Desde el diseño a la fabricación
(Moldflow)01/08/2003
Protodesign
Los esfuerzos iniciales en la optimización del diseño de pieza se han centrado, por ejemplo, en la ubicación y dimensionado de los sistemas de alimentación teniendo en cuenta ciertas restricciones impuestas por el propio diseñador. Posteriormente ha habido un interés muy grande en encontrar unas condiciones de proceso óptimas para poder inyectar una determinada combinación pieza-molde-máquina. Parte de este interés viene generado por la posibilidad de utilizar los resultados de la simulación directamente como información de partida en la máquina de inyección y ello puede considerarse en el marco de la optimización de las condiciones de proceso.
Mientras que la tecnología que impulsa y mueve la simulación ha ido avanzando muy rápidamente, ésta se encuentra principalmente enfocada al diseño tanto de pieza como del molde dentro del proceso del moldeo por inyección. Cierto es que las condiciones de proceso de los distintos materiales tienen una influencia crítica en la calidad del producto final y es por ello que se han realizado grandes esfuerzos en intentar controlar la propia máquina de inyección. Dichos esfuerzos principalmente han sido orientados a garantizar la repetitibilidad de cada uno de los ciclos de la máquina con aras de obtener así un proceso capaz.
Mientras que esto es verdaderamente importante, la calidad de la pieza depende en gran medida de las características instantáneas del flujo del material plástico en el interior de la cavidad del molde. Gran parte de los esfuerzos realizados en "controlar" la máquina se han orientado en hacer que la máquina "responda" a las variaciones de las condiciones del proceso, antes de que la misma tenga una capacidad real de "manipular" y de hacer las correcciones necesarias para mantener las condiciones óptimas de dicho flujo.
Además, los controladores de las máquinas de inyección no proporcionan hoy en día herramientas sistemáticas para la puesta a punto y optimización global de los diferentes parámetros que entran en juego en la inyección.
Los esfuerzos iniciales en la optimización del diseño de pieza se han centrado, por ejemplo, en la ubicación y dimensionado de los sistemas de alimentación teniendo en cuenta ciertas restricciones impuestas por el propio diseñador. Posteriormente ha habido un interés muy grande en encontrar unas condiciones de proceso óptimas para poder inyectar una determinada combinación pieza-molde-máquina. Parte de este interés viene generado por la posibilidad de utilizar los resultados de la simulación directamente como información de partida en la máquina de inyección y ello puede considerarse en el marco de la optimización de las condiciones de proceso.
Mientras que la tecnología que impulsa y mueve la simulación ha ido avanzando muy rápidamente, ésta se encuentra principalmente enfocada al diseño tanto de pieza como del molde dentro del proceso del moldeo por inyección. Cierto es que las condiciones de proceso de los distintos materiales tienen una influencia crítica en la calidad del producto final y es por ello que se han realizado grandes esfuerzos en intentar controlar la propia máquina de inyección. Dichos esfuerzos principalmente han sido orientados a garantizar la repetitibilidad de cada uno de los ciclos de la máquina con aras de obtener así un proceso capaz.
Mientras que esto es verdaderamente importante, la calidad de la pieza depende en gran medida de las características instantáneas del flujo del material plástico en el interior de la cavidad del molde. Gran parte de los esfuerzos realizados en "controlar" la máquina se han orientado en hacer que la máquina "responda" a las variaciones de las condiciones del proceso, antes de que la misma tenga una capacidad real de "manipular" y de hacer las correcciones necesarias para mantener las condiciones óptimas de dicho flujo.
Además, los controladores de las máquinas de inyección no proporcionan hoy en día herramientas sistemáticas para la puesta a punto y optimización global de los diferentes parámetros que entran en juego en la inyección.
Optimización global: de la teoría a la realidad
Ambos métodos son rentables y recomendables usados por separado, sin embargo se obtienen resultados óptimos cuando se utilizan de manera integrada. La dinámica básica de funcionamiento de ambas soluciones se describe a continuación.
Optimización teórica
Se parte de información como la geometría de la pieza a analizar, la caracterización del material utilizado, y las condiciones de contorno del proceso, que serían las condiciones de contorno habituales de cualquier análisis convencional; a ello se le añade una caracterización específica de la máquina en la que se va a inyectar la pieza, entre otros: el tiempo de respuesta, la máxima velocidad de inyección, el número de escalones que pueden programarse para perfilar tanto velocidades como presiones en el controlador de máquina.
También se especifican diversos criterios de calidad, los objetivos del análisis, es decir, qué es lo que se quiere optimizar: los tiempos de ciclo, los alabeos o los rechupes.
Con ello es el sistema el que de forma automática y realizando una serie de cálculos de manera iterativa nos proporciona resultados tan valiosos como pueden ser:
• La carga de material a inyectar.
• El perfil teórico óptimo de velocidades de inyección.
• El punto de conmutación.
• El perfil teórico óptimo de presión de compactación.
Dichos resultados pueden ser introducidos directamente en el controlador de la máquina de inyección, pues han sido obtenidos teniendo en cuenta específicamente sus características.
Es por ello que mediante este método se obtienen habitualmente reducciones de los tiempos de ciclo, mejora de las condiciones proceso y un aumento de la robustez del mismo.
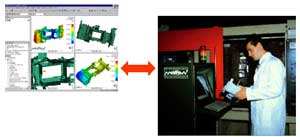
Optimización real
• Realizar la puesta a punto de una combinación molde-máquina de forma científica, sistemática y documentada.
• Encontrar la ventana de inyección más robusta mediante la realización de diseños de experimentos automatizados previos al comienzo de la producción real. Con ello se pueden determinar cuales van a ser los límites de la calidad de nuestras piezas y establecer mecanismos de seguridad para garantizar que vamos a respetar dichos límites durante la producción.
• Y ya en tiempo de producción realizar una monitorización y un control de la misma en tiempo real, en la que el sistema se encarga de corregir automáticamente los parámetros de inyección cuando las variables del proceso que delimitan la calidad de nuestra pieza se desvían de los límites calculados anteriormente.
Este tipo de herramientas aparece en un mercado dónde continuamente se está buscando la forma de reducir las ineficiencias ligadas a cada fase del proceso de producción. La presión por reducir los índices de rechazo de piezas con sus correspondientes devoluciones de cliente, reducir las paradas de máquina, aumentar el grado de conocimiento y la forma de compartir el mismo de forma documentada; en definitiva obtener la máxima productividad y eficiencia para cada máquina y cada molde, conlleva una tecnificación de la industria hacia sistemas expertos de monitorización y control de la producción.
De forma específica lo que aportan este tipo de soluciones es:
• Planificar mejor la utilización tanto de moldes, máquinas como recursos humanos.
• Reducir los tiempos de puesta a punto de cada combinación molde-máquina y reducir con ello la cantidad de rechazo derivado de la propia puesta a punto.
• Optimizar los tiempos de ciclo.
• Mejorar la calidad de las piezas inyectadas.
• Reducir los índices de rechazo de piezas.
• Controlar de forma robusta el proceso de inyección.
• Documentar y obtener una trazabilidad absoluta de nuestra producción.
• Tener información para poder tomar las decisiones más adecuadas.
La utilización de sistemas expertos de automatización del proceso y tecnología de control puede dividirse conceptualmente en 3 fases:
1. Puesta a punto.
2. Optimización.
3. Producción.
Durante la fase de puesta a punto de un molde en una máquina de inyección el usuario va a pasar por una serie de rutinas o procedimientos sistemáticos para la eliminación de defectos tales como piezas faltadas, rebabas, marcas de quemados, rechupes, etc. El objetivo va a ser obtener aquella primera inyectada correcta tanto des de un punto de vista cualitativo (defectos) como cuantitativo (tiempo de ciclo). Operativamente se va a inyectar una pieza y el usuario va a informar al sistema de la calidad de la misma mediante una serie de defectos tipificados en función de la fase o rutina que se esté siguiendo en aquel momento. Por ejemplo, al iniciar una puesta a punto, una de las primeras cosas que hay que determinar es la carga de material necesaria para poder llenar la pieza correctamente; en este caso, los únicos defectos que van a tenerse en cuenta a la hora de informar al sistema para la determinación de dicha carga son piezas faltadas o piezas con rebabas. El sistema experto procesa dicha información conjuntamente con la información adquirida directamente de la máquina en cada inyectada (señales específicas de proceso) y eventualmente, si es necesario, efectúa modificaciones de los parámetros de inyección para corregir el defecto encontrado.
Este es un proceso que se repite de manera iterativa hasta que la inyectada satisface las necesidades del usuario a cargo de la puesta a punto.
Llegado este punto la práctica habitual de la industria es empezar la producción continuada de piezas e ir realizando ajustes finos sucesivos durante minutos, horas, días o incluso semanas. A pesar de haber obtenido unas condiciones de proceso satisfactorias para la calidad de la pieza inyectada, todavía no se conocen la ventana de proceso admisible para dicha pieza y por tanto no se sabe si por cualquier variabilidad inherente al proceso de inyección, la calidad de las piezas se puede ver afectada. Dicha variabilidad es normal y nuestro objetivo va a ser determinar de forma científica mediante la técnica de los diseños de experimentos dicha ventana robusta de proceso.
Una ventana de proceso se define como la máxima variabilidad admisible del proceso; admisible porqué dentro de ella se tiene la seguridad de estar produciendo piezas buenas.
Históricamente, la percepción de las técnicas basadas en los diseños de experimentos ha sido de que estos pueden resultar complicados, largos y costosos en el tiempo y de difícil interpretación. Nada más lejos de la realidad si se automatiza y se sistematiza su utilización mediante sistemas expertos dónde es el propio sistema el que determina: a) la variabilidad del proceso y b) calcula aquellos limites de proceso dentro de los cuales las piezas van a tener la calidad deseada. No obstante, a pesar de la automatización de dicho proceso y de la facilidad de manejo del mismo con este tipo de herramientas, dicha metodología está lejos de ser sencilla. Cabe la posibilidad de realizar diferentes tipos de diseños de experimentos en función de los criterios de calidad de cada pieza y así poder jugar con diferentes variables de proceso para obtener la calidad deseada.
En este contexto, la propuesta de realizar uno o varios Diseños de Experimentos para determinar la ventana de proceso más robusta posible, garantiza que durante la etapa posterior de producción el proceso sea capaz y consecuentemente la calidad de las piezas inyectadas así como los índices de productividad aumenten considerablemente.
Ya en fase de producción, a pesar de tener una ventana de proceso lo más robusta posible, y de tener unos límites de proceso perfectamente caracterizados, es importante disponer de mecanismos de control y de auto-ajuste que permitan corregir cualquier tipo de desviación inherente el proceso de inyección. Los sistemas expertos están dotados de dichas herramientas y es por ello que se convierten en sistemas de control que mantienen las condiciones de proceso optimizadas durante la fase de optimización.
Con ello los ratios de rechazo disminuyen, los índices de productividad aumentan y tenemos una trazabilidad cien por cien de toda la producción realizada. Se ha optimizado así la totalidad del proceso de puesta punto de un molde en una máquina de inyección.
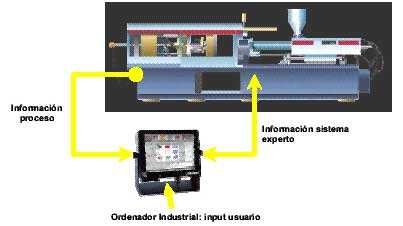
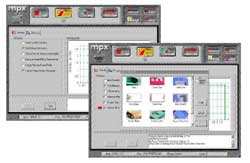
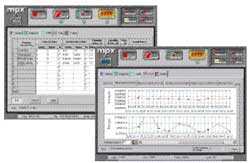
Conclusión: cerrar el lazo
Gracias a la integración de ambos sistemas (simulación-sistemas expertos) se puede empezar la fase de puesta a punto de un molde partiendo de unos resultados "teóricos óptimos" obtenidos de la simulación ya muy próximos a los que van a quedar en producción. Ello va a permitir evolucionar de una forma extremadamente rápida durante dicho proceso de puesta a punto y optimización del molde.
Esta ponencia se leyó en el Congreso Internacional de Diseño, Tecnologías e Ingeniería de Producto Protodesign, (Feria de Valencia, 6-9 mayo 2003)