Nuevo sistema de disipación y recuperación de calor para aviones eléctricos más eficientes
Belén García, Virginia Sáenz, Amaya García y Asier Salicio, de Cidetec
08/05/2024Aviones eléctricos impulsados por hidrógeno
Las pilas de combustible de hidrógeno no producen emisiones de CO2 en vuelo y son más eficientes y sostenibles que los motores de turbina tradicionales que se alimentan de queroseno. Además, el hidrógeno es un recurso natural abundante y renovable, por lo tanto, la propulsión de los aviones con hidrógeno puede ser clave para lograr la neutralidad climática en la aviación de aquí a 2050. Sin embargo, es necesario afrontar y resolver varios retos, como la gestión térmica y la disipación de calor de las pilas de combustible en el avión, para que los aviones eléctricos basados en pilas de combustible puedan ser una solución viable para el transporte aéreo.
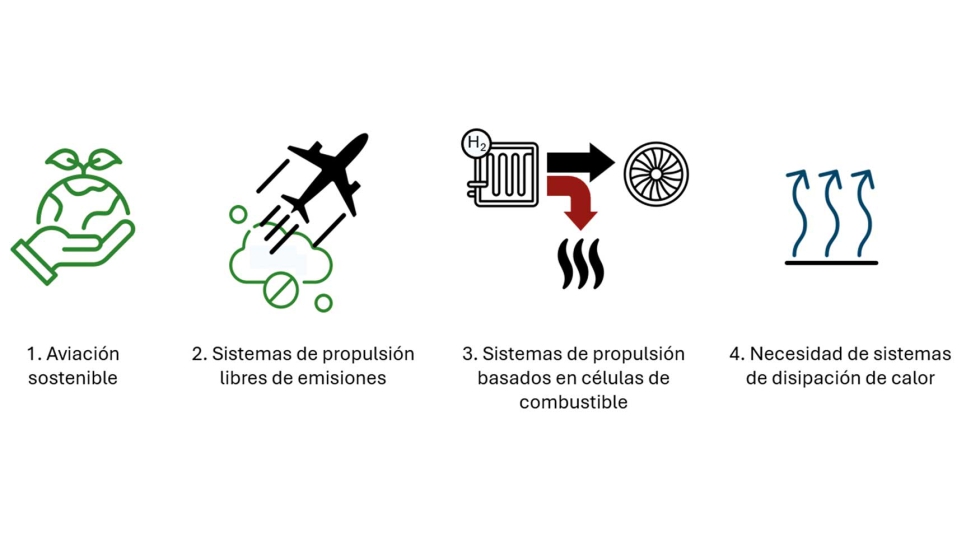
Aunque los motores de turbina producen más calor que las pilas de combustible, pueden disiparlo fácilmente en forma de gases de escape calientes. Por el contrario, una pila de combustible, al igual que una batería, se calienta durante su funcionamiento y requiere de un sistema especial de gestión térmica para mantenerla en su temperatura de funcionamiento óptima. Se prevé que la eficiencia eléctrica de las pilas de combustible alcance el 50% en 2030, lo que significa que cada vatio de electricidad producido en la pila de combustible generará un vatio de calor residual. Recuperar este calor para un uso posterior en el avión sería una ventaja adicional de la tecnología.
En este contexto, los socios del proyecto Europeo exFan están investigando una solución que permita disipar el calor residual generado en las pilas de combustible, sin pérdidas adicionales por arrastre y el uso de ese calor residual para generar empuje o propulsión adicional para el avión.
Dispositivo de recuperación de calor basado en el efecto Meredith
El dispositivo de recuperación de calor en el que se centra el proyecto exFan se basa en el efecto Meredith. Este efecto es un fenómeno físico que tiene lugar en el conducto de un avión en el que el aire que circula por él, que se mueve a mayor velocidad que el avión, es calentado por un intercambiador de calor. El aire fluye por el conducto cuya sección transversal es divergente, lo que provoca un aumento de la presión del gas al reducirse su velocidad; este efecto se denomina efecto ramjet. A medida que circula por el intercambiador, el aire se calienta, aumentando su energía térmica y la entalpía del flujo, es decir, su energía total. Este aire calentado y presurizado sale por un conducto de escape que tiene un diseño convergente (se hace estrecho hacia el final) que acelera el aire saliente con una velocidad superior a la de su entrada (gracias a la energía obtenida a través del intercambiador de calor). La diferencia de movimiento del flujo de aire entre la entrada y la salida del conducto genera una fuerza que, según la tercera ley de Newton, se traduce en un empuje efectivo.
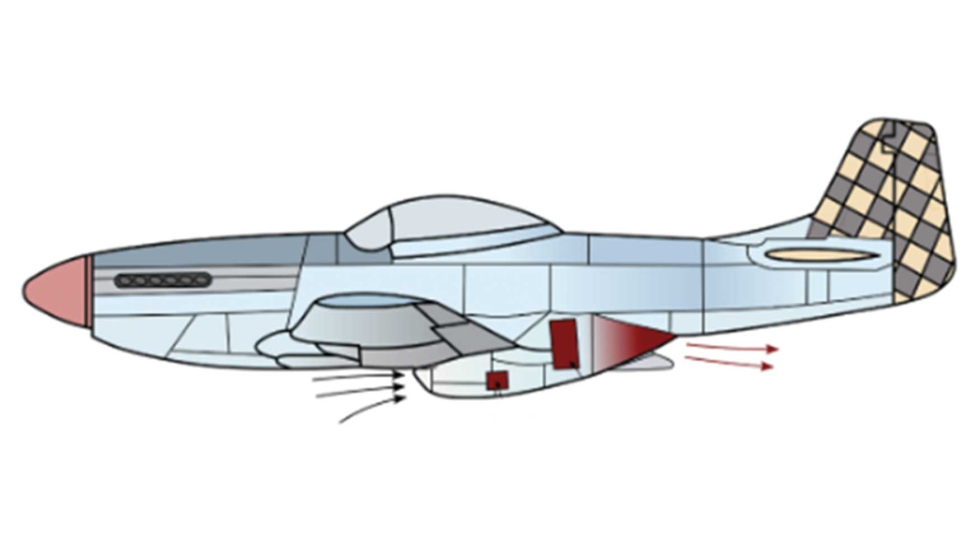
El dispositivo de recuperación de calor que se está diseñando en el proyecto exFan está formado por el ventilador, los componentes aerodinámicos de la trayectoria del flujo y el intercambiador de calor. El ventilador es accionado por un motor eléctrico de alta velocidad mediante reductor y comprime el aire aspirado. Esta arquitectura permite obtener la mayor potencia específica. El motor eléctrico y su correspondiente electrónica de potencia y controladores se alimentan principalmente de una pila de combustible y durante los picos de demanda de potencia, una batería comparte la carga con la pila de combustible (por ejemplo, durante el despegue). Un sistema de gestión térmica se conecta a todos los componentes mencionados anteriormente, para proporcionar unas condiciones térmicas de funcionamiento adecuadas.
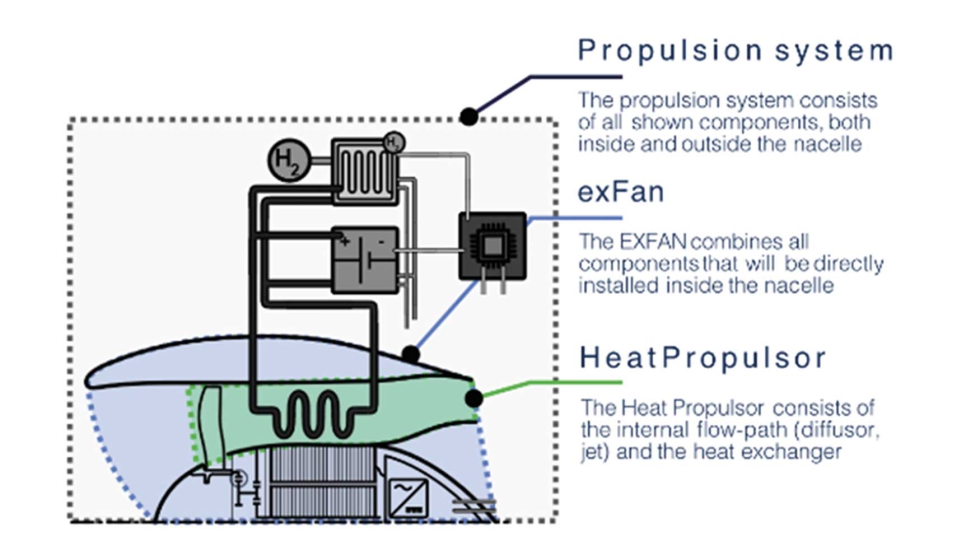
El sistema exFan engloba todos los componentes que no están relacionados con el almacenamiento y conversión de energía. Este nuevo concepto de propulsión propuesto requiere de intercambiadores de calor que presenten una serie de características que los hagan más eficientes y duraderos.
Intercambiadores de calor eficientes y duraderos producidos por fabricación aditiva
En este escenario, uno de los principales objetivos del proyecto es el diseño y fabricación de un intercambiador de calor eficiente y duradero, es decir de alta resistencia al fouling, al desgaste y a la corrosión. Los objetivos de diseño para alcanzar el equilibrio entre empuje y resistencia —alta transferencia de calor y bajas pérdidas de presión— son en cierto modo opuestos en el diseño del intercambiador de calor. Por lo tanto, deben equilibrarse cuidadosamente. La alta transferencia de calor en los intercambiadores de calor se consigue con estructuras o geometrías que conducen a un flujo turbulento, pero la baja resistencia se consigue con estructuras que conducen a un flujo laminar. En el proyecto exFan se está trabajando en el diseño eficiente del intercambiador de calor que será producido por fabricación aditiva (FA) mediante la tecnología de lecho de polvo L-PBF empleando un diseño biónicos o bio-inspirados. El empleo de la FA permite fabricar intercambiadores de calor más eficientes debido a las geometrías complejas y diseño de canales internos que pueden fabricarse con esta tecnología y que no sería posible obtener por métodos convencionales.
Optimización multifísica para aumentar la eficiencia de los intercambiadores de calor
El concepto de optimización multifísica consiste en combinar múltiples disciplinas para crear diseños de alto rendimiento optimizados según múltiples objetivos de optimización. Los principales objetivos de optimización para el diseño de un intercambiador de calor son una elevada relación superficie/volumen y el equilibrio adecuado entre flujo turbulento y laminar, así como la durabilidad estructural y la ligereza. Para lograr estos objetivos y crear diseños de piezas complejas, se utiliza una combinación de diferentes herramientas CAD, así como simulación CFD y FEM. Estos diseños pueden incluir canales internos complejos, superficies de forma libre o estructuras reticulares de relleno. Para ello son especialmente adecuadas las estructuras reticulares formadas por superficies mínimas triplemente periódicas (TPMS, Triply Periodic Minimal Surfaces), que pueden describirse mediante una ecuación matemática y presentan una relación mínima entre volumen y superficie.
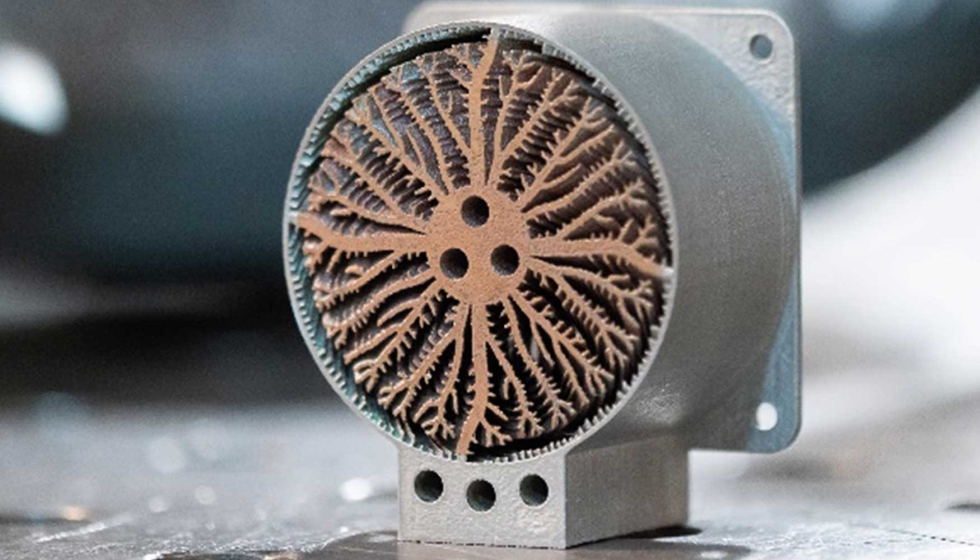
Sin embargo, las nuevas soluciones suelen plantear nuevos retos. El empleo de la fabricación aditiva para fabricar intercambiadores de calor introduce nuevas particularidades no contempladas hasta ahora en los materiales fabricados de forma convencional.
Por un lado, la acumulación de partículas es un problema importante en los intercambiadores de calor de aeronaves de fabricación aditiva en bruto, debido a la elevada rugosidad de las superficies obtenidas por estas tecnologías. Las partículas acumuladas pueden aumentar significativamente las pérdidas de presión del intercambiador de calor y reducir la transferencia de calor. Además, la corrosión y la erosión también limitan la capacidad de transferencia de calor de estos componentes. Para hacer frente a estos eventos que afectan a la eficacia de los intercambiadores de calor, exFan plantea la aplicación de recubrimientos protectores en las superficies de los intercambiadores, así como de los pre-tratamientos necesarios para disminuir la rugosidad de este tipo de superficies y aumentar así la eficiencia del componente.
Tratamientos superficiales para aumentar la eficiencia y durabilidad de los intercambiadores de calor
Como se ha comentado anteriormente, el empleo de la fabricación aditiva permite fabricar intercambiadores de calor con geometrías con diseños complejos, que no permiten la aplicación de la mayoría de los tratamientos superficiales necesarios para reducir la rugosidad de los componentes y protegerlos frente al desgaste y la corrosión. En este contexto, los tratamientos superficiales químicos son los únicos que pueden emplearse para tratar cualquier tipo de geometría independiente de su estructura interna ya que únicamente requieren del contacto entre la superficie a tratar y un electrolito específico a una temperatura determinada durante un tiempo concreto.
Por tanto, la aplicación de tratamientos superficiales químicos, como el pulido o metalizado, permite mejorar las prestaciones del intercambiador de calor en términos de eficiencia, resistencia a la corrosión y al desgaste y/o fouling.
Pulido químico
El pulido químico implica generalmente la inmersión de la pieza a tratar en un tanque que contiene un electrolito ácido que, con una concentración óptima y unas condiciones de temperatura y agitación adecuadas, reduce su rugosidad superficial. La superficie de una pieza puede visualizarse como una serie de ‘picos y valles’. Para que un electrolito reduzca la rugosidad de esta superficie y por tanto sea adecuado para el pulido, debe ser capaz de eliminar más material en los picos que en los valles. Para ello es imprescindible que durante el proceso reaccione con el material a tratar formando una película viscosa en su superficie que proteja a los valles de la reacción de disolución frente a los picos, mediante un proceso de oxidación controlada.
Metalizado químico
Por otro lado, el metalizado químico, a diferencia de los procesos de electrodeposición, es una tecnología para la aplicación de recubrimientos por inmersión en el que no es necesario aplicar un potencial eléctrico para que el proceso tenga lugar ya que este se produce mediante un agente reductor presente en la propia disolución. Entre los diferentes metales susceptibles de ser aplicados mediante esta tecnología (Ag, Au, Ni, Cu, etc.), el niquelado químico copa el 95% de las aplicaciones industriales. El recubrimiento obtenido por esta tecnología es una aleación de níquel y fósforo (proveniente del agente reductor) que presenta propiedades variables, tanto mecánicas como de resistencia a la corrosión, en función del contenido en P de la aleación. Este tipo de proceso de metalizado puede aplicarse tanto sobre sustratos dieléctricos como conductores. En este último grupo, el aluminio es uno de los materiales más habitualmente tratados con níquel químico con el objetivo de mejorar sus prestaciones para ampliar el rango de aplicaciones en las que puede utilizarse este material, entre ellos, el sector aeronáutico.
Sin embargo, la aplicación de níquel químico sobre aluminio, material habitual en intercambiadores de calor producidos por fabricación aditiva, no es directa y requiere de una preparación específica de este tipo de materiales para poder llevarlo a cabo. En el caso del aluminio, para poder lograr un depósito adherente, es necesario eliminar la capa de Al2O3 nativa de estos materiales mediante tratamientos en medio ácido específicos. Sin embargo, la diferencia de reactividad entre el níquel y aluminio provocaría problemas de adherencia en las etapas posteriores del proceso de metalizado. Para evitarlo, se incluye una etapa adicional previa mediante la cual se deposita una capa en base Zn que permite la aplicación controlada de la etapa de níquel químico y da lugar a recubrimientos adherentes sobre sustratos de aluminio.
Procesos químicos out-of-bath para el tratamiento de geometrías internas complejas
Históricamente, los tratamientos superficiales químicos, tanto pulido como metalizado, han sido aplicados mediante la inmersión del componente a tratar en tanques que alojaban las diferentes etapas descritas anteriormente. Esta aproximación implica, excepto en zonas enmascaradas, que el proceso se produce de forma homogénea en toda la superficie del componente, tanto interna como externa. Existen aplicaciones, como en el caso de los intercambiadores de calor, en el que la zona de interés donde aplicar el recubrimiento es una zona de difícil acceso (canales interiores, geometrías intrincadas, etc.), y es aquí donde la necesidad de una aplicación selectiva de recubrimientos metálicos cobra sentido.
El proyecto exFan dará solución a esta necesidad mediante el desarrollo de un innovador dispositivo de recirculación que distribuya el electrolito en el proceso de recubrimiento directamente en los complejos canales internos del intercambiador de calor. De este modo, se protegerá la superficie interna y se reducirá la posible acumulación de partículas en comparación con la superficie sin acabar. Esto aumentará la transferencia de calor en funcionamiento y permitirá utilizar canales extremadamente finos (<200 µm de diámetro), para los que un depósito de partículas de 20 µm supondría aproximadamente 1/3 menos de área de sección transversal. Si se aplica correctamente, el revestimiento también tiene excelentes propiedades anticorrosión, siendo casi totalmente resistente a las soluciones salinas, los hidrocarburos, los álcalis y los ácidos.
Debido a la selectividad requerida en el tratamiento de los intercambiadores de calor, se llevará a cabo la aplicación de los procesos químicos mediante la aproximación out-of-bath. Ésta consiste en recircular los electrolitos, de cada una de las etapas del proceso, a través de los canales del intercambiador para lograr de esta forma el tratamiento (pulido y metalizado) de su superficie interna. El sistema out-of-bath requiere además de una menor cantidad de electrolito comparado con el sistema de inmersión tradicional, por lo tanto, es un proceso más sostenible y económico.
Proyecto Europeo exFan
El proyecto exFan, abreviatura de “Novel Recuperation System to Maximize Exergy from Anergy for Fuel Cell Powered Geared Electric Aircraft Propulsion System”, es una iniciativa de investigación financiada por la Unión Europea (GA 101138184) como parte del programa HORIZON EUROPE. Este proyecto, que comenzó en diciembre de 2023, tiene una duración de 4 años y reúne a un consorcio de 10 socios procedentes de 5 países. Cidetec Surface Engineering lidera la coordinación del proyecto, en colaboración con ADT, que actúa como coordinador técnico, y TUW como coordinador de investigación, mientras que socios como Fraunhofer IAPT, DLR, PowerID, EASN-TIS, IRES, FZG/TUM y Egile Mechanics aportan su experiencia y recursos para impulsar el proyecto. Más detalles en la web de exFan (https://exfan-project.eu/home).
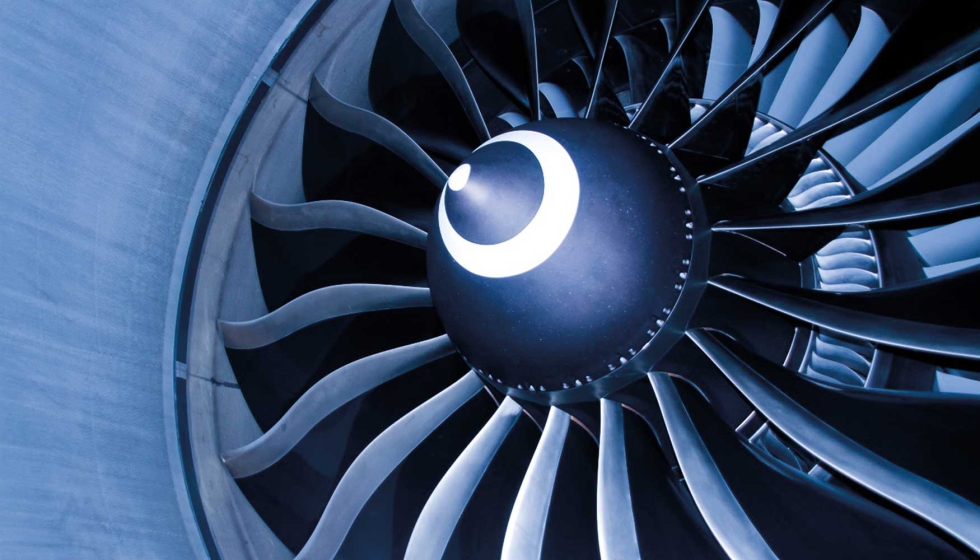
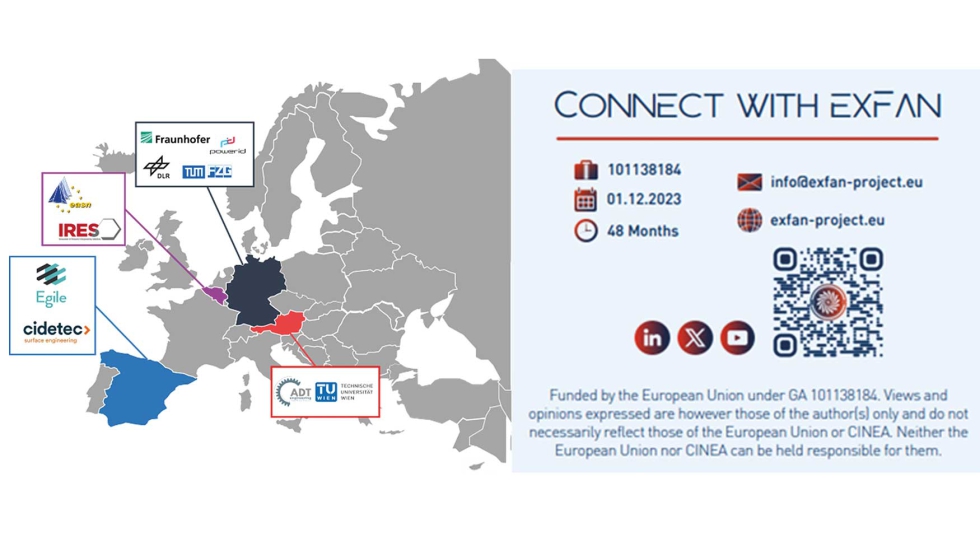
En el proyecto exFan, Cidetec trabaja en el diseño de un sistema out-of-bath ad-hoc para el tratamiento de las geometrías de intercambiadores de calor más prometedoras diseñadas y fabricadas en el proyecto por el socio alemán Fraunhofer IAPT. Además, optimizará los tratamientos químicos de pulido y deposición de capas metálicas, mediante el ajuste de parámetros como la temperatura, caudal y composición del electrolito, así como el tiempo de proceso, para lograr los objetivos marcados. Actualmente, Cidetec está inmerso tanto en la fase de diseño del sistema experimental para la aplicación de los tratamientos químicos, como en la optimización de las condiciones de trabajo a escala de laboratorio para, una vez definidas, aplicarlas sobre los demostradores reales.
En resumen, el intercambiador de calor diseñado en el proyecto exFan tendrá un diseño biónico con un acabado superficial adecuado para impedir la acumulación de partículas, la corrosión y la erosión. Además, se está diseñando un novedoso sistema de gestión térmica para optimizar la calidad del calor residual y controlar el flujo térmico del sistema de propulsión. También se investigan las condiciones óptimas de funcionamiento, y se creará un modelo de simulación para optimizar los parámetros de funcionamiento. Las primeras pruebas funcionales de exFan a escala de laboratorio servirán para verificar dicho modelo.
Cidetec Surface Engineering
La Unidad de Coatings y Tratamientos de Superficies de Cidetec Surface Engineering está orientada al diseño, desarrollo, aplicación y caracterización de recubrimientos y superficies para la mejora de las propiedades estéticas y funcionales de los materiales. Dispone con 4.000m2 de instalaciones vanguardistas equipadas con tecnología punta. La investigación a llevar a cabo en el proyecto exFan cubre diferentes líneas de investigación como el desarrollo de recubrimientos multifuncionales y tratamientos superficiales de aleaciones ligeras y el estudio de fenómenos de corrosión, tribología y degradación. Para ello, la unidad cuenta con un equipo humano altamente cualificado en diferentes tecnologías de aplicación por vía húmeda como electrodeposición, deposición ‘electroless’, anodizado, deposición electroforética, formulación y aplicación de esmaltes, procesos de electro-pulido, pulido químico y mecánico.
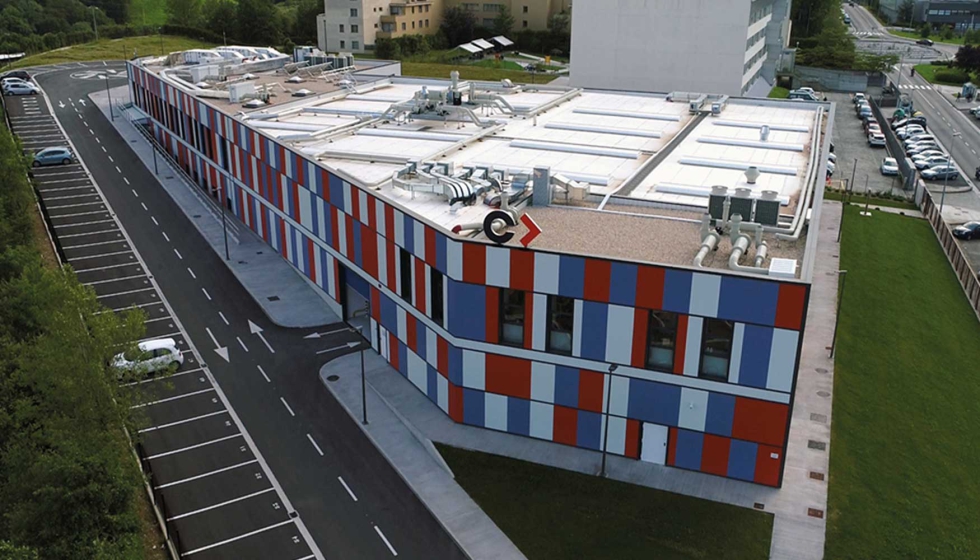