Coperion presenta el nuevo alimentador FET en la K 2010
La nueva tecnología FET es ideal no solo para la zona de alimentación de la extrusora de doble husillo ZSK, sino que también lo es para el alimentador lateral ZS-B de doble husillo que dosifica materiales en polvo directamente en la masa fundida. Coperion mostrará en su stand de la K un alimentador lateral A ZS-B de doble husillo con FET.
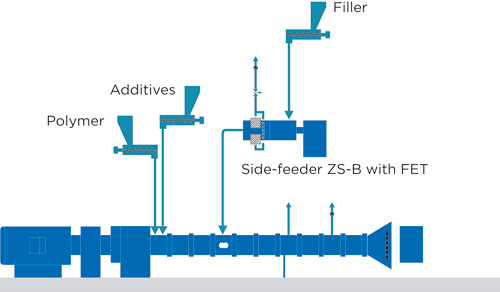
Entre las principales ventajas de FET para procesos limitados de alimentación de compuestos destacan:
- Bajo coste de inversión, porque una unidad más pequeña de compounding puede proporcionar el rendimiento requerido.
- Menor consumo de energía
- Menores costes de producción gracias al uso de cargas no coompactadas, más económicas.
- Mejora la calidad del compuesto mediante un procesado más cuidadoso de productos sensible, debido a la mayor utilización del volumen de procesado disponible.
- Reduce los niveles de residuos, ya que no es necesaria la ventilación trasera.
- Mejora la seguridad del proceso gracias a una mayor ventana de procesado en lo respecta al límite de la zona de alimentación.
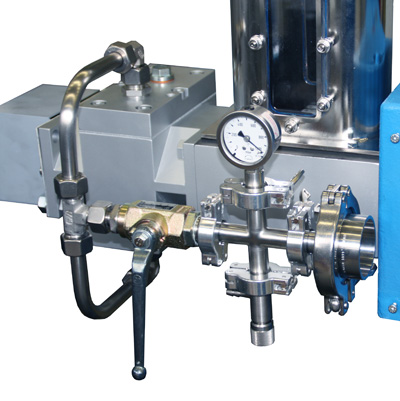
FET, éxito en numerosas aplicaciones
El sistema FET ha sido probado en numerosas nuevas máquinas Coperion desde su lanzamiento al mercado. Además, en estrecha colaboración con plantas de ingeniería de proceso, Coperion ha realizado mejoras para conseguir mayores capacidades de producción.
Por ejemplo, se instaló un sistema FET en una extrusora con doble husillo ZSK con un diámetro de 240 mm para la transformación de poliolefinas en polvo. Esto incrementó el rendimiento de 14 a 17 t/h, lo que significa un 20% de mejora.
Borealis utiliza en su sede de Linz (Austria) un talco muy fino, para fabricar compuestos reforzados con talco. Con la ayuda del FET fue posible aumentar el rendimiento hasta un 200% y eliminar de forma económica el cuello de botella. Otro fabricante de compuestos alcanzó un significativo incremento de las prestaciones gracias a FET con una ZSK 92.
Con un 20% de talco (en peso) el rendimiento aumentó de 2,4 a 3,3 t/h, lo que supone un 40% de mejora.
En ensayos intensivos desarrollados en una ZSK 40 y una ZSK 50 con varios grados de talco, se lograron mejoras hasta 300%. También fueron posibles otros éxitos con otros aditivos: ensayos en una a ZSK 40 resultaron en una mejora de rendimiento del 55% con retardantes de llama y con hasta un 200% de grafito.
Granulador bajo el agua: rompiendo la barrera de 100 t/h
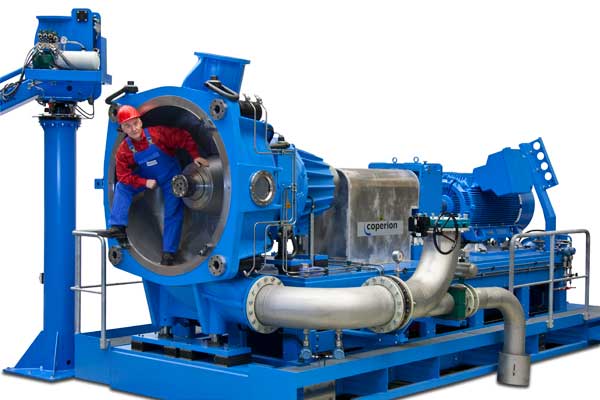
Bombas de masa fundida hasta 65 t/h de poliolefinas
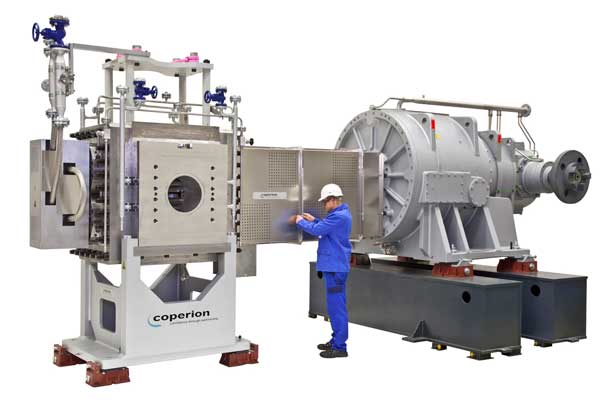