Un enfoque global para el acabo de bordes en componentes críticos
El control y la eliminación de rebabas constituyen aspectos de gran relevancia económica en diversas operaciones de mecanizado, lo que ha convertido a estos procesos en un foco central de investigación en el ámbito del corte en los últimos años [1]. En la industria aeronáutica, donde se trabaja con componentes de alto valor añadido, incluso errores mínimos pueden acarrear consecuencias significativas, debido a la considerable inversión de tiempo y recursos en los procesos previos.
En el dibujo técnico, la forma geométrica ideal se representa sin desviaciones y, generalmente, sin contemplar las condiciones de los bordes. Aunque en ocasiones se especifica la inclusión de un chaflán como característica de la pieza, se presupone que este posee una geometría ideal, algo que resulta difícil de alcanzar o que implica un elevado coste. Sin embargo, para garantizar el funcionamiento óptimo de una pieza o por motivos de seguridad, es imprescindible definir condiciones específicas, tales como bordes libres de rebabas o aristas suavizadas que eviten superficies cortantes [2].
Las operaciones de acabado en este contexto se distinguen principalmente en dos procesos: el rebabado y el achaflanado. El rebabado consiste en la eliminación selectiva y completa de las rebabas, preservando la forma nominal de la arista. Esta técnica se utiliza frecuentemente como paso previo al redondeo o achaflanado, siendo especialmente útil en piezas con rebabas de gran tamaño y distribución irregular, ya que reduce la variabilidad inherente al corte inicial. Por otro lado, el achaflanado implica cortar el borde de la pieza en un ángulo determinado, generando una superficie inclinada entre dos caras. Aunque este proceso puede sustituirse en algunos casos por un redondeo a un radio específico, en ambos escenarios resulta fundamental para eliminar bordes afilados, facilitando el ensamblaje de componentes y aumentando la capacidad de la pieza para soportar cargas.
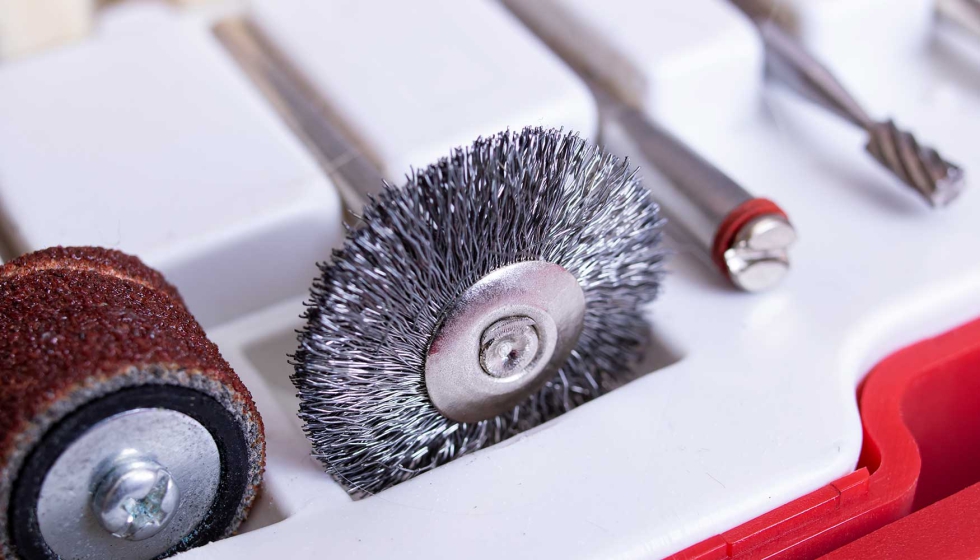
Entre las herramientas más empleadas en el proceso de rebabado se encuentran los cepillos, los abrasivos flexibles y las fresas diseñadas específicamente para este fin. Estas herramientas destacan por su versatilidad y eficiencia, ya que pueden utilizarse tanto de forma manual, a través de amoladoras portátiles con accionamiento eléctrico o neumático, como de forma automática, en el husillo de máquinas CNC o robots. Además, su diseño permite que actúen como consumibles, operando de forma localizada en las áreas afectadas por rebabas. La elección de la herramienta más adecuada depende de varios factores, incluyendo la capacidad de arranque de material requerida, el acceso a las diferentes partes de la pieza y el grado de desgaste de la herramienta. En esta línea, son varios los trabajos llevados a cabo por el CFAA y el Grupo de Fabricación Avanzada del Dpto. de Ingeniería Mecánica de la UPV-EHU, en colaboración con diferentes empresas del sector.
Los cepillos se emplean principalmente para suavizar y limpiar superficies sin dañar el material base, siendo especialmente eficaces en la eliminación de rebabas ligeras y en la preparación de bordes. Su geometría de corte flexible les permite adaptarse a superficies irregulares y complejas, garantizando un acabado uniforme y reduciendo la agresividad respecto a otras herramientas abrasivas. Cada arquitectura de cepillo está diseñada para satisfacer necesidades específicas del proceso de acabado, y la elección de la configuración adecuada depende de la geometría de la pieza, el tipo de material y la naturaleza de las rebabas a eliminar. En este sentido, destacan los cepillos con filamentos metálicos de JAZ Zubiaurre, cuya robustez permite el arranque de grandes rebabas sin comprometer la integridad de la pieza. Asimismo, los cepillos frontales con filamentos cerámicos de Xebec han demostrado una elevada capacidad de corte en materiales de gran dureza, como las aleaciones base-níquel, combinando un rebabado eficiente con un buen control del acabado superficial. Los abrasivos flexibles son una tecnología similar a los cepillos, que combinan la eliminación de material con un excelente acabado superficial. En este caso, fabricantes como 3M y VSM cuentan con un amplio catálogo de abrasivos, destacando sus granos abrasivos estructurados Cubitron III y Xelerion en el procesamiento de metales no férricos.
Sin embargo, cuando es necesario actuar de forma localizada sobre el contorno de piezas con rebabas de gran dureza, las fresas enterizas de metal duro siguen siendo indispensables. Fabricantes como Pferd y Lukas ofrecen una amplia variedad de geometrías y dentados, lo que permite adaptar la herramienta a las características específicas del material y del tipo de rebaba a eliminar. A diferencia de las herramientas flexibles, cuyas trayectorias son más sencillas al poder adaptar su forma a las características de la pieza, las fresas de rebabado requieren ajustes meticulosos y frecuentes para garantizar una eliminación efectiva del material, requiriendo un mayor grado de precisión en el posicionamiento y movimiento de las fresas.
En este tipo de operaciones con herramientas enterizas, la posición y orientación de la herramienta de corte determinan el arranque de material. Por ello, las trayectorias se programan mediante modelos digitales del robot y la pieza, permitiendo calcular con precisión estas posiciones. En el CFAA, gracias a la colaboración con Mecdata, disponemos de múltiples licencias del software ENCY para definir y simular trayectorias con robots. Además, la célula de superacabado, configurada por MEK&BOT en el entorno físico del taller, cuenta con su modelo digital correspondiente, lo que permite controlar los movimientos articulares del Kuka KR 240 R2500 y evitar configuraciones potencialmente problemáticas.
Las particularidades del acabado de bordes generan dificultades adicionales que, en la actualidad, impiden automatizar de forma efectiva estos procesos mediante robots. En concreto, la discrepancia entre los modelos digitales teóricos y la forma real de las piezas provoca errores de posicionamiento en las trayectorias de corte, los cuales se reflejan directamente en el resultado al trabajar con herramientas rígidas. Las estrategias para corregir estas desviaciones se basan en dos enfoques.
Por un lado, los sistemas de compensación de la herramienta utilizan la trayectoria original diseñada por ordenador y ajustan su posición en función de la fuerza de contacto. Estos se dividen en sistemas activos, que retroalimentan al robot con nuevas posiciones [3], y pasivos, que ofrecen una respuesta más rápida al no interactuar directamente con el robot [4]. Un ejemplo extendido de los sistemas pasivos son los portaherramientas flotantes con muelles intercambiables [5], combinados con herramientas cónicas, que corrigen las desviaciones durante el achaflanado gracias a la elasticidad del muelle. Sin embargo, el bajo nivel de automatización en estos procesos ha limitado los estudios, que no abordan el control de las fuerzas de corte ni del tamaño del chaflán, ni diferencian si la variación en la fuerza se debe a deformaciones o a la presencia de rebabas. Por ello, es imprescindible desarrollar métodos adicionales de inspección previa para reconocer las acumulaciones de material y permitir su eliminación selectiva durante el rebabado. Aprovechando las superficies planas resultantes del mecanizado, esta inspección puede realizarse con una única cámara orientada frontalmente [6], lo que simplifica significativamente el diseño del sistema y facilita su integración en una amplia variedad de máquinas. Aunque el procesamiento de imágenes y la detección de objetos han avanzado significativamente en el ámbito industrial [7], aún no existen soluciones específicas para el reconocimiento de rebabas y la corrección de trayectorias de rebabado en el ámbito industrial. Esto se debe a la complejidad inherente a identificar y clasificar dichas imperfecciones, así como a la necesidad de adaptar los algoritmos de visión a diversas geometrías.
La importancia de identificar la arista
Dentro de las líneas de investigación desarrolladas en el CFAA, se han diseñado y fabricado piezas de prueba que reproducen las geometrías extruidas comunes en las carcasas de turbina obtenidas por fundición. Estas piezas presentan una desviación de ±2 mm en su contorno, simulando los efectos de los tratamientos térmicos típicos en este tipo de componentes. Con Inconel 718 como material base y mediante el planeado con herramientas cerámicas, se generan múltiples rebabas de alta resistencia y dureza a lo largo del borde exterior.
El enfoque de este estudio se fundamenta en movimientos previamente simulados por ordenador, lo que permite determinar la configuración óptima del robot en términos de rigidez. Así se establecen tanto la configuración del sexto eje como los ángulos de orientación de la herramienta, corrigiendo las coordenadas de posición conforme al contorno detectado en cada pieza. Para ello, se ha desarrollado un algoritmo de procesamiento de imágenes en Python que se apoya en las librerías de OpenCV, la biblioteca de código abierto líder en aplicaciones de visión industrial.
La captura de la imagen se realiza en una disposición frontal y a una distancia adecuada para minimizar las distorsiones de perspectiva. Previo a la adquisición, se efectúa un procedimiento de calibración mediante la toma de múltiples fotografías de un patrón de dimensiones conocidas desde distintos ángulos, lo que permite determinar los parámetros intrínsecos de la lente. Una vez capturada, la imagen se binariza en función de la intensidad de los píxeles, utilizando un algoritmo que ajusta localmente el umbral de discretización para facilitar la detección de contornos, incluso en condiciones de iluminación variable. Además, el contraste entre la superficie mecanizada y brillante de la pieza y las caras mate del cuerpo fundido favorece la identificación del contorno exterior.
Para seleccionar automáticamente el contorno exterior de la pieza entre todas las geometrías identificadas en la imagen, se comparan los momentos de Hu [8] de cada contorno con los de una plantilla de referencia que representa el diseño nominal de la pieza. De este modo, se identifica el contorno que mayor similitud presenta con la forma teórica, independientemente de las deformaciones y rebabas presentes. Una vez identificado el contorno exterior, es fundamental correlacionar los píxeles de la imagen con posiciones en el espacio tridimensional de la célula robotizada. En este sentido, se emplea una sonda de palpado acoplada al robot, que posiciona el plano de la superficie mecanizada y mide una característica relevante de la pieza: el agujero interior previamente taladrado. Este agujero, que define el origen del sistema de referencia para las trayectorias, se utiliza para relacionar sus dimensiones con los píxeles de la imagen, obteniéndose un factor de escala de 39 µm/px (para una lente de 24 MP).
Posteriormente, las coordenadas X e Y de las nuevas trayectorias de acabado se derivan de las posiciones de los puntos del contorno, una vez aplicada la transformación correspondiente. Es importante destacar que la trayectoria resultante no replica de forma exacta el contorno detectado, ya que se filtra la geometría de las rebabas para evitar movimientos indeseados de la herramienta y se ajusta la distancia de separación en función del radio de corte requerido. Finalmente, se simplifica el conjunto de puntos que conforman la trayectoria, conservándose únicamente aquellos que contribuyen de manera significativa a definir la forma de la pieza. Este proceso optimiza el procesamiento por parte del controlador del robot, permitiendo una ejecución más eficiente y precisa de las trayectorias de acabado.
![Figura 1. Detección de contornos y diseño de trayectorias de contorneado [9] Figura 1. Detección de contornos y diseño de trayectorias de contorneado [9]](https://img.interempresas.net/fotos/5034347.jpeg)
Para las trayectorias de achaflanado, al utilizar herramientas cónicas con el filo a 45 grados, el valor de la coordenada en el eje Z determina el tamaño del corte producido en la pieza. En este sentido, el tamaño del chaflán se corresponde con la diferencia entre la profundidad de corte y la separación lateral aplicada en el diseño de la trayectoria.
La visión artificial aplicada al acabado de bordes va más allá de la simple corrección de deformaciones en las piezas. Durante el procesamiento de imágenes, las rebabas filtradas se aprovechan estratégicamente para medir su altura, es decir, la proyección hacia el exterior de la pieza, y de ese modo generar una trayectoria adicional de rebabado. Este innovador enfoque sirve como preparación previa de la arista antes de iniciar la operación de achaflanado, optimizando la calidad y eficiencia del proceso.
![Figura 2. Medición de la altura de las rebabas y programación adaptativa de las trayectorias para su eliminación selectiva [9]... Figura 2. Medición de la altura de las rebabas y programación adaptativa de las trayectorias para su eliminación selectiva [9]...](https://img.interempresas.net/fotos/5034348.jpeg)
Gracias a estos avances, ahora es posible generar una trayectoria optimizada que se adapta tanto a las deformaciones como a las rebabas de la pieza. Este enfoque inteligente permite eliminar solo aquellas rebabas que superen un umbral determinado, ajustando con precisión la profundidad de pasada en cada posición. El resultado: un proceso más eficiente y controlado, que garantiza un acabado de alta calidad sin comprometer la integridad de la pieza.
Un modelo para controlar el proceso de corte
Con la variabilidad asociada a la pieza resuelta por medio del procesamiento de imágenes, el siguiente desafío es corregir las imprecisiones en el movimiento del robot al ejecutar las trayectorias. Para ello, los portaherramientas flotantes con muelles intercambiables se han convertido en una solución ampliamente utilizada, especialmente en combinación con herramientas cónicas, garantizando un contacto uniforme en operaciones de achaflanado. Sin embargo, la compensación pasiva de la herramienta depende directamente de la fuerza de corte, la cual varía según las condiciones del proceso. Esto, en muchos casos, requiere múltiples ensayos experimentales hasta lograr un control preciso del tamaño final del achaflanado.
Para abordar esta problemática, las investigaciones se han centrado en analizar la geometría del corte en este tipo de operaciones, desarrollando un modelo mecanístico capaz de estimar las fuerzas de corte en condiciones rígidas. Este modelo se basa en coeficientes obtenidos experimentalmente y, a diferencia de otros enfoques más simples, solo requiere cuatro ensayos para su calibración. En estos ensayos, se registran las fuerzas de corte en dos tamaños de chaflán y dos velocidades de avance, utilizando un centro de mecanizado Hermle C52 UMT y chapas previamente mecanizadas. Esto permite un control preciso de la posición de la herramienta y garantiza estabilidad en la adquisición de datos.
![Figura 3. Set-up experimental y simulación de las fuerzas de corte bajo condiciones rígidas [10] Figura 3. Set-up experimental y simulación de las fuerzas de corte bajo condiciones rígidas [10]](https://img.interempresas.net/fotos/5034349.jpeg)
Como resultado, los coeficientes obtenidos permiten simular con precisión las fuerzas generadas por cada filo de corte a lo largo de una revolución completa de la herramienta. La fuerza total simulada se compara con la fuerza media estabilizada medida en la mesa dinamométrica, con desviaciones inferiores al 15% en la mayoría de los casos. Estos resultados no solo validan la fiabilidad del modelo en condiciones rígidas, sino que también sirven como base para la simulación de condiciones propias de los portaherramientas flotantes.
A partir de esta base, el modelo se adapta a condiciones en las que se libera un grado de libertad en la dirección axial mediante la inclusión de un muelle. En este caso, la posición de la herramienta queda determinada por la compresión ejercida en el muelle, la cual depende de la fuerza de corte en esa dirección. Con este enfoque, la fuerza axial caracterizada en el modelo rígido se vincula con el comportamiento elástico del sistema, permitiendo que el tamaño del chaflán resultante dependa únicamente de las condiciones del proceso y de nuevos coeficientes a determinar. Dado que estos coeficientes varían con el avance, el nuevo modelo se constituye en base a cuatro ensayos experimentales, bajo diferentes condiciones de avance, en los que se mide el tamaño del chaflán con un perfilómetro por contacto.
![Figura 4. Modelos mecanísticos aplicados a la operación de achaflanado [10] Figura 4. Modelos mecanísticos aplicados a la operación de achaflanado [10]](https://img.interempresas.net/fotos/5034350.jpeg)
El modelo de achaflanado con compensación axial representa un avance significativo en el control del proceso, al permitir la simulación precisa del tamaño del chaflán en función de las propiedades elásticas del muelle y las condiciones del proceso, en particular la velocidad de avance. Esto no sólo permite identificar el muelle más indicado según el tipo de operación, sino que también permite determinar las condiciones óptimas del proceso.
De esta manera, la operación de achaflanado integra diferentes estrategias de control. Por un lado, la compresión inicial del muelle se ajusta mediante trayectorias adaptadas obtenidas por procesamiento de imágenes, lo que permite una configuración precisa antes del corte. Por otro, el modelo mecanístico desarrollado calcula la velocidad de avance óptima para garantizar un mecanizado estable y preciso. Además, las imprecisiones inherentes al movimiento del robot se compensan de forma pasiva gracias al desplazamiento flotante de la herramienta, asegurando que el tamaño del chaflán se mantenga constante pese a posibles desviaciones en la ejecución de la trayectoria.
Este enfoque, que combina compensación mecánica y optimización de parámetros de corte, mejora la precisión y repetibilidad en los procesos automatizados de achaflanado, minimizando la necesidad de ajustes manuales y ensayos experimentales.
Conoce tu robot
Si bien los desarrollos anteriores son aplicables a cualquier arquitectura de máquina, en operaciones de precisión con robots, donde se requiere un control continuo de la velocidad de avance, como en el caso del achaflanado con compensación axial, la programación de trayectorias adquiere un papel crítico.
Para evitar detenerse en cada punto de control, los robots industriales emplean una estrategia de anticipación, iniciando la transición al siguiente punto una vez alcanzada una posición suficientemente cercana al actual. Además, las trayectorias se descomponen en pequeños segmentos lineales, donde el controlador interpola los movimientos articulares para aproximarse a la velocidad de avance requerida en la herramienta. Sin embargo, la cantidad y distribución de estos puntos afectan directamente el comportamiento del robot: un mayor número de puntos con menor espaciado restringe el margen de transición, obligando al robot a reducir su velocidad para cumplir con la trayectoria. Por el contrario, un mayor espaciado permite mantener velocidades más altas, pero introduce errores cordales, desviando el recorrido de la geometría real de la pieza.
En la adaptación de trayectorias generadas mediante procesamiento de imágenes, no basta con optimizar el espaciado exclusivamente en función de la forma de la pieza; también es necesario considerar la capacidad del robot para seguir la trayectoria con precisión y a la velocidad requerida. No obstante, los softwares de simulación actuales presentan limitaciones en este aspecto, ya que no permiten calcular con precisión la evolución del avance real del robot ni cuentan con la resolución suficiente para evaluar el impacto del espaciado en la calidad del corte.
Para abordar esta limitación, se ha desarrollado una metodología innovadora que permite evaluar el comportamiento del robot sin necesidad de equipamiento adicional. Aprovechando la monitorización continua de la compensación de la herramienta, en este caso, en dirección radial, es posible registrar tanto el tiempo efectivo de contacto de la herramienta con la pieza como el tiempo total del recorrido. A partir de estos datos, se han definido indicadores específicos para analizar la velocidad real de avance y la precisión en el posicionamiento, proporcionando una herramienta cualitativa para comprender cómo afecta el espaciado entre puntos en trayectorias con diferentes velocidades objetivo.
![Figura 5. Análisis cuantitativo del seguimiento de las trayectorias mediante los indicadores de velocidad y posicionamiento [11]... Figura 5. Análisis cuantitativo del seguimiento de las trayectorias mediante los indicadores de velocidad y posicionamiento [11]...](https://img.interempresas.net/fotos/5034351.jpeg)
Gracias a este enfoque, es posible conocer cómo se comporta el robot en el seguimiento de trayectorias de contorneado utilizando únicamente los cabezales de trabajo empleados en las operaciones de acabado, sin necesidad de sensores externos ni equipos adicionales de medición.
Dado que la calidad del achaflanado depende tanto de la precisión en el posicionamiento como de la velocidad de avance, se introduce un indicador global que evalúa el seguimiento de la trayectoria a partir del producto de ambos factores. Para visualizar su impacto de manera clara, el análisis experimental se amplía considerando distintos diseños de trayectoria y velocidades de avance, lo que permite generar un mapa de colores en el que se visualizan, de forma intuitiva, las combinaciones que garantizan un resultado óptimo.
![Figura 6. Identificación de las condiciones óptimas [11] Figura 6. Identificación de las condiciones óptimas [11]](https://img.interempresas.net/fotos/5034354.jpeg)
Este enfoque no solo permite adaptar las trayectorias de achaflanado a la morfología de las piezas mediante el procesamiento de imágenes, sino que también optimiza su ejecución considerando las limitaciones del seguimiento de trayectorias del robot. Al integrar ambos aspectos, se superan los principales obstáculos que hoy en día dificultan la automatización de estos procesos de acabado, garantizando un control más preciso sobre la calidad del resultado y reduciendo la necesidad de ajustes manuales o ensayos experimentales.
Conclusiones
Las diferencias entre los modelos digitales del robot y la geometría real de la pieza representan un obstáculo clave para la automatización del rebabado en aplicaciones de precisión. Para que las trayectorias generadas por ordenador sean realmente efectivas, deben adaptarse tanto a las características del robot como a las particularidades de cada pieza.
Con este objetivo, los desarrollos llevados a cabo en el CFAA abordan estos desafíos de manera integral. En primer lugar, la morfología de las piezas se inspecciona mediante una imagen frontal, cuyo procesamiento permite ajustar las trayectorias originales al contorno real, corrigiendo deformaciones y generando una trayectoria previa específica para la eliminación selectiva de las rebabas detectadas. Una vez asegurado el posicionamiento inicial de la herramienta, los errores asociados al seguimiento de trayectorias del robot se compensan mediante el uso de portaherramientas flotantes, garantizando un contacto uniforme con la pieza durante todo el proceso. Para un mayor control sobre la dimensión final del chaflán en estos sistemas pasivos, el modelo mecanístico desarrollado permite predecir las fuerzas de corte con un número reducido de ensayos experimentales, optimizando así las condiciones de operación para obtener un chaflán con las dimensiones requeridas. Además, la monitorización de la compensación de la herramienta ha permitido analizar el rendimiento del robot en función de la discretización de la trayectoria, lo que ha facilitado la optimización de su programación. Como resultado, el robot puede alcanzar la velocidad de avance óptima sin desviarse en exceso de los puntos corregidos mediante el procesamiento de imágenes.
En conjunto, estos avances mejoran significativamente la calidad y precisión de las operaciones de acabado con robots programados a partir de modelos digitales ideales, representando un paso clave hacia la automatización completa del proceso. La reducción de la intervención humana no solo incrementa el control sobre la operación, sino que también mejora la productividad y asegura la consistencia en el acabado de las piezas, abriendo nuevas posibilidades para la automatización de procesos de precisión en la industria.
El conocimiento en abrasivos como clave del éxito en pulido
Lograr un proceso de pulido eficiente y de alta calidad no depende solo de la maquinaria utilizada o de la precisión del propio proceso, sino también del conocimiento sobre los abrasivos. Con el paso de los años, los avances en la composición y fabricación de abrasivos han permitido mejorar su rendimiento y durabilidad, optimizando cada fase del trabajo.
En la actualidad, la tecnología abrasiva ha evolucionado hasta el punto en que factores como la distribución del grano, la estructura del ligante o el control de la temperatura en la fricción resultan determinantes. Gracias a la innovación constante de empresas líderes en el sector, como VSM Abrasivos, se han desarrollado soluciones que ofrecen acabados más homogéneos, con menor desgaste y mayor estabilidad térmica durante el proceso. Los abrasivos han evolucionado de simples superficies rugosas a herramientas de precisión que, cuando se comprenden y emplean adecuadamente, permiten obtener resultados repetibles y controlados.
Uno de los aspectos clave en el uso eficiente de estas herramientas radica en la selección del abrasivo para cada operación. Comprender la interacción del abrasivo con diferentes geometrías, materiales y condiciones de trabajo permite optimizar el proceso y aumentar la posibilidad de alcanzar un resultado óptimo. Los materiales actuales están diseñados para ofrecer una abrasión más eficiente sin comprometer la integridad del componente, un factor esencial en el tratamiento de piezas críticas, como las utilizadas en aeronáutica. Desde métodos de colocación electrostática de granos y estructuras diseñadas para mantener el filo de los abrasivas, hasta recubrimientos que reducen la acumulación de calor, cada detalle influye directamente en la calidad final del acabado.
En este sentido, la microestructura cristalina del grano cerámico de forma triangular Actirox constituye un avance destacado en aplicaciones de alto arranque de material sobre materiales termorresistentes. Su innovadora tecnología de autoafilado asegura una agresividad constante y sostenida a lo largo de toda la vida útil del grano. Gracias a su forma geométrica, optimiza el arranque de material de manera eficiente, mientras que su desgaste definido garantiza la generación continua de nuevas aristas de corte afiladas. Este proceso asegura un rendimiento estable y de alta eficacia, incluso en condiciones exigentes.
La colaboración con empresas que apuestan por la mejora continua en el desarrollo de abrasivos permite mantenerse a la vanguardia en el pulido de precisión. Aprovechar al máximo estas innovaciones no solo mejora la productividad, sino que también conduce a procesos más sostenibles y rentables.
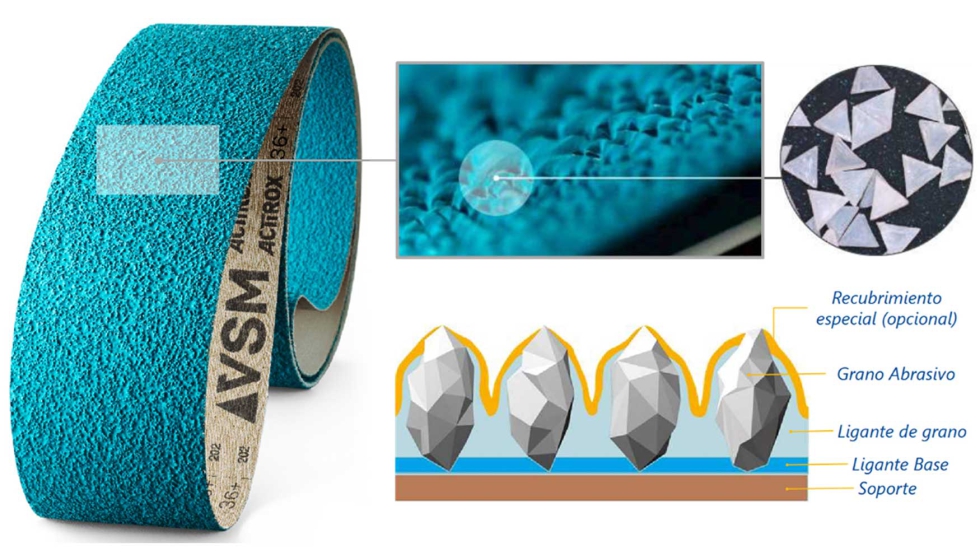
Agradecimientos
Parte de estos desarrollos se han realizado Proyecto de investigación PLEC2024-011247 de acrónimo SARA financiado por MICIU/AEI /10.13039/501100011033 y por FEDER, UE. También se agradece al proyecto de acrónimo CRESCENDO referencia CPP2021-008932 financiado por MCIN/AEI/10.13039/501100011033 y por la Unión Europea ‘NextGenerationEU’/PRTR. Por último, agradecer al grupo del Gobierno Vasco IT 1573-22, al proyecto Elkartek MHARSH y al Aula AIMS (Artificial Intelligent Manufacturing for Sustainability Unit) de la UPV/EHU.
Referencias
[1] Falandys, K.; Kurc, K.; Burghardt, A.; Szybicki, D. Automation of the edge deburring process and analysis of the impact of selected parameters on forces and moments induced during the process. Applied Sciences, 13(17), 9646, 2023.
[2] Franke, V. Burr. Capítulo disponible en: CIRP Encyclopedia of Production Engineering, ISBN: 978-3-642-35950-7, 2018.
[3] Lloyd, S.; Irani, R. A.; Ahmadi, M. Precision robotic deburring with Simultaneous Registration and Machining for improved accuracy, quality, and efficiency. Robotics and Computer-Integrated Manufacturing, 88, 102733, 2024.
[4] Burghardt, A.; Szybicki, D.; Kurc, K.; Muszyñska, M.; Mucha, J. Experimental study of Inconel 718 surface treatment by edge robotic deburring with force control. Strength of Materials, 49, 594–604, 2017.
[5] Sugino Corporation. What is Float Deburring for Automation? Disponible en: https://www.suginocorp.com/automated-deburring-solution/ [Último acceso: marzo 2025].
[6] MacMillan, W. R.; Irani, R. A.; Ahmadi, M. Planar image-space trajectory planning algorithm for contour following in robotic machining. CIRP Journal of Manufacturing Science and Technology, 42, 1–11, 2023.
[7] Hu, Q.; Xu, X.; Leng, D.; Shu, L.; Jiang, X.; Virk, M.; Yin, P. A method for measuring ice thickness of wind turbine blades based on edge detection. Cold Regions Science and Technology, 192, 103398, 2021.
[8] Hu, M. K. Visual pattern recognition by moment invariants. IRE Transactions on Information Theory, 8, 179–187, 1962.
[9] González, M.; Rodríguez, A.; López-Saratxaga, U.; Pereira, O.; López de Lacalle, L. N. Adaptive edge finishing process on distorted features through robot-assisted computer vision. Journal of Manufacturing Systems, 74, 41–54, 2024.
[10] González, M.; Rodríguez, A.; Pereira, O.; Celaya, A.; Lopez de Lacalle, L. N.; Esparta, M. Axial-compliant tools for adaptive chamfering of sharp-edges: Characterisation and modelling. Engineering Science and Technology, an International Journal, 41, 101407, 2023.
[11] González, M.; Rodríguez, A.; Lopez de Lacalle, L. N. A novel methodology to improve robotic contour following by using radial-compliant pneumatic spindles. The International Journal of Advanced Manufacturing Technology, 2025.