Aimplas ha demostrado buenos resultados en la separación de gases y la eliminación de contaminantes, así como en el almacenamiento de energía
Membranas mixtas para la separación de gases, la eliminación de fármacos y la generación de energía
Daniela Ramírez, investigadora del Departamento de Descarbonización de Aimplas, Instituto Tecnológico del Plástico
24/09/2024Las membranas de matriz mixta (MMM) son membranas compuestas fabricadas mediante la combinación de un material híbrido inorgánico o inorgánico-orgánico en forma de micro o nanopartículas (la fase dispersa; aditivo o relleno) y una matriz polimérica (la fase continua) capaces de ofrecer un gran potencial dado su rendimiento superior de permeación y separación de gases que involucran al dióxido de carbono (CO2) y al metano (CH4). Las separaciones de las principales mezclas de gases industriales CO2/CH4 y CO2/N2 se encuentran entre los procesos de separación de gases más importantes como la obtención del gas natural o en la generación de los gases de combustión de las industrias. Esta separación es tan importante y necesaria debido a que la presencia de CO2 en la corriente gaseosa reduce el poder calorífico de la misma, además hace que sea corrosiva, perjudicando a las tuberías utilizadas para el transporte de la corriente de gas. De igual forma las MMMs se emplean en la eliminación de fármacos y/o contaminantes en las corrientes acuosas, dado sus cualidades intrínsecas como alta eficiencia, respeto por el medio ambiente, bajo coste, escalabilidad, huella mínima y simplicidad. Uno de los principales riesgos en el tratamiento de las aguas residuales es la posible transferencia de compuestos farmacéuticos tóxicos (PhC) al ecosistema. La eliminación de compuestos farmacéuticos se puede lograr a través de varias rutas, incluidos los procesos de oxidación avanzada (AOP), la adsorción o la tecnología de filtración por membrana. Muchos productos farmacéuticos se han eliminado de forma eficiente mediante ultrafiltración (UF), nanofiltración (NF) y ósmosis inversa (RO).
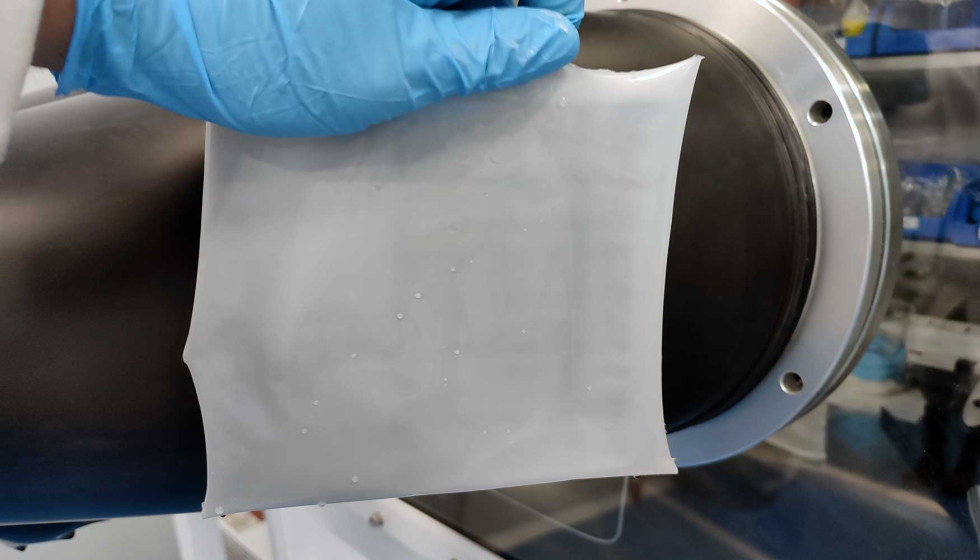
Durante estos últimos años, en Aimplas hemos estado trabajando tanto en la separación selectiva de gases, como en la eliminación de contaminantes farmacéuticos a través del desarrollo de MMMs, basadas en materiales adsorbentes tipo zeolitas, MOFs, carbones o silíceos, desarrolladas y/o modificadas por nosotros. Durante el desarrollo de estas membranas se ha trabajado con una amplia gama de poliméricos, desde polímeros termoplásticos y poliolefinas hasta polieterimidas y poliamidas.
Principalmente el desarrollo de estas membranas se ha llevado a cabo mediante la metodología solvent-casting, la cual consiste en la disolución del polímero en un solvente apropiado, dispersión de las partículas en la disolución, casting sobre placa de vidrio empleando un doctor Blade o cuchilla de conformado y la posterior evaporación controlada del solvente para formar una membrana sólida. No obstante, existen diversas tecnologías de síntesis como template leaching, sol-gel, sintering, stretching o track-etching.
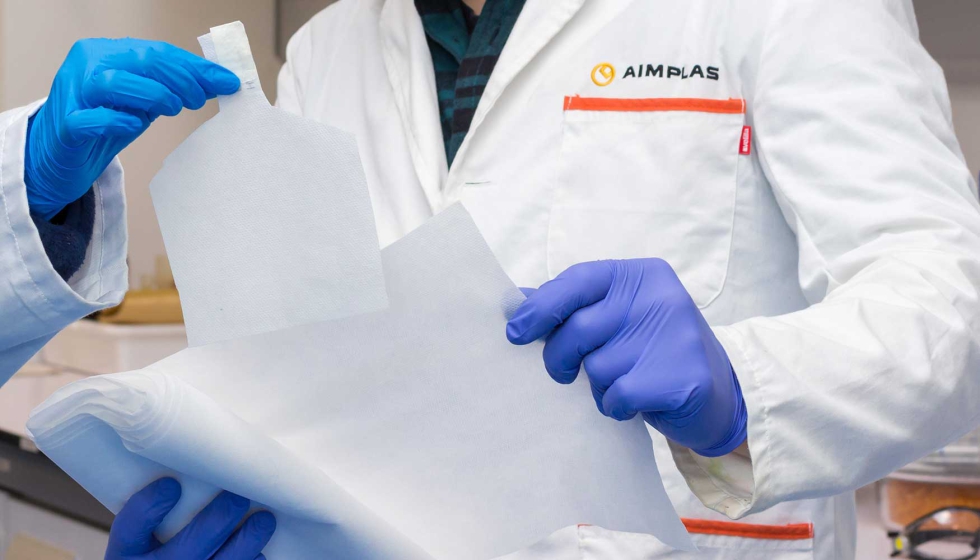
La técnica de template leaching (lixivación de patrón) consiste en mezclar el polímero base con un material que será removido posteriormente, como sales solubles o polímeros sacrificables. Tras la formación del film, se somete a un tratamiento químico o lavado con solventes para lixiviar o eliminar el componente removible, generando una estructura porosa en la membrana. Este método permite ajustar el tamaño y la distribución de los poros en función de la proporción y el tamaño del material lixiviable.
Por otro lado, en la técnica sol-gel se utiliza un precursor (generalmente un alcóxido metálico o sales inorgánicas) al que se le aplicarán reacciones de hidrólisis y policondensación para formar un gel. Este gel se seca y se calienta para obtener membranas cerámicas, metálicas y de vidrio. Este método es altamente versátil y permite controlar las propiedades finales del material, como la porosidad y el tamaño de los poros.
La técnica sintering o sinterizado permite obtener las membranas a partir de polvos (poliméricos o inorgánicos) por compresión y tratamiento térmico posterior, en este caso la temperatura debe estar entre 70 y 90% del punto de fusión del material. Este calentamiento promueve la coalescencia de los polvos y la eliminación de espacios vacíos (poros), formando una membrana sólida pero porosa. La porosidad resultante puede controlarse mediante la selección del tamaño de los polvos y las condiciones de sinterizado.
Por su parte, el stretching o deformación mecánica consiste en deformar mecánicamente el film aplicándole una tensión determinada. Se puede realizar en frío o en caliente, en una o más direcciones, normalmente sobre polímeros parcialmente cristalinos, formándose celdas por rotura parcial de las regiones amorfas del polímero. Finalmente, la técnica de track-etching consiste en la irradiación de una película polimérica delgada con iones pesados de alta energía que crean huellas de daño lineal en la estructura del polímero. Seguidamente, se somete a un grabado químico selectivo para agrandar dichas huellas y formar poros cilíndricos bien definidos. Esta técnica permite un control muy preciso sobre el tamaño, la densidad y la distribución de los poros.
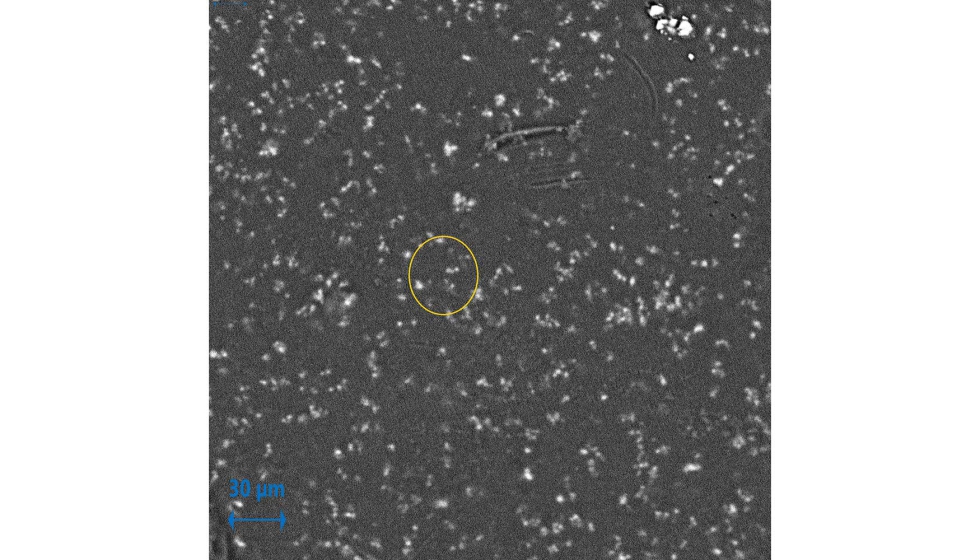
Entre los desarrollos llevados a cabo por Aimplas destaca una eliminación de un 94% de fármaco presente en una corriente acuosa mediante la síntesis de MMMs en el proyecto Eternal y la fabricación de membranas con buena selectividad para la separación de CH4/CO2 o H2/CO2 producidas en el proyecto MatenergyH2. En la siguiente imagen de SEM se observa una buena distribución de las partículas inorgánicas dentro de la matriz polimérica de la membrana desarrollada.
Analizando de forma adicional mediante espectroscopia infrarroja con transformada de Fourier, se observa la aparición de los grupos funcionales característicos de cada partícula inorgánica (en este caso el enlace de silíceo) dentro de la matriz polimérica (en el grupo sulfonilo).
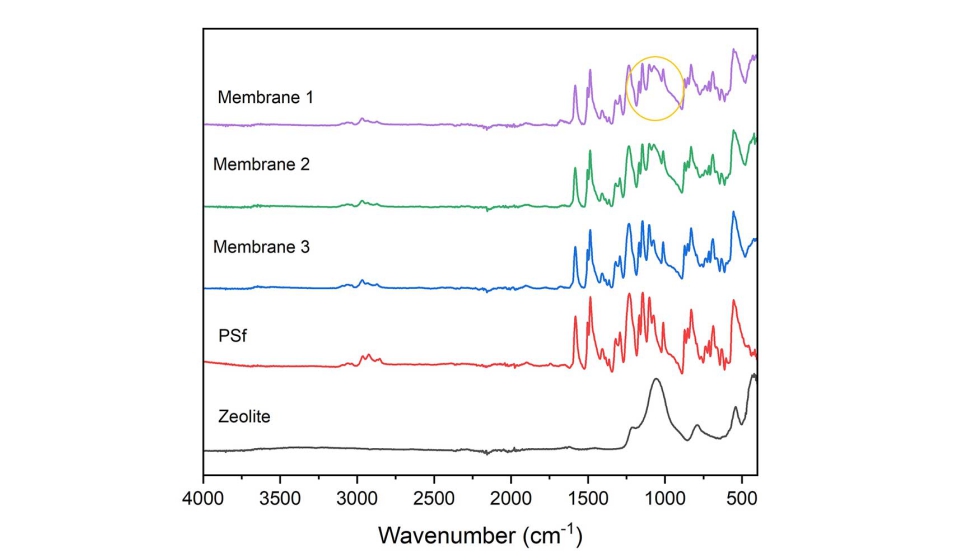
Diversos estudios han desarrollado varios tipos de tecnologías de almacenamiento de energía electroquímica, incluidas las baterías de iones de litio (Li), las baterías de plomo-ácido, las baterías de metal-aire, las baterías de flujo redox, las pilas de combustible y los supercondensadores. Hoy en día, la batería de iones de litio está ampliamente utilizada; Sin embargo, debido a su baja densidad de energía y a las preocupaciones sobre la seguridad, se están buscando alternativas. En este sentido, las baterías de metal-aire han llamado mucho la atención debido a sus diversas ventajas, como el bajo coste, las altas densidades de energía teóricas y los beneficios ambientales. Las membranas utilizadas en baterías metal-aire poseen la capacidad de transportar iones entre el electrodo de aire y el electrodo metálico, al tiempo que proporciona una barrera física entre los dos electrodos para evitar cortocircuitos eléctricos. El rendimiento de esta batería se ve muy afectado por las propiedades fisicoquímicas de la membrana empleada. No obstante, es importante resaltar que estas membranas deben tener alta resistencia estructural, estabilidad química y alta conductividad iónica para garantizar la seguridad y la fiabilidad a largo plazo de la batería. En este tipo de aplicación la reacción de reducción de oxígeno (ORR) es el núcleo de los dispositivos de conversión y almacenamiento de energía, debido a la lenta cinética. Por lo tanto, es necesario el desarrollo de electrocatalizadores eficientes y estables para reducir la barrera de energía y acelerar la velocidad de reacción para mejorar la eficiencia de conversión de energía, donde las membranas de matriz mixta y los electrocatalizadores podrían tener un papel fundamental. En este sentido, desde Aimplas se empezó a trabajar dentro del marco del proyecto Acumulareq en el desarrollo de membranas poliméricas biobasadas para su uso como separadores en baterías metal-aire.
Es por todo ello que en Aimplas estamos comprometidos con la innovación en el desarrollo de membranas avanzadas que permitan aportar soluciones a las industrias y al sector tecnológico. Con nuestras capacidades en la creación de membranas de matriz mixta y otras tecnologías de vanguardia, hemos demostrado buenos resultados en la separación de gases y la eliminación de contaminantes, así como en el almacenamiento de energía. Y seguimos fomentando la colaboración con empresas, centros tecnológicos y universidades para llegar a este objetivo común de desarrollo soluciones eficientes y sostenibles que impulsen la competitividad y el rendimiento en sus procesos industriales y aporten valor a la sociedad.