Monitorización de defectos y machine learning en la tecnología aditiva L-PBF
Para la fabricación de piezas empleando la tecnología L-PBF se parte de polvo metálico. Este polvo se deposita directamente en la cámara de fabricación, con atmósfera libre de oxígeno, y se distribuye en una capa homogénea, de un espesor de entre 15 y 90 µm dependiendo del material utilizado y la calidad de la pieza. Una vez distribuida la capa de polvo un láser, movido a muy alta velocidad por un escáner, funde el área especificada en el archivo y, tras esto, la plataforma de trabajo desciende el grosor de una capa para depositar la siguiente capa. El proceso se repite capa a capa, hasta que toda la pieza se fabrica. Los beneficios de esta tecnología son notables, ya que gracias a la fabricación capa a capa se pueden obtener geometrías complejas que son muy difíciles de obtener con tecnologías de fabricación convencionales.
Por otro lado, uno de los inconvenientes de esta tecnología son los defectos que se crean durante la fabricación. Estos defectos son muy variados y, en ocasiones, difíciles de monitorizar e inspeccionar mediante técnicas no destructivas, NDTs. Pero, para poder dotar al proceso de inteligencia y garantizar la calidad de las piezas, es necesaria una monitorización, sobre todo en los defectos no visibles por medio de técnicas NDTs.
Defectos comunes en piezas
Los defectos intrínsecos de la tecnología L-PBF son de diversa índole y tamaño. El hecho de que sean piezas fabricadas a partir de polvo de cierta granulometría por fusión focalizada, con gran cantidad de parámetros de fabricación (+ de 150), a muy alta velocidad (hasta 7.000 mm/s), punto a punto, línea a línea, área a área, capa a capa… dota a la pieza la posibilidad de tener defectos muy variados. A continuación, se presenta una clasificación de defectos que son motivo de que la pieza no obtenga la calidad necesaria en el componente fabricado:
- Porosidad: Este tipo de defecto es uno de los más problemáticos en la tecnología L-PBF ya que para la mayoría de aplicaciones se requieren piezas completamente densas y libres de poros, debido a que los poros disminuyen las prestaciones mecánicas de las piezas finales. Además, debido a su tamaño, son defectos que si son localizados son muy difíciles de inspeccionar. En algunas ocasiones los poros pueden aparecer por no tener ajustados correctamente los parámetros y trayectorias de fabricación. Si la densidad de energía aplicada para la fusión del material es demasiado baja o las trayectorias definidas en la pieza no llegan a solaparse correctamente, es posible que se creen zonas sin fundirse completamente y aparezcan poros, normalmente de gran tamaño. Esta porosidad es conocida como ‘lack of fusion’ o ‘falta de fusión’ (figura 1a). Por el contrario, si la densidad de energía es demasiado elevada, la profundidad de material fundido es excesiva y puede que quede gas atrapado en este fundido, generando así la porosidad denominada ‘key-hole’, ‘over-melting’ o ‘sobrecalentamiento’ (figura 1b). Pero, debe de mencionarse que aun ajustando correctamente los parámetros pueden aparecer poros esféricos de pequeño tamaño (<50µm), debido a pequeñas burbujas de gas atrapadas en el baño fundido. Este tipo de porosidad es inherente al proceso y es necesario controlarla para obtener piezas válidas. Normalmente es una porosidad aceptada hasta cierto nivel en el que el pequeño cambio de densidad no afecte a las propiedades mecánicas del material.
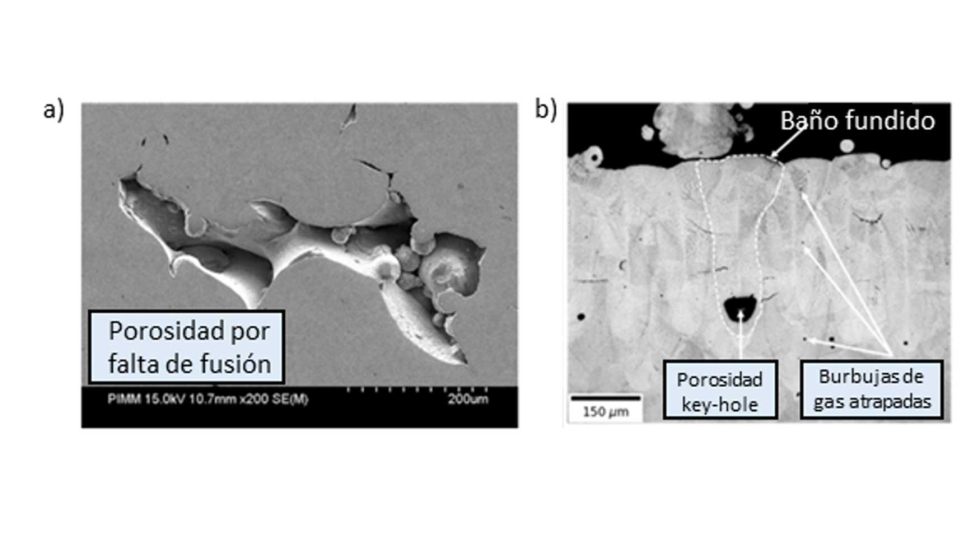
- Rugosidad: La rugosidad se presenta como otro gran reto de la tecnología L-PBF, ya que al igual que la porosidad una alta rugosidad puede llegar a afectar a las prestaciones mecánicas de la pieza y con ello limitar su aplicabilidad. Uno de los principales factores que afectan a la rugosidad es el ángulo de incidencia del láser respecto a la plataforma. En esta tecnología el láser está situado sobre la parte central de la plataforma y, por ello, incide completamente perpendicular a la plataforma únicamente en la parte central, mientras que en los bordes de la plataforma incide con cierto ángulo. Así, en la parte central de la plataforma el láser genera un trazo circular, mientras que en los extremos este círculo se distorsiona abarcando un área mayor. Sin embargo, al emplear los mismos parámetros de fabricación en toda la plataforma, la energía aplicada es la misma independientemente al tamaño del área a fundir. Esto genera que en las zonas alejadas al centro la energía aplicada no sea capaz de fundir por completo el área a fundir, quedando por ello partículas parcialmente adheridas a la superficie o patrones de fundido que demuestran la distorsión del lecho fundido. En la figura 2a se muestra el acabado superficial de una pieza fabricada en el centro de la plataforma junto al acabado de una fabricada en el borde de la plataforma (figura 2b), donde puede apreciarse la distorsión del baño fundido.
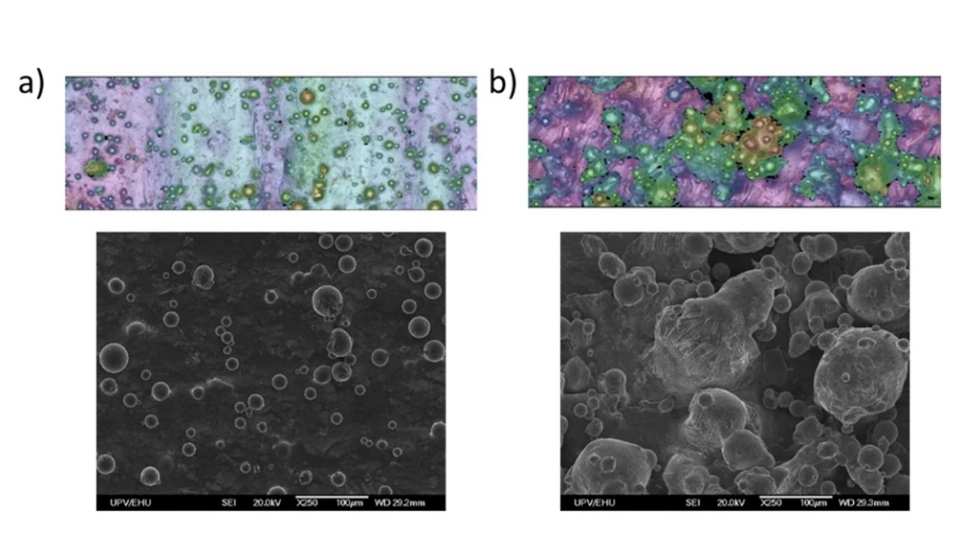
- Tensiones residuales y rotura de la pieza: La fase de solidificación y de enfriamiento de las capas generan tensiones residuales en la pieza que generan deformaciones. Si las tensiones residuales son superiores a las tensiones de rotura del material, dichas tensiones son aliviadas en forma de rotura, dando lugar al fenómeno ‘crack’. Estas roturas se pueden observar entre capas cuando la soldadura inter-capa no es lo suficientemente sólida para soportar dichas tensiones residuales. En la figura 3 se observa un fallo por rotura entre capas donde la unión entre los soportes y la pieza no ha sido capaz de aguantar las tensiones residuales generadas durante el proceso.
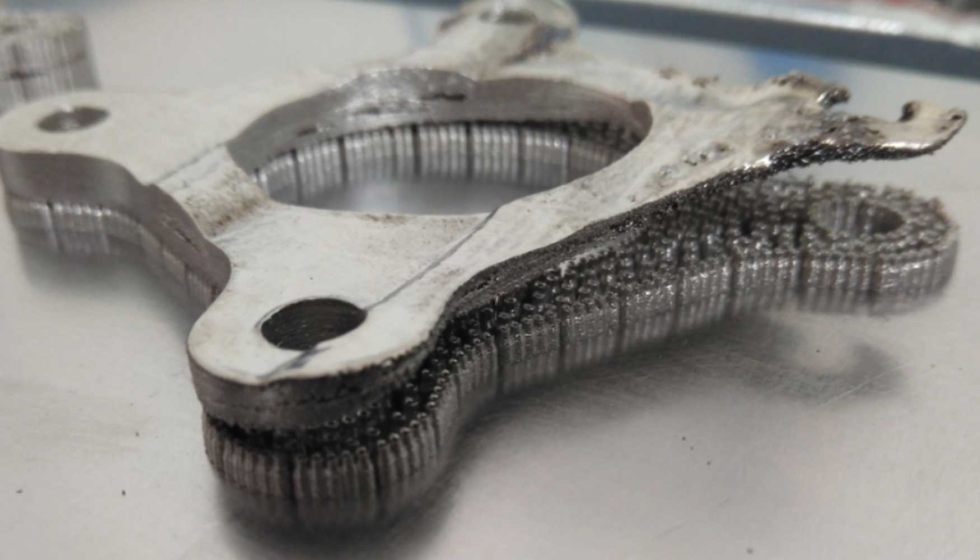
- Contracción de la geometría: Las piezas fabricadas por L-PBF padecen una contracción principalmente por dos motivos: la solidificación del material fundido y el gradiente térmico durante el enfriamiento. Una forma de mitigar este problema y lograr piezas con dimensiones requeridas es sobredimensionar la pieza por un factor. Pero, esta contracción, además de causar que la pieza final pueda no ajustarse a las tolerancias exigidas puede acarrear otros problemas; como pueden ser deformaciones sobre todo en esquinas con elevado voladizo o en el caso de transiciones de secciones muy bruscas.
Debido a estos defectos presentes en las piezas fabricadas mediante la tecnología L-PBF y a las altas exigencias exigidas por industrias cómo la aeronáutica, deben someterse a exhaustivos controles de calidad, que en algunos casos cómo la porosidad, puede que no sean detectables. La monitorización nace como una alternativa a dichos controles de calidad, ya que gracias a una correcta monitorización in-process se pueden llegar a detectar gran parte de los defectos generados en la pieza.
Monitorización en máquinas de fabricación aditiva por L-PBF
La monitorización se basa en la captación de las señales provenientes del proceso de fabricación, como podrían ser las propias emisiones del baño fundido, las trayectorias del escaneo, la vibración que sufre el elemento encargado de arrastrar el polvo… Los sensores o dispositivos que se emplean para captar las señales mencionadas anteriormente varían en función del objetivo y del tipo de defecto a monitorizar. Además, algunos parámetros intrínsecos del proceso de L-PBF dificultan la colocación y adquisición de datos de este proceso. A continuación, se resumen algunos puntos a tener en cuenta durante la monitorización del proceso L-PBF:
- Se trata de un proceso láser. Si el sensor se introduce en la cámara de trabajo debe de aguantar hasta 70-100 °C y, si se quiere realizar una monitorización externa sin contacto, debe de tenerse en cuenta que el cristal de visión a la cámara de trabajo anula algunas longitudes de onda para que, por seguridad, los reflejos del láser no dañen los ojos de la persona que se encuentra mirando la fabricación.
- Se trabaja en atmósfera inerte y, en algunas máquinas, se realiza el vacío para mejorar la inertización. Si el sensor se introduce dentro de la cámara, además de aguantar la presión de vacío (1.000 mbar), se debe de garantizar que por la salida de los cables no surjan pérdidas de vacío o entre oxígeno durante el proceso.
- La herramienta es un haz láser movida por espejos a muy alta velocidad: monitorización coaxial del a zona fundida. Para monitorizar la zona fundida con precisión el sensor se debe de mover con el haz láser y deben de ser los mismos espejos que mueven el láser los que muevan las distintas señales de los sensores (hasta 7 m/s). Esta monitorización es de fotodiodos a distintas longitudes de onda coaxiales con el láser y se introduce directamente por los fabricantes de las máquinas. Es la única opción para monitorizar in-process el baño fundido y los defectos locales.
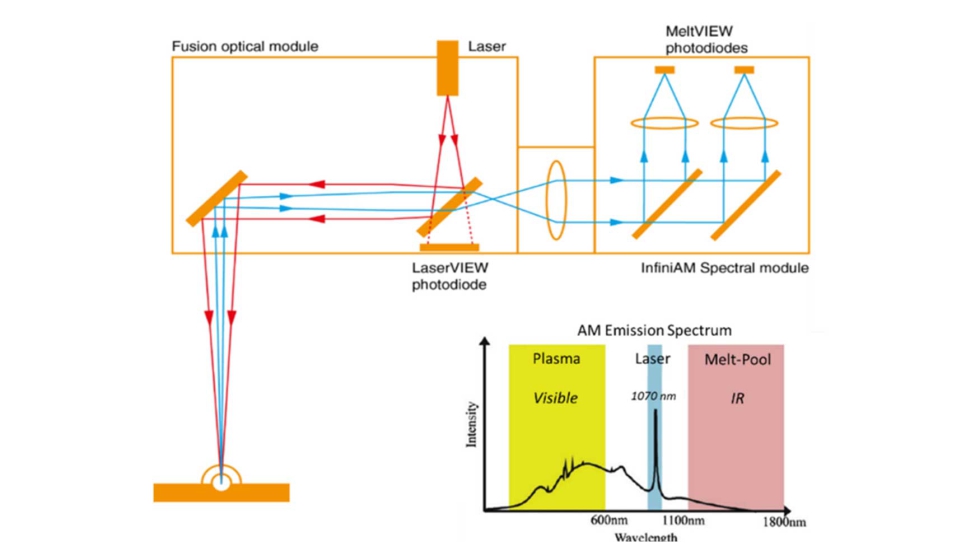
- Baja resolución en la monitorización no coaxial. La monitorización con cámaras termográficas/ópticas no coaxiales con el haz láser es para defectos macro, para una monitorización global de toda la capa. Hay que tener en cuenta que un dato común en este proceso es tener un baño fundido de entre 150 y 300 µm, y las dimensiones de trabajo por láser son de entre 400 y 900 mm2, lo que haría una resolución necesaria de la cámara de 2.000 x 2.000 píxeles para tener un único pixel en el baño fundido y, por otro lado, deberían de ser de alta frecuencia de adquisición de imágenes.
- La pieza se va creando durante la fabricación. Sensores sin contacto con la pieza. Es un proceso en el que la pieza se crea desde cero sobre una base metálica por lo que no se puede poner un sensor en contacto con la pieza ya que se va creando durante la fabricación. Si se quiere monitorizar con un sensor por contacto, cómo pueden ser las galgas extensiométricas o acelerómetros, se deben de colocar en la placa base o en otras zonas de la máquina, pero no en la pieza.
- Son fabricaciones largas y con un láser moviéndose a gran velocidad. Debe de tenerse en cuenta la gran cantidad de datos que se pueden generar en una fabricación para la monitorización offline y coaxial del proceso (hasta 500 GB por fabricación en archivos de texto)
Como se ha comentado, la monitorización puede realizarse de una forma global, en todo el lecho de polvo, para un defecto de pieza, un defecto macro, o de una forma local para defectos más localizados y de menores dimensiones, defectos micro. Entre las posibles opciones en dispositivos y sensores para la monitorización se encuentran las cámaras de alta velocidad, las cámaras termográficas, los fotodiodos, los acelerómetros, los sensores acústicos, etc.
Técnicas de machine learning
El objetivo de todos los dispositivos de monitorización es poder llegar a detectar errores en la pieza sin necesidad de llevar a cabo procesos destructivos o costosos. Pero estos procesos de monitorización generan gran cantidad de datos y, por ello, es crucial tener algoritmos inteligentes capaces de analizar todos los datos obtenidos para poder obtener información útil, comprensible por el usuario, y poder actuar en consecuencia.
Las técnicas de Machine Learning abren un nuevo campo puesto que dichos algoritmos facilitan el procesamiento de gran cantidad de datos. Se trata de una rama que se encuentra dentro de la Inteligencia Artificial (IA), y que se basa en el aprendizaje automático por medio de un algoritmo. Es decir, inicialmente se desarrolla un modelo con la capacidad de resolver un problema concreto, este modelo se va entrenando empleando gran cantidad de datos, así el modelo va aprendiendo de estos datos hasta que el modelo llega a ser capaz de hacer predicciones basadas en los datos. Con estas predicciones el sistema es capaz de actuar para corregir o, por otro lado, actuar cómo inspector in-process de la pieza y que entre dentro de la calidad requerida.
En la tecnología de L-PBF, se debe comentar que actualmente la mayoría de marcas comerciales integran monitorización coaxial y externa en la máquina, pero se está trabajando en dotar de inteligencia a esos datos monitorizados para poder relacionarlos con defectos no deseados y, todavía más a futuro, poder actuar sobre parámetros y conseguir eliminar los defectos durante la fabricación.
Los tipos de implementación de Machine Learning pueden clasificarse en distintas categorías tal y como se muestra en la figura 5.
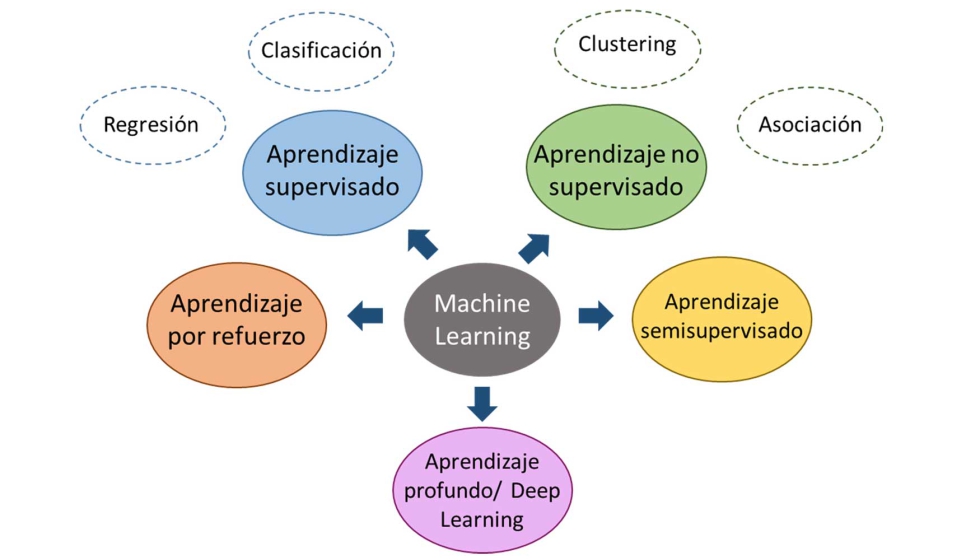
Aprendizaje supervisado: el algoritmo se entrena con un conjunto de datos etiquetados, que son introducidos por el usuario. El algoritmo puede ser de dos tipos, dependiendo del resultado que se desea, tal y como se muestra en la figura 8:
- Clasificación: Se emplea para clasificar los datos de entrada en distintas clases. Por ejemplo, un algoritmo de clasificación sería adecuado para clasificar la calidad de las piezas como ‘buena’ o ‘mala’. En la figura 6 puede apreciarse el diagrama de un algoritmo de clasificación.
- Regresión: Se emplea para predecir un valor numérico según los datos de entrada. Podría ser por ejemplo un algoritmo capaz de predecir la porosidad de la pieza fabricada.
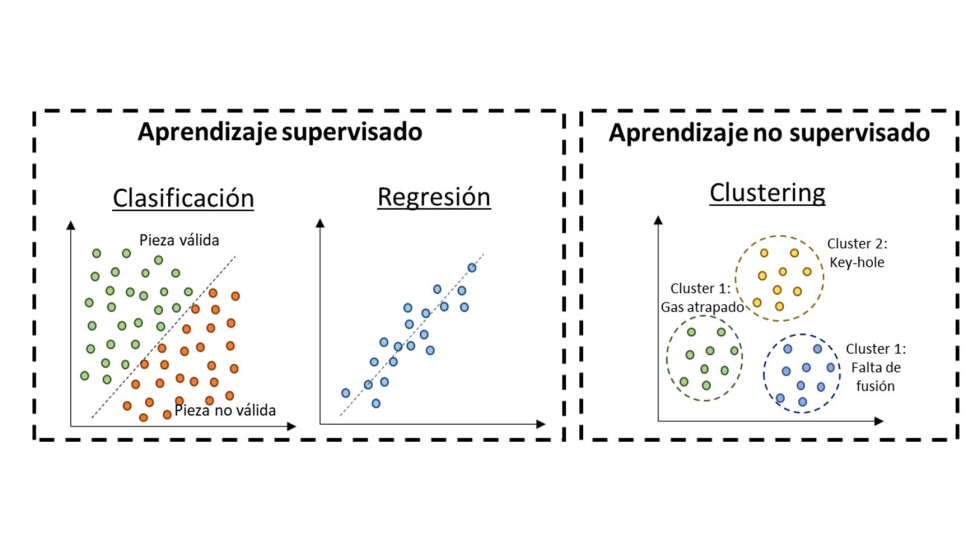
Aprendizaje no supervisado: En este caso el usuario no introduce directamente los datos de entrada, sino que el algoritmo aprende de datos o elementos no etiquetados, buscando patrones o relaciones entre ellos. En este caso también existen dos tipos de algoritmos principalmente:
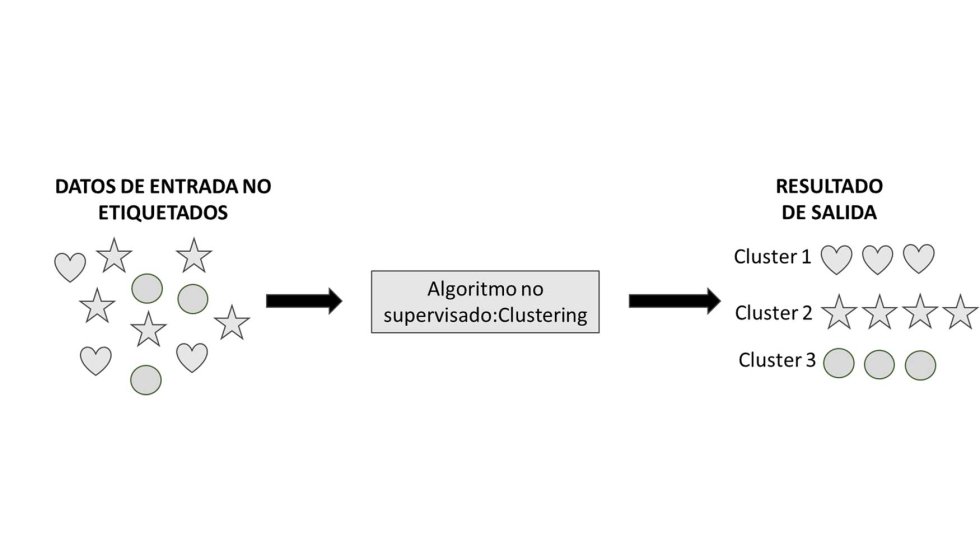
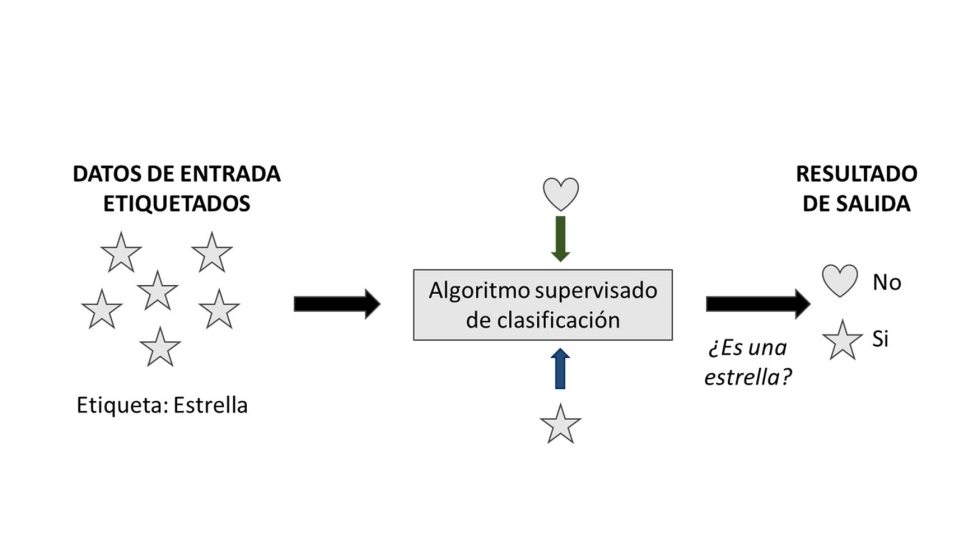
- Clustering: Clasifica en grupos los datos de salida, en la relación a los datos de entrada. Por ejemplo, podría tratarse de un algoritmo que se encarga en clasificar en grupos el tipo de porosidad de la pieza (Falta de fusión, key-hole…). El diagrama de este tipo de algoritmo puede verse en la figura 7 y el resultado de salida esperado en la figura 8.
- Asociación: El algoritmo se encarga en buscar relaciones entre los distintos datos. Por ejemplo, este tipo de algoritmo podría emplearse para detectar la relación que puede existir entre la porosidad de las piezas fabricadas y sus propiedades mecánicas.
Aprendizaje por refuerzo: este algoritmo nace para suplir las carencias de los otros dos tipos de algoritmos y cubrir las aplicaciones que estos no suplían. La singularidad de este algoritmo es que aprende en un esquema basado en ‘premios y castigos’ al interactuar con su entorno. Así, el algoritmo recibe una recompensa numérica cada vez que resuelve una acción con éxito, y el algoritmo trata de aprender a seleccionar las acciones que maximizan la recompensa acumulada. Un ejemplo de este tipo de algoritmo son los coches autoconducidos [4].
Aprendizaje semi-supervisado: combina el aprendizaje no supervisado y el supervisado. El aprendizaje semi-supervisado combina una pequeña o limitada cantidad del conjunto de datos etiquetados con una gran cantidad de conjunto de datos no etiquetados durante el entrenamiento del algoritmo. Este tipo de aprendizaje es beneficioso en las aplicaciones de fabricación aditiva, donde la obtención del conjunto de datos etiquetados es una tarea muy difícil.
Aprendizaje profundo/Deep Learning: por último, debe mencionarse el aprendizaje profundo. En este caso la maquina también aprende automáticamente analizando la gran cantidad de datos mediante estructuras de redes neuronales que pueden estar compuestas por varias capas dependiendo de la complejidad del modelo. Ejemplo de este modelo son los algoritmos de los asistentes virtuales [5].
Las técnicas de Machine Learning tienen muchas aplicaciones diferentes dentro de la tecnología L-PBF, entre otras: optimización de parámetros, predicción de propiedades de las piezas fabricadas, detección de defectos, predicción de calidad, control en lazo cerrado del proceso, control de la desviación geométrica de las piezas, estimación de costes… No obstante, existe algún que otro inconveniente. Los principales problemas son, el tamaño de los datos, la falta de etiquetas para entrenar los algoritmos y la falta de conocimiento a la hora de extraer las variables importantes de los datos para entrenar el algoritmo correctamente.
Machine learning en la tecnología L-PBF EN EL CFAA
El Centro de Fabricación Avanzada Aeronáutica, CFAA, es un centro mixto de la UPV/EHU y la Agrupación Empresarial para el desarrollo de Técnicas de Fabricación Avanzada en Aeronáutica, donde se desarrollan proyectos de investigación de gran interés industrial, aprovechando la sinergia generada entre la universidad, empresas y entidades públicas. Entre las tecnologías presentes en el centro se encuentra la tecnología Laser Powder Bed Fusion (L-PBF) que se trata de una de las tecnologías de fabricación aditiva metálica con más acogida industrial.
Uno de los retos actuales en la tecnología L-PBF es dotar a las máquinas de la sensorización adecuada para la correcta monitorización del proceso y que los datos recogidos, por medio de técnicas de Machine Learning, sean capaces de encontrar los defectos de las piezas durante la fabricación y, en medida de lo posible, sirvan para corregir esos defectos durante la fabricación o ser una manera fiable de etiquetar las piezas cómo no válidas, tener un método de inspección fiable basado en la monitorización del proceso. Esta monitorización y actuación sobre parámetros se está consiguiendo para el caso de defectos macro cómo el levantamiento de piezas o la falta de polvo en zonas por distintos defectos de fabricación, pero todavía hay un largo camino en la monitorización de defectos micro cómo es el caso de la porosidad debida a falta de fusión o sobrecalentamiento.
En el CFAA, junto con Renishaw y otras empresas socias del centro, se está trabajando en analizar los datos recogidos por monitorización coaxial en la nueva máquina disponible en el centro, la Renishaw RenAM500. Cómo se muestra en la figura 4, esta máquina recoge los datos coaxiales de 3 fotodiodos, con alta frecuencia de adquisición (cada 20 µs) y a distintas longitudes de onda para monitorizar el estado del láser y, por otro lado, señales del plasma y baño fundido que se crean durante la fusión del polvo metálico. Con estas señales cómo base se está trabajando en relacionarlas con distintos defectos del proceso, lack of fusion y over-melting, por medio de técnicas de Machine Learning. Así, mediante el filtrado específico de datos localizados dependientes del barrido del escáner, el entrenamiento de algoritmos de regresión junto con técnicas de clustering se está consiguiendo dar una probabilidad de fallo o porosidad localizada con datos no entrenados en el algoritmo. Actualmente se está trabajando en ajustar la probabilidad validando los resultados con piezas reales y obtener una etiqueta de fallo o no fallo en cada dato de la monitorización coaxial. Los primeros resultados de esta investigación se pueden observar en la siguiente figura donde se compara la porosidad en un corte de una probeta fabricada por L-PBF con los resultados de los datos de monitorización con las técnicas de Machine Learning introducidas.
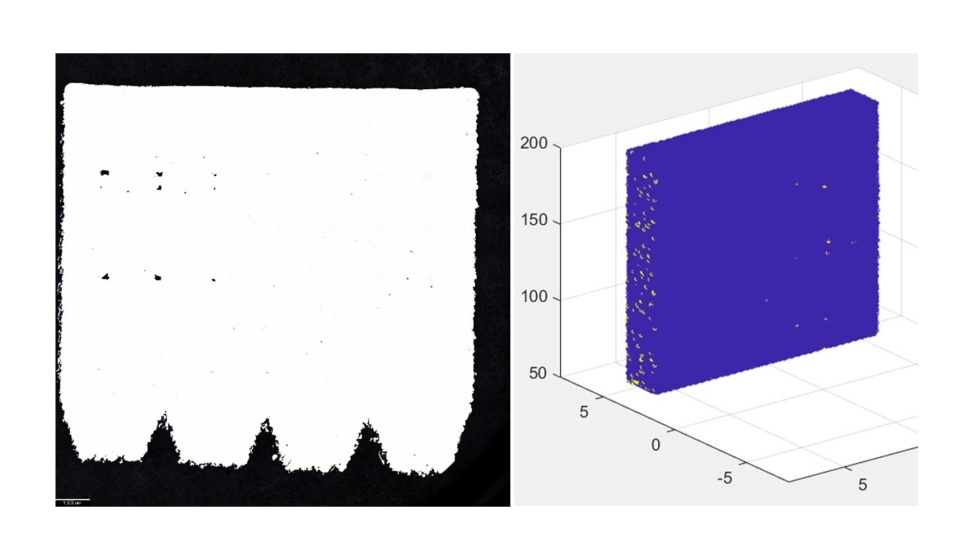
Referencias
[1] Thibaut de Terris, Olivier Andreau, Patrice Peyre, Frédéric Adamski, Imade Koutiri, Cyril Gorny, Corinne Dupuy. (2019), Optimization and comparison of porosity rate measurement methods of Selective Laser Melted metallic parts. Additive Manufacturing, 28, 802-813. https://doi.org/10.1016/j.addma.2019.05.035.
[2] S Sendino, S Martinez, A Lamikiz, F Lartategui, M Gardon, JJ Gonzalez. Analytical study of the melt pool distorsion in the Laser Powder Bed Fusion Process caused by the angle of incidence of the laser and its effect on the surface finish of the part. IOP Conf Ser Mater Sci Eng. 2021; 1193(1):012010 doi: 10.1088/1757-899X/1193/1/012010
[3] https://aprendeia.com/aprendizaje-no-supervisado-machine-learning/
[4] https://www.aprendemachinelearning.com/aprendizaje-por-refuerzo/