, mejores propiedades mecánicas y un espesor total de pared reducido, lo que reduce el coste del material.
Para reducir aún más el coste, la costosa fibra de carbono se sustituyó parcialmente por fibra de vidrio, gracias a la hibridación en capa dentro de un tejido no ondulado (NCF). Por lo tanto, una baja cantidad de fibras de carbono es suficiente para añadir rigidez a las capas de fibra de vidrio. Todas estas optimizaciones producen un 16% de ahorro de material para el bastidor del techo en comparación con RTM con resina epoxi.
Para garantizar el menor coste posible, Forward Engineering también se centró en la integración de insertos metálicos con el fin de garantizar transferencia de carga optimizada y de minimizar los costes de montaje del techo en producción en masa. Se usan dos tipos de insertos en el demostrador: insertos moldeados en Al tratados para una adhesión ideal de la matriz aplicada directamente sobre las preformas secas, e insertos de acero roscados aplicados por tuercas remachables. Durante el proceso de RTM, se produce un bloqueo de forma adicional debido al sobremoldeo con resina pura, y la resina también previene la corrosión galvánica.
Categoría: Automoción exterior
- Ganador: LG Hausys (Corea del Sur)
- Socio: Hyundai-Kia Motor Company (Corea del Sur)
- Nombre del producto o proceso: Portaequipajes de una pieza
Descripción:
Con la creciente presión sobre los fabricantes de automóviles para que reduzcan la huella de carbono de sus vehículos, la reducción de peso se está convirtiendo en un prerrequisito fundamental.
El objetivo de este proyecto es reducir el peso y el coste de una pieza que tradicionalmente está hecha de aluminio y que, en gran medida, pasa desapercibida en la industria del material compuesto.
Esta innovación tiene como objetivo reducir el peso y el coste de un portaequipajes mediante el uso de un material compuesto termoplástico de fibra continua (CFT). Para lograr este objetivo, LG Hausys desarrolló un proceso de fabricación donde el CFT, hecho de polipropileno y fibras de vidrio, se preforma primero a la forma deseada y luego se sobremoldea para formar las nervaduras que añadirán rigidez al portaequipajes. En la etapa final, el portaequipajes formado se pinta usando una nueva tecnología de tratamiento superficial.
La ventaja de este proyecto es que la tecnología se desarrolló para una alta libertad de diseño, lo que permite una mejor adaptación del portaequipajes sobre el techo, lo que ayudará a reducir el coste de parte de la producción en masa dentro de una amplia gama de vehículos. Esta innovación redujo el peso de la pieza de 3,8 kg a 2,76 kg, lo que representa una reducción del 28%, manteniendo al mismo tiempo el rendimiento requerido. Este portaequipajes CFT también es beneficioso desde el punto de vista de montaje, ya que el número de piezas se reduce a 1 de 5 en portaequipajes de aluminio existentes.
En general, en comparación con un portaequipajes de aluminio, el coste se reduce en 5,2 €/pieza.
Categoría: Construcción
- Ganador: Acciona Construcción SA (España)
- Socios: Owens Corning (España), Scott Bader (Reino Unido), Celo – Apolo Construction Systems (España), LUM-Industry (Francia), BYK-Chemie GmbH (Alemania), Nanjing Loyalty Composite Equipment Manufacture Co. Ltd. (China)
- Nombre del producto o proceso: Innovadores paneles de material compuesto, una alternativa al acero y al hormigón para la construcción de túneles ferroviarios de alta velocidad
Descripción:
Cuando los dos túneles ferroviarios de alta velocidad de Pajares, de 24 km de largo, se enfrentaron al problema de la infiltración continua de agua en aproximadamente el 30% de la longitud total del túnel, pocas de las soluciones disponibles en el mercado fueron capaces de resolver el problema.
Los innovadores paneles de material compuesto desarrollados por Acciona demostraron ser la mejor solución en este exigente trabajo de construcción, ya que lograron afrontar todos los retos técnicos cumpliendo con los requisitos ignífugos asociados a este tipo de aplicación.
Los desafíos de esta innovación fueron diversos debido a los muchos criterios que se tenían que cumplir. Desde un punto de vista mecánico, el uso de materiales compuestos permitió satisfacer los requisitos estructurales, al tiempo que resultó lo suficientemente delgado para no cambiar el diámetro del túnel y ser compatible con sistemas de catenaria. La flexibilidad de diseño ofrecida por los materiales compuestos también permitió a Acciona desarrollar un sistema con juntas a prueba de fugas y un sistema de anclaje. Los paneles de 9,2 metros de largo también fueron lo suficientemente flexibles para adaptarse a la forma del túnel y sus irregularidades.
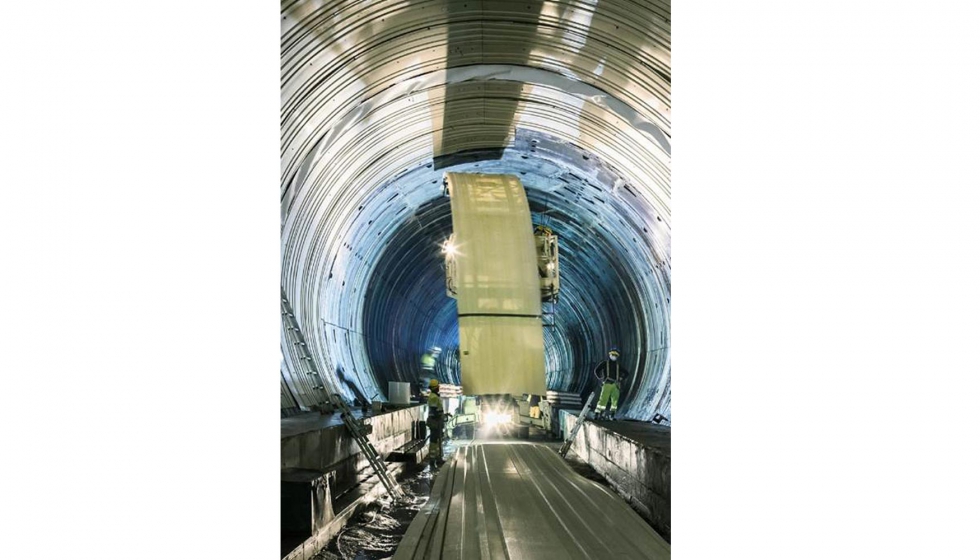
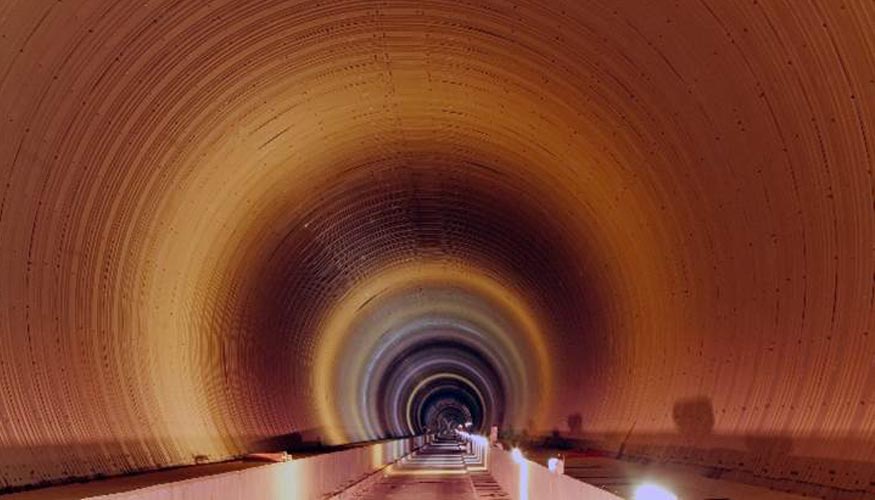
Construcción SA (España) Innovadores paneles de material compuesto, una alternativa al acero y al hormigón para la construcción de túneles ferroviarios de alta velocidad. Foto: JEC Group/ Acciona Construcción S.A.
Otra preocupación en este proyecto fue la necesidad de producir hasta 15.000 paneles dentro del calendario de entrega y mantener el coste de los paneles de material compuesto lo más bajo posible. Para conseguirlo, Acciona optó por un proceso de pultrusión y desarrolló un sistema de inyección de resina de bajo coste y una cámara de impregnación de fibras que se adaptó a la viscosidad de la resina ignífuga formulada para el proyecto. Este nuevo sistema hizo posible producir un panel de material compuesto en 34 minutos de forma continua.
Las otras ventajas de los compuestos en esta aplicación fueron su bajo mantenimiento y alta resistencia a la corrosión en comparación con los materiales de construcción tradicionales. Por último, la manipulación y la instalación de los paneles en el túnel fueron fáciles y rápidas gracias a la naturaleza ligera de los paneles de material compuesto.
Para resumir e ilustrar el tamaño del proyecto, se produjeron más de 15.000 paneles, cubriendo aproximadamente 200.000 metros cuadrados de túneles para un total de 1.700 toneladas de materiales compuestos.
Categoría: Proceso
- Ganador: IRT M2P (Francia)
- Socios: Arkema (Francia), Compose (Francia), Faurecia (Francia), Chomarat (Francia), Hexion (Francia), Hutchinson (Francia), Composite Integrity (Francia), Sise (Francia), Pinette P.E.I. (Francia), Renault (Francia)
- Nombre del producto o proceso: RTM rápido
Descripción:
Esta innovación es el resultado de una serie de innovaciones desarrolladas por los socios del proyecto de colaboración RTM rápido.
Pinette P.E.I. (dispositivo de prensa compacta y carga & descarga), Compose (herramientas innovadoras para piezas de precisión), SISE (sistema de termorregulación rentable), Chomarat (materiales de refuerzo optimizados), Hexion & Arkema (resinas reactivas), Composite Integrity (proceso con molde cerrado) y Renault, Faurecia & Hutchinson (integración y diseño) trabajaron juntos para proporcionar las soluciones que harían del proyecto un éxito.
Todos estos desarrollos individuales dieron como resultado la creación de una plataforma a escala industrial para demostrar la viabilidad de las piezas de automoción de material compuesto estructurales producidas en serie usando procesos RTM reactivos. Esta plataforma totalmente automatizada se basa en C-RTM (moldeo por transferencia de resina de compresión) y es compatible con resinas termoplásticas y termoestables reactivas, que impregnan la pieza más rápido y mejor que RTM y hacen al proceso flexible y adaptable a las necesidades de los fabricantes de automóviles.
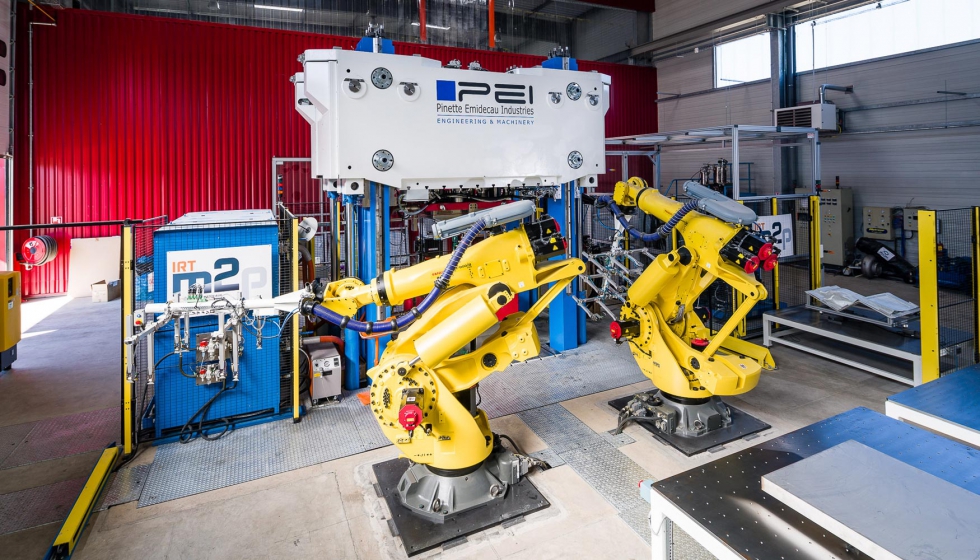
IRT M2P (Francia) RTM rápido. Foto: JEC Group/IRT M2P.
Gracias a un entorno automatizado (carga y descarga) y equipos de vanguardia especialmente desarrollados para el proyecto, la plataforma de RTM rápido puede producir piezas de material compuesto grandes (de hasta 3 m²), con una forma completamente acabada, funcionalizadas y estructurales en un tiempo de ciclo de 120 segundos. Para garantizar la trazabilidad y la calidad de las piezas resultantes, la plataforma también está totalmente equipada con adquisición automática de datos, trazabilidad de parámetros del proceso, sistemas de medición del consumo de energía y sistemas de control no destructivo en línea.
Siendo el objetivo inicial de esta innovación el automóvil de consumo masivo, el proyecto RTM rápido se centró en una solución técnica y económicamente optimizada, integrando funcionalidad, forma acabada y un proceso totalmente automatizado para mantener los costes y tiempos de ciclo lo más bajos posible. Gracias a este enfoque, el proceso fue fácilmente adoptado por otras industrias que necesitan mayores velocidades de producción, como la aeronáutica, los ferrocarriles y todo el sector del transporte.
Categoría: Fabricación
- Ganador: Voith Composites GmbH & Co. KG (Alemania)
- Nombre del producto o proceso: Aplicador de hilos de fibra de vidrio Voith
Descripción:
Esta innovación es una máquina de colocación de fibra directa totalmente automatizada, llamada el Aplicador de hilos de fibra de vidrio Voith (VRA).
El VRA usa hilos de fibra de vidrio no tratados y aglutinación en polvo para generar una pila seca con precisión de forma. La pila se produce en cuatro etapas diferentes: en primer lugar, los hilos de fibra de vidrio se extienden y se ensamblan en una cinta de 50 mm de ancho, se aplica un aglutinante sobre las cintas en línea, a continuación se comprueba el ancho de la cinta mediante un control de calidad en línea y finalmente, las cintas aglutinadas son colocadas sobre una mesa giratoria/móvil mediante varios pares de pinzas.
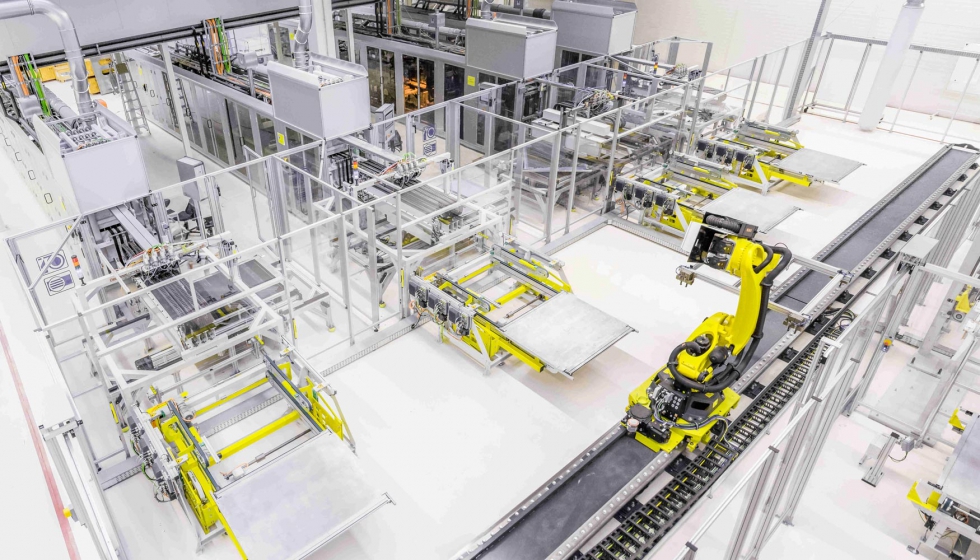
Voith Composites GmbH & Co. KG (Alemania) Aplicador de hilos de fibra de vidrio Voith.
Esto da como resultado el ensamblaje de una pila preforma de forma casi acabada “near-net-shape” etapa a etapa, con refuerzos o capas locales que pueden colocarse en cualquier ángulo en cualquier zona.
La principal ventaja de este proceso de fabricación es que la preforma resultante está totalmente adaptado a los requisitos mecánicos y cargas de la pieza final, con gran flexibilidad y rápida adaptación. Al estar el VRA conectado con una cadena de producción automatizada ya utilizada para un material CFRP de serie de alto volumen para automoción, proporciona una mayor eficiencia y una mejor integración.
Además, a pesar de que las pinzas individuales son bastante estándar, el VRA es adaptable a escala: la velocidad de colocación se puede incrementar en un factor de dos duplicando el número de pinzas. Y varias unidades pueden colocarse en líneas paralelas de fabricación de cintas anteriores, lo que presenta una fuerte ventaja en comparación con las máquinas estándar de colocación de fibras secas.
Además de este aumento de la velocidad de producción, esta innovación tiene un fuerte objetivo de reducir los costes de producción. Los hilos de fibra de vidrio no tratados y el aglutinante se utilizan debido a su rentabilidad, pero también porque, gracias al VRA, estas materias primas pueden ser transformadas en una preforma utilizable directamente a partir de la fibra en una sola etapa, sin tener que usar etapas intermedias costosas o semiacabadas, y casi sin residuos.
Categoría: Sostenibilidad
- Ganador: Faurecia (Francia)
- Socio: Automotive Performance Materials (APM) (Francia)
- Nombre del producto o proceso: Material espumado microcelular NAFILite
Descripción:
Para satisfacer las preocupaciones medioambientales en la industria del automóvil, esta innovación se centra en la reducción de los impactos ambientales durante todo el ciclo de vida del material.
Mientras que los materiales compuestos tradicionales permiten reducir las emisiones de CO2 de los vehículos durante su vida útil, los materiales compuestos de origen biológico pueden ayudar a reducir este impacto durante el proceso de fabricación y la eliminación al final de la vida útil.
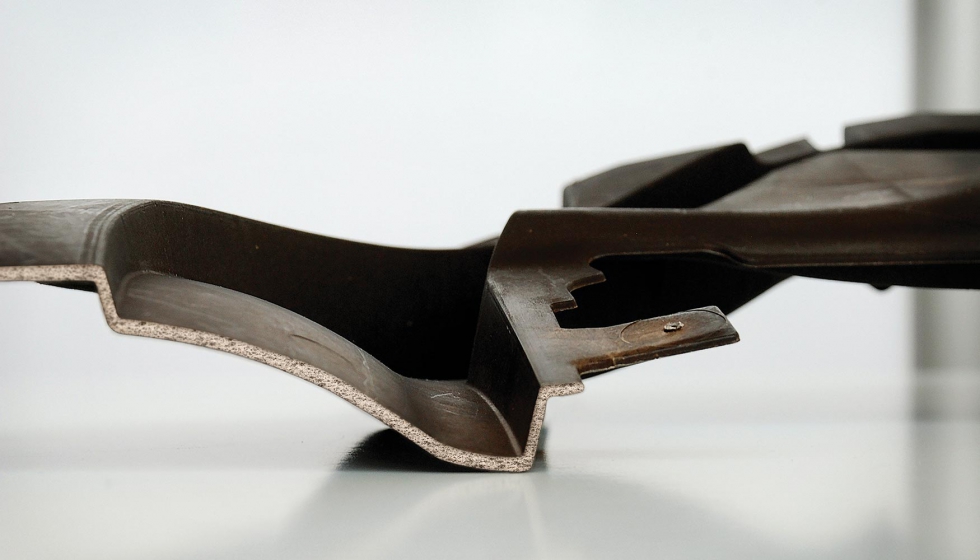
Faurecia (Francia) NAFILite material espumado microcelular. Foto: JEC Group/Faurecia.
El objetivo del material espumado microcelular NAFILite desarrollado por Faurecia es reducir aún más el impacto medioambiental de los materiales compuestos.
NAFILite combina un proceso de formación de espuma microcelular basado en la inyección (con tecnología de apertura de molde) con el material NAFILean existente: un material inyectable y reciclable compuesto por el 20% de fibras de cáñamo y polipropileno. El compuesto NAFILean con un 20% de contenido renovable se inyecta con aditivos en un molde cerrado. A continuación, el molde se abre ligeramente para adaptarse a la expansión del material (debido a la liberación de CO2).
La espuma resultante es un 30% más ligera que la referencia actual del mercado para las piezas estructurales inyectadas usadas en interiores del automóvil. La combinación de ahorro de peso, fibras naturales renovables y un material termoplástico reciclable reduce su impacto medioambiental hasta en un 30%.
Además, para alcanzar los estándares de calidad de los fabricantes de equipos originales de automoción, la estructura microcelular del material final proporciona una mejor calidad percibida en términos de robustez y ajuste y acabado, y también presenta buenas propiedades termomecánicas frente a materiales estándar.
Categoría: Náutica
- Ganador: Vabo Composites (Países Bajos)
- Socios: ICO BV (Países Bajos), Spil Composites (Países Bajos)
- Nombre del producto o proceso: Puerta para buque de material compuesto ‘lista para usar’
Descripción:
Tradicionalmente, las puertas de los buques son de acero o aluminio, lo cual es perjudicial para el peso, pero también para la resistencia a la corrosión. Al ser la corrosión una amenaza que implicaba enormes costes, era natural que alguna alternativa se aplicara a la producción.
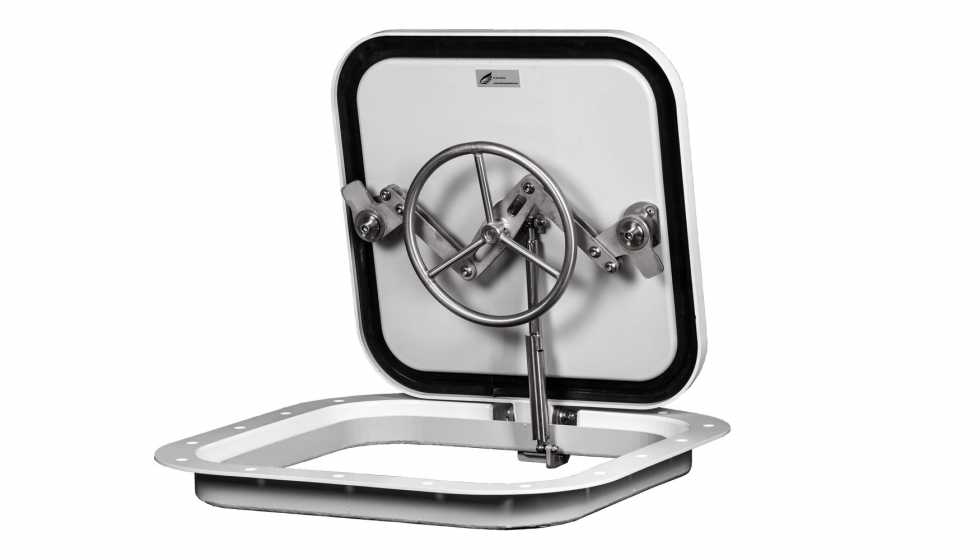
Vabo Composites (Países Bajos) Puerta para buque de material compuesto ‘lista para usar’. Foto: JEC Group/VABO Composites.
Esta innovación ofrece dicha alternativa, ya que Vabo Composites desarrolló una puerta para buque de material compuesto “lista para usar” y escotillas diseñadas para reemplazar a la solución metálica existente.
La puerta y las escotillas son producidas por RTM en un sistema de moldeo modular, que permite la producción de varias dimensiones de la puerta a un coste más bajo. El procesamiento central y de postproducción se realiza mediante fresado CNC y todas las demás piezas son ensambladas y verificadas en el taller de Vabo para asegurar que los productos pueden ser utilizados directamente en yates, cruceros, buques comerciales, etc.
Las ventajas de esta innovadora puerta para buque son obviamente el hecho de que los materiales compuestos tienen una gran resistencia a la corrosión y son más ligeros que el metal –una puerta completamente equipada con dimensiones 1.800 x 800 mm pesa menos de 45 kg, es decir, aproximadamente un 60% de ahorro de peso frente a la versión de acero– mejorando de este modo el equilibrio y la eficiencia del combustible de los buques. Pero las puertas de material compuesto también requieren un bajo mantenimiento, ya que no se necesita lubricación, e incluyen algunas funciones adicionales.
Las puertas superaron con éxito las pruebas de resistencia al fuego y tienen excelentes propiedades de amortiguación acústica y aislamiento, lo que significa que no hay necesidad de añadir aislamiento, como es el caso para las puertas de aluminio y acero.
Categoría: Impresión 3D
Ganador: +LAB - Politecnico di Milano University (Italia)
Socio: Owens Corning (Francia), Kuka Robotics (Alemania)
Nombre del producto o proceso: Fabricación inteligente de materiales compuestos de fibra continua: Atropos
Descripción:
Atropos es el nombre del primer brazo robótico de 6 ejes capaz de imprimir en 3D materiales compuestos de fibra continua utilizando resinas termoestables.
En el proceso que soporta Atropos, las fibras son impregnadas y estiradas hasta el cabezal de una máquina controlada numéricamente que puede colocarlas de una manera precisa y repetible. Una vez extruido por el cabezal de impresión, el material es irradiado por una lámpara UV dedicada para curar rápidamente la resina.
La elección de centrarse en resinas termoestables con tiempos de curado inferiores a un segundo hace posible colocar fibras continuas a velocidades de aproximadamente 50 mm/s por ahora, generando rápidamente productos caracterizados por temperaturas de trabajo significativamente más altas en comparación con las resinas termoplásticas convencionales.
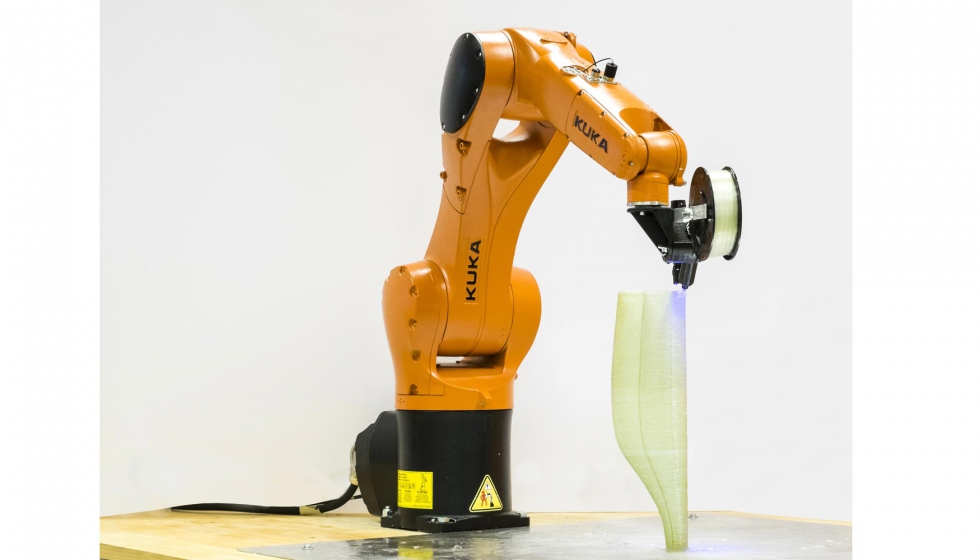
+LAB - Politecnico di Milano University (Italia) Fabricación inteligente de materiales compuestos de fibra continua: Atropos. Foto: JEC Group/+LAB - Politecnico di Milano University.
Para optimizar la forma interna y externa del objeto, +LAB desarrolló un algoritmo de corte que puede planificar de forma predictiva los movimientos de la máquina para colocar el material de refuerzo donde aparecen las tensiones máximas en el objeto final. Además, el algoritmo también puede variar la relación fibra/matriz hasta un 60% en volumen. Con estas dos características, es posible obtener una pieza ligera y personalizable con un rendimiento optimizado según su uso.
La principal fortaleza de este proyecto es la capacidad de controlar la dirección de la fibra a medida que la pieza se produce para obtener lo mejor de la naturaleza anisótropa de las fibras, gracias al algoritmo desarrollado por +LAB. De este modo, se pueden producir y personalizar diferentes piezas con las mismas formas, de acuerdo con sus cargas en servicio.
Categoría: Software
- Ganador: e-Xstream (Luxemburgo)
- Co-Ganador: Solvay (Francia)
- Nombre del producto o proceso: Digimat AM
Descripción:
Con la impresionante tasa de crecimiento de la fabricación por adición (AM) en los últimos años, e-Xstream estableció una solución para ayudar a la industria de la AM a pasar de la creación de prototipos a la fabricación real de piezas de material compuesto.
Esta innovación combina diferentes programas informáticos para ofrecer soluciones para el desarrollo de materiales, simulación de procesos y rendimiento de piezas impresas.
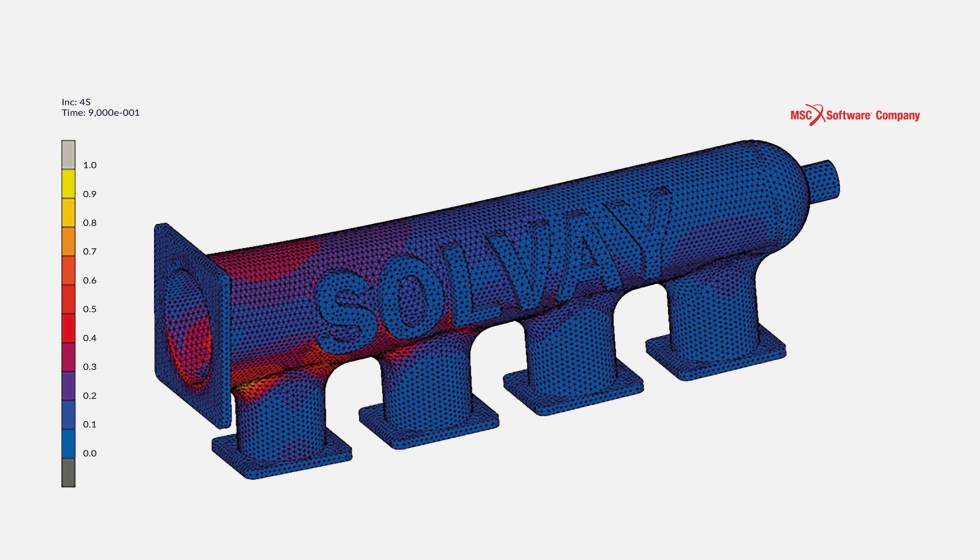
Predicción de la distribución del indicador de fallo debido a la presión de rotura de una cámara de sobrepresión del polimotor impreso usando el material Sinterline. Foto: Solvay Engineering Plastics.
Desde el punto de vista de los materiales, e-Xstream proporcionará las herramientas (Digimat-MF y Digimat-FE) para diseñar materiales compuestos avanzados específicamente para AM.
En cuanto a la simulación de procesos, Digimat-AM es un innovador programa informático totalmente dedicado a modelar los procesos de modelado por deposición en fusión (FDM) y de sinterización láser selectiva (SLS) para materiales reforzados. El objetivo de Digimat-AM es poder “imprimir correctamente a la primera” optimizando la calidad del proceso de fabricación (minimizando la deformación de piezas, por ejemplo) y prediciendo el rendimiento de la pieza impresa.
La plataforma Digimat también será capaz de simular el rendimiento de las piezas impresas en función del material y los parámetros del proceso de impresión tales como la herramienta o la trayectoria del láser de sinterización. Esta herramienta única es un gran paso adelante para el desarrollo y el diseño de piezas de material compuesto mediante AM, llevando el rendimiento y la eficiencia de las piezas impresas en 3D al nivel requerido para la industria.
Digimat es el único software en el mercado que permitirá a los usuarios finales y los fabricantes de impresoras aportar fiabilidad a las piezas impresas, gracias a la predicción del alabeo, la evaluación de muchos parámetros de proceso mediante la simulación, eliminando el coste de los ensayos y errores previamente necesarios para optimizar estos parámetros. Además, como se puede evaluar el impacto de la dirección de impresión, la simulación numérica reduce la necesidad de muchas pruebas mecánicas a unas pocas validaciones.
Categoría: Deportes
- Ganador: Leibniz-Institut fu¨r Polymerforschung Dresden e.V. (IPF) (Alemania)
- Socios: Hochschule fu¨r Technik und Wirtschaft (Alemania), Faculty of Design (Alemania)
- Nombre del producto o proceso: Maneral de arco recurvo
Descripción:
Esta innovación es una nueva generación de manerales de arco hechos de materiales compuestos de fibra de carbono.
Mientras que el uso de materiales compuestos en los manerales de arco es ahora bastante común, este maneral se fabricó utilizando un diseño no convencional, pero adaptado a la tensión, lo que le hace hasta un 40% más ligero que las soluciones actuales (carbono o aluminio), al tiempo que mejora la rigidez específica de la masa en aproximadamente un 43% en comparación con un maneral de referencia de aluminio.
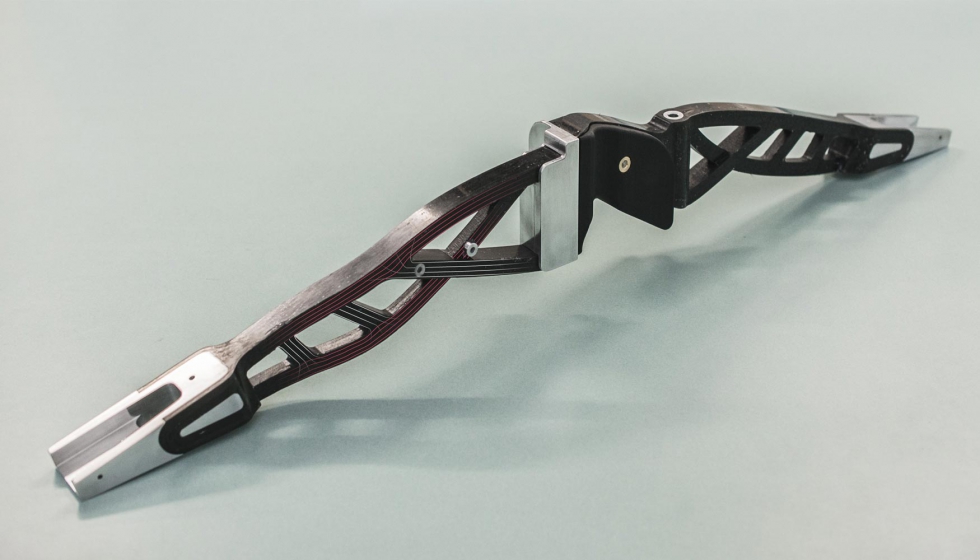
Leibniz-Institut für Polymerforschung Dresden e.V. (IPF) (Alemania) Maneral de arco recurvo. Foto: JEC Group/ Leibniz-Institut für Polymerforschung Dresden e.V.
Para poder fabricar una pieza real, IPF utilizó la tecnología de colocación de fibra personalizada (TFP), un proceso inventado en IPF Dresden, para producir cuatro preformas con una estructura de tipo cercha. Con esta tecnología altamente versátil, IPF logró demostrar la capacidad de un diseño de material compuesto de eje variable. Debido a que la fabricación de materiales compuestos de vanguardia se basa principalmente en el diseño multiaxial, la realización de un diseño adaptado a la tensión puede resultar bastante difícil, si no inviable en absoluto.
La aplicación de materiales compuestos de acuerdo con las direcciones de eje variable calculadas previamente puede, por lo tanto, conducir a un rendimiento superior de la pieza, usando la naturaleza anisótropa de las fibras de la mejor manera posible, y puede ayudar a usar menos recursos, permitiendo de este modo ahorrar costes.
Otra fase importante del proyecto fue el desarrollo del proceso de fabricación. Debido a la forma compleja de la pieza, con varios orificios e insertos, no fue posible el desarrollo de un molde RTM presurizado cerrado. En su lugar, se fabricó una herramienta cuasi-cerrada con insertos especiales para entrada de resina y zonas para la evacuación de presión de aire. El proceso de consolidación final es básicamente un proceso de infusión a molde cerrado, lo que ayuda a reducir los costes de fabricación ya que no se requiere ningún dispositivo de presurización RTM, sin afectar a la calidad de la pieza.
Categoría: Materias primas
- Ganador: Covestro Deutschland AG (Alemania)
- Nombre del producto o proceso: Desmocomp, una solución novedosa para materiales compuestos
Descripción:
Una de las principales preocupaciones de los fabricantes de edificios e infraestructuras con respecto a los materiales compuestos es su capacidad para resistir la degradación medioambiental y, en particular, la luz UV. Para hacer frente a este problema, Covestro desarrolló el material de matriz Desmocomp.
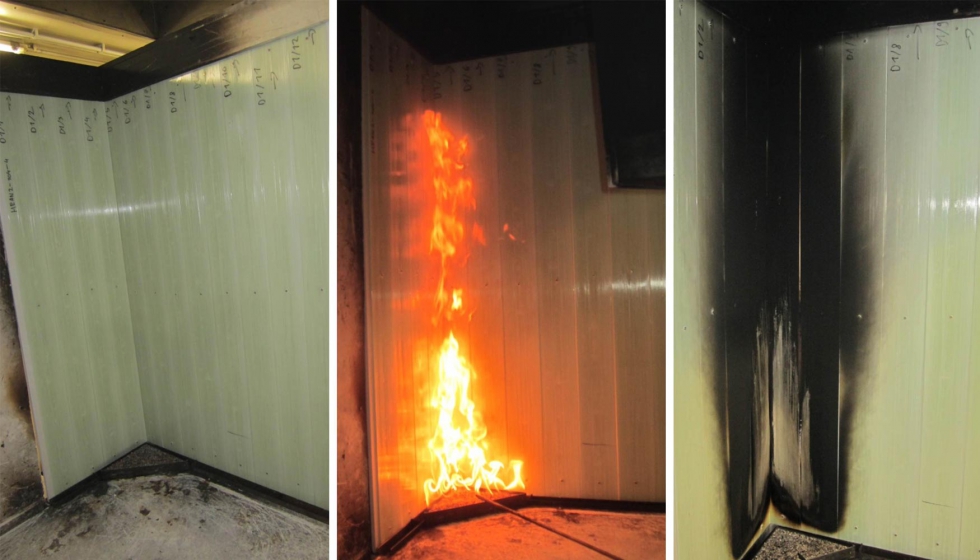
Covestro Deutschland AG (Alemania) Desmocomp - una solución novedosa para materiales compuestos Foto: JEC Group/ Covestro Deutschland AG.
Este polímero se basa en poliuretano alifático (PU) y presenta buena resistencia a la intemperie y a los rayos UV para proteger el material compuesto de las influencias ambientales, haciendo innecesario el uso de estabilizadores UV, velos UV y recubrimientos protectores.
Para proporcionar una solución completa para aplicaciones en exteriores, Desmocomp también puede confiar en las buenas propiedades mecánicas del PU, como la estabilidad dimensional (bajo coeficiente de expansión térmica), el aislamiento térmico, la buena resistencia química y al fuego, así como las propiedades antigraffiti.
Desmocomp, desarrollado por primera vez para el proceso de pultrusión, uno de los principales procesos utilizados para los materiales compuestos en la infraestructura, se puede usar en moldes abiertos y cerrados y, gracias a un innovador sistema monocomponente, es fácil de procesar y rentable, ya que no hay cajas de inyección, bombas mezcladoras-dosificadoras o inversiones adicionales.
Categoría: Vivir mejor
- Ganador: Brødrene AA (Noruega)
- Co-Ganadores: Saertex GmbH & Co KG (Alemania), DIAB group (Noruega), Reichhold (Noruega)
- Nombre del producto o proceso: Vision of the Fjords, Barco del año 2016 en Noruega
Descripción:
Cuando se encargó a Brødrene AA el desarrollo de un barco para usarlo en excursiones turísticas en el fiordo de Nærøyfjord, declarado Patrimonio de la Humanidad por la Unesco, la compañía se enfrentó al desafío de combinar el turismo de masas y la necesidad de preservar el medio ambiente con un impacto lo más bajo posible. La solución que Brødrene AA ideó fue un barco con un montón de espacios abiertos externos para disfrutar de las vistas, así como amplias zonas acristaladas y un eficiente diseño de catamarán para reducir las olas y limpiarlo a orillas del fiordo.

Brødrene AA (Noruega). Vision of the Fjords, Barco del año 2016 en Noruega. Foto: JEC Group/Brødrene AA.
La única solución que proporcionó la rigidez requerida para materializar la intención de los diseñadores fueron los polímeros reforzados con fibra de carbono y los materiales intercalares de carbono. Todos los elementos estructurales de la embarcación están hechos de laminados intercalares de carbono (cubiertas, paredes, escaleras, techos...), incluidos los cascos de 42 metros de eslora y 5 metros de altura de la estructura de catamarán, que se producen en un proceso de infusión al vacío de un solo paso, por lo que el Vision of the Fjords es el barco de pasajeros comercial más grande que se construirá en fibra de carbono. Saertex proporcionó los tejidos, Diab el núcleo de bajo peso para el material compuesto intercalar y Reichhold el éster vinílico modificado con caucho.
El bajo peso de los laminados intercalares también permitió que el barco fuera propulsado por motores eléctricos de menor potencia, haciéndolo limpio y silencioso. En este proyecto, el uso de materiales compuestos era obligatorio para poder proporcionar el diseño requerido al tiempo que también se hacía al barco respetuoso con el medio ambiente en el proceso.