Planificación automática del torneado
1. Introducción
Teniendo en cuenta estas consideraciones, en este artículo se comenzará suponiendo que ya ha sido realizado el diseño de la pieza y del material de partida, así como han sido determinados la forma de sujeción de la pieza, el número de amarres y las superficies a mecanizar en cada uno de ellos [3]. Se realiza un análisis de las principales operaciones y se proporcionan métodos para determinar las zonas a mecanizar sobre la pieza, las direcciones de movimiento de las herramientas en cada una de ellas, la realización de las operaciones de desbaste y acabado, así como una preselección de las herramientas que pueden ser válidas. Finalmente se establecen las secuencias de operaciones en función de aspectos tecnológicos.
2. Operaciones habituales de torneado
Existen otras operaciones de mecanizado interior, tales como el taladrado, escariado y mandrinado. Otras operaciones más específicas son el roscado, ranurado, tronzado y moleteado. En la figura 1 se muestra una clasificación de las principales operaciones de torneado según su aptitud para distintas aplicaciones.
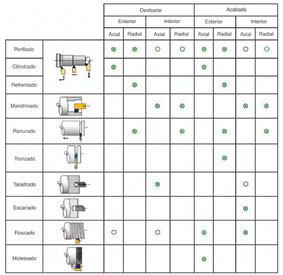
3. Operaciones generales de desbaste
3.1. Determinación de los volúmenes de mecanizado
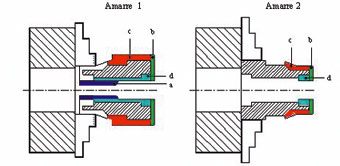
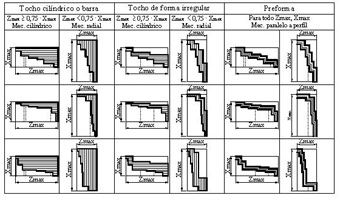
Zmáx >= 0,75. Xmáx y mecanizado radial en caso contrario.
El factor 0,75 da prioridad al mecanizado axial frente al radial, ya que los esfuerzos de corte aparecen mayoritariamente en la dirección axial, produciendo una menor flexión de la pieza y permitiendo mayores profundidades de corte para la herramienta en condiciones de estabilidad. Para las zonas interiores se aplican las mismas reglas que para el exterior. El mecanizado de preformas se realiza siguiendo paralelamente el perfil de la pieza, independientemente de la relación Zmáx / Xmáx.
En la figura 4 se muestran las direcciones de avance de la herramienta tras la aplicación de la regla anterior a la pieza de ejemplo.
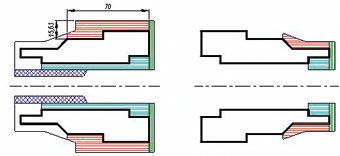
3.2. Determinación de las operaciones para un volumen de mecanizado
Se mecaniza con una herramienta en dirección al plato de garras (Z-). Si el perfil real obtenido (PRDd) difiere del teórico (PTD), es necesario realizar el siguiente paso. En caso de que ambos perfiles coincidan, se habría conseguido el mecanizado completo del volumen y no sería necesario realizar los siguientes pasos.
Se mecaniza con una herramienta en dirección contraria al palto de garras (Z+). Si el perfil de desbaste obtenido (PRDi) no coincide con el resultado deseado, se realiza el siguiente paso. En caso de coincidencia, el siguiente paso no es necesaio.
Utilizando una herramienta de ranurar en dirección radial (X-), se mecanizan aquellas zonas no eliminadas previamente.
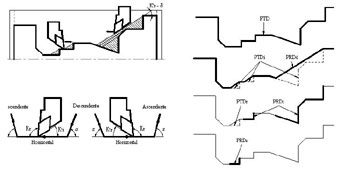
siendo d y d’ ángulos de seguridad para el desahogo de la herramienta (entre 2º y 5º) y a y d los índices de los tramos ascendentes y descendentes, respectivamente, del volumen de mecanizado.
Pueden existir ocasiones en las que no se encuentren herramientas que satisfagan la doble condición expresada anteriormente. En estos casos, se seleccionan aquellas herramientas cuyos ángulos se aproximen más a los valores deseados.
4. Operaciones generales de acabado
En las zonas exteriores, el procedimiento es parecido al llevado a cabo para el desbaste. Se comparan los perfiles reales con los teóricos al utilizar primero herramientas de avance en Z-, después en Z+ y, finalmente en X-. Los ángulos de posición de las herramientas coinciden con los calculados en el desbaste debido a que los condicionantes geométricos son los mismos. En fases posteriores para la selección de las herramientas, se determinará si se utilizan las mismas que para el desbaste ya que, al transcurriur en condiciones diferentes, se requerirán distintos sistemas de sujeción, tamaños, formas y calidades de plaquitas.
En general, en las zonas interiores se realiza el acabado con herramientas de mandrinar, avanzando desde el exterior hacia el interior de la pieza (Z-) y, si quedan zonas sin mecanizar, se utilizan herramientas cuyo avance es en tracción (Z+). Si es necesario, el mecanizado se complementa con herramientas de ranurar.
Las zonas interiores con diámetros menores de 20 ó 25 mm requieren operaciones de escariado siempre que no sean accesibles mediante herramientas normales de mandrinar, que así lo requieran las especificaciones de tolerancia y rugosidad (Rt <= 15 ím) [6] y que la zona a escariar sea accesible (zona de menor diámetro interior de las comprendidas entre el extremo de la pieza y la zona de mecanizado).
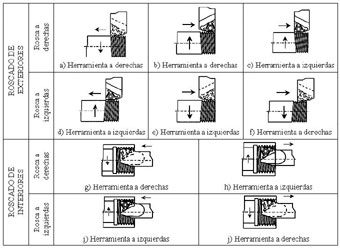
5. Operaciones de roscado
El torneado de roscas se considera una operación multipasada, pudiéndose realizar la penetración de la herramienta en cada pasada según distintas técnicas (figura 7). En general, se busca una buena evacuación de la viruta, con un buen acabado de los flancos de la rosca y con una vida de herramienta adecuada. Todos estos factores son función del material a mecanizar, del tamaño de la rosca y de la geometría del corte. En general, en control numérico se realiza la penetración en flanco modificado, que proporciona un buen comportamiento según los criterios anteriores.
En el torneado de roscas, los parámetros velocidad de corte, profundidad y avance aparecen relacionados entre sí mediante ciertos factores limitadores, tanto geométricos como tecnológicos. Así, por ejemplo, la velocidad de corte suele ser un 25 por ciento menor que en el cilindrado debido a que la forma de la plaquita dificulta la evacuación de calor y esto podría originar una deformación en el filo. En cuanto al avance (mm/rev), debe coincidir con el paso de la rosca (mm). En relación a la profundidad de corte, para cada pasada interesa una distribución de tensiones constante en los filos. Teniendo en cuenta que en cada pasada aumenta la longitud de contacto entre material y filo, para mantener constante la tensión es necesario reducir el espesor de viruta y, por tanto, la profundidad de corte.
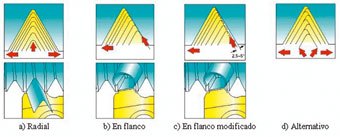
siendo d la profundidad total de la rosca, np el número de pasadas (estos dos datos son proporcionados normalmente por el fabricante de la herramienta) e i el número de la pasada que se va a mecanizar (i = 1, 2, ..., np). En la Fig. 8 se muestran los valores de las profundidades de corte en cada pasada para una rosca métrica de paso p = 1,5 y np = 6 pasadas, obtenidas a partir de la expresión anterior, y se comparan con las proporcionadas por el fabricante Sandvik Coromant.
Cuando la profundidad total de la rosca no es un dato conocido, se puede calcular mediante la expresión:
d=C.p,
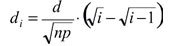
En cuanto a la velocidad de rotación del husillo, ésta se mantiene constante en cada una de las profundidades para que la entrada de la rosca coincida en todas ellas. Como contrapartida, al mantener constante el régimen de giro del husillo, la velocidad de corte se irá reduciendo a medida que la herramienta profundiza. Sin embargo, este efecto no es muy acusado, dado que la diferencia entre profundidades es muy pequeña y, por tanto, la variación de la velocidad de corte es poco significativa.
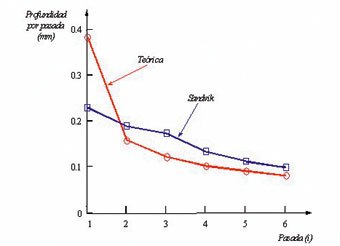
6. Operaciones de ranurado y tronzado
En el desbaste de ranuras, el avance de la herramienta se realiza en dirección radial. Cuando la ranura es más ancha que la herramienta, se repite el movimiento radial de la misma en distintas posiciones hasta cubrir todo el ancho. Si la forma de la ranura es simétrica, el mecanizado se realiza comenzando por el centro y reposicionándose alternativamente a la izquierda y a la derecha. Cuando la ranura es asimétrica, se comienza a mecanizar por la zona menos profunda (figura 9a), de manera que se facilita la evacuación de la viruta.
En el acabado de ranuras, la herramienta se desplaza paralela al perfil, procurando que los movimientos radiales los realice entrando hacia el centro de la pieza (X-) para garantizar un mejor control de viruta que en el caso de que se moviese en sentido saliente (Fig. 9a).
La operación de tronzado se puede considerar como un caso especial del ranurado, en el que la herramienta mecaniza hasta el centro de la pieza (figura 9b) o hasta la zona hueca interior, en el caso de existir ésta.
Si el extremo a tronzar tiene un chaflán o un redondeo, éste se realiza con la herramienta de tronzar mediante el procedimiento de la figura 9b.
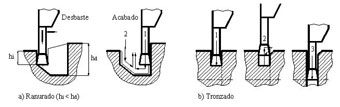
7. Secuenciación de las operaciones
Para cada amarre, PPSys establece el siguiente orden de operaciones:
- Operación de refrentado en desbaste y acabado y punto de centrado si se requiere.
- Taladrado al diámetro máximo posible, si la pieza precisa mecanizado interior.
- Desbaste de volúmenes exteriores e interiores.
- Acabado de las zonas exteriores y desbaste y acabado de ranuras exteriores.
- Acabado de las zonas interiores y desbaste y acabado de ranuras interiores.
- Mecanizado en desbaste y acabado de roscas exteriores e interiores.
- Realización de moleteados.
Es posible que durante la etapa posterior de optimización económica se realicen algunos ajustes relacionados, por ejemplo, con la minimización de los cambios de herramienta.
8. Conclusiones
9. Referencias
[2] S.V.B Reddy, M.S. Shunmugham, T.T. Narendran. Operation sequencing in CAPP using genetic algorithms. Int. J. Prod. Res., 37 (5) (1999) 1063-1074.
[3] J.C. Rico, G. Valiño, S. Mateos, E. Cuesta, C.M. Suárez. Automatic selection of clamping surfaces in the turning process for rotational parts. IMechE, 214B (2000) 693-708.
[4] S. Hinduja, H. Huang. OP-PLAN: an automated operation planning system for turned components. IMechE, 203B (1989) 145-158.
[5] P.K. Jain, N.K. Metha, P.C. Pabdey. Automatic cut planning in an operative process planning system. IMechE, 212B (1998) 129-140.
[6] Kaczmarek, J. Principles of machining by cutting, abrasión and erosion. Vol. I.. Ed. Peter Peregrinus Limited, 1976.
[7] Asensio París, I. Torneado y fresado por control numérico: Manual para operarios y programadores. Servicio de Publicaciones de la Universidad de Zaragoza, 1996.