Alternativas a los recubrimientos de cromo duro
Naroa Imaz, Asier Salicio y Eva García-Lecina, de Cidetec Surface Engineering
30/04/2020En el caso concreto del cromo funcional o cromo duro, cabe destacar que una ventaja añadida de este tipo de recubrimientos es que su proceso de obtención, la electrodeposición, es sencillo, versátil y barato y que se suele aplicar directamente sobre el sustrato. El cromo duro está caracterizado por tener espesores superiores a 0,80 µm y se utiliza en aplicaciones industriales, donde proporciona elevada resistencia al calor, dureza, resistencia a la abrasión, a la corrosión y a la erosión, así como un bajo coeficiente de fricción, soportando las condiciones más extremas manteniendo su calidad en sectores tan diversos como automoción, máquina-herramienta, aeronáutica, bienes de equipo, textil, papel etc. En el caso del sector de máquina-herramienta, en procesos como el mecanizado y el pulido, tiene lugar un desgaste mecánico de las herramientas debido a la solicitación mecánica entre los componentes en contacto. Si además sumamos la contribución de la corrosión debida al efecto del agua de los fluidos de corte o los lubricantes en el metal de la herramienta, el resultado puede llegar a ser devastador.
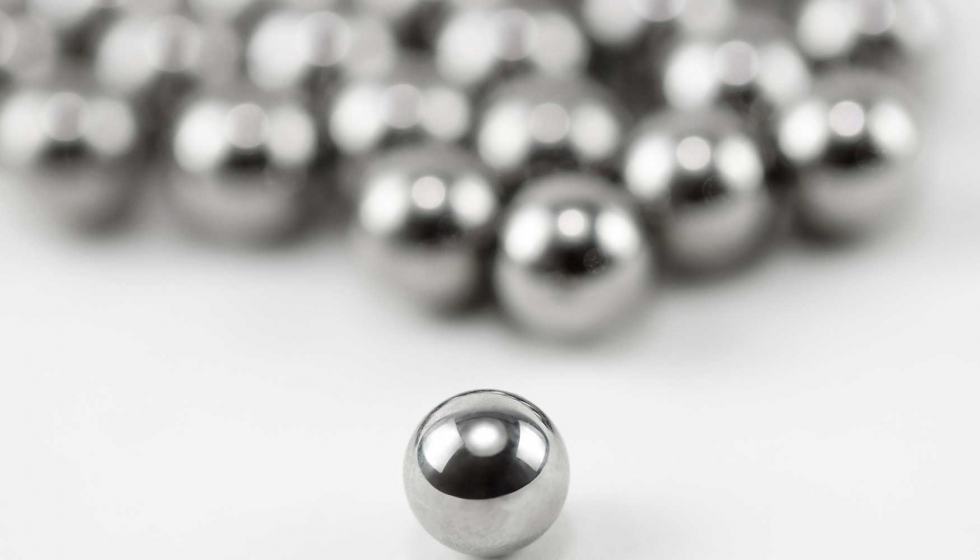
A pesar de las extraordinarias propiedades de los recubrimientos de cromo duro mencionadas, los procesos de electrodeposición a partir de electrolitos basados en cromo hexavalente, presentan un grave problema relacionado con la demostrada toxicidad, carcinogeneidad y tendencia a bioacumularse de dicho ion [4-7]. Está clasificado como cancerígeno por la Agencia Internacional para la Investigación del Cáncer (I.A.R.C.) y existen diferentes normativas y directrices europeas que limitan y regulan el uso y empleo del ion Cr6+ en determinadas aplicaciones. Estas restricciones de la Unión Europea en la utilización de determinadas sustancias peligrosas (RoHS [8], REACH [9], SVHC [10]), además de otras restricciones a nivel mundial [11], conllevan la necesaria eliminación de la utilización de Cr (VI) en cualquier tipo de tecnología o proceso, lo que obliga a encontrar un recubrimiento alternativo capaz de reemplazarlo de forma adecuada.
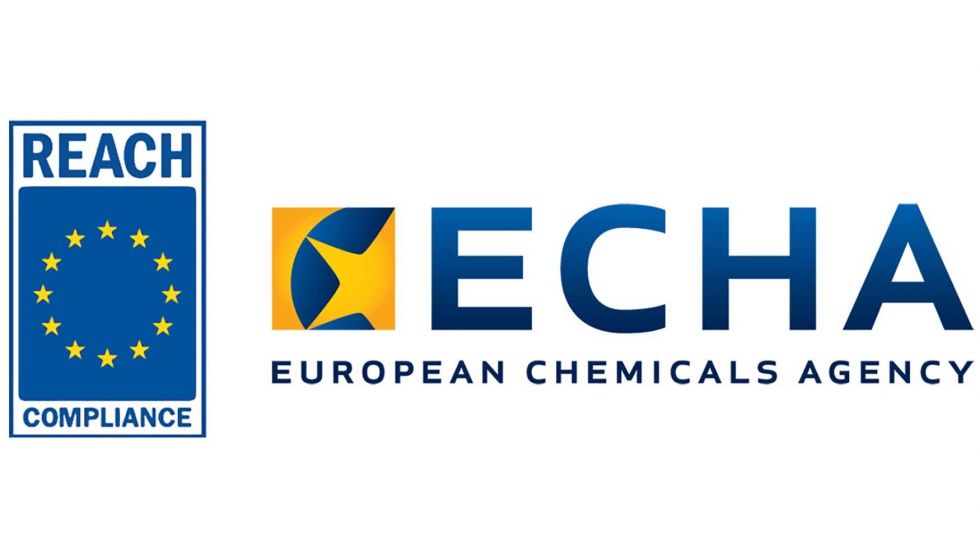
Es por ello que una de las líneas actuales de investigación más importantes en el tratamiento de superficies de piezas y componentes utilizados en sectores estratégicos como el aeronáutico, el de automoción o el de máquina-herramienta, es el desarrollo de nuevos tratamientos menos tóxicos que los anteriores, pero con las mismas propiedades, de forma que se puedan conseguir procesos implementables a escala industrial, competitivos y capaces de cumplir con los estándares medioambientales y de calidad actuales. Teniendo en cuenta además que las Normativas Medioambientales exigen la aplicación de las mejores técnicas disponibles desde el punto de vista medioambiental (Normativa IPPC) [12] en los procesos industriales y, dado que los sectores mencionados presentan estándares de calidad muy altos, existe una gran presión para dar solución a esta problemática, mejorando además la seguridad de la planta y del personal.
En este contexto, durante los últimos años se está invirtiendo un gran esfuerzo, tanto a nivel científico como industrial, en la búsqueda de alternativas viables que permitan sustituir los procesos de electrodeposición basados en Cr (VI). Las alternativas más importantes se pueden dividir en cuatro grupos principales: electrodeposición de cromo a partir electrolitos de cromo trivalente, electrodeposición de otros metales, aleaciones y composites, depósitos electroless y métodos físicos como el PVD.
De entre todas estas líneas Cidetec Surface Engineering, como centro experto en tecnologías químicas y electroquímicas, trabaja activamente en las tres primeras, ya que son tecnologías viables para sustituir al cromo a nivel industrial, tanto por su fácil implantación, como por su rentabilidad. A continuación, se detallan particularidades de cada una de estas tecnologías y el estado del desarrollo en Cidetec.
1. Electrolitos de cromo trivalente
Se han desarrollado formulaciones que han permitido sustituir al cromo hexavalente en aplicaciones decorativas, ofreciendo además una mayor eficiencia catódica, mayor poder de penetración y dureza, resistencia a la corrosión y aspecto comparables a los procesos de Cr (VI) [13, 14]. Sin embargo, a pesar de que muchas investigaciones [15,16] han intentado desarrollar una formulación basada en Cr (III) para aplicaciones funcionales, no se ha conseguido obtener una alternativa que presente unas propiedades físicas comparables a las del proceso de cromo duro sin utilizar capas adicionales, además de constituir procesos difíciles de reproducir industrialmente debido a la complejidad de las formulaciones desarrolladas, su sensibilidad a impurezas y su difícil control [17,18]. Uno de los mayores problemas asociados a los recubrimientos obtenidos a partir de formulaciones basadas en cromo trivalente es su baja resistencia frente a la corrosión, asociada a la estructura agrietada de estas capas. Diferentes grupos de investigación y casas comerciales han tratado de solventar este problema, destacando Faraday Technologies, que tiene registrado el proceso Faradayic [19] de electrodeposición de cromo mediante pulsos de corriente que permiten modificar la microestructura de los recubrimientos; y Atotech, quien comercializa el proceso BluCr basado en un electrolito de Cr (III) exento de ácido bórico pero que requiere de la aplicación de una capa previa de níquel para alcanzar la resistencia frente a la corrosión demandada en muchas aplicaciones industriales de los recubrimientos de cromo duro [20].
Cidetec Surface Engineering tiene experiencia en el desarrollo de nuevos electrolitos en base a cromo trivalente (proyecto FP5 Ecochrom, ID: G1RD-CT-2002-00718), en la modificación de la composición, estructura y propiedades de recubrimientos de cromo mediante pulsos de corriente [21], así como en el estudio de procesos comerciales para realizar su adaptación a los estándares de calidad exigidos en los diferentes sectores/aplicaciones que lo demanden.
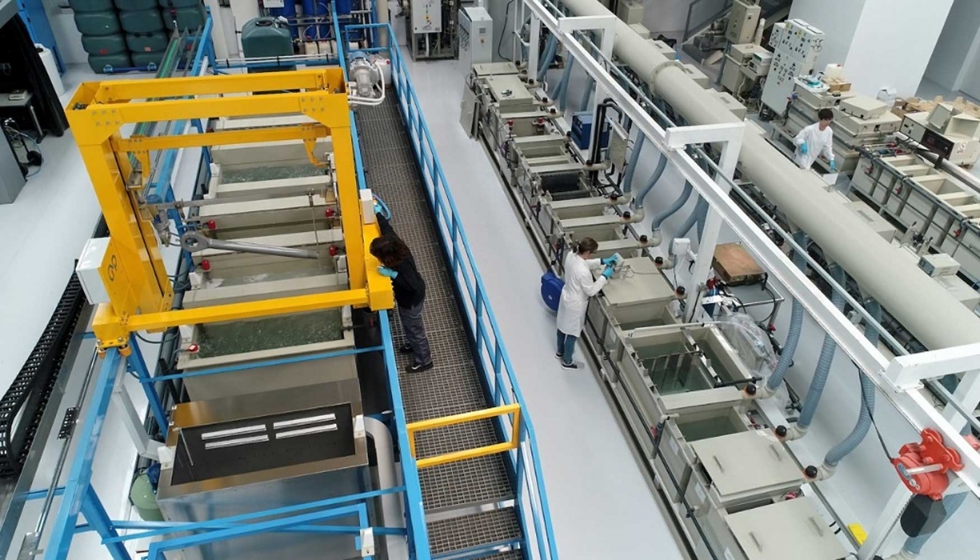
2. Electrodeposición de metales, aleaciones y composites
Las aleaciones y los composites basados en níquel y cobalto constituyen la mayoría de los recubrimientos propuestos hasta el momento como sustitutos del cromo. El cobalto y las sales de este metal han sido clasificados por la Agencia Internacional de Investigación sobre el cáncer (IARC) dentro del grupo 2B (posiblemente cancerígeno), lo que ha hecho que la Administración de Seguridad y Salud Ocupacional (OSHA) haya marcado su valor límite de exposición permitido (PEL) en 0,1 mg m-3 (TWA de 8 horas) [22]. Por ello, los recubrimientos basados en níquel se están erigiendo como una de las alternativas con más perspectivas de futuro en este campo, debido especialmente a sus buenas propiedades mecánicas y anticorrosivas [23]. A pesar de que el níquel es un material relativamente blando, los recubrimientos nanocristalinos de este metal exhiben altos valores de dureza y pueden ser obtenidos mediante un adecuado control de los parámetros químicos y eléctricos del proceso de electrodeposición. Muchas investigaciones han demostrado que se pueden alcanzar durezas similares a las del cromo duro mediante la aleación del níquel con otros metales como el boro, molibdeno o wolframio y la aplicación de un tratamiento térmico posterior [24]. Asimismo, la codeposición de partículas de materiales como SiC, CrC o WC conduce a la mejora de propiedades como la dureza, resistencia al desgaste y a la abrasión, aunque la obtención de recubrimientos composite requiere un control exhaustivo de las condiciones hidrodinámicas del sistema y requiere una modificación del equipamiento de electrodeposición, por lo que aún son pocas las empresas que actualmente disponen de medios necesarios y de personal cualificado que hagan viable su implantación industrial [25].
En este contexto en Cidetec Surface Engineering trabaja activamente en dos líneas principales:
2.1. Recubrimientos composite:
Los recubrimientos composite se obtienen mediante la inclusión de partículas (generalmente poliméricas, cerámicas u óxidos) en una matriz metálica depositada electrolíticamente. Estos recubrimientos combinan sinérgicamente las propiedades de los dos materiales, de manera que se obtiene un recubrimiento con propiedades superiores a cada uno de sus componentes.
Cidetec ha desarrollado formulaciones basadas en composites de níquel/carburo de silicio (Ni/SiC), níquel/carburo de tungsteno (Ni/WC) y níquel/alúmina (Ni/Al2O3), todos ellos con excelente resistencia al desgaste y a la abrasión.
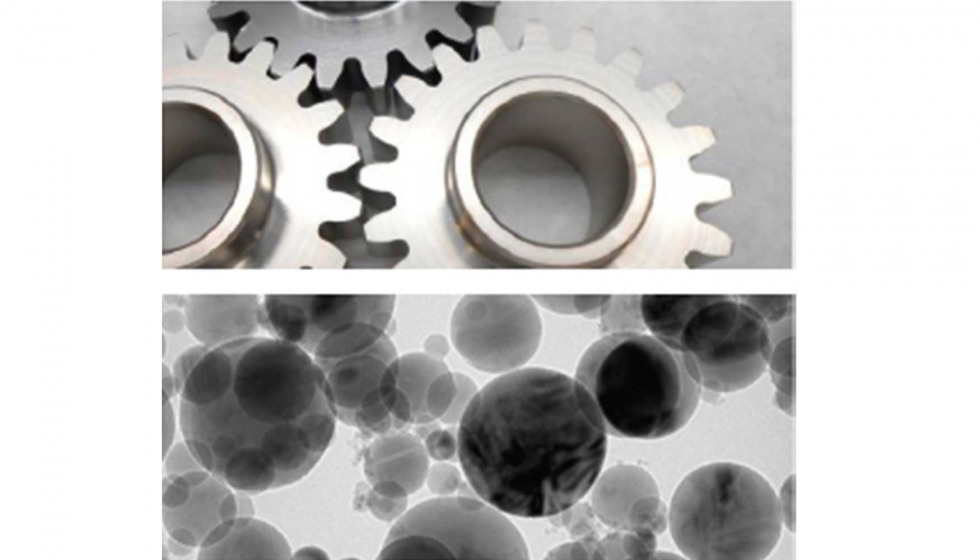
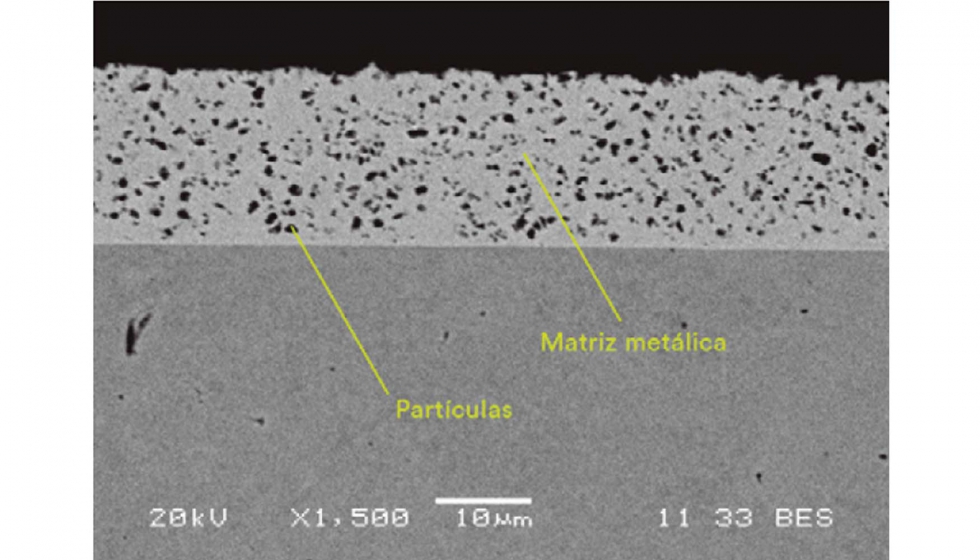
2.2. Electrodeposición de aleaciones de NiW:
Cidetec ha desarrollado una formulación de NiW que posee excelentes propiedades de dureza y resistencia a la corrosión, incluso a temperaturas elevadas, así como un proceso de electrodeposición adaptado a sus características [26, 27]. Asimismo, se ha trabajado en la modificación de la estructura cristalina y el contenido en W mediante la aplicación de pulsos de corriente durante la electrodeposición [28], consiguiendo así una mejora de las propiedades del recubrimiento. Se ha analizado el efecto del tratamiento térmico sobre los recubrimientos desarrollados en Cidetec y se ha observado una mejora de sus propiedades mecánicas a diferentes temperaturas de tratamiento, manteniendo su resistencia al desgaste y a la corrosión [24].
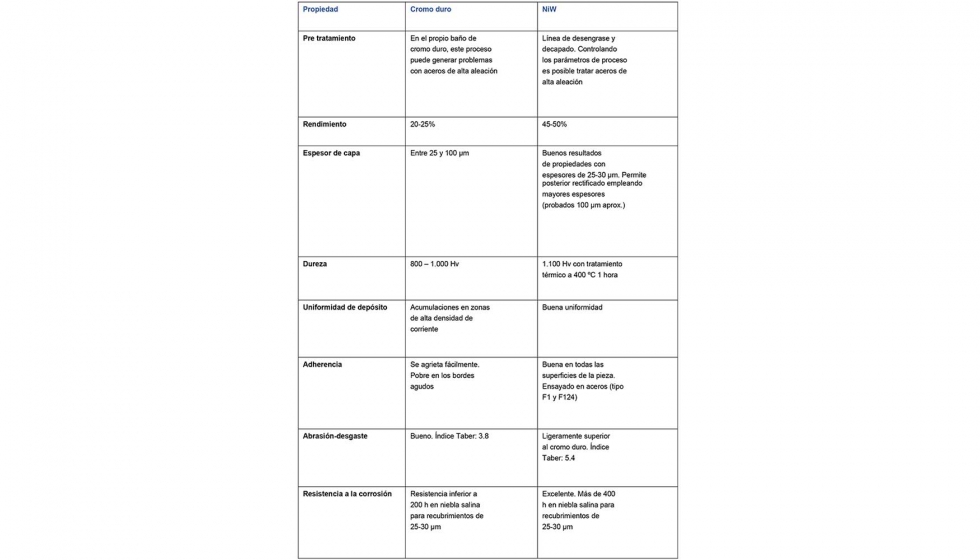
3. Depósitos electroless
Entre los metales depositados mediante esta técnica, destaca el níquel por su excelente comportamiento frente a la corrosión y sus propiedades físicas.
El níquelado químico se basa en una reacción catalítica de codeposición de níquel y fósforo o boro a partir de una amplia variedad de procesos que contienen hipofosfito o borohidruros como agente reductor, respectivamente. Una de las principales ventajas de este tipo de procesos es su habilidad para producir depósitos con un alto grado de uniformidad de espesores, lo que resulta de especial interés en piezas con complejidad geométrica. Aunque tanto los recubrimientos de NiB como de NiP pueden representar una alternativa al cromo duro en muchas aplicaciones, las aleaciones con un contenido en P de 2-14% son las más empleadas debido a sus características funcionales.
La estructura del níquel químico es responsable de sus propiedades y la variación del contenido en P da lugar a diferencias importantes en su resistencia a la corrosión y dureza. La aplicación de un tratamiento térmico (350-400 °C) permite alcanzar durezas comparables a las del cromo duro [29].
Además, con la finalidad de incrementar la resistencia a la corrosión de este tipo de recubrimiento, Cidetec ha estudiado un proceso multicapa. Las interfases generadas actúan evitando la propagación de grietas y defectos a lo largo del espesor, mejorando las prestaciones del recubrimiento [30, 31].

Mediante la aproximación multicapa es posible mejorar las prestaciones de resistencia a la corrosión de los recubrimientos. Este efecto, especialmente en los recubrimientos tratados térmicamente, es debido a la presencia de las interfaces generadas durante el proceso que permiten retrasar la progresión de la corrosión dotando de una mayor resistencia al recubrimiento. Además del aumento en la resistencia a la corrosión aportado por el sistema multicapa, la aproximación multicapa permite mantener intactas sus excelentes propiedades mecánicas. Se trata de una tecnología muy versátil ya que, además, posibilita la combinación de capas de diferente naturaleza, permitiendo combinar diferentes funcionalidades en un único recubrimiento.
Con estos desarrollos queda patente que Cidetec Surface Engineering posee un probado know-how en el desarrollo y caracterización de recubrimientos y tratamientos de superficies para mejorar las propiedades de los materiales y alcanzar los requerimientos funcionales (propiedades mecánicas, tribológicas, anticorrosivas…), estéticos y medioambientales demandados por la industria. Para lograr este objetivo, Cidetec dispone de un edificio de 4.000 m2 equipado con la tecnología más avanzada para dar servicio a empresas de los sectores estratégicos de automoción, aeroespacial, condiciones extremas y otros, ofreciendo a la industria instalaciones en las que se cubra toda la cadena de valor, desde la formulación de electrolitos, la aplicación y caracterización de recubrimientos, el escalado de los procesos, la obtención de prototipos, hasta el ensayo en condiciones muy próximas a la realidad, siempre orientado a una disminución del impacto medioambiental de las tecnologías utilizadas, en línea con las regulaciones europeas medioambientales y de salud. Para ello, dispone de plantas piloto de hasta 500 litros de capacidad. Posee además varios laboratorios químicos equipados con técnicas electroquímicas de análisis y control de electrolitos, así como laboratorios de metalografía y caracterización con amplio rango de equipos como SEM, FE-SEM, microscopía confocal, XRD, AFM, FTIR, etc. Cidetec Surface Engineering invierte además en la adquisición de equipos e instalaciones y en la obtención de acreditaciones específicas para ofrecer una firme cartera de servicios. Cabe destacar la realización de ensayos no destructivos del sector aeronáutico bajo acreditación NADCAP (inspección por ataque Nital, Líquidos penetrantes, partículas magnéticas y ruido Barkhausen).
Por otra parte, es importante señalar que Cidetec Surface Engineering realiza una gran apuesta por comprender los mecanismos de degradación de los materiales en sistemas con especial interés industrial, en los que la seguridad y la fiabilidad son esenciales, como es el caso del sector de la máquina herramienta. En procesos como el mecanizado y el pulido tiene lugar un desgaste mecánico de las herramientas debido a la solicitación mecánica entre los componentes en contacto. Si además sumamos la contribución de la corrosión debida al efecto del agua de los fluidos de corte o los lubricantes en el metal de la herramienta, el resultado puede llegar a ser devastador ya que aparece la tribocorrosión. Para comprender y atajar este problema, además de los ensayos de corrosión acelerada, en Cidetec se utilizan técnicas electroquímicas convencionales y localizadas para profundizar en los mecanismos de corrosión, y simultáneamente, llevar a cabo una monitorización y control de la corrosión con el tiempo, seguido de una caracterización exhaustiva tanto de los materiales degradados como del ambiente/entorno al que están expuestos.
Entender correctamente los fenómenos de desgaste y de corrosión que ocurren en los materiales es el primer paso para proponer nuevas soluciones, alternativas al cromo duro basadas en formulaciones exentas al cromo hexavalente, como las que se proponen en el presente artículo y que constituyen una vía competitiva y viable para solucionar este problema.
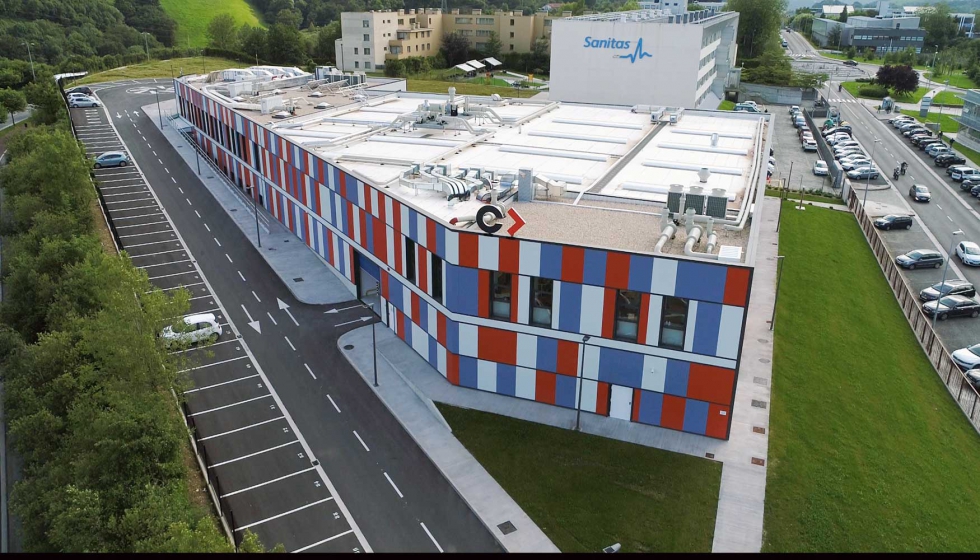
Referencias
[1] M. Schlesinger, M. Paunovic, ‘Modern Electroplating’, Fifth Edition, JOHN WILEY & SONS, EE.UU., 2010
[2] F. A. Lowenheim, ‘Electroplating’, McGraw-Hill Book Co., New York (EE.UU.), 1978
[3] G.A. Lausmann, Surface and Coatings Technology 86-87 (1996) 814.
[4] M.D. Cohen, M. Costa, ‘Chromium’ in ‘Environmental toxicants: human exposures and their health effects, M. Lippmann’, Wiley-Interscience, New York (Estados Unidos), 2000.
[5] C. Pellerin, M.S. Booker, Environmental Health Perspectives 108 (2000) A402
[6] U.S. Environmental Protection Agency, ‘Toxicological Review of Hexavalent Chromium, National Center for Environmental Assessment’, Office of Research and Development, Washington DC (1998)
[7] J.P. Navarro-Aviñó, I. Aguilar, J.R. López-Moya, Ecosistemas 16 (2007) 10
[8] RoHS (Restriction of the use of certain Hazardous Substances) Directiva Europea 2002/95/CE (1 Julio 2006).
[9] REACH (Registration, Evaluation, Authorisation and Restriction of Chemicals). (Aprobado el 18 de diciembre de 2006 y en vigor a partir del 1 de junio de 2007 (Reglamento (CE) nº 1907/2006 del Parlamento Europeo y del Consejo).
[10] SVHC (Substances of Very High Concern for Authorisation) (in accordance with Article 59(10) of the REACH Regulation).
[11] Enhesa 2011. Asia's Regulatory Outlook 2012.
[12] IPPC (IntegratedPollutionPrevention and Control). http://ec.europa.eu/environment/air/pollutants/stationary/ippc/index.htm
[13] https://industrial.macdermidenthone.com/products-and-applications/decorative/decorative-finishes
[14] https://www.atotech.com/products/general-metal-finishing/decorative/trichrome-family/
[15] Li, J.Z., Li, Y.J., Tian, X.H., et al. (2015), SUR/FIN, Chicago, 6-8 June (2015)
[16] F.I. Danilov, V.S. Protsenko, V.O. Gordiienko, S.C. Kwon, J.Y. Lee, M. Kim, Applied Surface Science (2011) 257, 8048-8053.
[17] MTU Aero Engines AG, Analysis of alternatives, Application for Authorisation (AfA) for the use of chromium trioxide in functional chrome plating of aircraft engine components (2016)
[18] Pfonline 2013: http://www.pfonline.com/articles/functional-trivalent-chromium-electroplatingof-internal-diameters
[21] N. Imaz, Aplicación de técnicas de electrodeposición mediante pulsos de corriente para la obtención de recubrimientos metálicos, Universitat de Barcelona (2013)
[22] www.osha.gov
[23] Z. Mahidashti, M. Aliofkhazraei, N. Lotfi, Terans Indian Inst Met (2018) 71, 257
[24] N. Imaz, J.A. Díez, E. Pellicer, J. Sort, H. Grande, E. & Garcia-Lecina, Trans. IMF. 2967 (2017).
[25] A. K. Chaudhari, V.B.Singh, Journal of Alloys and Compounds 751 (2018) 194-214
[26] I. García-Urrutia; L.A. Jones; J.A. Díez; C. Müller. Effect of bath stabiliser on performance of electrodeposited Ni–W coatings. Transactions of the Institute of Metal Finishing. 89, pp. 132 - 136. 2011.
[27] I. García-Urrutia; J.A. Díez; C. Müller; P. Calvillo. Estudio en célula Hull de un baño electrolítico de NiW y evaluación de sus propiedades. Metalurgia. 45(2), pp. 92 - 99. 2009.
[28] N. Imaz, J.A. Díez, M. Ostra, M. Sarret, E. García-Lecina, Transactions of the Institute of Metal Finishing 92 (2014).
[29] H. Zhang, J. Zou, N. Lin, B. Tang, Surf. Rev. Lett. 21 (2014) 1
[30] Salicio-Paz et al. Surface & Coatings Technology 368 (2019) 138
[31] Electroless nickel multilayers in V. Vittry, F. Delaunois, L. Bonin, Electroless Nickel Plating: From fundamentals to Applications, Boca Raton, CRC Press (2020)