Gemelo Digital e IA para reducir el rechazo y mejorar las propiedades mecánicas de componentes fabricados mediante microfusión
Dr. Javier Nieves; David García; Jorge Angulo-Pines; y Fernando Santos, de Azterlan Centro de Investigación Metalúrgica; y Dr. Pedro Pablo Rodriguez, de EIPC Research Center
27/03/2025Con el objetivo de reducir la producción de piezas defectuosas, con sus consiguientes costes económicos (en forma de materiales, consumo energético y otros costes de proceso) y medioambientales asociados, la empresa EIPC, fabricante de componentes fundidos, y el centro tecnológico Azterlan, especializado en metalurgia y procesos de fabricación metálica, han desarrollado un sistema inteligente de control, predicción y recomendación orientado a evitar dos de los defectos más críticos que se producen en este tipo de componentes de aluminio, como son la porosidad y la elongación de esas piezas (i.e., una de las propiedades mecánicas críticas en el funcionamiento de este tipo de piezas). A continuación, se presenta de forma resumida el trabajo de investigación llevado a cabo para este desarrollo.
1. Creación de un Gemelo Digital para observar y analizar el proceso de fabricación
El primer paso abordado por el equipo de investigación consistió en el desarrollo de un gemelo digital que representase virtualmente el proceso de fabricación de la planta a través de sus etapas principales: (i) recubrimientos primarios (aplicación de la primera capa de cera al molde de farbricación), (ii) recubrimientos secundarios (agregación de capas adicionales y arena para crear un cascará más dura en ese molde), (iii) fusión (preparación del metal y llenado de los moldes), e (iv) inspecciones finales (controles realizados una vez la pieza ha sido desmoldeada).
Se realizó una auditoría digital para evaluar la trazabilidad, la frecuencia y la precisión de los datos generados durante las distintas etapas del proceso (gráfico 1) y se digitalizaron y analizaron los datos de producción ya existentes (históricos) para valorar su potencial de procesamiento y visualización. También se desarrollaron e implementaron agentes de captura para controlar los parámetros de interés identificados y hasta entonces no monitorizados. Por tanto, a lo largo del proceso nos encontramos con un mix de fuentes de datos: sensores, equipos con sistemas de control y datos introducidos manualmente por inspectores humanos, así como datos históricos almacenados en distintos tipos de archivos y plataformas.
Para la recopilación y almacenamiento de datos de proceso se utilizó la herramienta PDManager (Production Data Manager), desarrollada por Azterlan, en la que se configuraron diferentes módulos para gestionar las distintas áreas del proceso. De esta forma, se configuró un Sistema de Sistemas (del inglés System of Systems - SoS) basado en una arquitectura de recopilación de datos donde cada sistema puede operar de forma independiente y solucionar problemas relacionados con la adquisición de datos en su dominio particular.
Esta arquitectura de datos centralizados y accesibles para su consulta conforma la base sobre la que se desarrolló el Gemelo Digital de la planta, esto es, una representación virtual del proceso orientada a monitorizar y analizar la operativa del mismo, con el fin de establecer correlaciones entre las variables controladas y las características finales de los productos.
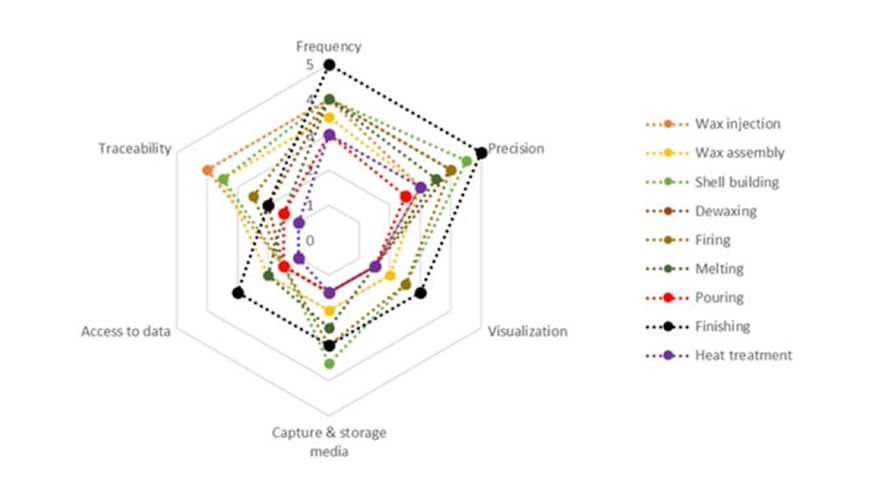
Esta arquitectura de datos también permite proveer información a distintos usuarios con diversos propósitos. Para facilitar la visualización de esos datos de interés y la llegada de la información adecuada a los perfiles adecuados en el momento oportuno se implementó el sistema de monitorización y control Sentinel, desarrollado también por Azterlan. En este caso, la plataforma Sentinel combina información y rangos de operación generando alertas y notificaciones cuando algún parámetro se encuentra fuera de rangos.
Para poder generar una herramienta capaz de representar la realidad del proceso de fabricación, en concreto la producción de moldes y piezas que fluyen en el flujo de trabajo de fundición a la cera perdida, es necesario poder representar el flujo de estos moldes en el proceso, así como los eventos que ocurren en el mismo. En este caso, los datos obtenidos de las áreas de recubrimiento primario, recubrimiento secundario, fusión e inspección se transforman en una secuencia de elementos en cola que se caracterizan secuencialmente en cada etapa y se representan digitalmente.
Atendiendo a criterios de priorización de datos (nivel de importancia para el buen desempeño del proceso y relevancia para cada fase), se diseñaron paneles de control atendiendo a las necesidades de información de los diferentes usuarios. Estos paneles se muestran mediante pantallas ubicadas en puntos clave de la planta de EIPC (como muestran las siguientes imágenes).
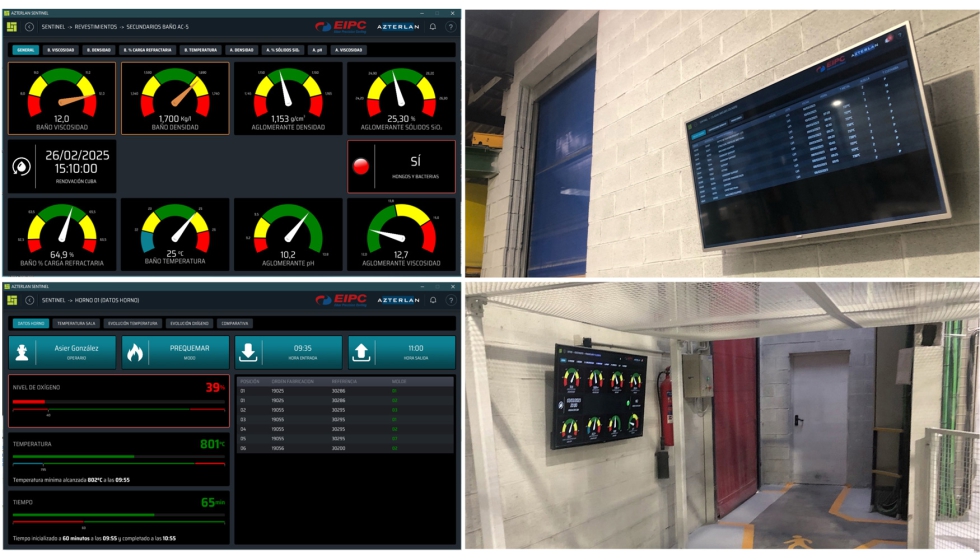
2. Creación de un sistema proactivo basado en predicciones
Todos los datos mencionados ofrecen la entrada bruta necesaria para crear un sistema de gestión de procesos inteligente capaz de anticiparse a posibles problemas. Para ello, el gemelo digital debe operar bajo tres claros axiomas: (i) la proactividad, esto es, debe ser capaz de determinar el posible estado del proceso productivo en un futuro próximo; (ii) ajuste, es decir, ninguna de las pruebas o simulaciones que se desarrollen romperá las reglas que rigen la representación física del proceso; y (iii) Business Intelligence, el gemelo servirá como una herramienta de gestión del conocimiento o, lo que es lo mismo, un repositorio que engloba todo lo necesario para gestionar todas las tareas asociadas al proceso real.
Para ello, el sistema debe realizar un diagnóstico orientado a la toma de decisiones que agreguen valor al proceso. Posteriormente, estas decisiones serán remitidas en modo de propuestas de acción sea a personas (M2H–Machine to Human communication) o a máquinas (M2M-Machine to Machine communication).
Para desarrollar este sistema de predicciones el equipo de desarrollo utilizó el método de aprendizaje supervisado, un sistema de aprendizaje automático en el que los modelos se entrenan utilizando datos etiquetados que incluyen la salida correcta correspondiente. Este aprendizaje se realiza mediante clasificadores estadísticos para categorizar los datos en función de los patrones de los ejemplos etiquetados. Así, estos clasificadores aprenden de los datos etiquetados para hacer predicciones sobre datos nuevos y no vistos. El proceso se basa en métodos estadísticos para modelar la relación entre las entidades de entrada y las etiquetas de destino.
Para realizar las predicciones futuras y evaluar adecuadamente los modelos de aprendizaje automático para la predicción de los dos objetivos mencionados (porosidad y elongación de las piezas), se aplicó una metodología de validación cruzada en el aprendizaje de modelos utilizando clasificadores estadísticos clásicos (como, por ejemplo, redes bayesianas, kNN, redes neuronales artificiales, máquinas de vectores de soporte, árboles de decisión y voted perceptron).
3. Retro-feedback para el control y ajuste de los parámetros de fabricación
Los mencionados desarrollos permitieron crear un método ex ante para prever los defectos relacionados con porosidad y elasticidad, así como características específicas del proceso de fabricación. Con esta base, la etapa final se centró en la creación de un recomendador de acciones destinado a mantener el sistema dentro de los límites deseados. Este escenario se define como “producción estándar o normal”. Así, cuando los predictores mencionados detectan una anomalía, el sistema de asesoramiento comienza a trabajar para encontrar la forma de redirigir el proceso y prevenir que el problema previsto ocurra. El conocimiento necesario para construir este sistema de recomendación se basa en el equipo de ingeniería de EIPC y en los patrones identificados como reglas asociativas.
El módulo responsable de la evaluación y generación de recomendaciones conoce (i) el estado actual del proceso (información obtenida de la observación del gemelo digital), (ii) el estado previsto que alcanzará la producción (predicciones o simulaciones generadas por el gemelo digital) y, por último, (iii) los puntos de ajuste y límites dentro de los cuales debe operar el proceso (proporcionados por el equipo de ingeniería de la planta). Una vez unificados estos datos, el proceso tiene capacidad para redirigirse automáticamente y así evitar el problema o desviación detectados.
A veces, el sistema de recomendación se centrará en aumentar o disminuir el rango de trabajo de una o más variables. En otras ocasiones, determinará que es mejor comenzar a producir dentro de nuevos rangos, ajustando los límites de esa variable a una nueva zona óptima de producción. Este sistema tiene como objetivo modificar rangos de control que se han quedado obsoletos o descubrir nuevas tendencias de fabricación que optimicen el proceso, reduzcan el rechazo y, en consecuencia, aumenten la productividad.
Esta investigación forma parte del proyecto INEVITABLE, financiado por el prorgama Horizon 2020 de la Unión European bajo el acuerdo de licencia 869815.
Este artículo presenta de forma resumida el contenido de la publicación científica ‘An Artificial Intelligence-Based Digital Twin Approach for Rejection Rate and Mechanical Property Improvement in an Investment Casting Plant’ publicado por la revista Applied Sciences 2025 (DOI: 10.3390/app15042013).