Procesos de rebarbado no convencionales
El desbarbado de piezas ha sido generalmente relegado a sistemas cuasi-artesanales, en los cuales la labor manual ocupaba un lugar primordial. Como todos los que estamos involucrados con la producción de piezas destinadas a la industria automovilística, aeronáutica, médica o de la electrónica sabemos, garantizar calidad y productividad son requisitos indispensables para que los sistemas de producción globales funcionen correctamente. Los sistemas tradicionales de desbarbado, manuales, por vibración o por cepillado no aseguran ni calidad ni productividad, y como consecuencia vemos que están siendo substituidos por sistemas no-convencionales que se adaptan muy bien a las líneas de producción existentes en las plantas modernas que deben cumplir con las normas ISO, QS, etc.
Se hace necesario el considerar a la operación de rebarbado como una más en la cadena productiva y darle así la importancia que se merece, planeando el proceso de desbarbado a la hora de diseñar la pieza, y no como una solución a un problema inesperado.
Existen varios tipos de rebarbado no-convencionales dependiendo del material a ser tratado, del tipo de rebarba, de la geometría de la pieza o del nivel de producción. En este documento nos concentraremos en tres sistemas: rebarbado por flujo abrasivo, AFM; rebarbado térmico, TEM; y rebarbado electrolítico, ECM.
Estos tres procesos tienen características únicas que los diferencian del resto de los sistemas disponibles, siendo los más ampliamente usados debido a su confiabilidad, gran espectro de aplicaciones para los cuales son adecuados y la presencia de proveedores con amplia experiencia en estos productos. Extrude Hone Spain S.L. división de Extrude Hone Corp. ofrece los tres procesos tanto como proveedor de máquinas como en régimen de subcontratación.
Empecemos por explicar el proceso de rebabado por flujo abrasivo:
Rebarbado AFM
En este proceso hay tres elementos a tener en cuenta a la hora de determinar los parámetros del mismo. El tipo de polímero, que es el que controla la viscosidad de la pasta abrasiva, el tipo y tamaño del abrasivo, que nos permite controlar el grado de agresividad del trabajo de rebarbado y por último la presión de extrusión del elemento abrasivo, lo que permite controlar la velocidad de pasaje de la pasta a través de la pieza.
El tipo de polímero es importante ya que un polímero de alta viscosidad fluirá como un sólido, actuando en las paredes del pasaje, mientras que un polímero mas blando actuará mas como un líquido, siendo más efectivo en las aristas, como se puede apreciar en la figura 1.
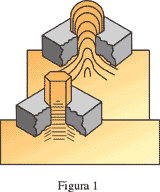
La correcta presión de extrusión de la pasta abrasiva controla la velocidad de pasaje de la pasta, y así el tiempo de proceso es disminuido o aumentado de acuerdo a las exigencias de productividad de la operación de rebarbado. Una presión demasiado baja resultará en tiempos de proceso excesivamente altos, pero permite el proceso de piezas de gran tamaño, mientras que una presión muy alta generará un aumento de la temperatura de la pasta que debe ser controlada con intercambiadores de calor.
Un equilibrio entre la viscosidad del polímero, el tamaño del abrasivo y la presión de extrusión hace posible la aplicación de este proceso a un sinnúmero de piezas ayudando a resolver problemas de rebarbado de distinta índole y características.
AFM, o mecanizado por flujo abrasivo, como denota la sigla en inglés, tiene las siguientes ventajas:
• Es capaz de rebarbar, pulir o redondear aristas de manera precisa en áreas de difícil acceso.
• Mejora la calidad de superficie
• Incrementa la vida de las piezas tratadas y reduce el desgaste de las mismas en el caso de matrices.
• Remueve las capas recocidas de electroerosión o de defectos de marcas de mecanizado.
• El proceso se puede controlar con gran precisión lográndose una gran repetividad.
• Es posible tratar varias piezas simultáneamente con los utillajes adecuados.
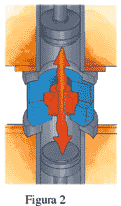
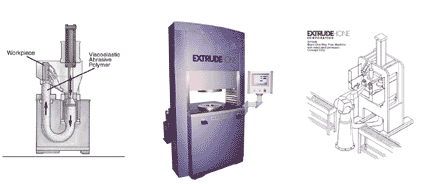
En cuanto a las limitaciones que este proceso presenta las más importantes son la incapacidad de procesar piezas con rebarbas externas, el a veces problemático paso de quitar la pasta abrasiva de las piezas una vez desbarbadas y la necesidad de utillajes generalmente complejos y caros.
Proceso de rebarbado térmico: TEM
La máquina de rebarbado térmico se compone de un sistema hidráulico que permite el cerrado de la cámara de ignición con fuerzas de hasta 400 toneladas, un sistema de alimentación de gases que recibe el oxígeno y el combustible de los depósitos presurizados, ajusta esta presión a la necesaria y los inyecta en la cámara, un sistema de refrigeración y un sistema de control por PLC con monitorización de todas las variables y componentes expuestos a la ignición. Esta última característica es muy importante debido al intrínsico peligro que el manejo de gases presurizados conlleva. La figura 4 nos muestra un esquema del equipo TEM.
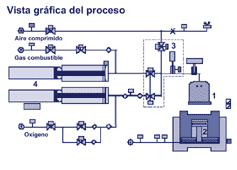
El proceso TEM presenta las siguientes ventajas:
• Remoción de rebarbas de cámaras cerradas
• Remoción de micro-rebarbas generadas por torneado, roscado o rectificado
• Remoción de rebarbas de inyección tipo ”flash”
• Aplicable a cantidades pequeñas o a grandes volúmenes
• Tiempo de preparación muy cortos
• El proceso no afecta el resto de la pieza
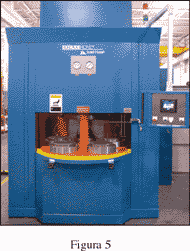
Las máquinas TEM se describen por el tamaño de las cámaras de ignición y la fuerza de cerrado del sistema hidráulico.
Con respecto a los costos del proceso la gran desventaja de este sistema es el alto costo de los equipos que en general son tres o cuatro veces más costosos que los de rebarbado por pasta abrasiva o electroquímicos. El costo operativo del proceso es probablemente el más económico de los tres, ya que el consumo de oxígeno y combustible por ciclo de máquina es muy bajo. El mantenimiento de las máquinas, especialmente de todos los componentes expuestos a la ignición es el factor de costo más significativo, ya que es indispensable un mantenimiento exhaustivo por razones de seguridad.
Los problemas más comunes que el sistema TEM presenta, se deben al carácter violento del proceso, ya que dentro de la cámara de ignición, las presiones a la hora de la misma son muy grandes. Por lo tanto en ocasiones ocurren golpes entre las piezas tratadas, por lo que es necesario colocar algún tipo de protección. Otro problema que surge es el cambio de color en las piezas una vez tratadas, que generalmente acaban siendo más oscuras que previo a la entrada en la máquina. Si estas piezas serán recubiertas con un baño, o tratadas térmicamente, ese cambio de color deja de ser un problema ya que estas operaciones finales dan solución al descoloramiento. De todas maneras, en el caso de piezas de acero o de metales ferrosos, es necesario un lavado posterior con un baño deoxidante, ya que la pieza sale de la cámara recubierta por una capa de óxido de hierro que hay que quitar.
Proceso de rebarbado electroquímico: ECM
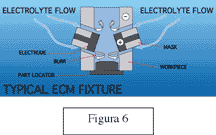
Las máquinas de rebarbado electroquímico se componen de un sistema de alimentación de electricidad, un generador de corriente continua generalmente de hasta 600 amps, un sistema de distribución de electrolito con su filtro, el utillaje compuesto por un cátodo y el ensamble de fijación de la pieza, y un sistema de control que monitoriza las variables del proceso a tiempo real. Estas variables son la conductividad del electrolito que está directamente relacionada con la concentración de sal en el agua, la temperatura que también afecta la conductividad, el Ph del electrolito, la presión del flujo de electrolito, el tiempo de proceso, y los dos parámetros de la corriente, el amperaje y el voltaje. Podemos apreciar el diagrama de una máquina ECM Extrude Hone con todos sus componentes en la figura 7.
El proceso presenta las siguientes características:
• Ciclos de proceso muy rápidos
• Piezas no afectadas por temperatura o procesos mecánicos.
• El tiempo o la efectividad del proceso es independiente de la dureza del material a ser rebarbado
• Mínimo desgaste de los utillajes y cátodos
• Posibilidad de tratar varias piezas o varias áreas de la pieza de forma simultánea
• Selectividad con respecto a donde aplicar el proceso
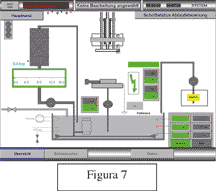
Cada pieza debe tener su utillaje dedicado, aunque es fácil adaptar las máquinas de una aplicación a otra.
Como se puede apreciar, los tres procesos tienen sus ventajas, desventajas, limitaciones y puntos fuertes.
A modo de guía rápida, los siguientes son algunos puntos a considerar a la hora de escoger un sistema de rebarbado que se adecue a una aplicación garantizando calidad a un bajo costo:
• Aplicaciones de muy alto volumen de producción: TEM (+ 30.000 piezas al día)
• Piezas donde es necesario un radio: AFM o ECM
• Aplicaciones donde es necesario una mejora en la superficie: AFM
• Aplicaciones con rebarbas internas y externas: TEM
• Aplicaciones con microrebarbas: TEM
• Piezas con rebarbas no accesibles: TEM o AFM
• Piezas de sinterizado: AFM o ECM
• Piezas con rebarbas excesivamente grandes: TEM
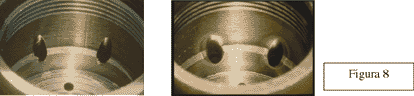
AFM, ECM y TEM constituyen un menú de soluciones que es capaz de resolver casi el 100% de los problemas presentados hoy en día en las plantas de producción. El conocimiento profundo de sus principios es esencial a la hora de plantear el uso de uno u otro de manera inteligente y efectiva.
Esperamos que esta guía a modo de introducción ayude a las empresas dedicadas al mecanizado, decoletaje, inyección de metales livianos o estampados a entender mejor las opciones disponibles a la hora de resolver sus problemas de rebarbado... ¿o se dice desbarbado?