Reparaciones ad-hoc: las posibilidades del LMD
Magdalena Cortina Burón, Marta Ostolaza Gaztelupe, Iker Villarón Osorno, Jose Exequiel Ruiz Salas y Jon Iñaki Arrizubieta Arrate, del Dpto. de Ingeniería mecánica, Escuela de Ingeniería de Bilbao (UPV/EHU)
03/06/2020La fabricación aditiva ha llegado para quedarse. Las tecnologías aditivas han supuesto un cambio de paradigma frente a los métodos de fabricación convencionales, ya que, entre otras cosas, permiten la manufactura de geometrías complejas previamente imposibles de fabricar [1] y la reparación o el reacondicionamiento de componentes de alto valor añadido, con el consecuente impacto económico que ello supone.
El proceso de aporte por láser, o LMD (del inglés Laser Metal Deposition), es un proceso aditivo donde una fuente de calor, en este caso un láser, crea un baño fundido en el material base, o sustrato, al mismo tiempo que se inyecta material metálico [2]. Este material inyectado puede presentarse en forma de polvo o hilo y, para ambos casos, es necesario el empleo de una boquilla o cabezal cuyo propósito es dirigir el material al baño fundido. El resultado del proceso es un cordón, cuyo solapamiento sucesivo genera capas; por su parte, la superposición de diferentes capas da lugar a la generación de recubrimientos o estructuras tridimensionales más complejas.
El láser es una fuente de calor que concentra la energía de forma puntual y, por lo tanto, dota al LMD de una gran ventaja, como es la baja afectación térmica sufrida por el material base. Esta capacidad de concentración de energía junto al uso del resto de la pieza, o el sustrato, como sumidero de calor, generan un gradiente térmico elevado, que impide que la zona de trabajo sufra un aumento de temperatura excesivo y vea degradadas, en consecuencia, sus propiedades mecánicas [3]. Otra ventaja del LMD es su capacidad para generar microestructuras más finas que otras fuentes empleadas en métodos de reparación tradicionales, como la soldadura por arco, consiguiendo mejores propiedades mecánicas. Por último, el LMD se emplea en un gran número de sectores debido al amplio abanico de materiales disponibles en forma de polvo, desde aleaciones aeronáuticas hasta una gran variedad de aceros, como es el acero de herramientas de trabajo en caliente [4]. En definitiva, la tecnología LMD, presenta una gran versatilidad tanto en lo referido a libertad geométrica como a materiales.
Dentro de sus principales nichos de aplicación, se encuentran los recubrimientos de alto rendimiento que permiten mejorar las propiedades superficiales del material base [5], así como la reparación de geometrías complejas de muy alto valor añadido presentes en la industria aeronáutica, nuclear y de moldes y matrices [6], cuyos componentes han de soportar solicitaciones muy exigentes, tanto mecánicas como de fiabilidad.
A lo largo de este texto se revisa el estado de aplicación de dicha tecnología a la industria de moldes y matrices, tanto para la reparación como para la generación de recubrimientos. Además, se recogen las ventajas que aporta esta alternativa frente a los métodos convencionales ya conocidos.
Las reparaciones de moldes y matrices
La industria de moldes y matrices, tradicionalmente caracterizada por la producción de lotes pequeños y, en muchos casos, piezas individuales, se enfrenta actualmente a nuevos desafíos a medida que la economía mundial avanza hacia la disminución de los plazos de entrega y la creciente diversidad de productos [7]. En un escenario tan competitivo, la optimización de estos útiles, junto con la extensión de su vida útil cobran una gran importancia. Los moldes y matrices están normalmente expuestos a condiciones de trabajo severas, tales como altas solicitaciones bajo elevadas temperaturas, ciclos térmicos, ambientes corrosivos y cargas cíclicas [8]. Como resultado, tienen una vida útil limitada y deben ser reemplazados o reparados, con el consiguiente coste económico. A esta limitada vida útil hay que sumarle el hecho de que los moldes y matrices son componentes complejos, que requieren una gran precisión en lo que a su geometría se refiere y son generalmente fabricados con materiales difíciles de trabajar, lo que los convierte en componentes de alto valor añadido. En consecuencia, su reparación ha llamado la atención de la industria y se han desarrollado diversos procedimientos que se adecuan a las necesidades de cada casuística.
Los modos de fallo de los moldes y matrices están directamente relacionados con el tipo de proceso en el que participan. Algunos de los principales mecanismos de fallo se resumen a continuación:
- Agrietamiento de carácter térmico: Este fenómeno se debe a los grandes gradientes térmicos a los que se somete la superficie de moldes y matrices. Los sucesivos ciclos de calentamiento y enfriamiento originan tensiones de compresión y tracción, respectivamente, lo que conduce al agrietamiento superficial [9]. Este es un modo de fallo típico de moldes y matrices de trabajo en caliente.
![Figura 1. Ejemplo de grieta inducida por los ciclos térmicos [10] Figura 1. Ejemplo de grieta inducida por los ciclos térmicos [10]](https://img.interempresas.net/fotos/2252936.jpeg)
- Desgaste: Es la pérdida progresiva de material causada por las cargas cíclicas a las que los moldes y matrices están expuestos, deteriorando así el elemento y perdiendo las tolerancias [11].
- Deformación plástica: Este modo de fallo es experimentado igualmente por los útiles de trabajo en frío y en caliente debido a que la presión de contacto excede la tensión de fluencia del material. Así, aquellas regiones que están sujetas a presiones y temperaturas extremas, así como a largos tiempos de contacto, como por ejemplo bordes afilados o protuberancias, tienden a experimentar deformaciones plásticas.
![Figura 2. Ejemplo de deformación plástica [12] Figura 2. Ejemplo de deformación plástica [12]](https://img.interempresas.net/fotos/2252937.jpeg)
- Soldadura y corrosión: Se deben a interacciones químicas entre el útil y la pieza de trabajo, lo que resulta en soldaduras locales entre ambas o efectos de corrosión.
- Fallo catastrófico: Este tipo de fallo ocurre debido a un choque térmico y al calentamiento del útil, causando inestabilidad en las propiedades mecánicas del mismo y el consiguiente fallo [13].
La soldadura manual es la técnica de reparación más popular para moldes y matrices agrietados o desgastados. Además, también puede ser empleada para reparar bordes cortantes, así como para corregir errores de mecanizado o cambios de diseño de última hora [14]. La soldadura no es un proceso sencillo, ya que los aceros de herramientas que se utilizan normalmente en los moldes y matrices son altamente aleados, y esto, junto con las altas temperaturas que se alcanzan en el proceso de soldadura, puede conducir a un endurecimiento local y el consiguiente agrietamiento. Sin embargo, los avances en las tecnologías de fabricación hacen que la reparación de estos elementos sea una realidad. Entre los diferentes métodos de soldadura disponibles, los cuales pueden observarse en la figura 3, la soldadura TIG (del inglés Tungsten Inert Gas) y la soldadura por plasma, PAW (Plasma Arc Welding), son procesos de reparación tradicionales, mientras que el empleo del LMD ha irrumpido recientemente como una alternativa a ellos.
![Figura 3. Reparaciones realizadas mediante soldadura (a) TIG; (b) PAW; (c) LMD [15], [16] Figura 3. Reparaciones realizadas mediante soldadura (a) TIG; (b) PAW; (c) LMD [15], [16]](https://img.interempresas.net/fotos/2252938.jpeg)
Aplicaciones del LMD en el sector de moldes y matrices
El proceso de LMD se caracteriza por un aporte de material muy preciso con una mínima afectación térmica del material base, cualidades que lo hacen destacar entre los demás. Así, el LMD no sólo abre las puertas a reparaciones de alta calidad, sino también a la fabricación de geometrías complejas que no son viables mediante la aplicación de métodos convencionales, así como al desarrollo de recubrimientos de alto rendimiento.
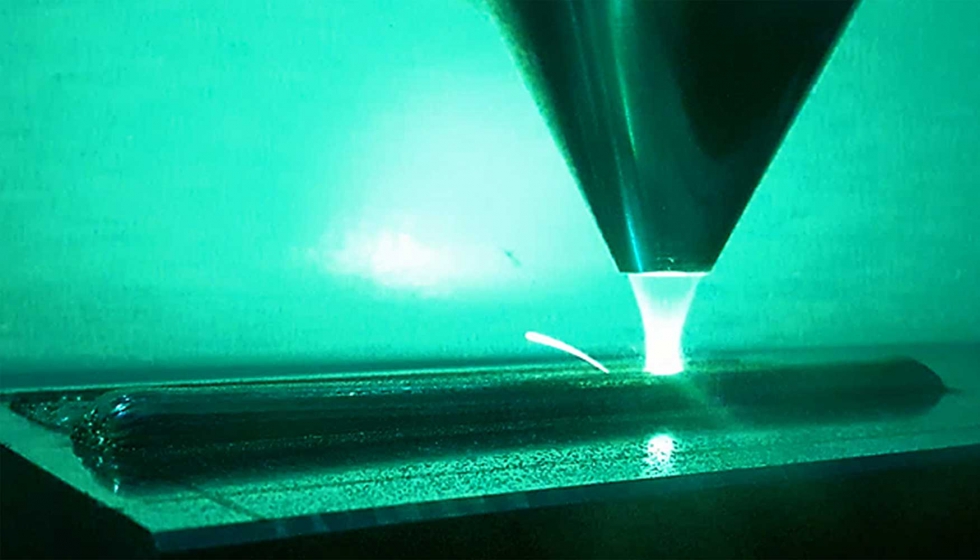
Entre las principales aplicaciones del LMD se pueden distinguir la siguientes:
- Reparación de piezas dañadas debido al uso: Se aporta material en aquellas zonas críticas que han resultado dañadas como consecuencia del proceso en el que toman parte.
- Recubrimientos superficiales: Tienen como objetivo principal mejorar las propiedades termomecánicas en zonas determinadas o en toda la superficie activa del componente.
- Modificaciones geométricas de última hora: Desde que se lanza la producción hasta que se termina el molde o matriz, pueden producirse ligeros cambios de diseño, que en algunos casos obligan a añadir material en zonas ya mecanizadas o generar geometrías que no existían en el diseño original.
- Operaciones de ajuste: En el proceso de ajuste de las dos mitades de los moldes, habitualmente ejecutado en procesos de conformado, se procede a la eliminación de material. No obstante, en algunos casos podría ser más conveniente añadir material.
De las cuatro aplicaciones mencionadas, las dos primeras son las que permitirán incrementar la vida útil de los moldes y matrices, por lo que en los siguientes apartados se tratan estos temas en mayor profundidad.
El LMD en las reparaciones de moldes y matrices
La reparación de moldes y matrices es una alternativa económica a la fabricación de nuevos componentes, especialmente cuando se trata de piezas complejas con un alto valor añadido. En este sector industrial, es habitual que el proceso de reparación se lleve a cabo manualmente por un operario experimentado. De este modo, el resultado depende en gran medida de dicho trabajador y de su destreza. El proceso de reparación incluye la detección de daños mediante inspección visual, eliminación de las zonas dañadas y recargue mediante soldadura manual. Finalmente, se requiere una última etapa de mecanizado que garantice las dimensiones y el acabado superficial finales en el componente reparado [17].
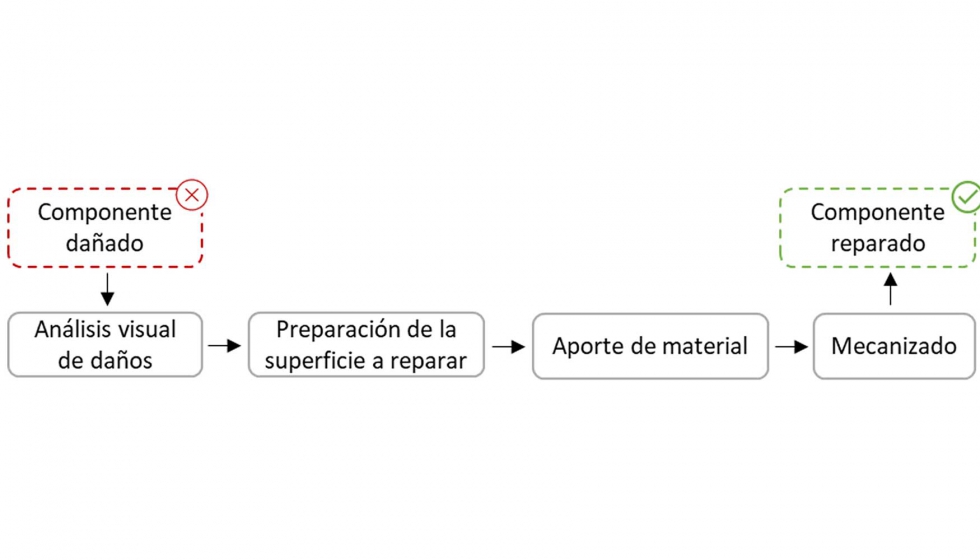
Debido a los altos costes asociados con el reemplazamiento y reparación de estos componentes, el desarrollo de métodos que reduzcan dichos costes y mejoren su vida útil, así como su desempeño durante la misma ha tomado una gran relevancia [18]. La aplicación del proceso LMD a las reparaciones supone una alternativa a las tecnologías convencionales que permite realizar recubrimientos, tanto a componentes completos como, a zonas concretas que hayan podido sufrir deterioro. Esta técnica permite también el recubrimiento con diferentes materiales, o incluso el uso de gradientes funcionales, lo cual posibilita la mejora de las propiedades mecánicas con respecto al componente original, con el fin de extender su vida útil a lo largo del tiempo. De igual modo, cabe destacar que este proceso de reparación es completamente automatizable, y por lo tanto su resultado es independiente de la destreza del operario.
Basándose en un modelo tridimensional del componente a reparar, el proceso LMD permite aportar material en las zonas que así lo requieran de una manera precisa y controlada, capa a capa. Esto permite una reparación del componente, más ajustada a su geometría. Además, el bajo aporte térmico que caracteriza a este proceso reduce considerablemente las deformaciones del componente. El LMD se caracteriza por la rápida solidificación del material, debido a las elevadas velocidades de enfriamiento que toman parte en él. En consecuencia, los aceros de herramienta aportados mediante esta técnica resultan templados, obteniéndose estructuras martensíticas con durezas que pueden llegar incluso a superar los 60 o 65 HRC [19]. Además, la fina microestructura generada cumple, y a veces excede, los requisitos mecánicos y tribológicos de los componentes a reparar.
![Figura 6. Recubrimiento por LMD de un útil de forja [20] Figura 6. Recubrimiento por LMD de un útil de forja [20]](https://img.interempresas.net/fotos/2252941.jpeg)
No obstante, la aplicación de esta tecnología no está exenta de retos, ya que la soldabilidad de los aceros de herramienta empleados para la fabricación de moldes y matrices, así como de estrategias de reparación, son todavía objeto de estudio. Es por ello por lo que aún se realizan avances en el análisis de la influencia de los parámetros de proceso y de la calidad del aporte realizado, ya sean a nivel microestructural o de propiedades mecánicas, como pueden ser dureza, fatiga o desgaste, entre otros. A este respecto, es frecuente que la microestructura y la dureza obtenidas en los recubrimientos difieran de aquellas del componente a reparar y que, además, sean diferentes también entre las sucesivas capas que forman dicho recubrimiento. Es por esto por lo que la aplicación de tratamientos térmicos posteriores al proceso de LMD adquiere una gran importancia, ya que contribuye a homogeneizar las propiedades de los materiales.
Sin embargo, esto no ha impedido la obtención de resultados satisfactorios en la reparación de moldes y matrices. Por ejemplo, se han desarrollado recubrimientos superficiales con buenas propiedades de resistencia a la corrosión, desgaste o fatiga térmica, entre otros. Así, se ha comprobado que aquellos recubrimientos con un mayor contenido en silicio contribuyen a mejorar el comportamiento frente a fatiga térmica, permitiendo extender la vida útil de los componentes reparados [21]. El aporte de aleaciones específicas muestra que, con los parámetros de proceso adecuados, se consigue mejorar la dureza del componente inicial, así como sus propiedades frente a desgaste. Por ejemplo, existen evidencias que indican que, al recubrir acero de herramientas de trabajo en caliente AISI H13, el cual es ampliamente utilizado en moldes y matrices, con aleaciones ricas en vanadio, se consigue incrementar su dureza hasta 64 HRC. Todo ello unido a que, además, se generan tensiones residuales de compresión, contribuye a extender la vida útil del componente [22]. De nuevo, al recubrir dicho material con aleaciones ricas en cobalto, como el Stellite®21, se han obtenido mejoras en el comportamiento a desgaste. Más concretamente, se ha conseguido un 49% de mejora en el abrasivo y un 67% en el adhesivo [18].
De este modo, se puede concluir que el proceso LMD es una alternativa adecuada a ser considerada en la reparación de moldes y matrices. Además, la correcta selección del material de recubrimiento, así como de los parámetros de proceso, ofrecen amplias mejoras en lo que a la calidad de las reparaciones se refiere.
Recubrimientos de alto rendimiento
Las exigencias de la industria actual son cada vez más críticas, ya que se requiere que los componentes trabajen debidamente bajo entornos corrosivos o abrasivos, y que resistan adecuadamente tensiones derivadas de esfuerzos térmicos [23]. En la industria de moldes y matrices, en particular, las herramientas sufren cargas cíclicas de naturaleza térmica y mecánica. En consecuencia, es habitual que estos componentes sufran desgaste y daño localizado. Para poder hacer frente a estas solicitaciones altamente exigentes, es necesario recurrir a materiales de alta calidad, lo que supone un gran impacto económico en la fabricación del componente. Alternativamente, es posible recurrir a la aplicación de recubrimientos de alto rendimiento, que permiten proteger o reforzar localmente las superficies de los componentes que estén más solicitadas. Es por esto que, es habitual emplear procesos de hardfacing, recubrimientos anticorrosivos u operaciones de reparación como las mencionadas en el apartado anterior, con el objetivo de prolongar la vida útil de los componentes [23].
Alternativas para la generación de recubrimientos
Las técnicas de recubrimiento tradicionales más empleadas son las de proyección térmica o la soldadura por arco (Figura 7). Dentro de los procesos de proyección térmica destacan la proyección térmica por llama con hilo (WFS), la proyección térmica al arco (AS), la proyección térmica de alta velocidad (HVOF), la proyección térmica por plasma (APS) y el Cold Spray. Por otra parte, dentro de los procesos de soldadura por arco se enmarcan principalmente la soldadura por arco con electrodo de metal revestido (SMAW), la soldadura por electrodo consumible protegido (MIG/MAG) y la soldadura por arco sumergido (SAW).
![Figura 7. Técnicas convencionales de recubrimiento: (A) Proyección térmica [24] y (B) Soldadura por arco [25] Figura 7. Técnicas convencionales de recubrimiento: (A) Proyección térmica [24] y (B) Soldadura por arco [25]](https://img.interempresas.net/fotos/2252942.jpeg)
Sin embargo, la técnica del LMD ha emergido como una solución a las limitaciones que estos procesos presentan. Para asegurar la calidad del recubrimiento es necesario garantizar una buena unión entre este y el sustrato. Mientras que, tanto el proceso de aporte por láser como el de soldadura por arco, están caracterizados por fundir el material de recubrimiento y el sustrato, garantizando así la unión metalúrgica entre ambos, no es este el caso de los recubrimientos realizados mediante proyección térmica. En función de la técnica empleada, la fusión total de los materiales no está asegurada y, por tanto, no siempre se obtiene una unión metalúrgica. En consecuencia, es más probable que el recubrimiento falle por delaminación. Por otra parte, resulta imperativo no deteriorar el sustrato y conservar sus propiedades durante el proceso de recubrimiento. Es por esto por lo que técnicas con un aporte energético muy local y preciso son especialmente interesantes. De las arriba mencionadas, la soldadura por arco es relativamente agresiva con el sustrato, generando una zona afectada térmicamente bastante mayor que el aporte por láser o la proyección térmica (Figura 8). Este elevado aporte energético fomenta la generación de tensiones residuales y de distorsiones geométricas en los componentes. Además, cabe destacar que, la posibilidad de automatizar el LMD es de vital importancia en el caso de recubrimientos de moldes y matrices, ya que estos suelen tener una geometría compleja, y es necesario controlar los distintos parámetros del proceso de aporte en todo momento (Figura 9).
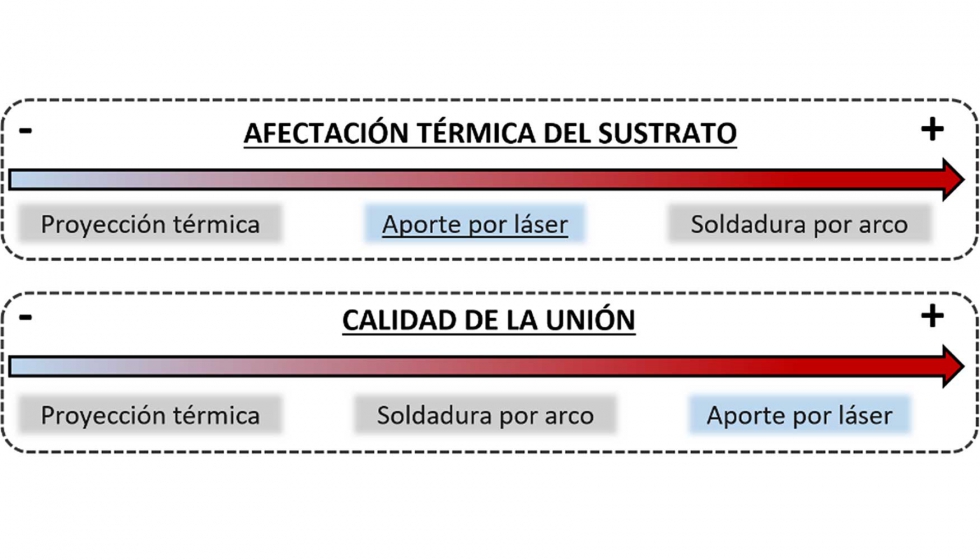
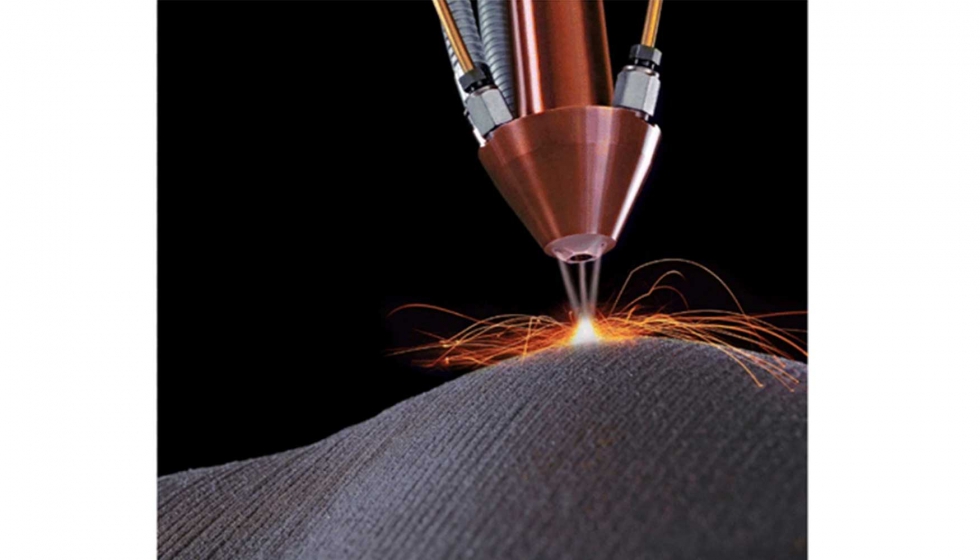
De esta forma, es posible generar recubrimientos de gran calidad con propiedades específicas que permitan mejorar las propiedades superficiales de componentes de alto valor añadido. Esto permite obtener una mejora en términos de resistencia al desgaste, corrosión, y a la oxidación a altas temperaturas. Además, esta técnica permite aportar materiales con propiedades superiores en lo que a homogeneidad, dureza y microestructura se refiere, ya que es posible generar recubrimiento sin faltas de fusión ni porosidad.
Recubrimientos con materiales compuestos
El objetivo del recubrimiento de moldes y matrices es, principalmente, dotar a las superficies de trabajo de una mayor dureza que resulte en una resistencia al desgaste superior. Con este fin, es habitual emplear recubrimientos comerciales de aceros inoxidables martensíticos o aleaciones con base cobalto como los Stellite® 6, 12 y 21.
Sin embargo, en las últimas décadas se ha llevado a cabo una gran labor de investigación en el ámbito de desarrollo de materiales con el fin de mejorar la eficiencia de los mismo y obtener materiales ad-hoc que se adapten a necesidades específicas; destacando, entre ellos, los composites de matriz metálica o MMC (del inglés Metal Matrix Composite). Se ha demostrado que mediante estos materiales es viable obtener propiedades superiores e imposibles de alcanzar mediante materiales homogéneos. Su principal aplicación, hoy en día, es la fabricación de recubrimientos que confieran propiedades mejoradas a las superficies de componentes altamente requeridos, mejorando su rendimiento y prolongando su vida útil [26]. Se trata generalmente de compuestos formados por una aleación metálica con base Al, Ni, Co, Ti o Fe y un refuerzo cerámico con partículas de SiC, Al2O3 o WC. Hay numerosos estudios que sugieren que este tipo de recubrimientos son adecuados para su empleo en herramientas de la industria del molde y la matriz. Por ejemplo, mediante combinaciones de AISI H13 y TiC o WC se han obtenido recubrimientos de durezas del orden de 60 HRC y 70 HRC, respectivamente. Además, se ha demostrado que la combinación de materiales de esta naturaleza permite mejorar la resistencia al desgaste de las superficies tratadas por hasta un factor de diez [26].
Asimismo, destacan los materiales con gradiente funcional o FGM (del inglés Functionally Graded Material), por el interés que han suscitado tanto en la industria como en el ámbito de la investigación. Esta técnica consiste en la introducción de un gradiente en las propiedades del material, ya sea mediante una variación composicional o mediante una variación micro o macroestructural. Así, se obtiene una transición gradual de sus propiedades, permitiendo generar materiales adaptados a las exigencias de cada zona de un componente. La aplicación de FGMs en recubrimientos supone una gran ventaja, ya que permite eliminar la transición repentina entre sustrato y recubrimiento. Por lo tanto, a través de la variación gradual de propiedades, en teoría, se puede reducir la concentración de tensiones en la intercara. En el caso de la industria de moldes y matrices, recubrimientos de esta naturaleza tienen un gran potencial de aplicación, ya que permiten obtener una gran dureza superficial con una transición hacia un núcleo más dúctil que asegure una correcta absorción de esfuerzos, evitando el fallo catastrófico de la herramienta. Además, la integración de MMCs en FGMs ya ha demostrado sus capacidades en el sector aeronáutico [27], de forma que, escogiendo una combinación adecuada de materiales, podría adecuarse al recubrimiento de herramientas de inyección, estampación, etc. (Figura 10)
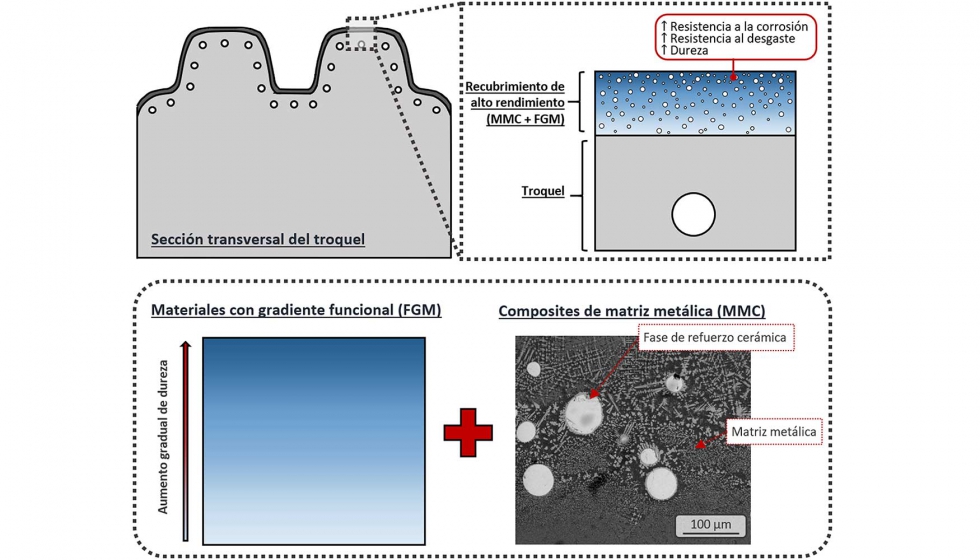
La versatilidad de los FGMs cuando se combinan con los MMCs, permite obtener materiales de excelentes propiedades, demostrando una mayor resistencia a la oxidación cuando los componentes están sometidos a cargas térmicas cíclicas, una mayor resistencia al desgaste, o una mayor tenacidad, empleando un único material con una concentración variable de la fase de refuerzo cerámica [27].
No obstante, el procesamiento de este tipo de materiales avanzados no es sencillo, y es por eso por lo que, si bien esta tecnología es conocida desde finales de los 80, es ahora cuando se ha empezado a emplear y a investigar con mayor éxito. Esto es posible gracias al desarrollo de nuevas tecnologías como la fabricación aditiva metálica y en particular el LMD, el cual, gracias a su gran versatilidad en lo a que a procesamiento de materiales se refiere, y a su capacidad de aporte multi-material, permite la fabricación de FGMs como MMCs.
Sensores embebidos
En su más básica definición, un sensor es un dispositivo que detecta una influencia externa y la traduce en información. Su uso está ampliamente extendido en la industria, donde es necesario monitorizar las propiedades y características de los procesos, con el fin de conseguir un mejor control sobre estos actuando sobre sus parámetros de entrada. Un claro ejemplo de ello se da en la industria de moldes y matrices, donde la temperatura y la presión son parámetros, no sólo de proceso sino, de control sobre el mismo, y por lo tanto su sensorización es de gran interés.
El uso habitual de sensores en la industria se realiza sobre superficies de fácil acceso, donde la instalación y reemplazo de estos se hace de manera sencilla [28]. Sin embargo, la creciente necesidad de conocimiento, modelización y predicción de los procesos ha llevado al desarrollo de tecnologías que permitan el acercamiento de estos sensores a las zonas más críticas, donde se observan con mayor frecuencia los fallos.
Los sensores embebidos, o integrados, se diseñan con la intención de cubrir esta necesidad, introduciéndose en los componentes, en zonas cercanas a las superficies o puntos en los que se desea realizar la medida. Este tipo de sensores han resultado ser muy efectivos en la ingeniería civil o de estructuras [29], sin embargo, en otros sectores han encontrado dificultades debidas al tamaño, la metodología de inserción y la problemática ligada a la conectividad, normalmente mediante cables. Aunque algunos de estos retos han sido superados, gracias a la miniaturización de los sensores y el uso de tecnologías inalámbricas muy presentes en la actualidad.
La capacidad de las tecnologías aditivas de fabricar un componente capa a capa ofrece la posibilidad de tener acceso al interior de este durante su creación. Estos procesos de fabricación aportan soluciones interesantes para resolver la integración de los sensores en una pieza. Sin embargo, existen retos inherentes a estas tecnologías que deben sortearse para conseguir dicho objetivo. Uno de ellos es el pobre acabado superficial, habitual en la fabricación aditiva, que interfiere en el contacto de la zona de interés con el sensor. La compatibilidad de materiales es de vital importancia, más aún cuando pueden existir grandes diferencias de temperaturas de fusión entre los materiales del sensor y la pieza. Por último, se requieren consideraciones especiales cuando los procesos aditivos se pausan, ya que podrían formarse intercaras que afectasen negativamente a la integridad de la pieza [30].
A pesar de las dificultades, en la actualidad existen tecnologías aditivas capaces de realizar con éxito la integración de sensores durante la fabricación de componentes. Entre ellas, las tecnologías PBF (Powder Bed Fusion) y DED (Direct Energy Deposition) permiten pausar la fabricación para la inserción de los sensores y reanudarla para su recubrimiento. Por su parte, las tecnologías de Cold Spray resultan eficaces para cubrir los sensores en los que la diferencia de temperaturas de fusión es importante, entre su encapsulado y el material del componente [31]. Los procesos DWTS (Direct Write Thermal Spray) permiten incluso fabricar, de manera aditiva, termopares ad-hoc sobre los componentes, que luego pueden ser recubiertos por otras tecnologías ya mencionadas [32]. Por supuesto, la fabricación mediante FDM (Fused Deposition Modeling) no es una excepción, y la creación de piezas con electrónica integrada es un hecho, gracias a las bajas temperaturas de fusión de materiales como el PLA (ácido poliláctico), ABS (acrilonitrilo butadieno estireno), Nylon y otros [30].
Así, las tecnologías aditivas permiten la creación de componentes inteligentes que brindan información durante su desempeño, ya sean parámetros de operación, como temperaturas, presiones, posición y aceleración, entre otros, así como también información logística de localización o identificación.
Referencias
[1] T. Babuska, K.L. Johnson, T. Verdonik, S.R. Subia, B.A. Krick, D.F. Susan, A.B. Kustas, “An additive manufacturing design approach to achieving high strength and ductility intraditionally brittle alloys via laser powder bed fusion” Additive Manufacturing, 2020, vol 34, 101187
[2] J.I. Arrizubieta, J.E. Ruiz, M. Cortina, E. Ukar, A. Lamikiz, “Evaluación de la sobreacumulación de material en los cambios de dirección durante el proceso de aporte por láser mediante un modelo integral”. Revista Iberoamericana de Ingeniería Mecánica 2018, 22 (2), 3-12.
[3] E. Toyserkani, A. Khajepour, S. Corbin, “Laser cladding”, 2005, ISBN: 0-8493-2172-7
[4] Oerlikon Metco, 2020. Disponible en: https://www.oerlikon.com/metco/en/products-services/coating-materials/coating-materials-thermal-spray/metals-alloys-composites-blends/ Último acceso: 26 de mayo de 2020
[5] X. Liu, O. El Fakir, Y. Zheng, M. Gharbi, L. Wang, “Effect of tool coatings on the interfacial heat transfer coefficient in hot stamping of aluminium alloys under variable contact pressure conditions” International Journal of Heat and Mass Transfer, 2019, vol.137, pp 74-83
[6] H. Gonzalez, J.I. Arrizubieta, A. Calleja, A. Lamikiz, “CAM development for additive manufacturing in turbo-machinery components” Procedia Manufacturing, 2013, vol 13 pp 802-809
[7] G. Schuh, M. Salmen, T. Kuhlmann, J. Wiese, Highly Iterative Product Development Within The Tool and Die Making Industry, Proc. CIRP, 61, 576-581, 2017
[8] W.R. Morrow, H. Qi, I. Kim, J. Mazumder, S.J. Skerlos, Environmental aspects of laser-based and conventional tool and die manufacturing, J. Clean. Prod., 15, 932-943, 2007.
[9] A. Srivastava, V. Joshi, R. Shivpuri, R. Bhattacharya, S. Dixit, A multilayer coating architecture to reduce heat checking of die surfaces, Surface and Coatings Technology, 163–164, 631-636, 2003
[10] L. Lavtar, T. Muhic, G. Kugler, M. Tercelj, “Analysis of the main types of damage on a pair of industrial dies for hot forging car steering mechanisms” Engineering Failure Analysis, vol 18, 2011 pp 1143-1152
[11] C. Chen, Y. Wang, H. Ou, Y. He, X. Tang, A review on remanufacture of dies and moulds, J. Clean. Prod., 64, 13-23, 2014
[12] A. Persson, S. Hogmark, J. Bergstörm, “Thermal fatigue cracking of surface engineered hot work tool steels” Surfdace & Coatings Techology, 2005, vol 191, pp. 216-227
[13] D. Klobcar, J. Tušek, Thermal stresses in aluminium alloy die casting dies, Comp. Mater. Sci., 43(4), 1147-1154, 2008.
[14] Welding of Uddeholm Tool Steels, Uddeholm, 2017. Disponible en: https://www.uddeholm.com/app/uploads/sites/45/2018/02/Uddeholm_welding_eng_1710_e7.pdf Último acceso: 12 de mayo de 2020.
[15] F.J. Xu, Y.H. Lv, B.S. Xu, Y.X. Liu, F.Y. Shu, P. He, Effect of deposition strategy on the microstructure and mechanical properties of Inconel 625 superalloy fabricated by pulsed plasma arc deposition, Mater. Des., 45, 446-455, 2013.
[16] C.P. Paul, H. Alemohammad, E. Toyserkani, A. Khajepour, S. Corbin, Cladding of WC–12 Co on low carbon steel using a pulsed Nd:YAG laser, Mater Sci Eng, A, 464–1, 170-176, 2007.
[17] B. Denkena, M.A. Dittrich, K.M. Heide, Automatic re-contouring of repair-welded tool moulds, Proc. Manuf. 40, 45-50, 2019.
[18] J. Foster, C. Cullen, S. Fitzpatrick, G. Payne, L. Hall, J. Marashi, Remanufacture of hot forging tools and dies using laser metal deposition with powder and a hard-facing alloy Stellite 21®. Jnl Remanufactur, 9, 189–203, 2019.
[19] S. Jhavar, C.P. Paul, N.K. Jain, Causes of failure and repairing options for dies and molds: A review, Engineering Failure Analysis, 34, 519-535, 2013.
[20] Fraunhofer Institute for Laser technology, Laser Cladding, 2020. Disponible en: https://www.ilt.fraunhofer.de/en/technology-focus/laser-material-processing/cladding.html Último acceso: 12 de mayo de 2020.
[21] M. Fazarinc, T. Muhic, A. Salej, D. Bombac, P. Fajfar, M. Tercelj, G. Kugler, Thermal fatigue testing of bulk functionally graded materials, Procedia Eng., 10, 692–697, 2011
[22] P. Kattire, S. Paul, R. Singha, W. Yan, Experimental characterization of laser cladding of CPM 9V on H13 tool steel for die repair applications, Journal of Manufacturing Processes, 20(3), 492-499, 2015.
[23] C. Brunner-Schwer, T. Petrat, B. Graf, M. Rethmeier, Highspeed-plasma-laser-cladding of thin wear resistance coatings: A process approach as a hybrid metal deposition technology, Vacuum 166, 123-126, 2019, https://doi.org/10.1016/j.vacuum.2019.05.003
[24] Hashtap (2020) Thermal Spray Coatings market – Worldwide & Regional Industry Size, Trends, Analysis, Statistics & Forecast!! Disponible en: https://www.hashtap.com/@shubham.gurav/thermal-spray-coatings-market-worldwide-regional-industry-size-trends-analysis-statistics-forecast-eDpBJqrDNg9R Último acceso: 11 de mayo del 2020
[25] Feworks (2019) Services. Disponible en: https://www.feworks.com.br/en/services/ Último acceso: 11 de mayo del 2020
[26] S. Oukach, B. Pateyron, L. Pawlowski, Physical and chemical phenomena occurring between solid ceramics and liquid metals and alloys at laser and plasma composite coatings formation: A review, Surface Science Reports 74(3), 213-241, 2019. https://doi.org/10.1016/j.surfrep.2019.06.001
[27] A. Ramakrishnan, G.P. Dinda, Functionally graded metal matrix composite of Haynes 282 and SiC fabricated by laser metal deposition, Materials & Design 179, 107877, 2019, https://doi.org/10.1016/j.mardes.2019.107877
[28] R. X. Gao, Z. Fan, D. O. Kazmer, Injection molding process monitoring using a selfenergized dual-parameter sensor, CIRP Annals – Manufacturing Technology, 57, 389–393, 2008.
[29] A. Ghazanfari, Wenbin Li, Ming C. Liu, Yiyang Zhuang, Jie Huang, Advanced ceramic components with embedded sapphire optical fiber sensors for high temperature applications, Materials and Design, 112, 197–206, 2016.
[30] D. Lehmhus, C Aumund-Kopp, F. Petzoldt, D. Godlinski, A. Haberkorn, V. Zöllmer, M. Busse, Customized Smartness: A Survey on links between Additive Manufacturing and Sensor Integration, Procedia Technology, 26, 284 – 301, 2016.
[31] P. Attridge, S. Bajekal, M. Klecka, X. Wu, S. Savulak, D. Viens, M. Carey, R. Gosselin, J. Miano, J. Needham, W. Rioux, J. Zacchio, and J. Mantese, Additively Manufactured IN718 Components with Wirelessly Powered and Interrogated Embedded Sensing, United States, 2017, https://doi.org/10.2172/1369567, https://www.osti.gov/servlets/purl/1369567 Último acceso: 15 de mayo de 2020.
[32] K. Martinsen, L. T. Gellein, K. M. Boivie, Sensors embedded in surface coatings in injection moulding dies, Procedia CIRP, 62, 386 – 390, 2017.