IK4-Tekniker trabaja en alternativas a las aleaciones tradicionales en el proyecto BioTiDent
Aleaciones de titanio biocompatibles para implantes dentales
El sector dental es pionero tanto por volumen de mercado como por su capacidad de innovación. Las prótesis de sustitución o restauración de piezas dentales se fabrican en laboratorios protésicos por encargo de odontólogos y clínicas dentales. Al tratarse de un sector segmentado y con un elevado nivel de competitividad, resulta constante la búsqueda de mejoras para sus soluciones, lo que hace que la tecnología empleada se sitúe siempre a la vanguardia. En los últimos años, los implantes de titanio se han convertido en una solución común para el sector dental por su alta biocompatibilidad y resistencia a la corrosión. Sin embargo, el nivel de fracaso sigue siendo considerablemente alto, lo que ha llevado a la industria a interesarse en el desarrollo de nuevas aleaciones y soluciones que puedan minimizar las debilidades de las aleaciones empleadas actualmente.
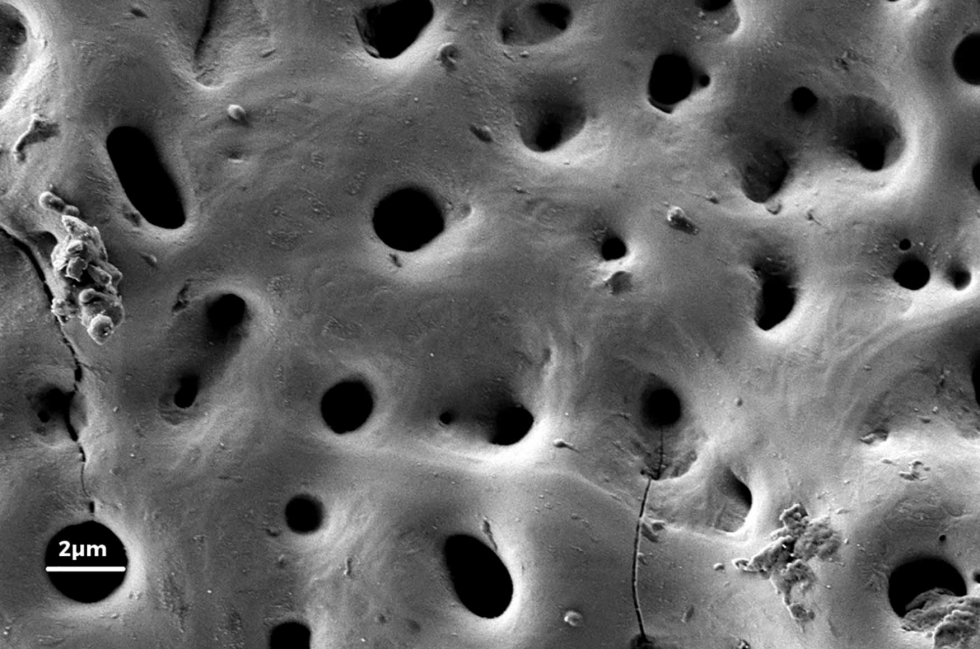
La mayor parte de los fallos en implantes están relacionados con la pérdida de las propiedades mecánicas y con los fenómenos biológicos que tienen lugar en la interfase entre el implante y el hueso, como la formación de colonias de bacterias, la generación de tejidos fibrosos y la acumulación de partículas del material del implante. Estas últimas son resultado del desgaste que sufren los implantes como consecuencia de la actividad diaria, como, por ejemplo, los micro-movimientos generados durante el masticado de la comida. Además, durante el atornillado del implante en la mandíbula del paciente se puede producir el desgaste de la prótesis y la liberación de partículas. Por estas razones, las propiedades tribológicas de los implantes son de elevada importancia. Asimismo, los fluidos corporales como la saliva son altamente corrosivos y pueden favorecer la disolución de la aleación del implante dando como resultado la liberación de iones metálicos. Todo ello puede dar lugar a una respuesta celular adversa, infecciones, aflojamiento del implante, dolor y en última instancia, al rechazo y la necesidad de reemplazo.
Cabe destacar el interés creciente en la industria biomédica en la sustitución de las aleaciones de titanio más comunes, como la Ti6Al4V (Ti grado 5) o la Ti6Al7Nb, por aleaciones más seguras y con mejores propiedades mecánicas como la alta resistencia mecánica, o una mayor capacidad de deformación. Además, estas aleaciones contienen aluminio, que ha sido recientemente relacionado con enfermedades degenerativas como el Alzheimer.
Con el objetivo de desarrollar una solución tecnológicamente avanzada que contribuya a revertir este escenario, IK4-Tekniker está trabajando en la creación de una nueva generación de implantes dentales basados en una aleación súper-elástica de titanio ß que presenta excelentes propiedades mecánicas. Además, el centro tecnológico busca funcionalizar la superficie de estos implantes con el fin de dotarlos de propiedades bioactivas y antibacterianas, que permitan la osteointegración y reduzcan las infecciones por acumulación de bacterias en la interfase entre la prótesis y el hueso.
De entrada, ¿cuáles son las principales características de la aleación en que están trabajando? ¿Se usa en alguna otra aplicación?
La aleación desarrollada es una aleación súper-elástica de Titanio ß altamente biocompatible para el cuerpo del implante. Las tecnologías para su síntesis y el tratamiento termo-mecánico aplicado le proporcionan con alta resistencia a la fatiga mecánica y bajos niveles de desgaste, lo que repercutirá en una mayor durabilidad y una mejor calidad de vida del usuario.
La aleación se ha desarrollado en el marco del proyecto, con el objetivo de obtener mejores propiedades mecánicas y minimizar elementos que puedan ser nocivos para la salud, como el aluminio. Al tratarse de un nuevo desarrollo, aún se encuentra en fase experimental y todavía no se comercializa ni se utiliza en ningún otro tipo de aplicación.
Comentan que buscan 'funcionalizar' la superficie de estos implantes. ¿De qué tratamiento estaríamos hablando? ¿Supone un avance para evitar infecciones y complicaciones derivadas de los implantes dentales?
La funcionalización de la superficie del implante consiste en dotarlo de propiedades adicionales para mejorar el comportamiento del implante y alargar su durabilidad, con el objetivo de minimizar la necesidad de realizar re-implantes.
En el proyecto, se utiliza la técnica de Electro-oxidación por plasma para conseguir esta funcionalización. Por una parte, la capa de óxido de titanio generada posee una elevada dureza, en comparación con la aleación base, lo que aumenta su resistencia al desgaste, y, además, al trabajar en un ambiente hostil bastante corrosivo (por la presencia de saliva), también mejora su resistencia a tribocorrosión (efecto simultáneo de la corrosión y el desgaste). Por otra parte, la morfología de la capa de óxido generada con esta técnica favorece el crecimiento celular, de forma que la osteointegración del implante se ve mejorada. Finalmente, para minimizar el efecto adverso de las bacterias presentes en el entorno oral, lo que genera infecciones que pueden dar lugar al rechazo del implante, se han incorporado a las capas de óxido agentes biocidas. Este tratamiento supone un avance importante en la búsqueda de soluciones para la implantología dental para evitar o minimizar las infecciones.
¿Y en cuanto al coste, qué repercusión puede tener en cuanto al precio final del producto?
Al tratarse de un proceso en fase experimental, aunque con buenos resultados de cara a la futura escalabilidad del proceso técnicamente, hasta el momento no se ha realizado una evaluación en términos económicos del coste final del producto. Si bien la idea es optimizar el proceso de escalado a nivel industrial de manera que se pueda obtener un producto competitivo.
¿El mecanizado de estas piezas será convencional o requerirá de algún trabajo específico?
En principio, la fabricación del implante no se ve alterada. Tanto la síntesis y el pretratamiento, como el posterior mecanizado siguen siendo los convencionales en este tipo de implantes. La única diferencia radicaría en el uso de la técnica de electro-oxidación por plasma en lugar del anodizado convencional que se aplica actualmente.
Actualmente es un proyecto en fase de desarrollo. ¿Para cuándo prevén que esté disponible en el mercado?
En efecto, al tratarse de un proyecto en fase de desarrollo quedan pendientes una serie de pasos para poder disponer en el mercado de este tipo de implantes. En primer lugar, es necesario acreditar la nueva aleación como biocompatible y obtener todos los certificados pertinentes. De forma similar, también sería necesario certificar el recubrimiento desarrollado con agentes biocidas. Finalmente, es necesario evaluar la conveniencia del escalado del proceso de electro-oxidación por plasma a nivel económico. Con todo ello, una vez pasado todos los controles y certificaciones, podría estar disponible en el mercado en un periodo de 2-3 años.
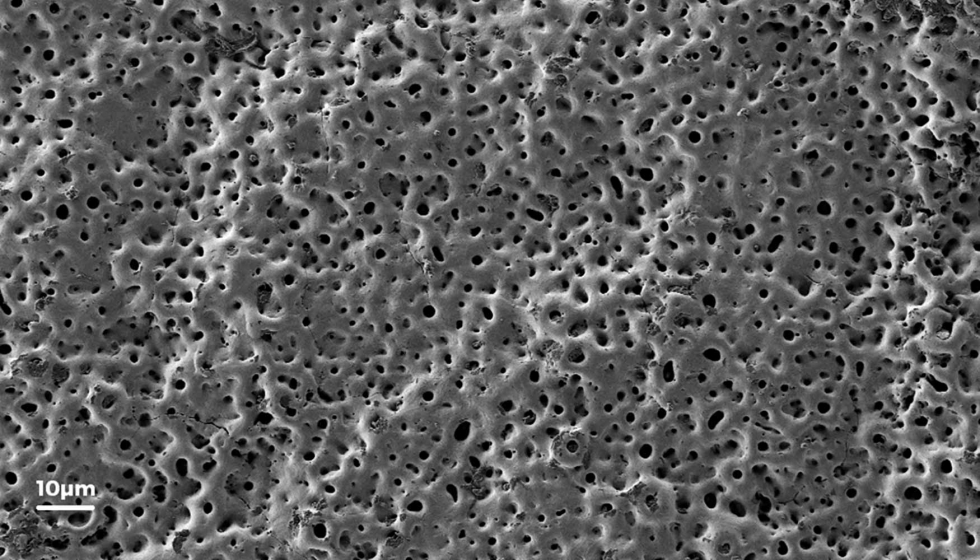
IK4-Tekniker, que cuenta con un alto grado de especialización en ingeniería de superficies, en los campos de la tribología y los recubrimientos, es experto en el desarrollo de soluciones específicas para distintas aplicaciones que abarcan un amplio rango de funcionalidades sobre distintos materiales (metálicos, poliméricos, cerámicos). De modo que, para llevar a cabo la funcionalización de las superficies de los implantes, IK4-Tekniker aplicará la avanzada técnica de Electro-Oxidación por Plasma (PEO, del inglés Plasma Electrolytic Oxidation). La tecnología PEO es un proceso electroquímico de oxidación mediante el que se genera una capa de óxido en la superficie de la aleación a consecuencia de las micro-descargas que tienen lugar en la superficie al polarizar las muestras.
La técnica se basa en el anodizado convencional, pero se utilizan mayores voltajes y corrientes. La composición de las capas generadas puede diseñarse de forma que se puedan añadir ciertos elementos al incorporarlos al electrolito del proceso. Por ejemplo, es posible generar capas de óxido con fósforo y calcio para favorecer la osteointegración, o con elementos biocidas como el yodo o la plata, para dotar el recubrimiento con propiedades antimicrobianas.
Las capas generadas por esta técnica son cerámicas, uniformes, de espesor controlado y densas —a la vez finamente porosas—. También poseen una gran adhesión al substrato, elevada dureza y una buena resistencia al desgaste.
En el marco de esta investigación, los investigadores se responsabilizarán asimismo de incorporar a las capas elementos como calcio y fósforo para favorecer la biocompatibilidad y la osteointegración, así como agentes biocidas que reduzcan las infecciones. Los recubrimientos también proporcionarán a la nueva aleación de titanio ß desarrollada mejores propiedades frente a la corrosión y el desgaste.
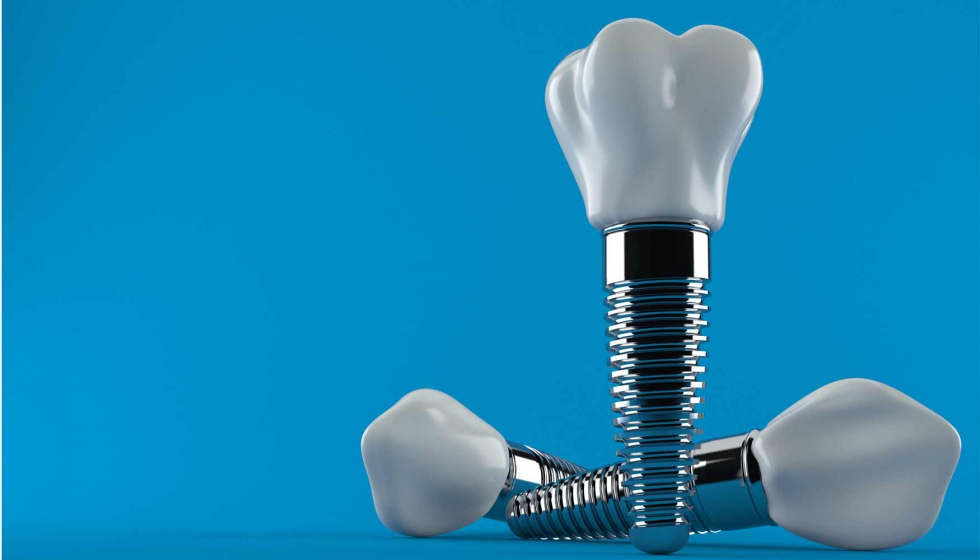
Para llevar a cabo los tratamientos superficiales funcionalizados mediante la técnica PEO, el equipo de IK4-Tekniker ha formulado, en primer lugar, distintos electrolitos hasta conseguir capas con la composición química deseada. Además, se ha diseñado un proceso, para el que se han probado distintas corrientes y tiempos de proceso, hasta conseguir capas con espesores, durezas y rugosidades determinadas.
Las capas generadas se han caracterizado con distintas técnicas microscópicas como la microscopía electrónica de barrido (SEM-EDS), para determinar su espesor y composición. Además, se ha evaluado la capacidad bactericida de las capas, mediante ensayos de actividad antimicrobiana, y se ha analizado la liberación iónica por el contacto con la saliva. La caracterización de las capas también ha contado con ensayos de corrosión, desgaste y tribocorrosión para validar la mejora de las propiedades conseguidas en la aleación de titanio tras el proceso PEO. Una vez concluido el diseño del proceso, IK4-Tekniker realizará el escalado de la técnica, adaptando el proceso para recubrir geometrías de implante real.
Más ventajas para el sector
El resultado de este trabajo será la creación de unos implantes dentales que ofrecerán múltiples ventajas como unas propiedades mecánicas superiores a las de las aleaciones utilizadas actualmente. Además, la aleación de titanio ß no presentará en su composición elementos nocivos como el aluminio, ni el vanadio por lo que resultará más segura para los usuarios.
Los recubrimientos generados aumentarán la resistencia frente a la corrosión y el desgaste, minimizando la liberación iónica que puede causar graves casos de infección y rechazo en pacientes. Además, las capas de óxido mejorarán la osteointegración y disminuirán la presencia de bacterias en la interfase entre el implante y el hueso. El uso de la técnica PEO en el recubrimiento de piezas de geometría compleja permitirá generar capas densas de alta dureza, a diferencia de otras técnicas actualmente utilizadas.