DZ 12K S Magnum: un solo equipo para el mecanizado completo
16 de noviembre de 2010
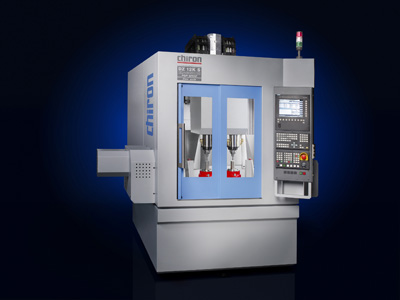
Comparado con estrategias de fabricación multietapa, una significativa ventaja del mecanizado de 5 ejes radica en la mejora de la calidad superficial y de la precisión geométrica. Los sistemas de medida directa de recorrido en todos los ejes son equipamiento estándar en todos los centros de mecanizado de 5 ejes de Chiron. Al utilizar centros de mecanizado de doble husillo junto con mesa rotativa de 2 ejes de inclinación y modernas herramientas de altas prestaciones, los usuarios obtienen múltiples aumentos de rendimiento.
La iniciativa de desarrollar DZ 12K S Magnum cinco ejes vino de clientes de Chiron en el ámbito de proyectos llave en mano que requieren una solución compacta capaz de soportar productividades punta con los mínimos requisitos de suelo y, que como sistema completo, funcionen de forma fiable y energéticamente eficiente.
Dirk Prust, director de Ventas, Tecnología y Servicio de Chiron-Werke GmbH & Co KG, Tuttlingen señala que: “La tendencia hacia series de piezas más complejas continua. Con el mecanizado de 5 ejes, puede alcanzarse precisión más alta, ya que no se requiere volver a fijar la pieza, por ejemplo. Para alcanzar las demandas de productividad de tales series de piezas, hemos implementado estos requisitos en un centro de mecanizado de doble husillo con buena relación coste-eficacia. DZ 12K S Magnum 5 ejes aporta las ventajas comprobadas de los centros de doble husillo Chiron, tales como los bajos requisitos de suelo ocupado y de personal, la reducción del coste por pieza a través de la reducción del tiempo de mecanizado y, en comparación con la solución de husillo único, doble productividad y un ahorro simultáneo del 30% del coste energético”.
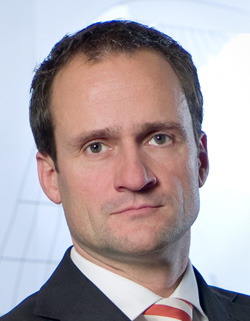
Otra prestación del nuevo centro de mecanizado es el asiento de herramienta reforzado a HSK-A 63, disponible inmediatamente de entrada para todos los Chiron serie 12. La mesa giratoria de 2 ejes de inclinación, de desarrollo y producción propios, destaca por su alta precisión y estabilidad extraordinaria. La conjunción del asiento de herramienta mejorado y el potente husillo con una velocidad máxima de 24.000 rpm permite alcanzar la más alta calidad superficial. Además, los ejes de giro accionados por motores de par, permiten operaciones simultáneas de giro a 1.000 revoluciones por minuto, ideales para completos mecanizados complejos. Los recorridos X, Y y Z son 550, 400 y 360 milímetros, espacio suficiente para posicionar y mecanizar piezas complejas de acero, fundición, aluminio o titanio. Las aceleración axiales son 10, 15 y 15 metros por segundo al cuadrado, y las alimentaciones rápidas en todos los ejes lineales alcanzan un máximo de 75 metros por minuto. La máquina también está preparada para automatizar con robot mediante el módulo estándar FlexCell Uno.
Tecnología y datos
- Recorrido (X - Y - Z): 550 - 400 - 360 mm
- Aceleración (X - Y - Z): hasta 10 - 15 -15 m/s2
- Marcha rápida: 75 m/min
- Velocidad de husillo: hasta 24.000 rpm
- Velocidad del eje A/C: 50/200 rpm
- Giro (eje C): hasta 1.000 rpm
- Margen de inclinación NC: ±120º/±360º
- Número de herramientas: 2x16/2x42/2x70
- Asiento de herramienta HSK-A 63
- Capacidad de fresado en acero St 60: 2x150 cm3/min
- Capacidad de taladrado en acero St 60: 2x Ø25 mm
- Capacidad de roscado: 2xM20
- Tiempo de cambio de herramienta: 0,9 s, aprox.
- Tiempo de viruta a viruta: 2,4 s, aprox.
- Precisión: 0,002 mm
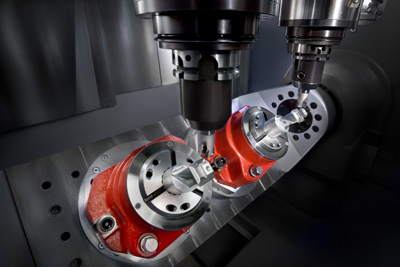