Nuevos horizontes para mecanizado de estructuras aeroespaciales de titanio
En los próximos años, se espera un enorme crecimiento del segmento aeroespacial como resultado de la demanda de nuevas rutas y una mayor frecuencia de vuelo por parte del consumidor. Asimismo, influyen la situación demográfica mundial y el enriquecimiento de Asia y Oriente Medio. De hecho, según Airbus, las cifras de tráfico aéreo actuales se duplicarán a lo largo de los próximos 15 años.
Más aviones
Todos estos factores dirigen hacia un mismo resultado: una mayor demanda de aviones. A su vez, el reto de los fabricantes de equipos originales aeronáuticos será acelerar la producción.
Asimismo, se produce un claro efecto ‘llamada’ para la cadena de suministro del sector aeroespacial. Los talleres de todo el mundo, dedicados a este sector, deben satisfacer requisitos cada vez más exigentes de capacidad, producción, calidad, entregas puntuales y precios. Según un reciente estudio realizado por Deloitte, se prevé que la cadena de suministro de la industria aeroespacial mantenga su transformación centrada en la reducción de costes, respuesta acelerada e inversión incrementada.
Con respecto a las estructuras aeroespaciales, la demanda de aumentar el nivel de titanio en las aeronaves sigue en auge, principalmente como resultado del impresionante rendimiento resistencia/peso. Sin embargo, las estructuras aeroespaciales son grandes y suele tener que eliminarse una gran cantidad de material antes de poder ver la pieza final, lista para ser montada. Por ello, es muy importante para los proveedores de herramientas de corte ofrecer soluciones que proporcionen una gran productividad y una vida útil larga y predecible. No obstante, es necesaria más de una única innovación en el ámbito de las herramientas para satisfacer los requisitos a los que se enfrentan los talleres modernos con una producción optimizada de estructuras aeroespaciales de titanio. A veces, se necesita una estrategia completamente nueva.
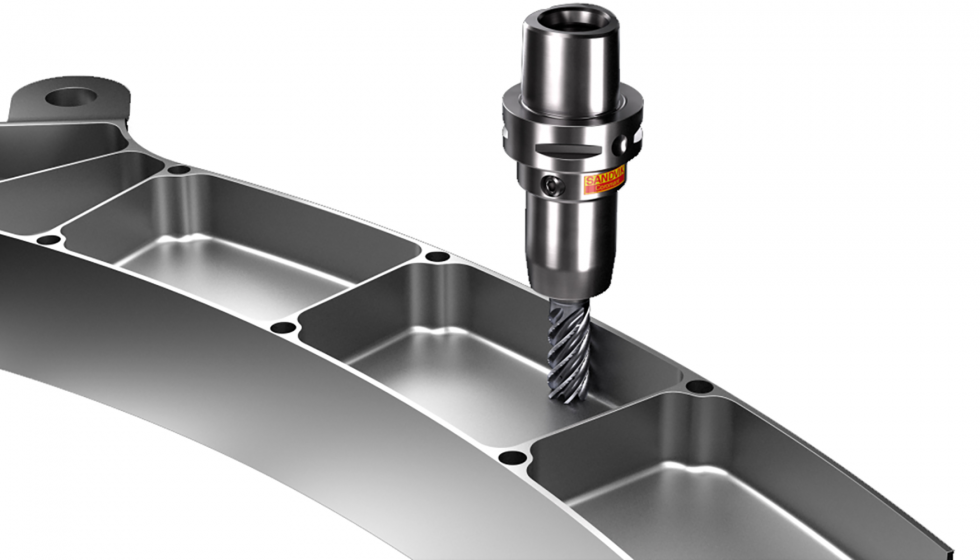
Un nuevo enfoque
Esta estrategia es el fresado lateral de alto avance, que se diferencia de los enfoques de mecanizado tradicionales que utilizan grandes empañes radiales y obligan a emplear velocidades de corte bajas de 40-60 m/min. Por el contrario, el fresado lateral de gran avance se caracteriza por un empañe radial pequeño, un espesor de viruta constante y velocidades de avance y corte grandes.
En Sandvik Coromant, el equipo de I+D estaba decidido a crear una herramienta de corte que permitiera beneficiarse de nuevas estrategias de fresado como el fresado lateral de alto avance con ayuda de la programación CAM, dado que una productividad elevada y una mayor vida útil de la herramienta podrían suponer grandes beneficios.
Tras dos años de intensivo trabajo de desarrollo, el resultado es la fresa de ranurar enteriza de metal duro CoroMill Plura para fresado lateral de alto avance (HFS por sus siglas en inglés), una solución exclusiva cuya geometría y calidad han sido específicamente creadas para mecanizar aleaciones de titanio y, específicamente, trabajar en combinación con estrategias de fresado lateral de alto avance.
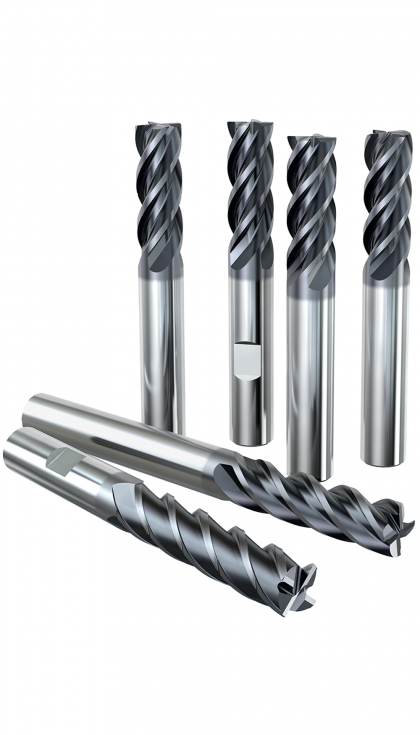
Velocidades de corte >100 m/min
La productividad siempre ha sido el punto débil de los talleres que producen piezas de titanio. Esto se debe a que la maquinabilidad es limitada por la alta reactividad química, baja conductividad térmica y propiedades de autotemplado del titanio. Para combatir estos problemas, la más reciente fresa de ranurar ha sido diseñada para ofrecer un rendimiento fiable al mecanizar aleaciones de titanio a velocidades de corte superiores a 100 m/min, con, a su vez, una vida útil prolongada.
El principal mecanismo de desgaste durante el fresado de aleaciones de titanio es el desgaste por difusión, provocado por una interacción química del titanio de la pieza y los elementos químicos del recubrimiento y el sustrato de la herramienta. Una mayor temperatura en la zona de corte intensifica la reacción química, por lo que para quienes buscan una herramienta más duradera es especialmente importante contar con un sistema de refrigeración efectivo.
Para mejorar la transferencia térmica de la zona de corte y usar refrigerante de forma más eficiente, la más reciente fresa de ranurar enteriza de metal duro está equipada con una solución de refrigerante interior recientemente desarrollada. Los canales de refrigerante tienen salidas (una por estría) específicamente posicionadas para permitir que el líquido llegue a la sección con mayor carga térmica de la zona de corte. Para incrementar más aún la eficiencia del refrigerante, la herramienta está equipada con el exclusivo sistema Coolant Booster (patente en tramitación) que presenta ranuras de suministro de refrigerante en el lado de incidencia, diseñadas para dispersar mejor el calor.
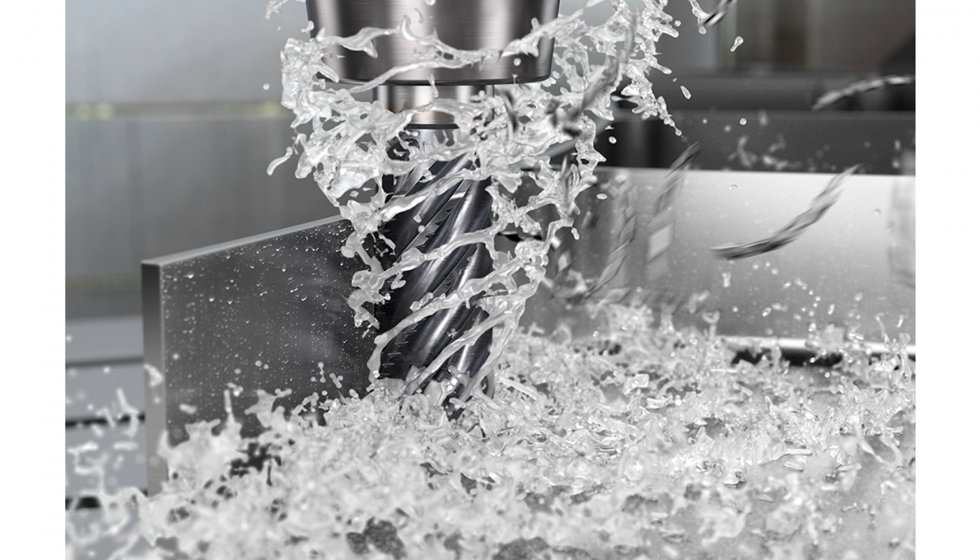
Calidad y geometría más definidas
Los filos agudos son otro requisito previo al fresar aleaciones de titanio dado que ayudan a reducir las fuerzas de corte y a minimizar el efecto de autotemple. En la nueva herramienta, se combinan filos agudos con un nuevo recubrimiento (patente en tramitación) que presenta una capa interior de TiAlN y una exterior con silicio. La capa exterior reacciona con las aleaciones de titanio y forma una fina capa protectora submicrónica encima del recubrimiento original. Durante el proceso de corte, las nuevas virutas formadas se deslizan por la capa de protección, lo que evita deterioro rápido del recubrimiento original y prolonga la vida útil de la herramienta.
Un importante fabricante de equipos originales del sector aeroespacial ha comprobado en su planta europea los potenciales beneficios de adoptar esta nueva fresa en combinación con las estrategias de fresado lateral de alto avance. La empresa buscaba aumentar el volumen de producción, ahorrar tiempo y controlar sus costes al mecanizar cavidades en estructuras aeroespaciales de Ti6Al4V en un centro de mecanizado horizontal de cuatro ejes.
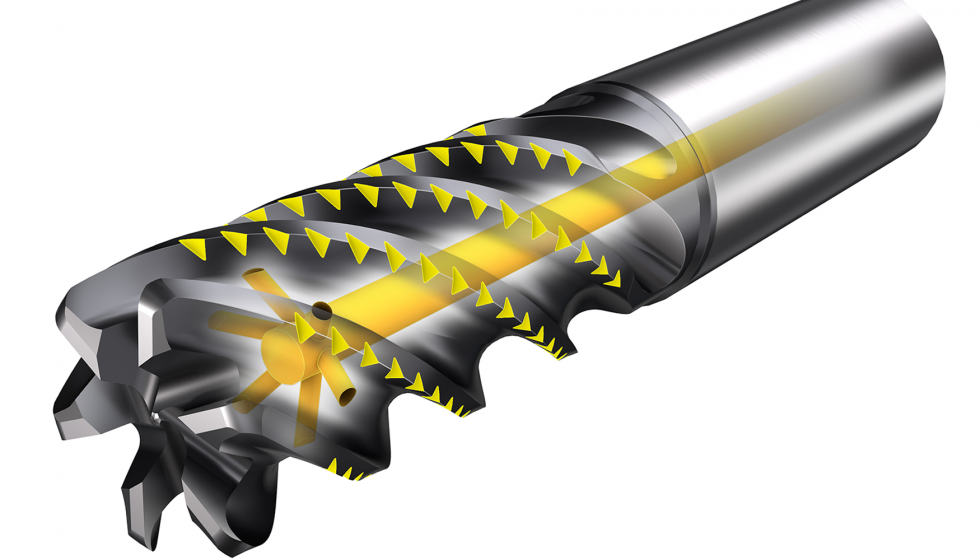
Los resultados
Sustituir la fresa de alto avance de plaquita intercambiable por la fresa de ranurar CoroMill Plura HFS ISO S permitió ajustar los datos de corte y alcanzar así los beneficios deseados. La velocidad de corte ascendió de 50 a 110 m/min y la profundidad de corte axial incrementó de 1 a 30 mm. A su vez, se redujo la profundidad de corte radial. Los resultados fueron impresionantes.
Antes, el tiempo de mecanizado de las cavidades en estructuras aeroespaciales era de 150 minutos, con una vida útil de 37,5 minutos. Al usar la fresa de ranurar CoroMill Plura HFS ISO S, el tiempo de mecanizado se redujo a un tercio y la vida útil fue cuatro veces superior. Como resultado, la planta experimenta unos ahorros anuales de 14.000 € tan solo en la operación de mecanizado de cavidades.