La fabricación aditiva de Stratasys acelera el desarrollo de nuevos trenes Bombardier Transportation
Gracias a la tecnología de impresión 3D de Stratasys, el proveedor mundial de soluciones de movilidad Bombardier Transportation está acelerando la producción de piezas destinadas a los componentes internos y externos de sus trenes en los países de habla alemana.
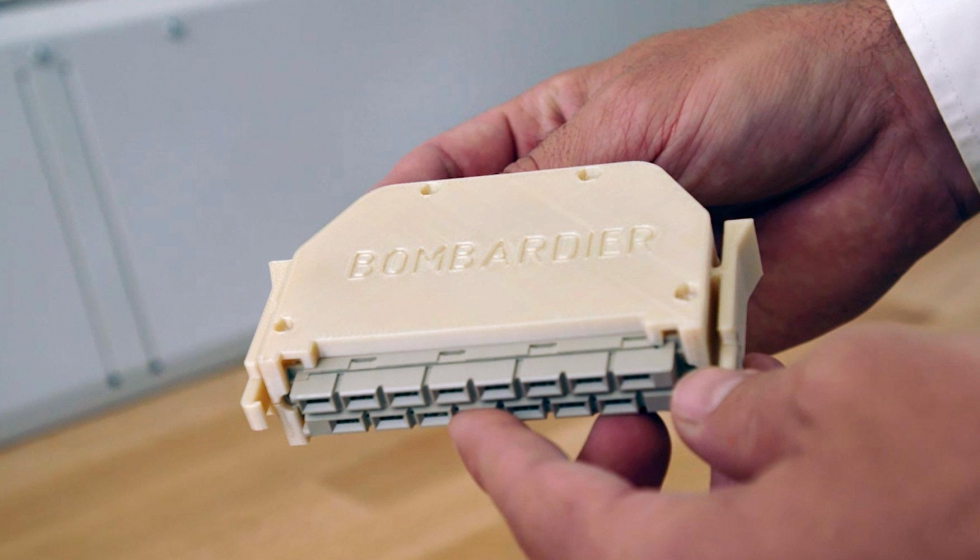
Según Marco Michel, vicepresidente de Operaciones de Bombardier Transportation, la integración de la fabricación aditiva de Stratasys en las instalaciones de Hennigsdorf ha permitido a la empresa fabricar ciertas piezas de repuesto personalizadas a petición mediante un inventario digital con un coste inferior.
André Bialoscek, responsable de la Integración Física de Vehículos de Bombardier Transportation Hennigsdorf, considera la instalación de una impresora industrial 3D F900 de Stratasys con tecnología FDM como un factor de transformación para la producción de piezas personalizadas.
“Nuestro objetivo durante el proceso de desarrollo de nuevos trenes es acelerar la producción de las piezas específicas del proyecto cuyo diseño requiere un cierto tiempo”, afirma Bialoscek. “A la vez que aceleramos la producción, tenemos que asegurarnos de que se mantiene una total funcionalidad, seguridad y repetibilidad. Con nuestra impresora 3D F900, podemos hacer todo eso, lo que ha constituido toda una revolución para nuestro departamento. Los conocimientos así adquiridos se transmitirán a nuestros proveedores en caso de producción en serie”.
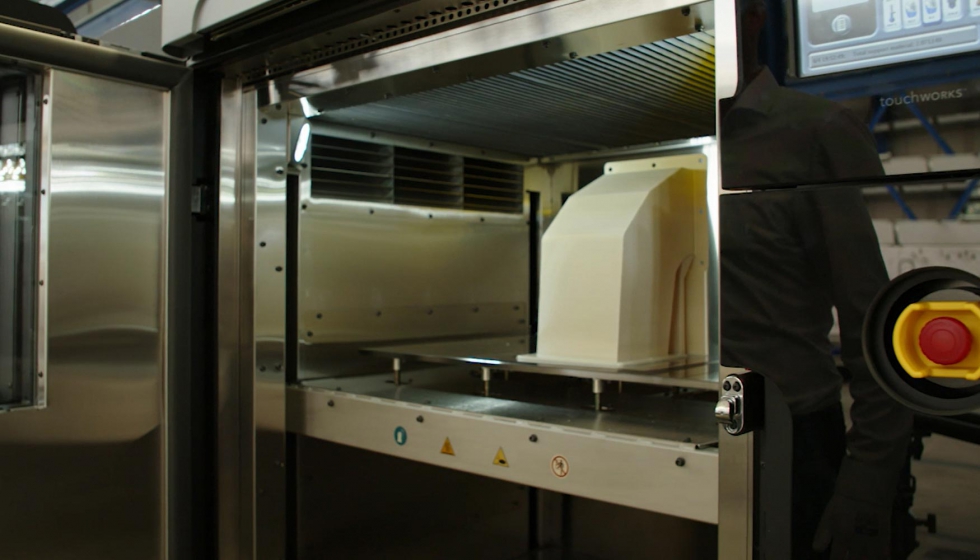
El departamento ha utilizado recientemente la F900 para fabricar un complejo sistema personalizado de ventilación para un tren prototipo alimentado por baterías, en mucho menos tiempo que el necesario en caso de aprovisionamiento externo de piezas.
La pieza de gran tamaño se imprimió en 3D en el material de resina Ultem 9085 de Stratasys que, debido a su peso ligero, reduce considerablemente el peso por pieza en comparación con otros materiales alternativos. Para los componentes internos producidos en Bombardier Transportation, con la resina Ultem 9085 se optimiza el uso general del material y el peso del componente. También es fundamental que el material cumple con las directrices de certificación ferroviaria EN45545-2 en cuanto a emisiones de humo, toxicidad e ignición, que es un requisito para todos los componentes de tren producidos en Bombardier Transportation.
“Con respecto al conducto de ventilación del tren que funciona con baterías, pudimos reducir el tiempo de producción de cuatro meses a aproximadamente cuatro semanas”, explica Bialoscek. “Esto supone un ahorro de tiempo de casi el 77%. Es un resultado increíble para el departamento y demuestra nuestra capacidad de producir ahora determinadas piezas a petición de acuerdo con nuestras necesidades exactas sin tener que esperar largos tiempos de producción ni sacrificar la calidad del material. Además, ahora es mucho más rápido sustituir las piezas durante el mantenimiento de trenes más viejos”.
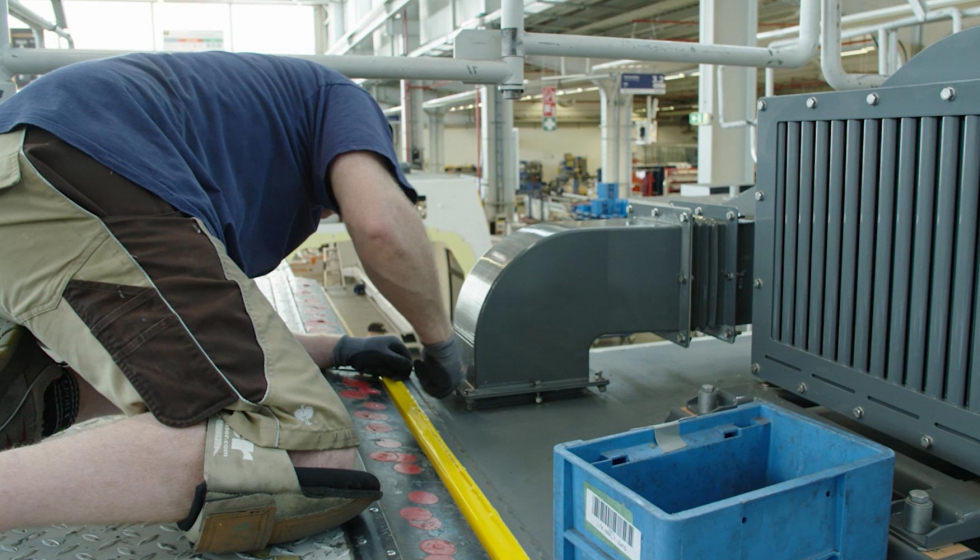
Bombardier Transportation utiliza ahora la F900 para crear un inventario digital y garantizar así que las necesidades de piezas de repuesto se satisfacen de inmediato, independientemente del modelo de tren o de su antigüedad. Con solo almacenar los escaneados 3D de las piezas, Bombardier Transportation evita el almacenamiento físico de las mismas. La F900 permite al equipo recrear rápidamente una de sus piezas «digitales» en una pieza certificada lista para el tren, lo que se traduce en un servicio rápido y directo a sus clientes.
“Ahora también estamos analizando la tecnología de impresión 3D PolyJet de Stratasys para nuestro proceso de validación de diseño y los resultados que hemos obtenido hasta ahora han sido convincentes”, comenta Bialoscek. “De hecho, en ingeniería, desde que utilizamos la impresión 3D para el prototipado, hemos reducido nuestro proceso de diseño en un significativo 30-40%, a la vez que aumentamos la calidad de nuestros diseños en general”.