Libertad en el diseño CAD gracias a la Fabricación Aditiva
Algunas de las tecnologías han alcanzado un nivel de madurez tal que permiten trabajar con materiales bien conocidos en la industria y, en la ingeniería, alcanzando las mismas características mecánicas que con otros procesos más conocidos. Y, lo que es más, que el aumento de la complejidad en el diseño no incremente al coste de producción sino que, como veremos en alguno de los casos siguientes, incluso lo reduce.
En este artículo nos referimos en exclusiva a productos de aleaciones metálicas obtenidos directamente de máquinas de sinterizado láser.
El primero de ellos refiere una pieza de grandes dimensiones fabricada por inyección de plástico, en el exigente sector de automoción, donde las ventajas de las tecnologías aditivas en colaboración con técnicas tradicionales ayudaron a solventar problemas de calidad y dimensionales.
En el segundo de ellos presentamos cómo unificar varias piezas en un único bloque permite ahorro de costes en varios ámbitos en una empresa pequeña, principalmente en mantenimiento y stock de repuestos.
El tercer caso nos habla de una pieza de gran complejidad destinada al sector aeronáutico, en el que la fabricación aditiva no sólo ahorra costes sino además acorta mucho elo tiempo de fabricación, desde el diseño hasta la pieza final lista para su uso.
Inyección de plástico
El campo del moldeo por inyección es uno de los que mejores y más espectaculares resultados está obteniendo con la aplicación de las tecnologías aditivas. La principal razón para ello es que permiten fabricar canales conformales de refrigeración muy complejos y perfectamente optimizados a la geometría de la pieza, que de otro modo serían imposibles de conseguir con tecnologías convencionales, en unos plazos de tiempo similares y con unos presupuestos del mismo orden; en general, serían directamente imposibles de conseguir.
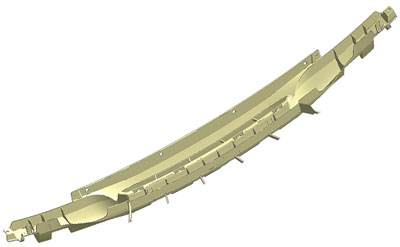
El caso en cuestión es una pieza de grandes dimensiones y alto valor /750 cm3), con tolerancias muy estrechas, altos requisitos dimensionales y estéticos, con zonas de paredes muy finas entre grandes masas de material conectadas por zonas de paso muy estrecho.
Cuando un molde no se enfría de la forma correcta pueden producirse en la pieza defectos de calidad como visos, líneas de diferente color, zonas sin llenar, zonas frágiles o retorcimientos y deformaciones inaceptables. Para ello hay una solución que consiste en esperar más tiempo con la pieza dentro del molde hasta que todo al plástico se haya solidificado, solución que encarece tremendamente el proceso.
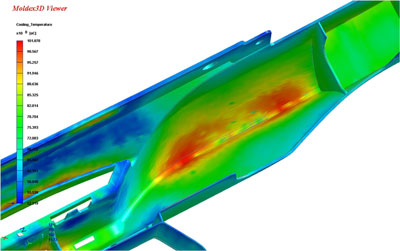
Mediante un diseño optimizado de los canales de refrigeración —creando canales conformales— se consigue suministrar la cantidad adecuada de fluido refrigerante a la distancia óptima de la pieza en relación con la cantidad de material a enfriar (espesor de material) y al flujo deseado de calor (velocidad de enfriamiento en cada punto). Con ello mejora mucho el rendimiento del proceso porque se pueden conseguir disminuciones muy importantes del tiempo de ciclo de entre el 20% y el 60% (abaratar el coste por pieza) a la vez que se mejora mucho la calidad del producto final, en estética, características mecánicas y dimensionales.
En este caso hemos contado con la estrecha colaboración de una empresa especializada en el diseño de moldes de inyección y en la simulación del proceso que con la ayuda de software específico puede simular el efecto que sobre el proceso de inyección tiene la geometría de los canales de refrigeración.
El diseño del molde existente antes de nuestra intervención —con la tecnología tradicional de canales rectos a base de taladros y tapones— deja ciertas zonas con una temperatura demasiado alta al final de los 56 segundos que duraba el ciclo de inyección. La distribución de densidad de material no es adecuada y el gradiente de temperaturas entre unas zonas y otras también es demasiado alto. Esto hace que las piezas se retuerzan (defecto geométrico) al acabar de enfriar fuera del molde y presenten defectos superficiales.
La solución adoptada consiste en construir un inserto con una eficiencia de refrigeración adaptada a las necesidades de cada una de las tres zonas problemáticas. En la figura 3 se muestra la superficie exterior de uno de los insertos y el sistema tradicional de enfriamiento. En la parte inferior se muestra la geometría del canal conformado obtenido tras varias iteraciones del proceso de diseño y simulación.
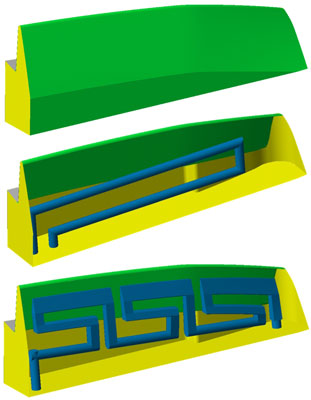
Es bastante obvio que estas geometrías espirales, y curvas con cambio de sección no se pueden fabricar a no ser que la precisión y materiales nos permitan acudir a procesos de fundición a la cera perdida, lo que no es aplicable para los moldes de inyección de grandes series. Sin embargo, las tecnologías de fabricación por adición de capas (AM) permiten fabricar estas geometrías complejas hasta límites nunca vistos hasta ahora.
En su contra se debe indicar que resultan muy ineficientes para fabricar formas simples y masivas, para lo que las tecnologías de arranque de viruta están perfectamente adaptadas y optimizadas.
En este caso gran parte del éxito se ha debido a la adecuada combinación de ambas para obtener un producto —los insertos— muy eficaces y a un precio muy competitivo.
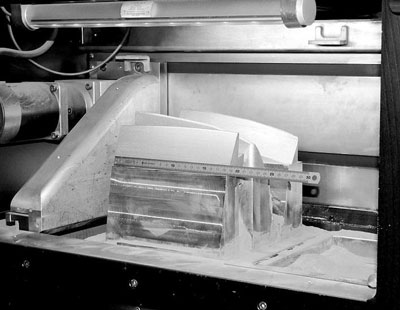
A pesar de que los tres insertos tienen distinta geometría se fabricaron simultáneamente en una sola plataforma de una máquina EOSINT M270 utilizando material 1.2738 TS. Una vez fabricados se procede al mecanizado y acabado por sistemas tradicionales de mecanizado y pulido.
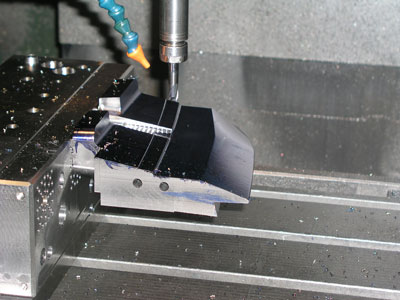
Los resultados obtenidos para la inyección de la pieza se corresponden con lo obtenido en la simulación por elementos finitos (FEA) del proceso de inyección. Se ha podido reducir el tiempo de inyección desde los 56 segundos iniciales hasta tan sólo 35 (reducción del 37%) a la vez que mejora la densidad del material y la temperatura media disminuye. En el momento de la eyección de la pieza ya no hay ningún punto por encima de la temperatura de solidificación sino unos 20 °C más abajo, lo que reduce virtualmente a cero el retorcimiento y mejora notablemente la calidad visual.
El ritmo de producción ha pasado de una pieza por minuto con defectos de calidad a casi dos piezas buenas por minuto, con un incremento del coste de los insertos de poco más del 20% incluyendo tanto la ingeniería y simulación como la fabricación por tecnología aditiva.
Reduccion de mantenimientos
Bionorte es una empresa Asturiana que produce biodiésel y otros subproductos de alto valor añadido a partir de aceites vegetales residuales. En un punto concreto de la instalación existe una bomba para los fluidos de proceso, cuyo estado tiene gran influencia en la productividad de la planta y en la calidad del producto final. Así es que en cuanto empieza a deteriorarse el rodete debe ser reemplazado de inmediato para evitar los costes de no calidad y de baja eficiencia de la planta. A pesar de que la parada para el cambio del elemento no es muy larga, la duración del mismo viene a ser de unos dos meses, con un coste de piezas de recambio razonable, procedentes de un fabricante extranjero con largo plazo de entrega entre 5 y 8 semanas. Esto obliga a la empresa a tener stock de pieza de recambio.
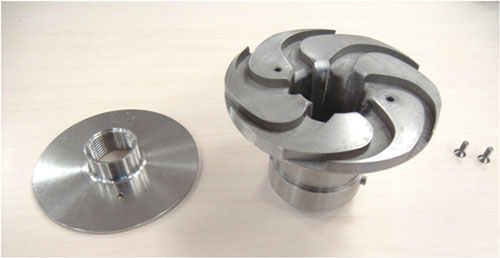
En este caso se ha procedido al diseño de una pieza sustitutiva de las tres que conforman el rodete, de modo que se puedan fabricar integradas en una sola mediante fabricación aditiva directamente en acero inoxidable, en un sistema EOSINT M-270. El coste de la reingeniería ha sido de aproximadamente la mitad del coste del conjunto de recambio y la fabricación de la pieza directamente en metal, incluyendo los costes de mecanizado y acabado de las zonas de asiento, etc. ha sido un poco más del doble que el conjunto de repuesto original.
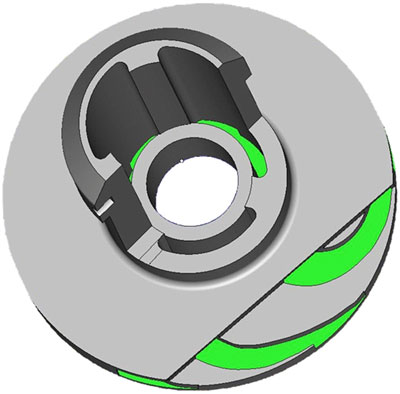
La nueva pieza fue puesta en funcionamiento en julio de 2011 y lleva trabajando desde entonces a pleno rendimiento y sin deterioro aparente. Esto se debe sin duda a la robustez del nuevo diseño en una sola pieza. Aparentemente supone un sobrecoste importante respecto del recambio original. No obstante, dado que hasta ahora se han evitado ya seis cambios, la empresa se ha ahorrado ya 4 veces el coste en piezas de recambio, la mano de obra, el coste del tiempo de parada, los costes de no calidad y rechazos o reprocesos, aunque es cierto que ha tenido que invertir una pequeña cantidad en ingeniería en la ingeniería de la pieza.
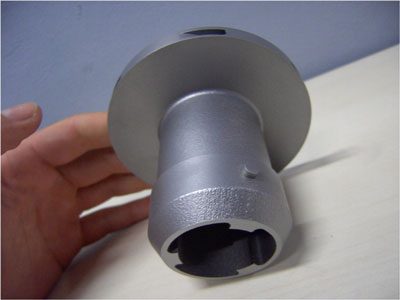
Instrumentacion aeronáutica
Ramem es una pyme madrileña de origen familiar, fundada en 1958, dedicada desde entonces al diseño y fabricación de equipos mecánicos y electromecánicos para la industria en general, que ha ido evolucionando desde la fabricación de utillajes para el sector de la automoción en sus inicios, al sector aeronáutico en los años 70, y a la actividad aeroespacial y científica, tanto civil como militar en la actualidad (Eurofigther, Airbus A380, Estación Espacial Internacional, Gran Telescopio de Canarias, ESRF, ALBA).
El caso que nos presenta es el de fabricación de unos Rake de instrumentación de presión para medir los perfiles de velocidad de gases a la salida de las turbinas de reacción, generalmente de uso aeronáutico. El requerimiento principal de estas piezas es que puedan trabajar a altas temperaturas (hasta 900 °C) resistiendo al ambiente corrosivo que suponen los gases de escape, sin merma en su resistencia mecánica por fluencia (creep).
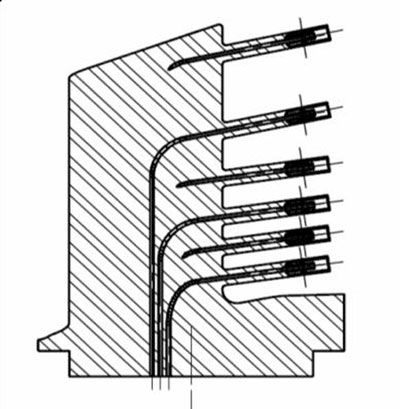
Al mismo tiempo y dadas las dimensiones se requiere una gran precisión: cada uno de los tubitos apunta en una determinada dirección y en su interior alojan una estructura de protección y un canal de unos 0,5 mm de diámetro que llega hasta la base del elemento. Todos los canales son independientes entre sí y no pueden comunicarse.
El material de fabricación es la aleación IN 718, material ampliamente utilizado en los motores de aviación por reunir las mencionadas características. No obstante es un material de procesado complejo ya que se endurece enormemente en los procesos de mecanizado sucesivo. El proceso actual implica partir de un bloque de material al que se elimina por mecanizado aproximadamente un 60% del material para dejar una preforma aproximada a la final.
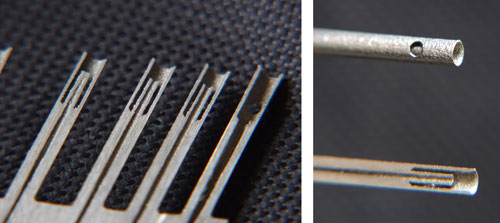
En esa preforma se talla un canal con un elevado grado de precisión y se fabrica una tapa para el mismo con encaje adecuado y que pueda deslizar hasta su posición. Mediante electroerosión se deja la forma de cada tubo exterior de protección con su tubito interior.
Seguidamente se fabrican por separado cada uno de los tubitos y se doblan hasta la posición adecuada y se sueldan por brazing a cada uno de los obtenidos en la preforma. El proceso es muy laborioso y delicado dada la delgadez de las paredes y los diámetros diminutos. Todos ellos se colocan y ajustan en posición sobre la preforma, conduciendo los tubos hasta una tapa en la parte inferior del Rake. A continuación se coloca la tapa deslizante y se suelda. Se prosigue con el mecanizado final y el pulido final.
El empleo del procedimiento de fabricación aditiva mediante sinterizado laser (DMLS) permite construirlo de una sola vez, en un único bloque, en el material elegido Inconel 718, en un sistema EOSINT M280 en atmósfera de Argón. La precisión de estos sistemas permite obtener las finas geometrías sin ningún problema en la orientación requerida. Un paso de electroerosión permite ajustar las tolerancias y la rugosidad, y un pulido posterior acaba el proceso.
La sustitución por el proceso de fabricación aditiva supone reducir el plazo de fabricación desde las 16 semanas actuales hasta tan sólo cuatro, aumentar la precisión por eliminar operaciones manuales de doblado y soldadura, reducir un 60% del coste y sobre todo aumentar la robustez del conjunto al evitar montajes por partes, uniones, etc.
Se debe considerar además que dadas las características de estos sistemas de fabricación aditiva se pueden fabricar simultáneamente varios Rakes incluso diferentes entre sí, disminuyendo aún más el coste y plazo de producción.
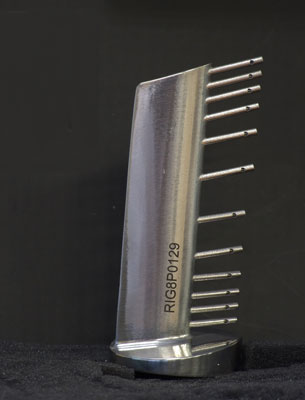