Inspección de tubos e intercambiadores de calor mediante APRIS
Texto original: Vignesh Sivanandam / Traducción: Ricardo Ferrer-Dalmau
23/10/2019APRIS es un sistema de inspección de tubos e intercambiadores de calor diseñado específicamente para detectar defectos como fugas, aumentos en diámetro interno causado por adelgazamiento de la pared y obstrucciones encontradas en tubos industriales, como intercambiadores de calor, condensadores y calderas.
Una serie de innovaciones algorítmicas patentadas permiten que el sistema realice la separación de las ondas matemáticamente, y así identificar los defectos anteriores automáticamente, con un tiempo de medición del orden de 10 segundos por tubo. En este artículo presentamos varios casos de estudios de inspección de tubos que muestran cómo se identifican los diferentes defectos y como se crea el reporte de inspección.
La tecnología APR y sus conceptos básicos
Durante las últimas décadas se ha estudiado la reflectometría de pulso acústico en varios laboratorios de investigación para sondeo de sistemas tubulares. Los principios de esta técnica son fáciles de explicar, aunque las dificultades teóricas y prácticas involucradas en la implementación de esta tecnología son numerosas.
Se propagará un pulso acústico inyectado en un tubo semi-infinito de pared recta por el tubo sin generar ningún reflejo. Este pulso se puede medir mediante micrófonos pequeños con su superficie frontal a ras de la pared del tubo interno, a través de un orificio en esta pared. El micrófono medirá el pulso solo una vez, ya que pasa sobre el diafragma del micrófono.
Sin embargo, si el pulso encuentra una discontinuidad en la sección transversal, se crea una reflexión. La amplitud y la forma de la reflexión están determinadas por las características de la discontinuidad: una constricción creará una reflexión positiva, mientras que una dilatación (aumento de la sección transversal) creará una reflexión negativa.
Ninguna de estas discontinuidades cambiará la forma del pulso en su vecindad, pero la reflexión medida por el micrófono será una réplica atenuada y manchada del pulso que incide, debido a las pérdidas de propagación [4]. Un agujero en la pared del tubo, por otro lado, creará una reflexión que tiene una forma más complicada, afectada por el tamaño del agujero y la radiación de energía acústica al espacio fuera del tubo [3]. Los ejemplos esquemáticos de estos casos se presentan en la figura 1.
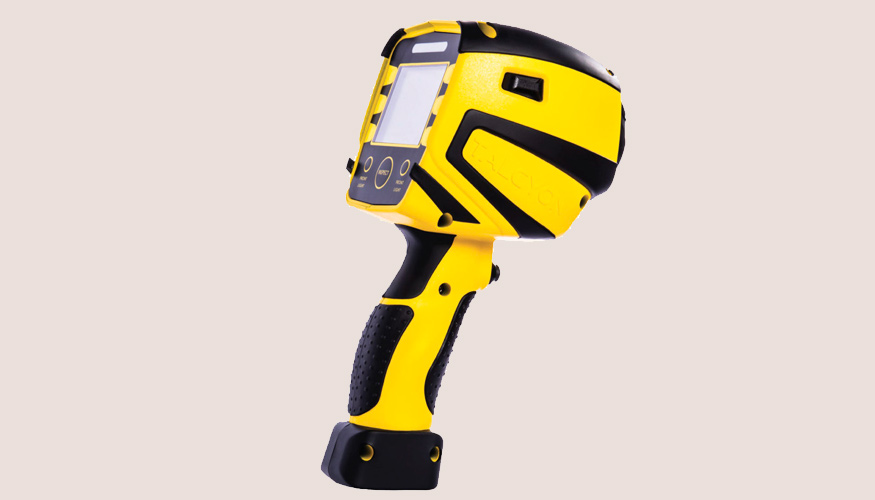
Aunque parte de la energía acústica presente en el pulso original se refleja en las discontinuidades, parte de esta energía continúa propagándose por el tubo. Cualquier otra discontinuidad creará nuevamente reflejos. Por lo tanto, diagnosticar la condición interna del tubo es una cuestión de interpretar correctamente los reflejos a medida que vuelven a los micrófonos.
Un aspecto de la interpretación es sencillo: el tiempo de llegada de un reflejo se puede usar para calcular la ubicación precisa de la discontinuidad, ya que tales reflejos se propagan a la velocidad del sonido. El segundo aspecto de la interpretación es más complicado, ya que implica inferir la naturaleza exacta de la discontinuidad a partir de la forma detallada de la reflexión.
APRIS, el sistema más práctico de APR
Un sistema APR práctico requiere de un transductor para crear el pulso y un micrófono que mida este pulso y los reflejos resultantes. El primer desafío para crear APRIS fue reducir su tamaño. Esto consistió principalmente en reducir los tubos fuente a 20 cm cada uno. Por lo tanto, todo el conjunto de transductores, micrófonos y tubos fuente podría instalarse en una sonda de mano, como se muestra en la fotografía de la figura 2. Todos los componentes electrónicos relacionados con la síntesis del pulso, amplificación, captura y análisis de los resultados, fueron instalados en una unidad separada.
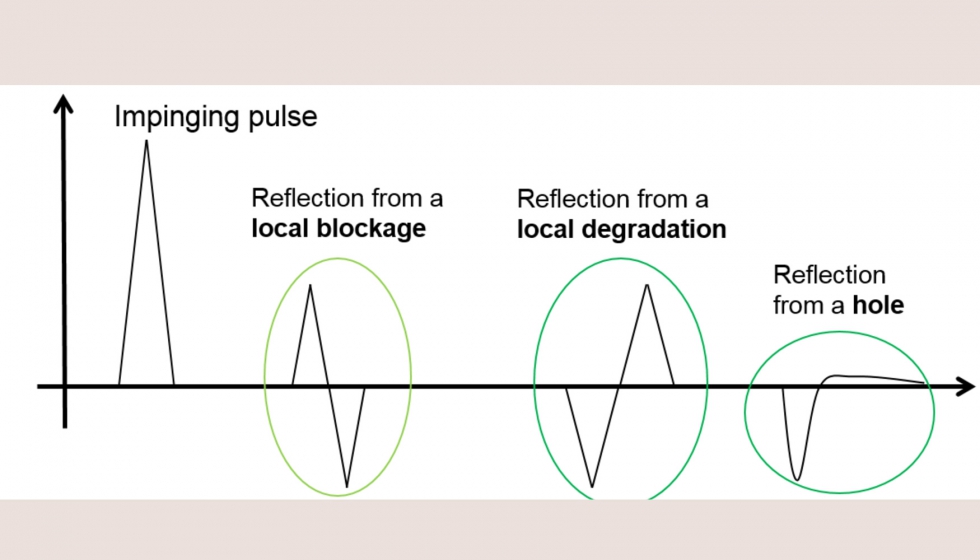
Figura 2: Ejemplo de aplicación del sistema APRIS.
Aplicando la tecnología de reflectometría de pulso acústico: APRIS
Varios factores determinan si el sistema APRIS identifica las fallas correctamente: el nivel de ruido de fondo, la distancia de la falla en el tubo (ya que los pulsos decaen con la distancia, debido a la fricción con las paredes del tubo) y la precisión de los algoritmos de detección. Para aislar estos factores lo más posible, se realizaron pruebas exhaustivas antes de aventurarse en el campo.
Seguidamente vamos a presentar los resultados de varios experimentos realizados, donde creamos defectos conocidos y determinamos si el sistema APR podría identificarlos correctamente.
Ejemplos genéricos de mediciones de laboratorio
Las pruebas iniciales se realizaron en tubos de aluminio con un diámetro interno de 25,4 mm y un espesor de pared de 1,04 mm. El APR es insensible al material del que están hechos los tubos. Por lo tanto, el aluminio se utilizó por conveniencia. Lo mismo los resultados se obtendrían si estuvieran hechos de latón, acero, titanio o cualquier otro material rígido. Se crearon varios defectos genéricos: se perforó un orificio de 0,5 mm de diámetro en un tubo. Se anotó otro tubo en el interior con un torno y se insertó una arandela en un tercer tubo para crear una constricción. Las figuras 3, 4 y 5 muestran las mediciones resultantes registradas por el sistema APRIS. Los 3 tipos de defectos se muestran claramente en comparación con una medición de referencia tomada de un tubo diferente. Estos tubos tenían una longitud de 3 metros, que es más corta que la mayoría de los tubos de condensador, pero los resultados fueron extremadamente alentadores. También se desarrollaron algoritmos para la detección automática y la clasificación de defectos, aunque no se discutirán aquí en detalle.
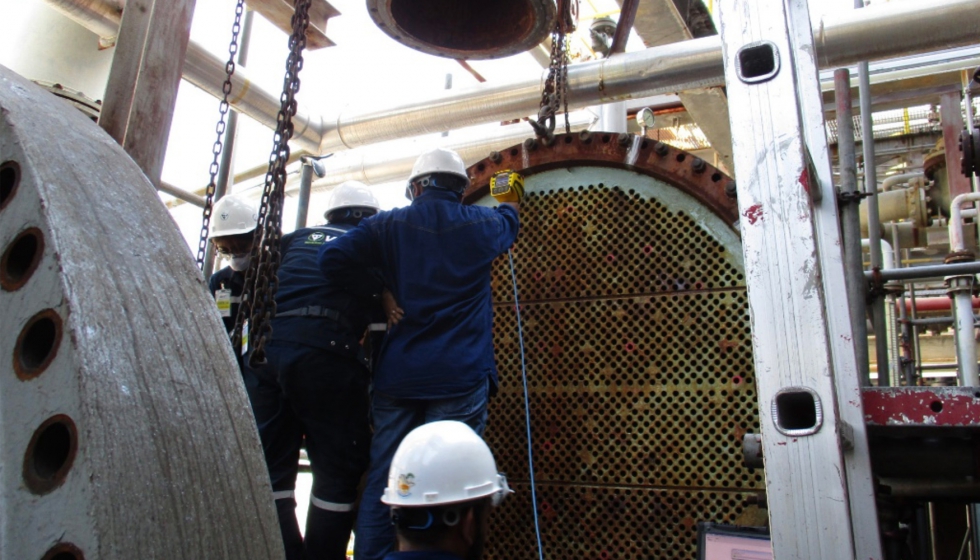
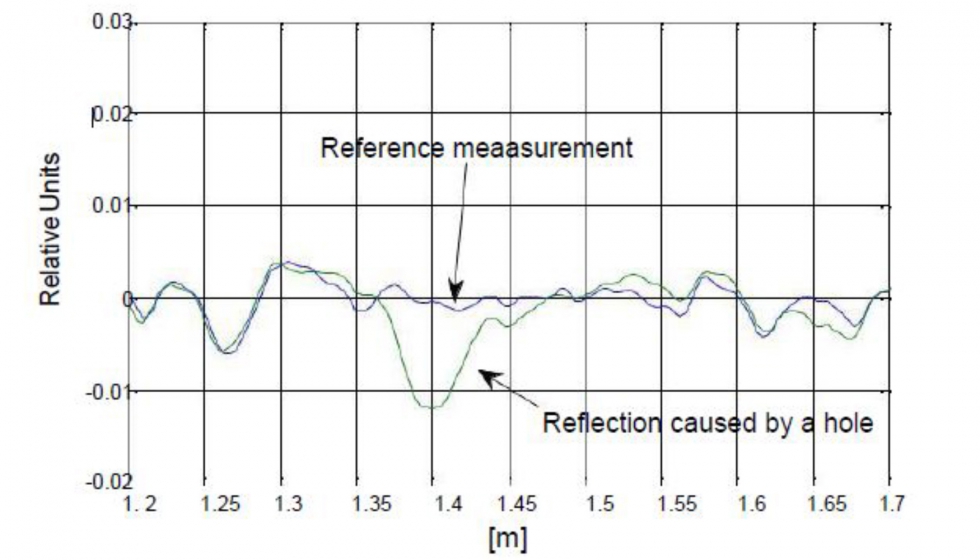
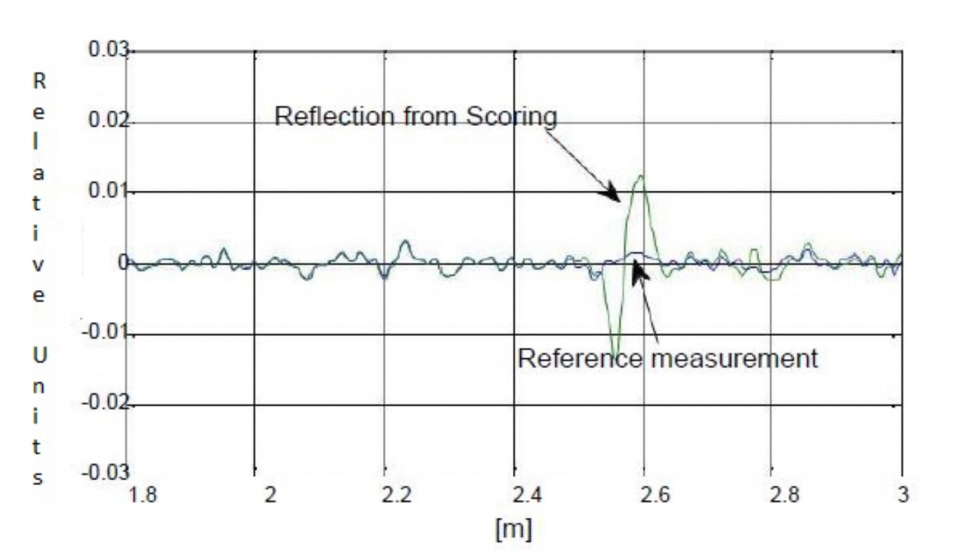
Pruebas de inspección en mantenimiento
A continuación, describimos dos test efectuados en aplicaciones reales, el primero en inspección de mantenimiento de emergencia, y el segundo dedicado a un mantenimiento rutinario.
Caso de mantenimiento de emergencia
En febrero de 2018 los sensores de una turbina de una central eléctrica mostraban que había una fuga en algunos de los tubos. Este problema ocurrió cuando la planta estaba trabajando a pleno rendimiento, por lo que la turbina no podía pararse para efectuar una inspección. El personal de mantenimiento decidió taponar bastantes tubos de unos de los cuadrantes en el que se sospechaba que estaban las fugas.
La noche siguiente se inspeccionaron los tubos del cuadrante sospechoso mediante APRIS. A pesar que la turbina estaba en funcionamiento y había un alto ruido de fondo, las pruebas se pudieron llevar a cabo con resultados positivos. La inspección se llevó a cabo de manera rápida y se encontraron 6 tubos con indicaciones de posibles fugas y acumulación de suciedad. En la siguiente figura se muestra la señal de uno de esos tubos.

Caso de mantenimiento rutinario
En este caso se utilizó APRIS para inspeccionar un condensador de una central de ciclo combinado durante la parada de mantenimiento. Se retiraron las placas frontales del condensador y se pudieron inspeccionar 1140 tubos de un cuadrante en 190 minutos (a 10 segundos por tubos). A continuación, mostramos el mapeo de este cuadrante.
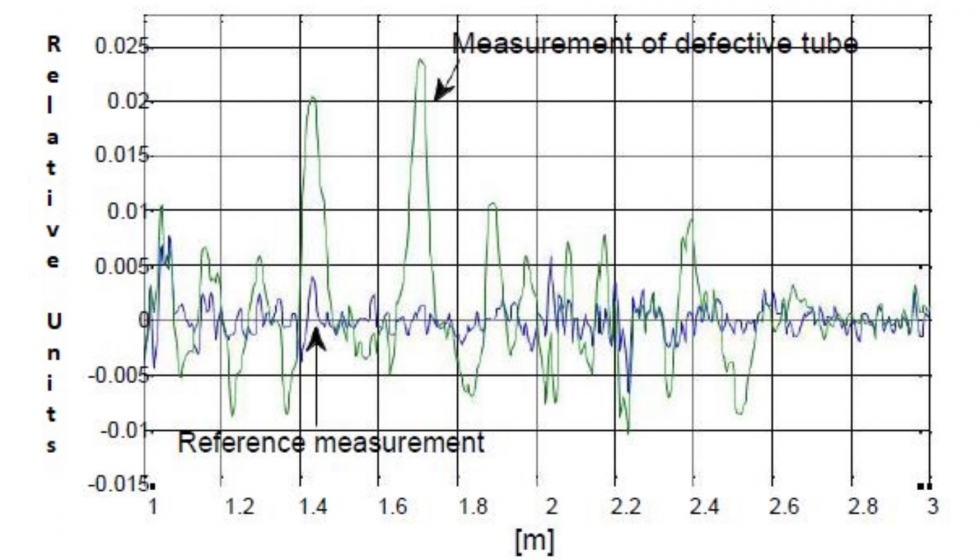
Conclusiones sobre la inspección interna de los tubos con APRIS
Inspeccionar este condensador usando APRIS reveló información interesante en referencia al estado interno de los tubos. Al igual que en otras tecnologías, para poder inspeccionar correctamente los tubos con APRIS es necesario una limpieza previa de los mismos, se ha de evitar que haya suciedad que tapone las posibles fugas o reducciones de espesor para evitar que éstos queden sin detectar. Mediante la inspección por APRIS se pudo detectar que muchos de los tubos no se habían limpiado correctamente. A continuación, mostramos las señales de uno de estos tubos.
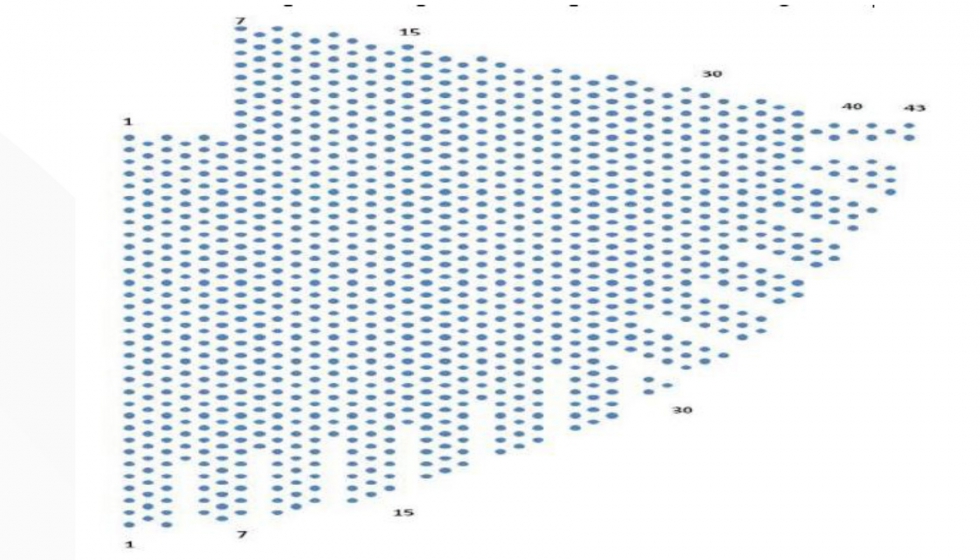
Finalmente, apareció un patrón interesante de degradación del tubo de pared en un área del condensador. La mayoría de los 80 tubos encontrados en las columnas 35 a 43 presentaron una de estas dos indicaciones: un aumento local en la sección transversal, que indica picaduras, o un aumento de la sección transversal en aproximadamente el último medio metro del tubo, en promedio. Las Figuras 9 y 10 muestran una medida cada una.
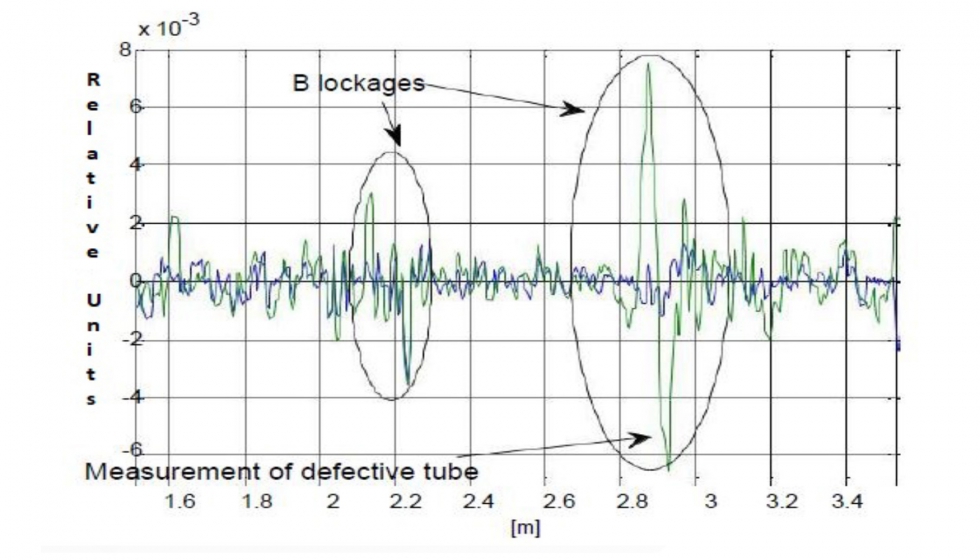
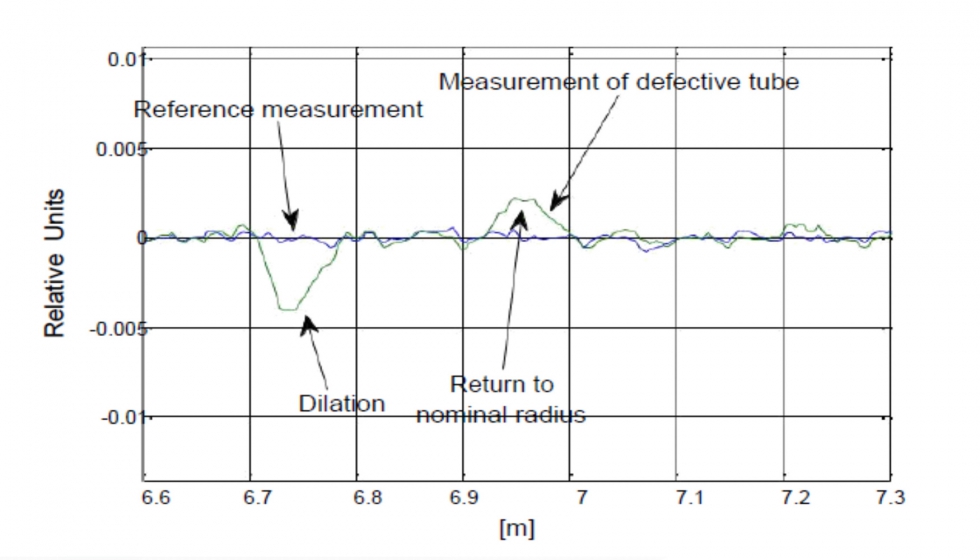
Figuras 9- 10.
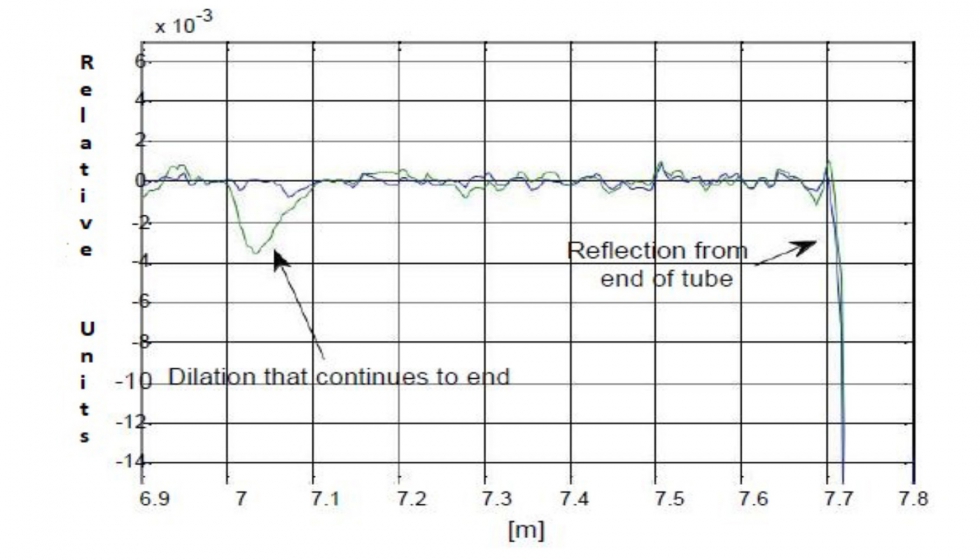
Dados los resultados obtenidos en laboratorios como en campo, se puede apreciar que APRIS es una buena solución para inspección en interior de tubos, con las siguientes ventajas:
- La inspección es rápida y fiable (unos 10 seg por tubo).
- El material del tubo y su geometría no afectan a la inspección.
- Posibilidad de detectar fugas, disminución de espesores y sobre espesores
- Posibilidad de certificar que la limpieza de los tubos es correcta.
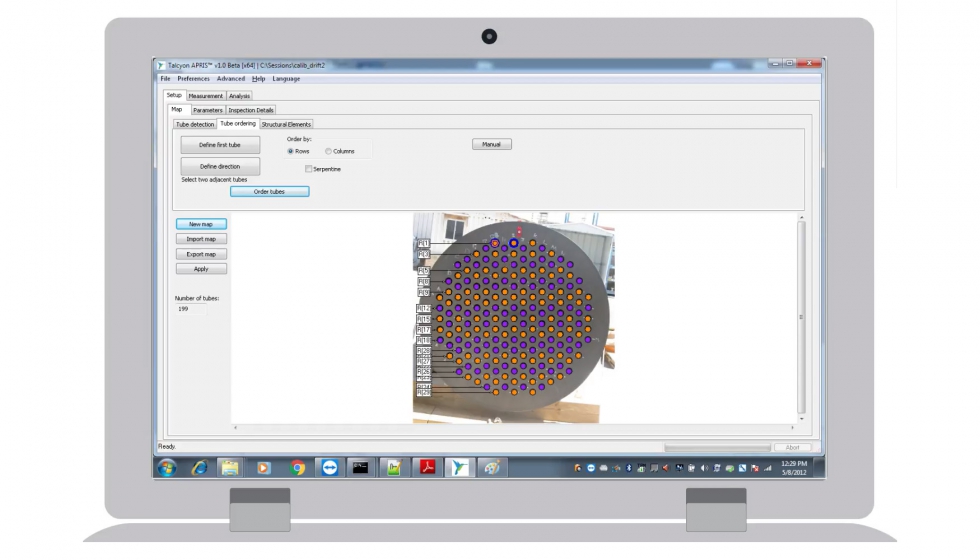
Referencias
[1]. N. Amir, U. Shimony, G. Rosenhouse. ‘A Discrete Model for Tubular Acoustic Systems with Varying Cross Section – The Direct and Inverse Problems. Part 1: Theory’. Acustica 81, [1995] 450-462.
[2]. N. Amir, U. Shimony, G. Rosenhouse. ‘A Discrete Model for Tubular Acoustic Systems with Varying Cross Section – The Direct and Inverse Problems. Part 2: Experiments’, Acustica 81, [1995] 463-474.
[3]. V. Chilekwa, D.B. Sharp and T.J.W. Hill, ‘Leak Detection in Musical Wind Instruments Using Acoustic Pulse Reflectometry’, Proceedings of the Stockholm Music Acoustic Conference, August 6-9, 2003 (SMAC 03), Stockholm, Sweden.
[4]. N. Amir, U. Shimony, G. Rosenhouse, ‘Losses in Tubular Acoustic Systems – Theory and Experiment in the Samples Time and Frequency Domains’, Acustica l 82 (1996) 1-8.
[5]. Victor Chilekwa, David Sharp, ‘Detection, location and sizing of multiple leaks in ducts’. Forum Acusticum 2005.
[6]. Application and methods for non-destructive testing of tubular systems PCT: Application No.IL05/000860 USPTO: No.60/703,450