Optimización de los costes totales de producción en cantera mediante la mejora continua en perforación y voladura
Dr. Liam Bermingham. Senior Explosives Engineer. EPC UK
Javier Muñoz García. Training Services Manager. EPC Groupe
04/05/2022La mayoría de explotaciones de áridos dependen en gran medida de la operación inicial de perforación y voladura; la calidad de sus resultados tiene una importante repercusión en los costes de las etapas posteriores.
Este artículo de EPC resume el trabajo llevado a cabo en una de las canteras de áridos más grandes de Europa, situada en el Reino Unido, con una producción anual de 6Mt; donde el empleo sistemático de tecnología en el diseño de voladuras (fotogrametría con drones, sonda de medición de desviación de barrenos y software de diseño Expertir) permitió una mejora considerable de todos los KPI definidos para seguir los consumos energéticos aguas debajo de la voladura y, por tanto, una clara optimización de los costes totales de producción en cantera.
1.- Ciclo de producción en cantera de áridos
1.1.- Perforación y voladura dentro del ciclo
La operación de perforación y voladura es indispensable en la gran mayoría de explotaciones de áridos, siendo además el primer eslabón en la cadena de producción en cantera. El arranque inicial del material se lleva a cabo en la mayoría de los casos mediante el empleo de explosivos por varios motivos:
De manera general, la dureza y consistencia del material hace materialmente inviable el arranque directo mediante excavadora o ripper.
Cuando se dan las circunstancias geológicas que permiten aventurarse con el arranque directo generalmente la maquinaria para este fin se encuentra con serias dificultades para dar la producción requerida a un coste razonable, obteniendo consumos excesivos de gasoil, fungibles, averías, tiempos desproporcionados de arranque, etc.
La perforación y voladura, hoy por hoy, es una técnica segura, que garantiza además el respeto del entorno y un nivel moderado de generación de vibraciones y onda aérea siempre que su diseño y ejecución esté a cargo de personal cualificado. Esta seguridad avanza cada día más con la introducción de la nueva tecnología en el diseño y control de la voladura, así como con la progresiva incorporación de nuevos equipos de perforación más precisos, explosivos tipo emulsión y detonadores electrónicos.
El hecho de constituir el primer eslabón de la cadena de producción hace que los resultados obtenidos tras la voladura afecten de manera notable al resto de etapas aguas abajo. De manera intuitiva, se puede comprender fácilmente que una pega que genera una fragmentación demasiado gruesa y una pila de escombro agarrada al frente va a comprometer los ritmos de excavación del escombro y, por tanto, los tiempos de ciclo de transporte y la alimentación en t/h de la machacadora primaria entre otros. Además, la calidad de la ejecución de la voladura afecta de manera directa a otros parámetros que comprometen la seguridad de la explotación, como por ejemplo la estabilidad de los taludes o las proyecciones de roca desde el frente.
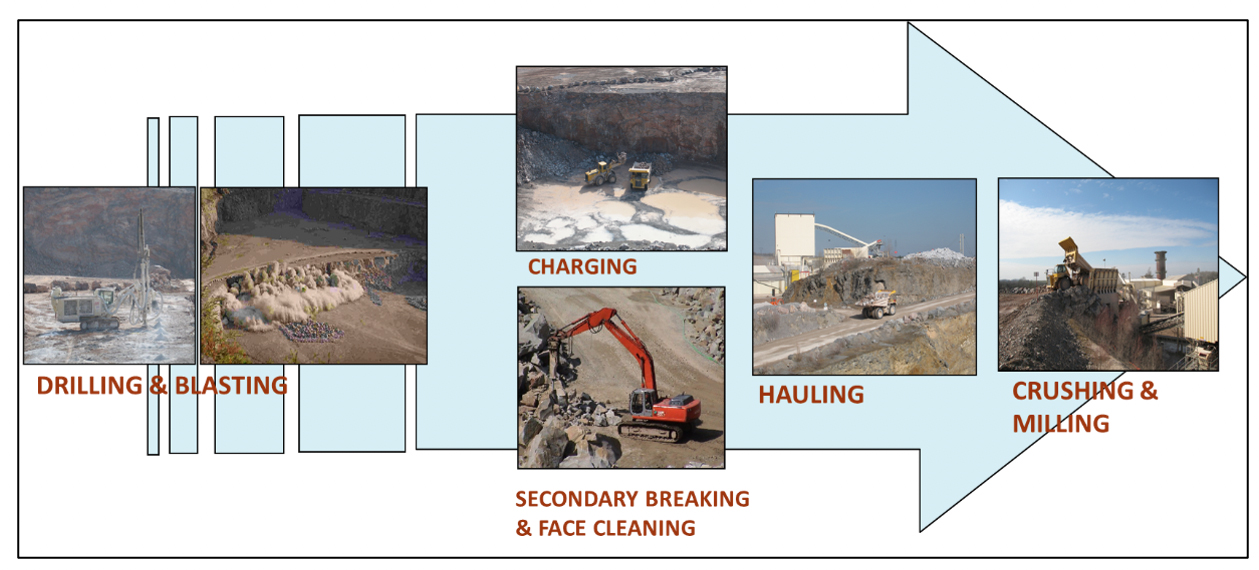
1.2.- El concepto 'Mine to Mill'
Mine to Mill se desarrolla en la universidad de Queensland, Australia, a finales de los años 90. Es un concepto que nace aplicado a la gran minería a cielo abierto, no a la explotación de canteras. El trabajo inicial demostraba que todas las etapas en la cadena de producción son interdependientes y, especialmente, se observó una relación directa de la fragmentación obtenida en voladura con los costes que se obtenían aguas abajo; de forma que una fragmentación más fina se traducía en un conjunto de costes menor a pesar del incremento de costes en perforación y en explosivos; ya que se conseguían reducir de manera más acuciada los costes totales de carga, de transporte del material y de molienda. Este efecto se manifestaba de manera especial con los molinos para molienda autógena o semi-autógena.
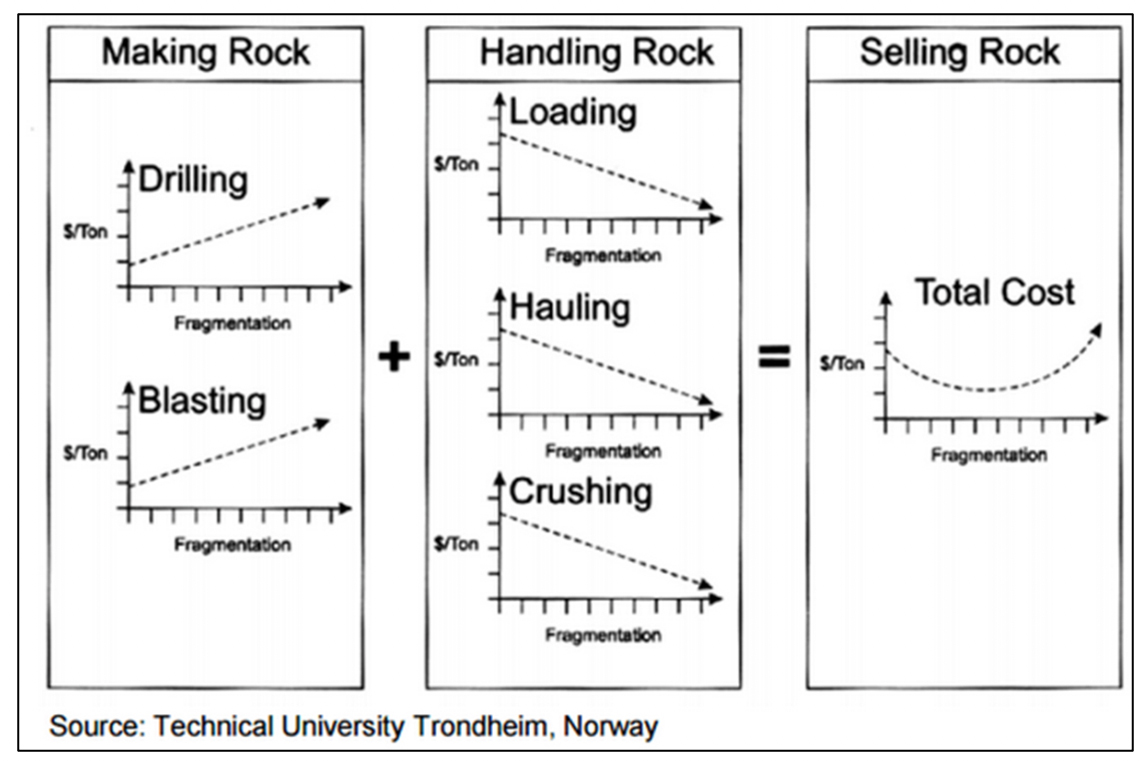
Figura 2.- Concepto Mine to Mill original.
Por tanto, el trabajo de desarrollo inicial de este concepto se centraba originalmente en aumentar más y más la fragmentación obtenida tras la voladura. Se trataba de obtener un material lo más fino posible a base de incrementar el consumo específico de explosivo en kg/m3. Esto requería cerrar la malla de perforación y/o aumentar el diámetro de perforación, manteniendo unos barrenos cargados con un explosivo lo más denso posible y, además, en muchos casos, manteniendo unos retacados demasiado reducidos.
Sin embargo, y a pesar de que se conseguían reducir costes en ciertas partes del proceso, se observó que los circuitos de trituración y molienda comenzaban a no dar la producción ni el tamaño final esperado ya que no estaban dimensionados para una alimentación tan fina. Además, el aumento sistemático del consumo específico en la voladura sin el debido control acarreaba problemas muy importantes de origen en mina: problemas de dilución excesiva, taludes excesivamente rotos y con una estabilidad final comprometida, además de los clásicos inconvenientes de proyecciones que pudieran llegar a ser un problema para la seguridad en ciertas circunstancias a pesar de las grandes dimensiones de las explotaciones.
1.3.- Evolución de 'Mine to Mill' en canteras
Esos primeros años ya fueron determinantes para llegar a la conclusión de que no todo podía girar únicamente en torno a una fragmentación más fina. Dicho de otro modo: una buena voladura, además de producir siempre una fragmentación adecuada, debe cumplir con múltiples requisitos y condicionantes de calidad. Esto es si cabe más cierto en el mundo de la explotación de canteras, donde hay restricciones ambientales muy importantes impuestas por la proximidad a vías de comunicación y zonas habitadas y donde no respetar los límites legales en generación de vibraciones o poner en riesgo la seguridad de personas y equipos con la generación de proyecciones puede llegar a generar el cierre temporal o definitivo de una explotación.
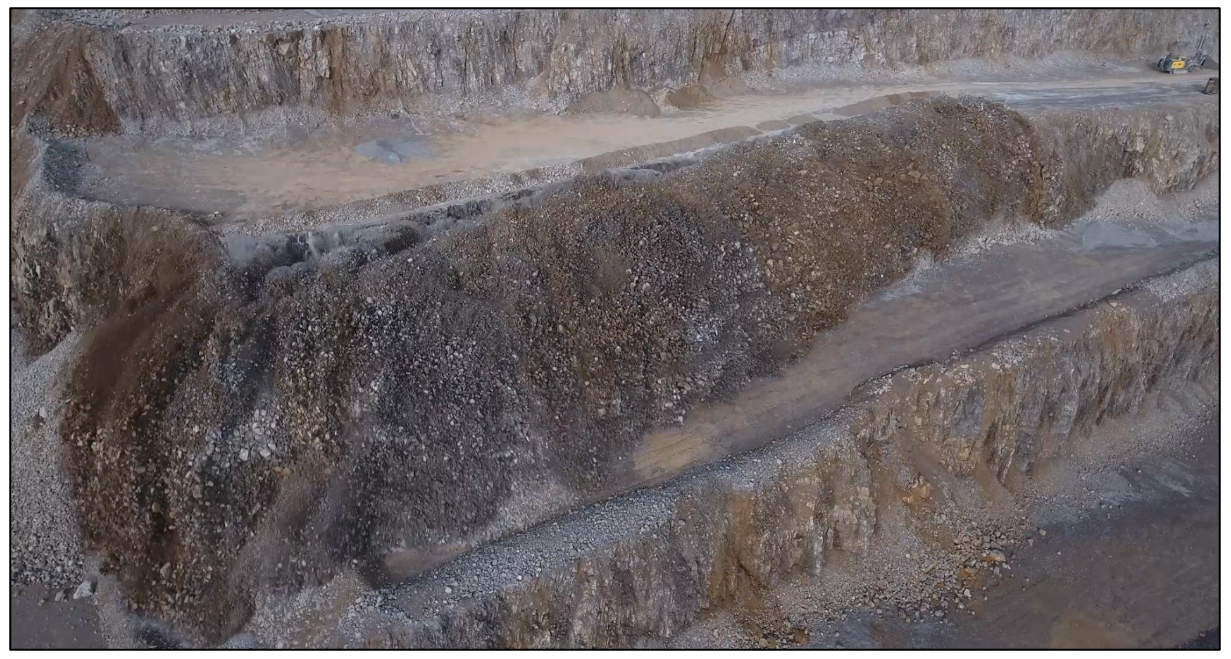
Cabe mencionar además en este punto que una fragmentación adecuada no tiene por qué significar siempre una fragmentación más fina: aparte del ejemplo evidente de las voladuras de producción de escollera; ciertos procesos industriales son incompatibles con la producción de finos en la cantera y una buena parte de las reservas de la explotación puede terminar en una escombrera por este motivo. De manera similar, en producción de áridos ciertos tamaños finos pueden resultar productos de menor valor de mercado por lo que la producción excesiva de estos puede suponer un problema considerable de rentabilidad para la explotación.
Una vez puesto todo esto en consideración, podemos exponer qué es la voladura óptima en una explotación de áridos. En primer lugar, esta debe garantizar, desde la fase de diseño, la seguridad durante su perforación, carga, disparo, en las operaciones posteriores de limpieza y desescombro; así como en las operaciones para preparar y perforar posteriores voladuras en la misma zona. En segundo lugar, asegura una fragmentación y empuje óptimos, a lo largo de todo el frente, de tal modo que se eliminan las operaciones de fragmentación secundaria y taqueos, y el saneo necesario del frente queda reducido a unas mínimas tareas de reacondicionamiento; además las operaciones posteriores de carga, transporte y reducción de tamaños se pueden llevar a cabo de manera fluida y con costes muy contenidos en uso de energía (gasoil, electricidad), de fungibles y de mantenimiento como consecuencia de averías por sobreesfuerzos de las máquinas cargadoras, etc. En resumen, la voladura debe:
- No producir fallos de disparo (misfires) totales o parciales
- Evitar la generación de proyecciones desde el frente durante la voladura
- Generar un nivel de vibraciones y de onda de presión lo más reducido que permita el estado de la técnica, siempre respetando los límites impuestos por la norma
- Producir una fragmentación adecuada para el conjunto del proceso, regular y consistente a lo largo de todo el frente
- Crear una pila de escombro bien esponjada, de forma y altura óptimas para las máquinas de carga de la explotación
- Dejar un frente tras la voladura limpio, seguro, estable y con ausencia de 'roturas atrás'
- Producir un corte horizontal limpio en todo el pie del banco y sin presencia de repiés en el frente
Se puede concluir por tanto que realmente el concepto original 'Mine to Mill' no es de aplicación en voladuras en banco en cantera. El objetivo final de incurrir en unos costes globales óptimos para el conjunto del proceso se mantiene; pero la manera que se tiene de llegar a este objetivo dista mucho del camino que se concebía originalmente (mayor consumo específico = menores costes totales). De hecho, en la mayoría de los proyectos de mejora en cantera se da la paradoja de que se consigue una mejora general de los resultados mediante un uso más racional de la energía del explosivo (energía repartida de manera más homogénea en el frente de voladura); y, frecuentemente, esto supone un consumo específico de explosivo algo menor que el que se obtenía en origen, antes de poner en marcha el proyecto. Sí se puede aplicar en cantera, por tanto, una evolución más tecnificada de este concepto original, que pretende la consecución del mismo objetivo, pero a partir de toda una serie de resultados óptimos tras la pega, obtenibles únicamente mediante la aplicación sistemática de la última tecnología disponible en el diseño y control de las voladuras.
2.- Diseño y control de voladuras en banco
2.1.- Herramientas disponibles en la actualidad
Hasta la llegada de la era digital, las herramientas de las que se disponía para el diseño de voladuras en banco eran muy rudimentarias y no permitían un diseño de precisión. No era posible conocer con exactitud la geometría del frente de voladura ni la trayectoria real de los barrenos por lo que, en aras de la seguridad y con muy buen criterio (para evitar proyecciones de roca desde el frente, por ejemplo), los diseños solían ser muy conservadores; otorgando una piedra excesiva o irregular en la primera fila y comprometiendo así la fragmentación y el empuje de la pila de escombro que proporcionan los costes óptimos para el conjunto del proceso. Es decir, era imposible pretender entrar en un trabajo técnico fino de optimización de resultados.
Desde hace ya más de 20 años las herramientas de diseño disponibles han ido progresando paulatinamente; llegando a dar un verdadero salto cualitativo en los últimos 5 ó 6 años con la eclosión de la era digital a todos los niveles. Las herramientas digitales de hoy en día permiten diseños de voladura muy exactos; así como almacenar de forma fácil infinidad de datos y filmaciones, y usar esta información para replicar los diseños de éxito de voladuras anteriores; pudiendo entrar en interesantes proyectos de mejora continua como el que se va a describir en el apartado 3.
2.1.1.- Drones
Conocer la geometría real del frente de voladura en toda su altura y profundidad es simplemente vital y, de hecho, es un requisito legal de seguridad en algunos países de nuestro entorno. A partir de un modelo digital tridimensional muy preciso del frente tenemos la posibilidad de conocer la piedra real frente a cada barreno. Esto permite ajustar la posición y contenido de las cargas y retacados a la piedra óptima de diseño; evitando además el riesgo de generación de proyecciones.
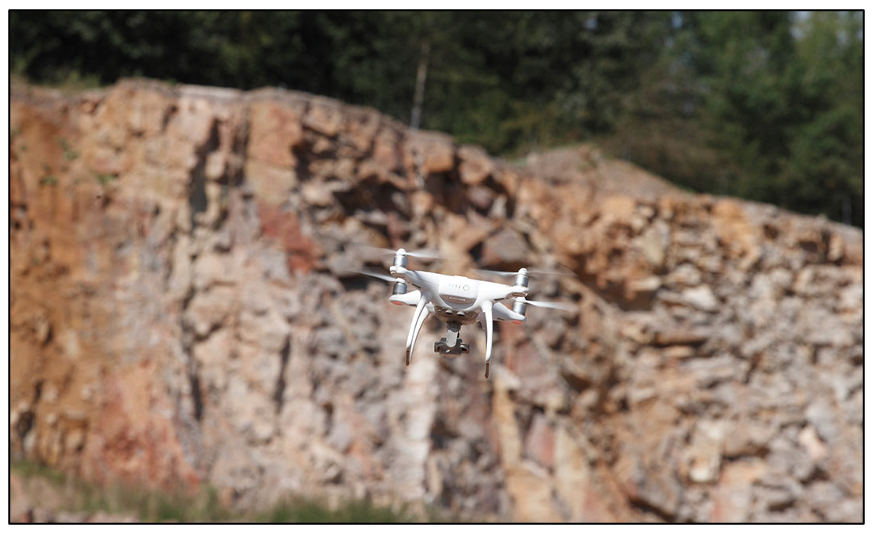
Hoy en día, este modelo digital se obtiene de manera muy rápida, económica y exacta mediante fotogrametría con drones. El tipo de dron que se emplea para esta tarea es el clásico cuadricóptero ligero, equipado con una cámara digital de alta resolución. Las fotografías obtenidas del frente, ligadas a un sistema de referencia o de posicionamiento tipo GPS, se procesan mediante un software de tratamiento de imágenes que permite la generación de un modelo digital mucho más preciso que el que se solía obtener con los antiguos sistemas de láser 3D. Además, este modelo va referenciado en coordenadas XYZ por lo que es posible conocer las coordenadas reales de cualquier punto del modelo obtenido.
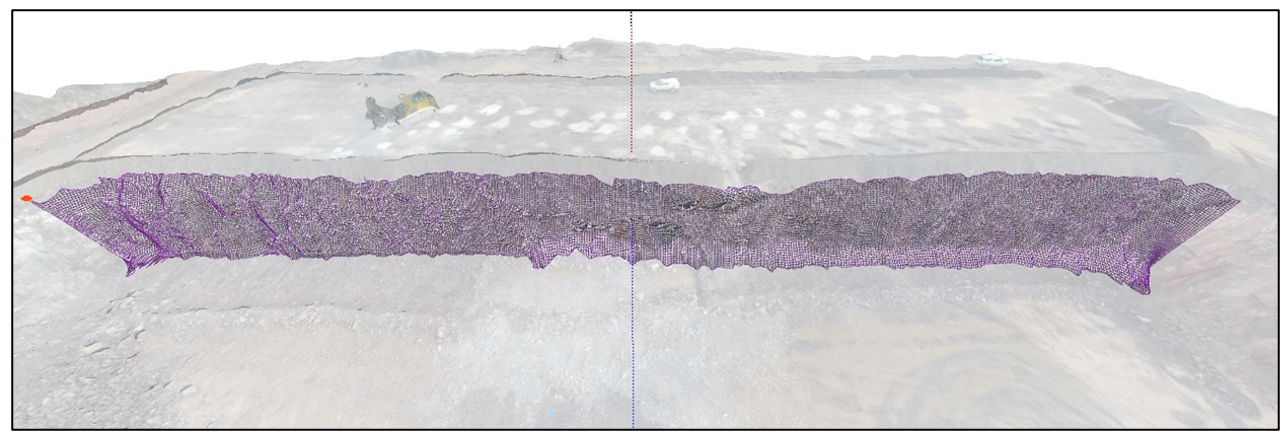
Estos drones se emplean además en la tarea de control de resultados de la voladura de manera muy eficaz; para la filmación de la voladura en alta resolución y la obtención de fotografías del escombro para su posterior análisis de empuje y granulometría.
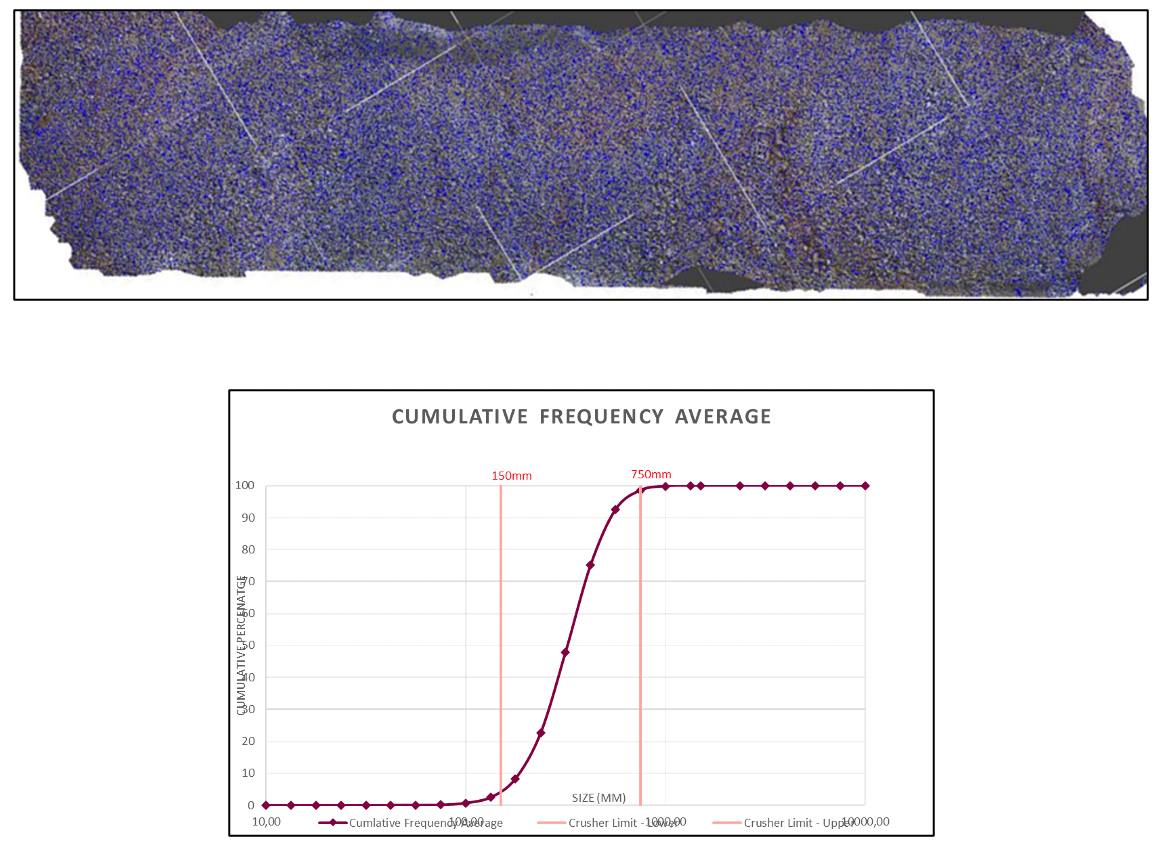
2.1.2.- Sistemas de posicionamiento por satélite
Las coordenadas de los emboquilles de los barrenos se determinan a partir del modelo digital anterior con el software Expertir y se llevan después al terreno, bien mediante herramientas portátiles de posicionamiento GPS o, lo que resulta más conveniente de manera general, mediante carros de perforación que ya están equipados con esta tecnología de posicionamiento por satélite.
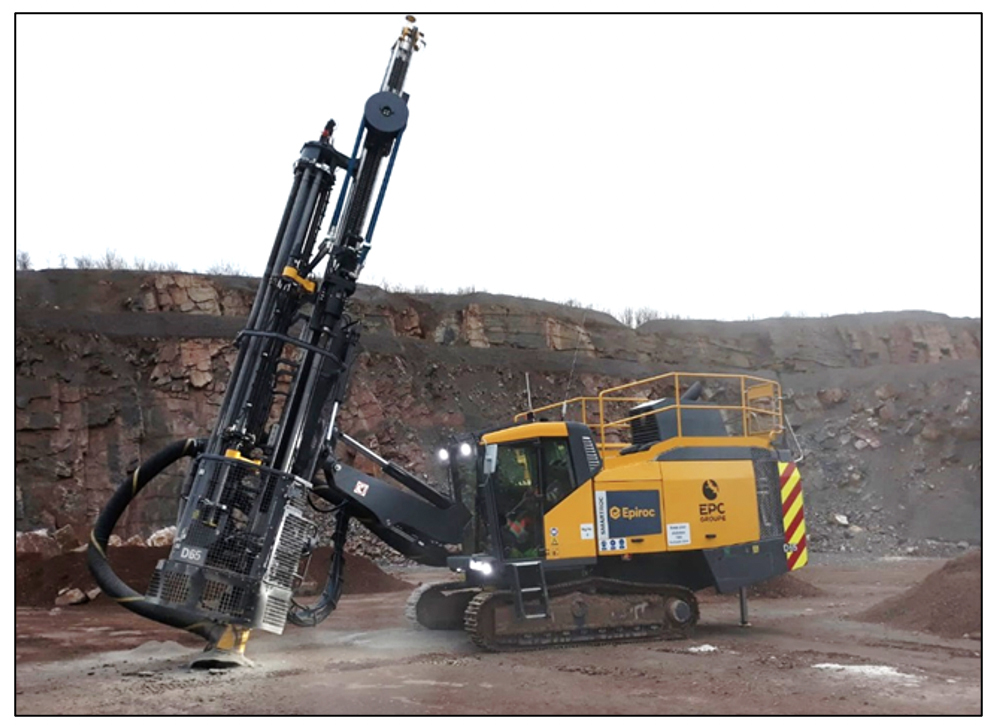
2.1.3.- Sondas electrónicas de medición de barrenos
Además de los posibles errores humanos de emboquille y de ejecución (ángulo y/o azimut incorrecto); bajo la combinación de condiciones desfavorables de altura de banco, ángulo de perforación, condicionantes geológicos, tipo de máquina y material de perforación; los barrenos pueden llegar a desviar de manera considerable; comprometiendo, primero, la seguridad de nuestro diseño y, segundo, la calidad pretendida de resultados. Por este motivo, una vez ejecutada la perforación, se debe verificar siempre la trayectoria real de los barrenos. Esta operación se lleva a cabo con sondas electrónicas de cable que proporcionan la trayectoria real del barreno metro a metro. Existen hoy en día modelos (Sistema Autoprobe de EPC) que efectúan las mediciones de manera autónoma haciendo esta tarea absolutamente liviana y sencilla.
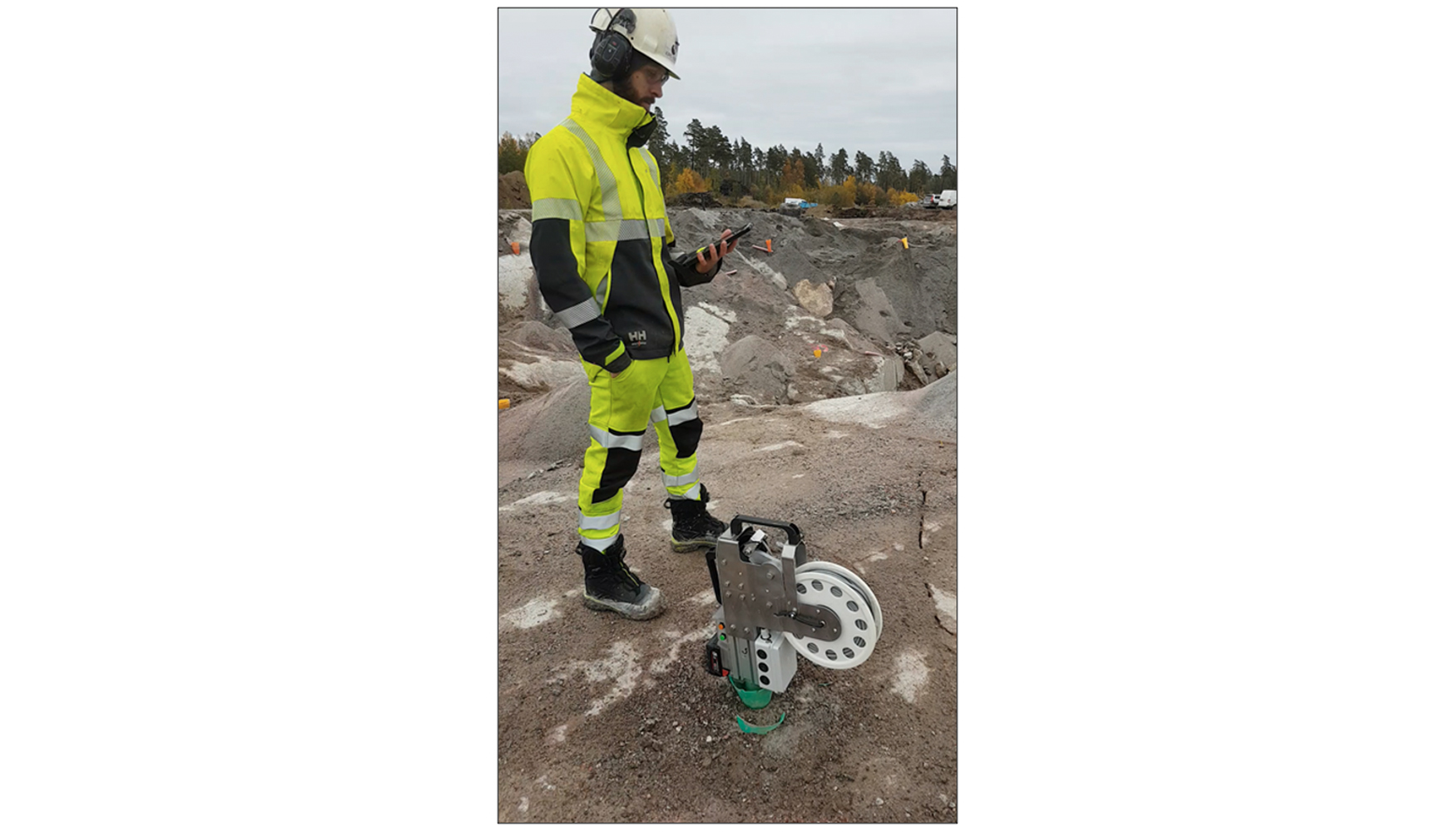
2.1.4.- Software de diseño Expertir
Todas las mediciones que se toman en el terreno se procesan mediante Expertir® Este software de diseño de voladuras permite el cálculo automático del plan de perforación (malla, ángulos y azimut) y la concepción automática de las cargas y retacados con el objeto de realizar un diseño seguro y buscando una distribución homogénea de la energía del explosivo en todo el frente que proporcione una fragmentación óptima y regular. También permite el diseño autónomo de secuencias de disparo, tanto con sistemas de detonadores no eléctricos como con sistemas electrónicos.
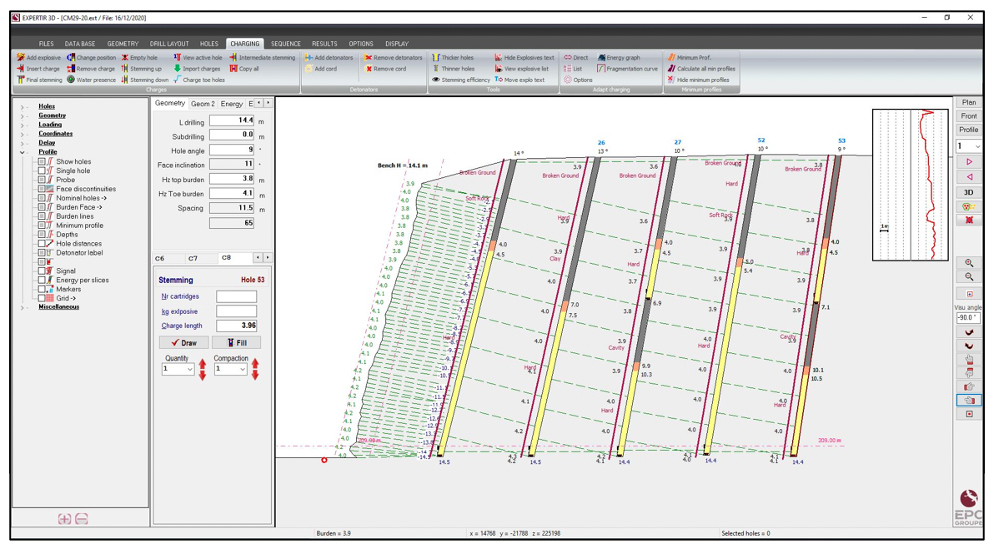
2.1.5.- Tableta de campo Expertab
Esta herramienta cumple varias funciones y se convierte en un apoyo muy importante para los artilleros y los ingenieros de voladura en el terreno. Por una parte, en esta tableta se descarga previamente el diseño final de cargas por barreno y secuencias desde Expertir, de manera que el artillero tiene acceso durante la carga de la voladura a la carga de diseño para cada barreno, su profundidad de diseño, etc.
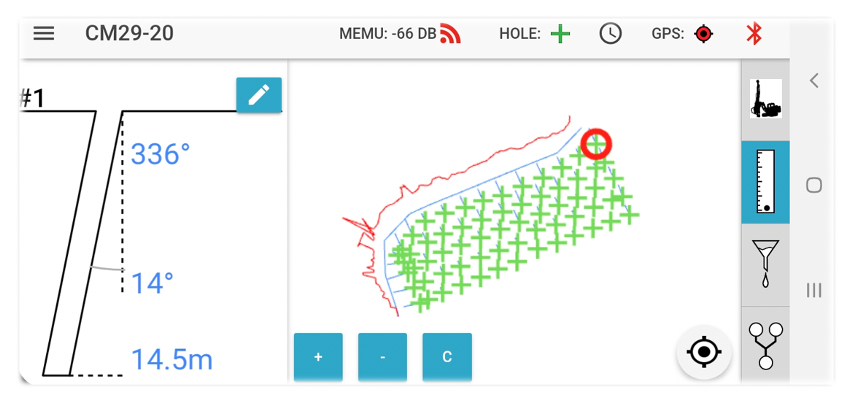
Figura 10.- Ejemplo de información mostrada en Expertab.
Además, la tableta identifica de forma única a cada barreno por sus coordenadas GPS por lo que evita cualquier posible confusión a la hora de cargar voladuras de malla compleja o con muchas filas. Cuando la carga se realiza mediante unidad MEMU, Expertab se conecta mediante bluetooth al autómata de la unidad y gestiona la carga automática de cada barreno.
Durante la carga se pueden dar circunstancias adversas que no permitan la carga conforme al diseño original: barrenos tupidos, por ejemplo. Por este motivo, la carga real por barreno se registra también en Expertab y se obtiene fácilmente el parte de carga real tras la voladura, barreno a barreno. Este registro es de gran importancia a la hora de investigar a posteriori posibles fallos o analizar la correcta salida y fragmentación de una voladura.
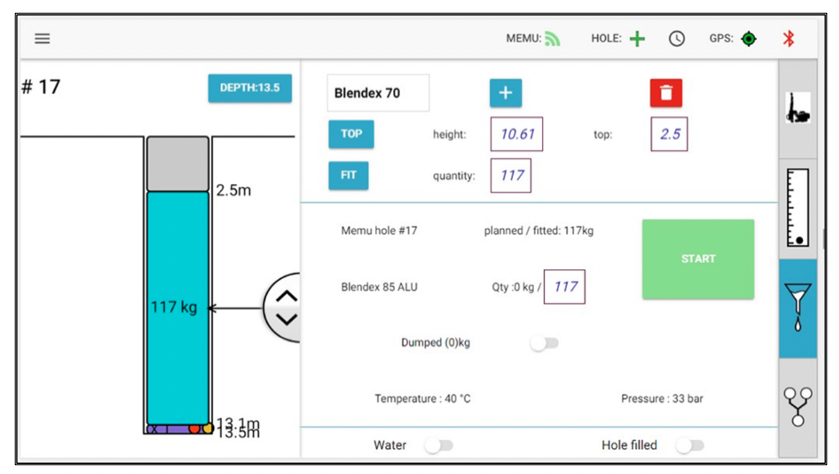
Figura 11.- Informe de carga real en Expertab.
2.1.6.- Base de datos Explore
El registro de todos los datos relacionados con la identificación, el diseño, carga, disparo y los resultados de las voladuras es de gran importancia. Este registro se lleva a cabo a través de la plataforma Explore que almacena toda la información en modo nube. Esta información está disponible para el usuario en cualquier momento.
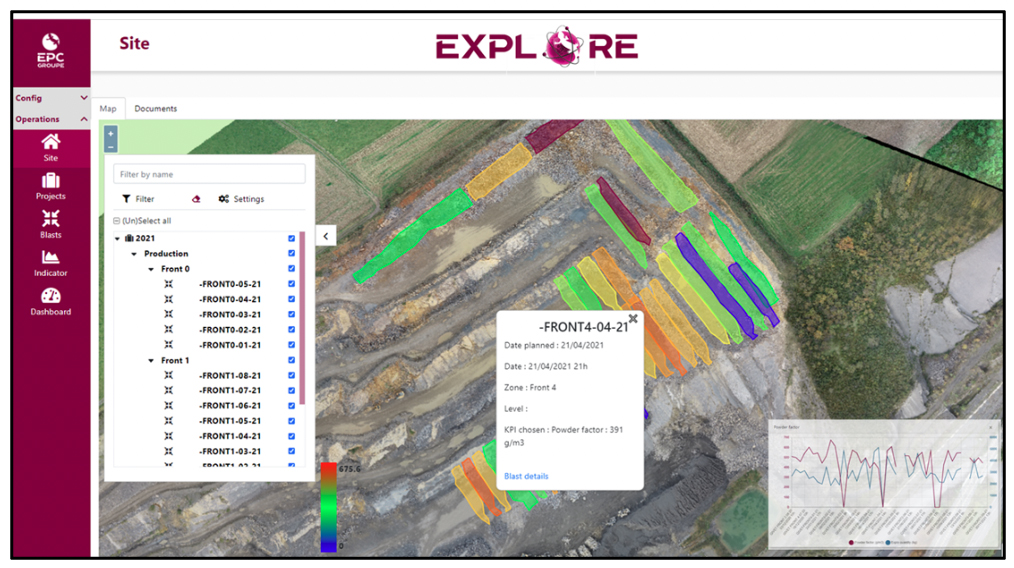
La base de datos se va alimentando con información actualizada conforme se progresa en el proceso de diseño, primero, y de carga y disparo, después. En concreto, se suben a Explore:
- Datos referentes a la identificación de la voladura, situación en plano de la explotación, fechas, etc.
- Parte de perforación y evolución de los diseños generados en Expertir
- Informe Expertrab de carga real por barreno
- Filmación de la voladura y registros de sismografía y onda aérea
- Análisis correspondientes a los resultados de voladura: granulometría, análisis de empuje de la pila
- Otros KPI de resultados asociados
2.2.- Metodología de trabajo en diseño y control
En el apartado anterior se han descrito las herramientas disponibles y se ha hecho una breve introducción de su aplicación que permite intuir la metodología de trabajo que se debe seguir en el diseño y control de voladuras en cantera; sin embargo, merece la pena dedicar un subapartado a este concepto para recalcar la importancia de esta metodología, el orden a seguir, y hacer una descripción más detallada de cada paso. Cada voladura se debe considerar como un proyecto independiente que debe ir referenciado en la base de datos Explore como tal. El proceso de trabajo se compone de diferentes etapas y es cíclico, repitiéndose desde el origen para cada nueva voladura a proyectar. Los resultados de voladuras precedentes y la experiencia obtenida con anterioridad en la zona de voladuras deben emplearse para alimentar el proceso de diseño desde el principio que, recordemos, tiene que garantizar la seguridad de la voladura en su conjunto; lo cual incluye también todas las labores posteriores como el desescombro y el acondicionamiento del frente. Los pasos a seguir en esta metodología de trabajo son, por este orden:
- Obtención del modelo 3D del frente de voladura mediante dron
- Tratamiento de este modelo original en Expertir y diseño preliminar de la perforación: Coordenadas XYZ de los emboquilles / Profundidad, ángulo y azimut para cada barreno
- Marcado de coordenadas de emboquilles en el terreno mediante sistema de posicionamiento GPS
- Perforación de la malla siguiendo el diseño Expertir. Obtención del parte de perforación por barreno
- Medición de posibles desviaciones de perforación mediante sonda electrónica
- Diseño final de las cargas por barreno y de la secuencia de disparo en Expertir
- Diseño final se pasa a Expertab
- Carga y conexión de la voladura con la asistencia de Expertab
- Registro del parte de carga real por barreno en Expertab
- Disparo de la voladura. Filmación de voladura mediante dron
- Registro de sismografía y onda aérea
- Obtención de imágenes y vídeos de los resultados para posterior análisis de empuje y fragmentación
La evolución del diseño de la voladura en Expertir y todos los datos asociados: partes de perforación, de carga real, vídeos, análisis de resultados, etc. alimentan progresivamente la base de datos Explore donde se guarda la especificación, o documentación técnica, de cada voladura de manera individual.
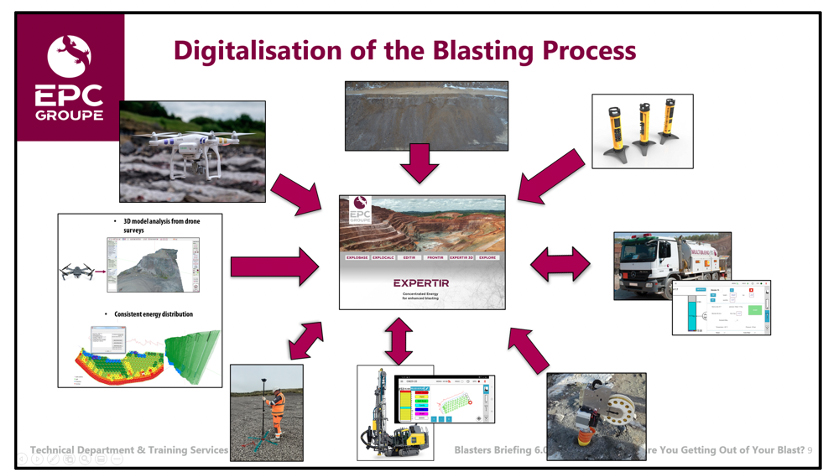
3.- Mejora continua en cantera de áridos en Reino Unido
3.1.- Descripción del tipo de proyecto
Las herramientas descritas anteriormente y la metodología de trabajo en cantera para la obtención de resultados óptimos están presentes en todos los contratos donde EPC Groupe es proveedor de servicios de perforación y voladura. En algunos de estos sitios, además, a lo largo de los últimos años, se ha entrado en proyectos concretos de mejora de resultados en colaboración con el cliente (operador de la cantera). En estos proyectos, además de medir de forma sistemática los resultados directos de voladura: fragmentación, empuje de la pila de escombro y sismografía, también se definen de manera conjunta con el operador de la cantera unos indicadores clave de desempeño (KPI) aguas abajo de la etapa de perforación y voladura, que dependen de la calidad de los resultados obtenidos por esta. Estos KPI se miden de manera continua a lo largo del proyecto y se evalúa su evolución durante el mismo. Algunos de estos KPI son cuantificables de manera directa no sólo en unidades físicas, sino también monetarias; por lo que extraer conclusiones de ahorro directo en este tipo de proyectos es relativamente sencillo siempre que estas mediciones se lleven a cabo de manera fiel y rigurosa.
3.2.- Descripción del sitio
Uno de los últimos trabajos de este tipo se está llevando a cabo en Reino Unido desde el año 2018 por parte del staff técnico de EPC UK. El sitio donde se lleva a cabo es una cantera de áridos con una producción anual de 6 Mt. El material a volar es una caliza de dureza alta y, debido al volumen de producción de la cantera, el número de voladuras anuales es elevado: unas 120 – 130 voladuras de media cada año; por lo que el trabajo de diseño y control de las voladuras por parte de EPC UK es continuo y a un ritmo muy elevado.
Las restricciones ambientales de las voladuras son PPV = 9 mm/s con un nivel de confianza del 95%; y 12 mm/s con un nivel de confianza del 99%. Para la medición sistemática de las vibraciones generadas por voladura, EPC UK dispone de tres sismógrafos fijos que miden de manera continua y envían los registros obtenidos de manera automática haciendo uso del servicio EPC Metrics.
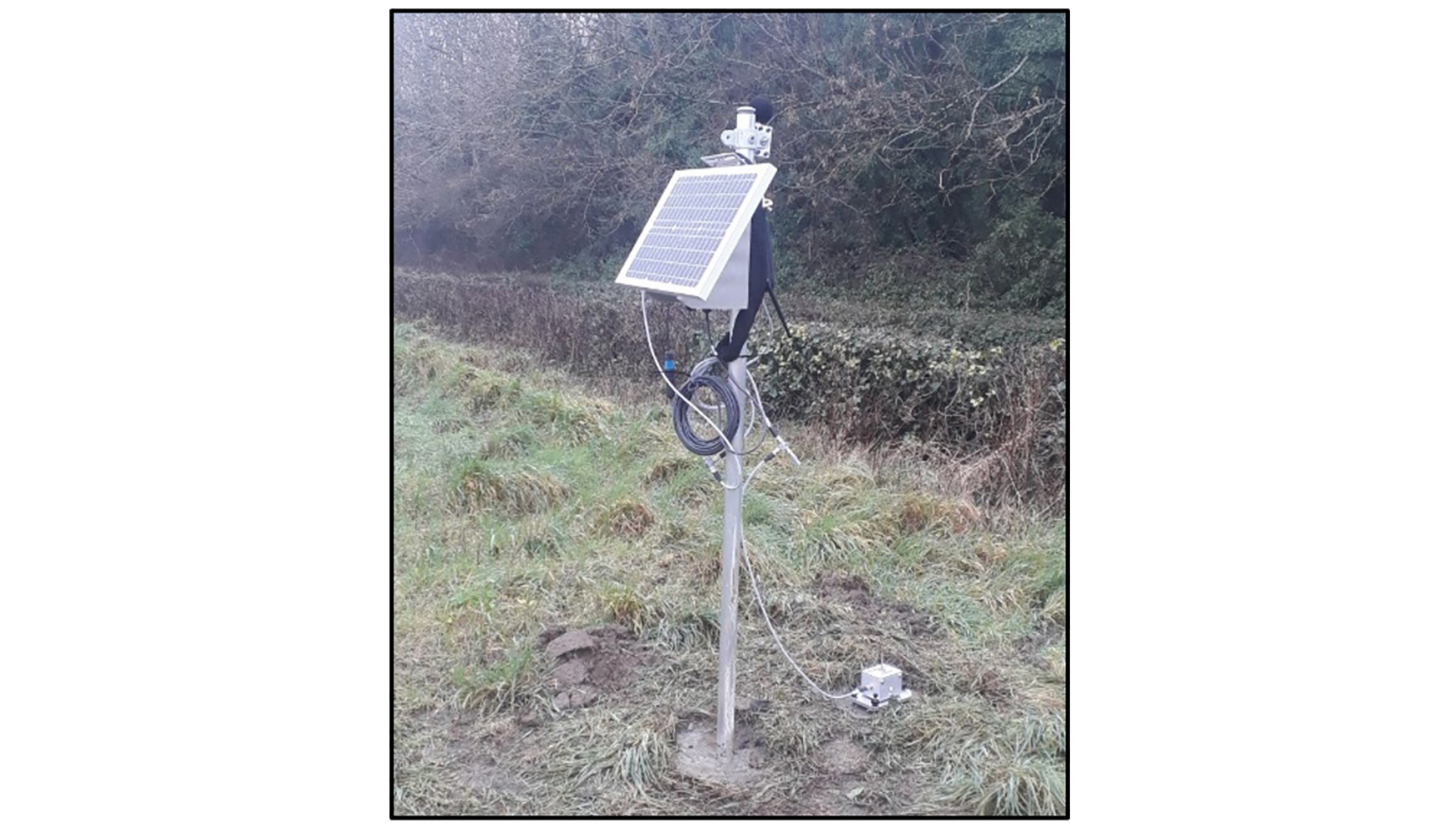
El explosivo utilizado es una emulsión dopada bombeable Blendex de EPC, sensibilizada in situ mediante unidad MEMU y cargada siempre desde el fondo del barreno. El cebado es con booster en el fondo de barreno. El sistema de iniciación es mediante detonadores electrónicos en todas las voladuras sin excepción.
La maquinaria de carga se compone de palas frontales de ruedas y el transporte a la machacadora primaria se realiza mediante volquetes desde el mismo frente de voladura. La cantera considera como 'scalpings', materiales finos de rechazo, los tamaños por debajo de 150 mm y como 'oversize' los tamaños por encima de 750 mm, que también se rechazan a la entrada del primario.
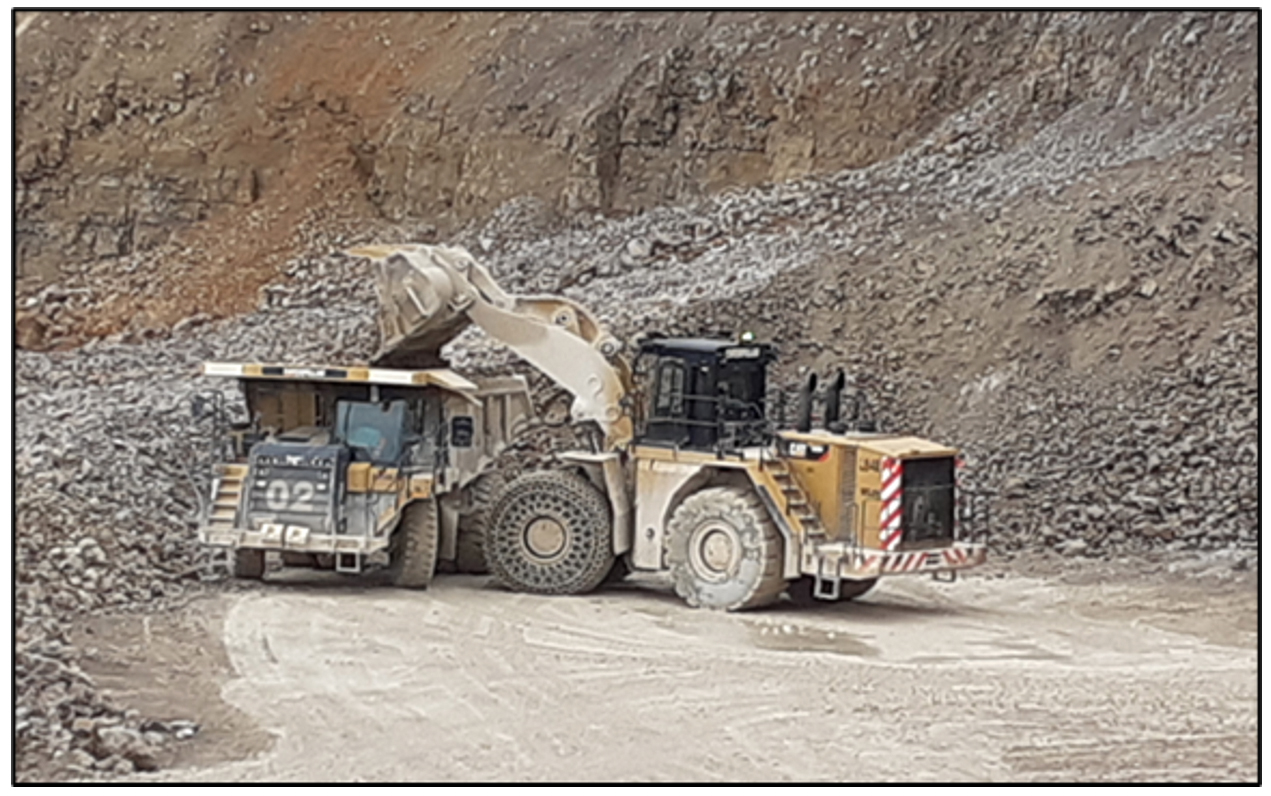
3.3.- Planteamiento del proyecto
Lo primero es definir una serie de KPI que hay que medir de manera continua, parámetros que dependen de manera directa de la calidad de las voladuras. En este caso se consideraron inicialmente los siguientes parámetros:
- Tiempos de carga en el frente
- Factor de carga
- Consumo de gasoil en maquinaria de carga y de transporte
- Horas de fragmentación secundaria
- Producción de machacadora primaria en t/h
- Consumo de energía eléctrica en el primario en KWh
- % de tamaños de rechazo en el primario: % Scalpings / % Oversizes
La evolución temporal de estos KPI se registra en la base de datos Explore. Además, EPC UK analiza las fotos de las pilas de escombro tomadas con dron tras cada voladura para estimar la fragmentación y el esponjamiento de la pila de escombro después de cada pega; esta información también se registra en Explore de forma sistemática.
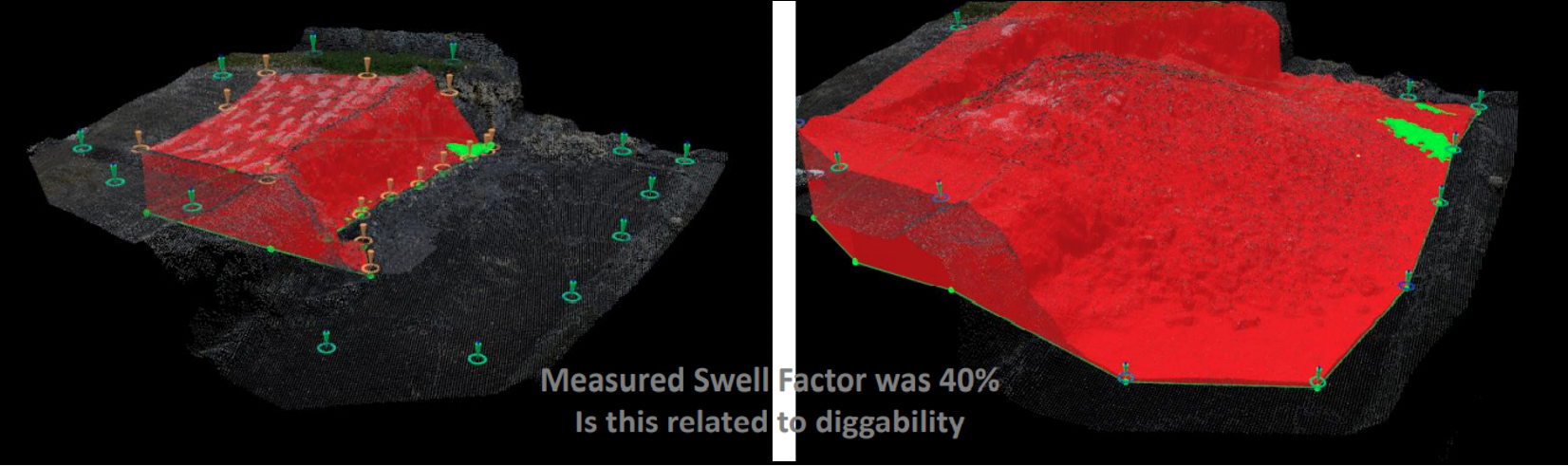
3.4.- Cambios introducidos en el tiempo y evolución de KPI
Durante 2018 no se introducen cambios en los diseños de voladura, pero se reemplaza el programa original de diseño por Expertir que, gracias a su función de cálculos de energía optimizada por volumen entre otras, permite una mejora sistemática en todos los diseños de voladura. Con el empleo de esta nueva herramienta, ya se aprecian mejorías en las mediciones de KPI de manera casi inmediata durante 2018.
En el año 2019 se introducen el grueso de innovaciones en cuanto herramientas de medición y control:
- Introducción de drones en la producción de modelos 3D del frente y en labores de control de resultados
- Empleo de Smart Rigs, carros de perforación equipados con sistema de posicionamiento por satélite
- El explosivo pasa a ser Blendex 70 (70% de matriz de emulsión sensibilizada, 30% de ANFO)
- Se emplea Expertir con la función Autodrill Layout: esta función diseña de forma automática el plan de perforación que asegura una distribución óptima de la energía por volumen de roca
- Introducción de mallas a tresbolillo. Tradicionalmente se habían empleado mallas cuadradas, las más frecuentes en Reino Unido.
Ciertos KPI definidos inicialmente no se pudieron seguir durante la ejecución del proyecto por problemas técnicos ajenos a EPC UK y al operador de la explotación. En concreto, no se pudo hacer un correcto seguimiento de:
- Tiempos de carga en el frente
- Factor de carga
- Consumo de gasoil en maquinaria de carga y de transporte
- Horas de fragmentación secundaria
El proyecto progresa durante 2019 y 2020, y el equipo de ingenieros de voladuras de EPC UK va introduciendo cambios paulatinamente en los diseños de las mallas, cargas y secuencias para ir afinando los resultados obtenidos de forma progresiva.
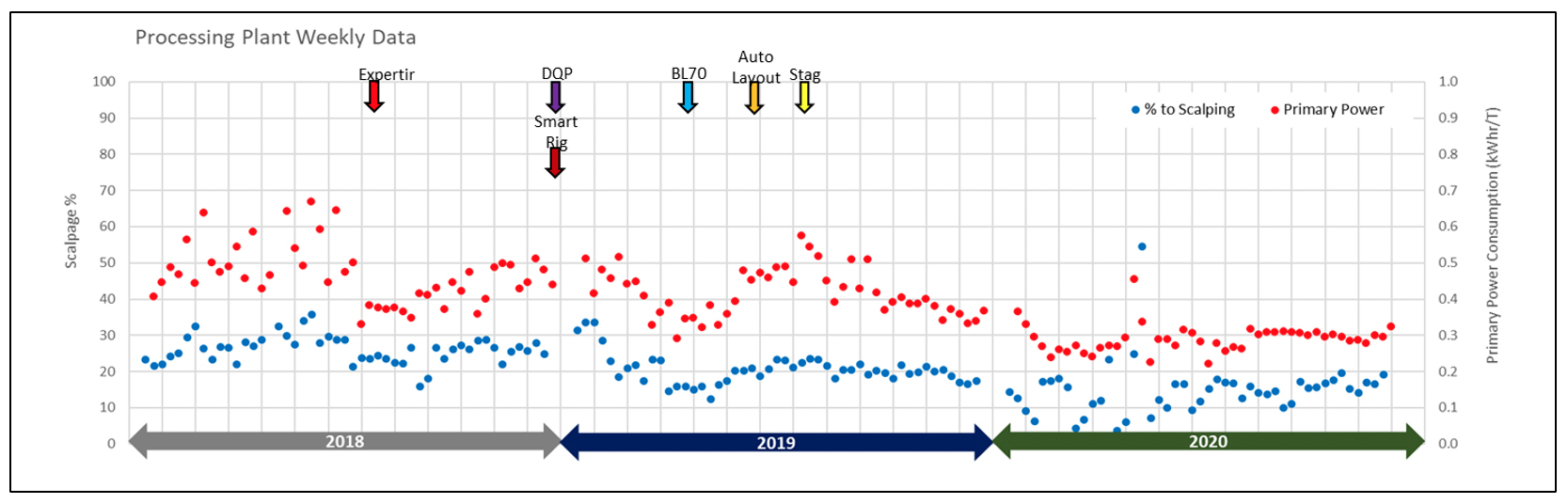
A partir de 2019 se obtienen interesantes resultados en las mediciones de los KPI previamente definidos. En concreto:
- Reducción de consumo de energía eléctrica en el primario de 0,18 kWh/t (Disminución del 38,3%)
- La cantidad de rechazos por finos (scalpings) se redujo en un 11,2%
- Se amplió en un 12,9% el porcentaje de material que entraba en el primario
- La producción semanal de la machacadora aumentó en un 12,5%
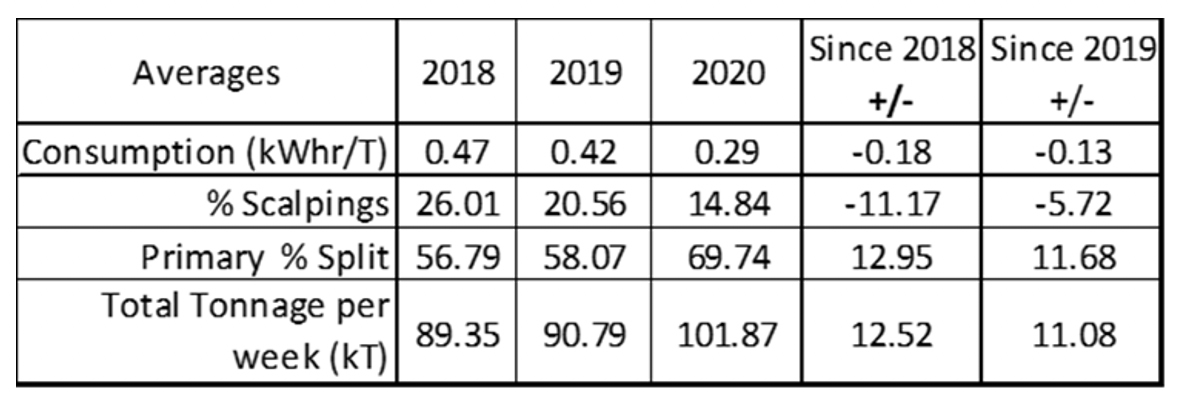
En definitiva, se aprecia en la progresión de estos KPI:
- Reducción importante en el consumo de energía y aumento del material que pasa a machacadora
- Mejoría en la fragmentación media obtenida por voladura: se obtiene una curva de fragmentación final más estrecha, con menor dispersión de tamaños
- Aumento en la producción horaria de la machacadora y disminución del material de rechazo
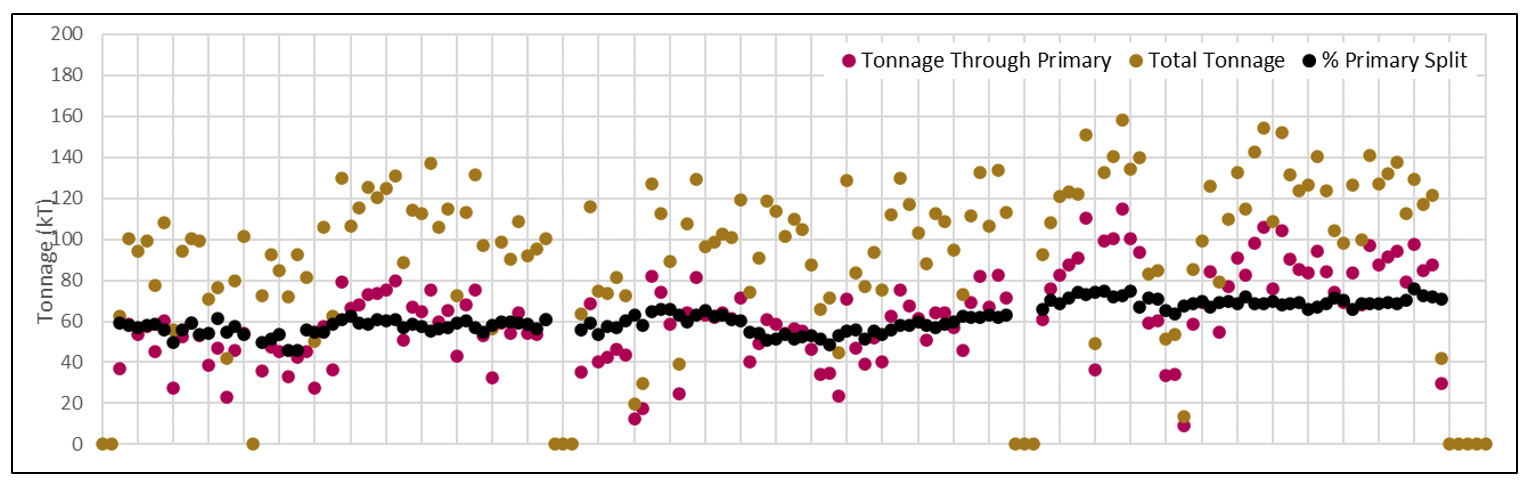
Estos resultados de mejora en fragmentación y consumos energéticos se obtuvieron gracias a una distribución óptima de la energía del explosivo en cada voladura. Para ello no fue necesario un incremento del coste en perforación y voladura; al contrario, gracias a este reparto óptimo de la energía del explosivo, se consiguió una reducción del 5,3% en el consumo específico de explosivos entre 2018 y 2020. Esto último choca frontalmente con la concepción original de Mine to Mill tal y como se presentó en el apartado 1 de este documento.
4.- Conclusiones
Las herramientas actuales de diseño y control de voladuras permiten una digitalización total del proceso, desde el diseño hasta la etapa de control de resultados. El análisis completo de KPI en cantera es posible gracias a:
- Tecnología de drones para análisis y control
- Sistemas telemáticos instalados en la planta
- Procesado y almacenamiento de los datos de rendimiento en la planta
De esta manera se puede cuantificar de manera absoluta el resultado de cada voladura y analizar su impacto en el conjunto de la operación en cantera. Esta información permite una toma de decisiones informada sobre futuros diseños para optimizar el proceso completo de fragmentación de la roca. Se entra de este modo en la posibilidad de llevar a cabo verdaderos proyectos de mejora continua con la reducción total de costes como objetivo último.
En el caso real presentado se han podido observar unas mejoras sustanciales en aquellos KPI que se pudieron medir con precisión, a la vez que se ha reducido el consumo específico de explosivo. Como consecuencia de esto se ha podido constatar una mejora evidente en el rendimiento energético del conjunto del proceso de arranque y reducción de tamaños en la cantera con los consiguientes ahorros asociados.
Bibliografía
- Queen’s University At Kingston. – Blasting Technology Course. 2000
- Work Safe BC.- Blaster’s Handbook. 2007
- Cordon / Christie. - The Institute of Quarrying. Explosives in Quarrying. 2010
- Comunidad de Madrid – Guía de Ahorro y Eficiencia Energética en Canteras de Áridos. 2011
- Bernaola / Castilla / Herrera.- Perforación y voladura de rocas en minería (ETSIM). 2013
- MP Awards – Explosives at Quarries (Quarries Regulations 1999 / Guidance Note Series). 2014
- Sfepa – Guide de Bonnes Pratiques en Pyrotechnie. 2015
- Miteco. - Guía de buenas prácticas en el diseño y ejecución de voladuras en banco. 2016
- Muñoz García. - El coste de no usar tecnología digital en el diseño de voladuras en banco. 2020
- http://www.encuentrometalurgia.com/mine-to-mill-2020/
- Muñoz García. -Voladura 4.0: Digitalización total en el ciclo de producción en mina. 2021
- EPC UK. – Shotfirer training material. 2021
- EPC Groupe. Blaster’s Briefing Webinar Series. 2020 & 2021