Los composites poseen muy buenas propiedades mecánicas y alta resistencia a la corrosión
Composites en automoción: pultrusión para grandes volúmenes de fabricación
Los materiales idóneos para llevar a cabo este cambio y reemplazar a los tradicionales metales son los composites (resinas termoestables combinadas con fibras de vidrio o de carbono). Los composites poseen muy buenas propiedades mecánicas y alta resistencia a la corrosión, todo esto combinado con un bajo peso. De hecho, el reemplazamiento de piezas de acero por composites representaría una reducción del peso del vehículo de un 40%. Aunque el consumo de plástico reforzado con fibra de vidrio en la industria del transporte es de unas 350.000 toneladas al año, habiendo sido introducido en diferentes áreas de los vehículos, la penetración de los composites en piezas estructurales es aún testimonial, ya que solo se utilizan en prototipos de coches. El uso extensivo de estructuras de composites garantizará que estos vehículos sean más ligeros que los de hoy en día.
La falta de automatización a la hora de procesar composites es la principal barrera para conseguir un alto volumen de fabricación en la industria automovilística, lo que incrementa sus costes. Entre todos los procesos de producción de composites, el más automatizado, eficiente y competitivo para obtener secciones de composites constantes es el conocido proceso de Pultrusión (figura 1). Actualmente, la tecnología de pultrusión consiste en la formación de fibras impregnadas con resina en un molde (la impregnación se lleva a cabo en un depósito abierto o por inyección). El molde es también responsable del curado de la resina a través de un sistema de calefacción (frecuentemente mediante resistencias al calor). Unas prensas van tirando del perfil curado y al final este perfil se corta, mediante una sierra movible según la largura deseada.
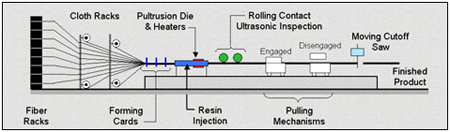
A pesar del alto grado de automatización de este proceso, todavía se han de abordar aquellos inconvenientes que reducen la competitividad de los perfiles pultrusionados comparados con otros materiales tradicionales. Por un lado, el proceso está limitado debido al tiempo que requiere la polimerización de la resina dentro del molde, por lo que es un proceso muy lento. Por otro lado, cuando se necesitan mejorar las propiedades del perfil aplicando un recubrimiento, la superficie del perfil debe prepararse cuidadosamente mediante procesos adicionales: principalmente lijado y pintado; procesos costosos ya que necesitan elevada mano de obra y son procesos contaminantes (compuestos orgánicos volátiles y partículas en suspensión).
Con el objetivo de resolver este problema, el proyecto Coaline, que recibe fondos del Séptimo Programa Marco de la Unión Europea (FP7/2007-2013), bajo acuerdo de subvención n° 609149 y está coordinado por Aimplas, empezó en septiembre del 2013. El principal objetivo del proyecto CoalinE (cuyo título es: ‘desarrollo de procesos innovadores de fabricación para el recubrimiento en línea de composites pultrusionados’) es conseguir un proceso limpio, en una sola etapa (en el interior del molde), libre de compuestos orgánicos volátiles (COVs) y de emisiones de pequeñas partículas. Este proceso será capaz de producir perfiles pultrusionados de composites adecuadamente recubiertos, utilizando para ello tecnología de detección (sensores), un avanzado diseño del molde y un curado con ayuda de microondas con el fin de mejorar la adhesión del composite/recubrimiento a un coste más reducido (figura 2.). Además, los perfiles de Coaline se unirán a otros materiales mediante la utilización de un primer, también incorporado en línea, y de adhesivos con propiedades de unión según demanda.
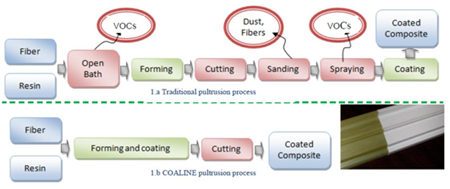
Los principales sectores de aplicación en los que Coaline se centra son la construcción y la automoción (piezas de coches eléctricos). El consorcio del proyecto está compuesto por 2 institutos de investigación (Aimplas, Fraunhofer), 1 Universidad (Riga Tehniska Unniversitate – Universidad Técnica de Riga), 2 socios industriales (Acciona, Muegge) y 7 Pymes (Alkè, Composites Aragón, Ecoinnova, Polymec, Resoltech, Rescoll, Synthesites).
Los procesos innovadores desarrollados en Coaline reducirán considerablemente el número de etapas necesarias y las emisiones de gases y partículas para obtener un composite recubierto de alta calidad mediante la integración de procesos de formado, recubrimiento y acabado en un solo paso. Por esta razón, se producirán materiales composite aptos para sustituir a los tradicionales metales en partes estructurales de vehículos, lo que reducirá el peso, el consumo de gasolina y las emisiones de COVs y partículas en suspensión. Además, la reducción del tiempo de producción de perfiles recubiertos de altas prestaciones permitirá el alto rendimiento y la continua producción que demanda la industria automovilística.
Coaline tiene previsto abordar la producción de valiosos perfiles recubiertos, reduciendo su coste muy significativamente (hasta el 35%) y el número de etapas del proceso, aumentando en gran medida la producción y mejorando la calidad en comparación con el estado de la técnica actual de perfiles recubiertos. Todo esto se conseguirá gracias a las siguientes innovaciones:
- Nuevo diseño de moldes en varias etapas con polimerización de la resina y del recubrimiento separados en una estructura con varias cavidades.
- Un sistema de calentamiento por microondas dentro del molde que reducirá el tiempo de polimerización y la energía utilizada para producir los composites. El sistema de microondas será aplicado independientemente del tipo de fibras empleadas para la producción de los composites (vidrio o carbón).
- Una nueva variedad de resinas y de gel-coats modificados con aditivos absorbentes de las microondas para mejorar la absorción de la radiación y conseguir un proceso de curado más rápido.
- Un innovador sistema de sensores para promover la adhesión del recubrimiento al composite mediante un control del grado de curado en cada etapa del proceso.
- Mejora de las condiciones de trabajo, minimizando las emisiones de los componentes orgánicos volátiles mediante la inyección de resina y recubrimiento directamente dentro del molde y evitando los procesos de post-fabricación de la superficie del composite.
- El desarrollo de nuevas formulaciones de primers de rápido curado que permitan la utilización de adhesivos con propiedades de despegue a la carta para promover la unión entre composites y partes metálicas, además del reciclado y el mantenimiento de estructuras pultrusionadas.
Resumiendo, este proyecto representa un paso adelante en el aumento del rendimiento del vehículo debido por una parte a la reducción del peso (lo que implica que se necesitará menos energía para mover el vehículo, habrá una menor tensión ejercida en el marco, mayor flexibilidad de éste, mayor capacidad de carga, etc.) y la obtención de recubrimientos con especificaciones mejoradas, lo que proporcionará beneficios al operar en ambientes críticos o corrosivos. Todas estas ventajas de los composites se lograrán a unos costes competitivos, gracias al aumento en la automatización del proceso de fabricación de composites que tanto los productores de composites como la industria automovilística necesitan para progresar juntos.