Ficep S3 muestra su ‘expertise’ en fabricación aditiva ante otras empresas industriales
Que la fabricación aditiva despierta interés no es ninguna novedad. Que levanta pasiones entre sus defensores, tampoco. Pero que sin duda las empresas industriales necesitan más información y, sobre todo, más demostraciones reales de sus aplicaciones para su día a día, es igualmente cierto. Quizá por ello desde Ficep S3 se organizó a primeros de febrero una jornada técnica con la participación de algunos de los nombres más representativos de la fabricación aditiva de Catalunya ante diversas empresas industriales.
Ficep S3 es una ingeniería industrial dedicada a la maquinaria industrial y especializada en ingeniería de fabricación aditiva, con el objetivo de apostar por la investigación y la innovación permanente, que quiso exponer en una jornada técnica su experiencia en la aplicación de la impresión 3D en sus proyectos industriales. Para ello se acompañó de algunos de los actores más representativos de la fabricación aditiva de Catalunya que, a través de sus presentaciones, ofrecieron una perspectiva global sobre la fabricación aditiva en el entorno del diseño y la producción industrial. Bajo el lema ‘Manufactura aditiva, diseñando para la función’, los ponentes abordaron cada uno desde su punto de vista, las ventajas que puede aportar esta tecnología a la vez que mostraron las herramientas necesarias para introducirse en la fabricación aditiva.
El objetivo, en palabras de la propia empresa, era “exponer la posibilidad de la fabricación aditiva y, a la vez, romper la barrera de la desconfianza a través de Ficep S3 como ejemplo de empresa que ha hecho este cambio de paradigma”. Recordar que la ingeniería inició este proceso a mediados de 2018 de la mano de Nuno Neves, director y cofundador de Ficep S3.
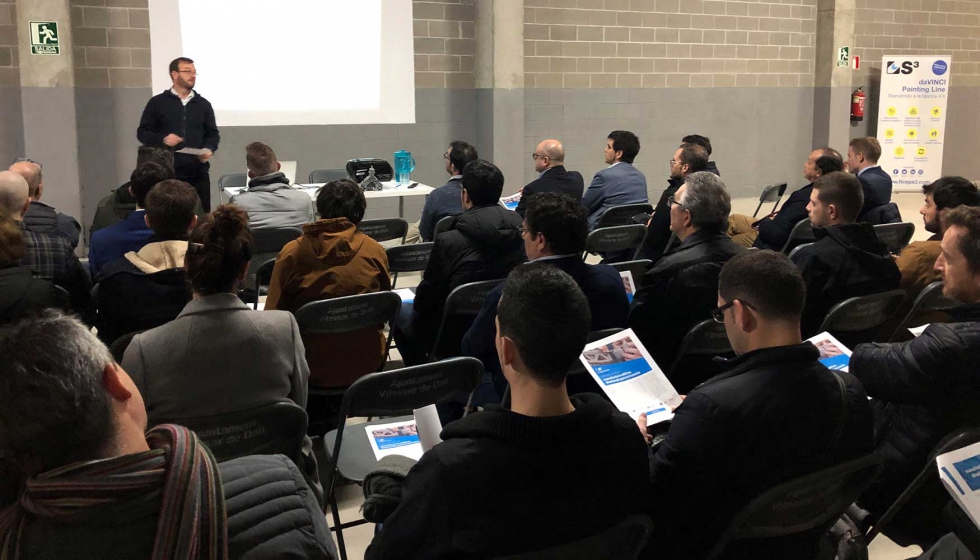
Introdujo la jornada Tomás Mejía, de Acció - Agència per a la Competitivitat de l’Empresa. Mejía expuso que actualmente existen en Catalunya un centenar de empresas proveedoras de fabricación aditiva, de maquinaria, de servicios de ingeniería… apuntando la importancia de esta tecnología y el potencial de crecimiento de la misma.
Diseñar para aditiva. Un cambio de concepto
Alfredo Gallozzi, ingeniero industrial especialista en diseño y formador en software de diseño 3D, expuso las diversas opciones de diseño en 3D actuales y cómo valorar el programa más adecuado según las necesidades de las empresas. En este sentido, hizo un repaso a las diferencias entre diseño 2D/3D como, por ejemplo, entre modelado sólido y modelado de superficies. En el primer caso, es un diseño más rígido y estricto, con un resultado final siempre sólidos y un proceso más sencillo, mientras que el modelado de superficies es una metodología libre, con menos restricciones, de formas suaves y estéticamente más atractivas, en un proceso de diseño más complicado y con la necesidad de llegar a una solución sólida para poder producir.
Igualmente, el diseño 2D es de tipo paramétrico —controlado mediado parámetros, relaciones y dependencias; con capacidad de configurar y capacidad de vincular archivos y trabajar de manera colectiva. En cambio, el diseño 3D es no paramétrico, con una metodología libre y rápida, sin parámetros ni relaciones, “con el único pensamiento de lograr la geometría más adecuada”.
Gallozzi concluyó apuntando que las tendencias actuales en el entorno de la producción van en la línea de los programas de diseño generativo, mientras que, en ámbitos más artísticos, la tendencia es la escultura digital. “El futuro va hacia la realidad virtual y la realidad aumentada, para lo que hoy ya existen programas de diseño”.
Aprender de los precedentes
A continuación, expusieron sus experiencias Bruno Romero, especialista en aplicación de la fabricación aditiva en HP, y Roman Reiner, ingeniero de diseño especializado en diseño generativo en EOS. El primero, hizo un breve repaso a los equipos de HP para fabricación aditiva y compartió las lecciones aprendidas de su experiencia con esta tecnología. En primer lugar, comentó el “enorme” potencial de la fabricación aditiva en la industria, apuntando a los factores que inciden en su implantación como el coste del material, la selección de los materiales o el diseño para aditiva, entre otros.
Por su parte, Reiner expuso que para diseñar con éxito para la producción en SLS —sinterizado selectivo mediante láser— es necesario tener en cuenta, en la mente, todo el proceso: “Las tres dimensiones, la orientación, la superposición de las capas y las tolerancias admitidas”. Asimismo, apuntó que es necesario también tener en cuenta la temperatura aplicada “puesto que esta afecta al grosor de la pieza, igual que el modo en que se aplica el polvo del material”. En su opinión, “la fabricación aditiva bien diseñada puede ayudar a reducir del orden del 80% el volumen del producto, reduciendo el peso y la cantidad del material”, concluyó.
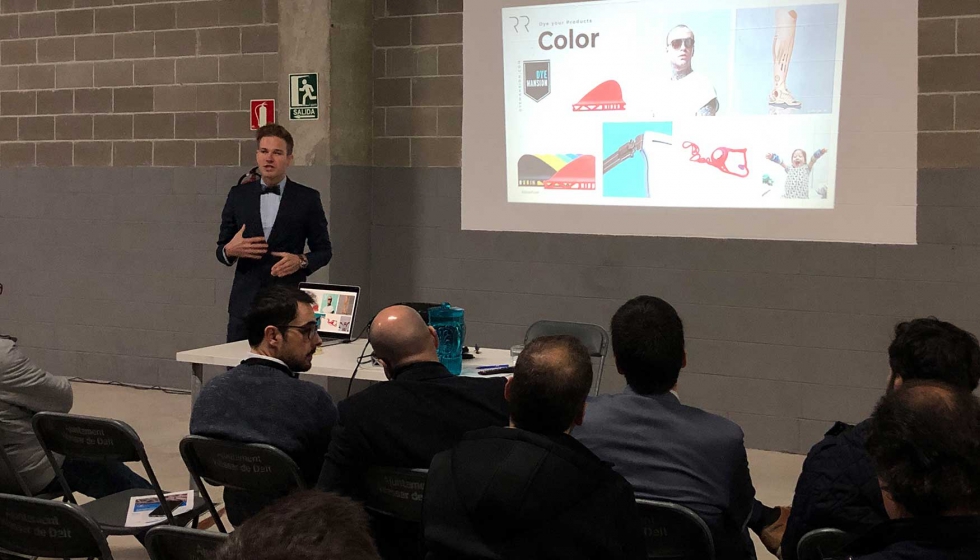
Ficep S3, un ejemplo del cambio a seguir
Nuno Neves, cofundador y director de Ficep S3, y especialista en fabricación aditiva, expuso las ventajas que desde la ingeniería valoran de esta tecnología: “la reducción de stock de piezas, del uso de lubricantes, lo que permite un proceso mucho más limpio y un menor coste para el medio ambiente, y la posibilidad de desarrollar en una sola pieza, evitando posteriores ensamblajes”, para mostrar a los asistentes algunos ejemplos de las piezas realizadas en la empresa.
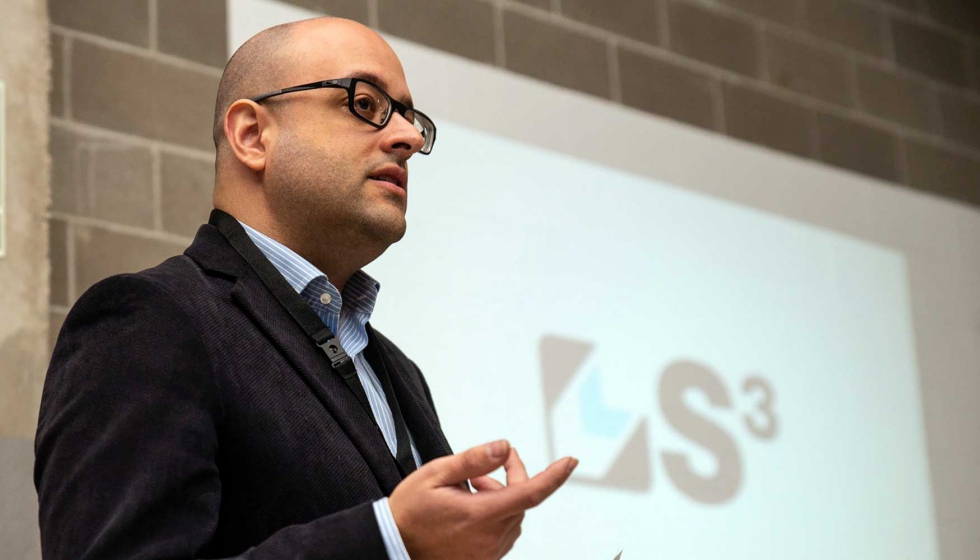
Le siguieron Josep Rius, B.U. Manager de Abrast AM Surface Finishing, y Marc Travesset, especialista en fabricación aditiva en Seat. El responsable de Abrast entró con detalle en los tratamientos superficiales a realizar posteriormente a la producción mediante tecnología aditiva. Unos trabajos que permiten añadir valor a las piezas impresas en 3D. En este sentido, explicó que el material abrasivo usado por Abrast consiste en material metálico esférico, “con algunas ventajas como evitar trabajos posteriores”. Un proceso indicado para piezas metálicas sometidas a deformaciones, molidos o tratamientos térmicos y que podría ser útil de forma similar para piezas plásticas.
Por su parte, el representante de Seat compartió con los asistentes el proyecto de un frontal realizado en aditiva que, si bien se fabrica en Alemania, en Catalunya diseñó en Seat: concretamente se trata de una parte plástica, ‘softnose’ que protege partes concretas de la chapa y evita daños tanto al automóvil como a los peatones en caso de colisión. Asimismo, Travesset también comentó que Seat utiliza también la fabricación aditiva para desarrollar posicionadores y utillaje en la cadena de montaje a fin de reducir el coste, además de usar galgas de control de calidad, calibres, etc. “En definitiva, productos que no llegan al producto final pero que sí están totalmente involucrados en el proceso de producción”, concluyó.
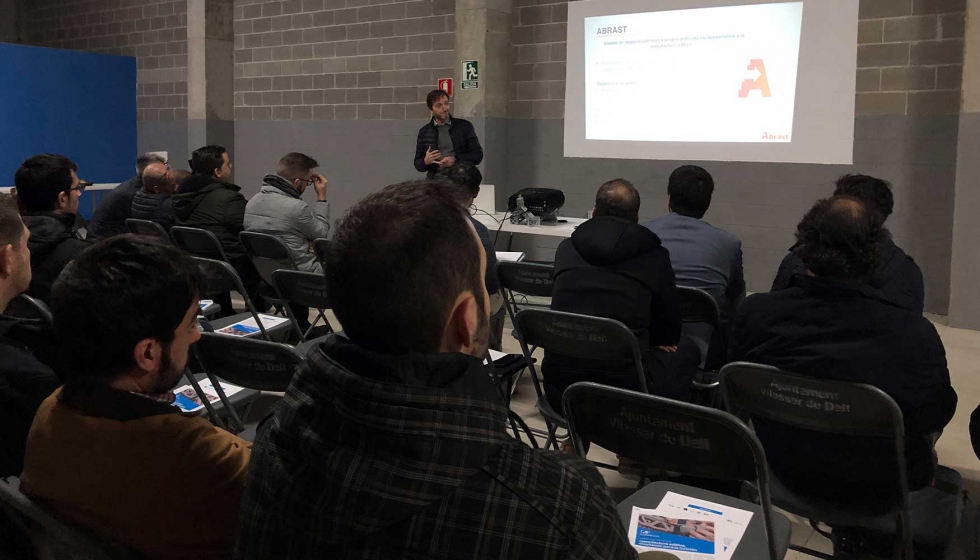
La jornada acabó con una mesa redonda entre los ponentes y moderada por Antoni Camí, experto en fabricación aditiva de Fira de Barcelona. En ella se hizo evidente la falta de información, de pedagogía sobre el cambio de mentalidad que supone la fabricación aditiva desde el punto de vista de diseño, puesto que desde la mesa se aseguró que “la tecnología va más avanzada que el mercado… posiblemente sea una de las pocas veces en que la demanda va por detrás”, concluyeron.
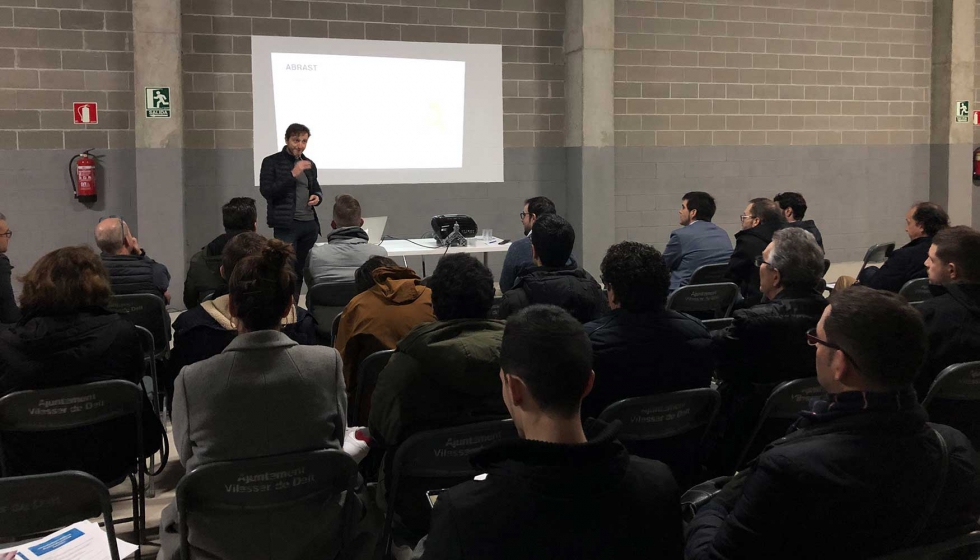
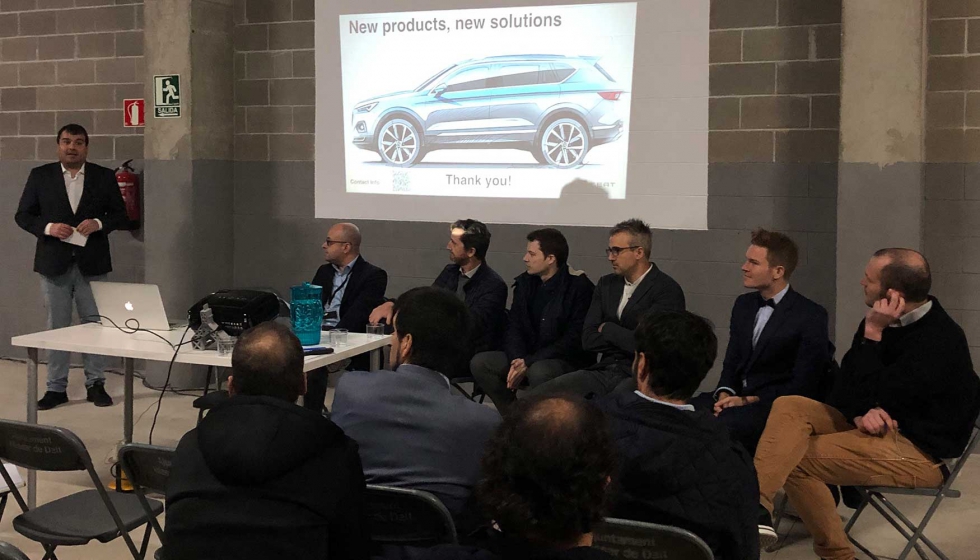
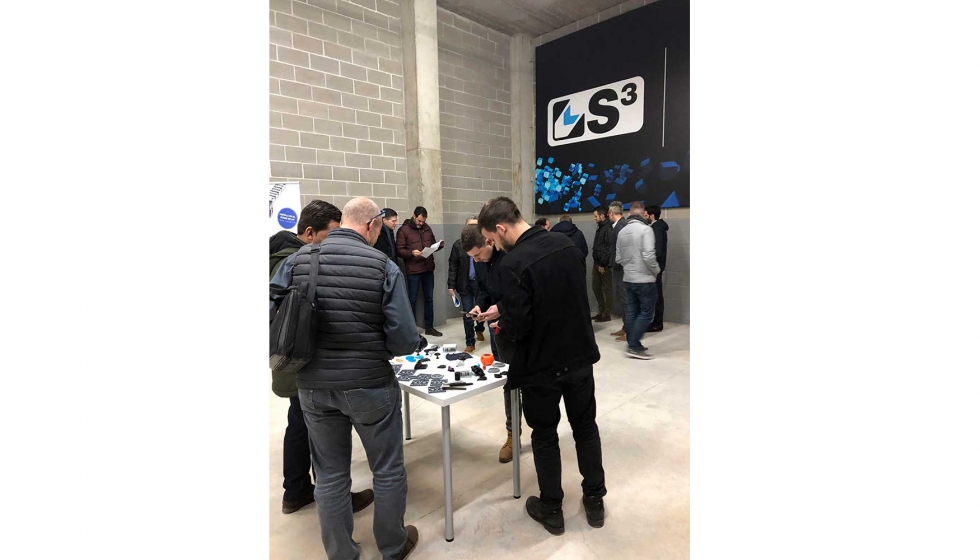