Krauss Maffei aumenta sus inyectoras GX y su oferta en extrusión
Un año después de su lanzamiento la serie GX ya está establecida en el mercado por lo cual Krauss Maffei (representada por Coscollola) presenta ahora un tamaño mayor de 900 toneladas de fuerza de cierre. Con un ciclo de 7 segundos y en una máquina de dos platos produce durante la feria un producto para el sector del packaging. A partir de la K 2013 con los modelos de tamaño 750 y 900 y con las unidades de inyección 6100 y 8100 se amplían las posibilidades de combinación de la serie GX hasta 44 tipos, en el rango de fuerzas de cierre de 400 a 900 toneladas. Ciclos rápidos y eficiencia energética son dos de sus características destacadas.
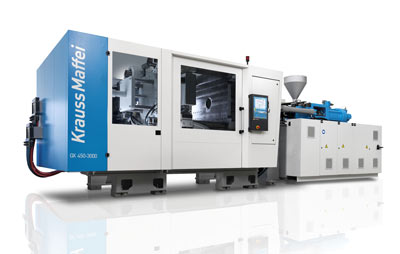
En una GX 900-8100 se demuestra durante la feria el rendimiento en ciclos rápidos, tal y como exigen sectores como el de la logística o el del envase y embalaje. Con una aplicación rápida y en un ciclo total de 7 segundos, la extracción de las piezas se realiza mediante un robot lineal y se transportan a un segundo robot. Ambos robots son del tipo LRX 250 HS y están equipados en versión alta velocidad. Tanto el robot como la máquina montan el control MC6.
Krauss Maffei también muestra una solución totalmente automática para el cambio horizontal del molde en la inyectora GX 900-8100. Es una solución ideal para empresas en las que se requieren muchos cambios de molde ya que el transformador se beneficia de una forma de trabajar que casi se podría denominar just in time.
Extrusión
KraussMaffei Berstorff, por su parte, presenta variaciones en su sistema de cambio rápido de dimensión QuickSwitch, que reduce el consumo de energía y de material durante el cambio y aumenta la disponibilidad para el transformador. Ahora está disponible para tubos con diámetros mayores, de 250 a 450 milímetros.
En la zona de extrusión de esta compañía llamará la atención también el sistema IPC de refrigeración interna del tubo, también disponible para la tecnología QuickSwitch. Esto aporta al transformador una mayor capacidad para competir porque el enfriamiento interno del tubo ofrece una mejor eficiencia de los costes. Junto a la refrigeración externa, el tubo se enfría también desde dentro utilizando el aire ambiental, que se succiona mediante un compresor por un canal lateral que fluye en sentido contrario a la extrusión. Esto reduce el espacio y reduce el consumo de agua.
En la feria también se pueden ver soluciones para responder a la exigencia del mercado de tubos cada vez más complejos y con capas funcionales.