Entrevista a Joaquin Moliner, director general de ATI Systems
ATI System es una firma especializada en la distribución de periféricos para la industria de la transformación de plástico, además de solucionar problemas técnicos en los procesos de producción y ofrecer, entre otros, un servicio técnico tanto para el mantenimiento como para la reparación de averías de las máquinas de inyección y periféricos. Ahora, además de su cartera de firmas representadas del sector de los periféricos, recientemente ha añadido dos nuevas marcas: Plastic Metal y los robots de Tecnomatic. Todo ello hace que la empresa ofrezca al mercado tecnología para satisfacer demandas exigentes como in mould labelling, alta precisión y todo ello consiguiendo importantes ahorros energéticos.
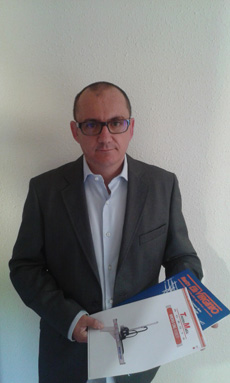
Ati System lleva desde 2003 en el sector de la inyección, ¿cómo ha sido la evolución del sector hasta hoy?
La evolución del sector es continua desde el año 2003 hasta 2007 siguiendo una tendencia que se veía reflejada con la situación económica de aquella época. A partir del año 2007 el sector modifica su tendencia habitual de sustituir la maquinaria obsoleta por nuevos equipos y se centra en mantener y mejorar con el mínimo coste sus unidades de producción. Nosotros nos adaptamos al cambio con el programa de ahorro energético y el plan renove, reduciendo los costes de nuestros clientes hasta tal punto que se convierten en beneficios.
Ustedes son distribuidores de la gama de Plastic Metal, ¿qué productos de esta firma ofrecen al mercado?
Ofrecemos al mercado toda la gama de maquinaria de inyección Plastic Metal, que dispone de una gran variedad de modelos y tonelajes. Desde la innovadora tecnología hibrida pasando por la convencional denominación ‘'Unyka’', hasta llegar a sistemas de multi inyección y PET. Incluida maquinaria de ocasión que el fabricante tiene en stock.
¿Cómo definiría el producto de Plastic Metal frente a otros del mercado?
Es un producto europeo de alta calidad que desde sus inicios en 1954 a hecho gala de su fiabilidad y su innovación tecnológica. Estas máquinas disponen de multiples aplicaciones llave en mano en las que se integran máquina y automatización para llevar a cabo proyectos de la manera más eficiente. Las unidades que tenemos trabajando en España no dan problemas, son máquinas robustas, fiables y tecnológicamente avanzadas, que se combinan perfectamente con el sistema de ahorro energético desarrollado por nosotros logrando unos resultados impecables.
Otra de sus líneas de negocio es el suministro de periféricos, ¿qué productos ofrecen a los transformadores?
Somos distribuidores de la firma Fratelli Virginio, una firma italiana con un largo recorrido en el sector del plástico y la automatización de sus procesos. Año tras año y con paso firme a logrado llegar a situarse entre las marcas punteras en el mercado europeo. La gama de periféricos es muy extensa, disponemos de cintas transportadoras, molinos, dosificadores de master, elevadores de material, deshumificadores, refrigeración… con una gran calidad y un precio muy competitivo.
Recientemente han adquirido nuevas representadas como los robots de Tecnomatic, háblenos de ellos. ¿Qué capacidades tienen y para qué aplicaciones?
Tecnomatic es una firma de robots que ha demostrado mucha fiabilidad y profesionalidad, donde el desarrollo y la innovación de sus productos ha ido en aumento desde 1987 consiguiendo el mejor resultado en todos sus proyectos. Dispone de una gama muy extensa de robots y extractores de colada para todo tipo de procesos y máquinas de inyección. Desde recoger pequeñas piezas o extraer la colada hasta llevar a cabo procesos de etiquetaje o inserción dentro del molde.
Esta seguridad que nos da la marca nos permite automatizar gran parte de la producción consiguiendo entregar al cliente el proyecto completamente resuelto y reduciendo nuestros costes considerablemente.
Tienen también robots especializados para el in mould labelling. Háblenos de una de sus últimas novedades.
El IML se trata de un proceso para etiquetar las piezas producidas dentro del molde. Es una tecnología que incorpora Tecnomatic para llevar a cabo proyectos en sectores diversos como el alimentario, el farmacéutico, el sector del juguete entre otros. Con esto conseguimos que el producto quede prácticamente acabado librándonos de costes adicionales y reduciendo el tiempo de producción.
También del Grupo NPM, esta vez para el transporte y automatización, también ofrecen los productos de la gama Filli Virginio, ¿qué incluye la gama? Háblenos de alguna novedad.
Como ya hemos apuntado anteriormente, la gama de Fratelli Virginio es muy extensa. Nosotros nos centramos en la problemática y diseñamos el sistema de automatización más eficaz para cada caso. También añadimos sistemas de detección de metales a estos sistemas de automatización para hacer el proceso mucho más completo y eficiente.
En cuanto a la robótica, ¿están suficientemente automatizadas las plantas de producción en España?
Creemos que falta mucho por automatizar, todo proceso es automatizable. El sistema de caída de pieza habitual debe quedar en el pasado, recoger las piezas con robot garantiza la estabilidad del ciclo, la ausencia de golpes en las piezas, la limpieza e higiene del proceso, el que todas las piezas se depositen correctamente en embalajes o en cintas.
Y lo más importante al fin y al cabo una reducción de costes y un aumento de agilidad y productividad en todo el proceso.
Uno de los objetivos del sector del plástico es dar con la fórmula que les aporte importantes ahorros energéticos, ¿qué soluciones propone Ati System para que el inyectador logre estos objetivos?
Nosotros apostamos por un desarrollo económico sostenible, en 2007 empezamos a gestionar y a desarrollar este ámbito para ajustarnos a las necesidades productivas y abaratar al máximo los costes. Disponemos de nuestros sistemas de ahorro energético, para aplicar en máquinas de producción, basados en la tecnología de variador de frecuencia, y de un nuevo sistema basado en la aplicación de servo-motores en las bombas hidráulicas. Ambos sistemas ofrecen unos resultados sorprendentes, aunque por motivos de amortización se demanda mas el sistema de variadores.
Defina qué es un sistemas de ahorro energético que ustedes instalan en máquinas y qué porcentajes de ahorro permiten…
Con una firma líder en tecnología puntera como es Delta Electronics y un software/hardware desarrollado por ATI System conseguimos reducir el consumo energético de maquinas inyectoras y prensadoras entre un 25% y un 65% dependiendo de cada caso.
Las ventajas competitivas hablan por si solas, optimizamos la velocidad incrementando la eficiencia del motor y reduciendo el consumo de energía reactiva en un 90%. Tambien hay menos necesidad de refrigeración y una notable reducción de la contaminación acústica. También gracias al sistema start-stop se genera un beneficio mecánico debido a que el motor alarga su vida útil al disminuir el tiempo de funcionamiento. Por lo tanto la maquina íntegramente aumenta la productividad y alarga la durabilidad. Tenemos equipos instalados en España y en el emergente mercado de América latina.
Sistemas de ahorro energético E-Servosystems, del fabricante Delta, permiten ahorros superiores al 30% y mejorando el ahorro que obtendríamos con el sistema
E-Saving.
Pero no sólo se pueden instalar en inyectoras, sino también de compresores, trituradores y bombas de refrigeración….. ¿es así?
Sí, actualmente hemos instalado en muchos y diversos equipos, también incluidas inyectoras de aluminio y prensas hidráulicas consiguiendo resultados muy buenos.
¿Realizan sistemas de llave en mano? Si es así, ¿pueden explicar algún caso?
Hemos realizado proyectos llaves en mano para proveedores de taponería cosmética, y desarrollado maquinaria para el ensamblaje de distintos componentes pero por motivos de confidencialidad no se nos permite dar mas información de estos proyectos.
¿Qué otros productos distribuyen?
Disponemos de equipos de control de calefacción de moldes con pantalla táctil y archivo de procesos, así como de sistemas de control para boquillas de inyección de molde.