El mecanismo del husillo
Aunque pueda parecer extraño, las primeras máquinas de inyección de plástico no disponían de este elemento. Por el contrario en la zona de fusión del plástico había un torpedo interior calefactado que era un elemento fijo pero que por su diseño obligaba al plástico a pasar por zonas estrechas y calientes con el fin de fundirlo durante la inyección. Afortunadamente, esto ha quedado en el recuerdo de los que somos ya “antiguos” en esta profesión. Eran los comienzos de esta tecnología.
El husillo es un elemento fundamental en la máquina de inyección de plásticos. Se trata de un enrollamiento helicoidal de acero cuyo diseño es muy importante para el posterior rendimiento y calidad de la máquina de inyección así como para la plastificación, homogeneización y transformación del polímero.
Todos los fabricantes de maquinaria tienen como objetivo la mejora continua, de los diseños de los husillos con ingenieros trabajando exclusivamente en esta parte de la máquina.

En el diseño del husillo están definidas tres zonas con diferentes funciones:
- Zona de alimentación. Es la zona del extremo posterior del husillo junto a la tolva. Es por donde el material en forma de granza es alimentado hacia la unidad de inyección. Se solicitan propiedades de transporte de sólidos hacia las zonas delanteras del husillo. Importante en esta zona el coeficiente de fricción entre la granza y el husillo.
- Zona de compresión. Zona donde se produce una disminución del volumen en el interior del filete provocando una compresión del material progresiva. Esto provoca calor por fricción y cizalla. Esto ayuda en la fusión del material y por tanto se produce también un aumento del volumen específico. En esta zona a través de esta compresión, el aire que hay entre la granza es desplazado hacia la zona anterior de alimentación.
- Zona de dosificación. Zona donde se produce la mezcla y homogeneización final de la masa fundida.
Las dimensiones ideales de cada una de estas zonas variará en función del tipo de termoplástico utilizado, variando sobre todo la zona de compresión. En materiales semicristalinos la longitud de esta zona será más corta que en materiales amorfos.
Cámaras, cilindros
Cilindro de acero tratado, recubierto externamente por resistencias eléctricas y sus correspondientes termopares, separadas en zonas independientemente regulables. En su interior se aloja el husillo.
La capacidad de plastificación de la unidad de plastificación vendrá determinada por la longitud de la misma y de su valor L/D.
El grupo plastificador está sometido a un gran desgaste por parte del termoplástico procesado. Este desgaste es el resultado de diferentes causas o variables, por ejemplo:
- Material del que está construido el conjunto husillo / diámetro
- Diseño del husillo
- Parámetros de inyección
- Tipos de materiales procesados (retardante de llama, refuerzos, etc)
- Los cilindros y husillos más utilizados son con acero nitrurado con capa dura superficial de un espesor de entre 0,4 a 0,5 mm.
El mecanismo del husillo
El husillo no debe entenderse como un núcleo con un enrollamiento helicoidal para transportar material hacia la punta del husillo para que este sea inyectado en el molde. Su funcionamiento va mucho más allá que el transporte de granza sólida desde la tolva hacia zonas delanteras del husillo.
- Zona inicial del husillo. Zona de llenado del canal del husillo con sólidos o granza. Cada giro, el filete empuja y atrapa la granza que ha caído por gravedad en la ranura del filete. Rendimiento afectado por: la geometría del husillo, el ángulo del filete, la anchura del canal, las revoluciones de giro del husillo.
- Zona de transporte de sólidos. La granza de material es comprimida rellenando el volumen libre del canal. Rendimiento afectado por: Coeficiente de fricción entre polímero, husillo y camisa de la cámara. Óptimo es que la granza se “pegue” a la camisa y resbale en el husillo.
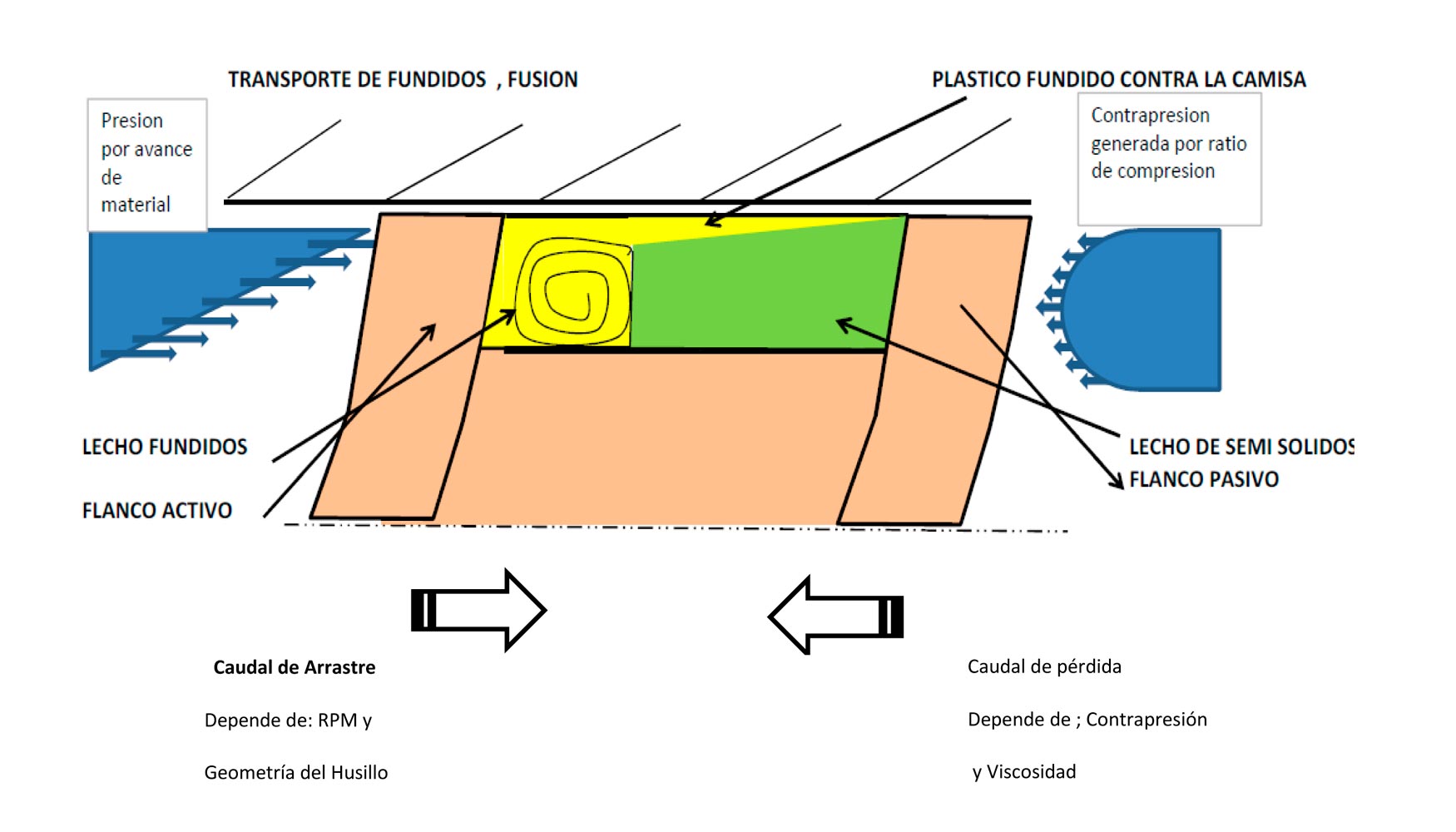
- En la zona de 2/3 de la altura del filete la velocidad es cero.
- En la zona superior a esos 2/3 de la altura del filete se produce un movimiento hacia el flanco activo del husillo.
- En la zona inferior a estos 2/ 3 de la altura del filete se produce un movimiento hacia el flanco pasivo.
Para que este efecto de turbulencia y homogeneización se produzca se tienen que dar las siguientes condiciones, por un lado debe existir contrapresión a la carga y por otro, el desgaste en el ajuste de diámetros de husillo y cámara de plastificación no debe ser excesivo.
Para que el material avance a través de la cámara de plastificación la fricción entre la granza y el husillo debe ser menor que la fricción contra la camisa de la cámara de plastificación. Si imaginamos una tuerca roscada hasta la mitad de un tornillo y lo hacemos girar, la tuerca girará y no avanzará a lo largo del tornillo. En este caso la tuerca es la granza comprimida en el filete y el tornillo es el husillo. Si colocamos algo que dificulte el giro de la tuerca, es decir aumento de la fricción, esta avanzará a lo largo del tornillo.
Cuando este equilibrio de fricción se rompe es cuando se produce el efecto de que el husillo gira pero el material no avanza hacia adelante.
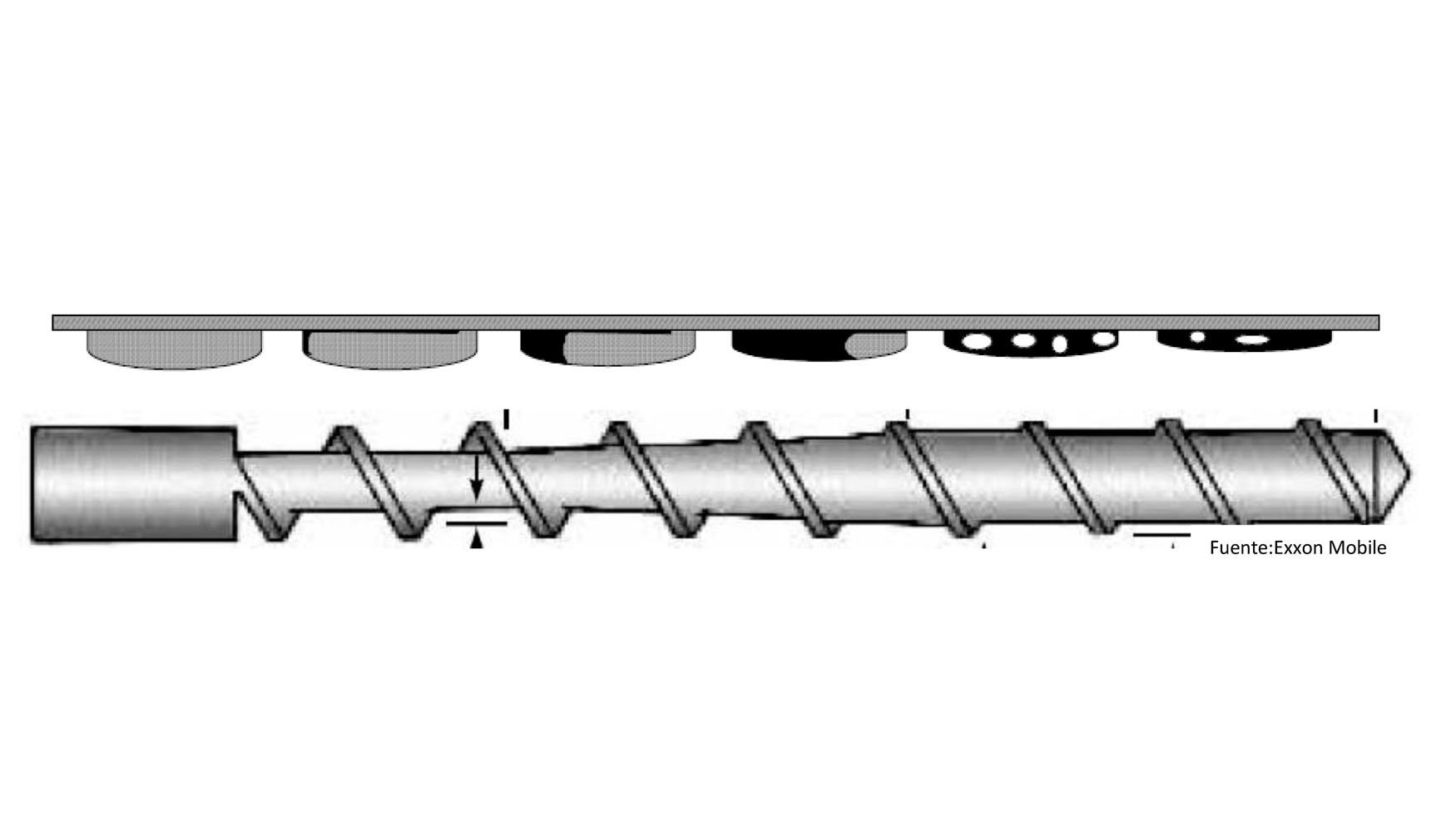
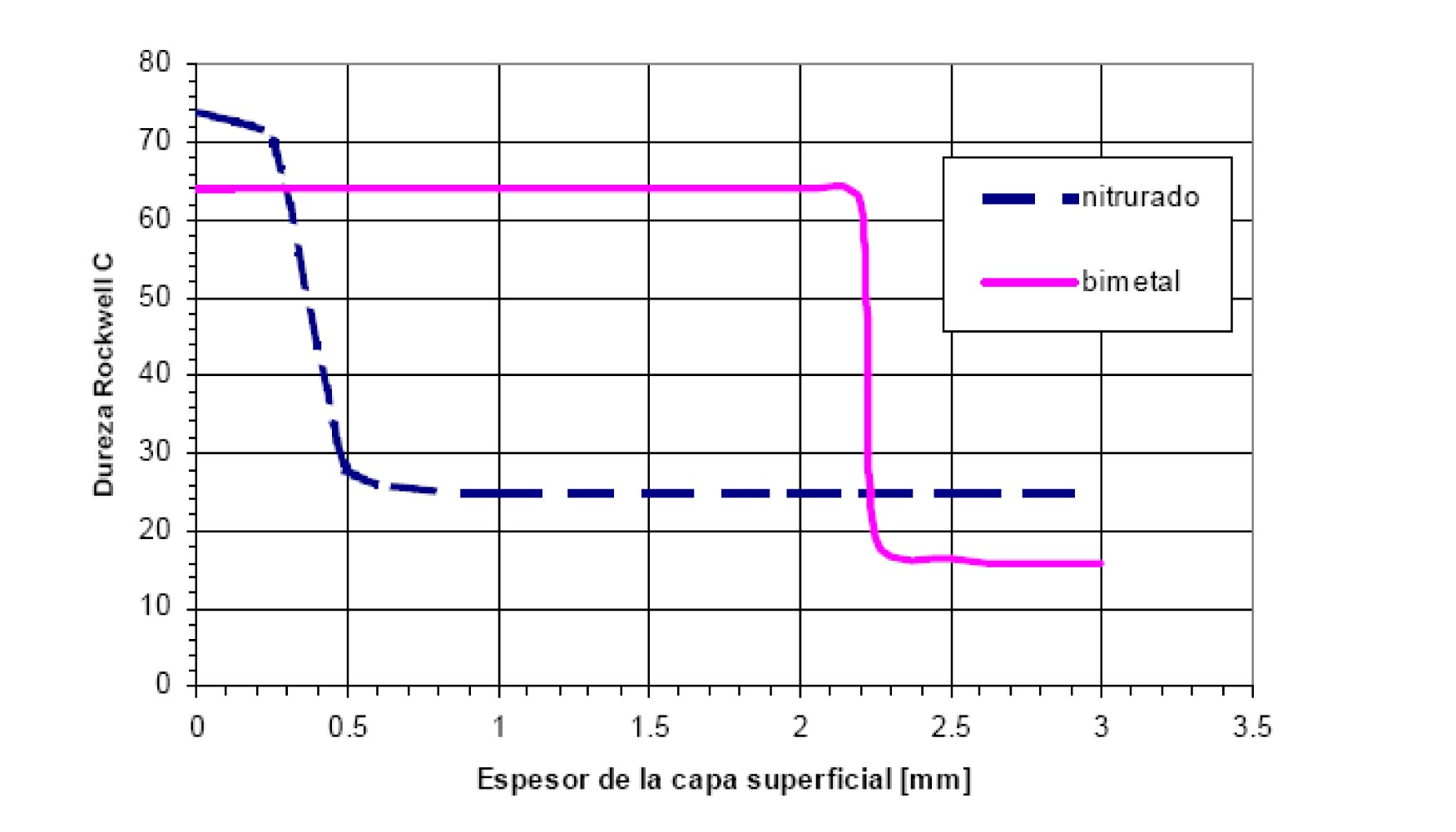
Ejemplo de abrasión y desgaste después de 1.500 horas de trabajo procesando poliamida con 50% de fibra de vidrio. Fuente Ascamm.
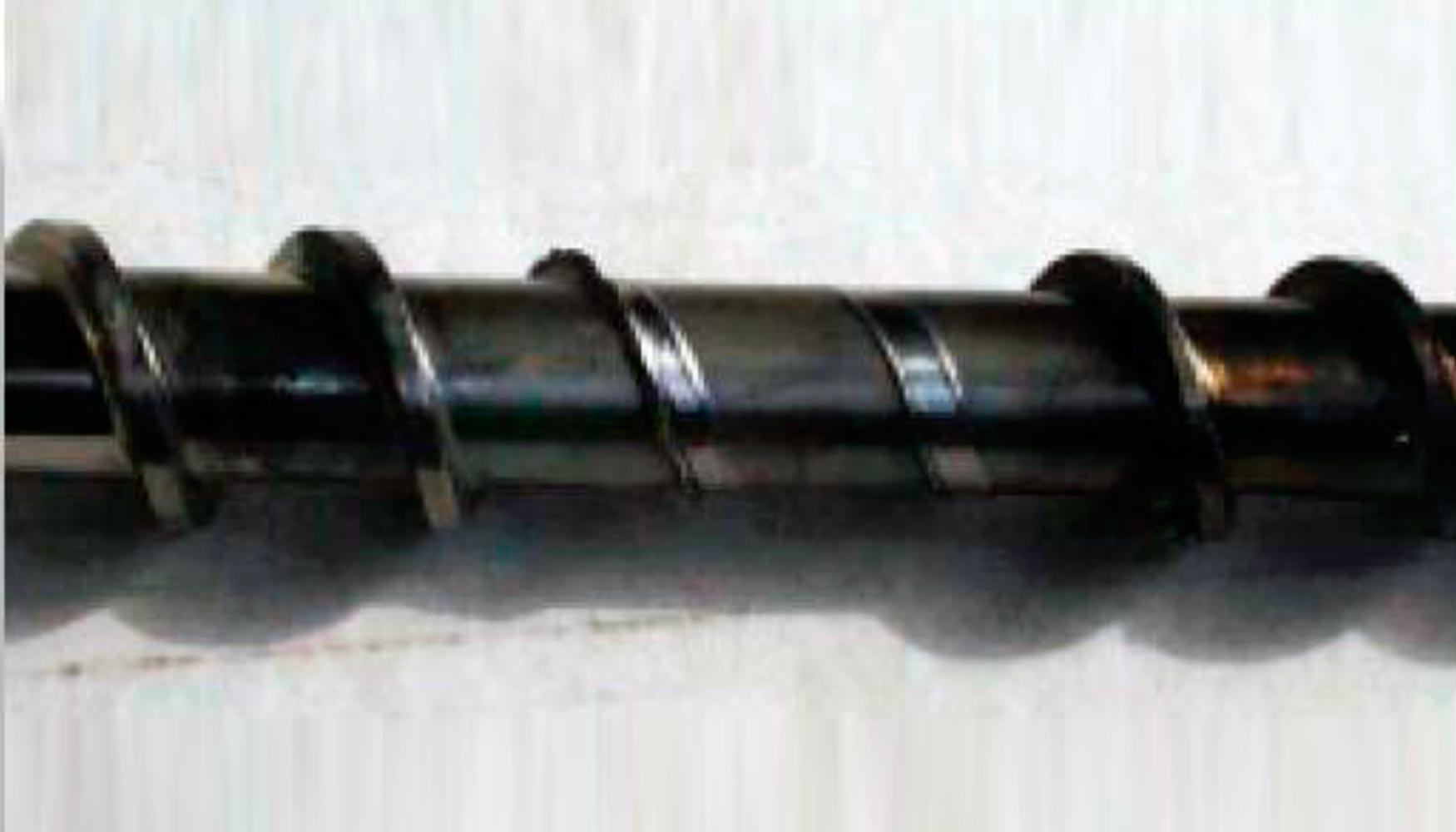
Válvula antiretorno
Elemento mecánico que evita el retorno del material hacia la parte trasera de la unidad de inyección durante la fase de inyección pero por el contrario permite el avance del material hacia la zona delantera del husillo durante la fase de dosificación.
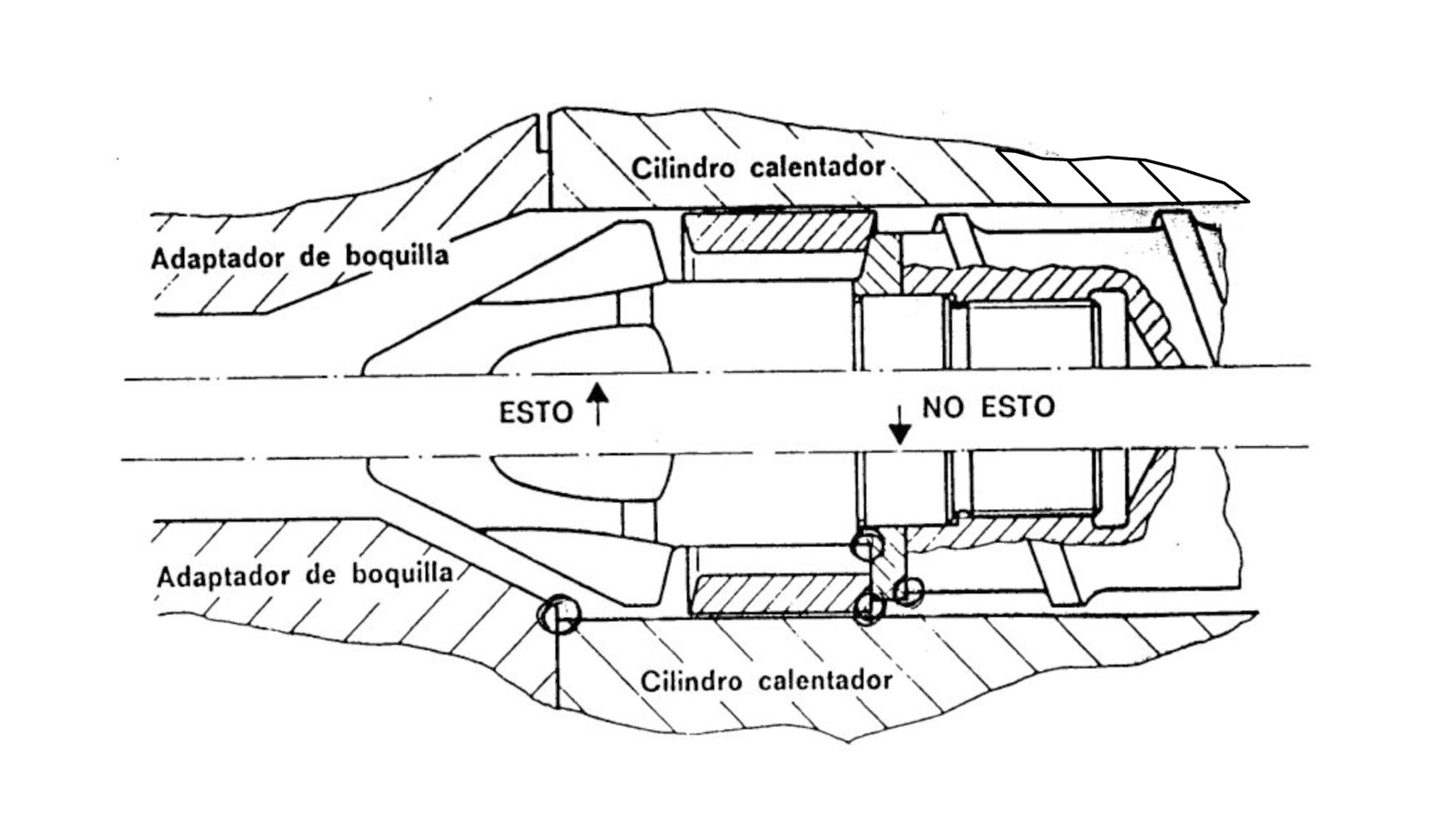
La válvula antiretorno debe ser con forma “aerodinámica” y no tener en ningún modo cantos vivos o ángulos muertos que pudieran dar lugar a retenciones de material.
La válvula antiretorno es un elemento crítico de la unidad de inyección. En el mercado existen diferentes tipos.
Válvula de casquillo o anillo de cierre (ver foto abajo)
- La más utilizada
- Buenas prestaciones en las purgas y cambios de color
- Optimo paso de flujo y características de cierre o sellado
Válvula de bola
- Estrecha dispersión de pesos entre inyectadas
- Especialmente recomendada para bajas velocidades de inyección
- Durabilidad
Válvula de bola interna
- Bajo desgaste
- Recomendada para grandes diámetros de husillo.
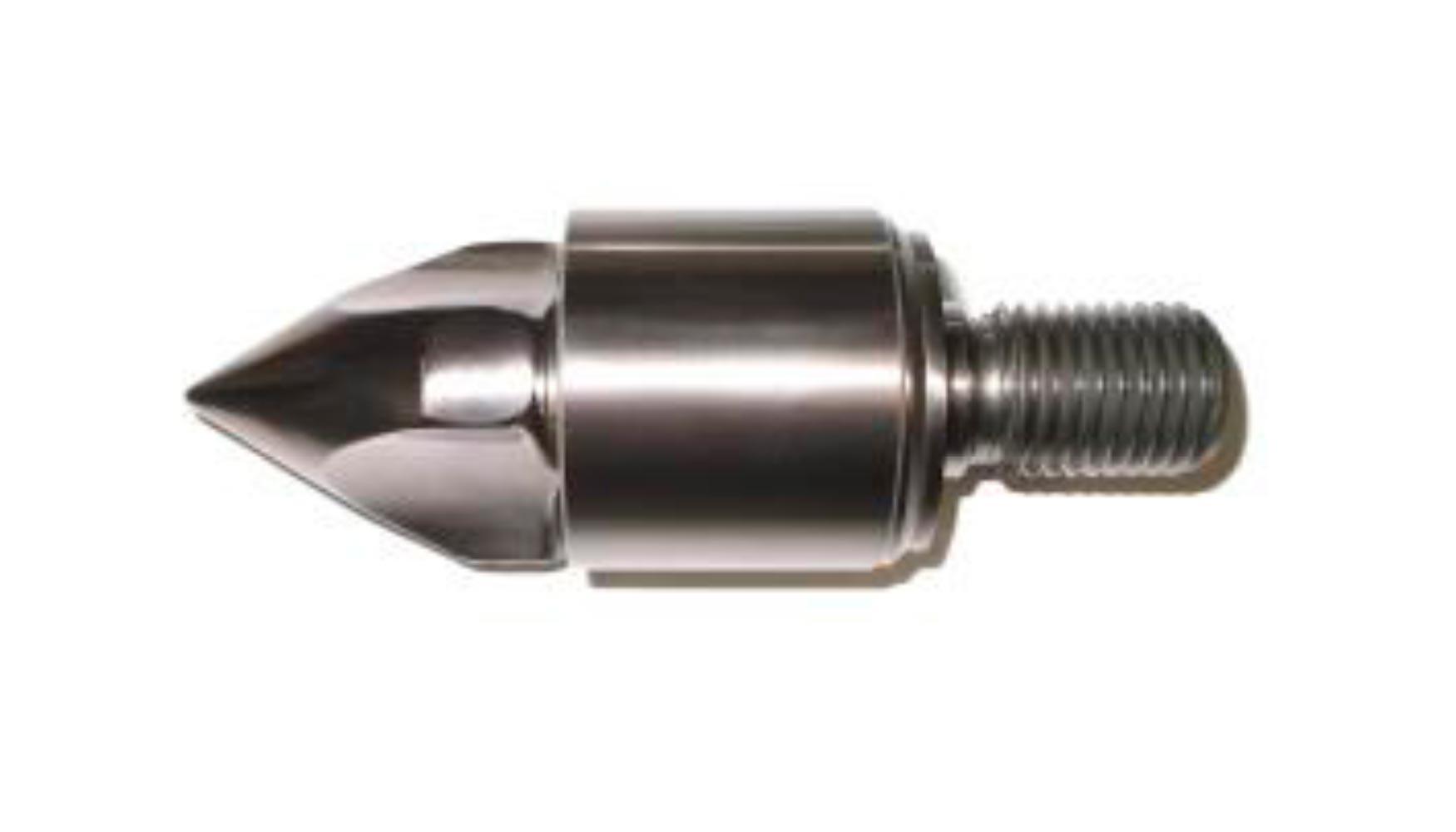
Los problemas que se pueden generar son:
- Dificultad para mantener estable el cojín de material
- Tiempos de dosificación largos e irregulares
- Contracción excesiva en las piezas
- Puntos negros quemados en el material
- Ráfagas en la superficie de las piezas
- Variación de las dimensiones de las piezas
Este elemento debe ser cuidadosamente controlado dentro del plan de mantenimiento para detectar desgastes o falta de estanqueidad.
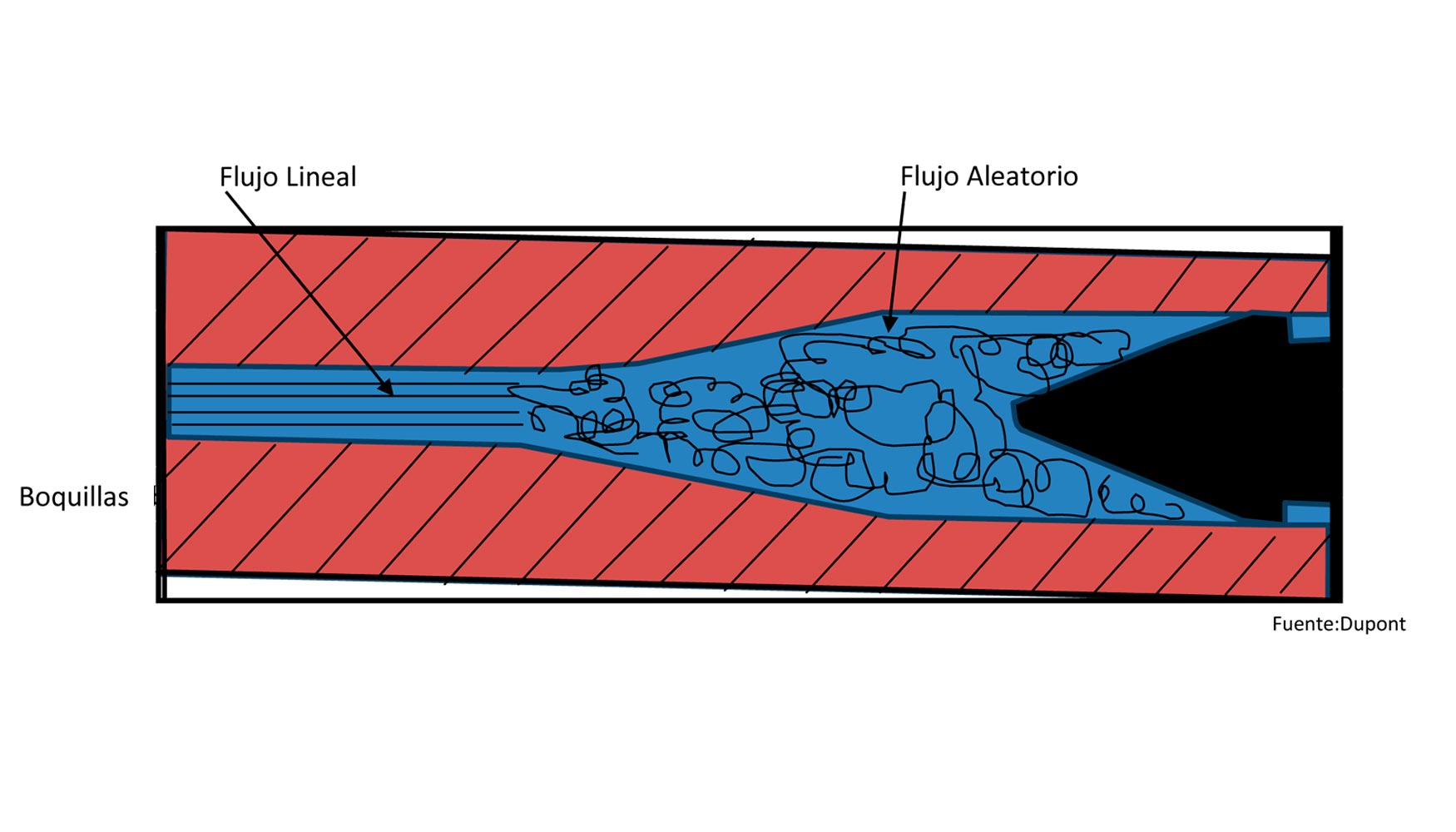
El flujo del material en la cámara de plastificación
En la imagen se puede observar la diferencia de flujo aleatorio en la zona del husillo y punta de husillo y el flujo laminar que se produce en la zona del portaboquillas y boquilla. En este caso un problema de retención o degradación del material en la zona de flujo laminar es muy probable que aparezca siempre en la misma posición de la pieza.
José Ramón Lerma es autor del Libro Manual Avanzado de Inyección de Termoplástico, que tiene como objetivo ser, por un lado, una herramienta para la formación y, por otro, un manual de ayuda para todo el personal de una empresa de inyección de plásticos. El libro, comercializado por Plásticos Universales / Interempresas (libros@interempresas.net), consta de detallados casos prácticos, amplia información de moldeo científico y un ‘pendrive’ con 20 hojas de cálculo y herramientas de SC Molding o Scientific Injection Molding, además de optimización y definición de proceso, lo que lo hacen único en el mercado. Página web sobre Scientific Injection Molding: www.asimm.es
Más información sobre los cursos Scientific Molding online impartidos en Inefco, en los que José Ramón Lerma es tutor https://www.ieaula.com/home/31-procesos-avanzados-de-inyeccion-de-termoplasticos.html