La impresión 3D realmente ha dejado huella durante la pandemia, ya que ha ofrecido a los fabricantes la solución ideal para facilitar un cambio inmediato en la producción
Uso de la impresión 3D para mejorar la resiliencia de la cadena de suministro y la flexibilidad de la producción
En tiempos de incertidumbre económica, la tecnología puede ser un activo muy valioso para reducir los riesgos y mantener la rentabilidad. Los recientes acontecimientos a nivel mundial han causado graves alteraciones en las cadenas de suministro y en las actividades de producción tradicionales, por lo que muchas empresas han tenido que revisar sus modelos de negocio y hacer cambios drásticos para garantizar su supervivencia. Con un futuro aún incierto, Andreas Langfeld, presidente de Stratasys para EMEA, señala el auge de la impresión 3D durante la pandemia y su idoneidad para las empresas como herramienta estratégica para solucionar las dificultades de la cadena de suministro y aumentar la flexibilidad de la producción. Aunque ha sido la reciente pandemia la que ha dado a conocer a muchas empresas las ventajas de la impresión 3D, Langfeld nos habla de algunas compañías visionarias que han integrado la tecnología en su modelo de negocio con gran éxito.
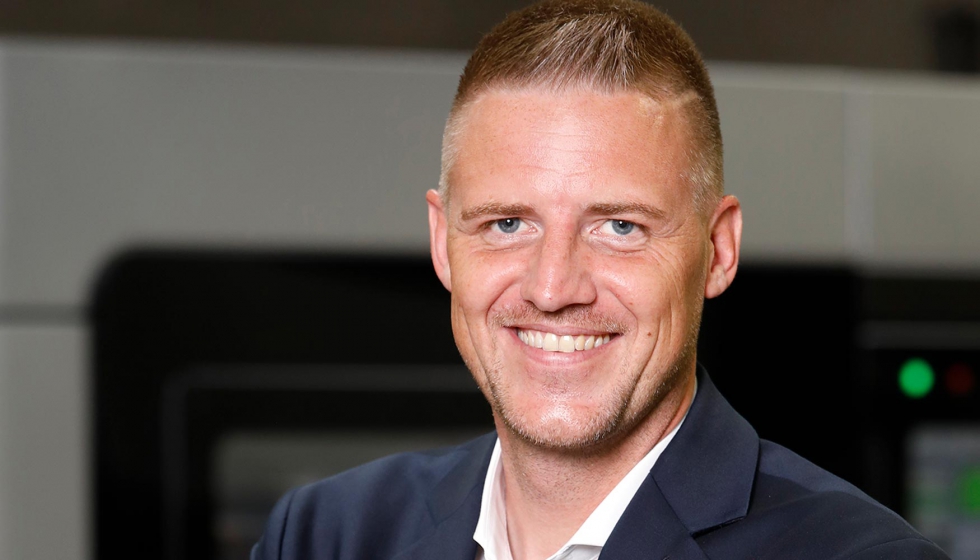
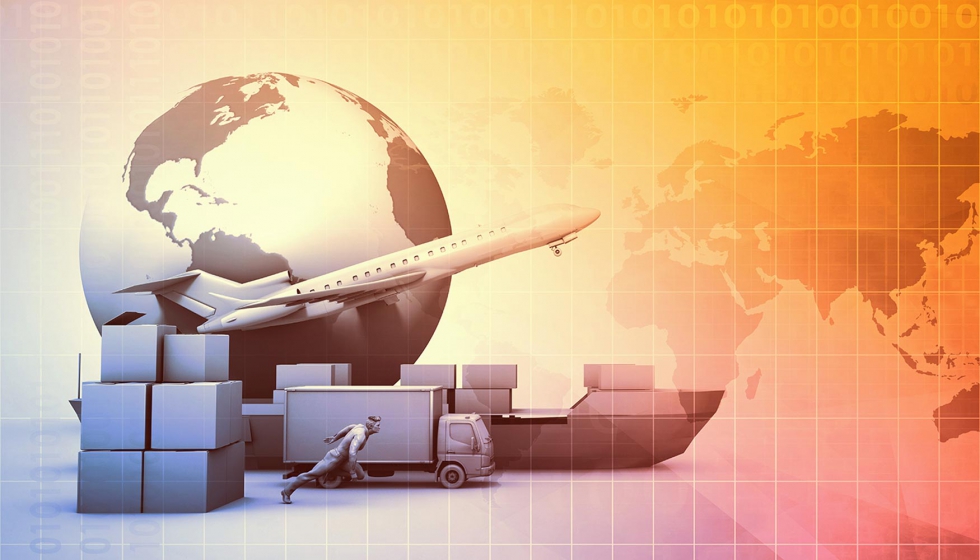
Existe una percepción real de que este es ahora el mundo en el que tenemos que aprender a trabajar con éxito. Con este nivel de incertidumbre que afecta a las empresas, las industrias y las economías, los responsables de fabricación y de cadenas de suministro buscan soluciones que proporcionen rapidez y adaptabilidad para acelerar o ralentizar la producción, cambiar de actividad e incluso trasladarse a nuevas ubicaciones. Todo ello ha centrado la atención en la impresión 3D.
Responder a la demanda
En cambio, la impresión 3D es como un motor eléctrico: solo hay que accionar un interruptor y está de inmediato a pleno rendimiento. En concreto, no se necesitan herramientas y una impresora 3D puede producir 10 cosas diferentes consecutivamente con la misma facilidad con la que fabrica 10 piezas idénticas. La impresión 3D ha sido un recurso esencial en la producción de pantallas de protección facial al permitir una producción rápida en función de la demanda, al tiempo que se producía un aumento en los volúmenes del proceso de moldeo por inyección.
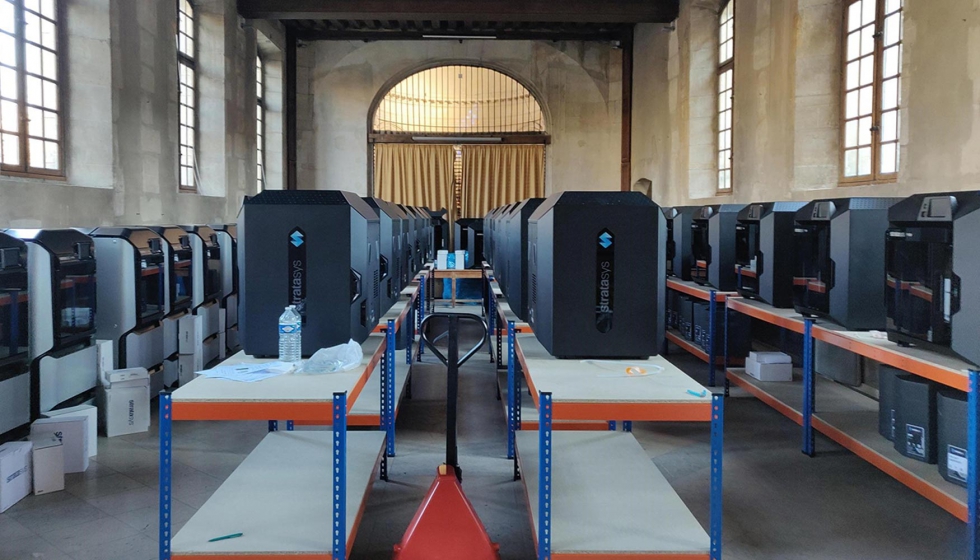
Dada la imposibilidad de seguir esperando a que sus proveedores fabriquen equipos médicos vitales de la manera tradicional, el University Hospital Trust (AP-HP) de París ha invertido en 60 impresoras 3D de la serie F123 para poder disponer in situ de capacidad de producción en función de la demanda.
En Francia, el University Hospital Trust (AP-HP) de París ha ido un paso más allá y ha invertido en 60 impresoras 3D de la serie F123 para poder disponer in situ de capacidad de producción en función de la demanda. Dada la imposibilidad de seguir esperando a que sus proveedores fabricasen equipos médicos vitales de la manera tradicional, el hospital tomó cartas en el asunto y desde entonces ha fabricado miles de piezas in situ utilizando sus impresoras 3D. Entre dichas piezas se incluyen pantallas de protección facial y mascarillas, bombas de jeringa eléctricas, equipos de intubación y válvulas para respiradores. Después de la crisis, las impresoras 3D se ubicarán en toda la red de hospitales de asistencia pública de París para contar con una capacidad de fabricación aún más repartida. Esto les permitirá reaccionar con mayor rapidez en caso de que se produzca otra oleada del virus u otra crisis en el futuro. Además, aparte de las situaciones de emergencia, la red de impresoras 3D estará disponible para satisfacer las necesidades de los hospitales locales de una producción de volúmenes pequeños de piezas, por ejemplo, modelos médicos personalizados para cada paciente utilizados para mejorar la atención sanitaria.
No solo productos médicos
En el ámbito industrial, muchos de nuestros clientes nos cuentan que si las herramientas de una línea de producción determinada se rompieran, se produciría una parada total de la línea de montaje. Siempre que la cadena de suministro sufre alguna alteración, la necesidad de herramientas de repuesto puede convertirse en un gran problema. Los fabricantes innovadores, como Deutsche Bahn, están reduciendo su dependencia de la cadena de suministro utilizando la impresión 3D para fabricar piezas de repuesto in situ, como y cuando se necesitan. Cuando se produjeron los confinamientos por la COVID-19 en toda Europa, la cadena de suministro de piezas de repuesto de la empresa se vio diezmada. Gracias a su capacidad de impresión 3D interna, Deutsche Bahn ha podido producir in situ varias de estas piezas de repuesto para trenes en las cantidades exactas necesarias para garantizar el cumplimiento de los calendarios de producción.
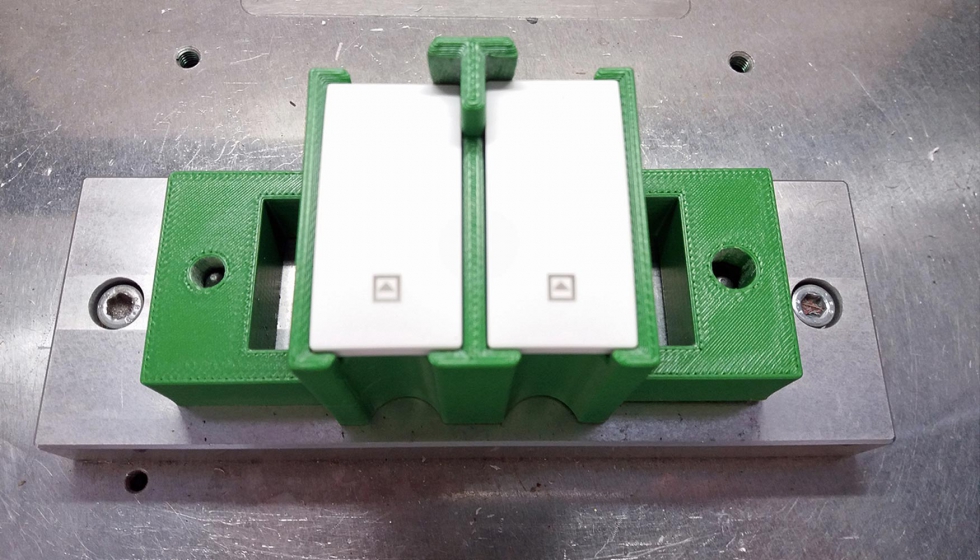
No es solo una solución para los malos tiempos...
Por ejemplo, el gigante del transporte Siemens Mobility lleva varios años implantando con éxito la impresión 3D para fabricar herramientas y piezas de repuesto en diferentes centros. Su centro de mantenimiento digital RRX en Alemania, encargado del mantenimiento y servicio de más de 100 trenes al mes, ha digitalizado por completo sus operaciones. Gracias a un inventario digital de toda la empresa, Siemens Mobility puede reaccionar rápidamente a los cambios en las solicitudes de mantenimiento imprimiendo en 3D herramientas esenciales y piezas de repuesto para sus trenes in situ, en función de las necesidades. Es importante señalar que este cambio en el modelo de negocio ha eliminado por completo su dependencia de proveedores externos. Ahora Siemens Mobility solo fabrica lo que necesita, sin necesidad de almacenamiento. El resultado ha sido un gran ahorro de tiempo para la empresa, de hasta un 95% en algunas piezas.
Y Siemens Mobility no es la única; otras empresas con visión de futuro adoptaron la fabricación aditiva a nivel estratégico mucho antes del azote de la pandemia de la COVID-19. El mayor fabricante de Reino Unido, el gigante del sector aeroespacial BAE Systems, ha hecho de sus impresoras 3D Stratasys de nivel industrial el centro de su exitosa iniciativa ‘Fábrica del futuro’. Esto le ha permitido reducir considerablemente los costes y tiempos de comercialización, y ha contribuido a mejorar la flexibilidad de producción de la empresa. Del mismo modo, el gigante industrial Schneider Electric se ha embarcado en la implantación a gran escala del proceso Industria 4.0 en sus operaciones en todo el mundo, una medida diseñada para aumentar la eficacia operativa y reducir costes para sus clientes. Como se ha anunciado recientemente, la impresión 3D de Stratasys también desempeña un papel clave en esta iniciativa; su fábrica de Navarra, España, ha conseguido ella sola un ahorro de más de 20.000 € al año en fabricación de herramientas para la línea de montaje. La empresa también ha comunicado una reducción de la dependencia de proveedores, lo que aumenta de manera importante la flexibilidad de la producción y acelera los tiempos de comercialización.
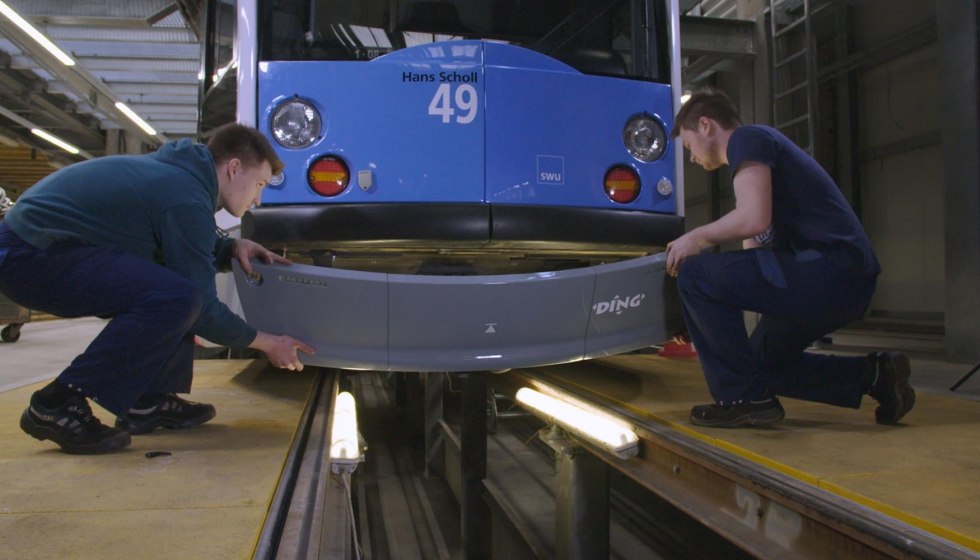