Recubrimientos multicapa de níquel químico como alternativa al cromo duro hexavalente
Los recubrimientos multicapa de níquel químico se han situado como una de las alternativas más cercanas para lograr una sustitución efectiva del cromado duro hexavalente para aplicaciones ingenieriles.
La deposición química de metales (ENP por sus siglas en inglés, Electroless Nickel Plating) es un proceso de deposición de capas metálicas en ausencia de corriente eléctrica, donde la reducción del catión metálico está asistida por un agente reductor, presente en la misma disolución, parte del cual se incorpora al recubrimiento dando lugar a una aleación metálica.
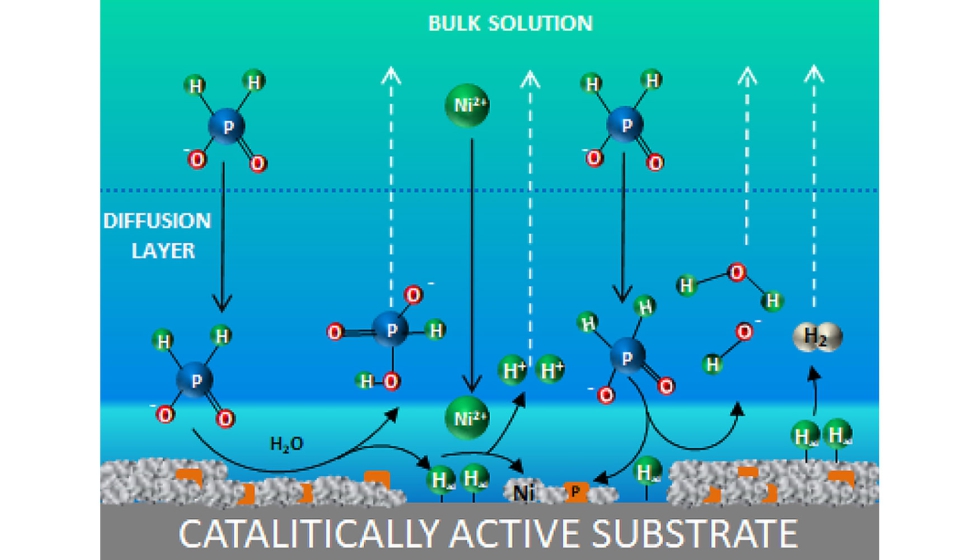
Entre los diferentes procesos de deposición química de metales, la de níquel es, con enorme diferencia, la que ha encontrado una mayor implantación industrial en un amplio abanico de aplicaciones ingenieriles. Como se puede observar en la siguiente figura, el níquel químico ha sido un proceso estudiado en profundidad y con un marcado impacto industrial, como se desprende del elevado número de artículos publicados en revistas de investigación, así como de patentes depositadas sobre este proceso.
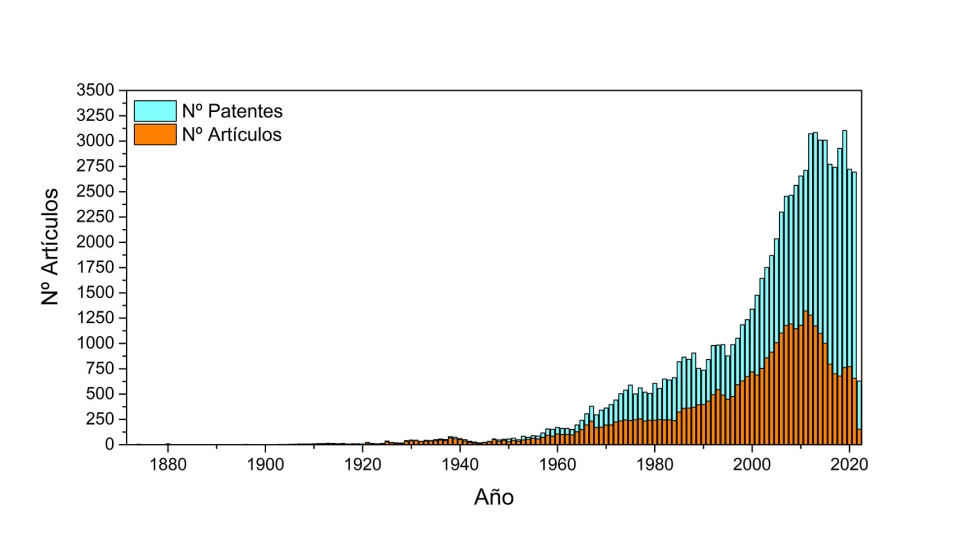
Una de las principales características de los procesos de deposición química, frente a los procesos asistidos por corriente, es la distribución homogénea de espesores independientemente de la geometría de la pieza a recubrir. Otras características destacables de este proceso son la posibilidad de aplicarlo tanto sobre sustratos conductores como dieléctricos, la facilidad para incorporar materiales de refuerzo en forma de nano/micro partículas así como la modulación de las propiedades de los recubrimientos en función de su composición.
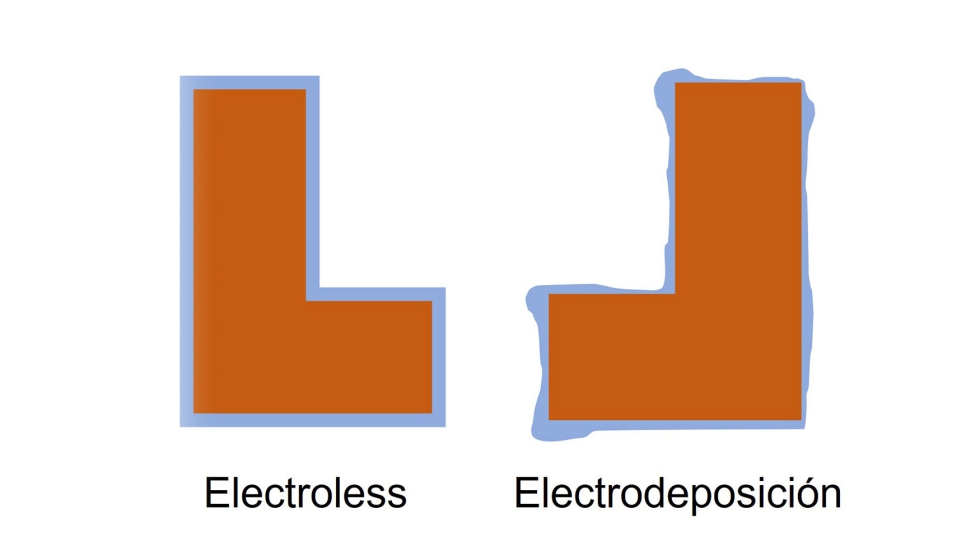
La mayor parte de los procesos industriales de níquel químico funcional emplean hipofosfito de sodio como agente reductor, dando lugar a aleaciones Ni-P. Así, existen 3 grandes grupos de recubrimientos de níquel químico en función de su contenido en fósforo, cada uno de ellos con unas propiedades claramente diferenciadas del resto:
- Ni-P de bajo contenido en P (1-4 wt.% P): presentan una estructura microcristalina dando lugar a recubrimientos de alta dureza (± 900 Hv) y elevada resistencia al desgaste. Presentan una baja resistencia a la corrosión en medio ácido, sin embargo, son muy resistentes a la corrosión en medio alcalino.
- Ni-P de medio contenido en P (5-9 wt.% P): Presenta una resistencia a la corrosión y propiedades mecánicas a medio camino entre los recubrimientos de alto y bajo contenido en P.
- Ni-P de alto contenido en P (10-12 wt.% P): Su naturaleza amorfa le confiere una excelente resistencia a la corrosión (≥ 1000h NSS) pero una dureza y resistencia al desgaste moderada.
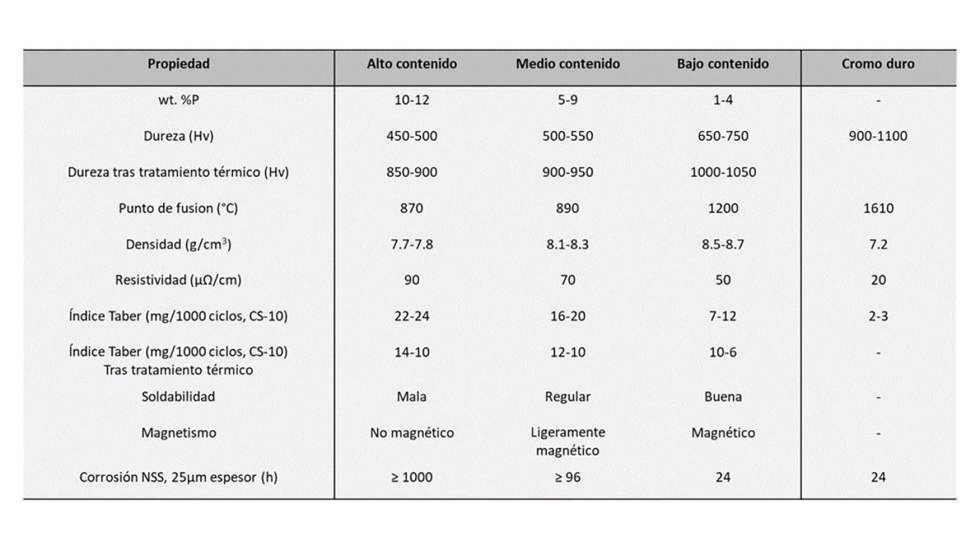
En todos los casos es posible incrementar la dureza de los recubrimientos mediante la aplicación de un tratamiento térmico adecuado, llegando a alcanzar valores de dureza de hasta 1.100 Hv, similares a las del cromo duro hexavalente. Esto ocurre como consecuencia, por un lado, de la recristalización de la matriz metálica de níquel y, por otro, por la precipitación de fosfuros de níquel (NixPy) que provocan un endurecimiento por precipitación, alcanzando los valores de dureza mencionados anteriormente. No obstante, esta mejora en las propiedades mecánicas, asistida por el tratamiento térmico, conlleva una disminución drástica de la resistencia a la corrosión que, sin embargo, es del mismo orden o superior a la aportada por el cromo duro, tal como se puede observar en la tabla 1.
Las excelentes prestaciones de los recubrimientos de níquel químico, así como la versatilidad del proceso de deposición, lo sitúan como una de las alternativas más directas a los recubrimientos de cromo duro. Estos, han sido la opción prioritaria para la mejora de las prestaciones de los materiales sobre los que se aplica, debido a sus excelentes propiedades mecánicas. Sin embargo, estos procesos emplean cromo hexavalente en su formulación, el cual es un reconocido agente carcinógeno y mutagénico, motivo por el cual su uso está sujeto a autorización por parte de la agencia química europea (ECHA) al estar incluido en el anexo XIV del reglamente REACH (por sus siglas en inglés, Registration, Evaluation, Authorisation and Restriction of Chemicals). La prohibición definitiva para su uso a nivel industrial se sitúa en 2024, motivo por el cual urge encontrar alternativas viables, sostenibles y maduras a nivel industrial que permitan lograr una sustitución efectiva del cromo hexavalente en el sector de los tratamientos superficiales.
Los procesos de níquel químico han evolucionado a lo largo de su historia adecuándose a las distintas normativas medioambientales en vigor, especialmente aquellas relacionadas con el uso de metales pesados tales como la RoHS (Restriction of Hazardous Substances), ELV (End of Life Vehicle) y REACH. Las formulaciones de níquel químico son soluciones multicomponente, que requieren de un control analítico continuo, tanto para asegurar las prestaciones de los recubrimientos como para aumentar la vida útil de los propios electrolitos. Entre los componentes principales de una formulación se encuentran las sales de níquel, el reductor, los agentes complejantes, los estabilizantes, tampones de pH, surfactantes, etc. En estas formulaciones se combinan tanto sustancias orgánicas como inorgánicas, en un amplio rango de concentraciones, que es necesario controlar continuamente.
En los últimos años, Cidetec Surface Engineering se ha dotado de instalaciones singulares para el desarrollo y control de procesos de niquelado químico en sus instalaciones. Así, cuenta con plantas piloto para el escalado preindustrial de nuevos procesos de níquel químico y con diferentes equipos de monitorización de electrolitos para lograr un control total de los mismos durante el proceso de deposición, actuando sobre el electrolito en caso de que alguno de sus componentes presente desviaciones respecto a su valor óptimo fijado. Este equipamiento permite a Cidetec Surface Engineering cubrir toda la cadena de desarrollo y control de proceso, desde los estadios iniciales de la investigación de proceso a escala laboratorio hasta su potencial implantación industrial.
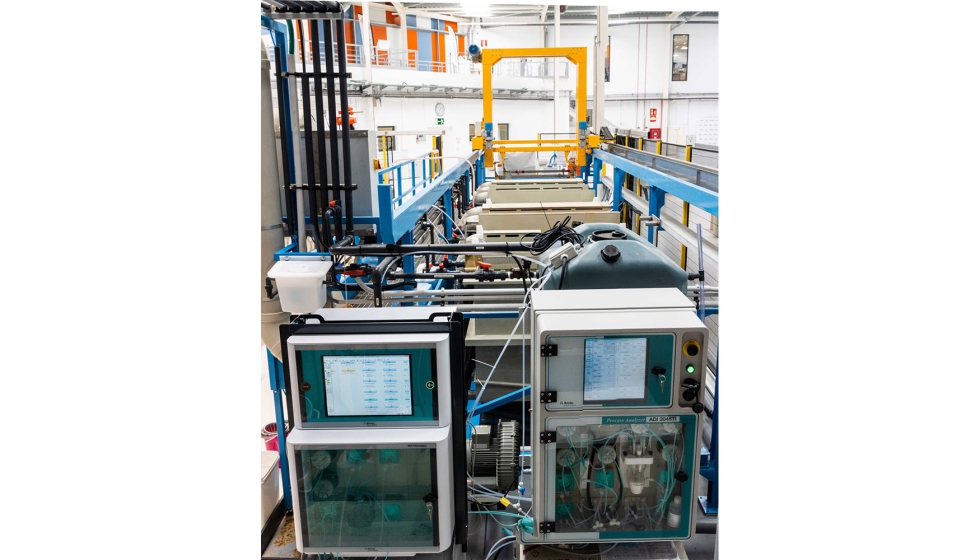
En este sentido, Cidetec Surface Engineering ha venido trabajando en el desarrollo de nuevos recubrimientos multicapa para la mejora de las propiedades mecánicas y de la resistencia a la corrosión de recubrimientos de níquel químico. Como puede verse en la siguiente imagen, los recubrimientos multicapa permiten, mediante la combinación de diferentes capas metálicas en el mismo recubrimiento, potenciar la funcionalidad de estos.
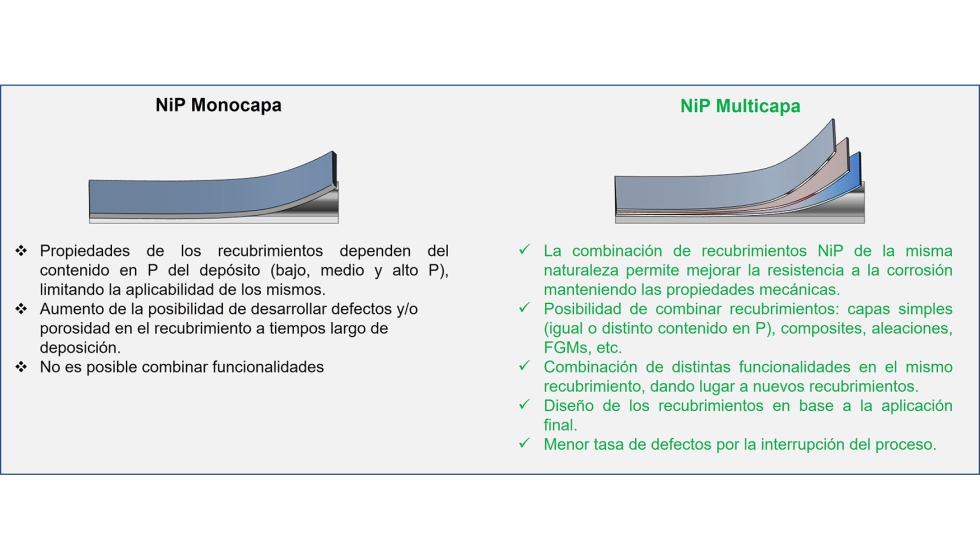
Incluso combinando recubrimientos de la misma naturaleza, la estrategia multicapa presenta distintas ventajas relacionadas con la generación de interfases artificiales como consecuencia del proceso de deposición. De esta forma, los estudios llevados a cabo por Cidetec Surface Engineering sobre multicapas de bajo contenido en P revelaron que, respecto a los recubrimientos monocapa convencionales, las multicapas de níquel químico son capaces de retrasar el avance de la corrosión. Este efecto es más acusado después de someter a las piezas a tratamiento térmico, ya que los recubrimientos multicapa son capaces de proteger efectivamente el sustrato metálico sobre el que se aplican ya que las distintas capas que conforman el recubrimiento van exfoliándose de manera controlada al exponerse al ambiente corrosivo. En el caso de los recubrimientos monocapa, al no contar con estas barreras artificiales, su resistencia a la corrosión disminuye llegando incluso a corroer el material base durante el ensayo.
Adicionalmente, esta estrategia de producción de recubrimientos tiene un claro impacto también cuando se somete a los recubrimientos a la acción combinada de desgaste y corrosión, condiciones de operación habituales en muchas aplicaciones ingenieriles. De esta forma, una investigación reciente de Cidetec Surface Engineering mostró como las multicapas presentan un volumen de desgaste 3.5 veces inferior al de recubrimientos monocapa equivalentes. Esta mejora está relacionada también con la presencia de las interfases artificiales creadas durante el proceso de deposición. Estas, son capaces de incrementar la capacidad de carga de los recubrimientos evitando daños en los mismos y disminuyendo la deformación plástica de la capa al someterla al esfuerzo mecánico, mejorando por tanto su comportamiento durante los ensayos.
Sin embargo, para lograr una sustitución efectiva de los recubrimientos de cromo duro por parte del níquel químico es necesario ir más allá en el desarrollo de este tipo de recubrimientos, bien a partir de nuevas arquitecturas de capa que permitan mejorar las prestaciones de los recubrimientos y/o mediante el empleo de materiales de refuerzo que incrementen sus prestaciones. Recientemente, Cidetec Surface Engineering, junto con Elcho, Chemplate Materials y la empresa portuguesa Smallmatek; ha participado en el proyecto True-Replace ‘Trustful and eco-friendly replacement to hexavalent hard chrome’ perteneciente a la convocatoria Eurostars-2 (ID proyecto: 113340), cuyo objetivo es la búsqueda de alternativas a los recubrimientos de cromo duro hexavalente mediante el desarrollo de nuevos recubrimientos multicapa de níquel químico, con y sin partículas de refuerzo (PTFE, SiC) en su estructura. Estos desarrollos, se dirigen al sector aeronáutico y de automoción ya que sus componentes están sometidos a exigentes condiciones de operación requiriendo una alta resistencia a la corrosión y unas excelentes propiedades mecánicas.
El proyecto True-Replace ha abordado el desarrollo completo del proceso de deposición, comenzando por el pretratamiento de los diferentes materiales base empleados. En el caso de las aplicaciones dirigidas al sector de automoción el material seleccionado fue acero de bajo contenido en carbono (AISI 1010) mientras que aquellos desarrollos enfocados a la industria aeronáutica se han realizado sobre acero de alta resistencia (300M). Estos desarrollos han estado basados en procesos habitualmente empleados en la industria galvánica, siendo optimizados para los materiales seleccionados.
Uno de los principales resultados del proyecto ha sido el desarrollo de una formulación de níquel químico de bajo contenido en P. Esta formulación, permite obtener recubrimientos Ni-P con valores de dureza en el entorno de los 900 Hv, muy similares a los aportados por lo recubrimientos de cromo duro hexavalente (1.000-1.100 Hv) y con un comportamiento frente a desgaste y corrosión muy similar. Esta formulación ha sido escalada en la planta piloto de CIDETEC Surface Engineering a un volumen de 250 litros, donde se están validando los recubrimientos producidos con la nueva formulación, así como los sistemas de monitorización acoplados a la instalación para el control de proceso.
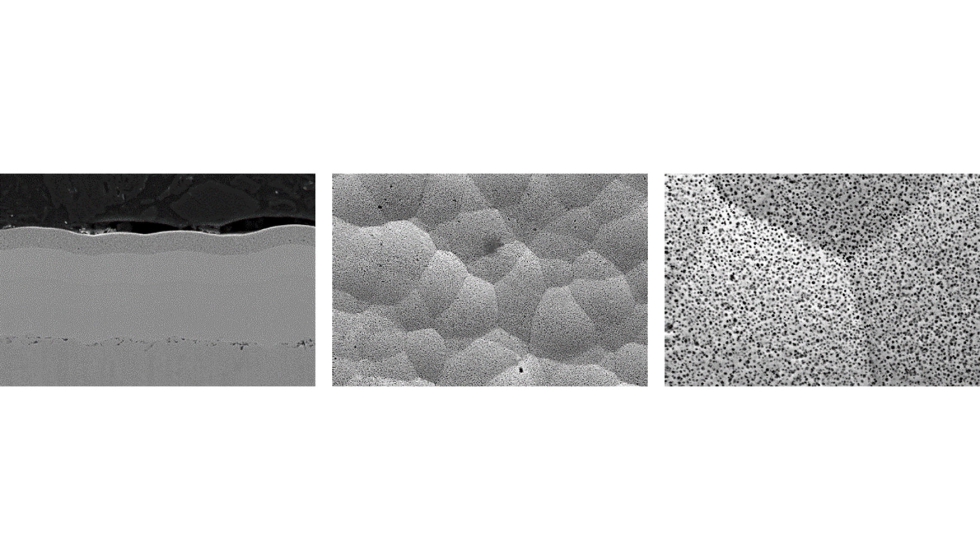
Adicionalmente, en el marco del proyecto, se han explorado diferentes combinaciones de recubrimientos, siempre basados en níquel químico, para lograr sistemas multicapa capaces de ofrecer unas prestaciones similares a los del cromo duro. En este sentido, se han desarrollado recubrimientos multicapa combinando recubrimientos de Ni-P de distinta naturaleza (bajo, medio y alto P) junto con capas finales Ni-P incluyendo partículas de PTFE. Tras la evaluación de las diferentes condiciones evaluadas, se seleccionó un sistema tri-capa, que incluye una capa de Ni-P-PTFE, como solución ganadora. Esta combinación de capas permite alcanzar valores de dureza en el entorno de los 900 Hv, y un comportamiento frente al desgaste similar a los aportados por el cromo duro. En el caso de la resistencia a la corrosión, los nuevos recubrimientos multicapa permiten alcanzar 2000h de resistencia en el ensayo de cámara de niebla salina, unos valores muy superiores a los aportados por el cromo duro el cual, debido a su microestructura fisurada, aporta una muy limitada resistencia a la corrosión.
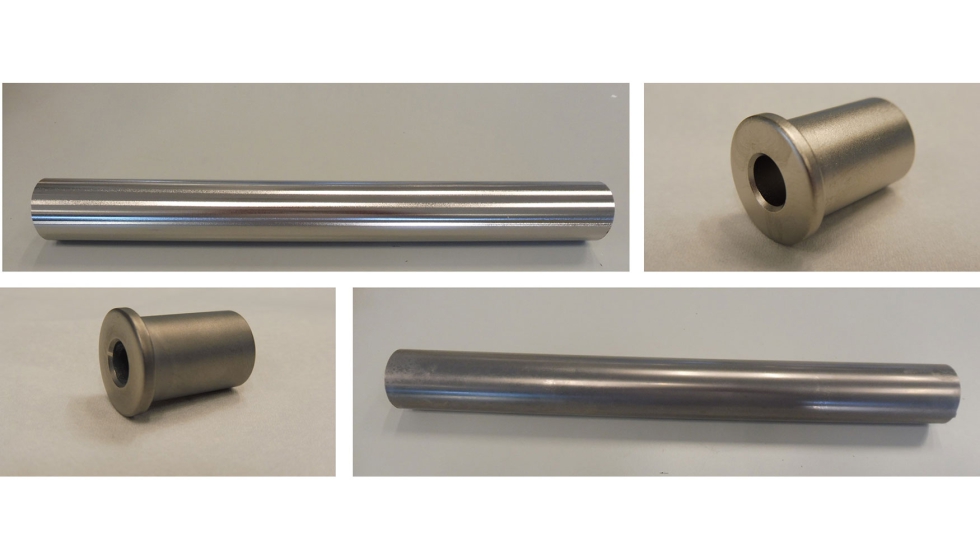
Cidetec Surface Engineering continúa apostando por los recubrimientos de níquel químico como alternativa a los basados en cromo hexavalente. Actualmente, cuenta con líneas de investigación sobre nuevas arquitecturas para los recubrimientos de níquel químico, estudiando nuevas combinaciones de materiales que, junto con la inclusión de distintos materiales de refuerzo, permitan mejorar las prestaciones funcionales de los componentes sobre los que se aplique, maximizando las aplicaciones potenciales de este tipo de recubrimientos funcionales.
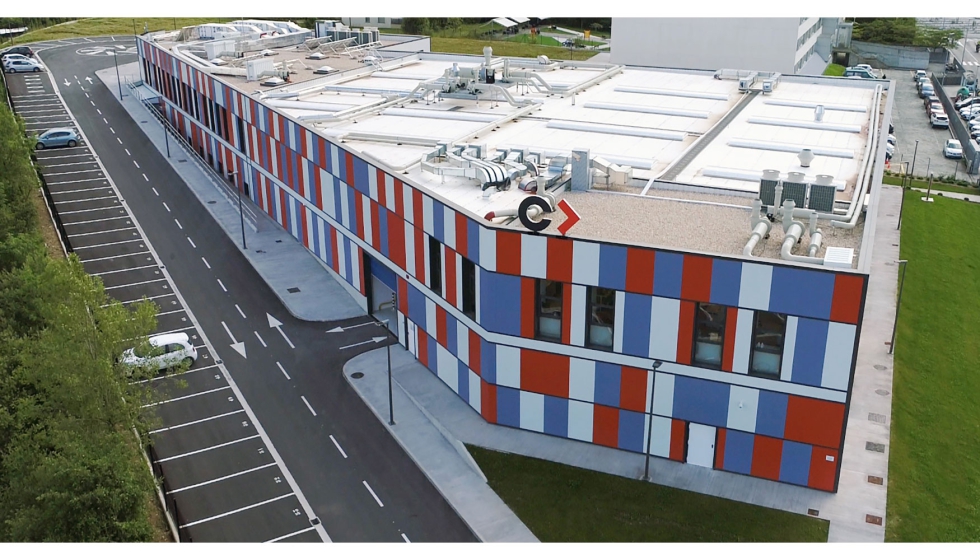
Figura 8. Instalaciones de Cidetec Surface Engineering. https://surfaceengineering.cidetec.es/en/our-offer/sustainable-surfaces-materials/reach-compliant-surfaces