Battenfeld-cincinnati, en la fabricación de suelos de calidad y agradables al tacto
Los revestimientos de suelo sintéticos hechos con Ceramin, de Classen, se han producido recientemente en una línea completa con una calandra Multi-Touch de Battenfeld-cincinnati. Classen, con sede en Kaisersesch, es el inventor y fabricante de los revestimientos de suelo sin PVC con el sello de calidad 'El Ángel Azul'. El material Ceramin está fabricado a base de polipropileno y está libre de sustancias nocivas, además es 100% reciclable y se produce con materiales reciclados.
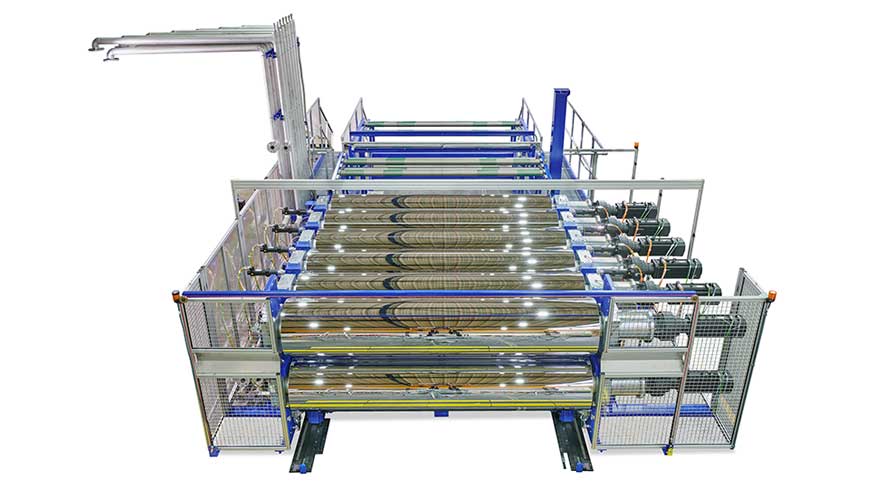
Los anteriores suelos de plástico basados en el PVC blando tienen el inconveniente de su escasa reciclabilidad y a veces son criticados por contener cloro, estabilizadores, ftalatos y otros plastificantes.
Las planchas de Ceramin están compuestas por un 60% de relleno mineral natural, un 39% de polímeros a base de polipropileno y un 1% de aditivos respetuosos con el medio ambiente y la salud. En el caso de los pavimentos sintéticos Classen, las planchas del núcleo están dotadas de una capa inferior, así como de una capa de imprimación y decoración con una capa superficial de tacto suave para una sensación agradable bajo los pies.
Ni que decir tiene que durante la producción del componente principal, es decir, el tablero de 2 a 5 mm de grosor, es importante que sea absolutamente plano, que tenga una superficie limpia y sin ondulaciones y que cumpla las tolerancias de grosor más estrictas. Esto es importante tanto para el procesamiento posterior como para el uso posterior como pavimento. La calidad ideal de la plancha hecha en la línea Battenfeld-cincinnati, firma representada por Comercia Douma, está garantizada sobre todo por la calandra Multi-Touch. El contacto constante entre el rodillo y la placa garantiza unas condiciones de calibración y refrigeración perfectas.
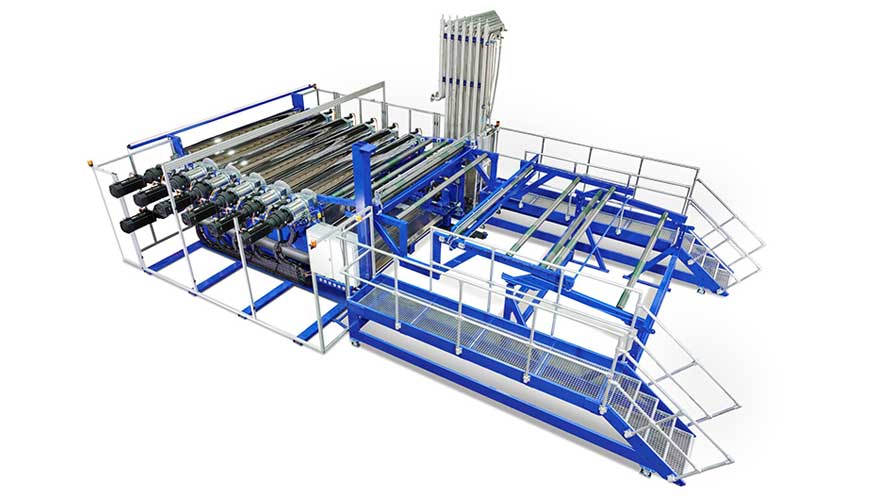
Las dos líneas instaladas hasta ahora en Classen están equipadas, después de la unidad de dosificación, con dos extrusoras de doble husillo de Leistritz Extrusion GmbH, que garantizan una perfecta homogeneización de hasta 8 toneladas de masa fundida por hora. A continuación, una boquilla especial hace que la película fundida entre en la calandra con una anchura de 2,6 metros. Aquí, dos rodillos realizan primero el precalibrado antes de que la plancha pase por varios rodillos para el poscalibrado. De este modo, la superficie de la placa está permanentemente en contacto con las superficies de los rodillos durante un largo periodo de tiempo, lo que se traduce en una perfecta estabilidad dimensional y unas excelentes propiedades ópticas. El sistema de corte se encuentra junto al arrastre. El sistema completo se controla a través del BCtouch UX, que se integra en el BDE del cliente. En un segundo paso del proceso, las placas se laminan con las distintas láminas de la manera descrita anteriormente y reciben una de las múltiples decoraciones individuales.