Ejecución de trabajos geotécnicos especiales en la línea 16 del Metro de París
Nicolás Cobo. Ingeniero de caminos, canales y puertos. Project manager en Grand Paris Express. Terratest
Gerardo Marote. Ingeniero de caminos, canales y puertos. Director de ingeniería y recursos. Terratest
08/02/2022Terratest, grupo internacional del sector de la construcción fundado en 1959 y referente mundial en Cimentaciones Especiales, Mejora del Terreno, Túneles y Medioambiente, repasa en este artículo los trabajos geotécnicos especiales que ha realizado en los lotes 1 y 2 del imponente proyecto Grand Paris Express.
1.- Grand Paris Express
Grand Paris Express es uno de los mayores proyectos de infraestructura que se están desarrollando en Europa en estos momentos. Se trata de una operación muy ambiciosa que pretende dotar a la ciudad de París de una solución de transporte multimodal y facilitar un modelo de crecimiento policéntrico. El proyecto consiste en la construcción de una nueva red de metro que conectará barrios periféricos clave sin necesidad de atravesar la ciudad. En cifras, las actuaciones contemplan la construcción de 4 líneas nuevas, 200 km de vía y 68 estaciones, que permitirán transportar a más de 2 millones de pasajeros al día con un intervalo entre trenes que oscilará entre 2 y 3 minutos [1].
Grand Paris Express comprende la construcción de la línea 15, de trazado circular alrededor de la ciudad, y las líneas 16, 17 y 18, que conectarán barrios en pleno desarrollo. Además, el proyecto incluye la ampliación de varias líneas existentes. El conjunto de la actuación proporcionará conexiones fluidas a los tres aeropuertos de París, centros de negocios y zonas de investigación [1].
La pandemia del COVID-19 ha dilatado notablemente el desarrollo de Grand Paris Express. La paralización de los trabajos del proyecto puede originar retrasos en la puesta en servicio de las nuevas líneas de metro, prevista en estos momentos para realizarse de forma progresiva entre los años 2024 y 2030 [2].
2.- Línea 16
La línea 16 de Grand Paris Express comienza en Saint-Denis Pleyel, al norte de la ciudad, y termina en Noisy-Champs, al este. Cuando la línea esté en operación, los pasajeros podrán realizar el trayecto completo de 10 estaciones en tan solo 26 minutos. La línea 16 será un eje principal de desarrollo del este de la ciudad y facilitará la movilidad de unos 800.000 habitantes pertenecientes a 16 municipios [3].
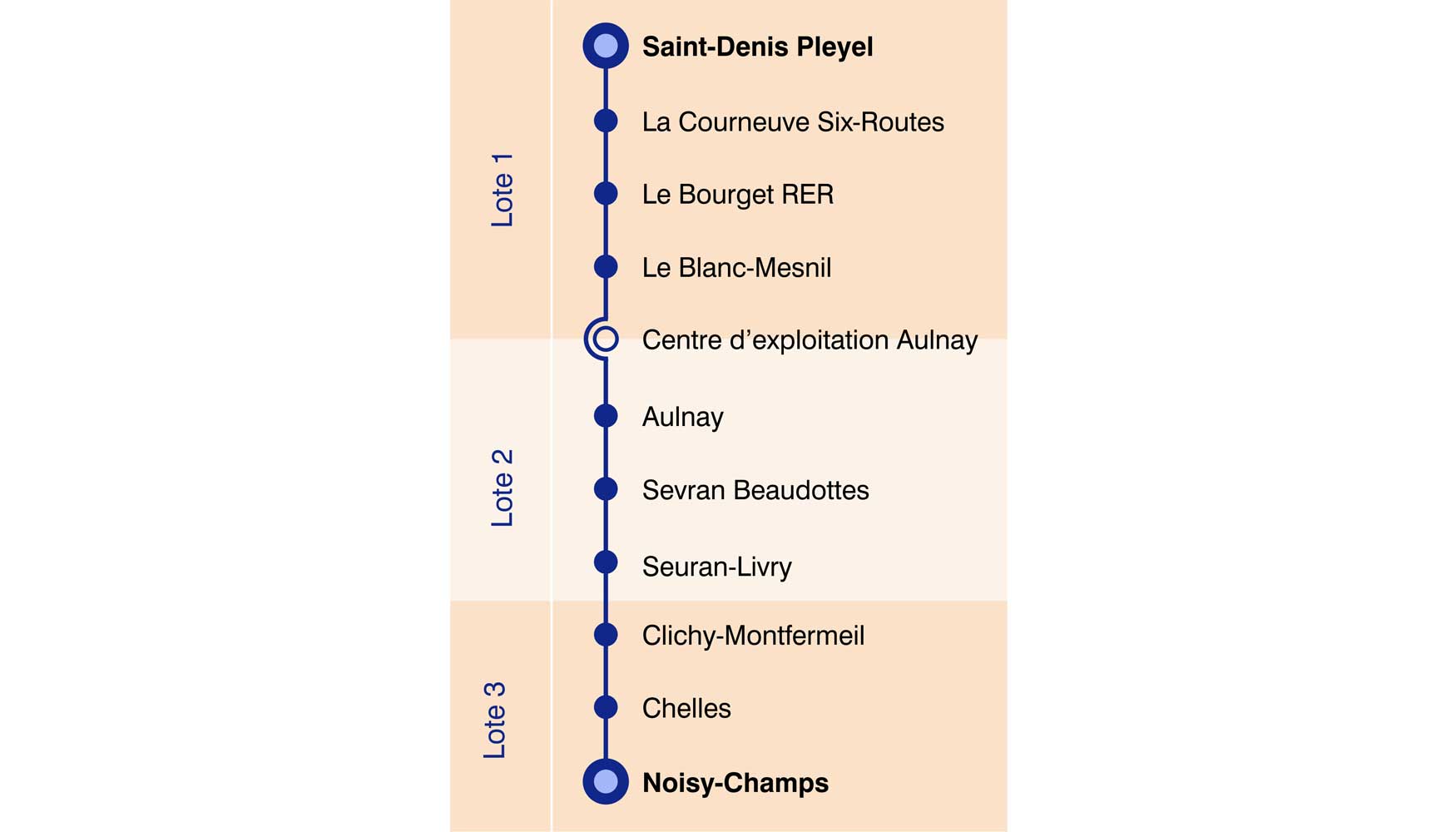
La construcción de la línea 16 se está realizando en tres lotes [4]. El primero comienza en Saint-Denis Pleyel y termina en el Centro de Explotación de Aulnay; el segundo da continuidad hasta la ciudad de Clichy; y el tercero completa la línea en Noisy-Champs y la conecta con el resto de la red de metro.
Terratest resultó adjudicatario de trabajos geotécnicos especiales en los lotes 1 y 2. Fue responsable de realizar las obras para el grupo Eiffage-TSO-Razzel Bec en el primer lote y para Salini Impregilo-NGE en el segundo.
3.- Trabajos geotécnicos especiales
Los trabajos de Terratest en el proyecto comprendieron soluciones integrales de cimentación en 2 estaciones principales, 1 pozo de ataque para la tuneladora y 6 obras auxiliares. En el lote 1, las actuaciones principales se concentraron en la estación La Courneuve Six-Routes, mientras que en el lote 2 el grueso de la operación se llevó a cabo en la estación de Sevran-Beaudottes. Además de estas dos estaciones, se ejecutaron trabajos geotécnicos en las obras auxiliares OA 3303P, OA 3304P, OA 3401P, OA 3402P y OA 0103P en el lote 1, y OA 0504P y OA 0501 P en el lote 2.
Al tratarse de un tramo muy extenso, el perfil geotécnico en cada localización presentó características particulares. Sin embargo, en líneas generales puede considerarse que las obras se ejecutaron en un terreno formado por 5 niveles geotécnicos principales:
- El primer nivel, el más superficial, lo forman un relleno antrópico seguido de un depósito aluvial de composición limosa, en el que se encuentra el nivel freático.
- El siguiente estrato, denominado localmente Calcaire de Saint-Ouen, está compuesto por una roca caliza con un alto grado de meteorización.
- La tercera formación, Sables de Beauchamp, se caracteriza por la alternancia de amplios horizontes arenosos con estratos limosos y arcillosos.
- Una potente capa de margas blandas, parcialmente litificadas, constituyen el cuarto nivel denominado Marnes et Caillasses, en el que también existe intercalación de niveles de yesos sujetos a procesos de disolución.
- Finalmente, el quinto nivel corresponde a la denominada Calcaire Grossier, un horizonte rocoso de caliza masivo, de elevada resistencia y excelentes valores de RQD.
En el contexto geotécnico que acabamos de definir, los trabajos de cimentación consistieron, por un lado, en la ejecución de recintos de muros pantalla de hormigón armado para proteger la excavación de las estaciones y obras auxiliares; y, por otro lado, en la ejecución del conjunto de tratamientos de terreno asociados a estas estructuras. Estos tratamientos de mejora fueron cuatro: el sellado de cavidades y fracturas de terreno para evitar la fuga de lodos durante la ejecución de las estructuras de contención, la creación de barreras de baja permeabilidad bajo el pie de las pantallas, la ejecución de bloques break-in y break-out para permitir el paso de la tuneladora y la consolidación de suelos en las zonas de conexión entre los recintos apantallados y el túnel.
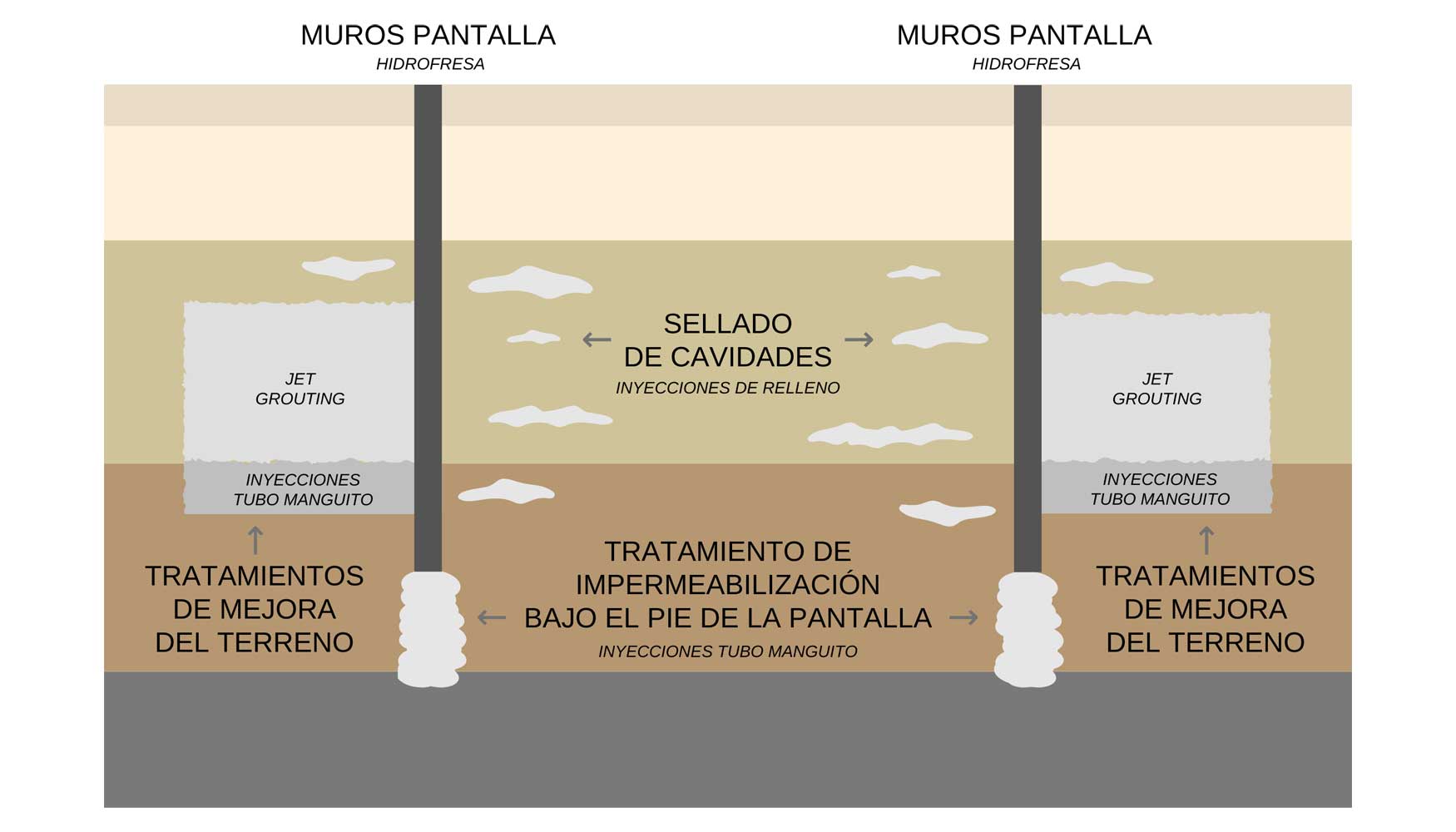
El alcance de los trabajos geotécnicos, en cifras, fue el siguiente:
- 14.000 m de inyección de relleno previa a la ejecución de las pantallas para prevenir las fugas de lodo bentonítico.
- 40.000 m2 de muros pantalla y barrettes con hidrofresa, con espesores de entre 0,60 y 1,80 m, profundidades de hasta 51 m y suministro de 51.000 m3 de hormigón y 5.700 toneladas de acero.
- 5.000 m de inyección de impermeabilización bajo el pie de los muros pantalla.
- 66.000 m de perforación, 8.000 m de inyecciones con tubo manguito y tratamiento de 14.000 m3 de terreno mediante la técnica de Jet Grouting, para la mejora de suelos en túneles de conexión y zonas de entrada y salida de la tuneladora en estaciones y obras auxiliares.
- 6.000 m de inyecciones de compactación para la mejora de la capacidad portante del terreno en la estación de Sevran-Beaudottes.
Entre los desafíos técnicos del proyecto destacaron, entre otros, la ejecución de muros pantalla de 1,80 m de espesor, la construcción de paneles con contrafuertes con una gran densidad de armado y la ejecución de perforaciones inclinadas y profundas en los tratamientos de mejora. Además, todas las técnicas de ejecución que acabamos de enumerar debían ejecutarse en un terreno muy heterogéneo que alternaba suelos de diferente naturaleza con capas de roca, por lo que para optimizar las tareas de perforación fue necesario contar con equipos de diferente categoría y una amplia batería de útiles de excavación capaces de adaptar la ejecución a las particularidades geotécnicas en cada sector. Por último, la gestión global del proyecto supuso un reto constante al desarrollarse todas las actividades al mismo tiempo y en un entorno urbano complejo.
Durante la construcción trabajaron de forma simultánea, en la fase de mayor concentración de obra, 3 equipos de hidrofresa, 3 plantas de fabricación y tratamiento de lodos, 4 grúas auxiliares y 4 equipos de inyección con sus medios auxiliares asociados. Para la operación de este equipamiento fue necesario contar con un equipo humano formado por 65 trabajadores.
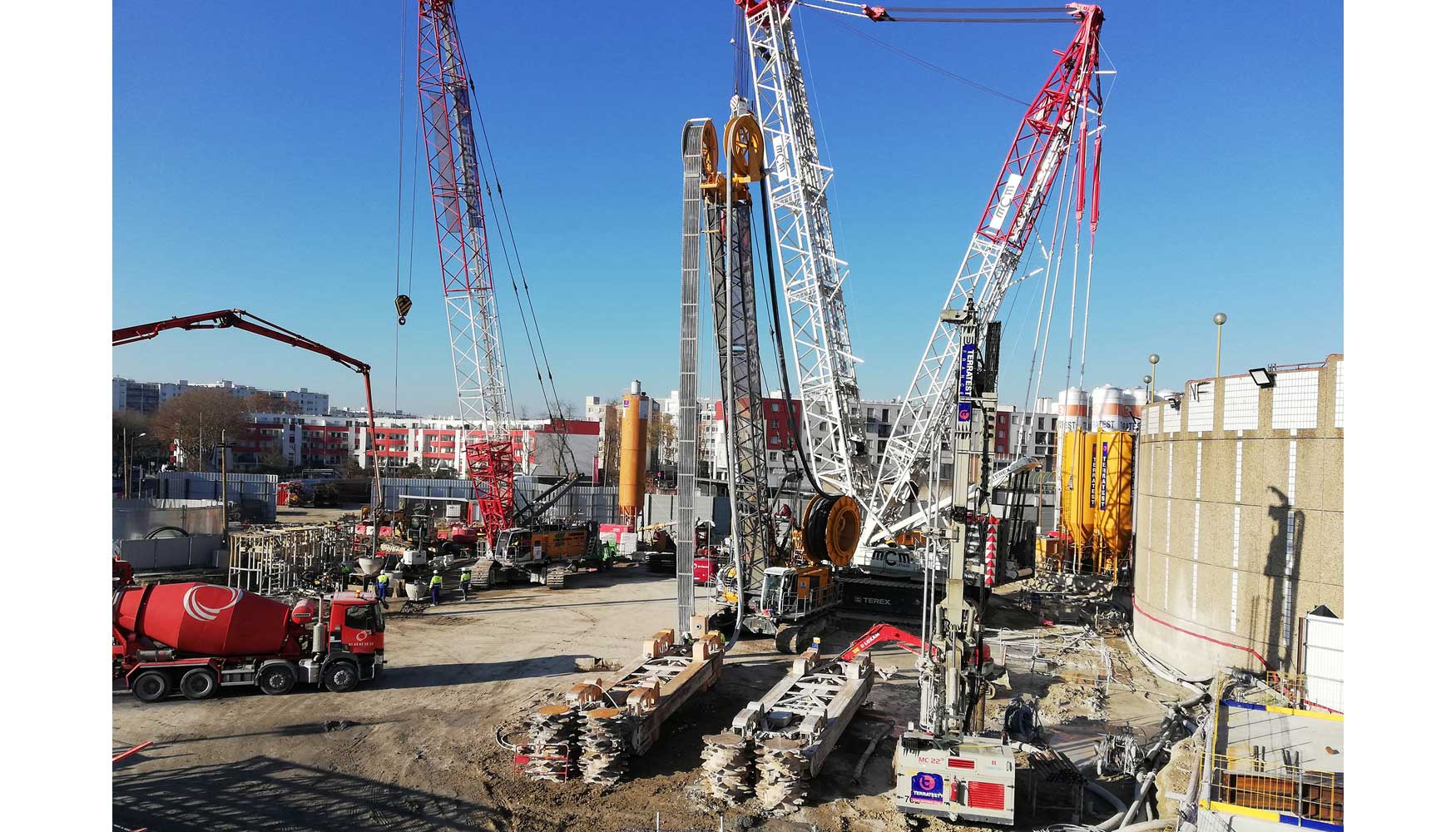
En los apartados siguientes se explican en detalle los aspectos más relevantes de las técnicas de ejecución empleadas.
4.- Inyecciones de relleno con mortero
El estudio geotécnico de proyecto constató la presencia de bancos de yesos en proceso de disolución en las capas denominadas Sables de Beauchamps y Marnes et Caillasses, con una importante proporción de suelo muy descomprimido con presencia de numerosas grietas y cavidades. En estas circunstancias, una pérdida súbita del fluido de perforación durante la excavación de los muros pantalla resultaba muy probable y suponía un riesgo muy elevado para el desarrollo de esta actividad.
Para prevenir esta situación, se ejecutaron inyecciones de relleno con mortero previas a la construcción de los muros pantalla, mediante mallas de perforaciones dispuestas al tresbolillo a lo largo del eje del muro pantalla, retranqueadas 50 cm con respecto a la pantalla y con una separación máxima entre taladros de 1,50 m.
El procedimiento de ejecución de las inyecciones constaba de 3 fases principales:
- En primer lugar, un equipo de perforación articulado realizaba las perforaciones verticales siguiendo la malla definida hasta alcanzar la cota inferior de la capa denominada Marnes et Caillasses. Inmediatamente después de la perforación, se introducía en ella un tubo de PVC de 60 mm de diámetro y superficie lisa hasta la cota de comienzo del tratamiento, el techo de las Sables de Beauchamps. A partir de esa cota, el tubo estaba proviso de ranuras circulares de 38 mm de diámetro, dispuestas cada 30 cm, para permitir el paso del fluido de inyección.
- La segunda etapa del tratamiento consistía en la inyección por gravedad de un mortero de relleno fabricado en obra con una fórmula específica que incluía, por un lado, una alta proporción de arena con respecto al cemento para favorecer la colmatación de cavidades y, por otro, incorporaba los componentes necesarios para obtener unos niveles de viscosidad compatibles con el bombeo del material. Además, el mortero era aditivado con bentonita para reducir sus niveles de decantación. La inyección se realizaba con bombas de pistón dual que enviaban el mortero al interior del tubo de PVC, de forma que el material fluía radialmente a través de las ranuras dispuestas y rellenaba las fisuras que encontraba a su paso. La inyección de mortero, realizada por gravedad, concluía una vez detectada la resurgencia del material en superficie.
- Debido a la retracción del mortero de relleno durante su fraguado, era necesario realizar una tercera fase de tratamiento denominada 'inyección de sellado'. Pasados 7 días desde la primera operación de relleno, un segundo mortero más fluido y con mayor proporción de cemento era inyectado a presión a través de los mismos tubos empleados para el relleno. Para ello, se instalaba un obturador simple y un manómetro en la cabeza del tubo de inyección y se efectuaba la inyección de sellado hasta alcanzar una presión de 5 bares.
Una vez finalizadas las inyecciones se ejecutaron perforaciones de control a lo largo del eje del tratamiento y se rellenaron con lodo bentonítico. En todas ellas se verificó que el nivel de lodo se mantenía constante a lo largo del tiempo, hecho que permitió afrontar la ejecución de los muros pantallas en condiciones de seguridad.
5.- Muros pantalla con hidrofresa
Los muros pantalla de estaciones y obras auxiliares se realizaron mediante la tecnología de hidrofresa. Esta técnica es la más adecuada para ejecutar pantallas profundas, realizar excavaciones en terrenos duros o rocas y respetar tolerancias estrictas de verticalidad; características que se combinaban en todas las actuaciones de la línea 16.
El proceso de excavación con hidrofresa, al contrario de lo que ocurre en los sistemas convencionales, es continuo, es decir, no es necesario extraer el útil de excavación de la zanja durante la perforación. Mediante el envío de lodo bentonítico desde la planta de fabricación y desarenado, se establece un circuito cerrado en el que la hidrofresa tritura el terreno, lo mezcla con el lodo y bombea la mezcla lodo-detritus a la central para la separación del material de excavación y el reciclado del fluido de perforación.
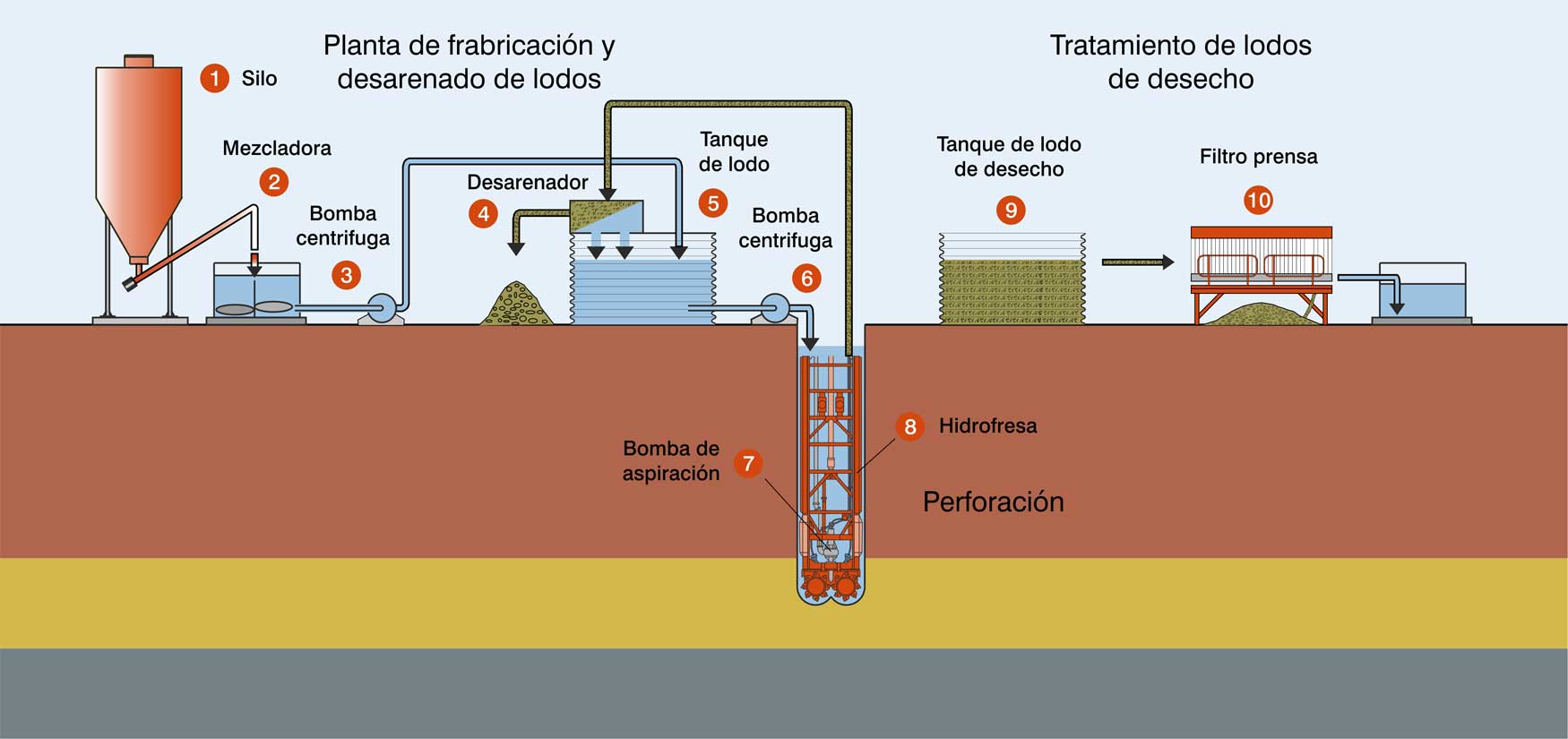
La clave de esta tecnología es el propio equipo de hidrofresa, que se fundamenta en una estructura pesada de acero provista en su parte inferior de dos ruedas de corte. El peso del bastidor, superior a 35 toneladas, en combinación con el elevado par de rotación aplicado por las ruedas, convierten a este equipo en el único capaz de excavar de forma eficaz pantallas en terrenos de alta resistencia (Terratest ha ejecutado con éxito numerosos proyectos en sustratos rocosos con más de 150 MPa de resistencia a compresión simple). Por otro lado, la continuidad de la excavación posibilita la ejecución de pantallas de gran profundidad (existen en la actualidad equipos diseñados para realizar excavaciones de hasta 250 m). Para garantizar la verticalidad de pantallas profundas, la hidrofresa incorpora inclinómetros, un ordenador de control en cabina y escudos hidráulicos que permiten corregir desviaciones instantáneas de la excavación en tiempo real.
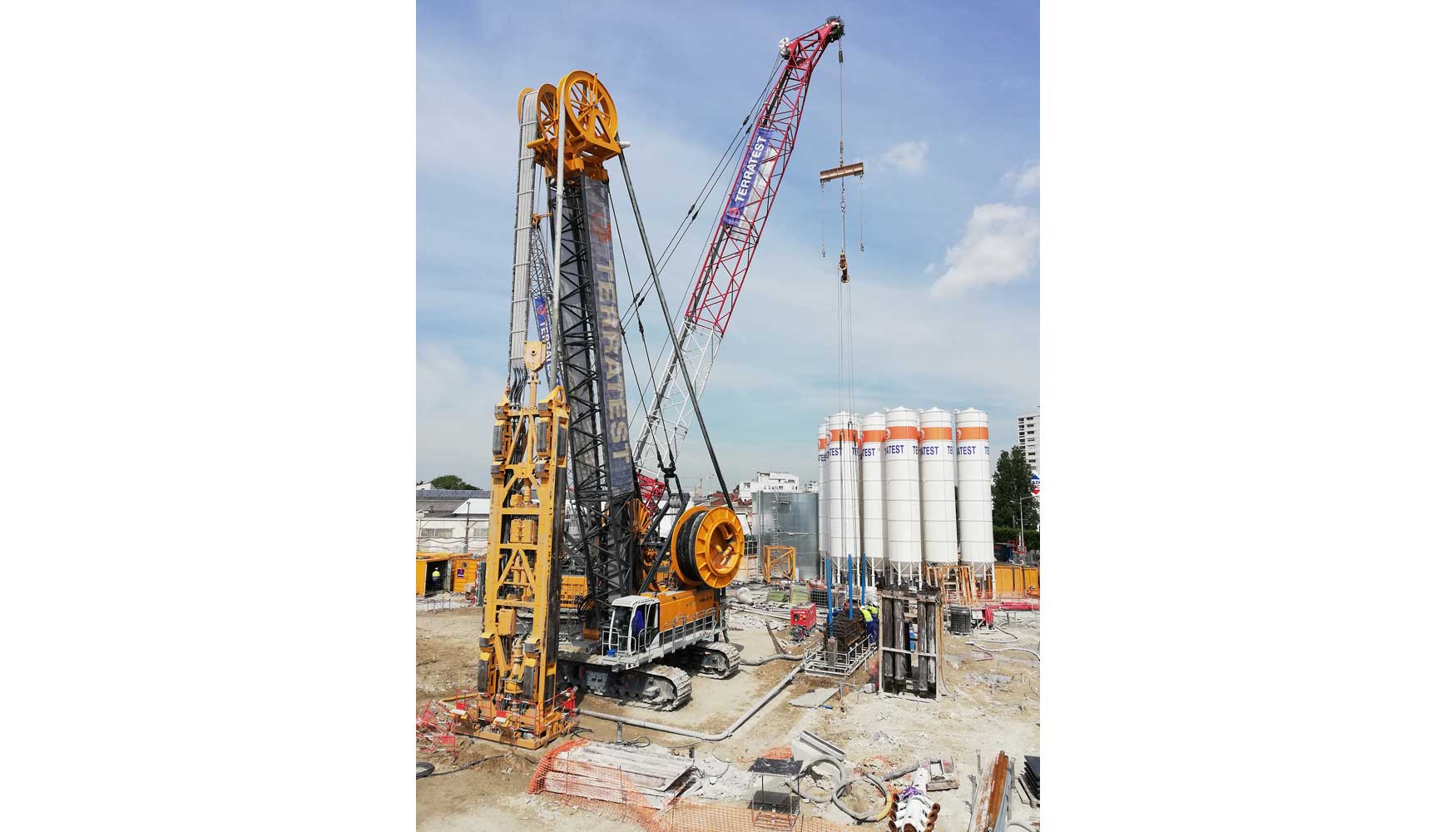
El proceso completo de ejecución de pantallas con hidrofresa consta de las siguientes fases: excavación del módulo de pantalla hasta la cota definida en proyecto, limpieza del fondo de la excavación, desarenado de los lodos de perforación, colocación de jaulas de armadura y hormigonado. El control de los lodos de perforación durante todas las etapas de construcción resulta fundamental para garantizar la calidad final de los trabajos. Es necesario monitorizar sus propiedades fisicoquímicas de forma continua y verificar que en todo momento son compatibles con las funciones del lodo como medio de estabilización de la zanja, vehículo de extracción del material de excavación y fluido refrigerante de los útiles de corte. Los lodos que no cumplen con las especificaciones requeridas son desechados y tratados en obra mediante filtros prensa que convierten el fluido sobrante en materia sólida y agua limpia.
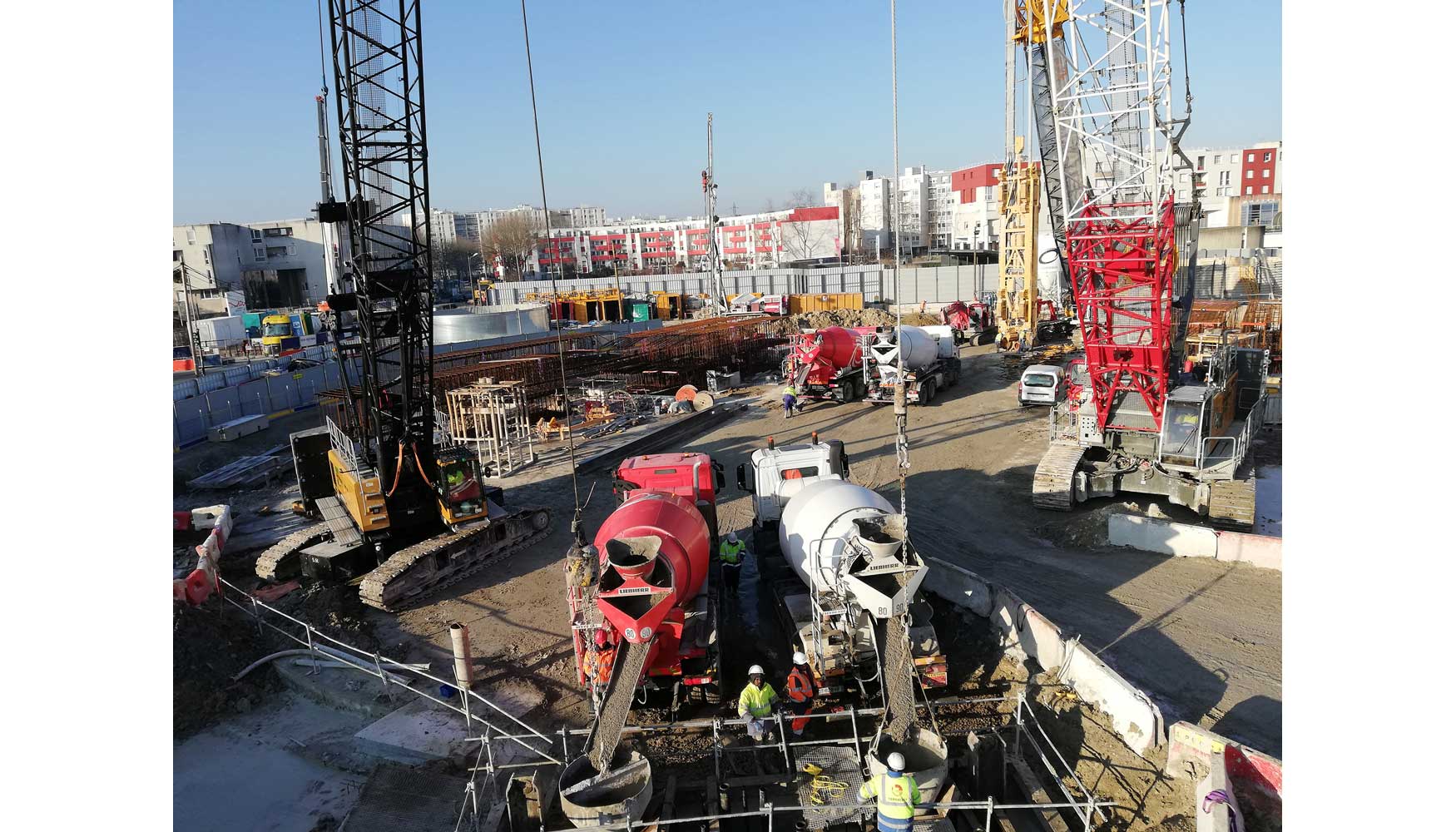
Los muros pantalla ejecutados en la línea 16 alcanzaron profundidades de hasta 51 m y atravesaron numerosos sustratos competentes con puntas de resistencia a compresión simple de 65 MPa. Además, las pantallas tuvieron que adaptarse a diferentes tipos de alineaciones: rectas en casi todas las secciones de las estaciones, circulares en las obras auxiliares y con contrafuertes en zonas singulares.
En la estación de Sevran-Beudottes, por ejemplo, se construyeron 4 módulos de 51 m de profundidad dotados de contrafuertes, con características muy singulares [5]. Estos elementos requerían la instalación de una armadura de acero en forma de 'T' cuyas dimensiones y peso resultaban excepcionales en el ámbito de las cimentaciones especiales. Las armaduras presentaban hasta 9 niveles de barras longitudinales de diámetro 40 mm y alcanzaban una cuantía media de acero superior a los 500 kg por m2 de pantalla. La instalación de estas jaulas se llevó a cabo con un sistema de pletinas metálicas de rigidización integrado en los módulos de armadura que permitía su montaje, transporte a obra e instalación sin que las jaulas sufriesen deformaciones. A su vez, el sistema incorporaba los elementos necesarios para el izado, unión y soporte de los módulos dentro de la excavación del contrafuerte. El conjunto alcanzaba un peso total de 190 toneladas, lo que requirió la movilización de 2 grúas de 1.000 toneladas de capacidad. Para la instalación de estos elementos tan pesados y voluminosos, fue necesario desarrollar un procedimiento de ejecución muy específico que suplementaba las medidas de seguridad habituales y permitía realizar toda la secuencia de operaciones con la máxima precisión.
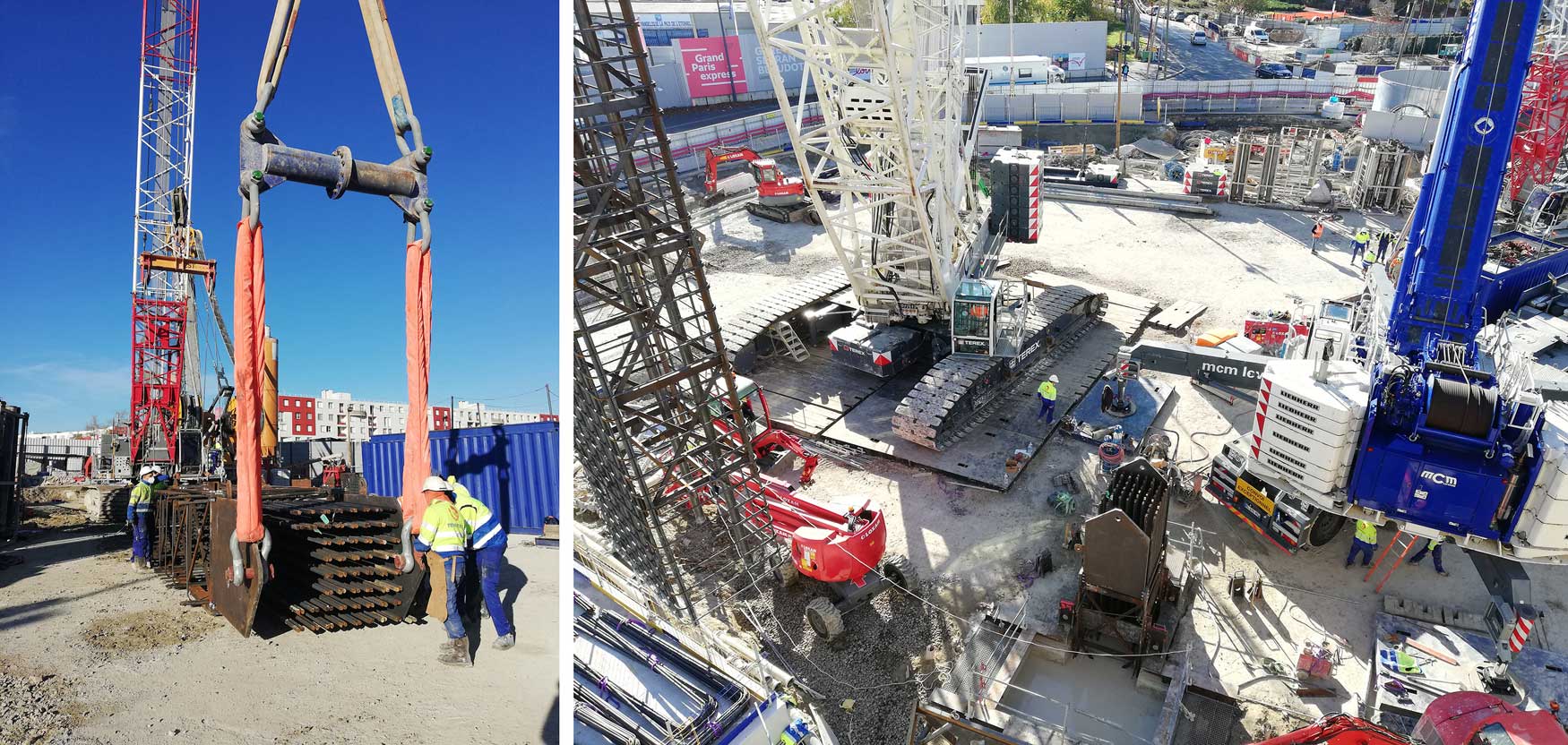
6.- Inyecciones con tubo manguito bajo el pie de la pantalla
Debido a que el diseño de las pantallas no contemplaba su empotramiento en el sustrato rocoso, se realizó un tratamiento de inyección bajo el pie de estas con objeto de crear una barrera impermeable que impidiera la circulación de agua bajo el recinto apantallado y hacia el interior de las estaciones y obras auxiliares durante su excavación. Para ello, se dispusieron tubos de reserva metálicos embebidos en el hormigón de los paneles de muro pantalla que daban acceso a la base de la estructura y permitían la perforación e inyección bajo la pantalla, desde su pie hasta el sustrato rocoso impermeable.
Las inyecciones se realizaron en dos fases. En primer lugar, se llevaron a cabo perforaciones desde la cota inferior de la pantalla hasta alcanzar un empotramiento de al menos 1 metro en el sustrato rocoso. Las perforaciones se realizaron con una perforadora hidráulica articulada desde la superficie y a través de los tubos de reserva embebidos en la pantalla. Como útiles de perforación se emplearon triconos de 114 mm de diámetro equipados con dientes de widia para permitir la penetración en la roca. Una vez alcanzada la cota final de la perforación, el agua utilizada como fluido de perforación se reemplazaba por una lechada de sellado de baja resistencia y se procedía a la inmersión de los tubos de inyección de PVC dotados de válvulas de goma antirretorno cada 30 cm, a través de las cuales se realizaba la inyección. A estos tubos se les denomina comúnmente 'tubos manguito'.
El proceso de inyección constituía la segunda etapa del tratamiento. El método de inyección empleado fue IRS (inyección repetitiva selectiva), en el que el empleo de un doble obturador permitía independizar la válvula del tubo a través de la cual se ejecutaba la inyección. El material inyectado fue una lechada de cemento elaborada en obra, aditivada con bentonita con el objetivo de reducir su decantación, limitada al 3% a las 3 horas. Con el procedimiento IRS se ejecutaba una primera fase de inyección en todas las válvulas a lo largo del tubo hasta registrar en cada una de ellas una presión superior a 15 bares, lo que se conocía como parada por presión, o un volumen inyectado superior a 470 litros, que constituía la parada por volumen. Transcurridas 24 horas, el proceso de inyección se repetía únicamente en aquellas válvulas en las que la primera inyección había registrado parada por volumen, hasta alcanzar en ellas 8 bares de presión.
Para validar el tratamiento efectuado se ejecutaron ensayos de permeabilidad Lefranc distribuidos de forma uniforme a lo largo del perímetro de la cortina de inyección, cubriendo toda la altura tratada con una separación vertical de 2 metros. Los valores del coeficiente de permeabilidad medidos se situaron en todos los casos por debajo de 10-6 m/s, criterio hidrogeológico fijado por el proyecto.
7.- Técnicas de mejora del terreno mediante tubo manguito y Jet Grouting
Además de los tratamientos de mejora indicados en los apartados anteriores, que tenían como principal objetivo impermeabilizar el terreno en el entorno del recinto apantallado, se realizó un segundo grupo de actuaciones para consolidar e incrementar la capacidad resistente del terreno y dar respuesta así a las necesidades constructivas durante la ejecución del túnel. Estos trabajos consistieron en la mejora de bloques de suelo en el trasdós de los muros pantalla de las estaciones, para garantizar la estabilidad del terreno durante la entrada y la salida de la tuneladora, y en el espacio comprendido entre el túnel y los muros pantalla de las obras auxiliares, con objeto de construir las galerías de conexión entre ambas estructuras mediante procedimientos manuales.
Las técnicas de mejora empleadas tuvieron que adaptarse a la heterogeneidad del terreno. Para ello fue necesario realizar un tratamiento mixto compuesto por inyecciones IRS con tubo manguito, similares a las ejecutadas bajo el pie de la pantalla, en los estratos en los que predominaban materiales plásticos o roca fracturada, e inyecciones mediante Jet Grouting en suelos con una alta proporción de material granular.
El sistema de Jet Grouting elegido para los trabajos fue el de doble fluido con aire, que consiste en instalar en la parte inferior del varillaje, sobre la herramienta de corte, un monitor de inyección de alto rendimiento que gestiona a través de una tobera la impulsión de una lechada de cemento envuelta en aire. Mediante un giro radial de 360°, la inyección disgrega el terreno y aporta la mezcla de cemento al tratamiento creando una columna de suelo mejorado. Las columnas se ejecutaron en escalones ascendentes de 4 cm mediante maniobras de recogida de un varillaje doble que permitía independizar el flujo de aire de la inyección de la lechada de cemento. El primero se realizaba a una presión de 10 bares mediante un compresor y la lechada se inyectaba a 400 bares desde una planta automática instalada en obra. Debido al entorno urbano en el que se desarrollaron los trabajos y a los múltiples servicios afectados, el diseño del tratamiento incluyó un alto porcentaje de columnas de Jet Grouting oblicuas, con inclinaciones de hasta 15°.
Antes de comenzar los tratamientos en cada zona de trabajo, se ejecutaba un campo de pruebas con objeto de medir in situ diámetros de columna y ajustar parámetros de ejecución como la presión y caudal de la lechada, presión del aire, velocidad de rotación o altura y duración de cada paso de inyección. El objetivo de las pruebas era obtener la combinación de parámetros de ejecución que permitían desarrollar columnas con el diámetro objetivo de 1,50 m. Debido a la gran profundidad a la que se ejecutaban las columnas, resultaba imposible medir su diámetro de forma directa excavando a su alrededor, por lo que fue necesario emplear un método geofísico de medida basado en la comparación de resistividades entre un sondeo en el eje de las columnas y otro de control en el terreno natural.
Como los bloques de Jet Grouting debían ser continuos y no podían presentar zonas sin tratamiento, se diseñó una malla densa de actuaciones basada en un criterio de desviación máxima de cada taladro del 1%. En obra se controló la verticalidad real de todas las perforaciones mediante inclinómetros, lo que permitió generar imágenes en tres dimensiones de los bloques de columnas realmente ejecutados y verificar la continuidad del tratamiento.
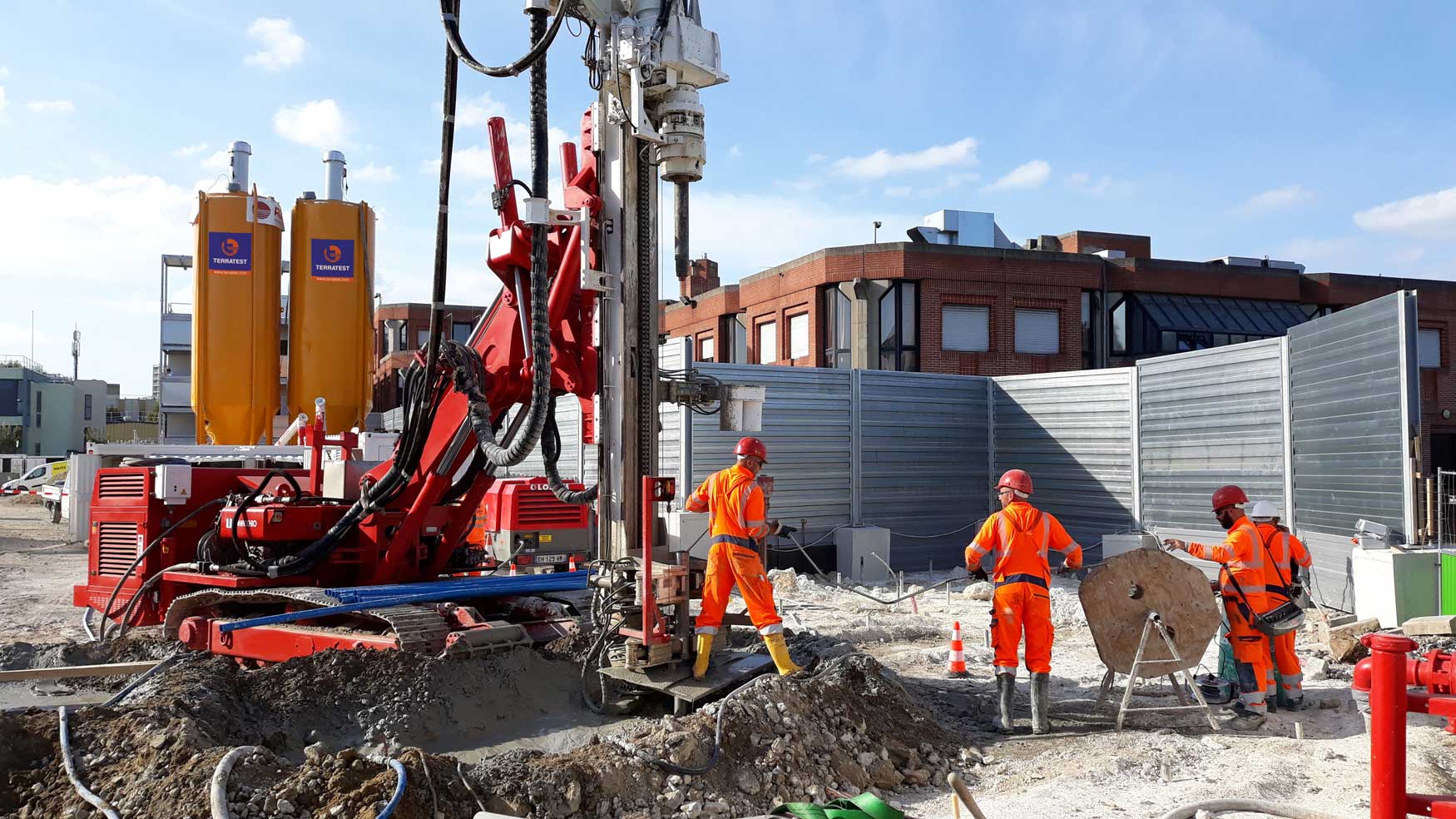
Durante la ejecución del Jet Grouting se obtenía en superficie material sobrante de la inyección, denominado 'resurgencia'. Su gestión es clave para el buen funcionamiento de los trabajos. En el proyecto se instaló un filtro prensa que permitía tratar el material de desecho mediante un proceso de deshidratación a razón de 10 m3 por hora.
Todos los ensayos de resistencia a compresión simple realizados en probetas extraídas de zonas tratadas mediante inyecciones con tubo manguito o Jet Grouting devolvieron valores a 28 días muy superiores a la resistencia objetivo de 5 MPa, lo que confirmó la eficacia de los tratamientos efectuados.
8.- Conclusiones
Los trabajos geotécnicos ejecutados por Terratest en los lotes 1 y 2 de la línea 16 de Grand Paris Express supusieron un desafío constante tanto a nivel técnico como en la gestión del proyecto. La complejidad de las técnicas empleadas, las estrictas especificaciones de proyecto y unos plazos de construcción muy ajustados obligaron a suplementar las medidas habituales de control de calidad y seguridad en los trabajos.
Las fases posteriores a las actuaciones geotécnicas, en las que se llevó a cabo la excavación de las estaciones y obras auxiliares, permitieron constatar la calidad de los trabajos de cimentación ejecutados. La tuneladora Sarah, en julio de 2020, y Batan, en agosto de 2021, realizaron con éxito su paso a través de las pantallas del pozo de ataque 3303P y de la estación de La Courneuve, respectivamente [6] y [7], lo que confirmó la buena ejecución de los muros pantalla y el conjunto de tratamientos de mejora de terreno asociados a estas estructuras.
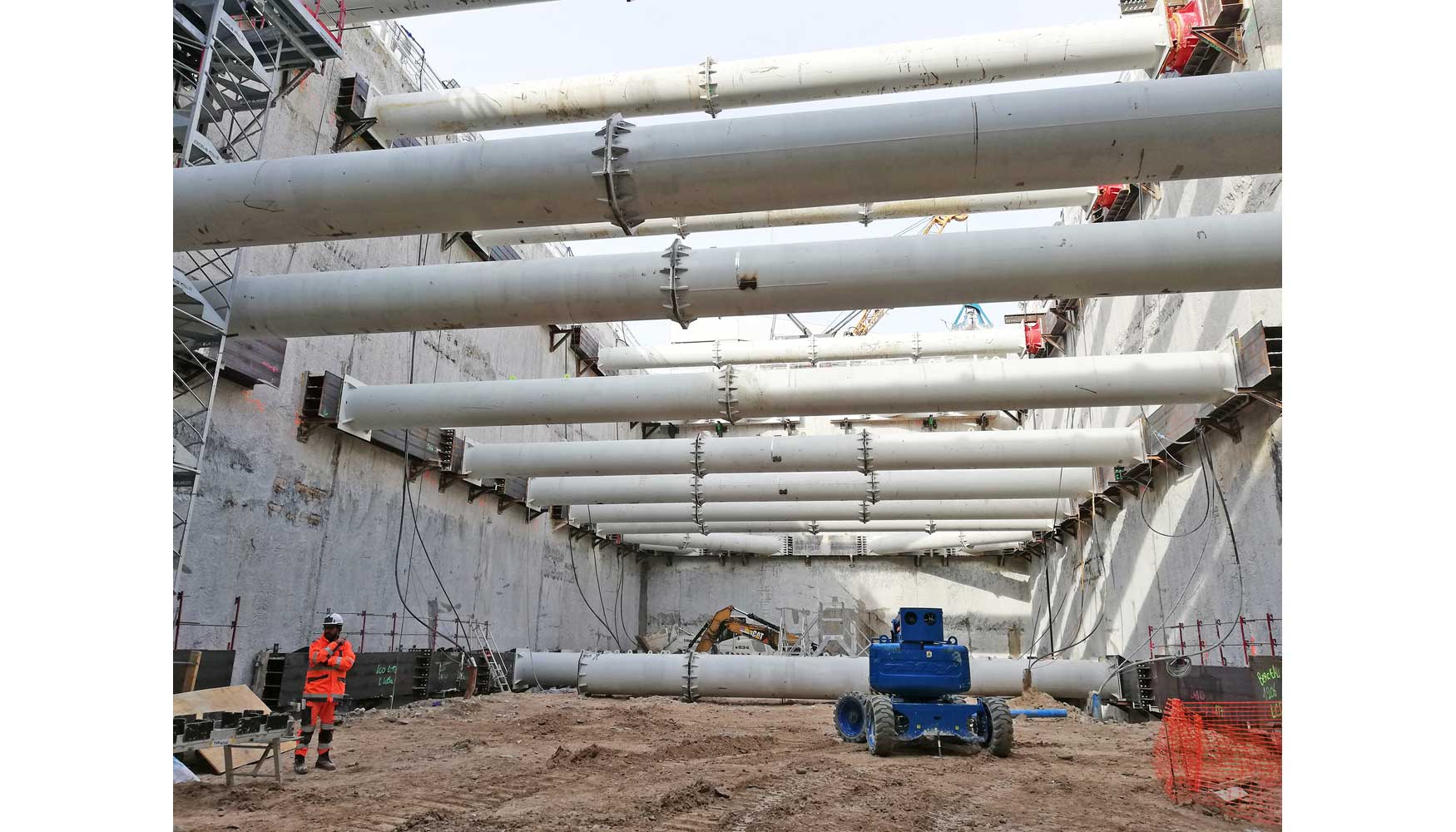
9.- Agradecimientos
Los autores de este artículo, en nombre de Terratest, quieren agradecer a Societé du Grand Paris, grupo Eiffage-TSO-Razzel Bec y grupo Salini Impregilo-NGE haber depositado su confianza en nuestra empresa para colaborar en el desarrollo de un proyecto tan emblemático como Grand Paris Express.
También nos acordamos en estas líneas de los trabajadores y trabajadoras de Terratest que han contribuido al éxito del proyecto y lo han convertido en una referencia para el futuro. ¡Muchas gracias! Bon boulot les gars!
10.- Referencias
[1] Página web de Societé du Grand Paris. Grand Paris Express, the largest transport project in Europe.
https://www.societedugrandparis.fr/info/grand-paris-express-largest-transport-project-europe-1061
[2] Página web de Societé du Grand Paris. L'essentiel du Grand Paris Express.
https://www.societedugrandparis.fr/nouveau-metro/grand-paris-express
[3] Página web de Societé du Grand Paris. Ligne 16.
https://www.societedugrandparis.fr/gpe/ligne/ligne-16
[4] Página web de Societé du Grand Paris. Ligne 16: les entreprises françaises et internationales invitées à concourir aux marchés de travaux.
[5] Terratest. Canal de YouTube. Terratest France Estación de Sevran Beaudottes (línea 16)
https://www.youtube.com/watch?v=z85qceX-lik
[6] Página web de Societé du Grand Paris. Puits du Canal.
https://www.societedugrandparis.fr/canal
[7] Página web de Societé du Grand Paris. La Courneve Six-Routes.
https://www.societedugrandparis.fr/gpe/gare/la-courneuve-six-routes