Herramientas de corte: El secreto está en el filo de corte
Sin embargo, tanto la tecnología como el know-how existente respecto a la fabricación de herramientas están en un nivel de exigencia tan alto que se hace necesario generar una diferenciación que llegue hasta el último detalle con el fin de alcanzar una nueva gama de herramientas avanzadas que además de ser robustas y fiables alcancen mayores vidas de herramienta para aumentar la productividad de los procesos de mecanizado. En esta tesitura, el tratamiento del filo de corte se muestra como un parámetro a controlar exhaustivamente siendo la clave para el éxito de las herramientas producidas por los fabricantes del entorno.
Introducción
Las cada vez mayores exigencias impuestas a los motores aeronáuticos en materia de reducción de peso y mayores temperaturas y tensiones de funcionamiento, están incrementando el uso de materiales poco habituales hasta hace unos años en el sector aeronáutico, tales como aluminuros de titanio, aleaciones base Ni y Co de última generación (Waspaloy Udimet) o materiales compuestos de matriz cerámica, además de Ti6-4 o Inconel 718 por ejemplo, que no por más comunes dejan de presentar retos únicos en lo que se refiere a las operaciones de mecanizado, y más concretamente al fresado y taladrado.
Para las operaciones de fresado y taladrado, los fabricantes del sector aeronáutico utilizan a menudo herramientas de metal duro. Como es habitual en el sector aeronáutico, las piezas llevan asociado un muy alto coste de la materia prima que las componen, así como un alto valor añadido, lo cual conlleva importantes pérdidas cuando las piezas se dañan después de horas o incluso días de mecanizado, además de influir negativamente en las ratios de entrega y montaje de los motores demandados por el cliente.
En lo referente a las aleaciones termorresistentes más conocidas, el Inconel (una superaleación con base de níquel) es el material más difícil de mecanizar. Tiene muy baja conductividad térmica y unos niveles muy elevados de temple por deformación, incluso más altos que los del titanio. El Inconel también tiene una alta adherencia, de manera que las velocidades de corte rara vez pueden superar los 25 o 30 m/min con el método de mecanizado convencional.
Las geometrías de la herramienta para el mecanizado en Inconel difieren considerablemente de las que se utilizan para el titanio, requiriendo desahogos muy pronunciados. Esa característica geométrica reduce, en la medida de lo posible, el contacto entre la fresa y el material, lo cual es muy importante dado que el Inconel es flexible y dispone de una gran capacidad de memoria, y significa que el material ‘cederá’ cuando se someta a las fuerzas de corte provocadas por la acción de la herramienta. Por tanto, cuanto más tiempo de contacto haya entre la herramienta y el material, más alto será el desgaste por abrasión de la herramienta y menor su vida útil.
Se ha visto que un filo de corte correctamente preparado de las herramientas utilizadas en procesos de arranque de viruta tiene un funcionamiento sustancialmente superior a uno que no ha sido tratado. De hecho existe un grupo en el CIRP [1] específico sobre este asunto. Es importante remarcar la importancia del radio de acuerdo de un filo de corte. Un filo con muy poco radio de arista, es decir, muy vivo, es susceptible de sufrir rotura prematura, se desgasta y entalla muy rápido, además de influir en la calidad del corte, ocasionando un corte más inestable. La preparación de filo es una etapa vital en el proceso de fabricación de las herramientas, destacando sobre todo las sub-etapas de redondeo de filo y suavizado de superficie del filo. Redondeando el filo con un pequeño radio de unas 15 micras, ya se consiguen importantes mejoras de fiabilidad y mayor vida de herramienta.
Preparación del filo de corte
La aplicación de nuevas estrategias de corte para mejorar la productividad de los procesos de mecanizado y la calidad de las piezas de trabajo requiere el desarrollo de modernas herramientas de corte de precisión. Para un desarrollo integral y sistémico de una herramienta de corte de precisión, se consideran cuatro aspectos que están relacionados: el material (substrato), el recubrimiento, la macrogeometría y el filo de corte de la herramienta. El control de cada uno de estos aspectos influye en la calidad y fiabilidad de la herramienta de corte.
En los últimos años, se ha visto que el control del filo de corte es un aspecto fundamental para conseguir un buen rendimiento de la herramienta.
La preparación del filo de corte consiste en generar la geometría del filo y la modificación de la micro-topografía del borde, así como el cambio en la rugosidad y la textura de las superficies de la herramienta en las proximidades del borde, con la consecuente eliminación de defectos de borde para mejorar el rendimiento y la fiabilidad de la herramienta de corte y también la calidad de la pieza mecanizada. Además del diseño de macro-geometría, la investigación y la aplicación práctica han demostrado que la geometría del filo de corte también tiene una gran influencia en el rendimiento y en la fiabilidad de la herramienta de corte de precisión.
La preparación de filo elimina los defectos microscópicos que suelen tener los filos, tales como micro-fracturas, rebabas, quemaduras, aspereza superficial e irregularidades, que generan baja resistencia mecánica y hacen que la herramienta sea susceptible al astillado y pueda producir un corte inestable. Por lo tanto, estos defectos deben eliminarse para lograr un rendimiento óptimo de la herramienta, siendo fundamental la selección adecuada del proceso de preparación de filo de corte [2].
La aplicación sistémica y controlada del proceso de preparación de filo tiene varios propósitos principales: aumentar la resistencia del filo, eliminar los defectos del filo y mejorar la preparación de las superficies de las herramientas para mejorar la adhesión del recubrimiento y con todo ello, mejorar la calidad de la pieza en cuanto a precisión y acabado superficial y aumentar también la vida de la herramienta.
Por tanto, la preparación del filo de corte de la herramienta es un aspecto importante a tener en cuenta en la fabricación de herramientas y su adecuado control es fundamental.
Para obtener una preparación de filo de manera productiva es necesario disponer de una tecnología de fabricación que asegure la repetitividad del proceso. Los procesos que más se utilizan son el micro-chorreado abrasivo, el cepillado y el ‘drag-finishing’ [3].
Antes de aplicar estas técnicas de preparación de filo las herramientas se suelen rectificar. Sin embargo, los granos abrasivos producen elevadas deformaciones plásticas que dan lugar a la aparición de varios defectos como rebabas, un acabado superficial pobre o el astillamiento del filo y un estado de tensiones residuales perjudicial para el rendimiento de la herramienta recubierta. Además, si se desea obtener micro-geometrías de filo complejas o conseguir un determinado radio de filo, el rectificado no es un proceso de preparación adecuado.
El micro-chorreado es un proceso en el cual los granos abrasivos son proyectados hacia la superficie de la pieza bien en un medio seco (únicamente con aire a presión) o bien mediante el empleo de agua. El impacto de cada uno de estos granos abrasivos en la superficie de la herramienta produce la deformación y eliminación del material, preparando el filo y mejorando las propiedades superficiales de la herramienta. Sin embargo, la integridad del filo de corte depende de un elevado número de parámetros, lo que hace que sea difícil conseguir resultados repetitivos.
La preparación de filo mediante cepillado consiste en emplear cepillos de filamentos metálicos o poliméricos que contienen un abrasivo en su extremo. Mediante este proceso, se consigue un redondeamiento del filo asimétrico que depende de si el cepillado se efectúa desde la cara de incidencia a la de desprendimiento o viceversa. El tamaño del redondeamiento dependerá de parámetros como el tamaño de grano abrasivo, la velocidad de corte o el tiempo de cepillado (entre otros). La gran variedad de geometrías de cepillos y abrasivos, junto con la introducción de máquinas de 5 ejes, posibilita obtener una alta variabilidad de geometrías como de materiales de herramienta que se pueden tratar. Sin embargo, el cepillado es un proceso que también requiere de prueba y error para conseguir la geometría de filo deseada.
El proceso ‘drag-finishing’ consiste en sumergir la herramienta a mecanizar en un medio abrasivo donde las partículas se mueven libremente. Una vez sumergida, un mecanismo orbital mueve las herramientas de tal forma que el abrasivo choca aleatoriamente con éstas generando un perfil redondeado aproximadamente simétrico en el filo de corte. La magnitud del radio de filo depende, entre otros aspectos, del tipo de abrasivo, de la velocidad de movimiento del sistema planetario y del tiempo de mecanizado. Una de las grandes ventajas de este proceso es que facilita la preparación de herramientas con filos complejos como fresas o brocas enterizas, lo que hace que sea el proceso que más posibilidades tiene de ser utilizado industrialmente.
Casos Práctico: fresado periférico de Inconel 718
Para estudiar la influencia que tiene la preparación del filo de corte en la vida de la herramienta se han realizado ensayos de fresado periférico de Inconel 718 en un centro de mecanizado de 3 ejes Kondia A6. Esta aleación se utiliza ampliamente para la fabricación de componentes críticos de motor aeronáutico debido a sus excelentes propiedades mecánicas a altas temperaturas. En cuanto a las herramientas de corte estudiadas, se han utilizado fresas de metal duro sin recubrir de 10 mm de diámetro.
El montaje experimental y las condiciones de corte empleadas en los ensayos se muestran en la figura 1. Se ha realizado el fresado periférico en concordancia de una chapa de 5mm de espesor y de 200 mm de longitud. Se ha programado una entrada y salida tangencial de la fresa con un radio de 15 mm. Se ha realizado el fresado en seco y la elección de las condiciones de corte está basada en experiencias previas de los autores [4]. El criterio de finalización de vida de herramienta está basado en los requerimientos aeronáuticos que son más estrictos y establecen un desgaste de flanco de 0,2 mm [5]. A lo largo de los ensayos se ha controlado el desgaste de la herramienta cada 200mm mediante un microscopio PCE-200 hasta que uno de los filos alcanzara el desgaste máximo establecido.
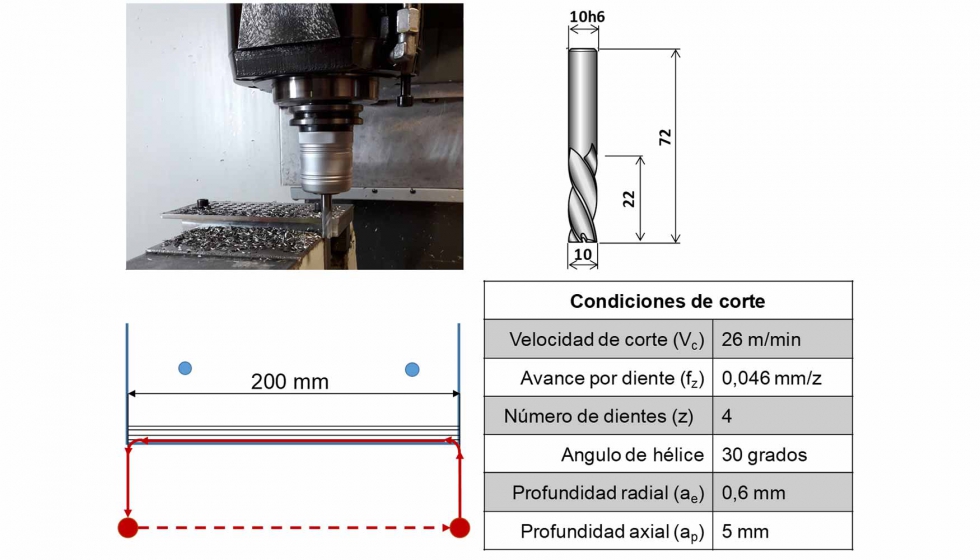
El método utilizado para la preparación del filo de corte de las fresas ha sido el ‘drag finishing’ en una máquina DF70 OTEC. El abrasivo utilizado ha sido una mezcla de cáscara de nuez y partículas de Sic en una proporción de 50% en peso. Para medir el filo de corte de las fresas se ha utilizado un microscopio Alicona Infinite Focus y utilizando el módulo específico EdgeMaster, que está enfocado a la medición de filos de corte. Los radios de filo ensayados han sido: sin preparación de filo (con el rectificado del fabricante de herramienta), 15 µm and 20 µm. En la figura 2 se muestra la máquina OTEC empleada para la preparación de los filos y el microscopio Alicona para la medición de los filos, con los resultados de las mismas. Se puede observar que la fresa de referencia (la rectificada) presenta un radio de filo de 3 µm, pero que la geometría de este filo sin tratar es más irregular que la obtenida mediante preparación de filo.
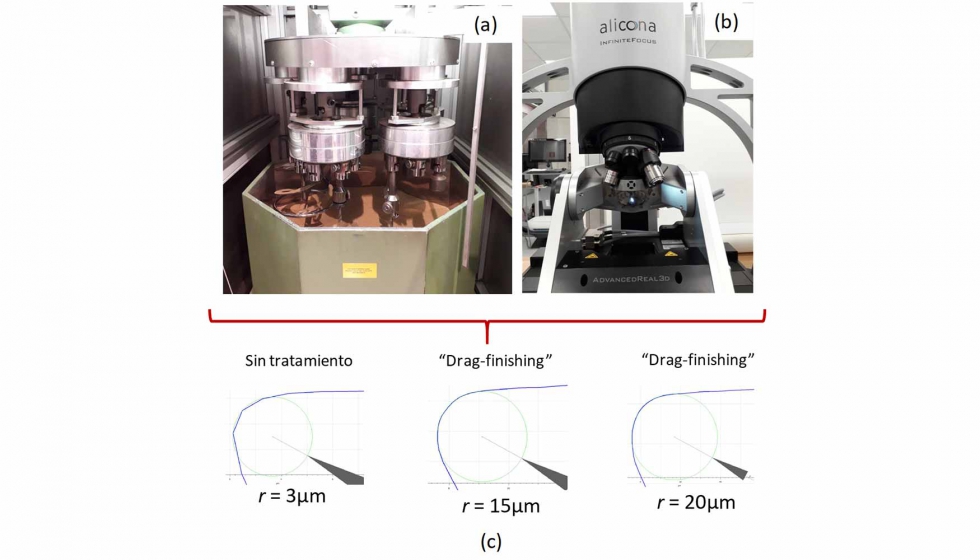
Los resultados de la evolución del desgaste de flanco de las diferentes fresas ensayadas se muestran en la figura 3. Tomando como referencia la longitud de mecanizado de la herramienta sin tratamiento de filo, la herramienta con un radio tratado de 15 µm ha superado esa longitud en un 12,5 % y la de 20 µm en más del 25%.
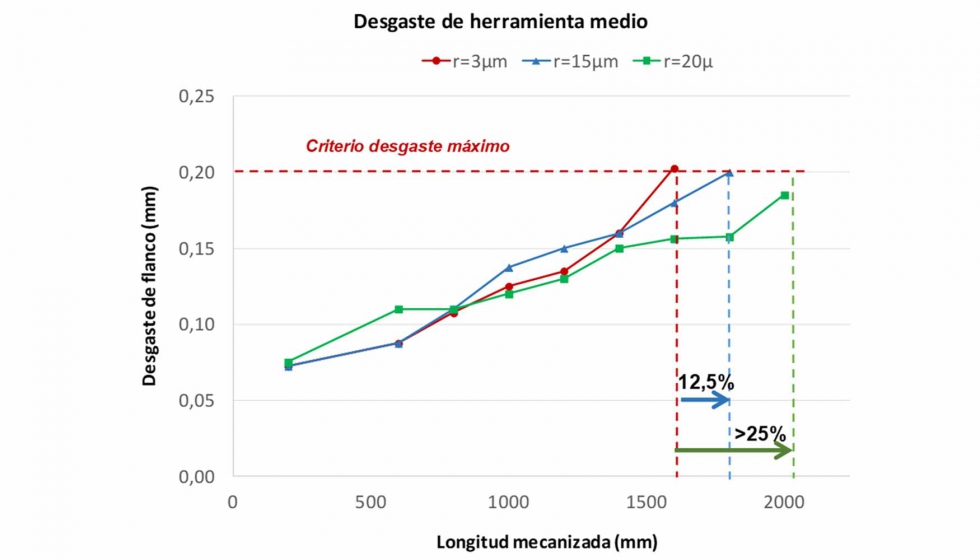
Por otro lado, la preparación del filo de corte también ha supuesto que el desgaste de flanco obtenido en las fresas sea más uniforme y con menor adhesión que el obtenido en las fresas rectificadas. En la Figura 4 se muestra este desgaste en la cara de incidencia de la fresa sin tratamiento de filo. Este desgaste se ha obtenido con el microscopio Alicona superponiendo la medida 3D de la fresa antes y después del mecanizado. En la imagen se observa que el desgaste de flanco obtenido es irregular a lo largo de la longitud del filo. Sin embargo, en las fresas tratadas no se ha observado esta irregularidad debido a que además de obtener un radio de filo definido, la preparación de filo también mejora la rugosidad de las superficies cercanas al filo repercutiendo en el rendimiento del proceso.
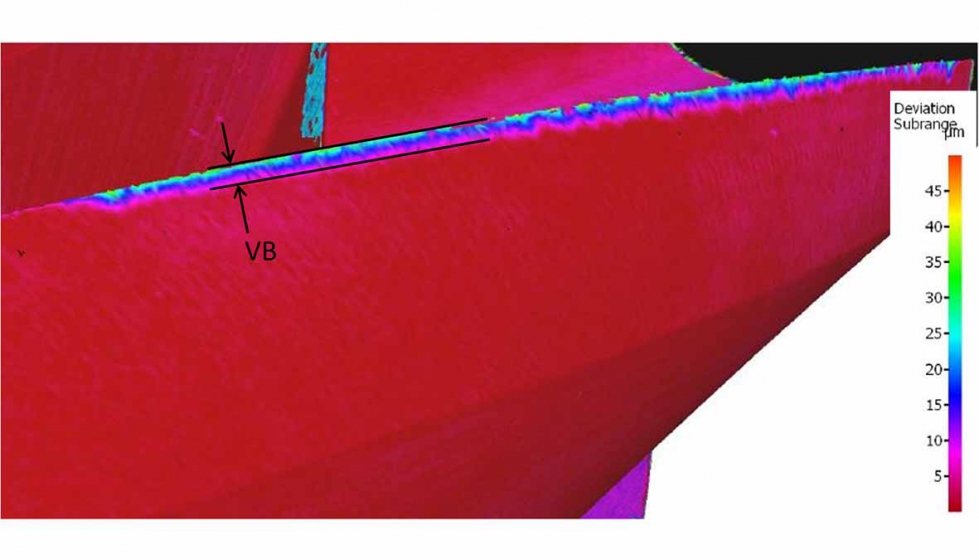
Conclusiones
Dominar las tecnologías de preparación de filo es fundamental para obtener un buen rendimiento en las diferentes herramientas de corte, independientemente de su aplicación, y es un aspecto esencial para que las empresas fabriquen las mejores herramientas del mercado a un coste competitivo.
Ensayos de fresado periférico de Inconel 718 han mostrado la eficiencia del tratamiento de los filos de corte en el rendimiento del proceso. Las herramientas con preparación de filo mediante ‘drag finishing’ incrementan la vida de las herramientas de metal duro presentando desgastes más uniformes y menor adhesión debido a la mejora de la micro-topografía en el filo y sus proximidades.
Referencias
[1] K.D. Bouzakis, E. Bouzakis, S. Kombogiannis, S. Makrimallakis, G. Skordaris, N. Michailidis, P. Charalampous, R. Paraskevopoulou, R. M’Saoubi, J.C. Aurich, F. Barthelma, D. Biermann, B. Denkena, D. Dimitrov, S. Engin, B. Karpuschewski, F. Klocke, T. O¨ zel, G. Poulachon, J. Rech, V. Schulze, L. Settineri, A. Srivastava, K. Wegener, E. Uhlmann, P. Zeman (2014) ‘Effect of cutting edge preparation of coated tools on their performance in milling various materials’, CIRP Journal of Manufacturing Science and Technology Vol. 7, pp. 264–273
[2] C.J.C. Rodriguez, ‘Cutting edge preparation of precision tools by applying microabrasive jet machining and brushing’, Ph.D. thesis, Kassel University, 2009.
[3] Denkena B, Biermann D (2014) ‘Cutting-edge geometries’. CIRP Ann. Manuf Technol 63:631–653.
[4] O. Pereira, G. Urbikaín, A. Rodríguez, A. Fernández-Valdivielso, A. Calleja, I. Ayesta, L.N. López de Lacalle. ‘Internal Cryolubrication approach for Inconel 718 milling’ in Procedia Manufacturing 13, pp. 89-93 (2017).
[5] A. Fernández-Valdivielso, L.N. López de Lacalle, G. Urbikain and A. Rodriguez, ‘Detecting the key geometrical features and grades of carbide inserts for the turning of nickel-based alloys concerning surface integrity’ in J. of Mech. Eng. Sci., in press. DOI: 10.1177/0954406215616145 (2015).