Conceptos básicos del plegado de chapa
Una buena manera de comenzar es conocer, de inicio, las partes de una plegadora, su tonelaje (la fuerza máxima que puede ejercer la máquina), la longitud máxima de plegado, los montantes (o cómo es la estructura transversal a la trancha), la distancia entre montantes (es decir, la longitud de plegado real), el cuello de cisne (el rebaje en los montantes), la trancha o tablero superior, la mesa (el tablero inferior donde se posicionan las matrices), la luz (esto es, la apertura máxima), la carrera o recorrido de la trancha y el control de la plegadora.
Asimismo, hay que tener en cuenta que actualmente existen un buen número de opciones añadidas a las plegadoras como:
- Mesa de compensación de flexiones: permite compensar las flexiones de la trancha y de la mesa de la plegadora. Permite obtener un ángulo de plegado constante en toda la longitud de plegado. También permite trabajar en estaciones de trabajo junto con los ejes Y1 e Y2.
- Acompañadores: adecuados para trabajar con piezas de gran peso o de grandes dimensiones.
- Amarres rápidos de utillaje hidráulicos / neumáticos: permiten el cambio rápido de los utillajes. Adecuado para empresas que trabajan series cortas y deben realizar muchos cambios de utillaje. Reducen los tiempos muertos de preparación de la plegadora.
- Control de ángulo: permite corregir el ángulo de plegado de forma dinámica. Es un proceso lento pero adecuado para piezas que precisan gran precisión de plegado.
- Cambio automático de utillaje: puede ser lento pero evita posibles errores al montar el utillaje o el posicionamiento de las estaciones de trabajo con relación a la posición programada de los topes de plegadora (Z1 y Z2)
- Robot: adecuado para series medias – largas, series que requieran una repetitividad uniforme, no requiere intervención de operarios pudiendo trabajar sola.
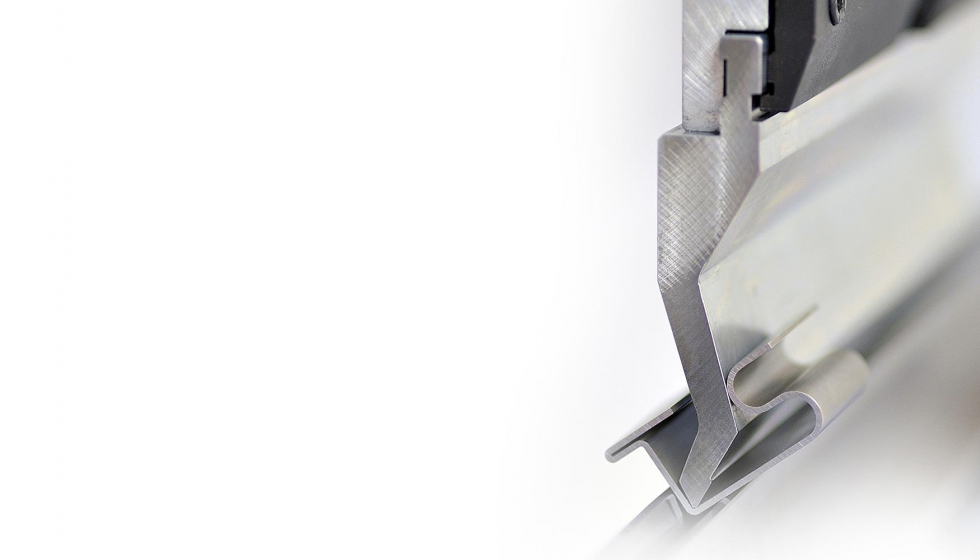
Tipos de plegadoras. Plegadoras hidráulicas de subida (Mebusa / tipo RG)
Son de movimiento ascendente mediante un motor hidráulico central. Permiten una regulación mecánica sencilla de la carrera y del punto final de la carrera de forma ‘activa’ mediante un volantín. Suelen utilizar utillaje Promecam con intermediarios regulables que permiten crear una ‘curvatura intermedia’ para compensar las flexiones de la plegadora durante el plegado.
Pueden incluir CN de 2 ejes: eje X, Profundidad del tope de chapa; eje Y: Bajada de la trancha; y en algunos casos un tercer eje (R) que controla la altura de los topes de chapa. Por sus características se debe plegar siempre en el centro de la plegadora.
Tipos de plegadoras. Plegadoras hidráulicas de bajada con barra de torsión
Son de movimiento descendente mediante 2 cilindros en los extremos de la trancha. La regulación del punto final de la carrera se realiza a través de unos topes interiores a los cilindros que limitan mecánicamente el movimiento del pistón hidráulico. Los topes de los 2 cilindros están unidos mediante una barra de torsión. Para su corrección la trancha debe estar arriba para que el pistón no presione el tope.
Tradicionalmente suelen utilizar diversos tipos de utillaje tipo coaxial (Ajial, Casanova, etc.). En algunas plegadoras el punzón se amarra directamente a la trancha y en otras a una pieza intermedia (porta-punzón) de longitud igual a l de la plegadora. En los últimos años empezaron a utilizar utillaje tipo Promecam con intermediarios regulables. Pueden incluir CN de 2 ejes (X e Y) y en algunos casos un tercer eje (R). Por las características de la plegadora se debe plegar siempre en el centro de la plegadora.
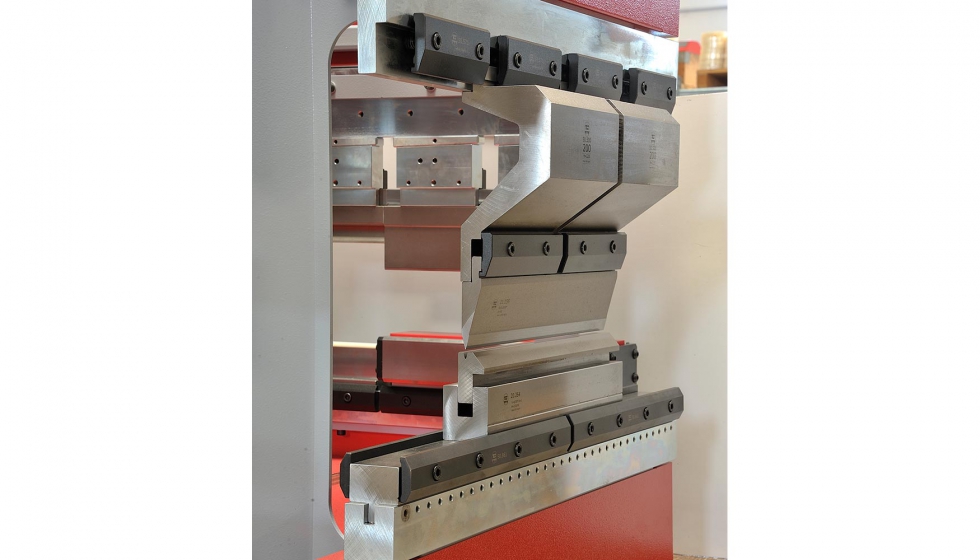
Tipos de plegadoras. Plegadoras hidráulicas de bajada sincronizadas
Son de movimiento descendente mediante 2 cilindros hidráulicos independientes controlados y sincronizados por CN. Son los ejes Y1 e Y2. El CN permite que los pistones de los cilindros (Y1, Y2) bajen uno más que otro dentro de un cierto límite. Esto permite compensar ciertas flexiones de la plegadora mediante el CN
También que no sea obligatorio plegar en centro de la plegadora pudiendo trabajar con estaciones de trabajo. Es decir, con más de un conjunto de utillaje (punzón + matriz) montado a lo largo de la plegadora.
Existen plegadoras con diversos tipos de utillaje: Coaxiales como Ajial, Beyeler, LVD, Wila, EHT, Weinbrenner, …. y tipo Promecam. Suelen tener como mínimo 4 ejes (X, Y1, Y2, R) pero puede llegar a tener hasta 8 ejes:
- Ejes X1 –X2: Profundidad de los topes de chapa independientes.
- Ejes Y1 – Y2: Bajada de los pistones de los cilindros hidráulicos.
- Ejes Z1 – Z2: Movimientos laterales (derecha / izquierda) de los topes
- Ejes R1 – R2: Movimiento vertical / en altura de los topes. Muchas veces los ejes R funcionan como uno solo.
Tipos de plegadoras. Plegadoras eléctricas
La fuerza se ejerce mediante servo motores eléctricos a través de husillos o a través de un sistema de correas y poleas que transmiten la fuerza en toda la longitud de la trancha. Son muy precisas y su mantenimiento es mucho menor que en las plegadoras hidráulicas. No necesitan mesa de compensación de flexiones y son máquinas de última generación. Pueden incluir la mayoría de las opciones.
Fabricación de la chapa
La fabricación de la chapa se produce en el alto horno, donde se funde chatarra de acero y hierro, obteniéndose el hierro colado. En procesos posteriores se ‘equilibran’ los componentes y se obtienen aceros con menos impurezas y menos concentración de carbono. Posteriormente el metal fundido se canaliza a través de un camino de rodillos, refrigerándolo hasta obtener unas placas gruesa y rugosa.
Mediante la laminación por rodillos se cambia el espesor aumentando principalmente la longitud y menos en el ancho. Este desplazamiento forzado tiende a crear estructuras alargadas de las fibras (evidente al plegar en el sentido de laminación o contra este).
El proceso de laminación de la chapa puede ser en frío o en caliente:
- En caliente: se utiliza pera espesores medios/altos (a partir de 5 mm). Tiene una estructura más homogénea. El espesor no es muy preciso.
- En frío: se utiliza para espesores finos/medios (menos de 8 mm). El alargamiento de las fibras es muy importante. Ofrece mayor dureza superficial, espesores más precisos y superficies más lisas y homogéneas.
Tipos de aceros
Los aceros que se suelen utilizar en el plegado se pueden diferenciar en aceros sin aleación y aceros aleados.
1. Aceros sin aleación o acero al carbono: aleaciones de hierro + carbono.
- La concentración de carbono es inferior al 2,11%
- A mayor concentración de carbono mayor dureza.
- Acero ‘extra dulce’ (‘extra suave’): 0,05-0,15%. 32 – 38 kg/mm2
- Acero ‘dulce’ (‘suave’): 0,15-0,25%. 38 – 46 kg/mm2
- Acero ‘semi dulce’ (‘semi suave’): 0,25-0,40%. 46 – 55 kg/mm2
- Aceros ‘semi duros’: 0,4-0,6%. 55 – 65 kg/mm2
- Aceros ‘duros’ (0,6-0,7%). 65 – 75 kg/mm2
- Aceros ‘muy duros’ (0,7-0,8%). 75 – 85 kg/mm2
2. Los aceros habitualmente utilizados son los dulces o suaves
3. Aceros aleados: aleaciones de hierro y carbono más otros metales que modifican las características del material. Por ejemplo, acero inoxidable, acero Cor-ten, etc.
4. Acero inoxidable: acero al carbono aleado con Cromo y Niquel que le confieren resistencia a la corrosión. De mayor dureza que el acero al carbono.
5. La presencia de cromo crea una película relativamente inerte sobre la superficie que evita reacciones del acero con el entorno: Pasivación. Esta capa es activa y se ‘regenera’ al cortar o perforar el metal.
6. Tipos de aceros inoxidables utilizados en plegado
- AISI 304 (X5CrNi1810): Bajo contenido en carbono (<0,1%), un 18% de cromo y un 10% de Níquel. Es habitual llamarlo acero inoxidable 18/10. Alto grado de inoxidabilidad, no es magnético y tiene unas características óptimas.
- AISI 316 (X5CrNiMo1712-2): Contiene cromo y níquel en la misma cantidad y un 2–3% de molibdeno. Resistente a la corrosión al agua marina y ciertos agentes químicos.
- AISI 430 (X8Cr17): Es magnético. Contiene un 0,8% de carbono y un 16-18% de cromo. Se utiliza en ambientes sujetos al calor. Es un poco más complicado de plegar que los anteriores ya que tiende a griparse en la matriz y provoca un plegado menos constante.
Utillaje de plegadora
Existen diferentes tipos de utillaje según el tipo de amarre de la plegadora:
- Adira: Promecam
- Amada: Promecam / Wila
- Axial: Ajial / Promecam / Wila
- Beyeler: Beyeler R / Beyeler S / Beyeler RF-A / Euro-beyeler.
- Loire: Loire / Promecam / Euro-beyeler.
- LVD: LVD (4 tipos) / Wila,
- Trumpf: Wila
- Turcos (Baykal, Durma, Ermaksan, etc): Promecam
Cualquier fabricante puede instalar el sistema de amarre Wila.
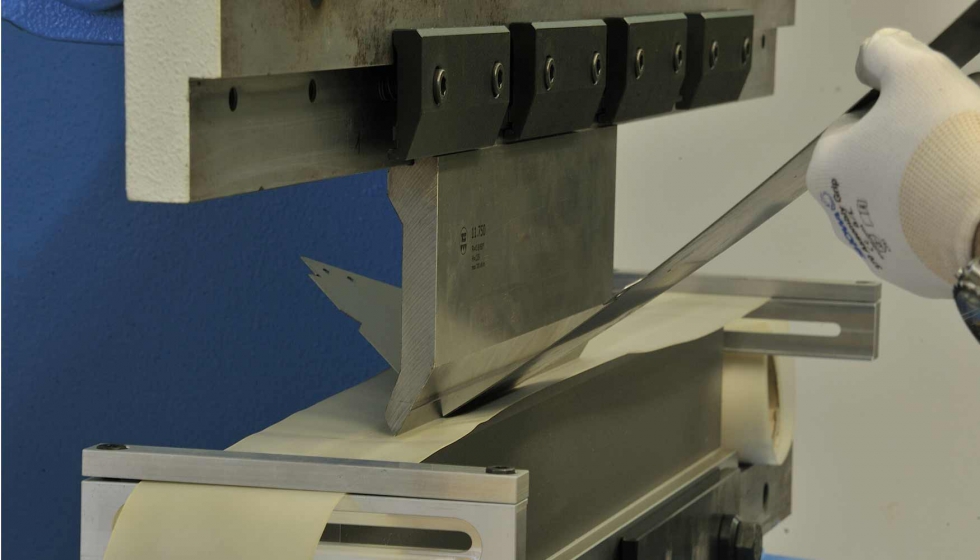
Utillajes Promecam
- Punzón: amarre de 30 mm de altura. Eje de plegado desplazado 7 mm del amarre del punzón.
- Matriz: Base de 60 mm con el centro de la V (eje de plegado) a mitad de la base de 60 mm
- Intermediario: Cuña para regulación de la altura. Eje del amarre del intermediario a 7 o a 20 mm según modelo de plegadora. Parte inferior de 14 mm para poder girar el punzón y mantener el eje de plegado
- El sistema permite suplementar un intermediario con otro (si el eje es de 7 mm) de esta forma podemos aumentar la altura del punzón
En Tecnostamp se utilizan diversos tipos de aceros para la fabricación de los utillajes de plegadora.
Los aceros que se suelen utilizar para la fabricación de utillaje de plegadora son los siguientes:
- Acero C45: UNI EN 10083 / Wr nº 1.1191 / UNE F-114
- Acero C45 bonificado: UNI EN 10083 Wr nº 1.1191 / UNE F-114 bonificado a 80-85 kg/mm2
- Acero Cromo Molibdeno 42CrMo4 o 1.2312: UNI EN 10083 Wr nº 1.7225 UNE F-1250 bonificado R=95-105 kg/mm2.
Son utillajes rectificados en las áreas importantes: amarre y en las zonas de trabajo como la punta del punzón o las ‘uves’ de las matrices. Con precisión de mecanizado de +/- 0,01 mm y garantía de acoplamiento.
Las longitudes estándar son 835 y 415 mm; y 805 fraccionado:
- Punzón:10, 15, 20, 40, 50, 100, 100BD, 100BI, 370
- Matriz: 10, 15, 20, 40, 50, 100, 200, 370
Se obtienen longitudes desde los 10 mm hasta los 805 mm de 5 en 5 mm.
Tipos de plegado
Existen 3 tipos de plegado:
- Plegado al aire
- Plegado a fondo
- Estampado
En los 3 tipos la chapa es presionada por el punzón en el interior de la obertura de la matriz manteniendo durante todo el proceso 3 puntos de contacto; el radio del punzón y los radios de los vértices de la V.
Plegado al aire
En este caso la chapa es presionada por el punzón en el interior de la obertura de la matriz, pero sin tocar la parte inferior. No es necesario que el radio del punzón de la herramienta superior y el ángulo V de la herramienta inferior sean iguales. Con una sola combinación de herramientas, se pueden plegar múltiples materiales y espesores en diferentes ángulos. Es un método muy flexible, lo que supone pocos cambios herramientas, requiere menos fuerza de flexión, pero también es menos preciso.
En este caso, la penetración debe tener una precisión muy alta y las variaciones en el espesor de la chapa y el desgaste local de punzones y matrices pueden ocasionar desviaciones inaceptables. Las propiedades de la chapa también afectan el ángulo de plegado debido al retorno elástico.
- V de 6 a 12 veces el espesor
- Precisión: ±30’ (0,5º)
- Radio interno de plegado: entre 1 y 2 veces el espesor
- tonelaje relativamente bajo
Las desventajas de esta técnica en términos de calidad se corrigen con medidas especiales. Por ejemplo, sistemas de medición de ángulos, amarres y sistemas de compensación ajustables y herramientas endurecidas / templadas.
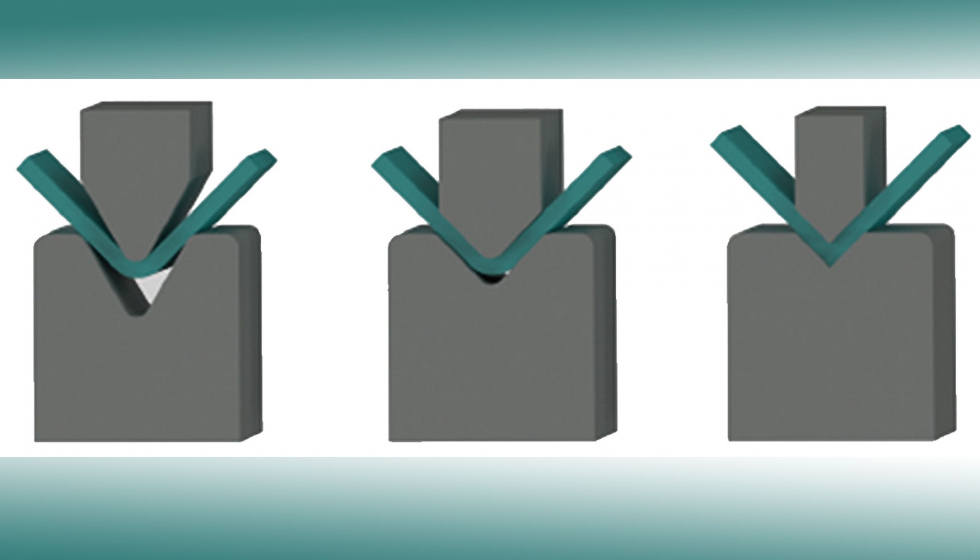
Plegado a fondo
El plegado a fondo es una variante del plegado al aire. La chapa se presiona contra los lados de la V. Continúa existiendo un espacio de aire entre chapa y el fondo de la V. Cada ángulo de plegado y cada espesor de chapa requiere un juego de herramientas, y lo mismo ocurre a menudo con los diferentes tipos de materiales debido a los diferentes retornos elásticos. El ángulo de plegado depende de la herramienta.
- V de 6 a 12 veces el espesor.
- Radio interno de plegado: entre 0,8 y 2 veces el espesor.
- Mayor precisión: +/- 15’ (0,25º)
- Tonelaje similar al del plegado al aire.
En este método, el material de chapa es ‘machacado’ por el punzón hasta el fondo de la V. Requiere un tonelaje de cinco a diez veces más alto que el plegado a fondo. Debido a la presión extremadamente alta ejercida en la punta del punzón sobre la chapa, se produce una deformación permanente en toda la sección transversal de la chapa y el retorno elástico se reduce prácticamente a cero.
El estampado implica el uso de matrices y punzones (a menudo con un radio fino) del mismo ángulo. Las variaciones en el espesor de la chapa y las propiedades del material tienen poca o ninguna influencia en los resultados de plegado, ofreciendo un alto nivel de precisión.
- V de 5 veces el espesor.
- Radio interno de plegado: desde 0,4 veces el espesor.
- Sólo se pueden doblar espesores finos de hasta 2,0 mm acero inoxidable y acero al carbono.
Factores que influyen en el plegado
Es difícil encontrar una lámina de metal prácticamente igual y las diferencias pueden ser significativas en el mismo paquete y también en la misma chapa.
Factores que influyen en el plegado:
Acabado de la chapa lagrimada / estriada
En este caso, el plegado es muy complicado: la trama de las lágrimas en diferentes espesores causa problemas dimensionales en grados y medidas de los plegados.
El plegado varía considerablemente si la lágrima está posicionada hacia abajo (matriz) o hacia arriba (punzón). El problema es mayor cuando tenemos contraplegados. En 2 plegados en paralelo en el mismo sentido no siempre se incide sobre el mismo punto de la lágrima. El ángulo de plegado puede variar en función de si el plegado se realiza en el centro del agujero o en un extremo de este.
Las dimensiones de las alas se comprometen ya que la chapa se ‘mueve’ (estirándose o moviéndose) bajo la presión de los radios del punzón.
Para un mismo espesor cuando mayores son los agujeros menos precisión se obtendrá. Para obtener precisión se recomienda plegar a fondo matriz o estampando.
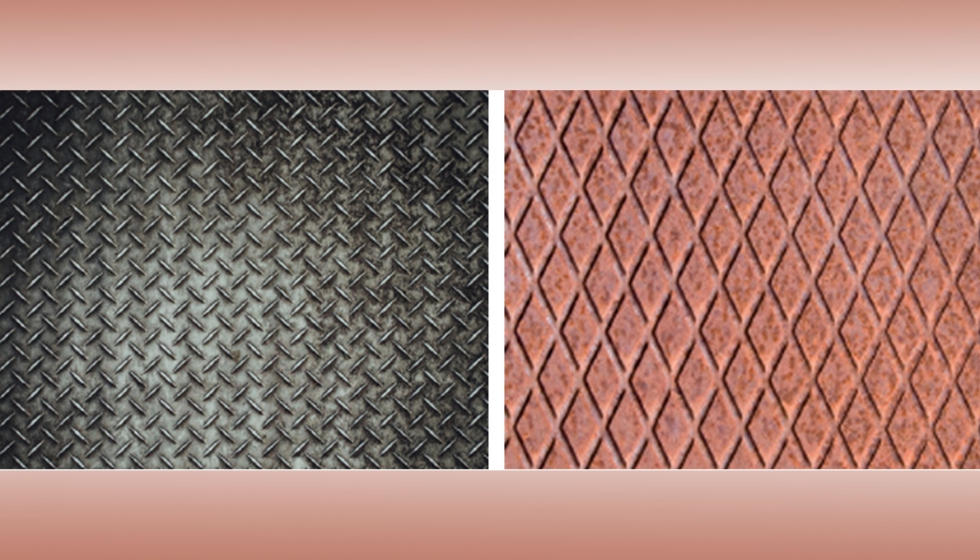
Arriba, chapa lagrimada/estriada.
Diferencia de espesores
Los fabricantes suministran la chapa con una tolerancia (±) del espesor que puede ser alrededor de un 10%. La diferencia de espesor puede causar falta de precisión en el ángulo de plegado. Donde el espesor sea menor el ángulo será más abierto.
La chapa laminada en frío tiene una menor tolerancia y, por lo tanto, es más precisa.
A mayor espesor mayor diferencia en milímetros. Para espesores grandes y si se requiere precisión se recomienda agrupar las piezas por espesores. Se recomienda que la distribución de piezas en una chapa estas estn a 3 – 4 cm del borde exterior.
Sentido de laminación
Durante el laminado, la estructura cristalina se estira; el material adquiere diferentes propiedades mecánicas a lo largo de su longitud que a lo largo de su anchura.
Dependiendo de si una chapa se dobla paralela o transversalmente a las fibras laminadas, se obtendrá fácilmente una diferencia en grados del ala y un desarrollo distinto. Conceptualmente siempre es mejor doblar una pieza con las fibras perpendiculares a la línea de plegado porque la chapa ofrece una mayor resistencia y, en presencia de materiales tenaces, menos tendencia a provocar grietas en el lado exterior del radio.
En el caso de los aceros de alta resistencia hay tablas oficiales que muestran el radio interno mínimo del punzón y el ancho de la matriz a utilizar en función de la dirección de laminación.
Curva de tensión/deformación
El comportamiento del material durante el proceso de plegado se refleja en la curva tensión/deformación. En ésta se hace una distinción entre la región elástica y la
región plástica. En la región elástica el material vuelve a su estado original cuando cesa la fuerza. La deformación aumenta proporcionalmente a la fuerza aplicada; la pendiente de la línea E, el módulo de elasticidad, indica la rigidez del material. La región plástica es cuando la fuerza pasa cierto valor crítico, el material mostrará deformación plástica. Esto se conoce como el límite elástico. Un cambio permanente ocurre en la estructura cristalina del material de la chapa.
Cuando se pliega una chapa en el radio exterior se crea una deformación por tracción y en el radio interior una deformación (contraria) por compresión. La deformación plástica se produce primero en el radio exterior y es la mayor en un plegado. En la sección hay una transición de un esfuerzo de tracción a una tensión de compresión. Hay una zona en el centro de la sección (cerca del centro) con baja tensión donde se produce una deformación elástica, por lo que la chapa siempre retorna algo cuando cesa la fuerza.
Retorno elástico
El retorno elástico depende lógicamente de la naturaleza del material de la chapa. Cuanto más rígido sea el material, mayor será el retorno elástico. Este retorno elástico en materiales blandos (cobre) puede ser de 0,5º, en acero al carbono de 1º y el espesores mayores o inoxidable hasta 3º. Cuanto menor sea el efecto relativo sobre el área elástica en la zona neutra, menor será el retorno elástico.
Si una chapa se pliega con un radio de punzón igual a 1 vez el espesor el retorno elástico será pequeño, pero si el radio del punzón es de 77 veces el espesor el retorno puede ser de 30º.
Cálculo del retorno elástico para acero laminado en frío (formula de Benson) Δ = R / 2.1. S
Factor de corrección de 0,5 para el cobre, 0,75 para el acero laminado en caliente y 2,0 para el acero inoxidable.
Flexión de la máquina
Cuando se ejerce un alto tonelaje, la flexión ocurre inevitablemente en sentido longitudinal en la herramienta superior y en la inferior. Como resultado de esta desviación, las herramientas superiores e inferiores ya no están paralelas durante el proceso de plegado, lo que a su vez provoca variaciones en el ángulo de plegado a lo largo de la longitud del producto.
En el pasado, este problema a menudo se solucionaba insertando papel o tiras demetal debajo de la herramienta inferior para compensar la deflexión.
Existen sistemas de compensación controlados por ordenador o ajustables de forma centralizada son ampliamente utilizados que compensan de forma rápida y precisa la flexión en toda la longitud de la máquina.
Fuerza de plegado
La fuerza de plegado se podría calcular utilizando la fórmula
F=C × (S2 × Rm) /V × L
donde
- F: fuerza de plegado (kN)
- S: Espesor de la chapa
- Rm: resistencia a la tracción del material (kN/cm2)
- V: ancho de la abertura (mm)
- L: longitud (metros)
- C: Constante que depende de S y V: C = 1 + 4S/V
Tabla de plegado
La tabla de plegado indica la fuerza necesaria (F) de un material (Rm=45 kg/mm2) con relación al espesor de la chapa (T), la ‘V’ de la matriz (V). Radio interior de plegado (ri) y el ala mínima (b).
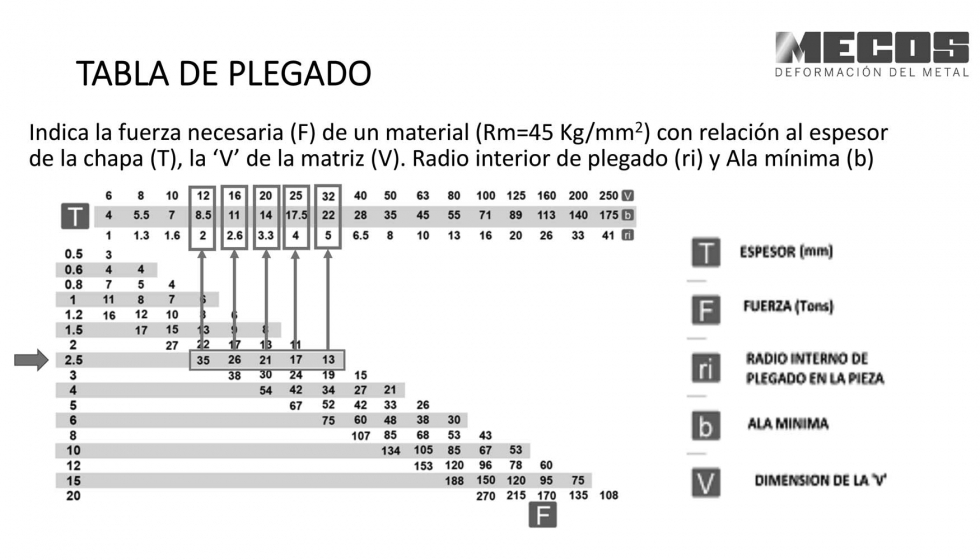
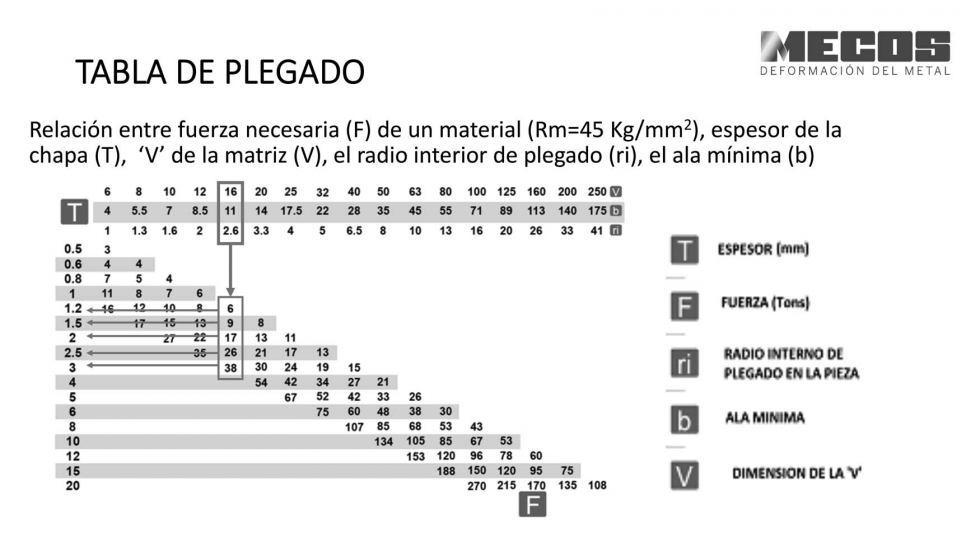
Concepto de tonelaje
Es muy importante tener en cuenta que la fuerza que nos indica la tabla es la fuerza o el tonelaje por metro. Es decir, la fuerza necesaria para plegar 1 metro de chapa.
La resistencia de los utillajes de plegadora (punzones, matrices, intermediarios, etc.) siempre viene expresada en toneladas por metro.
Factor para el tonelaje de otros materiales
- Inox: 1,6
- Aluminio: 0,5
Para plegar Inox (Rm=65-70 kg/mm2) de 2,5 mm en una V=20: F inox=Facero ×(Rm(inox))/(Rm (acero)) = 21 ×70/45 = 21 x 1,6 = 33,6 t/m
Y en aluminio (Rm= 20-25 kg/mm2): F Al=F acero × (Rm (Al))/(Rm (acero)) = 21 ×25/45 = 21 x 0,6 = 12,6 t/m
Ejemplo de plegado
Proyecto: plegar esta pieza en chapa de 2 mm inoxidable en la plegadora Mebusa con un punzón 10.501 (50 t/m)
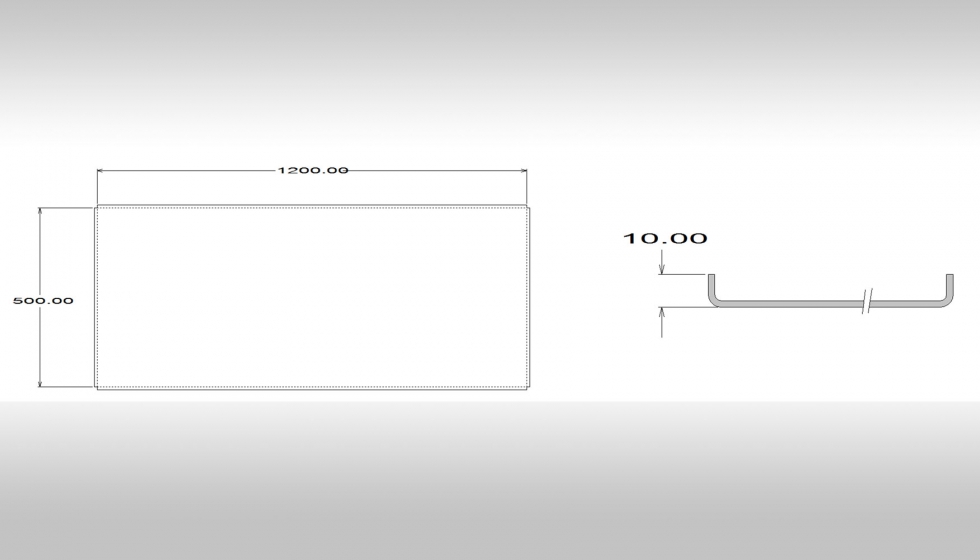
Sus características son:
- Esp. 2,0 mm y ala de 10 mm: V=12/90º
- Tonelaje: F=22 (acero) x 1,6 = 35,2 t/m
Para L=1.200 mm F total = 35,2 t/m x 1,2 m = 42,44 t, Se regula el tonelaje de la plegadora a 43 t, con una secuencia de plegado de 1º lados cortos después lados largos. Al plegar los lados cortos (500 mm) hay que compensar el retorno elástico aplicaremos 43 t. Si se aplican 43 t en 500 mm = 86 t/m. Si el punzón solo soporta 50 T/m de producirá la rotura del punzón.
En cambio, plegando al aire o a fondo matriz (con regulación correcta) no se rompería el punzón. La plegadora CN calcula y regula automáticamente el tonelaje que hace falta para plegar cada lado (longitud) de la pieza. Siempre y cuando se ‘engañe’ a la plegadora y, en lugar de plegar la longitud programada (500 mm), se indique una más corta. Para plegar un ala de 15 mm en 3 mm inoxidable a 90º, con un punzón ‘pata de cabra’ 10.502, ¿qué matriz utilizar?
El radio interno de plegado de la tabla se refiere al acero al carbono. Al plegar inoxidable suele ser un poco menor y en aluminio un poco mayor. Para obtener un radio menor: reducir la V pero verificar el tonelaje. El punzón ha de tener un radio inferior al radio indicado en la tabla. Pero cuanto más próximo mejor.
Concepto de radio de plegado – ala mínima
El radio interno de plegado de la tabla se refiere al acero al carbono. Al plegar inoxidable suele ser un poco menor y en aluminio un poco mayor. Para obtener un radio menor: reducir la V pero verificar el tonelaje. El punzón ha de tener un radio inferior al radio indicado en la tabla. Pero cuanto más próximo mejor.
Concepto de ala mínima
El ala mínima de plegado viene determinado por la V de la matriz. Para obtener un ala menor: reducir la V pero verificar el tonelaje. El ala mínima de la tabla es para plegado a 90º. Para otros ángulos aplicar factor de la tabla.
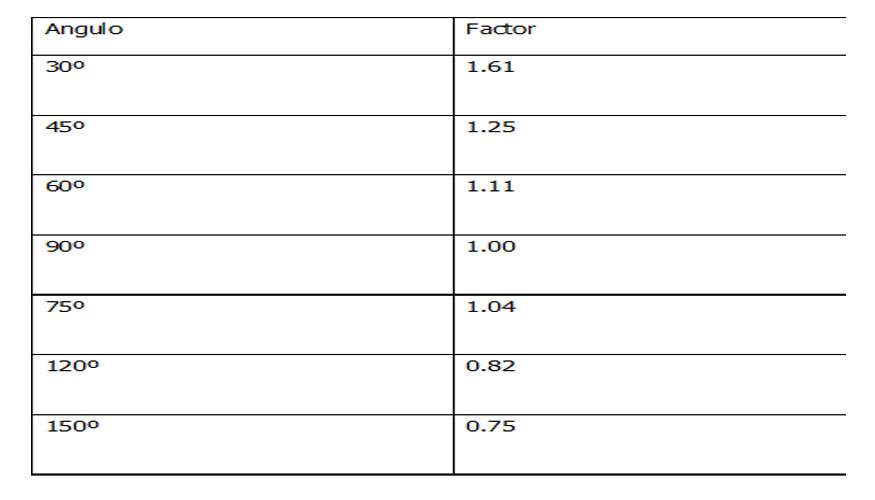
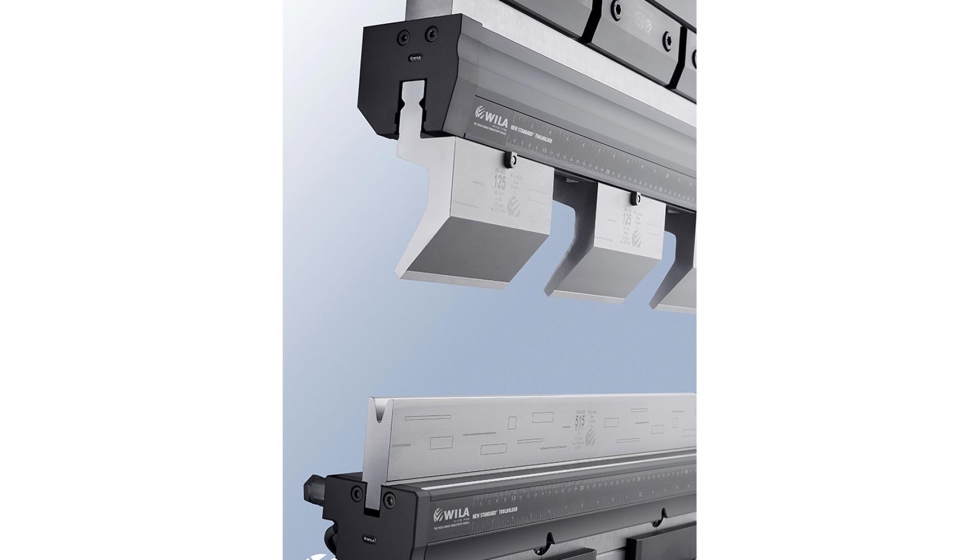
La elección del punzón
A la hora de elegir el punzón es necesario determinar ángulo del punzón según el plegado menor del perfil; determinar también el radio en función del espesor de la chapa y de la V; y, finalmente, determinar altura según perfil y plegadora además de especificar la geometría según perfil y secuencia de plegado.
Estaciones de trabajo
Se habla de estación de trabajo cuando se montan varios conjuntos de utillaje (punzón y matriz) en la plegadora para poder realizar todos los plegados de una pieza. Han de poder trabajar sin molestarse unos a otros y pueden ser conjuntos de utillaje (estaciones de trabajo) del mismo punzón y matriz, pero de diferentes longitudes. También pueden ser conjuntos de utillajes con diferentes punzones y matrices
En el último caso han de cumplir una condición: la altura del conjunto cuando está compactado el punzón y matriz debe ser igual en todas las estaciones de trabajo.
Plegado con radios grandes
Se consideran radios grandes los radios superiores a los que aparecen en la tabla para un espesor de terminado
Existen varios métodos para conseguir los radios grandes
- Con utillaje estándar en varios (muchos) plegados.
- Plegado a fondo matriz / estampado con utillaje especial
- Plegado al aire con utillaje standard o especial
- Plegado a fondo / estampado: Se suele utilizar cuando es necesario un ángulo Y un radio muy preciso. Habitualmente es necesario un utillaje especial y realizar pruebas en fábrica con la chapa que utilizará el cliente en producción.
Plegado al aire: se suele utilizar cuando el radio no necesita mucha precisión. Utilizando la matriz adecuada se puede obtener un ángulo preciso. El sistema es válido cuando la relación entre el radio interior de plegado y el espesor de la chapa es igual o inferior a 25. Para una relación mayor puede ocasionar problemas de marcas o plegados ‘poligonales’. Cuando mayor es el radio con relación al espesor de chapa mayor es el retorno elástico del material. Cuando se deje de aplicar la fuerza de plegado el ángulo y el radio de plegado aumentarán. Al aumentar el radio debido al retorno elástico el punzón ha de tener un radio inferior o igual al radio interno que se desea obtener. La V de la matriz debe ser entre 2,2 y 2,5 veces el radio exterior de plegado. El ángulo de la matriz debe poder compensar el gran retorno elástico del material si queremos obtener el ángulo de plegado preciso.
Si la relación entre Rint y espesor es superior a 25 y la chapa a plegar es fina (máximo 1,5 o 2,0 mm) se puede utilizar como matriz un contenedor + uretano. Para evitar los problemas de plegado ‘poligonal’. Ventajas: El retorno elástico es menor y no marca las piezas Inconvenientes: la vida del uretano es menor que una matriz fabricada en acero.
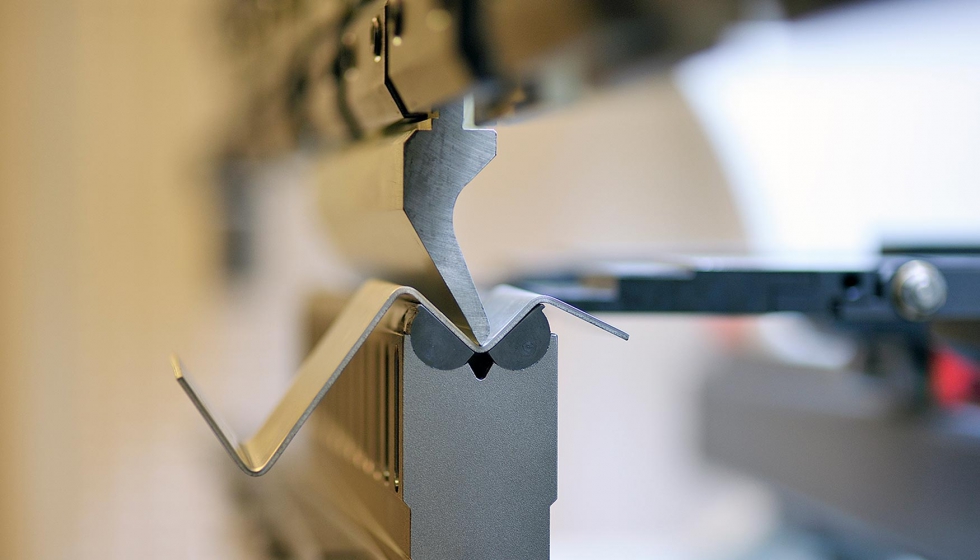
Plegado y aplastado
Existen 3 sistemas habituales para realizar el aplastado: el método tradicional, con matriz monolítica y con matrices móviles (muelle o neumática).
- Método tradicional: Se realiza en 2 fases con 2 tipos de utillaje. Requiere realizar primero el plegado pasado de grados con utillaje standard y tras cambiar el utillaje realizar el aplastado.
- Método matriz fija: se compone de una matriz con una ‘U’ profunda y un punzón que realizará el plegado previo al aire y el aplastado. Adecuado para aplastados tipo lágrima.
Ventajas:
o La matriz se puede fraccionar
o se puede utilizar como matriz standard.
o La altura es siempre la misma
Inconvenientes:
o El plegado al aire implica un radio grande. Lo que más cuesta aplastar es el radio (ver tabla)
o Recorrido para aplastar de 58 mm
o El radio de la ‘U’ puede ocasionar defecto en el aplastado
o El punzón solo tiene 10 mm de superficie de aplastado
- Método matriz móvil: Necesita punzón y matriz con los mismos grados. Se pliega en la parte superior de la matriz y se aplasta entre la parte móvil y la base fija. Es un plegado previo es un estampado. Adecuado para aplastado total (2 veces el espesor de la chapa).
Ventajas:
o Genera un radio interno de plegado pequeño por lo que es más fácil el aplastado.
o El recorrido de la matriz es de solo 15 mm
o La superficie de aplastado es de 20 mm. Mayor profundidad significa que ‘escupe’ menos la chapa.
o En la versión neumática la matriz está compactada cuando pliega y se abre (a través de CNC) cuando tienes que aplastar. Te ahorras recorrido de 15 mm, plegados más precisos (menos riesgo de que la chapa se mueva al descender la parte móvil), menos desgaste al abrirse y cerrarse menos veces, más adecuada para plegados con robot.
Inconvenientes:
o La matriz no se puede fraccionar ‘libremente’ ya que las partes están sujetas por tornillos y muelles
o Requiere bastante tonelaje en el plegado porque se acuña / estampado
o El operario debe estar atento durante el descenso de la matriz durante el plegado. Aunque la chapa esta ‘pinzada’ se podría mover de posición porque no está apoyada en los topes
o Requiere un cierto mantenimiento y limpieza
En general el aplastado requiere bastante tonelaje sobre todo si se quiere realizar un aplastado total (2 veces el espesor).
Para aplastar 1,0 mm inoxidable se necesitan unas 25 t para una lágrima de 3,5 mm y 60 t para un aplastado total.