Radiografía del sector metalúrgico
25 de abril de 2008
Cabe destacar que excepto la Comunidad Foral de Navarra, que presenta una tasa negativa del 0,3 por ciento, el resto de comunidades aumentaron sus ventas respecto al ejercicio anterior.
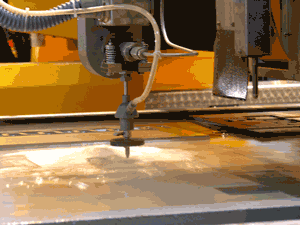
La industria del metal en España
El contexto económico, tanto a escala mundial como nacional, en el cual se ha visto inmersa la industria española del metal presentó una situación favorable, con un crecimiento por encima del 4 por ciento. Esta fase de expansión experimentada, con Estados Unidos y China como impulsores indiscutibles, fue el resultado de políticas expansivas llevadas a cabo por diversos de los países desarrollados, la bajada de los tipos de interés y la dinámica general del comercio.
España, como viene haciendo ya desde hace algunos años, mantiene un crecimiento superior a la media europea, fruto especialmente de la demanda nacional, de la fuerte creación de empleo y de la reactivación de la demanda exterior. Por lo que a la oferta respecta, destacan con fuerza el sector de la construcción y el sector terciario, convirtiéndose en motores esenciales del crecimiento español. El conjunto industrial, clave para el desarrollo de la actividad asociada al metal, mejora en sus exportaciones, aunque un comportamiento similar de las importaciones impide un balance mucho más positivo.
Evolución y situación actual del sector del metal
Contrariamente, en el 2006, casi todas las actividades mantuvieron un buen ritmo de crecimiento, salvo 'Maquinaria de Oficina y Equipos Informáticos', cuya variación es negativa. Las actividades que registraron un mayor crecimiento han sido 'Maquinaria y Material Eléctrico', 'Instrumentos de Precisión y similares' y 'Maquinaria y Equipo Mecánico', aun no siendo todas ellas las de más peso dentro del sector.
Comercio exterior
En 2005 las exportaciones crecieron un 3,8 por ciento anual, alcanzando la cifra de 76.651,6 millones de euros, lo que supone casi la mitad de las ventas totales que realizó España al exterior.
Al año siguiente, las exportaciones de productos metálicos en la media de los siete primeros meses del año anotaron un incremento del 10,8 por ciento en comparación al mismo período del año anterior, después de aumentar en junio un 11,1 por ciento y un 2,9 por ciento en julio.
Paralelamente, y retrocediendo de nuevo al 2005, las importaciones crecieron un 7,6 por ciento, alcanzando los 111.206,1 millones de euros, cifra que representa el 48,1 por ciento de las compras totales que realizó España del exterior.
Respecto al 2006, hasta julio las importaciones crecieron de media un 11,2 por ciento interanual, después de registrar un avance del 15 por ciento en junio y un 10 por ciento en el mes de julio.
En el 2006, desde enero hasta julio, el saldo comercial de productos metálicos aumentó su déficit en un 12,2 por ciento respecto al mismo período del 2005, situándose en -22.229 millones de euros.
La industria de la máquina-herramienta
La mejor forma de describir la importancia que tiene el sector de la máquina-herramienta dentro de la economía nacional e internacional es a través de sus cifras más representativas:
- España figura entre los 9 principales países productores de máquinas-herramienta del mundo
- Por volumen de exportaciones, ocupa el octavo lugar entre los líderes de la actividad exportadora del sector
- España ocupa el tercer lugar en la clasificación de la Unión Europea de los principales países productores y exportadores de máquinas-herramienta
- En la última década ha exportado el 58% de la producción a 120 países
- El 70% de la producción se ha exportado a países con un alto nivel de industrialización y desarrollo tecnológico.
Igualmente, en julio de 2006 la tasa acumulada ya se situaba en el 69 por ciento, aunque es una cifra inferior en 0,3 puntos a la de los siete primeros meses del 2005.
Resumiendo, las compras realizadas por demandantes extranjeros se han incrementado gradualmente pero, dado que las importaciones han experimentado una dinámica semejante, esta buena marcha no ha sido suficiente para repercutir significativamente ni en la mejora del déficit ni en la de la tasa de cobertura.
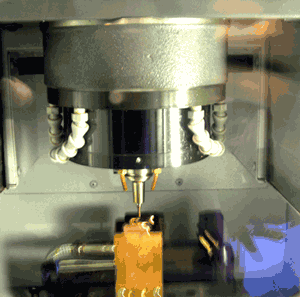
Gastos internos en I+D
Este organismo tiene como objetivo promover la mejora de la competitividad del tejido productivo español en el sector del metal, dados los retos que plantea la globalización de la economía, con la creciente competencia que supone, la preservación del medio ambiente y la sociedad del conocimiento y la innovación.
Una buena evolución de la industria manufacturera es indispensable para el crecimiento económico, y es por ello que se pretende unir esfuerzos para fomentar el desarrollo y la modernización tecnológica, potenciando la capacidad productiva y exportadora de las empresas y consolidando inversiones y ocupación, entre otros muchos aspectos.
Así pues, uno de los elementos esenciales a la hora de predecir el futuro de cualquier sector, y en este caso el del metal, es conocer su apuesta por la innovación tecnológica, hecho reflejado en sus gastos internos de I+D en cada una de sus ramas industriales.
En 2005, los gastos en Investigación y Desarrollo en el sector del metal crecieron más del 6 por ciento respecto al año anterior y alcanzaron así los 1.620,804 millones de euros.
Dada la diferente representatividad de cada una de las actividades dentro del sector del metal, es obvio que la inversión relativa o los gastos destinados a I+D variarán también en función del tipo de producto.
Por ramas de actividad, destacan los elevados gastos de Investigación y Desarrollo que realizan las industrias de “Otro Material de Transporte”, “Maquinaria y equipo Mecánico” y “Vehículos de Motor”.
Por otro lado, son poco significativos los gastos que a esta función destinan sectores como “Metalurgia” y “Máquinas de oficina, cálculo y ordenadores”.
Si se comparan los gastos en I+D que realiza el sector del metal con los fondos destinados al mismo concepto por parte del resto de actividades industriales, se puede apreciar que el sector metalúrgico contribuye en mayor medida al progreso técnico. Asimismo, el sector industrial en su conjunto también dedica más recursos dirigidos a la innovación tecnológica, en comparación con los sectores no industriales.
Los gastos en Investigación y Desarrollo que el sector metalúrgico realiza representan casi una tercera parte del total de España, con 1.620,804 millones de euros. A su vez, dentro del total de fondos destinados a I+D en el sector industrial, su inversión representa más de la mitad (53,6 por ciento).
Perspectivas
Sin embargo, por otro lado cabe esperar que mejore nuestra demanda externa gracias al impulso de las principales economías europeas con las que el metal español mantiene estrechos lazos comerciales, así como también una mejoría en la demanda interna con un incremento de la inversión en bienes de equipo y el mantenimiento de la inversión en construcción.
Producción
El valor de la producción del sector ha aumentando progresivamente desde el año 2003, aunque también es apreciable que esta situación ni se ha dado en todos los tipos de máquinas-herramienta ni tampoco con la misma intensidad.
Por grupos, tanto las máquinas de arranque como las de deformación vieron crecer el valor de su producción en 2005, en un 10 por ciento cada uno de ellos. Los tipos de máquinas-herramienta que experimentaron un mayor crecimiento en sus cifras fueron las mandrinadoras, los tornos y los taladros, con un 57 por ciento, un 29,4 por ciento y un 28 por ciento respectivamente. En cambio, las que presentaron tasas anuales más negativas, en términos de producción, son las Máquinas de procesos físicos-químicos (-17,45 por ciento), las máquinas especiales y transfer (-12 por ciento) y las prensas hidráulicas (-11,8 por ciento), seguidas de las cizallas guillotina, las sierras y tronzadoras y las rectificadoras con tasas también negativas aunque menores.
Tras algunos ejercicios complicados en los cuales el valor de la producción había sufrido algún ligero estancamiento o retroceso, para el sector el año 2005 se convirtió en un momento de inflexión a partir del cual la actividad se reavivó, prolongándose hasta el presente. Y así lo confirma el recuadro anterior, que muestra cómo la facturación del 2006 es de 991,38 millones de euros, lo que corresponde a un crecimiento superior al 9 por ciento en relación al año anterior.
El grupo que más ha contribuido a ello ha sido el de máquinas de arranque viruta, puesto que a parte de que su participación en el sector es mayor, su tasa de crecimiento también ha sido superior, de más del 14 por ciento en el 2006.
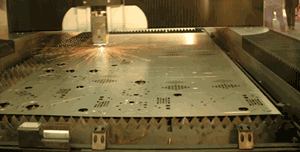
Comercio exterior
La exportación en el año 2005 llegó a ser el 55 por ciento del valor total de la producción, con 498,73 millones de euros, lo que representa un aumento de más del 19 por ciento, y se convierte así en uno de los elementos impulsores en esta fase de expansión que está viviendo el sector. Alemania se afianza como principal país destino de los productos del sector, acaparando un 15,8 por ciento de las ventas que realiza España al exterior. Detrás, le siguen Francia e Italia a nivel comunitario, y México y Estados Unidos como extracomunitarios, todos ellos países que van ganando cada vez más terreno en detrimento de Alemania.
Es importante remarcar la aparición en escena de países como la República Checa, Suecia, Argelia y Rumania, con aumentos del 314 por ciento, 100 por ciento, 560 por ciento y 84 por ciento, respectivamente. Por el contrario, hay países que han desaparecido del ranking de países destino de exportaciones españolas, como son Polonia, Canadá, Suiza y Países Bajos.
Tal y como ya se pudo ver con los países destino de las exportaciones del sector máquina-herramienta español, los países europeos se sitúan en primera línea también en cuanto al origen de las importaciones efectuadas por España. Sin embargo, aquí quien posee el liderato es Italia, con más de la cuarta parte del total, un 25,36 por ciento, aunque seguida de muy cerca por Alemania (24,62 por ciento). Ya a más distancia, encontramos a Japón y Suiza, con un 10,67 por ciento y 7,27 por ciento respectivamente.
Es interesante comentar la progresiva pérdida de influencia de EE UU en el comercio español, reduciendo sus ventas casi hasta la mitad en estos tres años, y a diferencia de la mayoría de países que, en general, se mantienen estables o incluso crecen.
Como puede apreciarse, el 2006 ha sido un año con balance positivo para el sector máquina-herramienta, empezando por la producción, cuyo valor ha aumentado en un 9,6 por ciento. Igualmente ocurre con las relaciones comerciales del sector español: las exportaciones han aumentado más de un 14 por ciento y las importaciones no han sufrido variación significativa alguna. Como consecuencia, la tasa de cobertura, obtenida a partir de la relación entre exportaciones e importaciones, ha mejorado considerablemente.
Las exportaciones, las cuales representan actualmente más de la mitad de la producción del sector, alcanzan los 569,34 millones de euros. Además, si se le restan al total de la producción se obtienen las ventas efectuadas en el mercado interior, que en el 2006 han sido de 422 millones de euros.
Por otro lado, el consumo aparente de máquinas-herramienta del mercado español, resultado de sumar la producción española y las importaciones y a esto restarle las exportaciones, alcanza la cifra de 877,88 millones, más del 80 por ciento del valor total de la producción.
El sector de moldes y matrices
En la integración hacia atrás en la cadena de valor, el sector se caracteriza por mantener una mayor relación con sus proveedores de componentes estandarizados y suministradores de acero, puesto que es una materia fundamental en su actividad. Asimismo, y al igual que en muchos otros campos industriales, este sector requiere de cuantiosas inversiones en capital, de modo que los proveedores de máquinas-herramientas para sus líneas de producción también son considerados importantes colaboradores en el sector.
La evolución del sector a lo largo de los últimos años no presenta muy buenas condiciones: el número de organizaciones de moldes y matrices ha ido disminuyendo paulatinamente y, lógicamente, también lo han hecho los empleados. Sin embargo, al estar esa reducción acompañada de un aumento del volumen de negocio, puede significar que el sector español está atravesando una etapa de reconversión con tal de avanzar hacia una industria basada en tecnología punta, automatizada, competitiva y eficiente, requiriendo quizás menos trabajadores pero con una mayor cualificación.
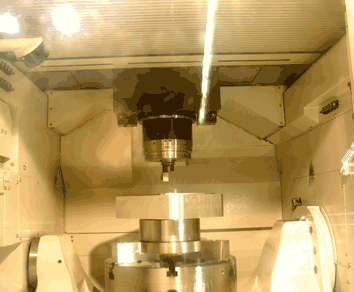
Situación actual
En 2005, el sector de moldes y matrices español era constituido por 800 empresas, la mayoría de ellas microempresas, proporcionando empleo a más de 10.000 personas.
El personal del sector se distingue por su alta formación y profesionalidad, derivado de las constantes transformaciones tecnológicas que envuelven el sector y de la necesidad de satisfacer las exigencias de los demandantes, ambos requisitos de competitividad.
Segmentos de la demanda
Como puede observarse, la producción española de moldes y matrices se caracteriza por la pluralidad de sus destinos. No obstante, es evidente que hay un colectivo que destaca sobre los demás: la industria del automóvil o el sector auxiliar de automoción acaparan casi la mitad de las ventas. Detrás, se encuentran el sector fabricante de electrodomésticos y el eléctrico y electrónico, absorbiendo un 15 por ciento del total cada uno de ellos.
El tercer cliente más importante es el de envases y embalajes (9 por ciento), seguido de otros con participaciones inferiores al 5 por ciento como son los sectores productores de juguetes, mobiliario, productos metálicos y otros.
Comercio exterior
Es indudable que el peso específico de las exportaciones del sector recae sobre Francia y Alemania, con cuotas del 25,3 por ciento y 23,3 por ciento, respectivamente. A distancia se sitúan Italia, Suecia y México, configurando así, el conjunto de los 5 países, más del 63 por ciento de la demanda externa de moldes y matrices.
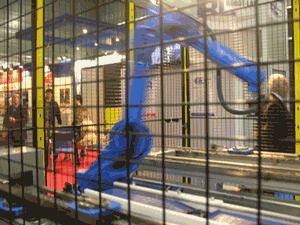
El sector de moldes y matrices en Cataluña
Con estas cifras, Cataluña se convierte en una de las principales regiones europeas en términos de fabricación de moldes y matrices, los cuales se diferencian por su elevado nivel tecnológico y una excelente relación calidad-precio. De esta manera, Cataluña se considera uno de los motores del sector en España.
El sector de accesorios, componentes y herramientas de corte para máquina-herramienta
Las empresas fabricantes de accesorios, componentes y herramientas de corte para máquina-herramienta se caracterizan por conseguir soluciones tecnológicas a medida y por sus constantes innovaciones, con lo que conceptos como modernidad y flexibilidad se convierten en primordiales en sus instalaciones y máquinas, así como la alta cualificación de su personal. Son muchas las empresas que dedican buena parte de sus recursos a I+D, aunque en muchos casos, debido al reducido tamaño de éstas, se realiza de la mano de centros tecnológicos.
Respecto a la demanda exterior, los sectores clientes clave son el de automoción e industria auxiliar y el sector siderometalúrgico, así que el sector queda integrado con los fabricantes de maquinaria, los de suministros industriales, los aceristas y las fundiciones.
Evolución y situación actual
Aun así, España ocupa el noveno lugar entre los principales productores, Japón, Alemania, Italia y China, convirtiéndose como uno de los referentes del sector a nivel europeo.
Según datos provisionales, el 2006 acabó con un balance, sin duda, positivo para los fabricantes nacionales, que facturaron un 9 por ciento más que el año anterior. En lo referente al empleo, su crecimiento ha sido más moderado, casi del 2 por ciento. Y por su parte, la cifra de exportación llegó a aumentar más del 20 por ciento, correspondiendo al 45 por ciento de la facturación, cifra que no se alcanzaba en muchos años y que en 2005 era del 39 por ciento.
El sector de los acabados de superficies
Una de las problemáticas que afecta al sector es la asociada a la materia medioambiental, fruto de la generación de disolventes y residuos tóxicos durante el proceso industrial. Sin embargo, la legislación sobre vertidos tanto líquidos, como sólidos o gaseosos se ha vuelto cada vez más restrictiva y la sociedad demanda nuevos procesos de producción más limpios y seguros. Todo ello, junto al desarrollo de nuevos procedimientos y tecnologías, además de las empresas especializadas en el tratamiento de los residuos, hacen que el impacto al entorno ambiental sea cada vez menor, y con el objetivo de avanzar hacia tecnologías de vertido cero.
Entre los sectores más demandantes del sector de los acabados superficiales se encuentran los fabricantes de moldes y matrices y las industrias como las de automoción o mecánica, aeronáutica y energética, química, alimentación o la eléctrica.
Actualmente, esta industria consta de una amplia gama de técnicas de acabados, las cuales se pueden clasificar en:
- Técnicas del tratamiento: revenido, templado, cementado, nitruración. La finalidad de estas técnicas es endurecer o desoxigenar los metales. Se utilizan como preparación o como acabado final, pero todas son de orden técnico y no decorativo.
- Técnicas de preparado. Las hay físicas: bruñido, limado, pulido, etc. Y también químicas: activado, desengrase, oxidado, etc. Se tratan de procesos previos a otros recubrimientos, procesos químicos o mecánicos.
- Técnicas de protección: lacado, pasivado, barnizado. El objetivo es proteger de la corrosión, es decir, proteger la superficie de cualquier pieza, con o sin recubrimiento, con tal de prolongar su estado de conservación y retrasar la oxidación.
- Técnicas de recubrimiento. Los de tipo técnico, por ejemplo el niquelado o cobreado, se aplican a moldes, matrices, piezas para la industria del automóvil, aeronáutica o telefonía, entre otros, con el fin de ofrecer dureza y resistencia ante la corrosión y el desgaste. Otros, como el anodizado o el cromado decorativo, cumplen además una función estética y decorativa en la automoción, construcción aeronáutica, iluminación y objetos personales y decorativos.
El sector de la soldadura
Además, hay que decir que es un sector muy atomizado, formado por empresas de mediana y pequeña dimensión, y este hecho dificulta mucho la obtención de datos económicos significativos del mismo.
Si se compara el sistema de la soldadura con otras técnicas de ensamblaje como el remachado o el atornillado, éste es más resistente, ligero y con costes de fabricación más baratos.
Además, existen más de cien procesos y variantes de procesos dentro del colectivo de tecnologías de la soldadura, para unir no sólo metales, sino también polímeros y cerámicas, entre otros materiales.
Por otro lado, la soldadura es una de las principales tecnologías llamadas horizontales, debido a su uso en prácticamente todos los sectores industriales, entre los que destaca la industria de la automoción, la petroquímica, la naval, la industria ligada a los bienes de equipo, la construcción en general y, en especial, la de estructuras metálicas.
Un dato alentador es la protección del medio ambiente y la prevención de riesgos laborales en el sector, aspectos cada vez más presentes en los diferentes procesos de soldadura.
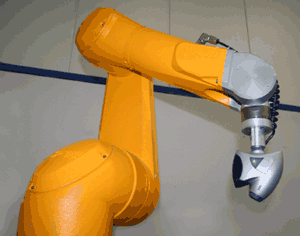
El sector de transmisiones oleohidráulicas y neumáticas
Los principales componentes que configuran los sistemas oleohidráulicos son:
- Acumuladores hidráulicos.
Los sistemas hidráulicos son almacenados y sometidos a considerables presiones. A diferencia de los gases, que son compresibles y pueden almacenarse durante un período de tiempo, los fluidos hidráulicos pueden ser incompresibles pudiendo generar golpes de presión y daños en el circuito.
Así que los acumuladores hidráulicos están diseñados para almacenar energía bajo la forma de presión, absorber golpes hidráulicos, reducir pulsaciones y fluctuaciones de caudal, brindando una operación segura y confiable a través del tiempo. - Bombas hidráulicas. Las bombas hidráulicas son dispositivos que convierten la energía mecánica generada por una fuente exterior en energía hidráulica, aportando caudal al circuito hidráulico.
- Motores hidráulicos. Su función consiste en impulsar las bombas hidráulicas, desarrollando un movimiento continuo y rotatorio.
- Depósitos hidráulicos. Los depósitos cumplen diversas funciones en el sistema hidráulico, como almacenar el fluido requerido, evacuar el calor, o permitir que los contaminantes se diluyan y se depositen en el fondo.
- Caudalímetros. Conocidos también con el nombre de decímetros, anemómetros, HMF o LMS, son medidores de la cantidad de flujo que circula a través de él, y de esta manera permitir un análisis del rendimiento de una bomba o la detección de posibles fugas. Los caudalímetros no acostumbran a instalarse de forma permanente.
El gran desarrollo experimentado por la oleohidrúalica y la neumática en la industria actual es posiblemente debido al atractivo de este medio de transmisión energética, sinónimo de seguridad, calidad y fiabilidad. Además, junto a la garantía de reducir los costes, conforman aspectos de vital importancia en muchos sectores industriales. De esta manera, se convierten en una respuesta eficiente al objetivo de mejorar la rentabilidad y, a su vez, lograr una mayor competitividad.
El sector de la robótica
Lo que se conoce como la robótica, desde que se inició en los años setenta, ha experimentado avances importantes y ha ampliado considerablemente su campo de actuación. Tradicionalmente, sus aplicaciones se centraron en los sectores manufactureros más desarrollados para la producción en masa: la industria del automóvil, las transformaciones metálicas, la industria química, etc.
Sin embargo, en la última década el peso de nuevas aplicaciones en sectores productivos, como son la construcción, la alimentación, la agricultura, y de servicios, como la medicina o la asistencia social, ha aumentado significativamente, con lo que ha creado nuevas oportunidades tecnológicas.
Actualmente, este sector se encuentra en la vanguardia de la innovación tecnológica, siendo el motor productivo de muchos sectores económicos tanto en nuestro país como en la mayoría de los países industrializados. Su rapidez para incorporar nuevas técnicas en los productos para después llevarlos al mercado lo convierte en uno de los sectores con mayor dinamismo y siendo, en muchos casos, el impulsor del desarrollo de muchas de esas tecnologías capaces de incorporar de inmediato la experiencia acumulada en el uso de sus sistemas.
Una de sus particularidades que le diferencia de otros sectores es su facilidad para adaptar los sistemas a las necesidades y demandas de las empresas que, muy a menudo, son dinámicas y requieren constantes reestructuraciones. Otras de las propiedades características del sector de la robótica son la actualización, diversificación de la producción y su relación permanente con el usuario.
Según la UNECE (United Nations Economic Comision For Europe) y la IFR (International Federation of Robotics), en el mundo hay unas 922.875 unidades de robots en el 2005, lo que corresponde a un crecimiento cerca del 9 por ciento respecto 2004. De éstas, la mayoría están concentradas en Asia, especialmente en Japón, y en el continente europeo.
Por regiones, destacan Japón con 373.481 unidades de robots y Norteamérica con 139.553 del total.
A nivel comunitario, Alemania está en cabeza con 126.725 unidades robóticas, y le siguen Italia (56.198) y Francia (30.434). España se sitúa en cuarto lugar dentro de la clasificación europea, con 24.081 unidades, lo que supone un crecimiento de casi el 10 por ciento en relación al 2004, por encima de la media mundial.
El sector de la ingeniería y servicios de soporte
- La industria del metal en España supone el 40% de la producción industrial a nivel nacional.
- Respecto al sector exterior, el sector del metal efectúa el 50% del total de ventas españolas al extranjero y de las cuales tres cuartas partes tienen como destino la Unión Europea.
- Realiza entorno al 30% de la inversión española en Investigación, Desarrollo e Innovación.
- La cantidad de empresas del metal en España representan el 5% del total de las empresas españolas.
- De cada 100 empleados en la industria española, 37 pertenecen a la del metal.
En este sector predominan las pymes puesto que un 87% de éstas son de menos de 10 asalariados y, si se tienen en cuenta las que proporcionan empleo a menos de 100 personas, el porcentaje se eleva hasta el 98%.
La subcontratación industrial
El primero de los objetivos se logra dejando parte del proceso productivo, que posteriormente se incorporará al producto final, en manos de empresas especializadas en ello. Y, simultáneamente, se racionaliza la estructura de costes de fabricación al no tener que soportar la inversión necesaria para afrontar el desarrollo de todo el proceso productivo y, por lo tanto, se aumenta la rentabilidad. Al final, la mejora de la competitividad es la meta que prima sobre cualquier empresa.
Esta descomposición de la cadena de valor se ha visto favorecida por una serie de factores comunes para el entorno productivo a nivel global: la accesibilidad a los mercados y la facilitación del transporte, la integración progresiva de los espacios económicos, la globalización de la información a raíz de la difusión y el uso de las Tecnologías de la Información y Comunicación (TIC) y la innovación y tecnología.
Por otro lado, hay que recalcar que en este sector, al igual que ocurre en otras actividades empresariales, el tamaño se convierte en un factor diferencial: la exclusividad, la implicación técnica y la capacidad de actuar como contratista es creciente con el tamaño de la empresa. Es decir, a medida que la dimensión de una empresa aumenta, ésta alude más a su propia gestión. Con todo ello, la subcontratación industrial se convierte en uno de los motores de la economía de un país, ya no sólo en el ámbito comercial, sino también como generador de empleo y riqueza y como fuente de incentivos hacia a la inversión.
Tradicionalmente, los sectores que habitualmente acuden a la producción subcontratada son el de la industria de la metalurgia y fabricación de artículos metálicos, el del automóvil, y el de maquinaria y equipo mecánico, tal y como puede observarse en la clasificación presentada a continuación. España se encuentra junto a países como Alemania, Francia, Italia y Reino Unido entre los principales países subcontratistas.
En España, las Cámaras de Comercio gestionan con la colaboración del Instituto Español de Comercio Exterior (ICEX), y a través de las Bolsas de Subcontratación Industrial, el Plan de Subcontratación Industrial. El principal objetivo es apoyar la consolidación e internacionalización de estas empresas mediante el asesoramiento, promoción, formación e información al respecto.
En total existen más de 30 cámaras en España, repartidas entre las diferentes Comunidades Autónomas.
Las perspectivas del sector se presentan inciertas: la reciente ampliación europea supone la construcción de un nuevo mercado en el que ni la demanda ni la oferta siguen siendo las mismas.
De modo que, este escenario en el que países de recién incorporación se están convirtiendo en focos cada vez más dinámicos y atractivos para sectores industriales maduros, tanto por sus bajos costes como por su posición geográfica, puede interpretarse como una señal de riesgo para el tejido industrial contratista y subcontratista de los países de la antigua UE-15.