Reparación de componentes mediante láser cladding
A modo de ejemplo, los gastos directos de la corrosión de componentes está cuantificada en el 3,5% del PIB de los países industrializados, incluyendo en este apartado los costes de protección, así como de sustitución de los componentes dañados por el ambiente al que están sometidos. A pesar que no existen datos oficiales en España, la extrapolación sitúa su impacto en los 18.000 millones de euros anuales. A este coste, hay que añadir los costes asociados a dichas modificaciones y que no pueden cuantificarse fielmente: costes de paralización de plantas productivas, fugas, contaminación medioambiental, y un largo etcétera que ralentizan la productividad mundial. Adicionalmente a este coste económico, hay que añadir el coste ecológico (tanto desde el punto de vista de materiales como energético) que supone la reposición de los materiales dañados: un 25% del acero producido a nivel mundial está destinado a restituir piezas dañadas.
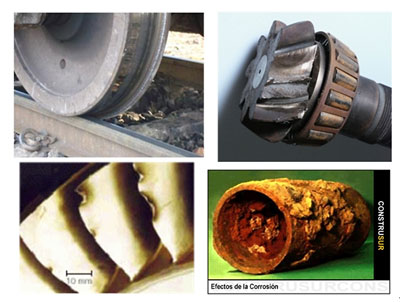
Láser cladding: la mejor alternativa
La reparación de componentes requiere la adición de material en el área desgastada, garantizando la correcta calidad del material añadido, tanto en cuanto a la ausencia de defectos (porosidad y grietas), como en cuanto a la estructura metalográfica, dureza y propiedades mecánicas.
Una de las principales tecnologías para realizar este aporte de material es el ‘láser cladding’ (o plaqueado láser). En esta tecnología una fuente de energía concentrada en una pequeña zona de trabajo (son habituales para estas tecnologías diámetros de foco a partir de 0,1 y hasta varios mm) calienta la superficie de trabajo hasta llegar a fundirla. Por otra parte, se envía material (ya sea en forma de hilo o en forma de polvo) al área fundida, que se funde y queda, de esta forma, adherido a la superficie del material. La reducida cantidad de calor aportado, permite el enfriamiento rápido del material, obteniéndose de esta forma una estrucutura con tamaño de grano pequeño y por tanto estructura mejor, en muchos casos, que el material original.
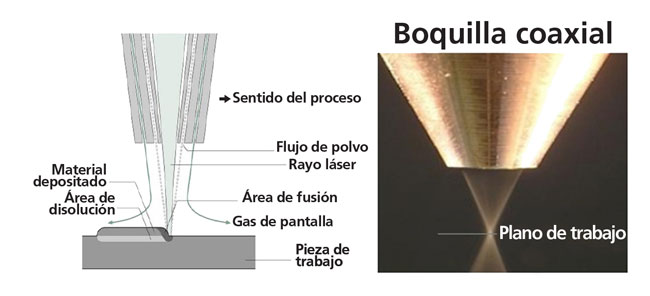
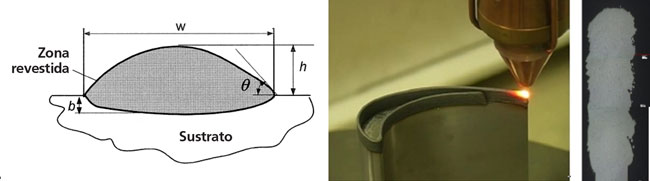
El aporte de material, y en particular el láser cladding, es una tecnología en auge tanto para la fabricación de componentes, como para la recuperación de los mismos del desgaste al que son sometidos durante su vida. En particular, y para componentes en los que el material base es susceptible de deformaciones, el láser cladding presenta ventajas respecto a otras tecnologías, debido a la menor distorsión de la pieza, menor zona afectada térmicamente, etc, además de conseguir una geometría más cercana al ‘near net shape’, y por tanto, reducir el tiempo de mecanizado posterior.
En la actualidad existen numerosas tecnologías de generación de recubrimientos en componentes sujetos a entornos de trabajo agresivos que limitan de esta forma la vida útil de la pieza. Entre los beneficios de las tecnologías de generación de recubrimientos destacan los siguientes:
- Resistencia al desgaste.
- Protección contra la corrosión.
- Recuperación de componentes desgastados o rotos.
Algunos de ellos están diseñados para la generación de recubrimientos protectores de pocas micras de profundidad (Cromado, PVD, CVD…), pero no son válidos para su uso en piezas de gran tamaño ni para la reparación de componentes dañados, a partir de la reconstrucción geométrica del material dañado. Para ello, utilizan, al igual que el láser cladding, una fuente de calor externa, que funde localmente el material, y la adición localizada de material (habitualmente en forma de polvo) en esa zona.
Entre las tecnologías actuales disponibles para la reparación de componentes, los más relevantes son los siguientes:
HVOF (High Velocity Oxigen Fuel): Proyecta partículas fundidas en un proceso de combustión y posteriormente aceleradas en una tobera logrando velocidades de los gases superiores a la velocidad del sonido. En contra de las distintas alternativas existentes, no existe calentamiento directo de la pieza, y por tanto, la adhesión del material en la pieza es peor.
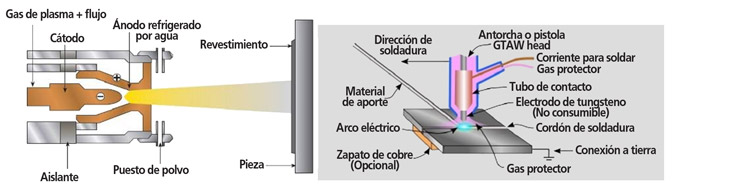
TIG: Es un proceso que utiliza un electrodo de tungsteno para generar un arco entre el mismo y la pieza, calentando de esta manera el material.
Plasma: Similarmente al aporte de material mediante TIG, se basa en la generación de un arco. La diferencia principal es la posición del electrodo, confinando de esta manera el plasma a un tamaño más reducido.
En todas estas técnicas, así como en láser cladding, el material añadido debe proporcionar a la pieza final las propiedades necesarias para el correcto funcionamiento de la pieza. Es de destacar, en este aspecto la oportunidad de utilizar material con elevadas prestaciones solamente a nivel local, reduciendo de esta forma el coste total en material de la pieza. En el caso del láser cladding, adicionalmente, el aporte de material mediante polvo permite obtener composiciones variables, para dotar a cada punto de las propiedades mecánicas necesarias.
Las ventajas del láser cladding respecto a las alternativas existentes actualmente son las siguientes:
- Posibilidad de automatización, debido al control y fiabilidad de la fuente de energía, en contra de la situación del resto de tecnologías. Adicionalmente, la ausencia de componentes como electrodos que se desgastan durante su vida útil permite un funcionamiento estable con el tiempo. Finalmente, es un proceso que (al contrario que los procesos basados en la generación de un arco), no es sensible a los cambios por las condiciones atmosféricas.
- Aporte de calor en zona de reducido tamaño. La utilización de una fuente de calor muy localizada permite un tratamiento local a las piezas de interés, permitiendo incluso la reparación de componentes con tamaños característicos por debajo del milímetro. De esta forma, el material aportado es mucho menor que con otras técnicas y por tanto el mecanizado posterior es más rápido.
- El aporte local y reducido de energía, da lugar a distintas ventajas desde el punto de vista microestrucutural. Por una parte, permite elevadas velocidades de calentamiento y enfriamiento, dando lugar a una microestructura con pequeño tamaño de grano y por tanto, mejores propiedades mecánicas. Por otra parte, permite evitar la aparición de grietas durante la recuperación del material, sin la necesidad de utilizar precalentamiento de pieza.
- Reducida dilución y distorsión de la pieza. Mediante otras tecnologías, es necesario en algunos casos mecanizar la pieza para recuperar la planitud requerida. El calentamiento local de la pieza, y el rápido enfriamiento lleva a una menor distorsión, de forma que es posible el mecanizado localizado en la zona aportada.
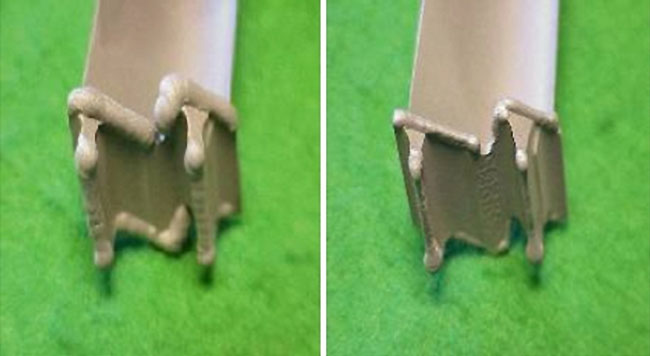
Ejemplos industriales y sectores de interés
El origen de la tecnología de reparación mediante láser cladding ha estado tradicionalmente en componentes que eran difícilmente reparables por las tecnologías tradicionales, ya sea por las variaciones existentes debido a la menor estabilidad del proceso, y la componente manual de los mismos. De esta forma, uno de los primeros sectores en utilizar el láser cladding ha sido el sector aeronáutico, en el que la compleja geometría de la pieza, su tamaño y su valor hace especialmente interesante el uso de esta tecnología.
En la actualidad, la mayor potencia de los sistemas láser, y las reducciones del coste de proceso permiten ampliar el uso de la tecnología a componentes, cada vez de mayor tamaño. La posibilidad de automatizar la tecnología, la reducida dilución y zona afectada térmicamente, y la reducida distorsión geométrica ofrecen ventajas competitivas también en componentes de elevado tamaño.
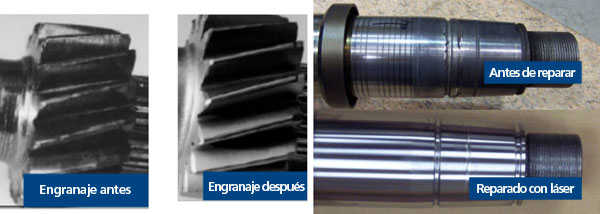
Hay numerosos ejemplos industriales que demuestran la viabilidad tecnológica y económica de la reparación de componentes mediante láser cladding está demostrada por numerosas aplicaciones, implantadas ya a nivel industrial. Así, existen aplicaciones industriales de láser cladding para reparación de componentes en sectores tan diversos como aeronáutico, sector petroquímico, minería, componentes de transmisión y engranajes o en herramientas de corte para mecanizado.
Destaca en este aspecto el sistema automático de reparación de álabes de compresor, desarrollado por DanobatGroup e IK4-Ideko e instalado en las instalaciones de Iberia en la Muñoza. Dicha célula, permite, de forma automática la reparación de 40 000 álabes al año, incluyendo mecanizado, aporte de material mediante láser cladding, y mecanizado final. Para garantizar tanto el aporte de material como el mecanizado final de la pieza a pesar de las variaciones geométricas existentes entre las distintas piezas, los procesos se adaptan a la geometría real de la pieza, medida individualmente.
Adicionalmente, el láser cladding ofrece además la posibilidad, no solo de reparar un componente, sino también la fabricación directa del componente. De esta forma, para componentes de geometría compleja y con una cantidad muy elevada de material a mecanizar (y por tanto, alto coste en material de desbaste), la fabricación aditiva del material es una alternativa viable a la fabricación convencional basada en el mecanizado de elevadas cantidades de material. Según previsiones de General Electric, en el futuro, el 50% de los componentes del motor serán fabricados mediante fabricación directa.
De esta forma, el uso de la tecnología de láser cladding para reparar (o para recubrir un área local de una pieza con materiales de mejores propiedades para aumentar la vida útil del componente) es una tecnología en vías de auge. De esta forma está en el camino de convertirse en una tecnología aceptada plenamente en la industria, de la misma manera que lo están ya en la actualidad procesos como el corte o la soldadura por láser, implantados en la industria y funcionando 24 horas al día.
Conclusiones
La tecnología de láser cladding es una tecnología que ha demostrado su viabilidad tecnológica en componentes de alto valor añadido y está expandiendo su rango de aplicación a nuevos componentes susceptibles de desgaste, corrosión o incluso errores en el mecanizado de la pieza. Ofrece, de esta forma, una oportunidad a las empresas de reducir los costes económicos asociados a la vida útil completa de la pieza a partir de una tecnología novedosa.