El macho multiaplicación
En comparación con otras modalidades de mecanizado con herramienta rotativa como taladrado, fresado, escariado, la temática asociada al roscado con macho presenta unos niveles de complejidad notablemente superiores a causa de la variedad, volumen y alcance técnico/económico del conjunto de las variables implicadas.
Ocupa posiciones preferentes en el ranking tanto por volúmenes de operación (el tercer puesto tras taladrado y fresado) como por responsabilidad económica —la primera posición—por tratarse con frecuencia de una operación final que culmina un proceso de mecanizado múltiple.
Desde un punto de vista conceptual podríamos definir una rosca como un arrollamiento espiral de un hilo con un perfil geométrico definido, siendo el más habitual triangular 60 º por ser el correspondiente a roscas Sistema Métrico DIN-ISO y roscas del sistema ANSI (USA).
Desde el punto de vista funcional los cometidos más importantes de las roscas se pueden englobar en 2 grandes áreas:
- Como elementos de unión /fijación principalmente.
- Como elementos de accionamiento en menor proporción.
El binomio rosca – macho de roscar
A título de referencia orientativa el esquema que figura a continuación ‘selección/identificación del macho de roscar’ recoge una panorámica general de roscado con macho. De acuerdo con el mismo vamos realizar un repaso abreviado de los principales factores implicados.
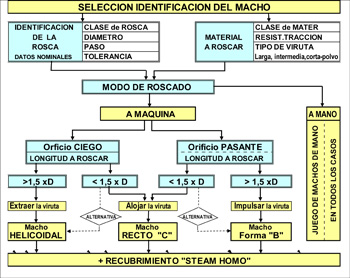
Fundamentos de la rosca a mecanizar
Este capítulo se compone de 3 áreas o apartados fundamentales:
- Características de la rosca
- Características del orificio
- Características del material a trabajar
1) Características de la rosca
Como premisa inicial, resulta imperativo identificar con claridad las características básicas de la rosca a mecanizar: clase de rosca, medida, paso y tolerancia.
A efectos explicativos vamos a tomar como ejemplo referencial una rosca M 10 x 1,50 6H.
M: el dato hace referencia a la clase de rosca. En este caso rosca Métrica, regulada por la Normativa DIN–ISO. A este respecto indicar que a nivel mundial existen 4 grandes normativas:
- DIN-ISO: Sistema Europeo predominante en Europa y en crecimiento constante en el resto del mundo.
- ANSI: Sistema USA predominante en América del Norte, Centro y Sur
- JIS: Sistema Japonés, predominante en Asia)
- BSI: Sistema Británico limitado al área de influencia anglosajona
Todo ello configura un gran número de tipos de rosca cuya relación se puede consultar en la norma DIN 202.
10: este dato hace referencia a la medida nominal de la rosca en mm. A este respecto indicar que las roscas de los sistema ANSI (USA) y BSI (Británico) el dato se expresa en fracciones o decimales de pulgada (ejemplo: 3 / 8” equivalente a 9,525 mm).
- Diámetro exterior (o diámetro nominal): se mide sobre las crestas de las roscas y sus niveles de criticidad /exigencia respecto a la precisión son inferiores al diámetro de flancos.
- Diámetro de flancos o diámetro medio: se mide sobre la línea virtual que discurre longitudinalmente por el punto medio del perfil de la rosca, dividiendo exactamente entre 2 el paso, generando por tanto, idénticas magnitudes entre la porción maciza y la porción vaciada del perfil de rosca.Es el parámetro determinante en la tolerancia de la rosca y por tanto su nivel de exigencia es el más elevado de los 3.
- Diámetro del núcleo o fondo: se mide sobre los fondos de rosca y sus niveles de criticidad/exigencia son notablemente inferiores a los otros dos parámetros.
1,50: es el paso de rosca o distancia entre dos perfiles contiguos, expresada en mm. En las roscas de los sistemas ANSI (USA) y anglosajón BS, el dato se expresa en Nº de hilos o perfiles en 1 pulgada (ejemplo: 16 hilos, 25,40/16 =1.5875 mm). Es un parámetro altamente crítico para la precisión de las roscas y en consecuencia está sometido a severas exigencias de Tolerancia a nivel de cota unitaria coma acumulativa en los sucesivos pasos a lo largo de la longitud roscada. Dichas tolerancias están fijadas por cada una de las Normativas y con carácter general el máximo error admitido es el 0,10% aproximadamente.
6H: hace referencia a la tolerancia diametral de la rosca interior en el sistema DIN-ISO. En combinación con la tolerancia de la rosca exterior determina el nivel de ajuste entre ambas.
Corresponde a la clase Media (6H tuerca - 6g tornillo) de las 3 calidades típicas Fina, Media, Gruesa y se sobreentiende como la tolerancia normal típica siempre que de manera expresa no se indique otra calidad. La estructuración de las tolerancias en 3 categorías, Fina, Media y Gruesa es un criterio común en todas las normativas.
Sentido de la rosca (a derecha / a izquierda): Como criterio estandar se sobreentiende que la rosca es a derecha: giro de atornillado en sentido horario, visto desde la cabeza del tornillo. La opción a izquierda (opuesta a derecha) es de utilización marginal y será objeto de indicación expresa y tratamiento específico.
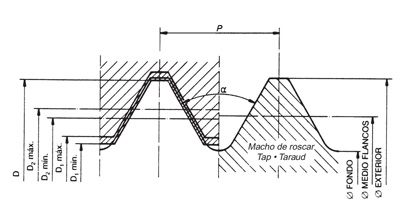
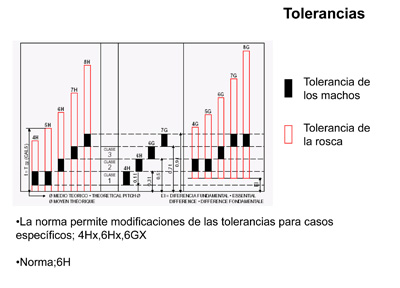
2) Características del orificio
Por causas que explicamos en la descripción del macho, la tipología del orificio a roscar constituye un factor determinante para el roscado con macho. Por tanto la adecuada identificación de sus características: forma o tipo y profundidad o longitud roscada constituye la 2ª premisa fundamental.
Si bien la casuística es muy amplia, a efectos prácticos se puede agrupar en 6 variantes principales (2 tipos x 3 longitudes roscadas en cada uno de ellos):
Orificio ciego (sin salida): con longitud roscada Corta (≤ 1xD), Media (1,5 xD), Larga (2,5xD);
Orificio pasante (con salida): con longitud roscada Corta (≤ 1xD), Media (1,5 xD), Larga (2,5xD), (D=diámetro nominal de la rosca).
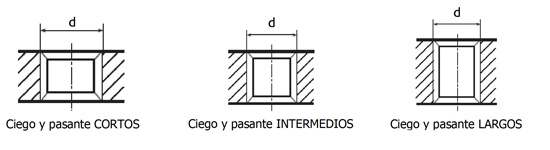
3) Material del substrato
Como en toda operación de mecanizado, la importancia del material trabajado resulta totalmente obvia en el roscado con macho.
Dado el amplio espectro de factores y condiciones que intervienen en la caracterización del material, desde el punto de vista práctico interesa su simplificación al máximo posible, siempre dentro de límites racionales que garanticen los niveles de eficiencia requeridos.
De acuerdo con lo citado resumimos la temática en 3 condiciones genuinamente representativas: Clase/ naturaleza, Características mecánicas y Tipología de viruta.
• Clase / naturaleza
En el contexto que nos ocupa centramos el tema en materiales metálicos de uso más común en la industria de Fabricación Mecánica y áreas aledañas:
- Aceros de construcción mecánica (baja y media aleación)
- Aceros aleados para tratamiento térmico
- Aceros inoxidables / refractarios preferentemente austeníticos (AISI 304, 316 y similares)
- Fundiciones, preferentemente Nodulares (GGG).
- Aluminio y aleaciones con contenidos de Silicio ≤ 8%
• Características mecánicas
Las centramos en resistencia a tracción y/o dureza, con limitación preferente a un máximo de 1000 Mpa (350 HB). En el apartado específico de roscado por laminación o conformado plástico —roll forming— sin desprendimiento de viruta, es necesario tener en cuenta, además, la plasticidad o coeficiente de deformación plástica (no inferior al 10%).
• Tipo de viruta
Es un factor directamente asociado a los dos anteriores y a efectos de simplificación práctica resumimos 3 tipos referenciales: larga, típica de materiales de reducida dureza y/o alta plasticidad en general, como aceros de baja aleación, inoxidables y aluminios bajos en Si; intermedia, típica de materiales de dureza intermedia y/o contenido medio de Carbono >0,50% o aceros de fácil mecanización, aleados con adición estratégica de Pb (plomo) o S(azufre); y muy corta/polvo, típica de fundiciones.
El macho de roscar
Lo podemos definir como herramienta rotativa de corte de precisión específicamente diseñada para el mecanizado de roscas interiores. Por tanto la herramienta por excelencia para el objeto en cuestión.
Desde el punto de vista tecnológico global podemos distinguir 2 tipologías principales:
- Macho de laminación (rolling tap) que trabaja por tecnología de conformado plástico sin presencia de viruta. Sus volúmenes de utilización son muy inferiores al macho de corte a pesar de sus propiedades y potencialidades y su tratamiento ocuparía un amplio capítulo que en principio queda fuera del presente trabajo.
- Macho de corte (cutting tap) que trabaja por tecnología de corte o desprendimiento de viruta. Es el tipo predominante a nivel universal y dentro del mismo como exponente destacado el macho multimetal que nos ocupa en el presente trabajo.
Velocidad de trabajo en roscado con macho
A título aclaratorio ante posibles errores de concepto, consideramos necesario hacer hincapié sobre este importante tema. En el mecanizado de orificios en general (taladrado, escariado, roscado con macho) la velocidad efectiva viene determinada por el ritmo de avance axial o velocidad de avance. La velocidad de giro o tangencial es un factor complementario. Bajo esta premisa resulta evidente que el macho de roscar es, per sé, una herramienta de alta velocidad a causa de la elevada velocidad de avance debida a su peculiar mecanismo de trabajo. En consecuencia rara vez el roscado con macho constituye un cuello de botella desde la perspectiva de tiempo de ciclo.
En comparación con el taladrado con brocas de metal duro —de alta velocidad— los ratios de avance x 1 rpm del macho son hasta 10x superiores, por lo que rara vez la velocidad de avance axial de la broca alcanza a el 75% de la velocidad axial del macho a pesar de la diferencia en velocidad tangencial o de giro (rpm) favorable a la broca (proporciones de 6 x.
Mecanismos de trabajo del macho de roscar
El mecanismo fundamental de actuación del macho se caracteriza por una condición exclusiva y determinante como es la supeditación del giro, a un único valor o ratio de avance, con lo que el valor del avance x 1 rpm debe ser exactamente igual al valor del Paso de rosca. Es lo que se conoce como sincronización.
Del hecho se derivan 2 consecuencias principales:
- Cualquier posible error, por exceso o por defecto, en la exactitud de dicha sincronización comporta inevitables consecuencias negativas, bien en la calidad de la rosca labrada (medida y acabado) y/o bien en la propia vida de la herramienta.
- Todo giro parcial del macho, obliga imperativamente a un desplazamiento axial de magnitud proporcional al valor del giro.
La consecuencia final es que el éxito en el roscado con macho, está severamente supeditado a los factores asociados al sincronismo giro - avance.
Notas importantes
En la práctica, la obtención de una coordinación precisa y permanente entre ambos sincronismos —el propio del macho y el propio del sistema de avance— en todas las fases del roscado (avance, parada, inversión, retroceso)— puede resultar complicada en determinadas situaciones y/o circunstancias, incluso con sistemas CNC avanzados. Solamente el conocido sistema mecánico mediante husillo patrón ofrece garantías plenas y de hecho es utilizado con óptimos resultados por varios fabricantes de prestigio, de máquinas especializadas en roscado con macho, sin obstáculos para su combinación con sistemas CNC.
En la práctica la problemática asociada a posibles errores de sincronización, se resuelve con la utilización de un elemento de fijación del macho o portamachos, dotado de flotación axial (desplazamiento elástico retráctil a tracción principalmente (campo 25% mínimo de la longitud a roscar) y compresión (campo 20% aproximadamente de tracción). La flotación axial actúa compensando permanentemente los posibles errores de sincronización. Por otra parte, y sin obstáculo de posibles opiniones divergentes, podemos asegurar que este dispositivo no comporta riesgos de efectos negativos en ningún caso.
Además de lo anterior, la utilización de sistemas dotados con limitadores de par o embragues, puede resultar beneficiosa en teoría pero en la práctica se presentan complicaciones de carácter relevante que cuestionan su utilidad.
Características fundamentales de la herramienta
Desde el punto de vista funcional la calidad global del macho de roscar es el resultado de la suma de 4 calidades parciales interactivas:
Calidad del material del substrato y tratamiento térmico apropiado + Calidad Geométrico –dimensional + Calidad de rectificado+ Calidad de acabado/tratamiento superficial.
A título referencial vamos realizar un breve recapitulativo.
• Material del substrato
Los aceros rápidos o súper rápidos constituyen la opción prácticamente totalitaria, con una participación marginal del metal duro WC carburo de Tungsteno. Las razones son de orden técnico y radican especialmente en la indiscutible superior tenacidad (minimización de riesgos de fragilidad) de los aceros rápidos respecto a los carburos, a pesar de los notables progresos experimentados en los últimos.
Dentro de los aceros rápidos destacar las 2 calidades específicas: M2 (1.3343, S 6-5-2) que es el acero rápido por excelencia hasta el punto de que sus capacidades reales pueden resultar insuficientemente apreciadas en algunos casos y M35 (1.3243, S6-5-2-5) calidad que sobre la base del M2 incorpora Co (Cobalto) en sus contenido de aleación, lo que le aporta una apreciable mejora en resistencia térmica (dureza en caliente) para trabajar a velocidades de corte muy elevadas. Como contrapartida incrementa moderadamente la fragilidad.
Ambos materiales son los utilizados en los machos multimetal.
• Dimensiones generales
Se entienden como tales la longitud total, longitud de cabeza (orientativo), diámetro del mango o mástil, medida e/caras del cuadrado de arrastre. Estos parámetros están definidos por cada una de las grandes normativas a mundiales antes citadas: DIN-ISO, ANSI, JIS, BSI y son diferentes para cada una de ellas. Los machos multimetal responden a la normativa DIN –ISO.
• Medidas diametrales de la rosca
Las medidas diametrales de la rosca del macho están estratégicamente dimensionadas —mediante criterios recogidos en las normativas correspondientes— para obtener las tolerancias exigidas en la rosca a mecanizar.
A título de observación destacar que por razones técnicas de cierta complejidad (niveles de esfuerzo y fricción), el macho no realiza el mecanizado del diámetro del núcleo o fondo de rosca por lo que esta medida diametral es obtenida en la fase anterior de mecanizado previo de los orificios.
Geometría activa
Engloba el conjunto de formas y elementos geométricos directamente implicados en la mecánica de trabajo del macho de roscar.
Ranuras o estrías: Además de configurar la cara de desprendimiento o corte y por consiguiente el ángulo de corte, son los elementos que se encargan del alojamiento y/o evacuación de la viruta cortada y de la conducción del fluido de corte o refrigerante.
Tienen una relación directa con el tipo de roscado a realizar y desde una perspectiva global se identifican 3 tipologías principales:
- Estrías rectas (straight flutes): típicas en los juegos machos de roscado manual. En trabajo a máquina se aplican para roscado de orificios ciegos o pasantes cortos, ≤ 1xD en general, así como largos ≤ 3xD en casos particulares como fundiciones. No pueden desplazar la viruta y por tanto deben alojarla en su interior, por lo que la relación volumen de viruta – capacidad /espacio de alojamiento resulta primordial.
- Estrías helicoidales (spiral flutes) típicas para extracción de la viruta en roscado de orificios ciegos con profundidad >1xD. En caso de necesidad este tipo pueden roscar cualquier tipo de orificio aunque se reducen los niveles.
- Ranuras rectas con forma espiral en una zona determinada de la punta o entrada del macho, también conocidas como forma B, Gun o Entrada corregida (spiral point): típicas para impulsión de la viruta en roscado de órificios pasantes en general preferentemente >1xD.
Cuña de corte: es el elemento que lleva a cabo la acción propiamente dicha de corte y está configurada por 3 ángulos típicos:
- α = ángulo de incidencia, destalonado o librado (relief angle)
- β = ángulo de corte o desprendimiento (rake angle)
- γ = ángulo del filo o cuña (edge angle) consecuencia de los otros 2
Si bien los 3 ángulos son importantes el de incidencia resulta especialmente crítico. En realidad los machos tienen 2 ángulos de incidencia:
- Ángulo de incidencia en los flancos de los dientes o perfiles de rosca. Es un parámetro clave para las prestaciones de los machos de roscar. Su dimensión es necesaria y estratégicamente reducida —inferior a 1º— a causa de su especial impacto sobre el comportamiento de los machos, incluso a niveles sub-grado (decimales de grado), por lo que su diseño resulta especialmente crítico. A partir del diseño, la extrema exigencia requerida– a nivel milesimal de mm– para un control preciso en la ejecución y en la medición de este parámetro, conlleva una especial complejidad técnica.
- Ángulo de incidencia en las crestas de los dientes del cono de entrada. Representa el 2º nivel de criticidad para las prestaciones del macho. A título orientativo su dimensión guarda una proporcionalidad aproximada de 10x respecto al anterior. Las exigencias requeridas para su tutorización —a nivel centésima de mm— presentan también una notable complejidad técnica.
La garantía de una adecuada tutorización de los parámetros citados exige medios y recursos tecnológicos altamente cualificados. Un exponente de los medios es el equipo específico de tecnología puntera alemana recientemente adquirido por Neco-Tivoly, el cual proporciona garantías totales de medición y constituye una respuesta al reto permanente de innovación/mejora de nuestro macho de roscar.
Existe un 3º ángulo de incidencia, que afecta a las crestas de las roscas, pero dada su baja criticidad omitimos referencias al mismo.
No obstante en el macho multimaterial el diseño responde a criterios particulares basados en resultados experimentales para garantizar su polivalencia.
Conicidad inversa: consiste en una reducción progresiva de la cota diametral en flancos y fondos de rosca. Orientada en dirección punta–mango, su objeto es reducir / minimizar el elevado componente de fricción o rozamiento congénito en el trabajo del macho por lo que se trata de un elemento altamente crítico. Su magnitud es obligatoriamente reducida (> 0,5%) y los imperativos y exigencias de calidad en su diseño y ejecución alcanzan niveles similares a los citados para la cuña de corte.
Cono de entrada: zona o área de la punta con perfiles truncados en cono. Realiza el trabajo propiamente dicho de mecanizado o elaboración de la rosca. La función de los perfiles de rosca subsiguientes se limita exclusivamente a una acción de guiado o acompañamiento.
Además del destalonado o incidencia el otro parámetro característico es la longitud, habitualmente expresada en Nº de hilos o dientes de rosca. La combinación entre nº de cortes o estrías (Z) y Nº de hilos (N), determina el espesor de la viruta cortada (E), de acuerdo a la fórmula E = H/(NxZ) donde H es la altura del perfil de rosca en mm (a título orientativo H = 0,5xP).
A efectos prácticos existen 2 variantes típicas de longitud:
- 2,5 hilos o pasos (tipo C o corta) típica de machos para orificios ciegos (machos helicoidales y rectos)
- 4,5 hilos o pasos (tipo B o media) típica de machos id, id pasantes (machos Forma B o Gun)
La limitación en la longitud del cono en los machos para orificios ciegos obedece a la exigencia habitual en los orificios ciegos, de minimización de la zona de roscas incompletas —no útiles— debidas a la geometría del cono.
Este detalle explica la inevitable diferencia en rendimiento a favor del macho forma B o pasante, cuya longitud de cono es netamente mayor (+ 80% aproximadamente respecto al tipo para orificios ciegos).
De acuerdo con todo lo citado, la importancia del cono resulta obvia y por tanto las exigencias de calidad se sitúan en niveles máximos.
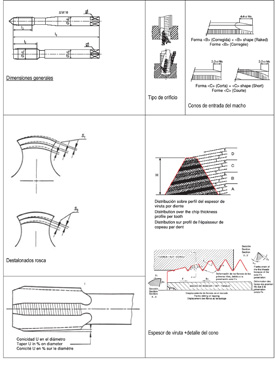
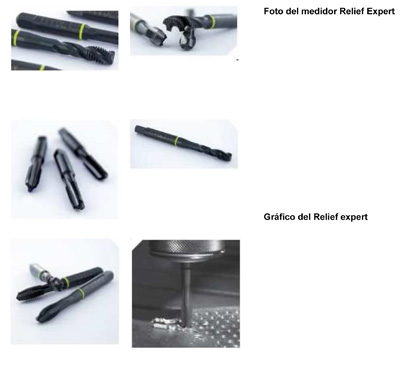
Acabado superficial con vaporización steam homo (Urdin)
Se trata de un tratamiento superficial por vía térmica, que genera una capa de óxido férrico Fe3O4 con espesor submicra y cuyo rasgo visual distintivo es su característico color negro-azulado.
Se realiza en hornos de cámara atmosférica específicamente preparados y el proceso —que resulta totalmente inocuo desde el punto de vista sanitario y ecológico— consiste básicamente en un ciclo de tratamiento térmico estructurado en etapas con distintos escalados en el binomio tiempo-temperatura y con aportación de vapor de agua en una determinada fase del mismo. Dentro del marco genérico, los datos de detalle concreto quedan a criterio de cada fabricante lo que permite obtener propiedades relativamente diferentes. Obviamente la temperatura no puede superar, en ningún caso, el umbral de revenido (550º).
Aparte del consabido efecto cosmético, aporta una notable contribución técnica en beneficio de la herramienta:
- El factor térmico aporta una reducción/eliminación el stress residual proveniente del proceso de fabricación resultan imposibles en la) lo que contribuye a incrementar la vida de la herramienta (amolados totalmente exentos de estrés son imposibles en la práctica).
- El mismo factor aporta un afinado de las aristas de corte por debilitamiento (acción de quemado) de las micro-rebabas asociadas a la micro-deformación plástica de rectificado a muela lo que contribuye a incrementar la vida y la calidad superficial de las roscas (amolados totalmente exentos de deformación plástica son imposibles en la práctica).
- La oxidación aporta una micro-craterización de la superficie y como consecuencia en la generación de multitud de traduce en micro-depósitos de fluido lubricante, lo que contribuye reducir/ eliminar el deterioro por adhesión (filos de corte recrecidos por soldadura en frío del material trabajado problemática frecuente en materiales férricos sobe todo de baja aleación).
Conclusiones sobre el macho multimetal
- La razón fundamental esta familia de Machos es la polivalencia en términos de respuesta eficiente al roscado de diferentes materiales, superando las barreras técnicas tradicionales que imponían modelos con especialización mono-material y las consecuencias derivadas del hecho.
- Es el resultado de un desarrollo, basado en un profundo estudio y análisis de la problemática real en roscado con macho, a través de una larga y extensa experiencia como fabricante. El desarrollo se completa con la aplicación del ‘know how’ correspondiente para la amplia y compleja serie de rediseños innovativos necesarios en producto y proceso.
- Las garantías de eficiencia están avaladas por multitud de resultados experimentales tanto en el ámbito interno (tests de roscado en nuestro laboratorio de ensayos I+D) como en el ámbito externo a pie de obra.
- Sin obstáculo de su contrastada eficiencia todoterreno como objetivo principal, los machos presentan capacidades especialmente destacadas en aceros de construcción mecánica e inoxidable.
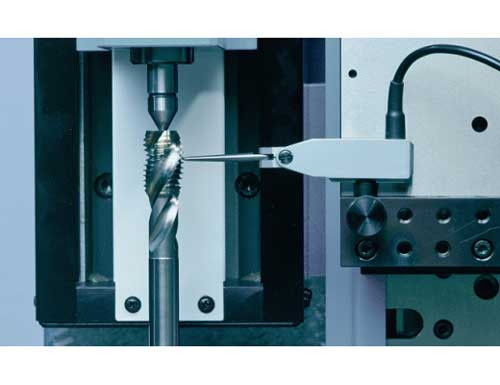
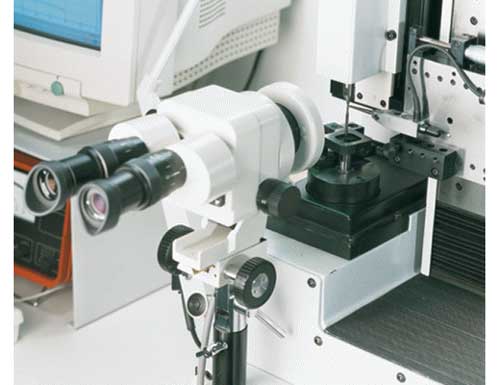