Sustitución de mecanizado en 5 ejes en piezas esbeltas por fabricación aditiva para el sector de la ciencia
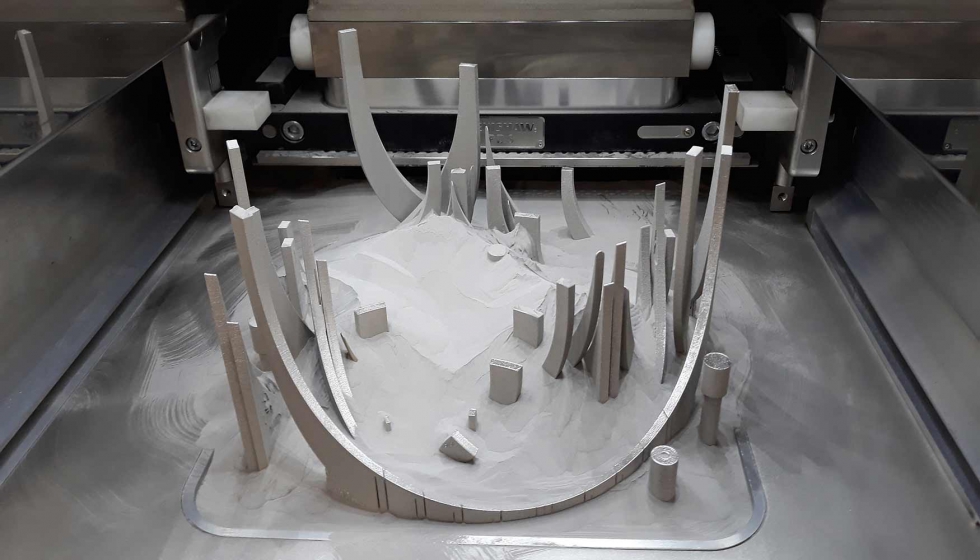
- Sector: ciencia
- Reto: fabricación aditiva vs. convencional de un kit de separadores de 316L para imanes superconductores. Análisis técnico-económico de viabilidad.
- Solución: el cliente ha visto una oportunidad clara de mejora de procesos y ha apostado por la fabricación aditiva en el caso de estos kits que antes se fabricaban por mecanizado.
Reto
El equipo de fabricación aditiva de Egile ha colaborado con un cliente del sector de la ciencia para realizar un análisis técnico-económico de fabricación aditiva de un kit de piezas que en la actualidad se fabrica por mecanizado y otros procesos convencionales.
Estos kits forman parte de imanes de altas prestaciones y cada uno está formado por unas 25-30 piezas de acero inoxidable 316L de geometría compleja, todas ellas diferentes entre sí. Estos kits se fabrican por mecanizado convencional (torneado y fresado), tras el cual las piezas son procesadas por electroerosión por hilo para generar unas ranuras que les dotan de cierta flexibilidad posibilitando el montaje. En cuanto a la demanda, el cliente necesita series cortas y las continuas mejoras que realizan en el diseño de estos imanes implican constantes pequeñas modificaciones en las geometrías de estos kits.
Las limitaciones de las tecnologías convencionales con las que se fabrican hasta el momento son:
- La variedad de geometrías en cada kit supone un gasto muy alto en utillajes de mecanizado que repercute fuertemente en el coste de las piezas, ya que se trata de series cortas.
- La complejidad de la geometría supone un aumento en tiempos de fabricación, ya que, por cada pieza, hay que partir de un bloque de 316L e ir mecanizando en varias operaciones.
- Los largos tiempos de fabricación, el continuo cambio de utillajes y la necesidad de dos procesos diferentes (mecanizado y electroerosión por hilo) supone que el lead time aumente.
- La repercusión económica que suponen los cambios de diseño en fabricación (adaptación programas CNC y coste de nuevos utillajes) hace que el cliente no siempre pueda mejorar su producto y tenga que conformarse con diseños obsoletos.
Solución
En este caso, la fabricación aditiva parece una tecnología más adecuada, en concreto la tecnología SLM (Selective Laser Melting) de lecho de polvo, por las complejas geometrías y las pocas unidades a fabricar:
- La necesidad de utillajes desaparece.
- La complejidad de la geometría no supone un aumento en el tiempo de fabricación.
- Los cambios en diseño de las piezas no suponen un coste añadido por lo que el cliente puede implementar de manera inmediata cualquier mejora en su producto.
Sin embargo, para valorar la factibilidad de cambiar el proceso de fabricación, es necesario un análisis preciso de los condicionantes de la fabricación aditiva para este caso.
Para ello, primeramente, se ha realizado un análisis de la simulación de las distorsiones durante la fabricación aditiva observándose que hay zonas de las piezas con unas distorsiones considerables, que imposibilitarían el montaje final de las piezas, por lo que es necesario comprender las causas y plantear una solución.
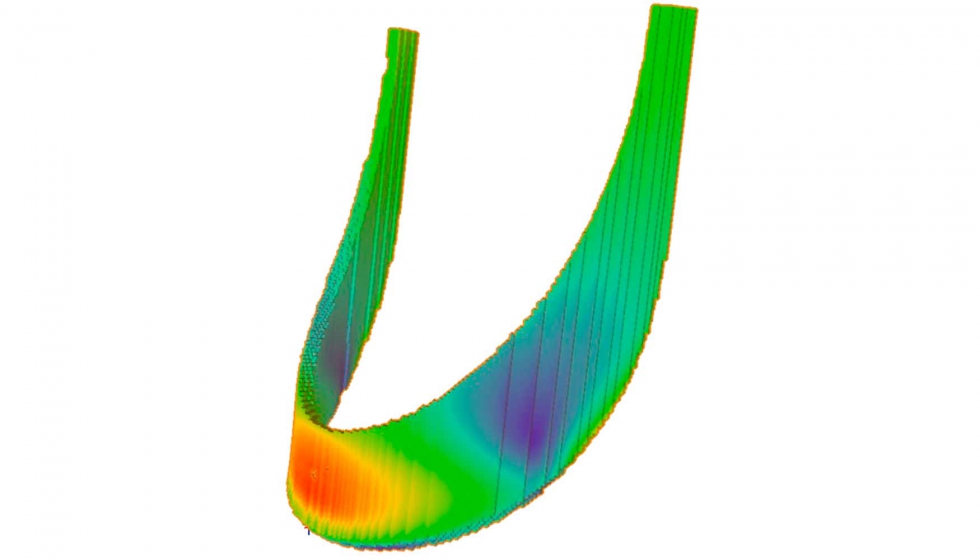
Las distorsiones observadas tienen lugar en la parte con mayor masa de las piezas y con mayor sección a fundir en cada capa, debido a las tensiones residuales que se generan durante el proceso de impresión.
Durante el análisis de los posprocesos, se propone al cliente integrar la fabricación de las ranuras en la propia impresión de las piezas (realizadas mediante electroerosión por hilo hasta la fecha). Al incluir las ranuras en el sólido, durante la impresión capa a capa, la sección a fundir pasa de ser una sola a convertirse en varias pequeñas secciones independientes.
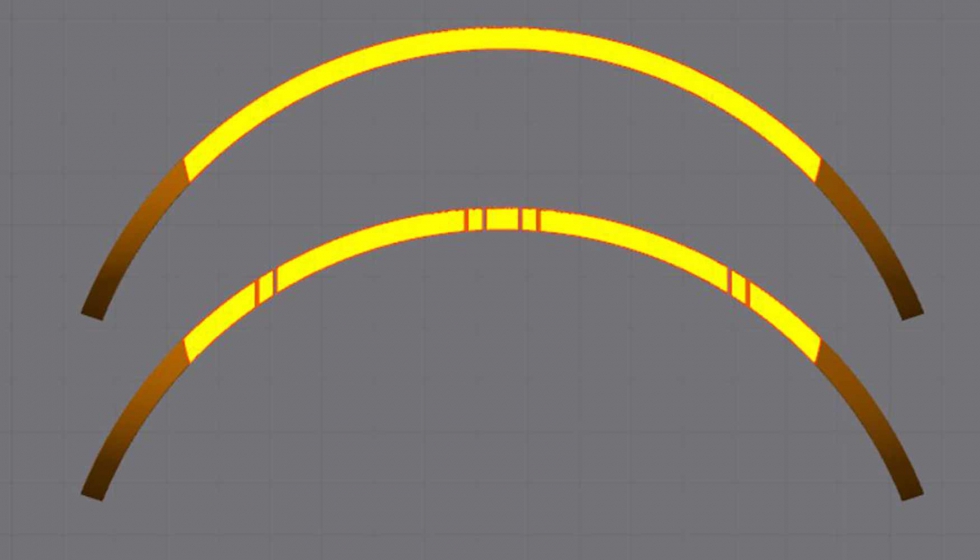
Finalmente, se ha realizado una optimización topológica de la pieza con el objetivo de reducir los tiempos de fabricación y el peso de las piezas. Para ello, se definen las condiciones de contorno, como las solicitaciones mecánicas, y el volumen disponible. Los resultados obtenidos han sido una reducción de peso de un 33% y un 44% aplicando estrategias de estructura lattice y optimización topológica, respectivamente.
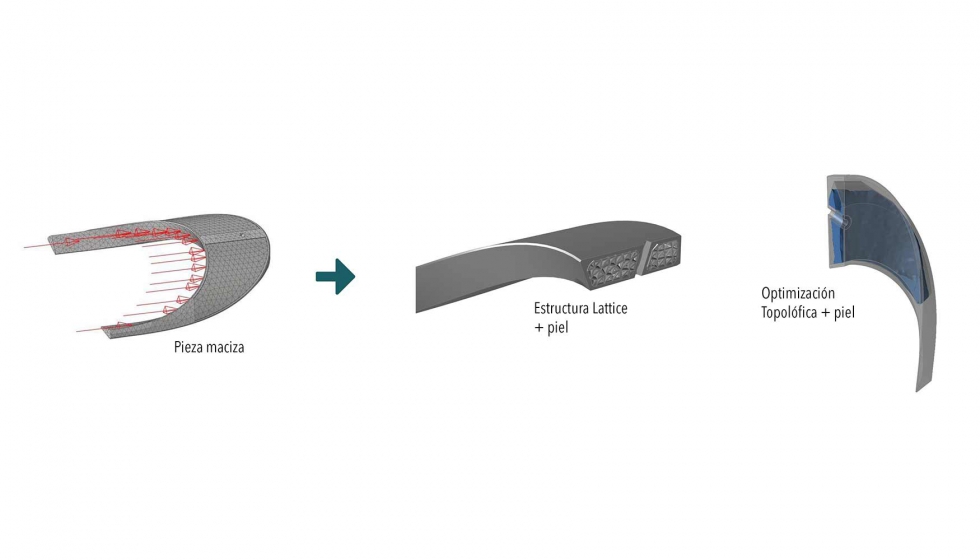
Beneficios

La capacidad de Egile de fabricación de piezas integrales en SLM, incluyendo los posprocesos, le permite tener una visión completa de toda la cadena de valor y ofrecer un acompañamiento tecnológico al cliente desde las etapas de diseño. En este caso, los principales beneficios han sido los siguientes:
- La integración de la geometría final en el proceso de impresión (incluyendo el ranurado, electroerosión por hilo), que incide en una reducción del lead time y del coste de fabricación de las piezas.
- La eliminación de utillajes y la flexibilidad para fabricar, implica que el cliente puede implementar de manera inmediata cualquier cambio de diseño o mejora en su producto: geometría, optimización topológica, estructura lattice, etc.