Los fabricantes de maquinaria muestran en GrindingHub soluciones de seguridad para los procesos digitales de rectificado
Los datos de los procesos son un activo valioso. “Los niveles de concienciación han aumentado considerablemente en los últimos años”, confirma Alexej Voigt, responsable de Ingeniería Eléctrica del fabricante de rectificadoras Danobat-Overbeck, de Herborn. Voigt dio una charla en la última conferencia de la Schleiftagung en Stuttgart-Fellbach, celebrada a finales de enero. Allí habló del potencial del análisis de datos de máquinas para la optimización del proceso de rectificado y también esbozó métodos para la adquisición y el análisis de datos en husillos motorizados digitales.
Fácil adquisición de datos
Para Alexej Voigt, el uso de componentes inteligentes que proporcionan datos para la supervisión en tiempo real es la clave para seguir optimizando el rendimiento, la eficacia y la fiabilidad de las máquinas. “También proporcionan la base para el análisis avanzado y el mantenimiento predictivo en forma de servicios digitales”, afirma el experto. Sin embargo, también es consciente de las preocupaciones de las empresas más pequeñas, en particular cuando se trata de mantener el control sobre sus propios datos y los posibles ciberataques. Voigt cree que los fabricantes de maquinaria tienen el deber de proporcionar información, transmitir la experiencia de proyectos faro anteriores y diseñar soluciones modulares que se adapten a las pequeñas y medianas empresas (pyme). “Unos estándares de seguridad elevados, unas interfaces claramente definidas y unos productos certificados representan las mejores formas de establecer la confianza”, está convencido, y subraya: “Nuestro objetivo es facilitar a nuestros clientes el acceso a tecnologías de producción basadas en datos sin necesidad de contar con un amplio equipo de ingenieros para desarrollar soluciones independientes específicas para cada aplicación”.
El Instituto Fraunhofer de Sistemas de Producción y Tecnología de Diseño (IPK) de Berlín ha observado que cada vez más fabricantes de sistemas equipan sus máquinas con amplios sistemas de sensores y monitorización desde el principio. Es importante orientar la digitalización ante todo a la configuración de la máquina y determinar qué datos de proceso proporciona automáticamente la máquina de producción. Según el IPK, los datos de rendimiento de la máquina o los parámetros y ajustes del proceso pueden servir como fuentes de información adicionales junto con los sensores y sistemas de control incorporados. Un vistazo a las soluciones digitales que ya ofrecen los fabricantes de rectificadoras da una idea de las ventajas que pueden obtenerse del uso de los datos. El primer paso consiste siempre en crear un espacio de datos cerrado (nube privada, intranet) limitado exclusivamente a la propia empresa. Las interfaces abiertas y estandarizadas basadas en OPC UA se utilizan para garantizar que las nuevas rectificadoras, las máquinas existentes, las máquinas de distintos fabricantes e incluso los robots de la fábrica puedan comunicarse entre sí e intercambiar datos. El escaparate umati (interfaz universal de tecnología de máquinas) de la feria GrindingHub, que la VDW (Asociación Alemana de Constructores de Máquinas-Herramienta) organiza en Stuttgart del 14 al 17 de mayo, destacará las ventajas en una demostración en directo.
La conectividad ha sido parte integrante de GrindingHub desde el debut del evento hace dos años. La iniciativa umati, lanzada por la VDW en 2017, es una comunidad creada por la industria de la ingeniería y sus clientes. Su objetivo es difundir y utilizar estándares de interfaz abiertos basados en OPC UA.
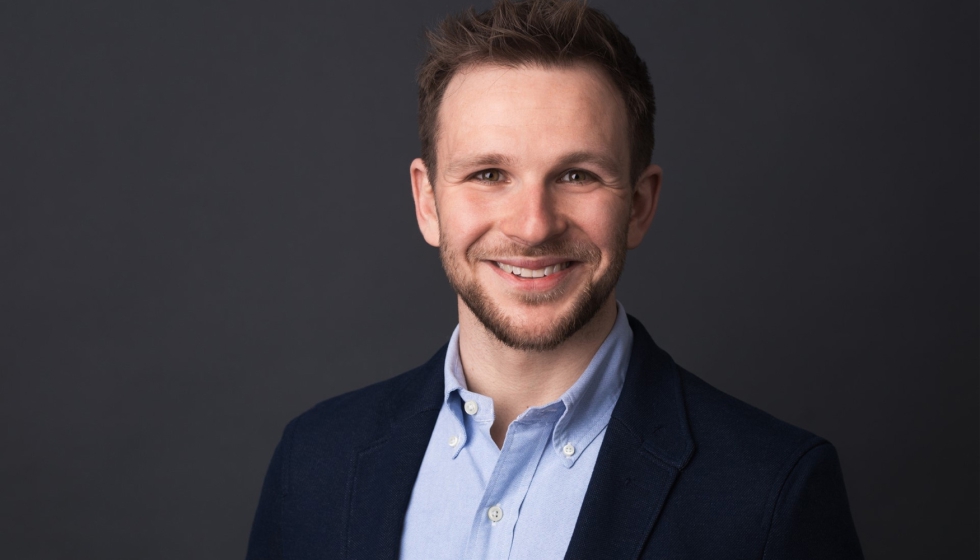
Creación de un IoT dedicado
Entre los socios y expositores de umati en GrindingHub también se encuentra la empresa de Coburgo Kapp Niles, especialista en máquinas para el mecanizado fino de engranajes y perfiles. André Wetz, jefe de proyecto de transformación digital, explica cómo puede estructurarse un sistema digital modular. Un paquete de hardware estandarizado (compuesto por sensores y un PC industrial con cortafuegos y servidor OPC UA) constituye la base del sistema. Los clientes pueden seleccionar las soluciones de software que necesiten, como la supervisión del estado de los ejes lineales y giratorios para determinar su desgaste, o la supervisión y evaluación de componentes específicos de los procesos de rectificado y reavivado en tiempo real para reducir las tasas de rechazo.
Otra solución digital es un sistema de bucle cerrado que permite la integración perfecta de las máquinas de procesamiento y medición. “Los empleados ya no tienen que intervenir para medir las piezas una vez rectificadas”, explica André Wetz. El sistema garantiza que los datos de la máquina de procesamiento se transmitan directamente a la máquina de medición. El informe de medición se devuelve a la máquina en formato GDE (intercambio de datos de engranajes), que puede realizar las correcciones necesarias de forma independiente.
André Wetz subraya que todas las soluciones funcionan en las propias máquinas del cliente y en su propia red. “Esto debería disipar desde el principio cualquier preocupación sobre una posible pérdida de soberanía de los datos o la amenaza de ciberataques”, señala. Esto permite a los clientes decidir por sí mismos si quieren optimizar su rendimiento y cómo, y qué beneficios quieren obtener del intercambio de datos con partes externas, como fabricantes de máquinas o socios en la cadena de valor. Según Wetz, son sobre todo los clientes de Kapp Niles de la industria automovilística y de proveedores los que actualmente se benefician de las mejoras de eficiencia gracias a la interconexión digital. Como ejemplo de una aplicación concreta, cita la supervisión inteligente de procesos para engranajes silenciosos. Puede utilizarse para identificar componentes ruidosos durante el mecanizado y reducir la tasa de rechazos. “Es un medio eficaz para cumplir los requisitos de calidad de los vehículos eléctricos”, afirma Wetz. Al mismo tiempo, sin embargo, los ejemplos dejaron claro que la conexión en red más allá de los límites de la empresa también aporta el mayor valor añadido.
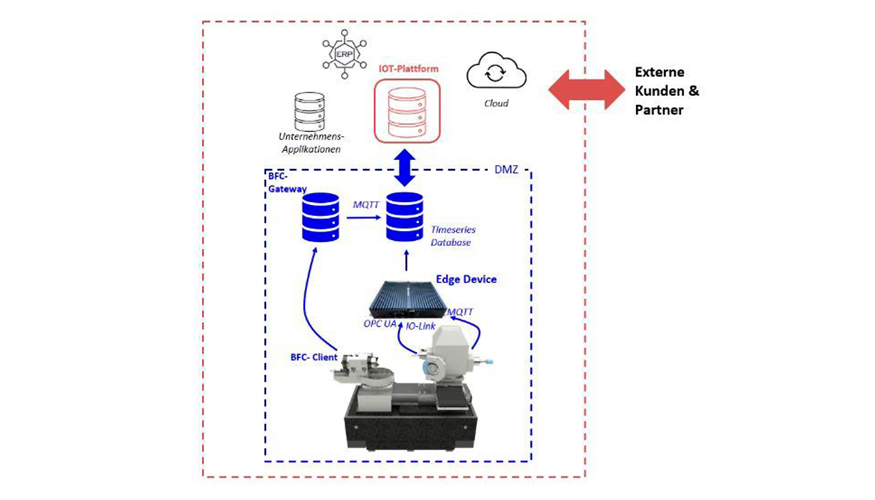
Valor añadido mediante aplicaciones seguras en la nube
El importante número de proyectos de investigación financiados con fondos públicos demuestra que el desarrollo de arquitecturas de nube seguras y translocalizadas suscita actualmente un considerable interés científico y político. Esto incluye el desarrollo de una arquitectura de sistema de nube de borde compatible con Gaia-X, que es el núcleo del proyecto de investigación Escom (Edge Services for Components). Danobat-Overbeck también participa en el proyecto a través de su colaboración con el Instituto de Gestión de la Producción, Tecnología y Máquinas Herramienta (PTW) de TU Darmstadt. Cuando se trata de desconfiar de las soluciones en la nube, las empresas no suelen ser diferentes de los particulares. Si las empresas no tienen una idea clara de lo que ocurre con sus datos o incluso de dónde se almacenan, esto puede apagar gran parte de la euforia que rodea a tecnologías por lo demás prometedoras. El Edge Computing consiste en procesar y almacenar los datos en el lugar donde se recogen. Sólo se envían
Sólo se envían cantidades significativamente reducidas de datos especialmente seleccionados ‘previa invitación’ a instancias informáticas externas o a la nube a través de una interfaz definida. “Este sistema aumenta la seguridad, pero la computación de borde también permite altas velocidades de transferencia de datos, capacidad en tiempo real y soberanía de los datos”, explica Alexej Voigt. Los usuarios mantienen en todo momento el control sobre qué datos salen de la red y cuáles no”.
El profesor Matthias Weigold, responsable del PTW en TU Darmstadt, escribió recientemente un artículo en el que destaca el papel especial de Escom en el desarrollo de aplicaciones Gaia-X en la industria manufacturera. Gaia-X es un proyecto europeo conjunto cuyo objetivo es facilitar el intercambio de datos a lo largo de la cadena de valor, garantizando al mismo tiempo que la soberanía digital permanezca en manos de los propietarios de los datos y asegurando la interoperabilidad de las distintas plataformas. Según Weigold, que también es miembro de la WGP (Asociación Académica Alemana para la Tecnología de la Producción, que agrupa a los principales académicos de las ciencias de la producción), Escom proporciona elementos clave para las aplicaciones de Gaia-X en la industria manufacturera. Así pues, el proyecto de investigación contribuye de forma importante a definir el valor añadido y los nuevos tipos de modelos producto-servicio.
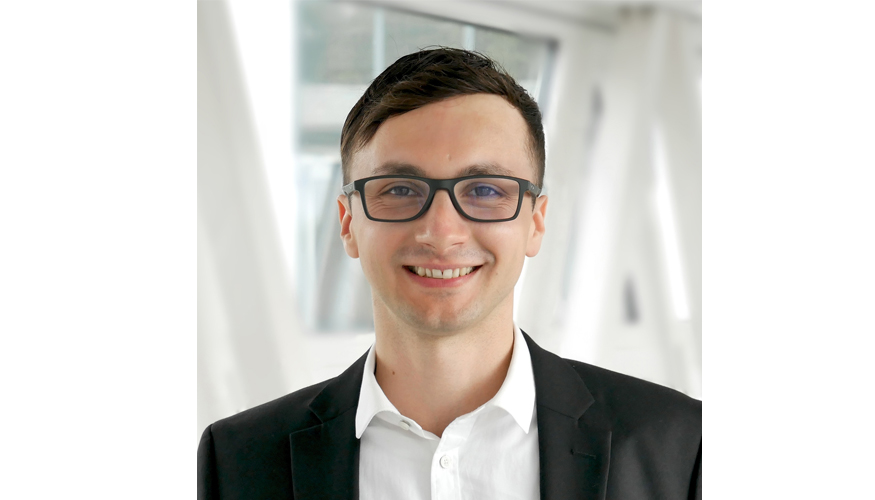
Gaia-X: una fuente de esperanza
Gaia-X también se dirige explícitamente a las pequeñas y medianas empresas. La red ‘Mittelstand-Digital’ enumera tres ventajas clave que una nube europea aporta a las PYME: en primer lugar, los servidores ubicados en Europa están sujetos a la legislación europea; en segundo lugar, las empresas pueden utilizar una infraestructura de datos en nube europea para cumplir las normas de seguridad europeas y que sus promesas de rendimiento y cumplimiento sean confirmadas por terceros independientes; y en tercer lugar, Gaia-X representa una solución europea para el intercambio de datos conforme al GDPR (Reglamento General de Protección de Datos). Queda por ver hasta qué punto Gaia-X puede aumentar la confianza en una infraestructura en nube. Sin embargo, Alexej Voigt, de Danobat-Overbeck, confía en que las actitudes hacia las tecnologías de producción basadas en datos puedan cambiar muy rápidamente, y cree que la sostenibilidad podría convertirse en el principal motor en este sentido. Por último, la digitalización también hace que el consumo de energía relacionado con la producción sea transparente y permite la evaluación comparativa de diferentes procesos de producción. “Esto podría suponer un gran paso hacia el cálculo de la huella de carbono del producto en todos los ciclos de vida”, afirma Voigt, “y contribuir así de forma decisiva a promover métodos de producción más sostenibles”.
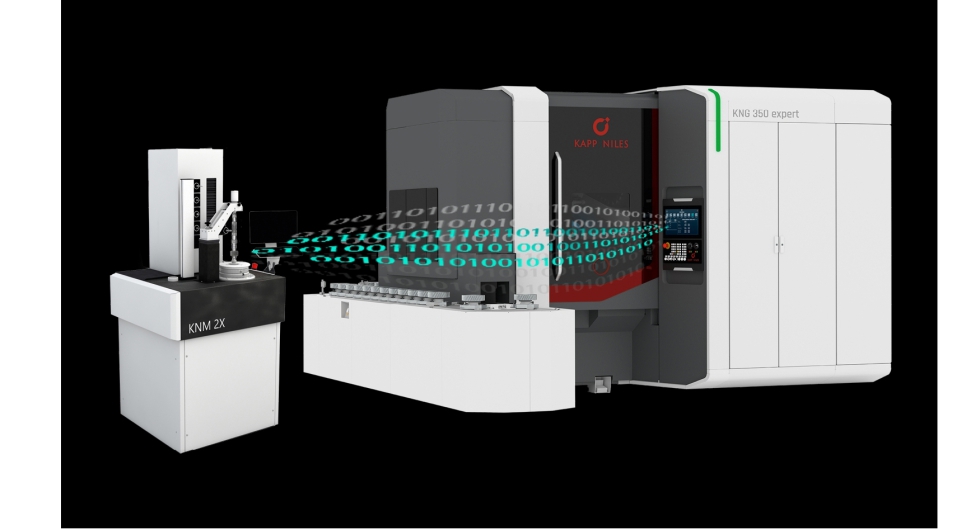