Norcort Engineering se consolida como proveedor del sector aeronáutico gracias a sus dos máquinas Chiron Mill 2000
17 de marzo de 2009
En todo el mundo hay cada vez más empresas dedicadas a la producción que desean acceder al creciente mercado aeronáutico. Además de soluciones constructivas, de técnica de materiales y de producción, absoluta calidad, flexibilidad y cumplimiento de plazos, los fabricantes de aviones esperan de sus empresas suministradoras unos costes por pieza lo más económicos posibles.
Esto también lo percibe Steve Fogg, el director de producción del fabricante inglés de piezas aeronáuticas Norcot Engineering Ltd.: “Por supuesto, la capacidad para solucionar problemas es lo más importante en nuestro negocio. No obstante, los clientes se orientan hoy en día en todo el mundo para efectuar sus compras de piezas y componentes. En nuestro planeta hay muchas sedes productivas claramente más económicas y más favorecidas. La gente que vive allí también quiere su trozo del pastel de bienestar. La competencia globalizada conlleva una bajada de los precios. Si queremos seguir viviendo de nuestro negocio, no sólo tenemos que convencer a nuestros clientes desde el punto de vista profesional y organizativo, sino que también necesitamos desarrollar y utilizar unos mejores conceptos de producción".

Según el director técnico David Broomfield “los países que carezcan de tecnologías propias que sean clave en la creación de valor con la técnica de mecanizado dejan de ser independientes y pierden su fuerza de innovación. Empresas como Norcot son sumamente importantes para nosotros y tienen muchas posibilidades de lograr exigentes pedidos de la industria aeronáutica”.
En este sentido, la empresa inglesa produce unas 600 piezas diferentes para una docena de empresas aeronáuticas bajo demanda en las propias instalaciones con recubrimiento galvanizado, pintadas y cada vez más, también montadas.
Están especialmente orgullosos de los tres componentes estructurales para el avión pequeño de dos motores Eclipse 500, entre los que se encuentran una placa base y dos piezas de fuselaje en 3D que deben fabricarse en dos versiones invertidas. Lo que tienen en común estas piezas que tienen un peso de hasta 80 kilogramos como pieza bruta, es su elevado porcentaje de mecanizado de hasta el 95%. Además del desbaste se realiza un gran número de mecanizados de tolerancias muy estrechas en todos los lados como, por ejemplo, alisado, taladrado, roscado, biselado, redondeado y desbarbado. A todo ello se añade la mala costumbre de las piezas de aluminio que su fijación fiable resulta tanto más difícil cuanto más haya avanzado el trabajo. Además, hay que suministrar just-in-time entre 40 y 60 unidades al mes dentro de los plazos. La automatización no entra en consideración. Los cambios rápidos de preparación se convierten en una obligación.
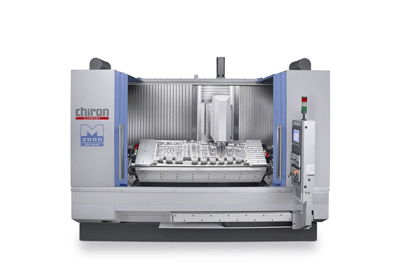
Steve Fogg: “Junto con nuestra planta de Bedford tenemos 40 centros de mecanizado CNC en uso, pero éstos no nos hubieran permitido cumplir las exigencias técnicas y de plazo y tampoco los objetivos de costes. No obstante, lo importante para nosotros es el cliente y sus piezas. Para poder entregar una oferta, hemos desarrollado un proceso de producción y hemos buscado un socio de soluciones adecuado. Después de muchas conversaciones con diferentes ofertantes de máquinas, nos hemos inclinado por la oferta de David Broomfield de Chiron UK.”
La base de la oferta eran dos máquinas Chiron Mill 2000 high speed plus de Chiron en Tuttlingen, cada una equipada con un cabezal giratorio H/V (+/- 100°, husillo de 20.000, 75 Nm), una mesa giratoria (400 mm x 2.000 mm), un almacén de cadena para 24 herramientas HSK-63, robustas cubiertas de acero inoxidable, así como un control Fanuc 18i MB5 como CNC. Como particularidad, Chiron entregó los dos centros de mecanizado de precisión de 5 ejes con una mesa rebajada en 100 mm a una altura de 700 mm.
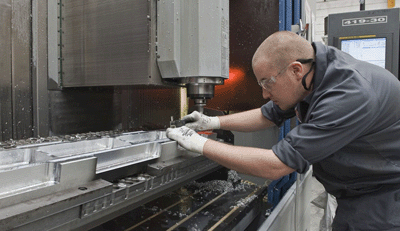
David Broomfield: “Hemos completado las máquinas sucesivamente hasta convertirlas en una solución turnkey y las instalamos en enero y mayo de 2007. La puesta en servicio la realizamos paralelamente al proceso e instruimos al mismo tiempo a los operarios". Entre las adaptaciones personalizadas del cliente estaba, por ejemplo, el equipamiento con un sistema de sujeción de punto cero, así como diferentes dispositivos de sujeción específicos para las piezas. También había un alojamiento con vacío para la fijación de la placa base del avión, así como varios alojamientos que se han fresado en la Mill 2000 3D para la sujeción sin deformación de los componentes estructurales para la cabina con su forma de bota de nieve. Para la medición de las piezas se ha integrado un palpador de medición Renishaw OMP en el software del control CNC. Este palpador tiene un puesto protegido dentro del cargador de herramientas y puede ser insertado automáticamente en el husillo como herramienta, en caso de ser necesario. Además, las máquinas venían equipadas con una alimentación de refrigerante de 30 bar con una reserva de 900 litros en cada caso, así como con dispositivos de aspiración del área de trabajo e instalaciones de filtro. Steve Fogg expresa su satisfacción: "Actualmente utilizamos la Mill para hasta 15 turnos por semana. Además de los componentes estructurales de grandes formatos para la Eclipse, también mecanizamos piezas claramente más pequeñas con cinco ejes. La gran mesa de trabajo resulta sencillamente ideal para sujeciones múltiples. Conseguimos unos tiempos de mecanizado desatendidos de hasta 3 horas. Y la preparación realmente no requiere mucho tiempo".
