Entrevista a Ramón Suárez, director de I+D+i del Centro de Investigación Metalúrgica IK4-Azterlan
IK4-Azterlan es un Centro Tecnológico especializado en metalurgia y procesos de transformación metálica con más de 30 años de experiencia en tecnologías de fabricación de componentes de seguridad, críticos en los vehículos, como la fundición, la estampación y la forja. Esta actividad le ha convertido en testigo directo y partícipe de la profunda transformación que, de la mano del automóvil, estos sectores industriales están viviendo. En palabras de su director de I+D+i, Ramón Suárez, las empresas de transformación metálica tienen por delante el reto de demostrar a fabricantes de vehículos y a diseñadores de componentes “las oportunidades que pueden ofrecer los materiales metálicos avanzados y los procesos de transformación” y asegura que “las tecnologías 4.0 tienen mucho que ver en ello”.
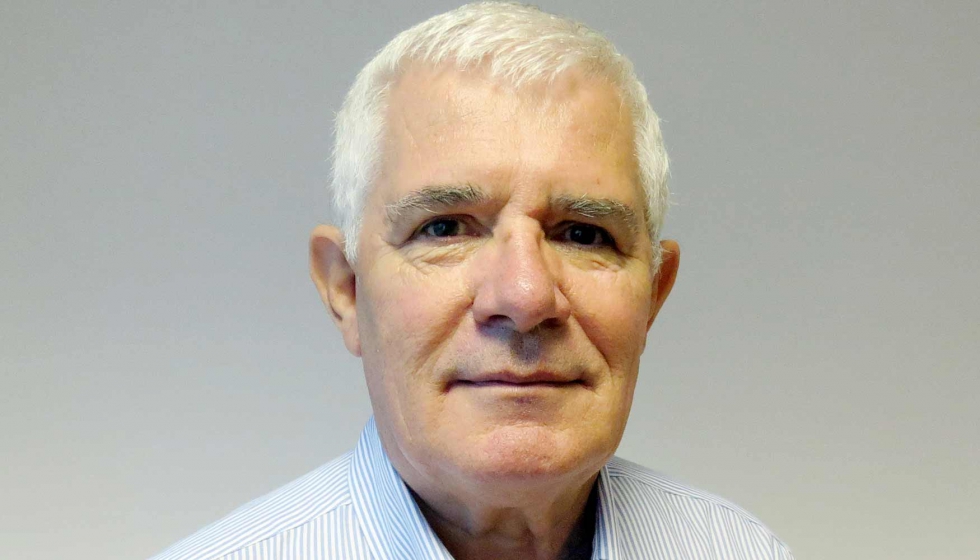
El profundo cambio que vive el sector del automóvil tiene una importante repercusión sobre sus sectores proveedores…
Y no puede ser de otra forma. La transición hacia el vehículo eléctrico y la necesidad, en general, de aligerar el peso del automóvil dirigen la mirada hacia los componentes del vehículo, e inherentemente, hacia su diseño y al material o la aleación aplicada en su fabricación. Los materiales metálicos, que son nuestro ámbito de trabajo, siguen y seguirán teniendo un rol relevante en la industria de automoción, pues ofrecen características de resistencia y desempeño, que difícilmente pueden ser sustituibles por otros materiales a un coste competitivo.
Sin embargo, ello no quiere decir que no deban producirse cambios… Al contrario, es necesario desarrollar nuevas aleaciones, más resistentes y ligeras, que permitan explorar nuevas oportunidades de aplicación y diseño.
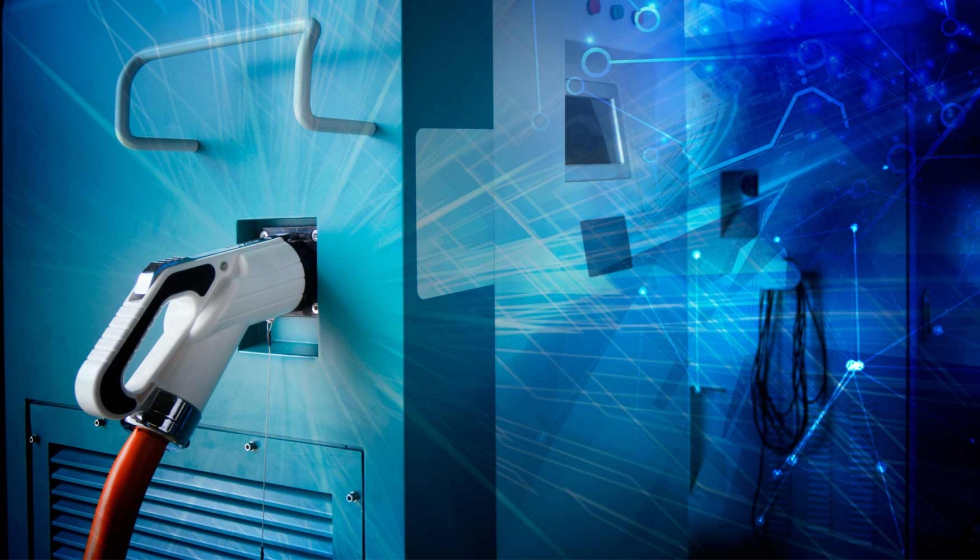
¿Cómo es esto posible?
En el ámbito de los materiales metálicos, es importante que las industrias de transformación metálica y OEMs trabajen de la mano para ‘romper’ los límites actuales. Se trata de preguntarse “qué características” necesitamos para conseguir los mejores y más eficientes diseños y buscar nuevas aleaciones con propiedades mejoradas, que nos ayuden a ir en esa dirección.
En el ámbito de los procesos de transformación, una de las claves es asegurar la fiabilidad de las piezas fabricadas, reduciendo la cantidad de rechazo, tanto interno como en cliente, asegurando la robustez de los procesos. Es necesario también reducir las operaciones de acabado que no aportan valor añadido. Del mismo modo, estas industrias tienen que ser capaces de dar respuesta a nuevas geometrías y funcionalidades, en base a requisitos de diseño y desempeño óptimos.
En todos estos ámbitos, las tecnologías 4.0 y el análisis de datos directamente relacionados con los procesos de fabricación y con el comportamiento de las piezas y los materiales es clave para seguir mejorando.
¿Cómo ayudan las tecnologías 4.0 y el análisis de datos a la mejora de los componentes metálicos?
La cantidad de datos relacionados con el proceso de fabricación de un componente potencialmente capturables es enorme. Desde que una materia prima inicia su proceso de transformación, pasando ya como componente formado por diversos procesos de acabado (mecanizado, tratamientos térmicos…), hasta su ensamblaje en el vehículo y su uso final, existe la posibilidad de capturar datos que ofrezcan información de gran relevancia sobre su desempeño en cada una de las fases anteriormente mencionadas.
Por supuesto, no todos estos datos son relevantes. Saber seleccionar y correlacionar aquellos que aportan valor, es el reto principal de las empresas que trabajan con tecnologías 4.0.
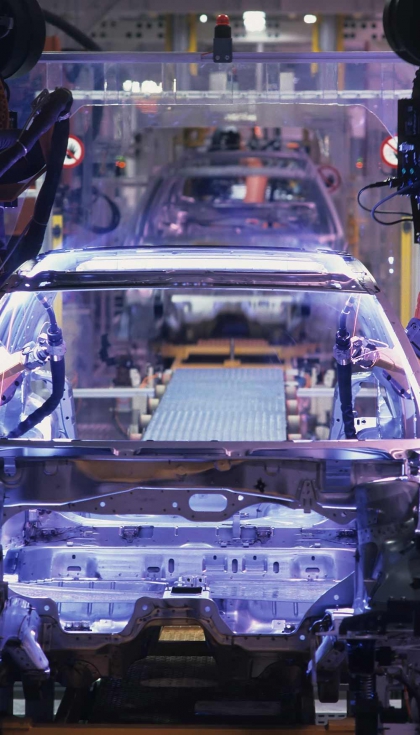
¿Cuál es su experiencia en este ámbito?
En IK4-Azterlan llevamos muchos años trabajando el ámbito de la explotación de datos ligados a procesos metalúrgicos. Hemos desarrollado software propio y contamos con sistemas de control inteligentes que nos permiten predecir la calidad final del componente fabricado y, lo más importante, aplicar acciones correctivas durante el propio proceso en caso de prever un mal resultado.
Actualmente, en el seno del proyecto Digimat, cofinanciado por la Unión Europea dentro del programa Fast Track to Innovation (H2020), estamos creando una arquitectura digital innovadora con la empresa portuguesa Sakthi (fundición) y la compañía alemana Continental Teves (fabricante de sistemas de freno). Con este proyecto, queremos dar un paso más, incorporando sensórica avanzada y explotando datos de ensayos actuales e históricos (destructivos y no destructivos) llevados a cabo sobre referencias actuales de sistemas de freno que se encuentran en el mercado. Ello nos permitirá optimizar, tanto el desempeño del material, como mejorar el diseño del componente y el rendimiento final de las piezas.
Se trata de un proyecto muy ambicioso con el que esperamos llegar al 35% del mercado europeo de fundición en los próximos 5 años.